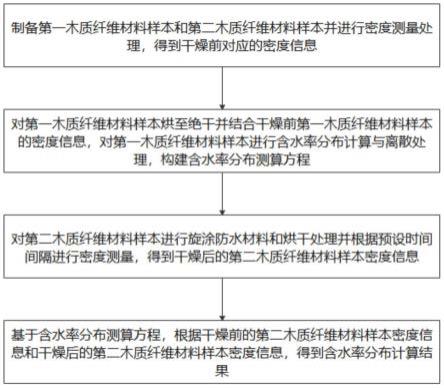
1.本发明涉及木质纤维材料含水率分布测算领域,尤其涉及一种木质纤维材料含水率分布的快速测算方法及系统。
背景技术:2.含水率分布是木质纤维材料的一项重要特性参数,木质纤维材料几乎所有的物理力学性质都与含水率及分布有关;含水率分布还是精准实施木质纤维材料干燥工艺的主要依据,干燥过程中含水率梯度过大容易引起木质纤维材料变形和开裂,使木质纤维材料的品质降低,造成经济损失;目前,常用的含水率分布测定方法主要有分层切片法和电测法;分层切片法的操作较为繁琐且耗费时间,切片过程中水分蒸发不可避免会产生一定的误差,同时受切片厚度的限制,分层切片法无法获取连续的木质纤维材料含水率分布信息;电测法测量精度容易受木质纤维材料种类、纹理方向、环境温湿度等因素的影响,且一般仅适用于含水率低于纤维饱和点以下的范围,x射线法常用于测量木质纤维材料密度,其基本原理是根据x射线透过材料的强度衰减率与材料密度成正比的关系,通过测量x射线透过材料的衰减变化计算材料的密度,现有的技术手段有基于容积密度计算的x射线法测定木质纤维材料含水率分布,但仅考虑了木质纤维材料厚度方向的干缩,忽视了长度和宽度方向的尺寸变化,会给计算结果带来较大误差,而干燥过程中木质纤维材料内部含水率检测的x射线扫描方法,实际干燥过程中木质纤维材料内部存在较大的含水率梯度,木质纤维材料的干缩变形并不均匀,因此按均分的厚度计算木质纤维材料含水率分布会产生一定的误差,因此现有的技术手段测量方法都对含水率分布信息的获取存在严重滞后现象,因此,有必要寻求一种简便而有效的木质纤维材料含水率分布检测方法。
技术实现要素:3.为了解决上述技术问题,本发明的目的是提供一种木质纤维材料含水率分布的快速测算方法及系统,能够更加快速精准的测算木质纤维材料样本的含水率分布情况。
4.本发明所采用的第一技术方案是:一种木质纤维材料含水率分布的快速测算方法,包括以下步骤:
5.制备第一木质纤维材料样本和第二木质纤维材料样本并进行密度测量处理,得到干燥前对应的密度信息;
6.对第一木质纤维材料样本烘至绝干并结合干燥前第一木质纤维材料样本的密度信息,对第一木质纤维材料样本进行含水率分布计算与离散处理,构建含水率分布测算方程;
7.对第二木质纤维材料样本进行旋涂防水材料和干燥处理并根据预设时间间隔进行密度测量,得到干燥后的第二木质纤维材料样本密度信息;
8.基于含水率分布测算方程,根据干燥前的第二木质纤维材料样本密度信息和干燥后的第二木质纤维材料样本密度信息,得到含水率分布计算结果。
9.进一步,所述制备第一木质纤维材料样本和第二木质纤维材料样本并进行密度测量处理,得到干燥前对应的密度信息这一步骤,其具体包括:
10.选取木质纤维材料;
11.在木质纤维材料上制备木质纤维材料样本并在木质纤维材料样本的厚度上进行划分处理,得到具有多个控制单元的第一木质纤维材料样本和第二木质纤维材料样本;
12.通过x射线密度仪分别对第一木质纤维材料样本和第二木质纤维材料样本进行密度测量处理,得到干燥前的第一木质纤维材料样本密度信息和干燥前的第二木质纤维材料样本密度信息。
13.进一步,所述木质纤维材料样本剖面密度计算公式表示如下:
[0014][0015][0016]
上式中,j1表示干燥前木质纤维材料样本控制单元内由x射线法测量密度分布值的数量,j0表示干燥后木质纤维材料样本控制单元内由x射线法测量密度分布值的数量,p表示干燥前木质纤维材料样本控制单元的密度,ρ表示干燥后木质纤维材料样本控制单元的密度,p(x)表示干燥前木质纤维材料样本的密度分布,ρ(x)表示干燥后木质纤维材料样本的密度分布。
[0017]
进一步,所述对第一木质纤维材料样本烘至绝干并结合干燥前第一木质纤维材料样本的密度信息,对第一木质纤维材料样本进行含水率分布计算与离散处理,构建含水率分布测算方程这一步骤,其具体包括:
[0018]
对第一木质纤维材料样本进行烘干处理,得到全干的第一木质纤维材料样本;
[0019]
通过x射线密度仪对全干的第一木质纤维材料样本进行密度测量处理,得到全干第一木质纤维材料样本密度信息;
[0020]
根据第一木质纤维材料样本的密度信息,结合第一木质纤维材料样本的长度与宽度信息计算得到第一木质纤维材料样本的质量;
[0021]
根据木质纤维材料的干缩率计算公式与全干第一木质纤维材料样本密度信息对第一木质纤维材料样本进行计算,得到第一木质纤维材料样本的干缩率;
[0022]
根据第一木质纤维材料样本的干缩率并结合木质纤维材料的特性进行推导,得到第一木质纤维材料样本的全干干缩率;
[0023]
对第一木质纤维材料样本的质量、第一木质纤维材料样本的密度信息和第一木质纤维材料样本的全干干缩率进行离散处理,构建含水率分布测算方程。
[0024]
进一步,所述干缩率计算公式如下所示:
[0025][0026]
[0027]
上式中,β1表示干燥前第一木质纤维材料样本的厚度方向干缩率,β2表示干燥后第一木质纤维材料样本的厚度方向干缩率,δz
green
表示第一木质纤维材料样本在饱水状态下的厚度,δz表示干燥前第一木质纤维材料样本控制单元的厚度,δz表示干燥后第一木质纤维材料样本控制单元的厚度,u表示干燥前第一木质纤维材料样本的含水率,u表示干燥后第一木质纤维材料样本的含水率。
[0028]
进一步,所述对第一木质纤维材料样本的质量、第一木质纤维材料样本的干缩率和第一木质纤维材料样本的全干干缩率进行离散处理,构建含水率分布测算方程这一步骤,其具体包括:
[0029]
对第一木质纤维材料样本的质量、第一木质纤维材料样本的密度信息和第一木质纤维材料样本的全干干缩率进行离散处理,得到初步的离散计算结果;
[0030]
基于迭代离散计算规则,判断到初步的离散计算结果满足预设阈值,停止离散计算,输出离散计算结果;
[0031]
基于高度约束条件,对离散计算结果中的第一木质纤维材料样本的全干干缩率进行修正处理,构建含水率分布测算方程。
[0032]
进一步,所述含水率分布测算方程具体如下所示:
[0033][0034][0035]
上式中,ui表示干燥前经过离散的第一木质纤维材料样本含水率,ui表示干燥后经过离散的第一木质纤维材料样本含水率,mi表示干燥前经过离散的第一木质纤维材料样本控制单元的质量,mi表示干燥后经过离散的第一木质纤维材料样本控制单元的质量,m
0,i
表示经过离散后第一木质纤维材料样本控制单元的绝干质量。
[0036]
进一步,所述迭代离散计算规则具体如下所示:
[0037][0038][0039]
上式中,u
′i表示最新迭代计算得到的第一木质纤维材料样本含水率值,δz
′i表示最新迭代计算得到的第一木质纤维材料样本控制单元的厚度。
[0040]
进一步,所述高度约束条件具体如下所示:
[0041][0042][0043]
上式中,β
′
max
表示最新迭代计算得到的第一木质纤维材料样本的全干干缩率,β
max
表示第一木质纤维材料样本的全干干缩率,ε表示修正因子,z
′
i+1
表示通过计算得到当前第一木质纤维材料样本的厚度,h表示测量得到的第一木质纤维材料样本的实际厚度。
[0044]
本发明所采用的第二技术方案是:一种木质纤维材料含水率分布的快速测算系统,包括:
[0045]
测量模块,用于制备第一木质纤维材料样本和第二木质纤维材料样本并进行密度测量处理,得到干燥前对应的密度信息;
[0046]
构建模块,用于对第一木质纤维材料样本烘至绝干并结合干燥前第一木质纤维材料样本的密度信息,对第一木质纤维材料样本进行含水率分布计算与离散处理,构建含水率分布测算方程;
[0047]
预处理模块,用于对第二木质纤维材料样本进行旋涂防水材料和干燥处理并每间隔预设时间段取出测量其密度,得到干燥后的第二木质纤维材料样本密度信息;
[0048]
计算模块,基于含水率分布测算方程,根据干燥前的第二木质纤维材料样本密度信息和干燥后的第二木质纤维材料样本密度信息,得到含水率分布计算结果。
[0049]
本发明方法及系统的有益效果是:本发明对木质纤维材料样本进行干燥过程中无需多次取出样本进行烘干和测量密度处理,而只需在初期将样本烘至绝干和对多组相邻样本进行干燥且每隔一段时间取出其中一组,有利于对干燥过程进行调控和避免多次取出同一样本造成样本变形带来对实验结果的干扰,并对构建的含水率分布测算方程进行离散处理,降低计算的复杂度,能够更加快速精准的测算木质纤维材料样本的含水率分布情况。
附图说明
[0050]
图1是本发明一种木质纤维材料含水率分布的快速测算方法的步骤流程图;
[0051]
图2是本发明一种木质纤维材料含水率分布的快速测算系统的结构框图;
[0052]
图3是本发明木质纤维材料控制单元的干缩模型示意图;
[0053]
图4是本发明进行实验模拟得到的毛白杨木材干燥过程含水率分布图;
[0054]
图5是本发明进行实验模拟得到的杉木木材干燥过程含水率分布图;
[0055]
图6是本发明进行实验模拟得到的毛竹竹片干燥过程含水率分布图。
具体实施方式
[0056]
下面结合附图和具体实施例对本发明做进一步的详细说明。对于以下实施例中的步骤编号,其仅为了便于阐述说明而设置,对步骤之间的顺序不做任何限定,实施例中的各步骤的执行顺序均可根据本领域技术人员的理解来进行适应性调整。
[0057]
参照图1,本发明提供了一种木质纤维材料含水率分布的快速测算方法,该方法包括以下步骤:
[0058]
s1、制备第一木质纤维材料样本和第二木质纤维材料样本并进行密度测量处理,得到干燥前对应的密度信息;
[0059]
s11、选取木质纤维材料;
[0060]
s12、在木质纤维材料上制备木质纤维材料样本并在木质纤维材料样本的厚度上进行划分处理,得到具有多个控制单元的第一木质纤维材料样本和第二木质纤维材料样本;
[0061]
具体地,在木质纤维材料上制备n组样品,每组样品由两块纤维相连的材料组成,分别标记为(a1,a1),(a2,a2),...,(an,an),样品尺寸为20~50mm(顺纹,长度)
×
20~50mm
(横纹,宽度)
×
自然厚度为3~100mm(横纹),所述组数取值范围为3~10。
[0062]
s13、通过x射线密度仪分别对第一木质纤维材料样本和第二木质纤维材料样本进行密度测量处理,得到干燥前的第一木质纤维材料样本密度信息和干燥前的第二木质纤维材料样本密度信息;
[0063]
具体地,参照图3,在厚度方向构建一维坐标系oz,假设干燥前木质纤维材料的长度、宽度和厚度分别为l、w和h,沿厚度方向将木质纤维材料划分为i个控制单元,所述控制单元的厚度为0.5mm~5mm,更精确的可以为1mm~2mm,进一步所述通过x射线密度仪分别对第一木质纤维材料样本和第二木质纤维材料样本进行密度测量处理,其密度计算公式具体如下所示:
[0064][0065][0066]
上式中,j1表示干燥前木质纤维材料样本控制单元内由x射线法测量密度分布值的数量,j0表示干燥后木质纤维材料样本控制单元内由x射线法测量密度分布值的数量,p表示干燥前木质纤维材料样本控制单元的密度,ρ表示干燥后木质纤维材料样本控制单元的密度,p(x)表示干燥前木质纤维材料样本的密度分布,ρ(x)表示干燥后木质纤维材料样本的密度分布。
[0067]
s2、对第一木质纤维材料样本烘至绝干并结合干燥前第一木质纤维材料样本的密度信息,对第一木质纤维材料样本进行含水率分布计算与离散处理,构建含水率分布测算方程;
[0068]
s21、对第一木质纤维材料样本进行烘干处理,得到全干的第一木质纤维材料样本;
[0069]
具体地,将第一木质纤维材料样本a1~an放入恒温干燥箱,从40℃缓慢升温至103℃,升温速率10℃/h,把第一木质纤维材料样本烘至绝干,所述绝干条件为木质纤维材料样本在103℃恒温干燥箱中烘至恒重即认为烘干。
[0070]
s22、通过x射线密度仪对全干的第一木质纤维材料样本进行密度测量处理,得到全干第一木质纤维材料样本密度信息;
[0071]
s23、根据第一木质纤维材料样本的密度信息,结合第一木质纤维材料样本的长度与宽度信息计算得到第一木质纤维材料样本的质量;
[0072]
具体地,根据控制单元的厚度和已获取的长度、宽度以及密度,可计算控制单元的质量。其质量公式计算如下所示:
[0073]
m=p
·
l
·w·
δz
[0074]
m=ρ
·
l
·w·
δz
[0075]
上式中,m表示干燥前第一木质纤维材料样本控制单元的质量,m表示干燥后第一木质纤维材料样本控制单元的质量,p表示干燥前第一木质纤维材料样本控制单元的密度,ρ表示干燥后第一木质纤维材料样本控制单元的密度,l表示干燥前第一木质纤维材料样本控制单元的长度,l表示干燥后第一木质纤维材料样本控制单元的长度,w表示干燥前第一木质纤维材料样本控制单元的宽度,w表示干燥后第一木质纤维材料样本控制单元的宽度,
δz表示干燥前第一木质纤维材料样本控制单元的厚度,δz表示干燥后第一木质纤维材料样本控制单元的厚度。
[0076]
s24、根据木质纤维材料的干缩率计算公式与全干第一木质纤维材料样本密度信息对第一木质纤维材料样本进行计算,得到第一木质纤维材料样本的干缩率;
[0077]
具体地,所述干缩率计算公式如下所示:
[0078][0079][0080]
上式中,β1表示干燥前第一木质纤维材料样本的厚度方向干缩率,β2表示干燥后第一木质纤维材料样本的厚度方向干缩率,δz
green
表示第一木质纤维材料样本在饱水状态下的厚度,δz表示干燥前第一木质纤维材料样本控制单元的厚度,δz表示干燥后第一木质纤维材料样本控制单元的厚度,u表示干燥前第一木质纤维材料样本的含水率,u表示干燥后第一木质纤维材料样本的含水率;
[0081]
木质纤维材料从饱水状态到纤维饱和点之间不发生干缩,而从纤维饱和点到绝干状态之间发生的干缩与含水率呈线性关系,假设木质纤维材料厚度全干干缩率为β
max
,纤维饱和点为30%。
[0082]
s25、根据第一木质纤维材料样本的干缩率并结合木质纤维材料的特性进行推导,得到第一木质纤维材料样本干燥后控制单元的厚度;
[0083]
具体地,所述第一木质纤维材料样本干燥后控制单元厚度的计算公式如下所示:
[0084][0085]
上式中,β
max
表示全干干缩率;
[0086]
进一步所述全干干缩率的初值可以设定为0.01~0.2更精确的可以设定为0.03~0.1。
[0087]
s26、对第一木质纤维材料样本的质量、第一木质纤维材料样本的密度信息和第一木质纤维材料样本的全干干缩率进行离散处理,构建含水率分布测算方程。
[0088]
具体地,为开发计算木质纤维材料含水率分布的迭代算法,需对x射线测量的密度分布和第一木质纤维材料样本的具体参数进行离散处理,依次降低计算过程的复杂程度,使得计算过程更为快速计算结果更为精确。
[0089]
s261、对第一木质纤维材料样本的质量、第一木质纤维材料样本的密度信息和第一木质纤维材料样本的全干干缩率进行离散处理,得到初步的离散计算结果;
[0090]
s2611、首先对第一木质纤维材料样本的密度分布进行离散处理;
[0091]
具体地,对第一木质纤维材料样本的密度进行离散处理公式如下所示:
[0092][0093][0094]
上式中,pi表示经过离散处理干燥前木质纤维材料样本控制单元的密度,ρi表示经过离散处理干燥后木质纤维材料样本控制单元的密度,f
j+1
表示干燥前第一木质纤维材料样本控制单元的上边界面,f
j+1
表示干燥后第一木质纤维材料样本控制单元的上边界面,fj表示干燥前第一木质纤维材料样本控制单元的下边界面,fj表示干燥后第一木质纤维材料样本控制单元的下边界面,p(xk)表示经过离散处理干燥前木质纤维材料样本的密度分布,λ表示x射线的扫描步距;
[0095]
若第一木质纤维材料样本控制单元边界与x射线密度分布位置不重合时取第一木质纤维材料样本控制单元内最接近下边界的密度分布位置,干燥前第一木质纤维材料样本控制单元的密度取该单元内密度分布均值计算,其中x射线的扫描步距为0.01mm~0.5mm,更精确的可以为0.05mm~0.2mm。
[0096]
s2612、对第一木质纤维材料样本干燥后控制单元进行离散处理;
[0097]
具体地,第一木质纤维材料样本干燥后控制单元进行离散处理的公式具体如下所示:
[0098][0099]
上式中,δzi表示经过离散的干燥前第一木质纤维材料样本控制单元的厚度,δzi表示经过离散的干燥后第一木质纤维材料样本控制单元的厚度,ui表示经过离散的干燥前第一木质纤维材料样本的含水率,ui表示经过离散的干燥后第一木质纤维材料样本的含水率。
[0100]
s2613、对第一木质纤维材料样本的质量计算过程进行离散处理;
[0101]
具体地,所述对第一木质纤维材料样本的质量计算过程进行离散处理的公式如下所示:
[0102]
mi=pi·
l
·w·
δzi[0103]
mi=ρi·
l
·w·
δzi[0104]
上式中,mi表示经过离散的干燥前第一木质纤维材料样本控制单元的质量,mi表示经过离散的干燥后第一木质纤维材料样本控制单元的质量,pi表示经过离散的干燥前第一木质纤维材料样本控制单元的密度,ρi表示经过离散的干燥后第一木质纤维材料样本控制单元的密度,δzi表示经过离散的干燥前第一木质纤维材料样本控制单元的厚度,δzi表示经过离散的干燥后第一木质纤维材料样本控制单元的厚度。
[0105]
s262、基于迭代离散计算规则,判断到初步的离散计算结果满足预设阈值,停止离散计算,输出离散计算结果;
[0106]
具体地,假设干燥后控制单元含水率和控制单元厚度最新迭代计算值为u
′i和δz′i,设定收敛标准为前后两次计算值对偏差的绝对值小于0.0001,停止对第一木质纤维材料样本参数的迭代离散,即如下所示:
[0107][0108][0109]
上式中,u
′i表示最新迭代计算得到的第一木质纤维材料样本含水率值,δz
′i表示最新迭代计算得到的第一木质纤维材料样本控制单元的厚度。
[0110]
s263、基于高度约束条件,对离散计算结果中的第一木质纤维材料样本的全干干缩率进行修正处理,构建含水率分布测算方程。
[0111]
具体地,以干燥后第一木质纤维材料样本的实际厚度h为约束条件,将计算的第一木质纤维材料样本厚度与实际厚度比较,对第一木质纤维材料样本的全干干缩率进行修正,所述修正过程如下所示:
[0112][0113][0114]
上式中,β
′
max
表示最新迭代计算得到的第一木质纤维材料样本的全干干缩率,β
max
表示第一木质纤维材料样本的全干干缩率,ε表示修正因子,z
′
i+1
表示通过计算得到当前第一木质纤维材料样本的厚度,h表示测量得到的第一木质纤维材料样本的实际厚度;
[0115]
引入修正因子对全干干缩率进行了修正,样本计算厚度与实际厚度完全一致,避免了因引入的全干干缩率与实际的全干干缩率偏差过大造成的计算误差;
[0116]
进一步的所述修正因子可以设定为0.001~0.1,更精确的可以设定为0.005~0.05;
[0117]
根据修正后的全干干缩率构建含水率分布测算方程,具体如下所示:
[0118][0119][0120]
上式中,ui表示干燥前经过离散的第一木质纤维材料样本含水率,ui表示干燥后经过离散的第一木质纤维材料样本含水率,mi表示干燥前经过离散的第一木质纤维材料样本控制单元的质量,mi表示干燥后经过离散的第一木质纤维材料样本控制单元的质量,m
0,i
表示经过离散后第一木质纤维材料样本控制单元的绝干质量。
[0121]
s3、对第二木质纤维材料样本进行旋涂防水材料和干燥处理并根据预设时间间隔进行密度测量,得到干燥后的第二木质纤维材料样本密度信息;
[0122]
s4、基于含水率分布测算方程,根据干燥前的第二木质纤维材料样本密度信息和干燥后的第二木质纤维材料样本密度信息,得到含水率分布计算结果。
[0123]
具体地,将第一木质纤维材料样本计算得到的含水率分布结果作为第二木质纤维
材料样本的初始含水率分布,用防水材料涂覆样品a1~an长度和宽度方向的侧面,旋涂防水材料为了模拟实际的干燥过程,让水分仅沿一维方向即厚度方向迁移,所述防水材料包括高温石蜡、玻璃胶和环氧树脂等物质,并将其放入干燥设备进行干燥处理,每隔一定时间从干燥设备中取出一组第二木质纤维材料样本,通过x射线密度仪测量其厚度方向的剖面密度,结合步骤s1测得的干燥前第二样本密度信息,通过构建的含水率分布测算方程计算第二木质纤维材料样本的含水率分布。
[0124]
参照图2,一种木质纤维材料含水率分布的快速测算系统,包括:
[0125]
测量模块,用于制备第一木质纤维材料样本和第二木质纤维材料样本并进行密度测量处理,得到干燥前对应的密度信息;
[0126]
构建模块,用于对第一木质纤维材料样本烘至绝干并结合干燥前第一木质纤维材料样本的密度信息,对第一木质纤维材料样本进行含水率分布计算与离散处理,构建含水率分布测算方程;
[0127]
预处理模块,用于对第二木质纤维材料样本进行旋涂防水材料和干燥处理并每间隔预设时间段取出测量其密度,得到干燥后的第二木质纤维材料样本密度信息;
[0128]
计算模块,基于含水率分布测算方程,根据干燥前的第二木质纤维材料样本密度信息和干燥后的第二木质纤维材料样本密度信息,得到含水率分布计算结果。
[0129]
本发明的仿真实验如下所示:
[0130]
参照图4,选取毛白杨木质纤维材料为试验材料,初含水率约60%,在纤维相邻的位置制取50mm(长度)
×
50mm(宽度)
×
25mm(厚度)的木质纤维材料样品6组,首先通过x射线密度仪测量a1~a6的剖面密度,扫描步长为0.05mm,然后烘绝干,重复测量其剖面密度;通过x射线密度仪测量样品a1~a6的剖面密度,然后放入干燥设备中干燥,每隔一段时间取出,再测量其剖面密度,利用构建的含水率分布测算方程计算毛白杨木质纤维材料在干燥过程的含水率分布,控制单元厚度1mm,计算过程迭代计算为147次,全干干缩率初始赋值为0.15,全干干缩率修正因子设定为0.005,全干干缩率计算结果为0.0652~0.0831;
[0131]
参照图5,选取杉木木质纤维材料为试验材料,初含水率约70%,在纤维相邻的位置制取50mm(长度)
×
50mm(宽度)
×
26mm(厚度)的木质纤维材料样品7组,首先通过x射线密度仪测量a1~a7的剖面密度,扫描步长为0.1mm,然后烘绝干,重复测量其剖面密度;通过x射线密度仪测量样品a1~a7的剖面密度,然后放入干燥设备中干燥,每隔一段时间取出,再测量其剖面密度,利用构建的含水率分布测算方程计算杉木木质纤维材料在干燥过程的含水率分布如图2所示,控制单元厚度1mm,计算过程迭代计算为46次,全干干缩率初始赋值为0.1,全干干缩率修正因子设定为0.008,全干干缩率计算结果为0.0613~0.0722;
[0132]
参照图6,选取毛竹竹片为试验材料,初含水率约50%,在纤维相邻的位置制取30mm(长度)
×
20mm(宽度)
×
12mm(厚度)的毛竹样品6组,首先通过x射线密度仪测量a1~a6的剖面密度,扫描步长为0.05mm,然后烘绝干,重复测量其剖面密度;通过x射线密度仪测量样品a1~a6的剖面密度,然后放入干燥设备中干燥,每隔一段时间取出,再测量其剖面密度,利用构建的含水率分布测算方程计算毛竹竹片在干燥过程的含水率分布如图3所示,控制单元厚度0.5mm,计算过程迭代计算为67次,全干干缩率初始赋值为0.1,全干干缩率修正因子设定为0.01,全干干缩率计算结果为0.0427~0.0582。
[0133]
上述方法实施例中的内容均适用于本系统实施例中,本系统实施例所具体实现的
功能与上述方法实施例相同,并且达到的有益效果与上述方法实施例所达到的有益效果也相同。
[0134]
以上是对本发明的较佳实施进行了具体说明,但本发明创造并不限于所述实施例,熟悉本领域的技术人员在不违背本发明精神的前提下还可做作出种种的等同变形或替换,这些等同的变形或替换均包含在本技术权利要求所限定的范围内。