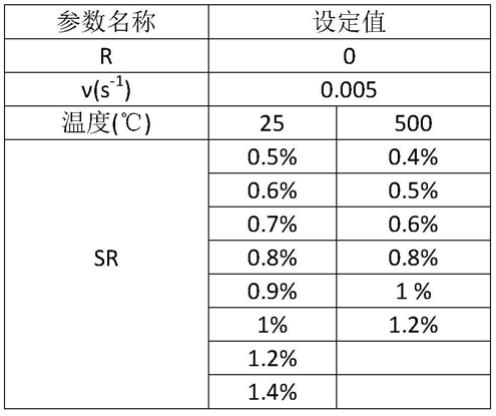
1.本发明涉及结构材料力学性能试验技术领域,涉及一种核燃料元件包壳用高强度f/m合金薄壁管材,用于第四代先进核能系统中液态金属冷却快堆高性能金属燃料元件的包壳;具体涉及一种适用于薄壁包壳管的高温疲劳试验夹具及试验方法。
背景技术:2.铅冷快堆在中子经济性、热工水力学特性、化学稳定性及安全性等方面具有独特的优势被认为是最具应用前景且有望率先实现工业示范的第四代核能系统。铁素体/马氏体合金(f/m合金)具有出色的抗辐照肿胀性能、良好的强韧性配合、稳定的热物理性能及相对较好的抗高温氧化和腐蚀能力,成为铅冷快堆首选的燃料包壳材料。
3.包壳是装载核燃料的密封外壳,其作用是防止裂变产物逸散,避免燃料受到冷却剂腐蚀及高效的导出热能,是核反应堆的一道安全屏障。在反应堆运行过程中,包壳内有裂变产物释热,外有冷却剂的浸蚀,铁马合金作为铅冷快堆的包壳材料,置身于强烈的快中子辐照、极端的液态金属腐蚀、更高的结构应力和热应力作用的复杂环境中,其结构的完整性对反应堆的安全运行至关重要。而根据以往的统计资料,在各类部件的失效破坏中约80%是疲劳断裂造成的,危害性较大,尤其是对于反应堆燃料包壳而言,一旦发生破坏,将会导致放射性物质泄漏,整个回路将被裂变产物污染,直接影响反应堆的安全运行,并带来巨大的经济损失。因此,研究包壳管的疲劳性能是反应堆安全、高效和经济运行的重要保障和有力支撑。
4.目前,对于f/m合金包壳管这种高强度金属薄壁小管的高温疲劳试验在国内外罕见报道,针对高强度f/m合金薄壁包壳管存在夹持部位易损伤、轴向加载易失稳、高温疲劳试验难以开展等技术难题。
技术实现要素:5.本发明所要解决的技术问题是针对高强度f/m合金薄壁包壳管存在夹持部位易损伤、轴向加载易失稳、高温疲劳试验难以开展等技术难题。本发明目的在于提供一种适用于薄壁包壳管的高温疲劳试验夹具及试验方法,本发明通过设计的薄壁包壳管高温疲劳试验夹具,解决高强度f/m合金薄壁包壳管存在的夹持部位易损伤、轴向加载易失稳、高温疲劳试验难以开展等技术难题,实现高强度f/m合金薄壁包壳管的轴向循环加载和疲劳试验,并建立相应的试验方法,并在此基础上研究了包壳管的高温应变循环行为。
6.本发明通过下述技术方案实现:
7.通过设计专用的试验夹具,解决高强度f/m合金薄壁包壳管试样的高温疲劳试验技术难题,试验夹具需满足以下几个条件:
8.(1)实现包壳管试样与试验夹具之间的紧密配合,防止因包壳管试样在夹持部位产生损伤而先于工作段发生破坏;
9.(2)提供足够的夹持力,满足试样轴向疲劳的加载条件;
10.(3)试验夹具和包壳管试样有较高的对中度,避免包壳管试样在加载过程中发生轴向失稳现象。
11.第一方面,针对上述要求,本发明提供了一种适用于薄壁包壳管的高温疲劳试验夹具,所述试验夹具为高强度f/m合金薄壁包壳管试样的专用试验夹具,所述试验夹具可以与包壳管试样紧密配合,并和包壳管试样有较高的对中度,有效的防止了包壳管试样在夹持部位产生损伤,避免了包壳管试样在加载过程中发生轴向失稳现象;能够配合实现高强度f/m合金薄壁包壳管的轴向循环加载和疲劳试验;
12.所述试验夹具包括上下对称设置的两个夹具结构,两个夹具结构之间放置高强度f/m合金薄壁包壳管试样;所述夹具结构包括主轴、锁紧螺帽、过渡套筒和锁紧套筒,所述锁紧套筒、过渡套筒、锁紧螺帽依次套设于所述主轴上,主轴和过渡套筒采用的材料为热膨胀系数不同材料。通过拧紧锁紧螺帽对过渡套筒产生的挤压力通过过渡套筒传递到锁紧套筒,使得锁紧套筒对主轴的锥部产生挤压力,从而实现试验夹具对包壳管试样抱紧。
13.使用时,所述试验夹具通过链接杆连接液压伺服材料试验机,通过液压伺服材料试验机对包壳管试样进行高温疲劳试验。
14.本发明的试验夹具可以与包壳管试样紧密配合,并和包壳管试样有较高的对中度,有效的防止了包壳管试样在夹持部位产生损伤,避免了包壳管试样在加载过程中发生轴向失稳现象。能够实现高强度f/m合金薄壁包壳管的轴向循环加载和疲劳试验。
15.进一步的,所述主轴依次包括连接段、螺纹段和工作段,所述工作段外周上套设过渡套筒和锁紧套筒,所述螺纹段外周上套设锁紧螺帽,所述连接段外接链接杆来连接液压伺服材料试验机;
16.所述工作段为中空的圆台体,沿所述圆台体的外壁均匀开设有多个槽,多个槽沿圆台体的母线方向开设;且在圆台体上底面(圆台体直径小的底面)槽的末端形成等值圆孔,这样防止了包壳管试样材料的破坏,圆孔保证了光滑性,避免夹持久了造成包壳管试样材料的开裂。
17.进一步的,所述主轴的工作段长度为60mm,工作段圆台体的下底面(圆台体直径大的底面)的外径为23.5mm,内部为内径12mm;
18.所述槽的宽度为1mm,槽的数量可以为4个或着别的数量;所述圆孔的直径为3mm;所述圆台体的锥角为3
°
。
19.进一步的,所述过渡套筒为中空的圆筒体,所述过渡套筒长度为44mm、内直径为20.5mm、外直径为30mm;
20.所述锁紧套筒长度为30mm,外直径为30mm(根据高温炉炉膛尺寸设计),内孔为与主轴工作段相同锥角的圆台体,其内孔两端孔径分别为19.96mm和23.2mm。
21.进一步的,所述锁紧套筒的线膨胀系数大于所述主轴和过渡套筒的线膨胀系数。
22.进一步的,所述锁紧套筒采用的材料为1cr17ni2,其线胀系数为10*10-6
/℃,屈服强度为691mpa;所述主轴和过渡套筒采用的材料为gh36,线膨胀系数为17*10-6
/℃,屈服强度为600mpa。拧紧锁紧螺帽后锁紧,螺帽对过渡套筒产生的挤压力通过过渡套筒传递到锁紧套筒,使得锁紧套筒对主轴的锥部产生挤压力,从而实现夹具对小管试样抱紧。但由于小管试样表面较为光滑,且未采取任何防滑措施,单靠锁紧螺帽的挤压力对小管试样的抱紧效果不理想。故使用时先在室温下通过锁紧螺帽让试验夹具与包壳管试样保持密配合,在
高温炉中随着温度升高,由于两种材料的线膨胀系数不同,主轴的热膨胀程度大于锁紧套筒,升温后试验夹具与包壳管试样之间夹配合更紧密,从而使得试验夹具对小管试样的抱紧力大大增强。
23.进一步的,针对f/m合金包壳管强度高、管壁薄、等壁厚的特点,为避免在循环加载过程中包壳管由于平行段无应力集中区域而出现表面裂纹生长不规则的现象,特将包壳管径向的中间部分用车床加工出一平行标距段,即所述包壳管试样为径向的中间部分设有平行标距段的核燃料元件包壳管材试样。
24.进一步的,所述包壳管试样两端均设有堵头,所述堵头为gh36材料制成薄壁管试样的堵头。且堵头的线膨胀系数大于所述主轴和过渡套筒的线膨胀系数。
25.进一步的,所述包壳管试样外径为12mm、壁厚2mm,所述标距段外径为11mm、壁厚为0.3mm、长度为15mm,所述包壳管试样总长度为65mm,表面粗造度为1.6以下。
26.第二方面,本发明还提供了一种反应堆用高强度f/m合金薄壁包壳管的高温疲劳试验方法,该试验方法采用所述的一种适用于薄壁包壳管的高温疲劳试验夹具实现高强度f/m合金薄壁包壳管的轴向循环加载和疲劳试验;该试验方法包括:
27.步骤1,安装所述试验夹具的各部件,并把高强度f/m合金薄壁包壳管试样装入所述试验夹具的上下两个夹具结构之间,所述包壳管试样一端插入上夹具结构的主轴下方中空的工作段内、另一端插入下夹具结构的主轴上方中空的工作段内;并把所述试验夹具通过链接杆与液压伺服材料试验机连接,并上电;
28.步骤2,疲劳试验开展之前,采集高温500℃下所述包壳管试样的静态力学信息,即静态拉伸试验数据;所述静态拉伸试验数据包括屈服应力、抗拉强度和延伸率;
29.步骤3,根据步骤2采集的静态力学信息,设置包壳管疲劳试验参数,所述包壳管疲劳试验参数包括应变幅sr、应变比r和应变速率γ;
30.步骤4,根据步骤2采集的静态力学信息和步骤3设置的包壳管疲劳试验参数,计算所述包壳管试样高温500℃条件各应变幅下半寿命周期的滞回曲线;并采用总应变幅和疲劳寿命的关系模型得到所述包壳管试样在高温500℃下的寿命曲线。
31.本发明与现有技术相比,具有如下的优点和有益效果:
32.本发明一种适用于薄壁包壳管的高温疲劳试验夹具,实现了高强度f/m合金薄壁包壳管的轴向循环加载和疲劳试验,设计的试验夹具可以与管试样紧密配合,防止因试样在夹持部位产生损伤而先于工作段发生破坏;试验夹具和包壳管试样有较高的对中度,避免了包壳管试样在加载过程中发生轴向失稳现象。建立的疲劳试验方法适用于高强度f/m合金薄壁包壳管及同等类型的管材试样,试样安装简单、便捷,获得的试验数据有效,可以为新一代核反应堆系统包壳管的安全设计与性能评价提供数据支撑。
附图说明
33.此处所说明的附图用来提供对本发明实施例的进一步理解,构成本技术的一部分,并不构成对本发明实施例的限定。在附图中:
34.图1为本发明针对的包壳管试样结构示意图。
35.图2为本发明一种适用于薄壁包壳管的高温疲劳试验夹具的主轴立体结构示意图。
36.图3为本发明一种适用于薄壁包壳管的高温疲劳试验夹具的主轴平面结构示意图。
37.图4为本发明一种适用于薄壁包壳管的高温疲劳试验夹具的主轴平面结构示意图中a-a的剖面图。
38.图5为本发明一种适用于薄壁包壳管的高温疲劳试验夹具的锁紧套筒结构示意图一。
39.图6为本发明一种适用于薄壁包壳管的高温疲劳试验夹具的锁紧套筒结构示意图二。
40.图7为本发明一种适用于薄壁包壳管的高温疲劳试验夹具整体结构示意图。
41.图8为本发明包壳管在室温条件各应变幅下半寿命周期的滞回曲线图。
42.图9为本发明包壳管在500℃条件各应变幅下半寿命周期的滞回曲线图。
43.图10为本发明包壳管a在室温下的寿命曲线图。
44.图11为本发明包壳管a在500℃下的寿命曲线图。
45.附图标记及对应的零部件名称:
46.1-包壳管试样,2-标距段,3-连接段,4-螺纹段,5-工作段,51-槽,52-圆孔,6-锁紧套筒,7-过渡套筒,8-锁紧螺帽,9-链接杆。
具体实施方式
47.在下文中,可在本发明的各种实施例中使用的术语“包括”或“可包括”指示所发明的功能、操作或元件的存在,并且不限制一个或更多个功能、操作或元件的增加。此外,如在本发明的各种实施例中所使用,术语“包括”、“具有”及其同源词仅意在表示特定特征、数字、步骤、操作、元件、组件或前述项的组合,并且不应被理解为首先排除一个或更多个其它特征、数字、步骤、操作、元件、组件或前述项的组合的存在或增加一个或更多个特征、数字、步骤、操作、元件、组件或前述项的组合的可能性。
48.在本发明的各种实施例中,表述“或”或“a或/和b中的至少一个”包括同时列出的文字的任何组合或所有组合。例如,表述“a或b”或“a或/和b中的至少一个”可包括a、可包括b或可包括a和b二者。
49.在本发明的各种实施例中使用的表述(诸如“第一”、“第二”等)可修饰在各种实施例中的各种组成元件,不过可不限制相应组成元件。例如,以上表述并不限制所述元件的顺序和/或重要性。以上表述仅用于将一个元件与其它元件区别开的目的。例如,第一用户装置和第二用户装置指示不同用户装置,尽管二者都是用户装置。例如,在不脱离本发明的各种实施例的范围的情况下,第一元件可被称为第二元件,同样地,第二元件也可被称为第一元件。
50.应注意到:如果描述将一个组成元件“连接”到另一组成元件,则可将第一组成元件直接连接到第二组成元件,并且可在第一组成元件和第二组成元件之间“连接”第三组成元件。相反地,当将一个组成元件“直接连接”到另一组成元件时,可理解为在第一组成元件和第二组成元件之间不存在第三组成元件。
51.在本发明的各种实施例中使用的术语仅用于描述特定实施例的目的并且并非意在限制本发明的各种实施例。如在此所使用,单数形式意在也包括复数形式,除非上下文清
楚地另有指示。除非另有限定,否则在这里使用的所有术语(包括技术术语和科学术语)具有与本发明的各种实施例所属领域普通技术人员通常理解的含义相同的含义。所述术语(诸如在一般使用的词典中限定的术语)将被解释为具有与在相关技术领域中的语境含义相同的含义并且将不被解释为具有理想化的含义或过于正式的含义,除非在本发明的各种实施例中被清楚地限定。
52.为使本发明的目的、技术方案和优点更加清楚明白,下面结合实施例和附图,对本发明作进一步的详细说明,本发明的示意性实施方式及其说明仅用于解释本发明,并不作为对本发明的限定。
53.实施例1
54.如图1至图7所示,本发明一种适用于薄壁包壳管的高温疲劳试验夹具,所述试验夹具为高强度f/m合金薄壁包壳管试样的专用试验夹具,所述试验夹具可以与包壳管试样紧密配合,并和包壳管试样有较高的对中度,有效的防止了包壳管试样在夹持部位产生损伤,避免了包壳管试样在加载过程中发生轴向失稳现象;能够配合实现高强度f/m合金薄壁包壳管的轴向循环加载和疲劳试验;
55.所述试验夹具包括上下对称设置的两个夹具结构,两个夹具结构之间放置高强度f/m合金薄壁包壳管试样;如图7所示,所述夹具结构包括主轴、锁紧螺帽8、过渡套筒7和锁紧套筒6,所述锁紧套筒6、过渡套筒7、锁紧螺帽8依次套设于所述主轴上,主轴和过渡套筒采用的材料为热膨胀系数不同材料。通过拧紧锁紧螺帽8对过渡套筒7产生的挤压力通过过渡套筒7传递到锁紧套筒6,使得锁紧套筒6对主轴的锥部产生挤压力,从而实现试验夹具对包壳管试样1抱紧。
56.所述试验夹具通过链接杆9连接液压伺服材料试验机,通过液压伺服材料试验机对包壳管试样1进行高温疲劳试验。本发明的试验夹具可以与包壳管试样紧密配合,并和包壳管试样有较高的对中度,有效的防止了包壳管试样在夹持部位产生损伤,避免了包壳管试样在加载过程中发生轴向失稳现象。能够实现高强度f/m合金薄壁包壳管的轴向循环加载和疲劳试验。
57.本实施例中,如图2-4所示,所述主轴依次包括连接段3、螺纹段4和工作段5,所述工作段5外周上套设过渡套筒7和锁紧套筒6,所述螺纹段4外周上套设锁紧螺帽8,所述连接段3外接链接杆9来连接液压伺服材料试验机;
58.所述工作段5为中空的圆台体,沿所述圆台体的外壁均匀开设有多个槽51,多个槽51沿圆台体的母线方向开设;且在圆台体上底面(圆台体直径小的底面)槽51的末端形成等值圆孔52,这样防止了包壳管试样材料的破坏,圆孔保证了光滑性,避免夹持久了造成包壳管试样材料的开裂。
59.本实施例中,所述主轴的工作段5长度为60mm,工作段5圆台体的下底面(圆台体直径大的底面)的外径为23.5mm,内部为内径12mm;
60.所述槽51的宽度为1mm,槽51的数量为4个;所述圆孔52的直径为3mm;所述圆台体的锥角为3
°
。
61.本实施例中,所述过渡套筒7为中空的圆筒体,所述过渡套筒7长度为44mm、内直径为20.5mm、外直径为30mm;
62.如图5、6所示,所述锁紧套筒6长度为30mm,外直径为30mm(根据高温炉炉膛尺寸设
计),内孔为与主轴工作段相同锥角的圆台体,其内孔两端孔径分别为19.96mm和23.2mm。
63.本实施例中,所述锁紧套筒6的线膨胀系数大于所述主轴和过渡套筒7的线膨胀系数。
64.本实施例中,所述锁紧套筒6采用的材料为1cr17ni2,其线胀系数为10*10-6
/℃,屈服强度为691mpa;所述主轴和过渡套筒7采用的材料为gh36,线膨胀系数为17*10-6
/℃,屈服强度为600mpa。拧紧锁紧螺帽8后锁紧,螺帽对过渡套筒7产生的挤压力通过过渡套筒7传递到锁紧套筒6,使得锁紧套筒对主轴的锥部产生挤压力,从而实现夹具对小管试样抱紧。但由于小管试样表面较为光滑,且未采取任何防滑措施,单靠锁紧螺帽的挤压力对小管试样的抱紧效果不理想。故使用时先在室温下通过锁紧螺帽让试验夹具与包壳管试样保持密配合,在高温炉中随着温度升高,由于两种材料的线膨胀系数不同,主轴的热膨胀程度大于锁紧套筒,升温后试验夹具与包壳管试样之间夹配合更紧密,从而使得试验夹具对小管试样的抱紧力大大增强。
65.本实施例中,针对f/m合金包壳管强度高、管壁薄、等壁厚的特点,为避免在循环加载过程中包壳管由于平行段无应力集中区域而出现表面裂纹生长不规则的现象,特将包壳管径向的中间部分用车床加工出一平行标距段,即所述包壳管试样为径向的中间部分设有平行标距段2的核燃料元件包壳管材试样。
66.本实施例中,所述包壳管试样1两端均设有堵头,堵头的形状酷似子弹头。所述堵头为gh36材料制成薄壁管试样的堵头。且堵头的线膨胀系数大于所述主轴和过渡套筒7的线膨胀系数。
67.本实施例中,所述包壳管试样1外径为12mm、壁厚2mm,所述标距段2外径为11mm、壁厚为0.3mm、长度为15mm,所述包壳管试样1总长度为65mm,表面粗造度为1.6以下。
68.使用时,所述包壳管试样一端旋入上夹具结构的主轴下方中空的工作段内、另一端插入下夹具结构的主轴上方中空的工作段内;具体地,首先将包壳管试样的夹持端塞入gh36塞头,然后将其插入上夹具结构主轴下部的中空工作段内(图中5),然后依次穿入锁紧套筒6、过渡套筒7,然后通过锁紧螺帽8向下不断旋入,通过压迫锁紧套筒6,将包壳管试样夹紧。同样的,安装包壳管试样另外一边下夹具结构。安好后将其安装在试验机上即可进行疲劳试验。图7中仅展示该夹具的上夹具结构,下夹具结构位于下夹具结构的正下方。
69.经验证,采用本发明设计的包壳管疲劳试验夹具,在液压伺服材料试验机上可以实现f/m合金包壳管的高温疲劳试验。本发明实现了高强度f/m合金薄壁包壳管的轴向循环加载和疲劳试验,设计的试验夹具可以与管试样紧密配合,防止因试包壳管样在夹持部位产生损伤而先于工作段发生破坏;试验夹具和包壳管试样有较高的对中度,避免了包壳管试样在加载过程中发生轴向失稳现象。
70.实施例2
71.如图8至图11所示,本实施例与实施例1的区别在于,本实施例提供了一种反应堆用高强度f/m合金薄壁包壳管的高温疲劳试验方法,该试验方法采用实施例1所述的一种适用于薄壁包壳管的高温疲劳试验夹具实现高强度f/m合金薄壁包壳管的轴向循环加载和疲劳试验;该试验方法包括:
72.步骤1,安装所述试验夹具的各部件,并把高强度f/m合金薄壁包壳管试样装入所述试验夹具的上下两个夹具结构之间,所述包壳管试样一端插入上夹具结构的主轴下方中
空的工作段内、另一端插入下夹具结构的主轴上方中空的工作段内;并把所述试验夹具通过链接杆9与液压伺服材料试验机连接,并上电;
73.步骤2,疲劳试验开展之前,采集室温和高温500℃下所述包壳管试样的静态力学信息,即静态拉伸试验数据;所述静态拉伸试验数据包括屈服应力、抗拉强度和延伸率;
74.具体地,在疲劳试验前开展包壳管样品的静态拉伸和压缩试验。试验样品采用图1所示样品。控制方式为位移控制,应变速率γ为1
×
10-3
s-1
直至样品断裂试验结束,每组试验采用3个样品,以减少试验误差。通过采集、分析试验数据,获得包壳管样品的力学参数信息,试验数据有效,结果如表1所示。
75.表1包壳管单轴拉伸性能
76.试验温度℃)屈服应力σ
0.2
(mpa)抗拉强度σb(mpa)延伸率δ(%)259021051950051152415
77.步骤3,根据步骤2采集的静态力学信息,设置包壳管疲劳试验参数,所述包壳管疲劳试验参数包括应变幅sr、应变比r和应变速率γ等;具体参数如表2所示。采集各应变幅下有效数据,以对其疲劳寿命数据进行统计分析。安装包壳管疲劳样品时,注意上下夹头的是否中心对称,否则样品在循环力作用下容易径向受力不均匀发生侧弯现象。
78.表2包壳管疲劳试验参数
[0079][0080]
步骤4,根据步骤2采集的静态力学信息和步骤3设置的包壳管疲劳试验参数,计算所述包壳管试样在室温和高温500℃条件各应变幅下半寿命周期的滞回曲线;并采用总应变幅和疲劳寿命的关系模型得到所述包壳管试样在室温和高温500℃下的寿命曲线。
[0081]
4.1、材料的滞回环特性
[0082]
一般来说滞回曲线最直观反映的是试件应力和产生应变的关系,这样的曲线中可以看到在某个力作用下产生的应变有多少。滞回曲线所围成的面积就是所消耗的能量,从曲线中还可以得出试件的疲劳数据。图8-图9给出了室温和500℃条件下不同应变幅下的应力-应变滞回环,图8和图9的横坐标表示应变,纵坐标表示应力;通过比较可知,随着应变幅的增加,应力幅增加,应力-应变滞环的面积逐渐增大,疲劳寿命逐渐降低。高温下材料滞回环面积随着应变增加而增加的速度较快,说明材料在高温下的破环更加迅速。
[0083]
4.2、疲劳寿命
[0084]
材料的疲劳寿命主要取决于疲劳变形过程中材料所承受的应力幅或应变幅的大小。目前,为人们所普遍接受的描述应力控制和应变控制条件下材料的疲劳寿命行为的方法主要有两种:一种是由basquin提出的以循环应力幅为参量的疲劳寿命表达方法。另一种是由coffin和manson提出的以塑性应变幅为参量的疲劳寿命表达方法,具体的表达式为:
[0085]
δε
t
=δεe+δε
p
ꢀꢀꢀꢀꢀꢀꢀꢀꢀꢀꢀꢀꢀꢀꢀꢀꢀꢀꢀꢀꢀꢀꢀꢀꢀꢀꢀ
(公式1)
[0086][0087][0088]
式中δε
t
为总应变幅,δεe为弹性应变幅,δε
p
为塑性应变幅,σ
′f为疲劳强度系数,ε
′f为疲劳延性系数,b为疲劳强度指数,c为疲劳延性指数。根据公式1、2和3可得到相应的应变-疲劳寿命关系。
[0089]
综上所述,将basquin和coffin-manson公式结合,可以的到总应变幅和疲劳寿命的关系。
[0090][0091]
如图10和图11所示,图10和图11的横坐标表示倍寿命,纵坐标表示应变幅;利用basquin和coffin-manson公式可以拟合得到材料在室温和500℃下的总寿命曲线,先后拟合塑性应变幅和弹性应变幅与寿命反向次数的关系,如图中实心圆和实心三角点线及虚线所示,将两部分结合可以得到材料的总寿命曲线,如图中矩形实线所示。
[0092]
表3为包壳管的疲劳参数,如下所示:
[0093]
表3包壳管的疲劳参数
[0094][0095]
本发明建立的疲劳试验方法适用于高强度f/m合金薄壁包壳管及同等类型的管材试样,试样安装简单、便捷,获得的试验数据有效,可以为新一代核反应堆系统包壳管的安全设计与性能评价提供数据支撑。
[0096]
以上所述的具体实施方式,对本发明的目的、技术方案和有益效果进行了进一步详细说明,所应理解的是,以上所述仅为本发明的具体实施方式而已,并不用于限定本发明的保护范围,凡在本发明的精神和原则之内,所做的任何修改、等同替换、改进等,均应包含在本发明的保护范围之内。