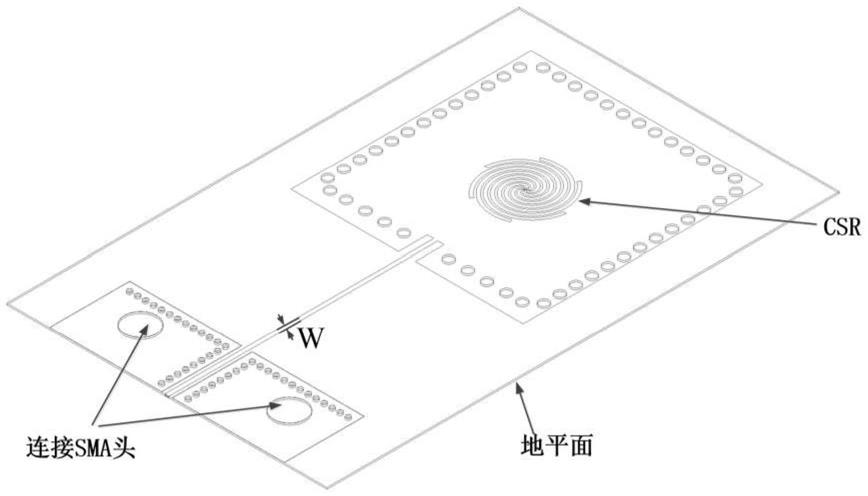
1.本发明属于焊接金属板内部缺陷检测技术领域,具体涉及一种涡流辅助焊接金属板内部缺陷微波无损检测方法。
背景技术:2.在交通、航空航天、核能、电力等诸多工程领域,材料或机件的突然断裂,在工程上是普遍存在的现象。疲劳断裂是其零件主要失效形式,而这种形式引起的裂纹往往没有明显的变形,不易察觉出来,从而导致灾难性的事故,造成巨大的经济损失和人员伤亡。因此,为了提前得知裂纹,避免不必要的损失,有效、可靠的无损检测技术必不可少。
3.微波技术以其便捷、高效等优点被广泛应用于金属材料缺陷的无损检测。微波对材料的无损检测特征和方法是由材料之间相互作用特性所决定的,电磁场透过金属表面进入内部的深度主要由材料的电导率和磁导率共同决定的,由于趋肤深度的影响,电磁场只能检测其表面的缺陷,而很难对金属材料深处的缺陷结构进行检测。
4.为了提高微波无损检测技术的检测能力,本发明尝试一种涡流辅助的微波无损检测方法,实现焊接金属板材较深(》2mm)区域缺陷结构的检测。
技术实现要素:5.为了实现焊接金属板内部缺陷的微波无损检测,本发明提供一种涡流辅助焊接金属板内部缺陷微波无损检测方法,通过涡流辅助方法,利用csr电磁检测单元感知焊接金属板不同位置涡流电磁场的异同,精确定位焊接金属板深处的缺陷结构。
6.为了达到上述目的,本发明采用的技术方案如下:
7.一种涡流辅助焊接金属板内部缺陷微波无损检测方法,步骤如下:
8.步骤1:根据测试要求,选择低频激励线圈,并且选择适配的激励频率,使激励频率能够在焊接金属板在深度大于2mm的区域产生恒定的涡流;
9.步骤2:进行csr检测单元设计,具体如下:
10.根据焊接金属板内部缺陷检测精度要求,选择双面覆铜的微波pcb板材,依据选定板材的介电参数,在三维电磁仿真软件hfss中进行csr检测单元设计;
11.在csr检测单元设计过程中,首先,利用三维电磁仿真软件hfss进行基片集成波导谐振腔设计,依据选定pcb板材的介电参数和板材厚度,在pcb板材上设计出基片集成波导谐振腔;接着,在基片集成波导谐振腔上表面的中心位置,利用三维电磁仿真软件hfss设计出满足检测指标要求的csr电磁结构,该csr电磁结构为分布在基片集成波导谐振腔上表面的六条螺旋缝隙结构;基片集成波导谐振腔一端连接微带线,微带线的另一侧为sma连接头,便于和矢量网络分析仪连接;
12.步骤3:为了便于测试以及减小低频激励线圈对csr检测单元的电磁干扰,将低频激励线圈和csr检测单元分别放置在金属焊接板的上下表面;
13.步骤4:在金属焊接板无缺陷位置处,调整低频激励线圈、csr检测单元和焊接金属
板的最佳垂直距离,使得csr电磁结构的谐振频率峰值达到最大;
14.步骤5:将低频激励线圈固定,在平行于焊接金属板的平面移动csr检测单元,当发现csr电磁结构谐振峰出现明显的频偏,表明检测位置处焊接金属板内部出现了缺陷。
15.本发明采用涡流辅助微波无损检测技术;将涡流引入金属焊接板内部缺陷的检测,克服了微波无损检测过程中,由于趋肤深度的影响,微波只能检测金属焊接板表面的缺陷,而很难对金属焊接板深处的缺陷结构进行无损检测。和现有技术相比较,本发明具有如下优点:
16.1)结构简单,成本低廉。本发明的涡流辅助微波无损检测方法,测试结构简单,制造成本低廉。
17.2)通过在测试件内部产生涡流,可以对测试内部的缺陷进行检测,大大拓展了微波无损检测的使用范围;
18.3)检测精度高。通过模拟和实验测试,结果表明。涡流辅助csr检测结构检测焊接金属板内部缺陷,其谐振频率会出现10mhz的偏差。
19.实现焊缝无损检测。该检测方式在检测过程中,会和金属保持安全距离,不会对金属材料产生新的缺陷。
附图说明
20.图1为csr检测单元示意图。
21.图2为csr电磁结构示意图。
具体实施方式
22.下面结合附图和具体实施方式对本发明作进一步详细说明。
23.本发明一种涡流辅助焊接金属板内部缺陷微波无损检测方法,步骤如下:
24.步骤1:根据测试要求,选择低频激励线圈,并且选择适配的激励频率,使激励频率能够在焊接金属板在深度大于2mm的区域产生恒定的涡流;
25.步骤2:进行csr检测单元设计,具体如下:
26.根据焊接金属板内部缺陷检测精度要求,选择双面覆铜的微波pcb板材,依据选定板材的介电参数,在三维电磁仿真软件hfss中进行csr检测单元设计;
27.在csr检测单元设计过程中,首先,利用ansoft公司的三维电磁仿真软件hfss(high frequency structure simulator,hfss)进行基片集成波导谐振腔设计。依据选定pcb板材的介电参数和板材厚度,如图1所示,在pcb板材上设计出长15mm、宽14.5mm、高1.27mm的基片集成波导谐振腔。接着,在基片集成波导谐振腔上表面的中心位置,利用三维电磁仿真软件hfss设计出满足检测指标要求的csr电磁结构,该csr电磁结构如图2所示,其核心辐射单元为分布在基片集成波导谐振腔上表面的六条螺旋缝隙结构。csr电磁结构中,螺旋缝隙宽度s为0.16mm、缝隙间距g为0.18mm、螺旋缝隙结构外径r为2.67mm;基片集成波导谐振腔一端连接阻抗为50欧姆的微带线,微带线宽度w为1.5mm,微带线的另一侧为sma连接头,便于和矢量网络分析仪连接。
28.步骤3:为了便于测试以及减小低频激励线圈对csr检测单元的电磁干扰,将低频激励线圈和csr检测单元分别放置在金属焊接板的上下表面;
29.步骤4:在金属焊接板无缺陷位置处,调整低频激励线圈、csr检测单元和焊接金属板的最佳垂直距离,使得csr电磁结构的谐振频率峰值达到最大;
30.步骤5:将低频激励线圈固定,在平行于焊接金属板的平面移动csr检测单元,当发现csr电磁结构谐振峰出现明显的频偏,表明检测位置处焊接金属板内部出现了缺陷。
技术特征:1.一种涡流辅助焊接金属板内部缺陷微波无损检测方法,其特征在于:步骤如下:步骤1:根据测试要求,选择低频激励线圈,并且选择适配的激励频率,使激励频率能够在焊接金属板在深度大于2mm的区域产生恒定的涡流;步骤2:进行csr检测单元设计,具体如下:根据焊接金属板内部缺陷检测精度要求,选择双面覆铜的微波pcb板材,依据选定板材的介电参数,在三维电磁仿真软件hfss中进行csr检测单元设计;在csr检测单元设计过程中,首先,利用三维电磁仿真软件hfss进行基片集成波导谐振腔设计,依据选定pcb板材的介电参数和板材厚度,在pcb板材上设计出基片集成波导谐振腔;接着,在基片集成波导谐振腔上表面的中心位置,利用三维电磁仿真软件hfss设计出满足检测指标要求的csr电磁结构,该csr电磁结构为分布在基片集成波导谐振腔上表面的六条螺旋缝隙结构;基片集成波导谐振腔一端连接微带线,微带线的另一侧为sma连接头,便于和矢量网络分析仪连接;步骤3:为了便于测试以及减小低频激励线圈对csr检测单元的电磁干扰,将低频激励线圈和csr检测单元分别放置在金属焊接板的上下表面;步骤4:在金属焊接板无缺陷位置处,调整低频激励线圈、csr检测单元和焊接金属板的最佳垂直距离,使得csr电磁结构的谐振频率峰值达到最大;步骤5:将低频激励线圈固定,在平行于焊接金属板的平面移动csr检测单元,当发现csr电磁结构谐振峰出现明显的频偏,表明检测位置处焊接金属板内部出现了缺陷。2.根据权利要求1所述的一种涡流辅助焊接金属板内部缺陷微波无损检测方法,其特征在于:在pcb板材上设计出长15mm、宽14.5mm、高1.27mm的基片集成波导谐振腔。3.根据权利要求1所述的一种涡流辅助焊接金属板内部缺陷微波无损检测方法,其特征在于:csr电磁结构中,螺旋缝隙宽度s为0.16mm、缝隙间距g为0.18mm、螺旋缝隙结构外径r为2.67mm。4.根据权利要求1所述的一种涡流辅助焊接金属板内部缺陷微波无损检测方法,其特征在于:微带线宽度w为1.5mm。
技术总结本发明公开了一种涡流辅助焊接金属板内部缺陷微波无损检测方法,1、选择低频激励线圈,并且选择适配的激励频率;2、进行CSR检测单元设计;3、将低频激励线圈和CSR检测单元分别放置在金属焊接板的上下表面;4、在金属焊接板无缺陷位置处,调整低频激励线圈、CSR检测单元和焊接金属板的最佳垂直距离,使得CSR电磁结构的谐振频率峰值达到最大;5、将低频激励线圈固定,在平行于焊接金属板的平面移动CSR检测单元,当发现CSR电磁结构谐振峰出现明显的频偏,表明检测位置处焊接金属板内部出现了缺陷。通过涡流辅助方法,利用CSR电磁检测单元感知焊接金属板不同位置涡流电磁场的异同,精确定位焊接金属板深处的缺陷结构。定位焊接金属板深处的缺陷结构。定位焊接金属板深处的缺陷结构。
技术研发人员:李勇 刘福广 杨二娟 米紫昊 王艳松 杨兰 刘刚 韩天鹏 王博
受保护的技术使用者:西安热工研究院有限公司
技术研发日:2021.12.31
技术公布日:2022/4/1