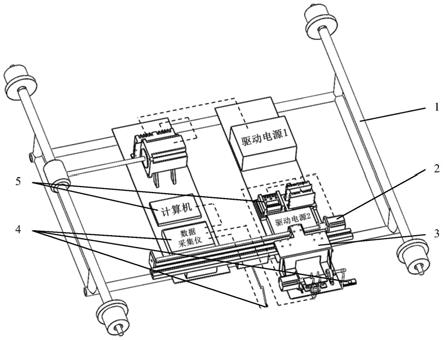
1.本发明涉及钢轨伤损识别技术领域,尤其是涉及一种基于微动特性的钢轨伤损识别装置及方法。
背景技术:2.钢轨是轨道交通的承载导向部件,要求具有绝对可靠性。随着我国轨道交通向高速、重载、高密度方向发展,钢轨伤损形式呈现复杂多样化趋势。小半径曲线钢轨受力环境复杂,钢轨受垂、横向动弯拉应力和局部变形拉应力,易产生疲劳裂纹,伤损率高,形式多样,其中早期轨颚裂纹和轨底裂纹隐蔽性强,发展初期不易被检出,扩展速度快,严重危及行车安全,是引发断轨事故的巨大隐患。钢轨伤损的有效识别,是当前国家和行业关注的焦点。
3.常见的现役钢轨探伤法和断轨监测法有许多。公开号为cn113447572a的发明专利中,提出了一种超声波探伤的钢轨探伤方法,超声波探伤多依赖主观因素,易受轨面平整度影响,漏检误判事件频发;公开号为cn214011477u的实用新型专利中,提出了一种基于电路原理的断轨监测系统,并不具备事故预判能力;公开号为cn214576884u的实用新型专利中,提出了一种光纤实时检测方法,将该方法应用于钢轨伤损识别邻域,复接技术难度大;另外还有应力断轨检测方法,灵敏度有待提高。此外,根据相关规定,凡钢轨表面检出裂纹,一律判为重伤,这是由于服役钢轨的现有探伤方法只能保证贯通裂纹或毫米级重伤裂纹的较高检出率,而对早期裂纹和潜在的伤损隐患不具备有效识别能力,且钢轨轨头下颚裂纹和轨底裂纹具有极强的隐蔽性,处于传统探伤方法的盲区中,这在一定程度上了降低了断轨事故的可控性。这在客观上要求,钢轨伤损识别领域亟需开展新的技术方法研究。
技术实现要素:4.本发明的目的就是为了克服上述现有技术存在的缺陷而提供一种基于微动特性的钢轨伤损识别装置。
5.本发明的目的可以通过以下技术方案来实现:
6.一种基于微动特性的钢轨伤损识别装置,该装置包括:
7.行走模块:用于架设在钢轨上并在钢轨上行走;
8.步进模块:沿行走模块行走方向布置在其侧边处;
9.锤击模块:用于锤击钢轨,所述的锤击模块安装在步进模块上,所述的步进模块驱动锤击模块沿钢轨方向步进移动;
10.测试模块:定位锤击模块当前位置并采集锤击力信号以及产生的振动信号;
11.控制模块:分别连接行走模块、步进模块、锤击模块和测试模块;
12.行走模块在钢轨上行走,步进模块控制锤击模块的锤击点位置,锤击模块锤击钢轨,采集锤击力信号以及产生的振动信号,控制模块对采集的数据进行分析获取测试区段的模态曲率分布,将现役钢轨和服役n天前钢轨的模态曲率作差得到模态曲率差分布,根据
模态曲率差分布中峰值位置、大小判定伤损位置及伤损级别。
13.优选地,所述的行走模块包括方形底盘、行走轮、行走步进电机,所述的行走轮设置在方形底盘四角处,所述的行走轮用于在钢轨上行走,所述的行走步进电机通过传动轴控制行走轮行走。
14.优选地,所述的步进模块包括丝杆步进电机、丝杆模组、导轨滑块模组,所述的丝杆模组和导轨滑块模组沿行走模块行走方向布置在行走模块侧边处,所述的丝杆模组和导轨滑块模组的滑块固定连接且同步移动,所述的锤击模块安装在丝杆模组和导轨滑块模组同步移动的滑块上,所述的丝杆步进电机连接丝杆模组。
15.优选地,所述的锤击模块包括联结座、锤头组件以及用于驱动锤头组件锤击动作的锤击驱动组件,所述的联结座与步进模块固定连接,所述的锤头组件可上下活动式安装在联结座上,所述的锤击动作组件安装在联结座上。
16.优选地,锤头组件包括套筒、锤头和回弹件,所述的套筒固定在联结座上,且联结座上开设有与所述的套筒适配的孔,所述的锤头穿过所述的套筒和联结座活动安装,所述的套筒约束锤头进行上下直线运动,所述的锤头顶部连接所述的回弹件,所述的锤头包括由上至下依次布置的锤击板、质量块、力传感器和端头,进行锤击动作时,所述的锤击驱动组件作用于所述的锤击板,所述的端头作用于钢轨,所述的锤击驱动组件包括锤击步进电机、锤击转轴和摆臂,所述的锤击转轴连接锤击步进电机输出端,所述的摆臂安装在锤击转轴上,所述的摆臂用于向锤头组件施加锤击驱动力。
17.优选地,所述的测试模块包括定位模块、振动采集模块和数据采集仪,所述的定位模块和振动采集模块均连接至数据采集仪。
18.优选地,所述的定位模块包括激光测距仪和第一转臂,所述的激光测距仪通过所述的第一转臂安装在锤击模块侧面。
19.优选地,所述的振动采集模块包括加速度传感器、固定臂、第二转臂,所述的固定臂安装在行走模块侧边,所述的第二转臂与所述的固定臂相连且初始状态下与所述的固定臂合并,所述的加速度传感器安装在转臂末端,所述的加速度传感器用于采集锤击钢轨产生的振动信号。
20.一种基于微动特性的钢轨伤损识别方法,该方法包括:
21.以n天作为一个检测周期,对相同测试区段钢轨进行锤击测试并获取对应的模态曲率分布;
22.对现役钢轨和服役n天前钢轨的模态曲率作差得到模态曲率差分布;
23.根据模态曲率差分布中峰值位置、大小判定伤损位置及伤损级别;
24.其中,锤击测试并获取模态曲率分布的方式为:
25.将测试区段相邻两个扣件之间的区域确定为一个测试单元,确定各个测试单元的锤击点位置;
26.依次对各个测试单元进行锤击测试,对于每一个测试单元,依次对各个锤击点施加锤击力,采集锤击力大小以及锤击点附近产生的振动信号;
27.对每一个测试单元采集的锤击力和振动信号分别进行分析,计算获得测试单元内p个锤击点的离散模态信息,并通过中心差分法得到各锤击点的模态曲率。
28.优选地,采用神经网络模型建立钢轨模态曲率差与伤损级别的量化关系,进而通
9为顶板,3-10为弹簧,3-11为锤头,3-11-1为锤击板,3-11-2为质量块,3-11-3为力传感器,3-11-4为端头,4为测试模块,4-1为定位模块,4-2为数据采集仪,4-3为振动采集模块,4-1-1为激光测距仪,4-1-2为第一转臂,4-3-1为加速度传感器,4-3-2为固定臂,4-3-3为第二转臂,5为控制模块,5-1为控制器,5-2为计算机。
具体实施方式
49.下面结合附图和具体实施例对本发明进行详细说明。注意,以下的实施方式的说明只是实质上的例示,本发明并不意在对其适用物或其用途进行限定,且本发明并不限定于以下的实施方式。
50.实施例
51.如图1~图10所示,本实施例提供一种基于微动特性的钢轨伤损识别装置,该装置包括:
52.行走模块1:用于架设在钢轨上并在钢轨上行走;
53.步进模块2:沿行走模块1行走方向布置在其侧边处;
54.锤击模块3:用于锤击钢轨,锤击模块3安装在步进模块2上,步进模块2驱动锤击模块3沿钢轨方向步进移动;
55.测试模块4:定位锤击模块3当前位置并采集锤击力信号以及产生的振动信号;
56.控制模块5:分别连接行走模块1、步进模块2、锤击模块3和测试模块4;
57.行走模块1在钢轨上行走,步进模块2控制锤击模块3的锤击点位置,锤击模块3锤击钢轨,采集锤击力信号以及产生的振动信号,控制模块5对采集的数据进行分析获取测试区段的模态曲率分布,将现役钢轨和服役n天前钢轨的模态曲率作差得到模态曲率差分布,根据模态曲率差分布中峰值位置、大小判定伤损位置及伤损级别。
58.行走模块1包括方形底盘1-5、行走轮1-1、行走驱动器1-2、行走步进电机1-4,行走轮1-1设置在方形底盘1-5四角处,行走轮1-1用于在钢轨上行走,行走步进电机1-4通过传动轴控制行走轮1-1行走,行走驱动器1-2驱动行走步进电机1-4,行走驱动器1-2通过第一驱动电源1-3供电。
59.本实施例中行走模块1的行走步进电机1-4选择110mm两相混合式步进电机,保持转矩为30n.m。与钢轨接触的行走轮1-1的外轮廓直径为100mm,材料为聚酰胺纤维。驱动电路的连接方式:第一驱动电源1-3
→
行走驱动器1-2
→
行走步进电机1-4;控制电路的连接方式:行走驱动电源
→
控制器5-1
→
行走驱动器1-2
→
行走步进电机1-4。行走轮1-1通过传动轴与行走步进电机1-4相连。第一驱动电源1-3、行走驱动器1-2、行走步进电机1-4安装于底盘1-5上。
60.步进模块2包括丝杆步进电机2-3、丝杆模组2-4、导轨滑块模组2-5,丝杆模组2-4和导轨滑块模组2-5沿行走模块1行走方向布置在行走模块1侧边处,丝杆模组2-4和导轨滑块模组2-5的滑块固定连接且同步移动,锤击模块3安装在丝杆模组2-4和导轨滑块模组2-5同步移动的滑块上,丝杆步进电机2-3连接丝杆模组2-4,丝杆步进电机2-3通过步进驱动器2-1驱动,步进驱动器2-1通过第二驱动电源2-2供电。
61.本实施例中步进模块2的驱动电路和控制电路的连接方式与行走模块1一致。丝杆步进电机2-3选择57mm两相混合式步进电机,保持转矩为1.2n.m。丝杆步进电机2-3的轴与
丝杆模组2-4的丝杆通过联轴器联结,丝杆模组2-4的有效行程为770mm,丝杆模组2-4与导轨滑块模组2-5固定安装于底盘1-5上,且两者的滑块通过联结座3-3固定联结且同步移动,导轨滑块模组2-5的有效行程为930mm。
62.锤击模块3包括联结座3-3、锤头3-11组件以及用于驱动锤头3-11组件锤击动作的锤击驱动组件,联结座3-3与步进模块2固定连接,锤头3-11组件可上下活动式安装在联结座3-3上,锤击动作组件安装在联结座3-3上。
63.锤头3-11组件包括套筒3-7、锤头3-11和回弹件,套筒3-7固定在联结座3-3上,且联结座3-3上开设有与套筒3-7适配的孔,锤头3-11穿过套筒3-7和联结座3-3活动安装,套筒3-7约束锤头3-11进行上下直线运动,锤头3-11顶部连接回弹件,锤头3-11包括由上至下依次布置的锤击板3-11-1、质量块3-11-2、力传感器3-11-3和端头3-11-4,进行锤击动作时,锤击驱动组件作用于锤击板3-11-1,端头3-11-4作用于钢轨,锤击驱动组件包括锤击驱动器3-1、锤击步进电机3-2、锤击转轴3-6和摆臂3-5,锤击转轴3-6连接锤击步进电机3-2输出端,摆臂3-5安装在锤击转轴3-6上,锤击驱动器3-1驱动锤击步进电机3-2,摆臂3-5用于向锤头3-11组件施加锤击驱动力,本实施例中锤击板3-11-1采用e型板,套筒3-7采用石墨套筒3-7。
64.在本实施例中,锤击模块3的驱动电路和控制电路的连接方式与行走模块1一致。锤击步进电机3-2通过锤击转轴3-6和轴承座3-4共同控制摆臂3-5的定轴旋转,摆臂3-5的有效半径为28mm,一个旋转周期分为三步:初始状态为水平位置,摆臂3-5与e型板接触;锤击时摆臂3-5快速向下转动,转速300rpm,转动3/4圈,摆臂3-5指向竖直向上;暂停3s,等待信号采集完毕;回正时摆臂3-5缓慢转动,转速15rpm,转动1/4圈,摆臂3-5再次与e型板接触。锤头3-11的e型板与质量块3-11-2通过焊接连接;质量块3-11-2、力传感器3-11-3和端头3-11-4通过螺栓连接,力传感器3-11-3可选用美国pcb公司生产的208c05型号石英力传感器3-11-3,灵敏度为0.2248mv/n;质量块3-11-2为304不锈钢材质,质量块3-11-2直径和套筒3-7内径都为25mm,两者为间隙配合;石墨套筒3-7长度为20mm,通过螺栓固定于联结座3-3上;顶板3-9的尺寸为100
×
40
×
3mm,通过上下两个m5螺母固定于螺栓3-8上,螺栓尺寸为m5
×
100;顶板3-93-9与锤头3-11的e型板通过弹簧3-10相连,弹簧3-10总刚度k=4n/m;摆臂3-5快速向下推动e型板来实现锤头3-11的自由敲击运动。
65.测试模块4包括定位模块4-1、振动采集模块4-3和数据采集仪4-2,定位模块4-1和振动采集模块4-3均连接至数据采集仪4-2。定位模块4-1包括激光测距仪4-1-1和第一转臂4-1-2,激光测距仪4-1-1通过第一转臂4-1-2安装在锤击模块3侧面。振动采集模块4-3包括加速度传感器4-3-1、固定臂4-3-2、第二转臂4-3-3,固定臂4-3-2安装在行走模块1侧边,第二转臂4-3-3与固定臂4-3-2相连且初始状态下与固定臂4-3-2合并,加速度传感器4-3-1安装在转臂末端,加速度传感器4-3-1用于采集锤击钢轨产生的振动信号。
66.本实施例中激光测距仪4-1-1可选用深圳深视智能科技有限公司生产的sgi500/505型点激光测距仪4-1-1,量程为125~875mm,再现性(精度)为5um,激光测距仪4-1-1通过第一转臂4-1-2安装于联结座3-3上,第一转臂4-1-2的有效转动半径为100mm;在装置行走定位的过程中,第一转臂4-1-2竖直向下,激光测距仪4-1-1通过实时测量与扣件铁垫板沿轨向的距离进行精确定位,实时测量距离符合定位要求后装置自动停止行走,第一转臂4-1-2通过定轴转动转变为水平状态。
67.数据采集仪4-2安装于底盘1-5上,可选用北京东方振动和噪声技术研究所生产的inv3062sv型采集仪,采样频率为6.25~51.2khz,频率误差<0.005%,幅值误差<0.5%。
68.振动采集模块4-3中的加速度传感器4-3-1采用磁吸式加速度传感器4-3-1,固定臂4-3-2安装于导轨滑块模组2-5底部,有效长度为138mm;第二转臂4-3-3与固定臂4-3-2相连且初始状态与固定臂4-3-2合并,有效转动半径为80mm;第二转臂4-3-3前端夹持有磁吸式加速度传感器4-3-1,可选用江苏成孚电子科技有限公司生产的cf0113型压电式加速度传感器4-3-1,灵敏度为97.9mv/g,量程
±
200g,分辨率(精度)为0.2mg;
69.装置行走定位完成后,通过第二转臂4-3-3转动将磁吸式加速度传感器4-3-1吸附于钢轨轨底顶面,吸附位置在靠左紧挨第m/2个测点(测点数m为偶数),开始本单元内的数据采集;待本单元数据采集完毕后,通过第二转臂4-3-3将磁吸式加速度传感器4-3-1与钢轨分离并回到初始状态。
70.控制模块5包括控制器5-1和计算机5-2。控制器5-1用于控制行走步进电机1-4、丝杆步进电机2-3、锤击步进电机3-2的转动、暂停动作;计算机5-2内置有相应软件用于数据采集仪4-2参数设置以及测试数据的实时处理。
71.基于上述钢轨损伤识别装置,本实施例还提供一种基于微动特性的钢轨伤损识别方法。如图12所示,该方法包括:
72.以n天作为一个检测周期,对相同测试区段钢轨进行锤击测试并获取对应的模态曲率分布;
73.对现役钢轨和服役n天前钢轨的模态曲率作差得到模态曲率差分布;
74.根据模态曲率差分布中峰值位置、大小判定伤损位置及伤损级别;
75.其中,锤击测试并获取模态曲率分布的方式为:
76.将测试区段相邻两个扣件之间的区域确定为一个测试单元,确定各个测试单元的锤击点位置;
77.依次对各个测试单元进行锤击测试,对于每一个测试单元,依次对各个锤击点施加锤击力,采集锤击力大小以及锤击点附近产生的振动信号;
78.对每一个测试单元采集的锤击力和振动信号分别进行分析,计算获得测试单元内p个锤击点的离散模态信息,并通过中心差分法得到各锤击点的模态曲率。
79.采用神经网络模型建立钢轨模态曲率差与伤损级别的量化关系,进而通过神经网络模型对钢轨损伤级别进行识别。
80.在上述基于微动特性的钢轨伤损识别方法的基础上,利用所述的基于微动特性的钢轨伤损识别装置进行损伤识别的具体操作步骤为:
81.第一步、开启第一驱动电源1-3、第二驱动电源2-2、数据采集仪4-2、控制器5-1、计算机5-2和激光测距仪4-1-1;通过计算机5-2的相应软件操作界面设置数据采集仪4-2的基本参数,通道参数及锤击触发条件。其中,基本参数包括:试验名,存储路径,试验号为自动增加,采样频率为30k;通道参数包括:通道数目为2,其中1通道为力信号,标定值(灵敏度)为0.2248mv/n,2通道为加速度信号,标定值(灵敏度)为97.9mv/g;锤击触发条件包括:触发通道为1通道、触发3次、每次采样点数为32768、滞后点数为128、触发比例0.5%,即锤击力大于222.4n时开始采样。
82.第二步、通过控制器5-1控制行走步进电机1-4转动来带动行走轮1-1行走,通过控
制器5-1控制激光测距仪4-1-1实时测量与扣件铁垫板沿轨向的距离进行精确行走定位;实时测量距离符合定位要求后装置停止行走,并通过第二转臂4-3-3将磁吸式加速度传感器4-3-1吸附于钢轨轨底顶面。本实施例中实时测量与扣件铁垫板沿轨向的距离x(m),控制行走速度v(m/s)与距离x之间的关系为v=19.55x
2-5.08x+0.33,即实时测量距离符合定位要求0.13m后装置停止行走。
83.第三步、开始采样,锤头3-11锤击轨底顶面,力传感器3-11-3拾取到力信号,吸附于轨底顶面的磁吸式加速度传感器4-3-1拾取到振动信号,数据采集仪4-2将数据实时传输到计算机5-2。
84.第四步、待一个测点的数据采集完毕后,存储其坐标信息,通过步进模块2驱动锤击模块3向前定距移动,改变锤击点位置,多次重复步骤三、四,完成一个单元内p个测点的数据采集,以扣件间距为0.625m为例,定居移动距离为0.625/p(m),然后步进模块2通过驱动器控制回到初始位置,磁吸式加速度传感器4-3-1通过第二转臂4-3-3从轨底顶面取下。
85.第五步、待一个单元内数据采集完毕后,计算机5-2内置软件对力信号和振动信号进行快速傅里叶变换(fft)和传递函数计算获得p个测点的离散模态信息,并转化为模态曲率。
86.其中,模态曲率的计算方法是基于材料力学中梁中性面的曲率方程:
87.k(x,t)=m(x,t)/ei(x)
88.式中,m(x,t)为钢轨任意截面任意时刻的弯矩;
89.ei(x)为为钢轨任意截面的抗弯刚度;
90.k(x,t)为梁上任意一点模态曲率。
91.采用本装置进行模态曲率计算时,步骤如下:
92.首先通过力传感器3-11-3、磁吸式加速度传感器4-3-1、数据采集仪4-2采样测得钢轨轨底顶面各锤击点的位移模态r=1,2,
……
p,组成一个测试单元内轨底顶面的整体位移模态振型(离散模态信息):
[0093][0094]
然后采用中心差分的方法,得到各测点相应的模态曲率:
[0095][0096]
通过各测点的曲率模态ρ(r),得到一个单元内轨底顶面整体模态曲率分布:
[0097]
p=[ρ(1) ρ(2)ρ(3)
…
ρ(r)
…
ρ(p-1)ρ(p)]
[0098]
式中:下标r表示第r个测点(锤击点),d表示相邻测点之间的距离。
[0099]
第六步、在对一个单元内数据进行计算分析的同时,装置通过行走模块1与定位模块4-1行走定位到下一个待测单元进行锤击测试,并通过采用第五步的方法得到相应测试单元测点的模态曲率分布,依次对各个单元进行锤击测试,直到整个区段的钢轨测试完毕。
[0100]
第七步、以n天作为一个检测周期,对相同区段钢轨重复步骤二、三、四、五、六;对每个单元内的现役钢轨和服役n天前钢轨的模态曲率作差值得到模态曲率差分布(每个测点一一对应作差,从而得到模态曲率差分布);通过某坐标信息的模态曲率差及其峰值大小来判定伤损位置及伤损级别,以可判定的伤损隐患、早期裂纹和重伤裂纹的相关参数(如坐
标、深度、长度等)作为一组伤损数据,通过计算机5-2内置的神经网络模型来学习伤损数据与模态曲率差之间的量化关系,并逐步建立精细化的钢轨伤损分类分级评价方法,最终达到钢轨伤损精确识别的目的。
[0101]
需要说明的是:为了保证识别结果的精准性,测量时每个测试分区需要选取尽量多的锤击点。当然,在其他一些实施例中,也可以通过拟合的方式,得到连续的模态曲率差分布曲线。例如图11所示,是深度为10mm裂纹的模态曲率差峰值大小。以可判定的伤损隐患、早期裂纹和重伤裂纹的相关参数(如坐标、深度、长度等)作为一组伤损数据,通过计算机5-2内置的神经网络模型来学习一组伤损数据与所对应的模态曲率差峰值之间的量化关系,并逐步建立精细化的钢轨伤损分类分级评价方法,最终达到钢轨伤损精确识别的目的。
[0102]
上述实施方式仅为例举,不表示对本发明范围的限定。这些实施方式还能以其它各种方式来实施,且能在不脱离本发明技术思想的范围内作各种省略、置换、变更。