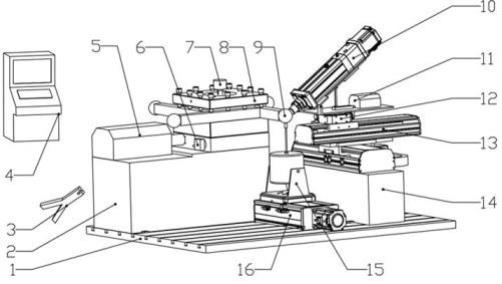
1.本发明属于数控车床制造和工业自动化控制领域的一种试验装置,更确切的说,本发明涉及一种四方刀架的可靠性试验装置及试验方法。
背景技术:2.随着近几年制造业的蓬勃发展,我国已经成为数控机床生产及应用的大国。目前,我国已经在数控机床的重要核心技术研究方面取得了重大突破,实现了一些具有自主知识产权的科技成果与核心技术。但与发达国家相比,我国的数控机床企业所生产的产品质量不高、产品的可靠性较低、机床的加工精度和效率较低。这些问题事实上已经成为数控机床产业发展的一大瓶颈。造成国产数控机床可靠性水平偏低的主要原因之一就是国产数控机床关键功能性部件的可靠性水平较低,因此对于数控机床的关键性功能部件开发相应的可靠性试验装置和试验技术对于提高国产数控机床可靠性具有重大意义。回转式刀架作为数控机床中最常用的关键功能部件之一,其可靠性的高低直接影响数控机床加工的精度、稳定度和加工质量。提高其自身的可靠性对于提高整机的可靠性水平有着重要影响。
3.目前我国数控机床关键功能部件可靠性试验起步较晚,目前刀架的试验台可以对刀架进行空转试验、偏重试验,或者采用液压缸对模拟刀具进行模拟静态。动态切削力的加载试验。但是位姿调节机构比较沉重、调节位置有偏差、且切削力加载精度与切削力加载频率受限。
技术实现要素:4.本发明的目的是为克服目前国内没有具备模拟数控机床四方刀架真实工况加载功能的可靠性试验装置和可靠性试验方法的问题,提供了一种电动缸与激振器混合加载的四方刀架可靠性试验装置及试验方法。
5.四方刀架可靠性试验装置,其特征在于:地平铁1、四方刀架系统、切削力自动加载部分、切削振动加载部分,它们固定在地平铁1上;所述的切削力自动加载部分包括:所述的切削力自动加载部分包括:电动缸10、倾角调节机构11、自动转台12和两轴滑台13,从上至下依次连接;两轴滑台13固定在地平铁1上;所述的切削力自动加载部分还包括:模拟刀杆9,其一端装卡在四方刀架系统的四方刀架8刀盘上, 其另一端为球体;所述的电动缸10为直连式伺服电动缸,包括:切削力加载杆1001、压力传感器1002、电动缸前端面1003,电动缸电机1004;所述的压力传感器1002前部固定连接切削力加载杆1001上,电动缸电机1004驱动丝杆转动,带动切削力加载杆1001移动;所述的倾角调节机构11包括:支撑底板1101,电动缸底座1102,铰支座1103,倾角传感器1104,支杆1105,丝杠滑块1106,伺服电机1107,丝杠1108,丝杠底座1109;
所述的电动缸底座1102的前端与支撑底板1101的前端铰接,其中部下方固定安装铰支座1103,铰支座1103与支杆1105铰接,丝杠滑块1106与支杆1105铰接,丝杠底座1109、伺服电机1107固定在支撑底板1101上,伺服电机1107转动带动丝杠转动,使得丝杠滑块1106进行位移,带动支杆1105移动;所述的倾角传感器1104设在后部下方;所述的电动缸10的电动缸前端面1003固定电动缸底座1102上;所述的自动转台22包括:转台底座1201、蜗轮1202、蜗杆轴承1203、蜗杆1204、蜗杆架盖板1205、旋转台面1206、转台伺服电机1207和转角传感器1208;转台伺服电机1207带动蜗杆1204转动,蜗杆1204带动相啮合的蜗轮1202转动,转角传感器1208设在蜗轮1202顶部;所述的两轴滑台13包括:x方向伺服电机1301、x方向滑块1302、y方向伺服电机1303和y方向滑块1304;所述的为y方向滑块1304为一t形结构件,底部与y方向伺服电机1303相连接,工作时由y方向伺服电机1303驱动 y方向滑块1304沿y轴方向进行移动,y方向滑块1304的顶部两侧设有螺纹孔与上方的自动转台12相连接,y方向伺服电机1303的底部与x方向滑块1302相连接,x方向滑块1302底部与x方向伺服电机1301相连接,工作时由x方向伺服电机1301驱动 x方向滑块1302沿x轴方向进行移动;x方向伺服电机1301的底部固定地平铁1上;转台底座1201固定在y方向滑块1304上;所述的切削振动加载部分包括:振动加载支撑装置16和切削振动加载装置15;切削振动加载装置15固定在振动加载支撑装置16上,振动加载支撑装置16固定在地平铁1上;所述的切削振动加载装置15包括:激振器底座1501、激振器主体1502、顶杆1503、加速度传感器1504;激振器底座1501为三块钢板所连接而成的结构件,两侧钢板上设有孔,通过孔连接激振器主体1502的两侧;顶杆1503在激振器主体1502的顶端,加速度传感器1504设在顶杆1503的顶部;所述的切削振动加载支撑装置包括:滑台导轨1601、滑块1602、激振器垫板1603、滑台伺服电机1604组成。
6.所述的滑块1602顶端开有螺栓孔,与激振器垫板1603相连接,滑块底部安装在滑台导轨1601上,由滑台伺服电机1604驱动滑块1602在滑台导轨1601上移动;激振器底座1501固定在激振器垫板1603上;所述的激振器垫板1603为一弹性材料板。
7.所述的四方刀架系统包括:四方刀架底座2、四方刀架8、刀架伺服电机5、振动传感器6、角度编码器7。
8.所述的四方刀架8为立式刀架,刀架伺服电机5为三相力矩电动机,振动传感器6为三轴向加速度传感器设在四方刀架8上;角度编码器7为电压输出角度传感器,安装在四方刀架8的主轴上;所述的四方刀架可靠性试验装置还设有电流钳和控制台4;所述的电流钳3为交直流钳,探头类型是交直流电流探头,当模拟真实工况时,四
方刀架伺服电机的电流情况通过电流钳3来检测,电流为三相交流电,有u、v、x三个相位,用三个电流钳分别对三相电流进行监测和信号采集;所述的控制台4包括:计算机、数据采集卡、可编程控制器;可编程控制器与倾角传感器、转角传感器、各个伺服电机电机相连;数据采集卡与电流钳、振动传感器、角度编码器相连接;数据采集卡、可编程控制器分别与计算机主板相连接;计算机安装了数据处理程序,它包括:第一部分为试验前设定的四方刀架试验程序和试验时切削力自动加载装置及切削振动自动加载装置的运动程序,第二部分为对整个试验过程中所采集到的数据进行记录和整理,第三部分为试验结束后统计四方刀架可靠性试验系统在不同负载情况下的振动情况、转角精度与刀架伺服电机的电流变化情况。
9.本发明又一个目的是提供了四方刀架可靠性试验装置的试验方法。
10.四方刀架可靠性试验装置的试验方法,它包括:(1)测试前准备:将模拟刀杆安装到四方刀架刀盘合适位置,将电流钳、振动传感器和角度编码器安装在四方刀架适当位置及刀架伺服电机导线处,在控制台输入待测的切削力加载位姿信息、模拟切削力大小及模拟切削振动频率,设置完成后,则开始做相关测试;(2)四方刀架多模式空转运行功能试验:对四方刀架的空转运行功能试验,四方刀架的空转运行时间为72h,转位换刀频率为12次/分,在四方刀架空转功能试验过程中,保证四方刀架样机自动的、连续的、随机的就近选刀,并检测四方刀架振动信号、转位精度及刀架伺服电机的电流信号;(3)四方刀架切削功能试验:将模拟刀杆安装在四方刀架的刀盘上,模拟刀杆的悬伸长度符合四方刀架实际使用情况,通过控制台控制切削力加载装置及切削力位姿调节装置对模拟刀杆进行切削力加载,通过控制台控制切削振动加载装置对模拟刀杆进行切削振动加载,四方刀架的运行时间为72h,转位换刀频率为12次/分,在四方刀架切削试验运行过程中,保证四方刀架样机自动的、连续的、随机的就近选刀,并检测四方刀架振动信号、转位精度及刀架伺服电机的电流信号。
11.本发明提供了四方刀架可靠性试验装置及试验方法,它括:地平铁、四方刀架系统、切削力自动加载部分、切削振动加载部分,它们固定在地平铁上;所述的切削力自动加载部分包括:所述的切削力自动加载部分包括:电动缸、倾角调节机构、自动转台和两轴滑台,从上至下依次连接;两轴滑台固定在地平铁上;所述的切削力自动加载部分还包括:模拟刀杆,其一端装卡在四方刀架系统的四方刀架刀盘上,其另一端为球体;所述的切削振动加载部分包括:振动加载支撑装置和切削振动加载装置;还设有电流钳、可编程控制器、倾角传感器、转角传感器、计算机和数据采集卡。进行模拟真实工况的可靠性试验,暴露和激发产品故障,提供丰富且实用的数据。
12.本发明用于四方刀架可靠性检测。与现有技术相比本发明的有益效果是:(1)本发明所述的采用的电动缸与激振器混合加载的四方刀架可靠性试验装置对四方刀架的可靠性及精度保持性进行试验和检测。通过对被测的采用刀架伺服电机驱动的四方刀架进行模拟真实工况的可靠性试验,暴露和激发产品故障,为产品的可靠性增长和评估提供丰富且实用的数据;
(2)本发明所述的采用电动缸与激振器混合加载的四方刀架可靠性试验装置采用电动缸和激振器对四方刀架所加持的模拟刀杆进行动、静态加载,从而模拟出四方刀架在实际生产加工过程中所承受的载荷。本发明所采用的电动缸和激振器均与控制台形成闭环控制,使得其加载具有较高的加载精度;(3)发明所述的采用电动缸与激振器混合加载的四方刀架可靠性试验装置中采用的激振器对四方刀架进行振动加载,相较于传统液压缸加载,振动频率的可选范围更多,输出数值更稳定,更能模拟四方刀架在真实切削加工过程中所受到的振动;(4)本发明所述的采用电动缸与激振器混合加载的四方刀架可靠性试验装置具有自动检测系统,通过在四方刀架上安装角度编码器和加速度传感器,在刀架伺服电机的导线上安装电流钳。可以实时监测并记录四方刀架在模拟真实工况下的相关精度数据,同时在出现精度失效或达到临界阈值时由控制台自动记录失效数据。
附图说明
13.下面结合附图对本发明作进一步的说明:图1为本本发明所述的采用电动缸与激振器混合加载的四方刀架可靠性试验装置对模拟刀杆加载状态的轴测投影图;图2为本发明所述的采用电动缸与激振器混合加载的四方刀架可靠性试验装置中切削力加载装置的电动缸的轴测投影图;图3为本发明所述的采用电动缸与激振器混合加载的四方刀架可靠性试验装置中切削力加载装置的倾角控制部分的轴测投影图;图4为本发明所述的用电动缸与激振器混合加载的四方刀架可靠性试验装置中切削力加载装置的自动转台爆炸分解的轴测投影图;图5为本发明所述的用电动缸与激振器混合加载的四方刀架可靠性试验装置中切削力加载装置的两轴滑台的轴测投影图;图6为本发明所述的采用电动缸与激振器混合加载的四方刀架可靠性试验装置中切削振动加载装置中激振器的轴测投影图;图7为本发明所述的采用电动缸与激振器混合加载的四方刀架可靠性试验装置中切削振动加载装置中支撑装置的轴侧投影图;图8为本发明提供的四方刀架可靠性试验方法的流程框图;图中:1.地平铁,2.四方刀架支撑座,3.电流钳,4.控制台,5.刀架伺服电机,6.振动传感器,7.角度编码器,8四方刀架,9.模拟刀杆,901.1号模拟刀杆,902.2号模拟刀杆,903.3号模拟刀杆,904.4号模拟刀杆,10.电动缸,1001.切削力加载杆,1002.压力传感器,1003.电动缸前端面,1004.电动缸电机,11.倾角调节机构,1101.支撑底板,1102.电动缸底座,1103.铰支座,1104.倾角传感器,1105支杆,1106.丝杠滑块,1107.伺服电机,1108.丝杠,1109.丝杠底座,12.自动转台,1201转台底座,1202.蜗轮,1203蜗杆轴承,1204.蜗杆,1205.蜗杆架盖板,1206.旋转台面,1207.转台伺服电机,1208.转角传感器,13.两轴滑台,1301.x方向伺服电机,1302.x方向滑块,1303.y方向伺服电机,1304.y方向滑块,14.切削力加载装置底座,15.切削振动加载装置,1501.激振器底座,1502激振器主体,1503.顶杆,1504.加速度传感器,16.振动加载支撑装置,1601.滑台导轨,1602.滑块,1603.激振器垫
板,1604.滑台伺服电机。
具体实施方式
14.下面结合附图对本发明作详细的描述:本发明是模拟四方刀架在实际运行中的不同工况,在受到不同切削力与切削振动的情况下,得到四方刀架的切削工作数据及精度可靠性数据,同时提出一套完整的四方刀架可靠性试验方法。
15.本发明所述的四方刀架可靠性试验装置及试验方法主要由两大部分组成,即四方刀架的可靠性试验装置和四方刀架的可靠性试验方法。
16.四方刀架可靠性试验装置参阅图1,本发明所述的采用四方刀架可靠性试验装置包括辅助系统、四方刀架系统、切削力自动加载部分、切削振动加载部分及数据检测系统。
17.一、辅助系统所述的辅助系统包括地平铁1、四方刀架底座2与切削力加载装置支撑底座14。
18.所述的地平铁1为一长方体形的板式铸造件,通过其中的底座平台安装在地基上,地平铁1的顶端设置有相互平行的结构相同的燕尾槽。所述的四方刀架底座2为箱体式结构件,由七块钢板焊接而成,两顶端面与底端面相互平行,第一顶端面与第二顶端面存在适当距离,便于安置伺服电机5与四方刀架8。顶板的四角处设置有用于安装四方刀架的螺纹通孔,底板的四角处设置有u型块,用于穿过螺栓将四方刀架底座2固定在地平铁1上。所述的切削力加载装置支撑底座14同为箱体式结构件,由六块钢板焊接而成,顶端面与底端面相互平行,顶板的四角处设置有用于安装双轴滑台的螺纹通孔,底板的四角处设置有u型块,用于穿过螺栓将切削力加载装置支撑底座14固定在地平铁1上。
19.二、四方刀架系统所述的四方刀架系统包括四方刀架8与刀架伺服电机5。
20.参阅图1,所述的四方刀架8为ldb4系列立式刀架,型号为ldb4-120,换刀时间:90
°
为2.7s、180
°
为3.4s、270
°
为4.1s,最大的许用力矩:mq为700nm、ms为600nm、mx为1800nm,重复定位精度《0.005mm。
21.参阅图1,所述的刀架伺服电机5为三相力矩电动机,型号为yxj83/60-120w-4p,功率为120w,频率50hz,转速1400r/min。
22.三、切削力自动加载部分所述的切削力自动加载部分包括模拟刀杆9、电动缸10,倾角调节机构11,自动转台12,两轴滑台13。
23.1.模拟刀杆9模拟刀杆9是在横截面为正方形或矩形的长方体形的杆件结构,模拟刀杆9的一端部和一个球体连接成一体。模拟刀杆9装卡在被测四方刀架8的刀盘上,代替刀具对其进行可靠性试验。
24.2.电动缸10参阅图2,所述的电动缸10由切削力加载杆1001,压力传感器1002,电动缸前端面1003,电动缸电机1104组成。
25.所述的电动缸10选用直连式伺服电动缸,额定输出力2.55kn、最大输出力3.82kn,丝杠导程为100mm,丝杆从电动缸10的前端伸出,电动缸前端面1003通过两根螺栓与电动缸底座1102相连接,丝杠前部装有压力传感器1002,压力传感器1002前部固定连接切削力加载杆1001,工作时由电动缸后部的电动缸电机1004驱动丝杆转动,带动切削力加载杆1001移动,当切削力加载杆1001到达模拟刀杆9前端的球状体时,电动缸电机1004继续驱动丝杠,逐渐增加对模拟刀杆9的压力,该压力可以通过压力传感器1002测量并实时反馈到控制台4,当电动缸1004施加的压力到达预设值后,控制台控制步进电机停止转动并保持丝杠在当前位置,以此模拟真实工况下四方刀架所受到的切削力。
26.3.倾角调节机构11参阅图3,所述的切削力自动加载支撑装置由支撑底板1101,电动缸底座1102,铰支座1103,倾角传感器1104,支杆1105,丝杠滑块1106,伺服电机1107,丝杠1108,丝杠底座1109组成。
27.所述的倾角传感器1104是北京齐开科技开发的一款高精度、低温漂、数显倾角传感器,属于qkqhb-oled系列,该系列产品采用最新mems机电生产工艺制备倾角测量核心部件,测量出传感器相对于水平面一维、二维的倾斜角度,采用高质量和可靠性的mems加速度计,采用最优算法保证测量精度,同时进行温度补偿,使传感器拥有出色的测量精度和极低的温度漂移量,该倾角传感器待机功耗为0.22ma,工作电流单轴48 ma、双轴55ma,可连续工作24小时以上,在
±
10
°
内精度高达0.003
°
,传感器11044通过螺栓固定在电动缸底座1102底部适当位置处,选择该倾角传感器1104与控制台4一起对切削力加载装置进行闭环控制电动缸的切削力加载角度。
28.所述电动缸底座1102为一长条形(横截面为矩形)板类结构件,顶部两侧有适当长度的圆柱与该板焊接,底部适当位置焊接有链接铰支座1103。支撑底板1011同为长条形(横截面为矩形)板类结构件,顶部处有两根立柱与底板焊接,立柱上设置两开孔与电动缸底座1102顶部所焊接的适当长度的圆柱形成间隙配合。支杆1105为一长条形杆类结构件,其顶端与电动缸底座1102底部所焊接的链接铰支座相铰接,底端与丝杠滑块1106相铰接,丝杠1108与丝杠滑块1106相互配合,丝杠滑块1106固定在丝杠底座109上,丝杠1108与伺服电机1107通过联轴器相互连接,伺服电机1107转动带动丝杠转动,使得丝杠滑块进行位移,带动支杆1105按相应轨迹移动,支杆1105顶端通过与电动缸底座1102底部所焊接的链接铰支座1103相铰接带动电动缸底座1102转动到合适的角度。该机构通过倾角传感器1104与控制台4起对切削力加载装置进行闭环控制电动缸的切削力加载角度。
29.4.自动转台12参阅图4,所述的自动转台12由转台底座1201,蜗轮1202,蜗杆轴承1203,蜗杆1204,蜗杆架盖板1205,旋转台面1206,转台伺服电机1207,转角传感器1208组成。
30.所述的转台底座1201为一盒类结构件,底部设有4个螺栓孔和自动转台下方的两轴滑台13相连接,蜗杆1204安装于转台底座1201的前部的开孔内,蜗杆轴承1203.1、蜗杆轴承1203.2安装于蜗杆1204的两侧,置于转台底座的前部开孔内,蜗杆1204的一端通过联轴器与转台伺服电机1207相连接,蜗轮1202置于转台底座1201内,并与蜗杆1204相啮合,蜗轮1202的上部安装有转角传感器1208,转角传感器顶端安装旋转台面1206,旋转台面1206顶面设有螺栓孔与上方的倾角调节装置11中的支撑底板1101相连接,蜗杆架盖板1205位于蜗
杆1204上方,转台伺服电机1207和转角传感器1208通过导线与控制台4相连接,在试验过程中通过控制台4控制转台伺服电机1207工作,转台伺服电机1207带动蜗杆1204转动,蜗杆1204带动相啮合的蜗轮1202转动,当蜗轮1202顶部的转角传感器1208达到设定角度时,即自动转台达到对应角度时,控制台4控制转台伺服电机1207停止,即自动转台12达到设定角度。
31.5.两轴滑台13参阅图5,所述的两轴滑台由x方向伺服电机1301、x方向滑块1302、y方向伺服电机1303、y方向滑块1304组成。
32.所述的为y方向滑块1304为一t形结构件,底部与y方向伺服电机1303相连接,工作时由y方向伺服电机1303驱动 y方向滑块1304沿y轴方向进行移动,y方向滑块1304的顶部两侧设有螺纹孔与上方的自动转台12相连接,y方向伺服电机1303的底部与x方向滑块1302相连接,x方向滑块1302底部与x方向伺服电机1301相连接,工作时由x方向伺服电机1301驱动 x方向滑块1302沿x轴方向进行移动,x方向伺服电机1301与y方向伺服电机1303均由控制台4进行控制住,工作时,由控制台4发出位移指令,伺服电机驱动滑台进行位移,当移动到合适位置时停止,即两轴转台达到设定位置。
33.四、切削振动加载部分所述的切削振动加载部分由振动加载支撑装置16和切削振动加载装置15组成。
34.1、切削振动加载装置15参阅图6,所述的切削振动加载装置15由激振器底座1501、激振器主体1502、顶杆1503、加速度传感器1504组成。
35.所述的激振器底座1501为三块钢板所连接而成的结构件,底部钢板在四角设置有螺栓孔,下连接激振器垫板1603,激振器垫板1603为一弹性材料板,其作用是工作中对激振器振动进行隔离,确保激振器在工作时振动不向外界传递,激振器底座1501的两侧钢板上设有孔,通过孔可以连接激振器主体1502。在激振器主体1502的顶端连接由顶杆1503,在顶杆1503的顶部装有加速度传感器1504,加速度传感器1504用以检测切削振动加载装置15在工作状态时对模拟刀杆9所施加的振动频率。
36.所述的激振器主体1502内部由上下两组弹簧片支撑一个可驱动线圈,使得驱动线圈处于由铁芯、磁极、壳体和永磁磁钢所组成的磁路的磁隙中,当功率放大器供给动圈可变频率电流时,驱动线圈讲受到点动力的作用,继而带动顶杆1503振动,再通过加速度传感器1504将振动传递到模拟刀杆9顶端的球状体上,以此来达到模拟四方刀架在真实工况中刀杆受到的切削振动。
37.2、振动加载支撑装置16参阅图7,所述的切削振动加载支撑装置由滑台导轨1601、滑块1602、激振器垫板1603、滑台伺服电机1604组成。
38.所述的滑块1602顶端四角开有螺栓孔,与激振器垫板1603相连接,滑块底部安装在滑台导轨1601上,由滑台伺服电机1604驱动滑块1602在滑台导轨1601上移动,滑台伺服电机1604由控制台4控制,当滑块1602达到预定位置后,控制台4控制滑台伺服电机1604停止,即达到工作位置。
39.五、数据检测系统
所述的数据检测系统由电流钳3、控制台4、振动传感器6、角度编码器7组成。
40.所述的电流钳3为交直流钳,探头类型是交直流电流探头,当模拟真实工况时,四方刀架伺服电机的电流情况通过电流钳3来检测,电流为三相交流电,有u、v、x三个相位,用三个电流钳分别对三相电流进行监测和信号采集,采集刀架伺服电机5的电流数据并记录到控制台4。
41.所述的振动传感器6为三轴向加速度传感器,型号为ult2011,该传感器可以对x、y、z三轴向的加速度信号进行测量和输出,带磁吸底座,可以直接吸附在四方刀架8上指定位置上采集振动信号,当四方刀架8工作时,采集刀架振动数据并记录到控制台4。
42.所述的角度编码器7电压输出角度传感器,属于qkj-v05系列,该传感器使用霍尔敏感元件、非接触式测量转轴的角度位置传感器,满量程角度测量范围为0
°
至359.9
°
,将角度编码器7安装在四方刀架8的主轴上,当四方刀架转动换刀时。采集转角数据并记录到控制台4。
43.参阅图1,所述的控制台4放置在地平铁1的左前方,所述的控制台4包括:显示器、键盘鼠标、计算机、数据采集卡、可编程控制器、多芯插头;所述的计算机是数据检测系统的核心,安装在控制台4下部的箱体内部,键盘鼠标、显示器、可编程控制器、数据采集卡分别与安装有数据处理程序的计算机相连接。
44.所述的键盘鼠标安装在操作台伸出部分的上端面,其导线连接在控制台4箱体内计算机的usb接口处,所述的显示器为液晶显示器,安装在控制台4上部端面上,显示器通过hdmi线连接在计算机的显示器接口处。
45.所述的数据采集卡为smacq品牌的usb-5000系列数据采集卡,采样率高,通道数满足试验要求,数据采集卡安装在计算机内部,连接在计算机的主板卡槽内,数据采集卡的信号通道采集接口依次与电流钳、振动传感器、角度编码器相连接,分别采集刀架伺服电机在工作状态下的电流与四方刀架在工作状态下的转位角度和振动信号。
46.所述的可编程控制器采用easy modicon m200系列的可控编程控制器,安装在计算机的内部,用导线连接到计算机的usb接口处,上述的切削力自动加载装置中的倾角传感器、丝杠伺服电机、转角传感器、转盘伺服电机、x方向伺服电机、y方向伺服电机、滑台伺服电机均与可编程控制器相连接,工作时,通过鼠标键盘输入所要模拟真实工况时切削力及切削振动加载的位姿状态数据到可控编程控制器,再由可编程控制器控制切削力自动加载装置及切削振动自动加载装置自动调节到对应位置。
47.所述的数据处理程序为预装到计算机中的,数据处理程序包括三部分,第一部分为试验前设定的四方刀架试验程序和试验时切削力自动加载装置及切削振动自动加载装置的运动程序,第二部分为对整个试验过程中所采集到的传感器数据进行记录和整理,第三部分为试验结束后统计分析四方刀架可靠性试验系统在不同负载情况下的振动情况、转角精度与刀架伺服电机的电流变化情况。
48.实施例2四方刀架可靠性试验装置的试验方法本发明所述的四方刀架可靠性试验方法是在采用前面所述的四方刀架可靠性试验装置基础上进行的方法,针对被测四方刀架提出了一套可靠性试验方法。
49.(1)测试前准备:将模拟刀杆安装到四方刀架刀盘合适位置,将测量装置安装在四方刀架适当位置及刀架伺服电机导线处,在控制台输入待测的切削力加载位姿信息、模拟
切削力大小及模拟切削振动频率,设置完成后,则开始做相关测试。
50.(2)四方刀架多模式空转运行功能试验:对四方刀架的空转运行功能试验,四方刀架的空转运行时间为72h,转位换刀频率为12次/分,在四方刀架空转功能试验过程中,保证四方刀架样机自动的、连续的、随机的就近选刀,并检测四方刀架振动信号、转位精度及刀架伺服电机的电流信号,以便及时发现四方刀架暴露出的故障。
51.(3)四方刀架切削功能试验:将模拟刀杆安装在四方刀架的刀盘上,模拟刀杆的悬伸长度符合四方刀架实际使用情况,通过控制台控制切削力加载装置及切削力位姿调节装置对模拟刀杆进行切削力加载,通过控制台控制切削振动加载装置对模拟刀杆进行切削振动加载,四方刀架的运行时间为72h,转位换刀频率为12次/分,在四方刀架切削试验运行过程中,保证四方刀架样机自动的、连续的、随机的就近选刀,并检测四方刀架振动信号、转位精度及刀架伺服电机的电流信号,以便及时发现四方刀架暴露出的故障。
52.上述四方刀架可靠性试验装置,通过切削力加载装置和切削振动加载装置模拟真实工况;检测系统获得四方刀架待检测部位的精度信息,并通过传输模块传输至控制台经过处理得到四方刀架的转位精度、振动信号数据及刀架伺服电机的电流信号数据;因此,上述四方刀架可靠性试验装置能实现对四方刀架真实工况下的转位精度,振动及电流信号进行检测。计算机处理后的数据可被读取、记录并分析,从而对四方刀架的可靠性综合性能进行评估。因此,与空载试验装置相比,本发明基于真实工况下的试验技术,试验数据更加真实丰富;并且与传统的基于液压缸的检测装置相比,本发明能更好地模拟真实切削振动并可以实现自动检测四方刀架的多方面性能指标。与二者相比,本发明可实现低成本的四方刀架的可靠性全面检测。
53.本发明中所述的实施例是为了便于该领域技术人员能够理解和应用本发明,本发明只是一种优化的实例,或者说是一种较佳的具体技术方案。如果相关的技术人员在坚持本发明基本技术方案的情况下,做出不需要经过创造性劳动的等效结构变化或各种修改都在本发明的保护范围内。