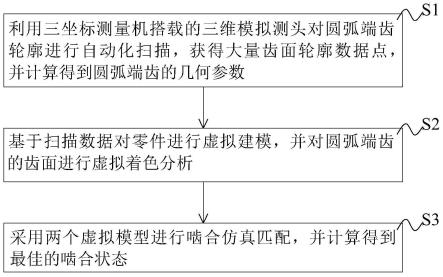
1.本发明涉及圆弧端齿测量技术领域,特别地,涉及一种圆弧端齿的数字化测量方法。
背景技术:2.圆弧端齿主要用于现代小型发动机高速旋转的叶片盘、转子、叶轮等部件连接,通过圆弧端齿把压气机、涡轮等各个转动部件连接起来。圆弧端齿是航空涡轴类发动机的涡轮盘、叶片盘核心结构,其设计为凸凹齿成对配合使用,精度要求非常高,在工作中承受较大载荷和扭矩,需要具备足够大的强度、表面积和支撑,并且有非常高的互换性要求。圆弧端齿参数的测量是航空发动机研制和生产过程中的一项关键重要检测要素,对于保证该机型产品质量起着重要的作用。圆弧端齿在加工过程中涉及检测的主要几何要素有:端齿的齿形轮廓、齿距、跳动和接触面、齿槽与齿厚相等的齿顶高、端面跳动、径向跳动等参数,端其齿面质量及其相关尺寸形位公差的检测非常严格和重要。
3.现有的圆弧端齿检测方法通过校对检验量规对零件进行检测,采用标准规-校对规-工作规-零件的标准传递和着色检测方式,检测量规采用二维截面检测,检测过程和数据处理过程人工干预多,误差大,检测效率较低。而且,着色面积判断靠目视,无量化实测值,检测时着色剂、着色刷、着色工艺对着色质量的判定都有较大影响。另外,进行齿顶高检验时是采用深度千分尺进行的,存在人为误差,无法检测条件齿顶高参数(即齿槽宽度等于齿厚时的齿顶高度)。另外,在进行径向和轴向跳动检查时也是采用分度转台和千分表等通用量具进行径向和轴向跳动检测,存在人为误差,并且,最佳的匹配啮合位置只能通过“试错法”进行,效率较低。另外,现有的检测方法由于量规的尺寸有限,故而无法对较大形状规格的圆弧端齿零件进行端齿参数检测,也无法进行数据逆向建模。
技术实现要素:4.本发明提供了一种圆弧端齿的数字化测量方法,以解决现有的圆弧端齿检测方法存在的检测误差大、检测效率低的技术问题。
5.根据本发明的一个方面,提供一种圆弧端齿的数字化测量方法,包括以下内容:
6.利用三坐标测量机搭载的三维模拟测头对圆弧端齿轮廓进行自动化扫描,获得大量齿面轮廓数据点,并计算得到圆弧端齿的几何参数;
7.基于扫描数据对零件进行虚拟建模,并对圆弧端齿的齿面进行虚拟着色分析;
8.采用两个虚拟模型进行啮合仿真匹配,并计算得到最佳的啮合状态。
9.进一步地,所述利用三坐标测量机搭载的三维模拟测头对圆弧端齿轮廓进行自动化扫描,获得大量齿面轮廓数据点,并计算得到圆弧端齿的几何参数的过程具体为:
10.以圆弧端齿的端平面为基准建立笛卡尔坐标系;
11.设定圆弧端齿的理论参数,并配置好三坐标测量机的扫描参数;
12.三坐标测量机根据建立的坐标系和配置好的扫描参数生成齿面网格坐标点,并依
据齿面网格坐标点进行网格式扫描;
13.根据三坐标测量机的扫描点云数据得到圆弧端齿的几何参数。
14.进一步地,所述三坐标测量机分两次进行网格式扫描,第一次扫描测量是对每个齿的两个工作面进行网格扫描,得到圆弧端齿的齿面数据,第二次扫描测量是沿圆弧端齿的端面进行径向扫描,得到圆弧端齿的齿顶高原始数据。
15.进一步地,圆弧端齿的几何参数包括条件齿顶高,条件齿顶高的计算过程为:
16.利用第二次扫描得到的点数据进行测头三维半径补偿,得到圆弧端齿的表面点数据;
17.采用圆弧展开算法,基于笛卡尔坐标系和极坐标系之间的转换公式对每个圆弧端齿的表面点数据进行转换,并对极坐标系的横轴进行比例缩放,从而将三维圆弧转换为二维轮廓;
18.从二维轮廓中选择相邻的齿和槽来分段截取数据,找到齿槽宽度和齿厚相等时的齿顶高,从而得到每个齿的条件齿顶高。
19.进一步地,所述基于扫描数据对零件进行虚拟建模,并对圆弧端齿的齿面进行虚拟着色分析的过程包括以下内容:
20.利用圆弧端齿的几何参数进行虚拟建模;
21.基于圆弧端齿的齿面点数据进行测头三维半径补偿,得到圆弧端齿的齿面实测点数据;
22.计算每个齿面实测点在法向矢量方向上的投影长度,即每个齿面实测点的偏差值;
23.将每个齿面实测点的坐标值投影到xy平面上,并以偏差值作为z值,得到二维化的点偏差矩阵;
24.基于每个实测点的偏差值对点偏差矩阵进行虚拟着色,以二维绘图的形式进行展现。
25.进一步地,所述基于每个实测点的偏差值对点偏差矩阵进行虚拟着色,以二维绘图的形式进行展现的过程具体为:
26.设置偏差值的公差变量,针对不同的公差变量范围定义不同的颜色,将每个实测点的偏差值与公差变量范围进行比对以确定每个实测点的着色,并根据实测点的点数计算不同着色的百分比,将百分比以着色图进行显示。
27.进一步地,所述采用两个虚拟模型进行仿真匹配,并计算得到最佳的啮合状态的过程具体包括以下内容:
28.利用一个虚拟模型的一个凹齿与另一个虚拟模型的多个凸齿逐一进行啮合仿真,或者利用一个虚拟模型的一个凸齿与另一个虚拟模型的多个凹齿逐一进行啮合仿真,在每次啮合仿真时分别进行平行度仿真匹配和同轴度仿真匹配,并根据多次啮合仿真的平行度仿真匹配结果和同轴度仿真匹配结果得到最佳匹配状态对应的配对齿号。
29.进一步地,所述在每次啮合仿真时进行平行度仿真匹配的过程具体为:
30.每次啮合后,计算得到每对齿的齿顶高之和,并筛选出齿顶高之和的最大值和最小值,计算得到齿顶高之和最大值和齿顶高之和最小值之间的齿顶高之和偏差值,齿顶高之和偏差值越小,平行度越好。
31.进一步地,所述在每次啮合仿真时进行同轴度仿真匹配的过程具体为:
32.每次啮合后,计算得到两个零件的中心距偏差值,中心距偏差值越小,同轴度越好。
33.进一步地,所述根据多次啮合仿真的平行度仿真匹配结果和同轴度仿真匹配结果得到最佳匹配状态对应的配对齿号的过程具体为:
34.每次啮合仿真时计算得到齿顶高之和偏差值和中心距偏差值的平方和的二次方根值,基于多次啮合仿真的计算结果筛选出最小者,该最小者对应的啮合状态即为最佳啮合状态,并得到最佳拟合状态对应的凹齿配对齿号和凸齿配对齿号。
35.本发明具有以下效果:
36.本发明的圆弧端齿的数字化测量方法,采用超高精度的三坐标测量机作为圆弧端齿数字化检测采集设备,将长期以来依靠量规传递的圆弧端齿测量方法替代为基于坐标检测原理的自动化和数字化测量方法,实现了对于圆弧端齿的数字化检测。并且,基于扫描数据进行了零件虚拟建模,采用虚拟着色的方式对齿面进行着色分析,替代了人工目视识别,提高了检测效率,不再存在着色剂、着色刷、着色工艺等对着色质量的影响,可以准确地对齿面啮合质量进行判别,并且具有具体的量化实测值,为圆弧端齿的批量检测和加工参数优化提供了重要的理论依据。另外,通过两个虚拟模型进行啮合仿真匹配,可以计算得到最佳的啮合状态,替代了原有依靠人工逐齿配对试错的检测方法,在凹齿和凸齿的几何参数测量完成后即可自动计算出最佳啮合齿对,大大缩短了检测时间,为圆弧端齿零件的数字化装配奠定了基础。
37.除了上面所描述的目的、特征和优点之外,本发明还有其它的目的、特征和优点。下面将参照图,对本发明作进一步详细的说明。
附图说明
38.构成本技术的一部分的附图用来提供对本发明的进一步理解,本发明的示意性实施例及其说明用于解释本发明,并不构成对本发明的不当限定。在附图中:
39.图1是本发明优选实施例的圆弧端齿的数字化测量方法的流程示意图。
40.图2是图1中步骤s1的子流程示意图。
41.图3是图2中的步骤s14中计算条件齿顶高的流程示意图。
42.图4是本发明优选实施例中生成的圆弧端齿的条件齿顶高评价报告的示意图。
43.图5是图1中步骤s2的子流程示意图。
具体实施方式
44.以下结合附图对本发明的实施例进行详细说明,但是本发明可以由下述所限定和覆盖的多种不同方式实施。
45.如图1所示,本发明的优选实施例提供一种圆弧端齿的数字化测量方法,包括以下内容:
46.步骤s1:利用三坐标测量机搭载的三维模拟测头对圆弧端齿轮廓进行自动化扫描,获得大量齿面轮廓数据点,并计算得到圆弧端齿的几何参数;
47.步骤s2:基于扫描数据对零件进行虚拟建模,并对圆弧端齿的齿面进行虚拟着色
分析;
48.步骤s3:采用两个虚拟模型进行啮合仿真匹配,并计算得到最佳的啮合状态。
49.可以理解,本实施例的圆弧端齿的数字化测量方法,采用超高精度的三坐标测量机作为圆弧端齿数字化检测采集设备,将长期以来依靠量规传递的圆弧端齿测量方法替代为基于坐标检测原理的自动化和数字化测量方法,实现了对于圆弧端齿的数字化检测。并且,基于扫描数据进行了零件虚拟建模,采用虚拟着色的方式对齿面进行着色分析,替代了人工目视识别,提高了检测效率,不再存在着色剂、着色刷、着色工艺等对着色质量的影响,可以准确地对齿面啮合质量进行判别,并且具有具体的量化实测值,为圆弧端齿的批量检测和加工参数优化提供了重要的理论依据。另外,通过两个虚拟模型进行啮合仿真匹配,可以计算得到最佳的啮合状态,替代了原有依靠人工逐齿配对试错的检测方法,在凹齿和凸齿的几何参数测量完成后即可自动计算出最佳啮合齿对,大大缩短了检测时间,为圆弧端齿零件的数字化装配奠定了基础。
50.可以理解,如图2所示,所述步骤s1具体包括以下内容:
51.步骤s11:以圆弧端齿的端平面为基准建立笛卡尔坐标系;
52.步骤s12:设定圆弧端齿的理论参数,并配置好三坐标测量机的扫描参数;
53.步骤s13:三坐标测量机根据建立的坐标系和配置好的扫描参数生成齿面网格坐标点,并依据齿面网格坐标点进行网格式扫描;
54.步骤s14:根据三坐标测量机的扫描点云数据得到圆弧端齿的几何参数。
55.具体地,首先在三坐标测量机上建立坐标系,例如,以圆弧端齿的端平面为xy平面,以垂直端平面朝上为z轴正方向,以内圆中心和端面高度确定原点,以内圆中心与任意齿的齿面中分点的连线作为x轴线。当然,在本发明的其它实施例中,可以根据实际需要调整坐标系的位置。然后,设定圆弧端齿的理论参数,理论参数包括凹齿/凸齿、层数(按实际单层端齿和多层端齿的数量选择)、内圆理论值直径和外圆直径,齿形角度、最大顶部直倒角、顶部倒角角度、最大齿根圆角半径、齿顶高、最小齿深以及圆弧端齿加工的两个重要参数:圆弧端齿中心与刀具中心距离,节平面处刀具半径(曲率半径),在设定好圆弧端齿的理论参数后,即可通过软件自动计算生成齿面网格工作坐标点和齿顶高测量坐标点。然后,设置好扫描参数,具体的扫描参数包括齿顶高检测位置、指定扫描的行数、倒角处圆角半径、扫描范围、扫描速度、扫描加速度、点密度、扫描偏置力参数等,再利用超高精度的三坐标测量机进行高速扫描。所述三坐标测量机分两次进行网格式扫描,第一次扫描测量是对每个齿的两个工作面进行网格扫描,扫描点密度不低于20点/mm,扫描速度不低于5mm/s,得到圆弧端齿的齿面数据,第二次扫描测量是沿圆弧端齿的端面进行径向扫描,固定扫描圆直径,扫描点密度不低于20点/mm,扫描速度不低于5mm/s,得到圆弧端齿的齿顶高原始数据。然后,根据三坐标测量机扫描得到的大量齿面轮廓数据点即可得到圆弧端齿的几何参数,具体包括齿形轮廓、齿距、跳动和接触面、条件齿顶高等参数。可以理解,三坐标测量机的精度要求比较高,精度需控制在0.6μm以下,而探头的球度和直径的精度均需控制在0.08μm以下。另外,在对圆弧端齿进行数字化测量时,需对圆弧端齿各表面进行彻底清洁,在20度
±
0.5度环境内恒温4小时以上方可进行测量。
56.其中,条件齿顶高参数是圆弧端齿最为重要的几何参数,其对于凹齿和凸齿能否啮合起到关键性作用,如图3所示,条件齿顶高的计算过程为:
57.步骤s141:利用第二次扫描得到的点数据进行测头三维半径补偿,得到圆弧端齿的表面点数据;
58.步骤s142:采用圆弧展开算法,基于笛卡尔坐标系和极坐标系之间的转换公式对每个圆弧端齿的表面点数据进行转换,并对极坐标系的横轴进行比例缩放,从而将三维圆弧转换为二维轮廓;
59.步骤s143:从二维轮廓中选择相邻的齿和槽来分段截取数据,找到齿槽宽度和齿厚相等时的齿顶高,从而得到每个齿的条件齿顶高。
60.具体地,沿着三维矢量方向进行球头半径补偿,从而得到圆弧端齿的表面点数据。例如,设测量点p的法向矢量n,通过增加或减少测头半径,从而计算得到实际测量点q处的坐标,计算公式为:q=p
±
r*n,其中,r表示测头半径。然后,采用圆弧展开算法,将三维圆弧转为二维轮廓,以消除极半径影响。具体先进行坐标变换,将笛卡尔坐标系的坐标点转换为极坐标点,横轴为极角、纵轴为极径,转换公式为其中,(x,y)表示笛卡尔坐标系中的坐标值,ρ表示极径,θ表示极角,从而得到圆弧端齿齿形的2维展开图。然后,对横轴极角值的比例进行改变,以进行比例缩放,对齿形图进行比例缩小。然后,对得到的圆弧端齿的齿形图进行分段截取,每次截取相邻的一个齿和槽,找到齿厚和齿槽宽相等时的齿顶高,即得到该齿的条件齿顶高,依次计算每个齿的条件齿顶高,形成整个圆弧端齿的条件齿顶高评价数据,并生成条件齿顶高评价报告,如图4所示。
61.可以理解,如图5所示,所述步骤s2具体包括以下内容:
62.步骤s21:利用圆弧端齿的几何参数进行虚拟建模;
63.步骤s22:基于圆弧端齿的齿面点数据进行测头三维半径补偿,得到圆弧端齿的齿面实测点数据;
64.步骤s23:计算每个齿面实测点在法向矢量方向上的投影长度,即每个齿面实测点的偏差值;
65.步骤s24:将每个齿面实测点的坐标值投影到xy平面上,并以偏差值作为z值,得到二维化的点偏差矩阵;
66.步骤s25:基于每个实测点的偏差值对点偏差矩阵进行虚拟着色,以二维绘图的形式进行展现。
67.具体地,先利用圆弧端齿的几何参数进行零件的虚拟建模。然后,基于圆弧端齿的点数据进行测头三维半径补偿,先求取测头中心点坐标沿着测量方向的法矢量,在法矢量的基础上通过增加或减少测头半径的长度,得到实际接触点的坐标。由于圆弧端齿齿面的扫描数据点密度非常高,故而选择齿面上不共面的4个点来求解次微小区域的法矢量。然后,根据凸凹齿相互匹配算法,计算得到每个实测点的偏差值,例如,设理论点为a,坐标为(x1,y1,z1),单位法矢量为(i,j,k),理论点a是根据圆弧端齿的理论参数计算得到的,而实际接触点为q,实际坐标值为(x2,y2,z2),则矢量oa=x1i+y1j+z1k,q点在单位法矢量方向上的投影长度为:即可得到q点的偏差值。然后,进行偏差转换,将
每个齿面实测点的坐标值投影到xy平面上,以偏差值作为z值,从而得到二维化的点偏差矩阵。最后,基于每个实测点的偏差值对点偏差矩阵进行虚拟着色,以二维绘图的形式进行展现,以便于快速判断着色情况。其中,具体的虚拟着色过程为:
68.首先,设置偏差值的公差变量,针对不同的公差变量范围定义不同的颜色,例如,定义偏差值从0到8μm以内对应绿色,即齿面良好啮合区域,从8μm到10μm之间为黄色,即齿面啮合警告区域,大于10μm为红色,齿面啮合超差区域。然后,将每个实测点的偏差值与公差变量范围进行比对以确定每个实测点的着色,并根据实测点的点数计算不同着色的百分比,将百分比以着色图进行显示。其中,可以对圆弧端齿的左齿面和右齿面分别进行虚拟着色,并单独进行图形化绘图。
69.可以理解,所述步骤s3具体为:
70.利用一个虚拟模型的一个凹齿与另一个虚拟模型的多个凸齿逐一进行啮合仿真,或者利用一个虚拟模型的一个凸齿与另一个虚拟模型的多个凹齿逐一进行啮合仿真,在每次啮合仿真时分别进行平行度仿真匹配和同轴度仿真匹配,并根据多次啮合仿真的平行度仿真匹配结果和同轴度仿真匹配结果得到最佳匹配状态对应的配对齿号。
71.其中,所述在每次啮合仿真时进行平行度仿真匹配的过程具体为:
72.每次啮合后,计算得到每对齿的齿顶高之和,并筛选出齿顶高之和的最大值和最小值,计算得到齿顶高之和最大值和齿顶高之和最小值之间的齿顶高之和偏差值,齿顶高之和偏差值越小,平行度越好。
73.其中,所述在每次啮合仿真时进行同轴度仿真匹配的过程具体为:
74.每次啮合后,计算得到两个零件的中心距偏差值,中心距偏差值越小,同轴度越好。
75.其中,所述根据多次啮合仿真的平行度仿真匹配结果和同轴度仿真匹配结果得到最佳匹配状态对应的配对齿号的过程具体为:
76.每次啮合仿真时计算得到齿顶高之和偏差值和中心距偏差值的平方和的二次方根值,基于多次啮合仿真的计算结果筛选出最小者,该最小者对应的啮合状态即为最佳啮合状态,并得到最佳拟合状态对应的凹齿配对齿号和凸齿配对齿号。
77.可以理解,理论上,凸齿轮和凹齿轮的啮合只需要三对齿即可啮合定位,实际零件的啮合过程属于过定位,理论上当平行度为0的时候,每对齿的凹齿齿顶高和凸齿齿顶高相加值都应该相等,当每对齿的凹齿齿顶高和凸齿齿顶高之和不一致的时候,即可造成凸齿的平行度偏差(以凹齿为基准)。同时,理论上凹、凸齿啮合后,每组齿对的节平面中点会完全重合,但受制造精度影响,此中点一定不重合,当中点不重合时,即可造成同轴度偏差。因此,本发明利用一个虚拟模型的一个凹齿与另一个虚拟模型的多个凸齿逐一进行啮合仿真,或者利用一个虚拟模型的一个凸齿与另一个虚拟模型的多个凹齿逐一进行啮合仿真,啮合仿真次数为齿数。例如,零件的虚拟模型共有11个齿,则将一个虚拟模型的一个凹齿逐一与另一个虚拟模型的11个凸齿进行啮合仿真,一共仿真11次。每次啮合后,计算出每对齿的齿顶高之和,共有11组数据,然后从11组数据中筛选出齿顶高之和的最大值和最小值,并计算得到最大值和最小值之间的齿顶高之和偏差值δp。同时,每次啮合后计算得到两个零件模型的中心距偏差值δs。一共啮合仿真了11次,故而可以得到11组齿顶高之和偏差值数据和中心距偏差值数据。然后,基于以下公式分别计算每次啮合状态评价指标:
其中,t表示啮合状态评价指标。从11个啮合状态评价指标中筛选出最小者,即为最佳的啮合状态,并得到该最小值所对应的凹齿配对齿号和凸齿配对齿号,在实际装配时按照该配对齿号进行装配即可获得最佳的啮合状态。
78.以上所述仅为本发明的优选实施例而已,并不用于限制本发明,对于本领域的技术人员来说,本发明可以有各种更改和变化。凡在本发明的精神和原则之内,所作的任何修改、等同替换、改进等,均应包含在本发明的保护范围之内。