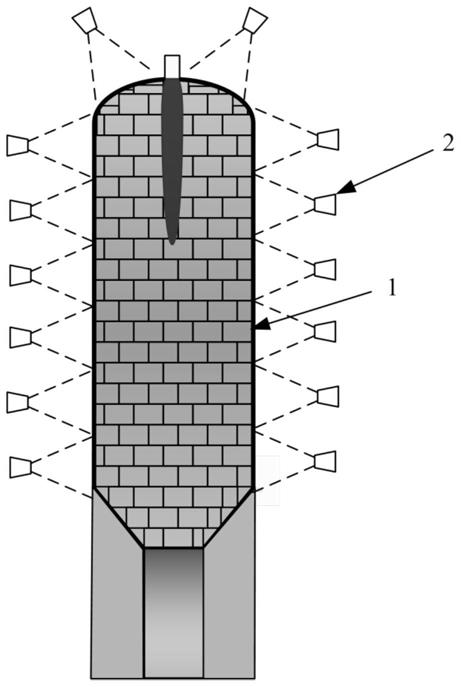
1.本发明涉及一种耐火砖层的厚度、温度的监测装置和监测方法。
背景技术:2.煤气化技术是当今煤炭等含碳物质清洁高效利用的关键技术之一,是将一次能源转化为洁净二次能源和化学产品的主要途径,该技术主要运用于合成氨、合成甲醇、炼厂制氢、高炉还原炼铁化工冶金行业和联合循环发电装置中。煤气化技术发展经历了固定床气化技术(lurgi技术、赛鼎气化技术为代表)、流化床气化技术(htw、ugas技术为代表)和气流床气化技术(以texaco、shell、多喷嘴、ht
‑
l、se技术为代表)。随着大规模能源安全、清洁、高效转化的技术需求,具有气化温度与压力高、负荷大,煤种适应范围广的气流床煤气化技术成为了煤气化技术发展和工业应用的主要方向。
3.在气流床煤气化技术中,高效、可靠的气化炉是整个技术的关键与核心装备。气流床气化炉为条件苛刻的高温高压(4.0~6.5mpa,~1300℃)多相复杂反应器,现有检测手段无法准确、长周期对其进行监控,使得其长时间处于“黑箱”运行状态。按气化炉隔热衬里结构可以分为耐火砖衬里气化炉(如:多喷嘴气化炉、ge气化炉、一代清华炉、多元料浆气化炉)和水冷壁衬里气化炉(如:航天炉、壳牌炉、二代清华炉、gsp炉)等,以水煤浆为原料的煤气化技术一般采用耐火砖衬里气化炉,以粉煤为原料的气化技术一般采用水冷壁衬里气化炉。水煤浆耐火砖衬里气化技术因工艺流程短、气化炉结构简单、热损失小、化学能转化率高等优点,在煤化工领域广泛应用,其在我国现代煤气化技术中的份额约占65%。耐火砖层的厚度是气化炉结构的关键参数之一,在气化炉运行过程中,耐火砖在高温熔渣的侵蚀作用下逐渐蚀损减薄,当耐火砖层厚度小于一定的临界值时,其隔热效果大幅降低,气化炉金属壳体出现超温,进而直接影响气化炉金属壳体的安全。因此工程上急需开发一种能够在线监控气化炉耐火砖层的温度、厚度的系统与方法。
技术实现要素:4.本发明要解决的技术问题是为了克服现有技术中无法直接测量高温高压的气化炉内耐火砖层的温度和厚度的缺陷,而提供了一种耐火砖层的厚度、温度的监测装置和监测方法。本发明提供的监测装置和方法通过对气化炉中内壁面的熔渣流动与传热过程分析,能够准确监测耐火砖层的厚度,为工业操作带来一定的指导。
5.本发明是通过下述技术方案来解决上述技术问题:
6.一种耐火砖层的厚度的监测装置,其包括与待监测炉体相连的测量部件,所述监测装置还包括计算模块i、计算模块ii和计算模块iii;
7.所述测量部件用于测量所述的计算模块i、所述计算模块ii和所述计算模块iii在运行计算时需要的参数;
8.所述待监测炉体为气化炉,由内至外依次包括液态熔渣层、耐火砖层和金属壁,所述耐火砖层由内至外依次包括向火面砖层、背衬砖层和隔热砖层;
9.所述计算模块i用于通过所述液态熔渣层流动传热过程的质量守恒方程计算得到所述液态熔渣层的厚度;
10.所述计算模块ii用于计算穿过所述金属壁的热流密度;
11.所述计算模块iii用于将穿过所述金属壁的热流密度和所述熔渣层的厚度,均代入基于能量守恒建立的“穿过所述向火面砖层、穿过所述背衬砖层和穿过所述隔热砖层”的热流密度的方程中,分别得到所述向火面砖层、所述背衬砖层和所述隔热砖层的厚度,所述向火面砖层的厚度、所述背衬砖层的厚度和所述隔热砖层的厚度总和即为所述耐火砖层的厚度;
12.所述计算模块i与所述计算模块iii电连接,用于将计算得到的所述液态熔渣层的厚度传输至所述计算模块iii;所述计算模块ii与所述计算模块iii电连接,用于将计算得到的穿过所述金属壁的热流密度传输至所述计算模块iii。
13.本发明通过气化炉中液态熔渣层的熔渣流动与传热过程分析,基于大气对流换热、环境温度、金属壁的外壁面的温度和气化炉的炉膛内的温度来预测气化炉内耐火砖层的厚度以及各层的厚度。所述气化炉的炉膛内的高温气体通过辐射传热和对流传热将热量传给所述气化炉的内壁面,同时熔渣沉积在所述气化炉的内壁面形成液态的熔渣层。所述气化炉的内壁面吸收传入热量和熔渣沉积代入的热量后,基于热传导,将热量依次传递至耐火砖层和金属壁,最后传给大气。大气的温升量与热传导量、熔渣沉积量、液态熔渣层的厚度有关。因此,通过测量大气的温升,建立所述气化炉的内壁面上熔渣沉积流动、热量传递模型,推算出来所述耐火砖层的厚度。本发明中,所述液态熔渣层的熔渣需为液态配合本发明中的上述3个不同的计算模块,才能够实现实时准确的测量耐火砖层的厚度。
14.本发明中,本领域技术人员知晓,所述的测量部件根据所述计算模块i、所述计算模块ii和所述计算模块iii中在计算过程中所需的参数合理的设置即可。
15.例如,所述计算模块i中在计算所述液态熔渣层的厚度的过程中,需要知晓沉积在所述气化炉的内壁面的熔渣量,则相应的需要测量熔渣量的流量计。本领域技术人员知悉,一般通过煤浆流量计或煤粉流量计,获得进入所述气化炉中的干基煤量,再结合灰分测量计测量得到的煤中的灰分含量,计算得到熔渣量。
16.例如,所述计算模块ii在计算所述金属壁的外壁面传热的热流密度时,需要知晓金属壁的外壁面的温度和环境温度,则需要测温部件1用于测量所述金属壁的外壁面的温度,以及测温部件2用于测量靠近所述金属壁的外壁面的环境温度。所述的测温部件1或所述测温部件2可为热电偶,所述的热电偶例如为红外测温仪。所述测温部件2的个数例如为3个。
17.例如,所述计算模块iii在计算所述耐火砖层的厚度时,需要知晓所述气化炉的炉膛内靠近内壁面的气体温度,则需要在所述炉膛内设置若干个测温部件3以测量所述炉膛内的温度。所述炉膛内的测温部件例如为2~6个以测量炉膛内从上至下的温度,所述测温部件可为热电偶。
18.本发明中,所述计算模块i的计算方式较佳地如下所示:
19.假设加入所述气化炉的煤经气化反应后产生的70wt.%沉积在所述向火面砖层的内壁面形成所述的液态熔渣层,且分布均匀,所述液态熔渣层中熔渣流动满足牛顿流体流动,对所述液态熔渣层流动传热过程建立的质量守恒的计算公式如方程
①
所示:
[0020][0021]
方程
①
中,δ
s,i
是指所述液态熔渣层的厚度,单位为m;ρ
s
为所述液态熔渣层中熔渣的密度;m
in,j
为沉积在所述气化炉的内壁面的熔渣量,单位为kg,其值为m
in,j
=入炉煤量
×
灰分含量
×
70%;l
i
为所述气化炉中筒体直段的当量周长,单位为m;x为质点在所述液态熔渣层中的位移;i为该点位置的坐标标识,j为从所述气化炉的顶部到i点处的坐标范围,物理意义为第i点的熔渣量为顶部到i点处所有沉积颗粒的和;
[0022]
v
i
(x)为所述熔渣层内的速度分布函数,通过动量方程
②
求出:
[0023]
方程
②
的边界条件为
[0024]
方程
②
中,η
s
为所述液态熔渣层的动力粘度,v为熔渣流动的速率、g为重力加速度、β为熔渣在气化炉内壁面上流动的倾斜角、ρ
s
是指熔渣层中熔渣的密度、τ为所述气化炉的内壁面的剪切力。
[0025]
其中,本领域技术人员知晓,所述气化炉本体包括拱顶和与所述拱顶相匹配连接的筒体直段。
[0026]
其中,所述气化炉中筒体直段的当量周长的计算可为本领域常规,一般利用公式l=π(d
‑
δ
s
‑
x)计算得到,其中d为所述气化炉的内径,由于(δ
s
‑
x)相对于d而言很小,数量级仅为其10
‑3,因此l的计算公式可以简化为l=πd来处理。
[0027]
其中,ρ
s
是指的取值可为本领域常规,例如2500kg/m3。
[0028]
其中,τ与气化炉结构和操作状态有关,一般可以近似为τ=0.0303ρ
g
u
02
。ρ
g
是指所述气化炉内合成气的密度、u
02
是指所述液态熔渣层的表面流速。本领域技术人员知晓,所述ρ
g
根据气化炉类型、温度、压力计算得到。
[0029]
其中,η
s
是熔渣的基础物性数据,需要通过分析测试得出,其数值与所述熔渣层内的温度分布有关,可以通过熔渣的粘温特性曲线和所述熔渣层内的温度分布求出。
[0030]
本发明中,所述计算模块ii中,计算所述金属壁的外壁面传热的热流密度的计算公式较佳地如下所示:
[0031]
q
out,i
=2πδzr0(t
m,i
‑
t
air
)h
air,i
ꢀꢀꢀꢀ③
[0032]
t
m,i
为所述金属壁的外壁面的温度、t
air
为环境温度、h
air,i
为所述金属壁的外壁面与大气的对流传热系数、
△
z为向火面砖层的高度,r0为所述气化炉的半径,所述气化炉的半径是指所述金属壁的外壁面至所述气化炉中心轴线的距离;所述向火面砖层的高度一般为假设所述向火面砖层中的砖上下没有错位时的高度。
[0033]
方程
③
中,h
air
根据如式
④
计算:
[0034][0035]
方程
④
中,h
conv
为自然对流常数、c为金属壁的常数。
[0036]
其中,t
m,i
一般通过在所述气化炉的金属壁的外壁面设置的热电偶测得。所述热电偶一般采用红外测温仪,也可以是表面热电偶,较佳地为红外测温仪。
[0037]
其中,t
air
一般通过在所述金属壁的外壁面设置的若干个环境温度热电偶,在计算热通量时,根据自然对流换热计算得到。所述环境温度热电偶的个数例如为3个,以取得平均值。
[0038]
其中,h
conv
可根据现场实际情况取值和修正得到,一般通过下述方程式
④‑
1计算得到:
[0039]
方程
④‑
1中,l为所述气化炉中筒体直段的高度。所述h
conv
较佳地为2.55w/m2·
k。
[0040]
其中,方程
④
,所述c较佳地为4.06w/m2·
k4。
[0041]
本发明中,所述计算模块iii中,计算公式较佳地如下所示:
[0042][0043]
方程
⑤
中,q
ref,i
=q
out,i
,t
g,i
为所述气化炉的炉膛内靠近内壁面的气体温度,通过所述气化炉内的热电偶测得;t
m,i
为金属壁的外壁面的温度;所述t
g,i
的数值同所述液态熔渣层与气体交界面温度的数值相同。
[0044]
r3=r2‑
δ
r,1
,r4=r3‑
δ
r,2
,r5=r4‑
δ
r,3
,r6=r5‑
δ
s,i
;r5为所述向火面砖层的内径、r6为所述液态熔渣层的内径、r4为所述背衬砖层的内径、r3为所述隔热砖层的内径;
[0045]
k
r,1
,k
r,2
,k
r,3
,k
s,i
分别为所述隔热砖层的导热系数、所述背衬砖层的导热系数、所述向火面砖层的导热系数和所述液态熔渣层的导热系数,由物性参数查询得到;
[0046]
δ
r,1
,δ
r,2
,δ
r,3
和δ
s,i
分别为所述隔热砖层的厚度、所述背衬砖层的厚度、所述向火面砖层的厚度和所述熔渣层的厚度;其中,所述隔热砖层、所述背衬砖层的厚度均为恒定值。
[0047]
本发明中,所述耐火砖层的厚度的监测装置较佳地还包括计算终端,以实现实时在线计算得到所述耐火砖层的厚度,用于所述计算模块i、所述计算模块ii和所述计算模块iii的计算。
[0048]
其中,计算终端例如为电脑或可编程控制器。
[0049]
本发明中,所述金属壁和所述隔热砖层之间较佳地还包括耐火棉层,以实现更准确的测量。
[0050]
当还包括所述耐火棉层时,本发明的监测装置还可计算所述耐火棉层和所述金属壁的厚度,将如下式代入所述方程
⑤
中即可:
[0051]
r0=r
m
,r1=r0‑
δ
m
,r2=r1‑
δ
r,c
,其中,r2为所述耐火棉层的内径、r1为所述金属壁的内径、r0为所述气化炉的半径;
[0052]
k
m
,k
r,c
分别为所述金属壁的导热系数、所述耐火棉层的导热系数,由物性参数查询得到,其中,k
r,1
=k
r,c
,k
r,0
=k
m
;
[0053]
δ
m
,δ
r,c
分别为所述金属壁的厚度、所述耐火棉层的厚度。所述金属壁、所述耐火棉层的厚度为恒定值。
[0054]
本发明还提供了一种耐火砖层的温度的监测装置,其包括所述的耐火砖层的厚度的监测装置和计算模块iv,所述计算模块iv用于建立如下所述的能量守恒方程:
[0055]
q
out,i
×
a
m
=q
ref1
×
a
r1
=q
ref2
×
a
r2
=q
ref3
×
a
r3
=q
refs
×
a
s
ꢀ⑥
[0056]
方程
⑥
中,q
out,i
、q
ref1
、q
ref2
、q
ref3
、q
refs
分别是指穿过所述金属壁、所述隔热砖层、所述背衬砖层、所述向火面砖和所述液态熔渣层的热流密度;a
m
、a
r1
、a
r2
、a
r3
、a
s
分别是指所述金属壁的径向传热面积、所述隔热砖层的径向传热面积、所述背衬砖层的径向传热面积、所述向火面砖层的径向传热面积和所述液态熔渣层的径向传热面积;
[0057]
所述计算模块iii与所述计算模块iv电连接,用于将所述计算模块iii中的所述耐火砖层的厚度传输至所述的计算模块iv。
[0058]
本发明中,所述耐火砖层的温度的监测装置较佳地还包括计算终端,以实现实时在线计算得到所述耐火砖层的温度,用于所述计算模块iv的计算。
[0059]
其中,计算终端例如为电脑或可编程控制器。
[0060]
本发明中,当所述金属壁和所述隔热砖层之间包括耐火棉层时,所述耐火棉层的温度通过q
out,i
×
a
m
=q
refc
×
a
rc
方程式计算得到,q
refc
是指穿过所述耐火棉层的热流密度,a
rc
是指耐火棉层的径向传热面积。
[0061]
本发明还提供了一种耐火砖层的厚度的监测方法,其包括如下步骤:气化炉的传热过程由内至外依次在熔渣层、耐火砖层、金属壁和大气之间进行;
[0062]
所述耐火砖包括由内至外的向火面砖、背衬砖和隔热砖;
[0063]
耐火砖层的厚度计算步骤如下:
[0064]
步骤(1),假设加入所述气化炉的煤经气化反应后产生的70wt.%沉积在所述向火面砖层的内壁面形成所述的熔渣层,且分布均匀,所述熔渣层中的熔渣流动满足牛顿流体流动,对所述熔渣层流动传热过程建立的质量守恒方程
①
,得出所述熔渣层的厚度:
[0065][0066]
方程
①
中,δ
s,i
是指所述液态熔渣层的厚度,单位为m;ρ
s
为所述液态熔渣层中熔渣的密度;m
in,j
为沉积在所述气化炉的内壁面的熔渣量,单位为kg,其值为m
in,j
=入炉煤量
×
灰分含量
×
70%;l
i
为所述气化炉中筒体直段的当量周长,单位为m;x为质点在所述液态熔渣层中的位移;i为该点位置的坐标标识,j为从所述气化炉的顶部到i点处的坐标范围,物理意义为第i点的熔渣量为顶部到i点处所有沉积颗粒的和;
[0067]
v
i
(x)为所述熔渣层内的速度分布函数,通过动量方程
②
求出:
[0068]
方程
②
的边界条件为
[0069]
方程
②
中,η
s
为所述液态熔渣层的动力粘度,v为熔渣流动的速率、g为重力加速度、β为熔渣在气化炉的内壁面上流动的倾斜角、ρ
s
是指液态熔渣层中熔渣的密度、τ为所述气化炉的内壁面的剪切力;
[0070]
步骤(2),计算穿过所述金属壁的热流密度:
[0071]
q
out,i
=2πδzr0(t
m,i
‑
t
air
)h
air,i
ꢀꢀꢀꢀꢀꢀꢀꢀꢀ③
[0072]
t
m,i
为所述金属壁的外壁面的温度、t
air
为环境温度、h
air,i
为所述金属壁的外壁面与大气的对流传热系数、
△
z为向火面砖层的高度;所述向火面砖层的高度一般为假设所述向火面砖层中的砖上下没有错位时的高度。
[0073]
方程
③
中,h
air
根据如式
④
计算:
[0074][0075]
方程
④
中,t
m,i
为所述金属壁的外壁面的温度、t
air
为环境温度、h
air,i
为所述金属壁的外壁面与大气的对流传热系数、h
conv
为自然对流常数、c为金属壁的常数;
[0076]
步骤(3),将步骤(2)中计算得到的q
ref,i
代入方程
⑤
中,且q
ref,i
=q
out,i
,计算出r
j
:
[0077][0078]
其中,t
g,i
为所述气化炉的炉膛内靠近内壁面的气体温度,通过所述气化炉内的热电偶测得;t
m,i
为金属壁的外壁面的温度;所述t
g,i
的数值同所述熔渣层与气体交界面温度的数值相同;
[0079]
根据方程
⑤
计算得到的r
j
代入下述式中,计算得到各层的厚度:
[0080]
r2=r1‑
δ
r,c
,r3=r2‑
δ
r,1
,r4=r3‑
δ
r,2
,r5=r4‑
δ
r,3
,r6=r5‑
δ
s,i
;r5为所述向火面砖层的内径、r6为所述液态熔渣层的内径、r4为所述背衬砖层的内径、r3为所述隔热砖层的内径;
[0081]
k
r,1
,k
r,2
,k
r,3
,k
s,i
分别为所述隔热砖层的导热系数、所述背衬砖层的导热系数、所述向火面砖层的导热系数和所述熔渣层的导热系数,由物性参数查询得到;
[0082]
δ
r,1
,δ
r,2
,δ
r,3
和δ
s,i
分别为所述隔热砖层的厚度、所述背衬砖层的厚度、所述向火面砖层的厚度和所述液态熔渣层的厚度;其中,所述隔热砖层、所述背衬砖层的厚度均为恒定值;
[0083]
联解方程
①
~
⑤
,即可求出δ
r,1
、δ
r,2
和δ
r,3
,求和即可所述耐火砖层的厚度。
[0084]
本发明中,所述液态熔渣层中熔渣的温度较佳地在1300℃以上。
[0085]
本发明中,所述气化炉中筒体直段的当量周长的计算可为本领域常规,一般利用公式l=π(d
‑
δ
s
‑
x)计算得到,其中d为所述气化炉的内径,由于(δ
s
‑
x)相对于d而言很小,数量级仅为其10
‑3,因此l的计算公式可以简化为l=πd来处理。
[0086]
本发明中,所述向火面砖层内径一般是指所述气化炉的轴心到所述向火面砖的最外层的距离。r4为所述背衬砖层的内径、r3为所述隔热砖层的内径、r2为所述耐火棉层的内径、r1为所述金属壁的内径的含义同所述向火面砖层内径的含义。
[0087]
本发明中,方程
①
和
②
中,ρ
s
的取值可为本领域常规,例如2500kg/m3。
[0088]
本发明中,τ与气化炉结构和操作状态有关,一般可以近似为τ=0.0303ρ
g
u
02
;ρ
g
是指所述气化炉内合成气的密度、u
02
是指所述液态熔渣层的表面流速。本领域技术人员知晓,所述ρ
g
根据气化炉类型、温度、压力计算得到。
[0089]
本发明中,方程
②
中,η
s
是熔渣的基础物性数据,需要通过分析测试得出,其数值与所述熔渣层内的温度分布有关,可以通过熔渣的粘温特性曲线和所述熔渣层内的温度分布求出。
[0090]
本发明中,方程
③
和方程
④
中,t
m,i
一般通过在所述气化炉的金属壁的外壁面设置的热电偶测得。所述热电偶一般采用红外测温仪,也可以是表面热电偶,较佳地为红外测温仪。
[0091]
本发明中,方程
③
和方程
④
中,t
air
一般通过在所述金属壁的外壁面设置的若干个环境温度热电偶,在计算热通量时,根据自然对流换热计算得到。所述环境温度热电偶的个
数例如为3个,以取得平均值。
[0092]
本发明中,本领域技术人员知晓,方程
④
中的h
conv
可根据现场实际情况取值和修正得到,一般通过下述方程式
④‑
1计算得到:
[0093][0094]
方程
④‑
1中,l为气化炉中筒体直段的高度。
[0095]
其中,所述h
conv
较佳地为2.55w/m2·
k。
[0096]
本发明中,方程
④
,所述c较佳地为4.06w/m2·
k4。
[0097]
本发明中,当所述金属壁和所述隔热砖层之间还包括耐火棉层时,所述的监测方法还可计算出所述耐火棉层的厚度,将如下式代入所述方程
⑤
中即可:
[0098]
r0=r
m
,r1=r0‑
δ
m
,r2=r1‑
δ
r,c
,其中,r2为所述耐火棉层的内径、r1为所述金属壁的内径、r0为所述气化炉的半径,所述气化炉的半径是指所述金属壁的外壁面至所述气化炉中心轴线的距离;
[0099]
k
m
,k
r,c
分别为所述金属壁的导热系数、所述耐火棉层的导热系数,由物性参数查询得到,其中,k
r,1
=k
r,c
,k
r,0
=k
m
;
[0100]
δ
m
,δ
r,c
分别为所述金属壁的厚度、所述耐火棉层的厚度。所述金属壁、所述耐火棉层的厚度为恒定值。
[0101]
本发明还提供了一种耐火砖层的温度的监测方法,根据上述耐火砖层的厚度在线监测方法得到的耐火砖层的厚度值,建立能量守恒方程
⑥
:
[0102]
q
out,i
×
a
m
=q
ref1
×
a
r1
=q
ref2
×
a
r2
=q
ref3
×
a
r3
=q
refs
×
a
s
ꢀꢀꢀ⑥
[0103]
q
out,i
、q
ref1
、q
ref2
、q
ref3
、q
refs
分别是指穿过所述金属壁的热流密度、所述隔热砖层的热流密度、所述背衬砖层的热流密度、所述向火面砖的热流密度和所述熔渣层的热流密度;a
m
、a
r1
、a
r2
、a
r3
、a
s
分别是指所述金属壁的径向传热面积、所述隔热砖层的径向传热面积、所述背衬砖层的径向传热面积、所述向火面砖层的径向传热面积和所述熔渣层的径向传热面积;即可得到耐火砖层的温度。
[0104]
本发明中,当所述金属壁和所述隔热砖层之间包括耐火棉层时,所述耐火棉层的温度可通过q
out,i
×
a
m
=q
refc
×
a
rc
方程式计算得到,qr
efc
是指穿过所述耐火棉层的热流密度,a
rc
是指耐火棉层的径向传热面积。
[0105]
在符合本领域常识的基础上,上述各优选条件,可任意组合,即得本发明各较佳实例。
[0106]
本发明的积极进步效果在于:本发明提供的方法基于传热原理对耐火砖层的温度和厚度进行监测;具体地,通过对气化炉的内壁面的熔渣流动与传热过程分析,基于大气对流换热来预测气化炉内耐火砖层的厚度和各层砖的温度方法,为气化操作提供指导。
附图说明
[0107]
图1为实施例1中气化炉的结构示意图。
[0108]
图2为实施例1中气化炉中熔渣流动与传热原理图。
[0109]
图3为实施例1中耐火砖层监测装置的结构示意图。
[0110]
图4为实施例1中的计算原理流程图。
[0111]
图5为实施例1中实时测量得到的金属壁的外壁面的温度分布。
[0112]
图6为实施例1中实时测量得到的气化炉的炉膛内靠近内壁面的气体温度分布。
[0113]
图7为实施例中实时测量得到的向火面砖层的厚度。
[0114]
附图标记:
[0115]
图1,1
‑
金属壁的外壁面;2
‑
红外测温仪;
[0116]
图2,11
‑
液态熔渣层;12
‑
向火面砖层;13
‑
背衬砖层;14
‑
隔热砖层;15
‑
耐火棉层;16
‑
金属壁;且设定炉身的径向方向为x,炉身的轴线方向为z。
具体实施方式
[0117]
下面通过实施例的方式进一步说明本发明,但并不因此将本发明限制在所述的实施例范围之中。下列实施例中未注明具体条件的实验方法,按照常规方法和条件,或按照商品说明书选择。
[0118]
实施例1
[0119]
本实施例中气化炉的结构示意图如图1所示,图1中1为金属壁的外壁面,2为红外测温仪。本实施例中含义耐火砖衬里的气化炉的操作压力为6.5mpa,温度为1300℃,气化炉的半径(外径)为1.7m,气化炉耐火砖封头高度为1.7m,筒体直段的高度为8.3m(即为图5、图6和图7横坐标中的气化炉高度)。额定的煤浆流量为27.4kg/s,煤浆浓度为60%,煤的灰分含量在6.8%
‑
12%波动。计算过程中,需要用于查找耐火砖层的物理性质数据、空气物性数据,如下表1所示。
[0120]
表1
[0121]
参数值参数值
‑‑
r
0 r
m mm3200η
s
(t)pa
·
sη(t)=1.41
×
108e
‑
0.011t
δ
m
mm,k
m
w/m
·
k100,17ρ
s
kg/m32500δ
c
mm,k
c
w/m
·
k19,0.9c j/kg
·
k1670δ
r,1
mm,k
r,1
w/m
·
k230,4.0k
s
(t)w/m
·
kk
s
(t)=0.176e
0.0014t
δ
r,2
mm,k
r,2
w/m
·
k200,4.1
‑‑
δ
r,3
mm,k
r,3
w/m
·
k80,0.9
[0122]
如图2所示为实施例1中气化炉中熔渣流动与传热原理图。图2中11为熔渣层;12为向火面砖层;13为背衬砖层;14为隔热砖层;15为耐火棉层;16为金属壁;且设定炉身的径向方向为x,炉身的轴线方向为z;竖直方向的实心箭头代表的是熔渣的流动方向。从图2中可以看出,整个传热过程是在液态熔渣层11、向火面砖层12、背衬砖层13、隔热砖层14、耐火棉层15、金属壁16和大气之间进行的,传热的热阻包括熔渣层、耐火砖层、耐火棉层、金属壁、大气对流换热。炉膛内的高温气体通过辐射传热和对流传热将热量传给壁面,同时熔渣沉积在壁面形成液态的液态熔渣层。壁面吸收传入热量和熔渣沉积带入的热量后,基于热传导,将热量依次传递至耐火砖层、耐火棉层和金属壁,最后传给大气。大气的温升量与热传导量、熔渣沉积量、熔渣厚度等参数有关。因此通过测量大气的温升,建立壁面熔渣沉积流动、热量传递模型,可以推算出耐火砖层的厚度δ
r,3
。
[0123]
本实施例中的耐火砖层的厚度的监测装置包括气化炉和监测模块,如图3所示为
监测模块的结构示意图,其包括计算模块i、计算模块ii和计算模块iii;计算模块i用于通过所述液态熔渣层流动传热过程的质量守恒方程计算得到所述熔渣层的厚度;计算模块ii用于计算穿过金属壁的热流密度;计算模块iii用于通过穿过金属壁的热流密度分别与“穿过向火面砖层、穿过背衬砖层和穿过隔热砖层”热流密度建立的能量守恒计算得到向火面砖层的厚度、背衬砖层的厚度和隔热砖层的厚度,即得耐火砖层的厚度;计算模块i与计算模块iii电连接,用于将计算得到的熔渣层的厚度传输至计算模块iii;计算模块ii与计算模块iii电连接,用于将计算得到的穿过金属壁的热流密度传输至计算模块iii。
[0124]
本实施例还提供了耐火砖层的温度的监测装置通过建立气化炉各层结构之间的能量守恒方程求解得到各层的温度,其包括耐火砖层的厚度的监测装置和计算模块iv,计算模块iii与计算模块iv电连接,用于将计算模块iii中的所述耐火砖层的厚度传输至计算模块iv。
[0125]
(1)计算模块i的计算公式如下:
[0126]
假设加入气化炉内的煤经气化反应后产生的熔渣70wt.%均沉积在向火面砖层的内壁面形成液态熔渣层,且分布均匀,且熔渣流动过程满足牛顿流体流动,则对液态熔渣层中熔渣流动传热过程建立质量守恒方程
①
:
[0127][0128]
方程(1)中,δ
s,i
是指液态熔渣层的厚度,单位为m,为本实施例要求解的第一个变量;ρ
s
为液态熔渣层中熔渣的密度;m
in,j
为沉积在气化炉壁面的熔渣量,单位为kg,其值为m
in,j
=入炉煤量
×
灰分含量
×
70%,具体地,通过煤浆或煤粉流量计,获得进入气化炉的干基煤量,结合煤中的灰分含量,计算得到炉内熔渣含量;l
i
为气化炉中筒体直段的当量周长,单位为m,利用公式l=π(d
‑
δ
s
‑
x)计算得到,其中d为气化炉的内径,由于(δ
s
‑
x)相对于d而言很小,数量级仅为其10
‑3,因此l
i
的计算公式可以简化为l
i
=πd来处理;v
i
(x)为熔渣层内的速度分布函数,可以通过动量方程
②
求出:
[0129]
熔渣流动速度方程为:
[0130]
方程
②
的边界条件为
[0131]
方程
②
中,η
s
为液态熔渣层的动力粘度,v为熔渣流动的速率、g为重力加速度、β为熔渣在气化炉内壁面上流动的倾斜角、ρ
s
是指液态熔渣层中熔渣的密度、τ为气化炉的内壁面的剪切力;η
s
为液态熔渣层内的粘度分布,是熔渣的基础物性数据,需要通过分析测试得出,其数值与液态熔渣层内的温度分布有关,可以通过熔渣的粘温特性曲线和液态熔渣层内的温度分布求出。τ=0.0303ρ
g
u
02
;ρ
g
是指所述气化炉内合成气的密度根据气化炉类型、温度、压力计算得到,u
02
是指液态熔渣层的表面流速。
[0132]
(2)计算模块ii的计算公式如下:
[0133]
q
out,i
=2πδzr0(t
m,i
‑
t
air
)h
air,i
ꢀꢀꢀꢀꢀꢀꢀꢀꢀꢀꢀꢀꢀꢀꢀꢀꢀꢀꢀꢀꢀꢀꢀꢀꢀ③
[0134]
方程
③
中,h
air
为金属壁的外壁面与大气的对流传热系数;可根据方程
④
进行计算:
[0135][0136]
其中,t
m,i
为金属壁的外壁面的温度,通过在金属壁的外壁面设置壁面温度测量热电偶测得,热电偶为红外线测温仪,如图5所示为实时测量得到的金属壁的外壁面的温度分布,即图5纵坐标标注的测量的气化炉壁面温度。图5(图6或图7)中的不同曲线代表的是气化炉耐火砖层累积使用的时间,时间计算的起点为耐火砖层的新砌砖开始。t
air
为环境温度,通过在金属壁外大气空间设置3个环境温度热电偶测得;h
conv
为2.55w/m2·
k,c为模型常数,数值为4.06w/m2·
k4。
[0137]
(3)计算模块iii的计算公式如下:
[0138][0139]
其中,t
g,i
为所述气化炉的炉膛内靠近内壁面的气体温度,通过所述气化炉内的热电偶测得,如图6所示为实时测量得到的气化炉的炉膛内靠近内壁面的气体温度分布,即图6中纵坐标标注的预测得到的气化炉内近壁面温度;
[0140]
r0=r
m
,r1=r0‑
δ
m
,r2=r1‑
δ
r,c
,r3=r2‑
δ
r,1
,r4=r3‑
δ
r,2
,r5=r4‑
δ
r,3
,r6=r5‑
δ
s,i
;
[0141]
r5为向火面砖层的内径、r6为液态熔渣层的内径、r4为背衬砖层的内径、r3为隔热砖层的内径、r2为耐火棉层的内径、r1为金属壁的内径、r0为气化炉的半径,气化炉的半径是指金属壁的外壁面至气化炉中心轴线的距离;
[0142]
k
m
,k
r,c
,k
r,1
,k
r,2
,k
r,3
,k
s,i
分别为金属壁的导热系数、耐火棉层的导热系数、隔热砖层的导热系数、背衬砖层、向火面砖层的导热系数和液态熔渣层的导热系数,由物性参数查询得到,其中,k
r,1
=k
r,c
,k
r,0
=k
m
;
[0143]
δ
m
,δ
r,c
,δ
r,1
,δ
r,2
,δ
r,3
,和δ
s,i
分别为金属壁的厚度、耐火棉层的厚度、隔热砖层的厚度、背衬砖层的厚度、向火面砖层的厚度和液态熔渣层的厚度,金属壁、耐火棉层、隔热砖层、背衬砖层的厚度是恒定值;
[0144]
联解方程
①
~
⑤
,即可根据金属壁的外壁面温度、环境温度、气化炉的炉膛内靠近内壁面的气体温度、煤中灰分含量及流量、气化炉结构参数与物性参数求出隔热砖层、背衬砖层和向火面砖层的厚度,求和即得耐火砖层的厚度。
[0145]
(4)通过能量守恒方程计算得到耐火砖层的温度。
[0146]
通过上面的分析可以看出,气化炉向大气的传热量(即气化炉的金属壁的外壁面热损失)与气化炉温度和液态熔渣层的厚度有关;液态熔渣层的厚度一方面与熔渣沉积量有关,另一方面与液态熔渣层内的温度分布有关。
[0147]
因此,将上述计算得到的耐火砖层的厚度代入下述方程中,即可计算出耐火砖层的温度:
[0148]
q
out,i
×
a
m
=q
refc
×
a
rc
=q
ref1
×
a
r1
=q
ref2
×
a
r2
=q
ref3
×
a
r3
=q
refs
×
a
s
ꢀꢀ⑥
[0149]
方程
⑥
中,q
out,i
、q
refc
、q
ref1
、q
ref2
、q
ref3
、q
refs
分别是指穿过金属壁、耐火棉层、隔热砖层、背衬砖层、向火面砖和液态熔渣层的热流密度;a
m
、a
rc
、a
r1
、a
r2
、a
r3
、a
s
分别是指金属壁、耐火棉层、隔热砖层、背衬砖层、向火面砖层和液态熔渣层的径向传热面积。
[0150]
如图4所示为本实施例的计算原理流程图。本实施例通过测量和计算得到的金属
壁的外壁面的温度、气化炉内炉膛的温度、熔渣流动的速率参数以及液态熔渣层的厚度,分别对熔渣流动、传热过程建立流动方程和热平衡两个方程,采用迭代法即可求解出耐火砖层的厚度。如图7所示为本实施例中实时测量得到的向火面砖层的厚度。由图可知,采用本实施例的方法能够实时且准确的测量得到的向火面砖层的厚度,进而实时得到耐火砖层的厚度。
[0151]
上述监测装置还包括测量部件和计算终端。测量部件包括用于测量熔渣量的流量计和灰分测量计,分别测得气化炉中的干基煤量和煤中的灰分含量。测量部件还包括若干个测温部件,用于测量金属壁的外壁面的温度t
m,i
、环境温度t
air
和气化炉的炉膛内靠近内壁面的气体温度t
g,i
。
[0152]
计算终端为电脑或可编程控制器,将通过仪器测量得到的煤浆或煤粉流、金属壁的外壁面面温度t
m,i
、环境温度t
air
、气化炉的炉膛内靠近内壁面的气体温度t
g,i
传输到计算终端;在终端上进行方程
①
~
⑥
的计算,实时在线得出气化炉内耐火砖层的温度和厚度。