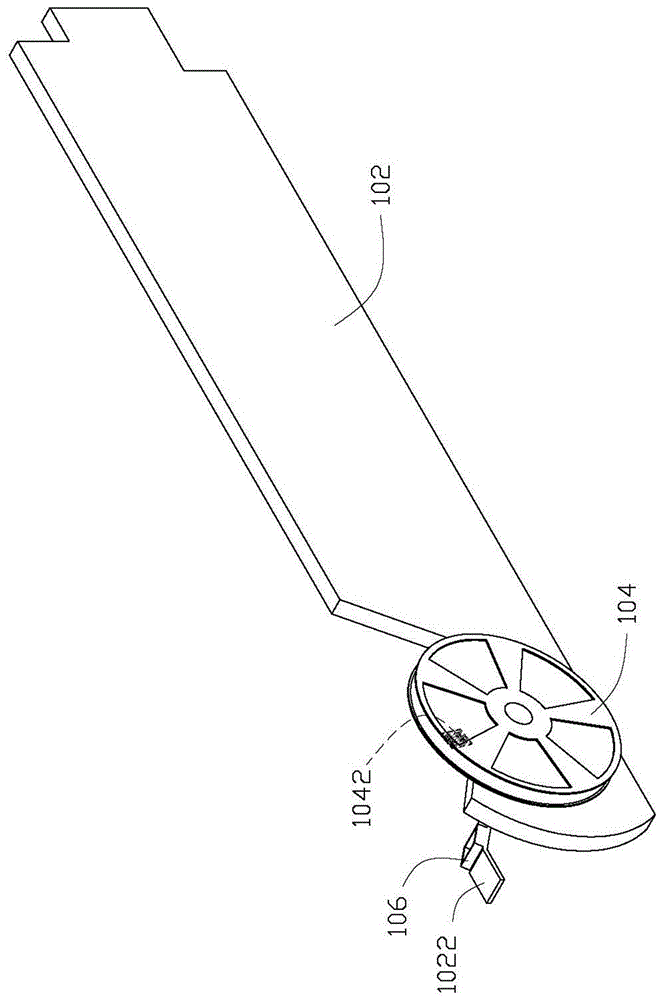
本发明涉及自动化技术,尤其涉及一种基于射频识别技术的智能上料设备及智能上料方法。
背景技术:
:在生产计算机板卡等电路板贴片的过程中,当表面贴片设备缺贴片物料时,需手动更换新的喂料盘。在手动更换新料盘时,需要从表面贴片设备上拿下喂料架并拆下旧料盘,再安装新料盘,最后将更换了新料盘的喂料架重新装回表面贴片设备。但是,在此过程中,工人常常会因为疏忽而拿错新料盘或者将喂料架安装在表面贴片设备的错误位置,造成生产错件或者坏件。随着表面贴片技术不断发展,表面贴片设备的生产速度逐步提升,生产错件或者坏件会造成巨大损失,因此,提升换料与贴片的准确性尤为重要。技术实现要素:鉴于以上内容,有必要提供一种智能上料设备,以解决上述问题。鉴于以上内容,有必要提供一种智能上料方法,以解决上述问题。本发明提供一种智能上料设备。该智能上料设备包括:至少一喂料组件,定位组件和监控组件。该至少一喂料组件设置于一表面贴片设备上,每一该喂料组件包括喂料架,可拆卸地设置于该喂料架上的喂料盘,及设置于该喂料架上的第一识别模块,该第一识别模块预存该喂料架的编号信息,该第一识别模块识别该喂料盘上的条形码信息及该喂料盘内的物料用量信息。该定位组件包括定位带、两个紧固组件和第二识别模块,该两个紧固组件将该定位带固定于该表面贴片设备的一侧,使得该定位带正对该喂料架具有该喂料盘的一端,该第二识别模块可滑动地设置于该定位带上并可沿该定位带滑动,该第二识别模块识别该两个紧固组件的位置信息,每一该喂料架的编号信息及位置信息。该监控组件包括工控机,该工控机根据该第一识别模块和该第二识别模块发送的信息,并根据预设的喂料盘条形码信息判断该喂料盘的条形码信息是否正确,根据预设的喂料架的位置信息判断该喂料架的位置信息是否正确,及根据该喂料盘的物料用量信息判断该喂料盘内的贴片物料是否用尽,且在该喂料盘的条形码信息,及/或该喂料架的位置信息不正确,或该喂料盘内的贴片物料用尽时发出警示。本发明还提供一种智能上料方法。该智能上料方法包括:识别一喂料盘的条形码信息及探测该喂料盘中的物料用量信息;读取一紧固滑块的内置电子标签的信息,并将该电子标签的信息作为一初始位置,依次识别一定位带的多个刻度标记,每个刻度标记对应一个喂料架,根据该刻度标记确定每个喂料架的位置信息,读取另一紧固滑块的内置电子标签信息,并将该电子标签的信息作为一终点位置;根据预设的喂料盘条形码信息判断该喂料盘的条形码信息是否正确;根据预设的喂料架的位置信息判断该喂料架的位置信息是否正确;根据该喂料盘的物料用量信息判断该喂料盘内的贴片物料是否用尽;及在该喂料盘的条形码信息,及/或该喂料架的位置信息不正确,或该喂料盘内的贴片物料用尽时发出警示。本发明的基于射频识别的智能上料设备和智能上料识别方法,能够从贴片物料源头到表面贴片设备的每个环节的操作都进行实时监控,每一部份的设备都有固定且唯一的设备身份识别码,从而确保喂料盘、喂料架和表面贴片设备一一对应,有效防止错件或坏件等重大生产问题,大大减小表面贴片厂商的经济损失。附图说明图1为本发明一实施方式的智能上料设备的结构示意图。图2为图1所示的喂料架的结构示意图。图3为图2所示的第一识别模组的模块示意图。图4为图1所示的定位组件的分解示意图。图5为图4所示的第二别模组的模块示意图。图6为监控组件与第一识别模块和第二识别模块通讯的模块示意图。图7为本发明一实施方式的智能上料方法的流程图。主要元件符号说明智能上料设备100喂料组件10喂料架102拆卸机构1022喂料盘104料盘识别条形码1042第一识别模块106无线识别器1062物料用量检测探头1064定位组件20定位带22刻度标记222定位孔224紧固组件24滑块轨道242紧固滑块244第二识别模块26高频读写单元262刻度标记识别单元264第一通讯单元266监控组件30工控机32设备控制器34第二通讯单元36表面贴片设备200设备本体210支撑面220保护板230收容空间240开口250如下具体实施方式将结合上述附图进一步说明本发明。具体实施方式下面将结合本发明实施方式中的附图,对本发明实施方式中的技术方案进行清楚、完整地描述,显然,所描述的实施方式仅是本发明一部分实施方式,而不是全部的实施方式。基于本发明中的实施方式,本领域普通技术人员在没有做出创造性劳动前提下所获得的所有其他实施方式,都属于本发明保护的范围。需要说明的是,当一个组件被认为是“连接”另一个组件,它可以是直接连接到另一个组件或者可能同时存在居中组件。除非另有定义,本文所使用的所有的技术和科学术语与属于本发明的
技术领域:
的技术人员通常理解的含义相同。本文中在本发明的说明书中所使用的术语只是为了描述具体的实施方式的目的,不是旨在于限制本发明。本文所使用的术语“及/或”包括一个或多个相关的所列项目的任意的和所有的组合。请参考图1,图1为智能上料设备100向表面贴片设备200提供贴片物料的立体结构示意图。该表面贴片设备200包括设备本体210。该设备本体210具有一支撑面220。该表面贴片设备200还包括设置于该支撑面220上的保护板230。本实施方式中,该保护板230位于该支撑面220的三侧,该三块保护板230和该支撑面220之间围绕形成收容空间240,并形成开口250。智能上料设备100包括至少一喂料组件10。至少一该喂料组件10设置于该收容空间240内。本实施方式中,该至少一喂料组件10的数量为四个,该四个喂料组件10并排且间隔地设置于该收容空间240内。可理解,在其它实施方式中,该至少一喂料组件10的数量可根据实际生产需要增减。请一并参考图2,每一该喂料组件10包括一喂料架102。该喂料架102呈船形状。该喂料架102设置于该收容空间240内并位于该支撑面220上,该喂料架102的一端伸出该开口250。本实施方式中,每一该喂料架102包括一拆卸机构1022。该拆卸机构1022设置于该喂料架102伸出该开口250的一端上。每一该喂料组件10包括一喂料盘104。该喂料盘104可拆卸地且转动地设置于该喂料架102伸出该开口250的一端,且邻近该拆卸机构1022。该表面贴片设备200正常工作时,该喂料盘104在该喂料架102中绕其自身轴线旋转,为该表面贴片设备200提供贴片物料。当该喂料盘104中的贴片物料用完时,该表面贴片设备200停机,手动下压该拆卸机构1022的操作手把,该喂料盘104便可从该喂料架102中弹出,以便更换新的喂料盘104。可理解,在其它实施方式中,该拆卸机构1022可采用拆卸按钮或者拆卸卡扣之类的代替,或者采用该喂料架102自身的卡合结构代替,该拆卸机构1022可相应的省略。每一该喂料组件10包括第一识别模块106。该第一识别模块106设置于一该喂料架102上。本实施方式中,该第一识别模块106设置于该拆卸机构1022的侧部。可理解,在其它实施方式中,该第一识别模块106还可设置于该喂料架102的其它位置上。该第一识别模块106存储该喂料架102的编号信息。该第一识别模块106用于读取位于同一该喂料架102上的喂料盘104的条形码信息及当前喂料盘104的物料用量信息。具体地,请一并参考图3,该第一识别模块106包括无线识别器1062和物料用量检测探头1064。该无线识别器1062和该物料用量检测探头1064被设置于一盒子中,且该盒子被安装在拆卸机构1022上。料盘识别条形码1042粘贴或者印刷在该喂料盘104上。本实施方式中,该料盘识别条形码1042粘贴或者印刷在为该喂料盘104的盘面位置。该料盘识别条形码1042采用一维码或者二维码等条形码技术。该料盘识别条形码1042用于贴片物料入库时记录该贴片物料的型号规格等信息。该无线识别器1062通过射频识别技术识别粘贴或者印刷在该喂料盘104上的料盘识别条形码1042。该无线识别器1062还采用2.4g无线通讯技术,具体不仅限于wifi、蓝牙或者zigbee等技术发送所识别的信息。该无线识别器1062用于检测、记录和擦除同一该喂料架102中的料盘识别条形码1042的信息及喂料盘104内的物料用量信息。物料用量检测探头1064正对该喂料盘104内的贴片物料。该物料用量检测探头1064采用声波或者光电等技术,具体不仅限于可见光,红外线或者激光,来检测该喂料盘104内的物料用量。该第一识别模块106将料盘识别条形码1042的条形码信息及喂料盘104内的物料用量信息通过2.4g信号发出。智能上料设备100还包括设置于该表面贴片设备200上的定位组件20。定位组件20安装在表面贴片设备200具有开口250的一侧。请一并参考图4,定位组件20包括定位带22。定位带22由布料或者皮质等柔性材料制成。定位带22表面标有与该至少一喂料架102间距相同的刻度标记222,刻度标记222可采用电子标签、容栅移位传感器或者磁铁等。每个刻度标记222对应一个喂料架102及位于其上的第一识别模块106。定位带22的两端各设有定位孔224。定位组件20包括两个紧固组件24。紧固组件24用于紧固该定位带22。每一紧固组件24对应一该定位孔224。每一紧固组件24安装在表面贴片设备200的一侧,用于将该定位带22固定于该表面贴片设备200具有开口250的一侧上。具体地,紧固组件24包括滑块轨道242和紧固滑块244。滑块轨道242固定在表面贴片设备200的侧边位置。紧固滑块244中内置有电子标签,用于确定定位带22的刻度方向及判断刻度标记222的初始位置。定位带22的每一端可以通过其定位孔224套在一该紧固滑块244的一端上,该紧固滑块244的另一端还伸入一该滑块轨道242中,从而将该定位带22固定于该表面贴片设备200具有开口250的一侧上。通过紧固滑块244滑动到滑块轨道242的合适位置,即可拉紧定位带22并锁定。可理解,通过滑动紧固滑块244在滑块轨道242的位置即可达到适用不同料盘的目的。定位组件20包括第二识别模块26。第二识别模块26套在定位带22上,且可以沿着定位带22滑动。请一并参考图5,第二识别模块26包括高频读写单元262、刻度标记识别单元264和第一通讯单元266。高频读写单元262可以读取内置紧固滑块244的电子标签的位置信息,并根据该位置信息确定定位带22的方向和刻度标记222的初始位置,还可以读取位于每一该第一识别模块106内的喂料架编号信息。刻度标记识别单元264可以检测到定位带22表面的刻度标记222,根据高频读写单元262确定的定位带22的刻度方向以及刻度标记识别单元264识别的刻度标记222,从而确定每一喂料架102的位置。第一通讯单元266用于将喂料架102的位置信息发送,该第一通讯单元266可采用不仅限于wifi、蓝牙或者zigbee等无线通讯技术。请一并参考图6,智能上料设备100还包括监控组件30。监控组件30包括工控机32,该工控机32采用2.4g无线通讯技术,该工控机32预存预设的喂料架编号信息,预设的喂料架位置信息,及预设的喂料盘条形码信息等。可理解,为了更好的控制该表面贴片设备200,监控组件30还包括设备控制器34和第二通讯单元36。监控组件30用于通过第二通讯单元36接收由第一识别模块106发回的喂料盘条形码信息以及第二识别模块26发回的喂料架位置信息,并分别与预设的喂料盘条形码信息和预设的喂料架位置信息比对,若其中一项或者多项不一致,监控组件30将以警报的方式提醒操作人员,并显示错误信息内容,以便有针对性的解决错误,同时设备控制器34控制表面贴片设备200停止运转,在所有信息正确后,设备控制器34控制表面贴片设备200再次启动。监控组件30还用于通过第二通讯单元36接收由第一识别模块106发回的喂料盘物料用量信息判断该喂料盘104内的贴片物料是否用尽,如该喂料盘104内的贴片物料已用尽,则发出缺料提醒,同时设备控制器34控制表面贴片设备200停止运转,在新的喂料盘104装好后,设备控制器34控制表面贴片设备200再次启动。图7为表面贴片设备200采用智能上料设备100智能上料的智能上料方法流程图。具体步骤如下:步骤s51,提供表面贴片设备200表面贴片时所需的多个喂料盘104,使用一无线扫描设备扫描每一该喂料盘104上的料盘识别条形码1042以读取喂料盘104的贴片物料信息,并将该贴片物料信息通过该无线扫描设备自带的无线模块发送至待组装新喂料盘104的喂料架102上的第一识别模块106,更换每一喂料盘104均做以上操作,然后将该喂料盘104安装到同一该喂料架102中。步骤s52,将已更新喂料盘104的喂料架102安装到表面贴片设备200中,第一识别模块106通过其无线识别器1062识别喂料盘104的条形码信息及通过其物料用量检测探头1064探测该喂料盘104中的物料信息,并将该些物料信息通过2.4g无线技术发送至监控组件30的工控机32上。步骤s53,将第二识别模块26拉向定位带22的一端,并开启第二识别模块26的电源,第二识别模块26首先读取紧固滑块244中内置的电子标签的信息,确定并记录第二识别模块26的初始位置,将第二识别模块26从该初始位置手动滑动到定位带22的另一端,并确定第二识别模块26的终点位置。在第二识别模块26滑动的过程中,第二识别模块26自动识别定位带22的刻度标记222和第一识别模块106中的喂料架编号,其中每个刻度标记222对应一个喂料架102,第二识别模块26根据刻度标记222及喂料架编号即可确定每个喂料架102在定位带22上的位置信息,即完成喂料架102的定位动作。同时,第二识别模块26通过2.4g无线技术发出喂料架102在定位带22上位置信息。步骤s54,监控组件30实时接收步骤s52中第一识别模块106发出的喂料盘104的条形码信息及物料用量信息,以及步骤s53中第二识别模块26发出的喂料架位置信息。步骤s55,监控组件30读取预存的喂料架102的位置信息及预存的喂料盘104的条形码信息,并与接收的喂料架102的位置信息及喂料盘104的条形码信息进行比较,判断该喂料架102的位置信息及喂料盘104的条形码信息是否分别与预设的喂料架位置信息及喂料盘条形码信息相匹配,如果是,步骤进入步骤s56,否则,步骤进入s510。步骤s56,监控组件30在其显示接口显示正常开机信息,即可操作表面贴片设备200正常开机运转。步骤s57,根据接收的物料用量信息判断贴片物料是否将用尽,如果是,进入步骤s58,否则继续步骤s57。步骤s58,监控组件30在其显示接口显示需更换的物料信息,提示操作人员更换新的喂料盘104。步骤s59,在喂料架从表面贴片设备拿下后,离开监控组件30的控制范围时,第一识别模块106自动擦除自身存储器中旧的物料信息,新的喂料盘104更换完成后,操作人员重复以上四步操作,表面贴片设备200即可继续正常工作。步骤s510,监控组件30在其显示接口显示具体的错误信息,同时设备控制器34控制表面贴片设备200停机,以便操作人员需根据该错误信息,纠正错误源。本发明提出了一种基于射频识别技术的智能上料设备100,该智能上料设备100从贴片物料源头到表面贴片设备200,每个环节的操作都进行实时监控,每一部份都有固定且唯一的设备身份识别码,从而确保喂料盘104、喂料架102和表面贴片设备200一一对应,有效预防错件或坏件等重大生产问题,大大减小表面贴片厂商的经济损失。可以理解的是,对于本领域的普通技术人员来说,可以根据本发明的技术构思做出其它各种相应的改变与变形,而所有这些改变与变形都应属于本发明权利要求的保护范围。当前第1页12