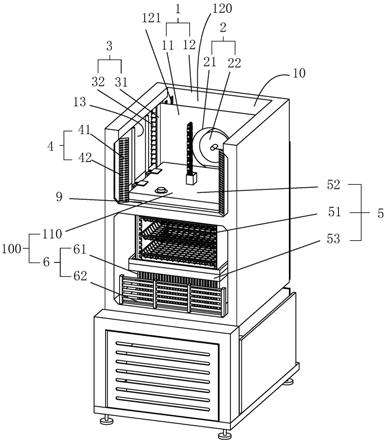
1.本技术涉及冷热冲击检测技术领域,尤其是涉及一种气流循环系统及其制热区温度加速复归的冷热冲击箱。
背景技术:2.冷热冲击试验用于测试材料结构或复合材料,是金属、塑料、橡胶、电子等材料行业必备的测试。冷热冲击试验是在单位时间内进行制热或制冷测试;完成测试后,在短暂的时间内完成从制热区到制冷区或从制冷区到制热区的区间转换和继续测试。然而,进行区间转换时,制热区和制冷区之间会产生对流气流,导致区间各自区间内的气温骤降或骤升。从制热区进入制冷区时,可以提前降低制冷区的温度,区间转换时,气流中和后,可使得制冷区内的温度快速地接近理想温度。制热区的预置温度已经较高,通过提高制热区温度以中和从制冷区流入的气流不再适用;制热区的热量因冷气流等消耗大,需要在越短的时间内恢复到理想的测试温度,测得的技术参数越精准确。
3.有鉴于此,提供一种在更短的时间内恢复制热区温度的制热区温度加速复归的冷热冲击箱成为必要。
技术实现要素:4.为了解决上述技术问题,本技术提供一种更短的时间内恢复制热区温度的制热区温度加速复归的冷热冲击箱。
5.本技术提供的一种适用于制热区温度加速复归的冷热冲击箱的气流循环系统采用如下的技术方案:所述冷热冲击箱包括箱体和气流循环系统;所述箱体包括制热区,所述气流循环系统包括顺次设置的吸气机构、调温区间和排气机构;所述吸气机构沿水平方向吸气,排气机构沿水平方向排气。
6.本技术提出的制热区温度加速复归的冷热冲击箱,通过在水平方向进行吸气和排气,使得制热区内的气体加速循环,以使得气温在较短时间内达到预定温度区间。气流经历短距高效的加热后,吸气机构抽吸并推送气流,气流经调温区间快速携热从排气机构排出,热气流进行热幅射后,吸气机构抽吸造成吸气机构外侧形成负压气流,较高气压区间的气流经热幅射后向低气压区间流动,再被吸气机构回吸加热,形成高效有序的气流循环,解决了气流交换后,温差调节需要较长的调节时间的技术问题。使得箱体内的整体温差小于2℃。
7.所述制热区包括第一侧壁、与所述第一侧壁相对设置的第二侧壁和连接于第一侧壁和第二侧壁之间的连接壁;所述第一侧壁包括内侧壁和外侧壁,所述内侧壁与所述外侧壁之间形成容纳腔;所述气流循环系统包括顺次进行气流控制的吸气机构、调温区间、排气机构和折流板,所述吸气机构和所述调温区间设于所述容纳腔内;所述吸气机构设有吸气口;所述吸气口开设于所述内侧壁上;所述排气机构设于内侧壁上,所述折流板接近于所述第二侧壁
与连接壁的连接处且设置于连接壁上,所述折流板与所述排气机构呈非垂直夹角地相对设置;所述发热丝接近于所述排气机构设置;所述折流板包括折流区和直通孔;所述调温区间内设有发热丝;气流经所述折流区形成折返气流、经直通孔形成直通气流;所述折返气流和所述直通气流经连接壁和/或第二侧壁后向箱体中部汇聚。
8.本技术提供的适用于制热区温度加速复归的冷热冲击箱的气流循环系统,设置于制热区温度加速复归的冷热冲击箱的制热区间,对制热区区间内的热度进行调节和控制,引导气体流向,调节气流的滞留时序,充分进行携热并进行热幅射,提高热交换效率。
9.吸气机构、调温区间、排气机构和折流板均设于制热区内,对制热区内的气流进行引导和控制实现热量传递和调节;具体是吸气机构抽吸制热区除容纳腔以外的气体,内侧壁以外的气流自吸气机构向调温区间推送气流,气流在排气机构位置附近通过加热丝进行热量吸收,从排气机构排出后进行热幅射。
10.本技术提出的气流循环系统,因排气机构与折流板相对设置,自排气机构流出的热气流主要流向折流板,其次因受连接壁、流体自由扩散等原因,部分气流自排气机构流出向箱体中部扩散。流向折流板的气流因折流区及直通孔,将气流分隔成两部分,其中部分气流被折返后与连接壁相作用,使得气流流向箱体中部;另一部分气流穿过直通孔,穿过直通孔的气流与第二侧壁相作用流向箱体中部,同时解决了箱体内的涡流现象和气流噪音。
11.本技术提出的气流循环系统,气流在排气机构处经历短距高效的加热,自排气机构排出携热气流经历排气机构、与折流板之间的长距滞留,再经折流板对气流进行分流,使得气流得到充分的热幅射时间,经充分热幅射后,气流再被吸气机构回吸加热,形成高效有序的气流循环系统。
12.进一步地,所述排气机构包括导流段、排气口和导流板,所述导流段自内侧壁向第二侧壁方向延伸,所述排气口设于所述导流段的前部,所述导流板设于排气口内,所述导流板与所述折流板相对设置。
13.本技术通过在上述排气机构设置短距导流构造,使得气流具有一定的导流向性,但是不能过度约束气流方向造成前端的气流扩散不充分。然而气流在经历多次的热量交换后,会形成上下温差连续相近,进行热幅射区域内的较高温与较低温气流温差相差较大的技术问题。因而导流构造需要解决同温气流层的问题。为打破气流分层现象,使得进行热幅射的气体的温度更均匀,温差更小,通过设置导流板进行上下层之间的气流层转换调节实现上述目的。
14.进一步地,所述直通孔为横向设置且两端圆滑过渡中部呈方形孔状;所述导流板引导气流与内侧壁呈非垂直夹角地向第二侧壁方向排出。
15.本技术提出的直通孔呈扁平开口的阵列设置,其开设于形成气流压缩穿过直通孔后,气流会再次产生扩散效应,使得气流进一步地进行混合、气温均匀化。
16.进一步地,所述排气机构至少包括有两个,其中两个所述排气机构分设于所述第一侧壁两侧,所述折流板相应于所述排气机构至少设置有两个,任一所述折流板相应于所述排气机构设置。
17.本技术提出的排气机构呈多个设置,多个排气机构与折流板相匹配,进一步保障幅射气流的温度均匀。进一步地,成对设置的折流和排气机构形成的气流循环系统,还可以
是三组、四组及更多组;而设置多组气流循环系统将影响第二侧壁一侧的温度,同行条件下,四组气流循环系统比二组气流循环系统的温度高,此时可通过调速折流孔大小进行有限次数的实验或计算得到。
18.进一步地,所述吸气机构还包括叶轮,所述吸气口呈开设于所述内侧壁上的圆形,通过设置所述吸气口于所述内侧壁与所述外侧壁之间形成吸气腔,所述叶轮设于所述吸气腔内。
19.通过使用叶轮,形成气流的推动的正向压力和气流流向抽吸方向更统一,形成的低压区域引导气流向吸气口方向汇聚,圆形吸气口与叶轮旋转形成的扇面结构相仿形,形成良好的气流效应。
20.进一步地,所述箱体还包括设于其内部中间的载物台,所述载物台无侧壁;自所述排气机构流出的气流在排气机构与折流板之间形成绕向气流,所述绕向气流、折返气流和正向气流向载物台方向汇聚。
21.载物台与制热区内形成无阻碍的气流直接对流,对试样热幅射的效果更佳。
22.本技术提出的制热区温度加速复归的冷热冲击箱通过气流循环系统保证制热区内的热能均匀程度保持在较高的程度下。
23.所述冷热冲击箱包括将所述箱体分隔为制热区和制冷区的隔热支撑板和载物台;所述载物台包括顺次设置的第一密封部、主体和第二密封部;所述隔热支撑板设有可供主体于制热区和制冷区之间往复运动的转换区间,所述第一密封部和第二密封部分设于隔热支撑板两侧;当所述主体位于制热区时,第二密封部与隔热支撑板气密性连接,当所述主体位于制冷区时,第一密封部与隔热支撑板气密性连接。
24.本技术提供的制热区温度加速复归的冷热冲击箱,该冷热冲击箱通过载物台于制热区和制冷区之间来回地进行往复运动,以检测试样的抗冷热冲击性能。
25.进一步地,所述箱体还设有箱门,所述第一侧壁相对于所述箱门设置,所述折流板设于与所述箱门相接的连接壁上。
26.本技术通过设置箱门,方便放取被测试样,同时内侧壁设于与箱门相对的位置更方便检测。
27.作为优选,所述制冷区还包括有蓄冷装置和蓄冷装置加热丝,所述蓄冷装置加热丝相应于所述蓄冷装置设置。
28.通过对蓄冷装置进行加热,调节制冷区内的温度。
29.所述制冷区设有保温层,所述制热区设有保温层,所述冷热冲击箱设有保温层。
30.通过设置保温层,减少造成能量流失,提高冷热冲击测试的质量。
31.综上所述,本技术提供的制热区温度加速复归的冷热冲击箱,将气流循环系统设置于制热区加速制热区温度的复归,对制热区区间内的热度进行调节和控制,引导气体流向,调节气流的滞留时序,充分进行携热并进行热幅射,提高热交换效率。吸气机构抽吸制热区除容纳腔以外的气体,并对容纳腔内的气体增压从排气机构推出,在紧挨排气机构位置处通过加热丝对气流进行加热,使气流携带大量热能从排气机构流出后进行热交换。
32.热交换过程中,因排气机构与折流板相对设置,自排气机构流出的热气流主要流向折流板;其次因受连接壁、流体自由扩散等原因,部分气流自排气机构流出后向箱体中部
扩散。流向折流板的气流因折流区及直通孔,将气流分隔成两部分,其中部分气流被折返后与连接壁相作用,使得气流流向箱体中部;另一部分气流穿过直通孔,穿过直通孔的气流与第二侧壁相作用流向箱体中部,同时解决了箱体内的涡流现象和气流噪音。
33.本技术提出的气流循环系统,气流经历短距高效的加热,自排气机构排出携热气流经历排气机构、与折流板之间的长距滞留,再经折流板对气流进行分流,使得气流得到充分的热幅射时间,经充分热幅射后,气流再被吸气机构回吸加热,形成高效有序的气流循环,解决了气流交换后,温差调需要在短暂时间内完成调节的问题,具有重要意义。
附图说明
34.图1是本技术提供的制热区温度加速复归的冷热冲击箱内部构造结构示意图;图2是制热区气流导向结构示意图;图3是制热区第二角度气流导向结构示意图;图4是本技术拆除部分外部结构的结构示意图;图5是载物台结构示意图;附图标记说明:1、第一侧壁;11、内侧壁;12、外侧壁;13、连接壁;2、吸气机构;21、吸气口;22、叶轮;3、排气机构;31、导流段;32、导流板;4、折流板;41、折流区;42、直通孔;5、载物台;51、主体;52、第一密封部; 53、第二密封部;6、制冷区;61、蓄冷装置;62、蓄冷装置加热丝;7、第二侧壁;8、箱门;9、隔热支撑板;10、容纳腔;100、箱体;110、制热区;120、调温区间;121、发热丝。
具体实施方式
35.以下结合附图1
‑
5对本技术作进一步详细说明。
36.如图1所示,本技术提供了一种适用于制热区温度加速复归的冷热冲击箱,该冷热冲击箱包括箱体100和气流循环系统(未示出);箱体100包括制热区110,气流循环系统包括顺次设置的吸气机构2、调温区间120和排气机构3;吸气机构2沿水平方向吸气,排气机构3沿水平方向排气。
37.如图1所示,本技术提供了一种适用于制热区温度加速复归的冷热冲击箱的气流循环系统,冷热冲击箱包括箱体100;箱体100包括制热区110,制热区110包括第一侧壁1、与第一侧壁1相对设置的第二侧壁7和连接于第一侧壁1和第二侧壁7之间的连接壁13。一般情况下,箱体100为正六面体,与之相连接的连接壁13为四个,四个连接壁13位于第一侧壁1与第二侧壁7之间。然而将连接壁13设为五个侧壁,此时,第一侧壁1和第二侧壁7为五边形的面;将连接壁13设为六个侧壁,此时,第一侧壁1和第二侧壁7为六边形的面;即不管其箱体100构造如何变换,基于气流循环系统的制热区温度加速复归的冷热冲击箱应属于本技术的精神所在;下面将以正六面体,四个连接壁13为示例进行阐述本技术提出的方案。
38.如图1所示,第一侧壁1包括内侧壁11和外侧壁12,内侧壁11与外侧壁12之间形成容纳腔10;气流循环系统包括顺次进行气流控制的吸气机构2、调温区间120、排气机构3和折流板4。吸气机构2用于从内侧壁11的其中一侧壁把气流抽进另一侧壁 ,即使得气流进入容纳腔10;调温区间120用于将气流进行升温;排气机构3用于进行气流引导和区域内温层
调节转换;折流板4用于进行气流控制、增量幅射和调整气流流向、消除噪音和涡流等。吸气机构2和调温区间120设于容纳腔10内,形成相组合在一起的动力构造,完成动力引导和维持,并将形成的动能于排气机构3处汇聚形成较高速的气流,该气流中的较大一部分经折流板4后向箱体100中部汇聚,气流在整个热幅射过程中,使被测物能够充分地进行加热。
39.如图图1、图2和图4所示,本技术提出的于内侧壁11和外侧壁12之间构建起容纳腔10,并且在容纳腔10上设置吸气机构2,吸气机构2的吸气口21设于内侧壁11上,即为容纳腔10在内侧壁11开设了进气的开口。作为优选,吸气口21开设于内侧壁11上,内侧壁11的主要部分正对于箱体100中部,吸气口21设于该处,抽吸气流效果更佳。排气机构3设于内侧壁11上,吸气机构2设于内侧壁11中部,排气机构3设于内侧壁11与连接壁13相连接的位置处,形成气流循环。
40.如图1、或图3所示,折流板4接近于第二侧壁7与连接壁13的连接处且设置于连接壁13上,折流板4相对应的排气机构3多设于接近于连接壁13上,然而通过隔离结构使得排气机构3与连接壁13不相接触也是可以实现的。如图1、图2、图3所示,发热丝121接近于排气机构3设置,尽量避免热能在容纳腔10内形成损耗,当气体接近于排气机构3时,再进行加热,使得容纳腔10内的主要气流始终保持在一个较低热能的形态下,而被赋予热能后的大部分气体能快速地经排气机构3排出。
41.如图1所示,折流板4包括折流区41和直通孔42;调温区间120内设有发热丝121;气流经折流区41形成折返气流、经直通孔42形成直通气流;折返气流和直通气流经连接壁13和/或第二侧壁7后向箱体100中部汇聚。
42.折返气流及直通气流的方向可通过调节折流板4与排气机构3之间形成的角度实现调节。
43.折流板4与排气机构3呈非垂直夹角地相对设置;该夹角还可以是30
‑
65度,夹角的大小一定程度上影响穿过直通孔42的气流量;较佳地,该夹角接近于45度,当折返气流量接近于穿过直通孔42的气流量。
44.作为优选,折流区41和直通孔42的面积比为1:0.45
‑
2,较佳地,折流板4与排气机构3的夹角接近于45度时,折流区41和直通孔42的面积比接近于1:1.2,通过折流板4的气流与通过直通孔42的气流相接近。
45.折流板4与排气机构3呈非垂直夹角地相对设置;该夹角还可以是30
‑
65度,夹角的大小一定程度上影响穿过直通孔42的气流量;较佳地,该夹角接近于45度,当折返气流量接近于穿过直通孔42的气流量。
46.如图1和图2所示,排气机构3包括导流段31、排气口(未示出)和导流板32,导流段31自内侧壁11向第二侧壁7方向延伸,对气流进行引导,排气口设于导流段31的前部,导流板32设于排气口内,导流板32与折流板4相对设置。本技术通过设置吸气机构2、调温区间120、排气机构3和折流板4相配合的短距导流构造,使得气流具有一定的引导流向性,但是不能过度约束气流方向,造成内侧壁11附近的高温气流稀薄,影响内侧壁11附近温度。然而气流在经历多次的热量交换后,会形成气流流向单一的温差气流层,进行热幅射区域内的较高温与较低温气流温差相差大的技术问题。因而导流构造还需要解决同温气流层的问题。为打破气流分层现象,使得进行热幅射的气体的温度更均匀,温差更小,通过设置导流板32进行上下层之间的气流层转换调节实现上述目的。直通孔42为横向设置且两端圆滑过
渡中部呈方形孔状;使得气流的流通及折返不会形成涡流。
47.如图1所示,作为优选,导流板32引导气流与内侧壁11呈非垂直夹角地向第二侧壁方向排出。较佳地,该夹角还可以是30
‑
150度且不包括90度,夹角的大小一定程度上影响穿过直通孔42的气流量;较佳地,该夹角接近于75度或105度。直通孔42呈扁平开口的阵列设置,该开口也可以是接近于菱形、椭圆形等构造,不在此枚举,然而通过改变直通孔42形状,应视为本技术的精神之所在。
48.如图1、图2所示,排气机构3至少包括有两个,其中两个排气机构3分设于第一侧壁1两侧,折流板4相应于排气机构3至少设置有两个,任一折流板4相应于排气机构3设置。本技术提出的排气机构3呈多个设置,多个排气机构3与折流板4相匹配,进一步保障幅射气流的温度均匀。作为优选,成对设置的折流和排气机构3形成的气流循环系统;该气流循环系统可以是三组,此时在接近于第二侧壁7方向的任意三个连接壁13上分别设置折流板4;气流循环系统还可以是四组,四组气流循环系统,此时在接近于第二侧壁7方向的四个连接壁13上均分别设置折流板4;而设置多组气流循环系统将影响第二侧壁7一侧的温度,同等条件下,第二侧壁7一侧在四组气流循环系统时比二组气流循环系统的温度高,此时可通过调节直通孔大小进行有限次数的实验或计算得到合理的折流区41与直通孔42大小比例。
49.如图3、图4所示,吸气机构2还包括有叶轮22,吸气口21呈开设于内侧壁11上的环形开口,环形开口与外侧壁12形成吸气腔(未示出),叶轮22设于吸气腔内。通过使用叶轮22,使气流的推动方向性更好,气流流向更统一。
50.如图1或图5所示,箱体100还包括设于其内部中间的载物台5,载物台5无侧壁;自排气机构3流出的气流在排气机构3与折流板4之间形成绕向气流,绕向气流、折返气流和正向气流向载物台5方向汇聚。载物台5与制热区110内形成无阻碍的气流直接对流,对试样热幅射的效果更佳。
51.作为优选,气流循环系统同样可适用于制冷区6。
52.本技术提出的制热区温度加速复归的冷热冲击箱通过气流循环系统保证制热区110内的热能均匀程度保持在较高的程度下。
53.如图1、图4所示,冷热冲击箱包括将箱体100分隔为制热区110和制冷区6的隔热支撑板9和载物台5;载物台5包括顺次设置的第一密封部52、主体51和第二密封部53;隔热支撑板9设有可供主体51于制热区110和制冷区6之间往复运动的转换区间(未示出),第一密封部52和第二密封部53分设于隔热支撑板9两侧;当主体51位于制热区110时,第二密封部53与隔热支撑板9气密性连接,当主体51位于制冷区6时,第一密封部52与隔热支撑板9气密性连接。本技术提供的制热区温度加速复归的冷热冲击箱,该冷热冲击箱通过载物台5于制热区110和制冷区6之间来回地进行往复运动,以检测试样的抗冷热冲击性能。作为优选,气流循环系统适用于制冷区6均衡温度效果同样出色。
54.第一密封部52、隔热支撑板9和第二密封部53可通过软体实现气密性隔绝,具体可以是硅胶等耐高温或耐低温的气密性压接。其中,测试箱顶壁安装有链条,箱体外侧安装有驱动组件,驱动组件驱动链条从而带动测试箱上下滑动。箱体通过导轨进行辅正和引导,升降时平稳度高。
55.较佳地,箱体100还设有箱门8,第一侧壁1相对于箱门8设置,折流板4设于与箱门8相接的连接壁13上。本技术通过设置箱门8,方便放取被测试样,同时内侧壁11设于与箱门8
相对的位置更方便检测。其中,箱门8可与第二侧壁7设为一体 ;进一步地,箱门与连接壁13设为一体。
56.制冷区6还包括有蓄冷装置61和蓄冷装置加热丝62,蓄冷装置加热丝62相应于蓄冷装置61设置。
57.制冷区6设有保温层,制热区110设有保温层,冷热冲击箱设有保温层。通过设置保温层,减少造成能量流失,提高冷热冲击测试的质量。
58.本实施例的实施原理为:本实施例提供的一种制热区温度加速复归的冷热冲击箱,将气流循环系统设置于制热区,加速制热区温度的复归,对制热区110区间内的热度进行快速调节和控制,引导气体流向,调节气流的滞留时序,充分进行携热并进行热幅射,提高热交换效率。吸气机构2抽吸制热区110除容纳腔10以外的气体,并对容纳腔10内的气体增压从排气机构3推出,在紧挨排气机构3位置处通过加热丝对气流进行加热,使气流携带大量热能从排气机构3流出后进行热交换。