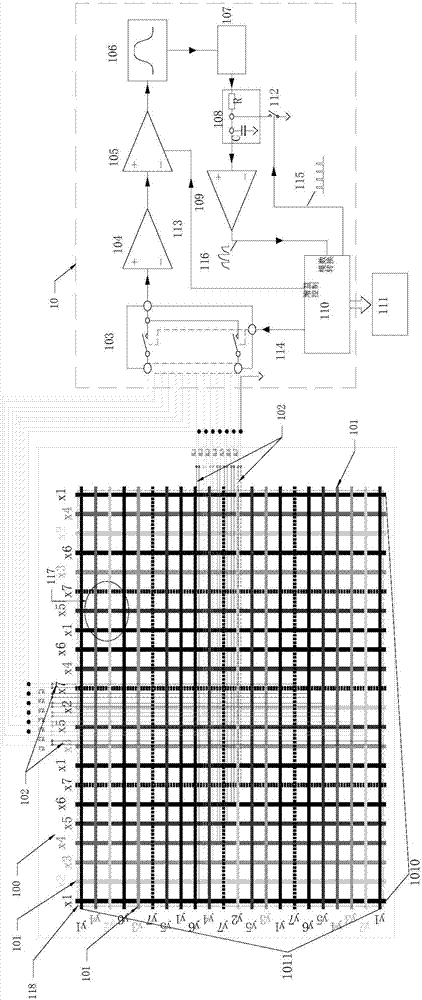
本发明涉及磁感应领域,特别涉及一种手写输入装置。
背景技术:
:随着电子产品和各类数控机床的进步与发展,对距离和二维面的位置传感感应器的应用和需求越来越广泛。现有的手写输入装置一般采用二维两个方向的若干地理电磁感应线圈来扫描检测电磁笔。专利号为cn201320756682.x,“电磁天线的单层布线系统”公布了一种在二维面两个方向设置若干独立电磁感应通道线圈来构成磁信号定位感应器,可用来扫描检测定位电磁笔以实现手写输入触控装置,这种磁信号定位感应器每个通道位置的设置一独立的电磁感应通道线圈。当磁信号定位感应器中的独立电磁感应通道线圈数量累积到一定程度,那么要区域扫描检测这样的磁信号定位感应器需要很长的时间,反映速度慢,定位感应的精度低,长距离移动累积误差大,这样的磁信号定位感应器十分复杂。技术实现要素:本发明旨在至少在一定程度上解决相关技术中的技术问题之一。为此,本发明的主要目的在于提供一种手写输入装置,旨在解决现有技术的磁感应装置检测时间长、反应速度慢、定位感应的精度低、长距离移动累积误差大和装置复杂的问题。为实现上述目的,本发明提供一种手写输入装置,包括显示组件,设置在所述显示组件前面或者后面距离显示组件100毫米范围内任意位置的磁信号感应组件,与所述磁信号感应组件对应设置的磁信号输出件,上述所有部件均设置在外壳中,所述外壳内还设有主板;其特征在于,所述磁信号感应组件包括感应元件和连接所述感应元件的检测控制电路,所述感应元件包括:水平编码阵列、与所述水平编码阵列垂直设置的垂直编码阵列,所述水平编码阵列与所述垂直编码阵列均由磁信号感应线圈单元组成。所述水平编码阵列由一个以上的磁信号感应线圈单元组成;所述垂直编码阵列由一个以上的磁信号感应线圈单元组成;所述磁信号感应线圈单元由至少两个磁感应线圈通过差分线串联而成;磁感应线圈由1圈到10圈的连续环形导线构成。所述磁信号感应线圈单元中串联磁感应线圈的差分线在磁感应定位有效区内。所述磁信号感应线圈单元中串联磁感应线圈的差分线在磁感应定位有效区外。所述检测控制电路包括多选一阵列开关、前级信号放大器、可控增益放大器、带通放大器、交直流变换器、积分电路、直流放大器、充放电开关和处理器;其中,所述多选一阵列开关一侧分别与所述水平磁感应线圈和所述垂直磁感应线圈连接,所述多选一阵列开关另一侧与所述前级放大器连接,所述前级放大器与所述可控增益放大器连接;所述可控增益放大器一端通向所述处理器,所述可控增益放大器另一端通向所述带通放大器,所述带通放大器通过所述交直流变换器与所述积分电路连接;所述积分电路一端通过直流放大器通向所述处理器,所述积分电路另一端通向所述充放电开关,所述处理器分别通向所述多选一阵列开关和所述充放电开关。所述显示组件与所述磁信号感应组件之间还设有中间件。所述磁信号输出件为电磁触控笔,所述电磁触控笔首端为交变电磁信号源。设置在所述水平编码阵列中的磁信号感应线圈与所述垂直编码阵列中的磁信号感应线圈相互交叉排列组合设置。排列组合设置为:水平编码阵列和垂直编码阵列中任意磁信号感应线圈单元上任意磁信号感应圈与相邻前或相邻后其它的磁信号感应线圈单元上的磁感应线圈的两两排列组合不与其它位置上的两两排列组合重复;并同时遵循同一所述磁信号感应线圈单元上的磁感应线圈在任意位置不连续出现参与两两排列组合。所述水平编码阵列和垂直编码阵列中任意位置相邻的两个磁感应线圈的两两排列组合是唯一的。有益效果如下:这种磁信号定位感应器的磁信号线圈单元由多个磁感应通道线圈串联而成,每一个串联磁信号感应线圈单元可以同时检测多个位置的交变磁信号源,这样电磁感应通道线圈的引出线的布线就更加简单,磁信号定位感应器对交变此信号源的扫描检测锁定时间短,速度快,定位感应的精度高、长距离移动累积误差小和装置和排线简单清楚。附图说明为了更清楚地说明本发明实施例或现有技术中的技术方案,下面将对实施例或现有技术描述中所需要使用的附图作简单地介绍,显而易见地,下面描述中的附图仅仅是本发明的一些实施例,对于本领域普通技术人员来讲,在不付出创造性劳动的前提下,还可以根据这些附图示出的结构获得其他的附图。图1本发明整体结构示意图图2为本发明磁信号感应组件结构示意图图3为本发明差分线设置在有效区内的磁感应单元结构示意图。图4为本发明差分线设置在有效区外的磁感应单元结构示意图。图5为本发明差分线设置在有效区内的水平阵列编码结构示意图。图6为本发明差分线设置在有效区内的垂直阵列编码结构示意图。图7为本发明差分线设置在有效区内的感应元件示意图。图8为本发明差分线设置在有效区外的水平阵列编码结构示意图。图9为本发明差分线设置在有效区外的垂直阵列编码结构示意图。图10为本发明差分线设置在有效区外的感应元件示意图。图11为本发明其他一种实施例结构示意图。具体实施方式下面将结合本发明实施例中的附图,对本发明实施例中的技术方案进行清楚、完整地描述,显然,所描述的实施例仅仅是本发明的一部分实施例,而不是全部的实施例。基于本发明中的实施例,本领域普通技术人员在没有作出创造性劳动前提下所获得的所有其他实施例,都属于本发明保护的范围。需要说明,本发明实施例中所有方向性指示(诸如上、下、左、右、前、后......)仅用于解释在某一特定姿态(如附图所示)下各部件之间的相对位置关系、运动情况等,如果该特定姿态发生改变时,则该方向性指示也相应地随之改变。在本发明中如涉及“第一”、“第二”等的描述仅用于描述目的,而不能理解为指示或暗示其相对重要性或者隐含指明所指示的技术特征的数量。由此,限定有“第一”、“第二”的特征可以明示或者隐含地包括至少一个该特征。在本发明的描述中,“多个”的含义是至少两个,例如两个,三个等,除非另有明确具体的限定。在本发明中,除非另有明确的规定和限定,术语“连接”、“固定”等应做广义理解,例如,“固定”可以是固定连接,也可以是可拆卸连接,或成一体;可以是机械连接,也可以是电连接;可以是直接相连,也可以通过中间媒介间接相连,可以是两个元件内部的连通或两个元件的相互作用关系,除非另有明确的限定。对于本领域的普通技术人员而言,可以根据具体情况理解上述术语在本发明中的具体含义。另外,本发明各个实施例之间的技术方案可以相互结合,但是必须是以本领域普通技术人员能够实现为基础,当技术方案的结合出现相互矛盾或无法实现时应当认为这种技术方案的结合不存在,也不在本发明要求的保护范围之内。一种手写输入装置,包括显示组件,设置在所述显示组件前面或者后面距离显示组件100毫米范围内任意位置的磁信号感应组件,与所述磁信号感应组件对应设置的磁信号输出件,上述所有部件均设置在外壳中,所述外壳内还设有主板;其特征在于,所述磁信号感应组件包括感应元件和连接所述感应元件的检测控制电路,所述感应元件包括:水平编码阵列、与所述水平编码阵列垂直设置的垂直编码阵列,所述水平编码阵列与所述垂直编码阵列均由磁信号感应线圈单元组成。所述水平编码阵列由一个以上的磁信号感应线圈单元组成;所述垂直编码阵列由一个以上的磁信号感应线圈单元组成;所述磁信号感应线圈单元由至少两个磁感应线圈通过差分线串联而成;磁感应线圈由1圈到10圈的连续环形导线构成。所述磁信号感应线圈单元中串联磁感应线圈的差分线在磁感应定位有效区内。所述磁信号感应线圈单元中串联磁感应线圈的差分线在磁感应定位有效区外。所述检测控制电路包括多选一阵列开关、前级信号放大器、可控增益放大器、带通放大器、交直流变换器、积分电路、直流放大器、充放电开关和处理器;其中,所述多选一阵列开关一侧分别与所述水平磁感应线圈和所述垂直磁感应线圈连接,所述多选一阵列开关另一侧与所述前级放大器连接,所述前级放大器与所述可控增益放大器连接;所述可控增益放大器一端通向所述处理器,所述可控增益放大器另一端通向所述带通放大器,所述带通放大器通过所述交直流变换器与所述积分电路连接;所述积分电路一端通过直流放大器通向所述处理器,所述积分电路另一端通向所述充放电开关,所述处理器分别通向所述多选一阵列开关和所述充放电开关。所述显示组件与所述磁信号感应组件之间还设有中间件。所述磁信号输出件为电磁触控笔,所述电磁触控笔首端为交变电磁信号源。设置在所述水平编码阵列中的磁信号感应线圈与所述垂直编码阵列中的磁信号感应线圈相互交叉排列组合设置。排列组合设置为:水平编码阵列和垂直编码阵列中任意磁信号感应线圈单元上任意磁信号感应圈与相邻前或相邻后其它的磁信号感应线圈单元上的磁感应线圈的两两排列组合不与其它位置上的两两排列组合重复;并同时遵循同一所述磁信号感应线圈单元上的磁感应线圈在任意位置不连续出现参与两两排列组合。所述水平编码阵列和垂直编码阵列中任意位置相邻的两个磁感应线圈的两两排列组合是唯一的。所述磁感应线圈的材质为合金材料,该合金材料由以下质量配比的合金制成:(fexco1-x)a(ni1-y-zalycez)bcucbdsiecrf,其中a=30-60,b=30-55,c=1-5,d=1-8,e=1-5,f=1-5,x=0.1-0.8,y=0.1-0.5,z=0.01-0.08;该合金的制备方法包括以下步骤:步骤一,纳米合金粉体的制备:采用铁粉、镍粉、铬粉和铜粉作为基础粉体;所采用的铁粉的颗粒度60~100μm,纯度≥99%;镍粉的颗粒度为3~6μm,纯度>99%;铬粉的颗粒度80~120μm,纯度≥99.9%;铜粉的颗粒度为50~130μm,纯度≥99.9%;所述铁粉、镍粉、铬粉和铜粉的质量比为20-40∶15-30∶1-6∶1-5,配置成混合粉末,加入无水乙醇搅拌均匀,放入密封罐后,在行星式球磨机上于常温下进行星式球磨,球磨时间为100-190h,获得颗粒尺寸为1-10nm的fe-ni-cu-cr纳米合金粉末,所述基础粉体与无水乙醇的质量比为1-2∶0.5-3;步骤二,合金粉体基体的制备按照合金的质量配比将步骤一所得到的纳米合金粉体进行干燥后加入粉体si、al、co、ce和b,将上述原料放入真空感应炉中,在1000-1500℃下进行熔炼,反复熔炼2-4次,每次熔炼30-120min,熔炼完毕后,在氦气的保护下进行铸坯,冷却后得到合金铸锭,将冷却后的合金铸锭,放入密封罐后,在行星式球磨机上于常温下进行星式球磨,球磨的时间为50-200h,球磨得到粒度为小于15nm的合金粉体基体;所述si,al,co,ce和b的纯度达到99.8%以上,si粒径为粒径为10-100μm,al的粒径为10-80μm,co的粒径为10-120μm,ce的粒径为10-90μm,b的粒径为10-110μm;步骤三,烧结将步骤二所制得的合金粉体基体在氩气气氛烧结炉中烧结成型,在烧结过程,首先以10-15℃/min的升温速率在400-500℃预烧1-3h,然后以30-40℃/min的升温速率在1250-1350℃烧结5-8h得到基础合金;步骤四,淬火将步骤三烧结的基础合金置于淬火炉内进行淬火处理,首先在淬火温度为1100-1200℃保温时间15-25min,之后在5-10min内降温至50-80℃保温时间30-40min;步骤五,退火处理将步骤四淬火得到的基础合金置于氩气气氛的退火炉中,首先加热到450-455℃,保温1-2h,再次加热到525-535℃,保温2-3h,然后加热到720℃,保温3-4h,停止加热,在30-40min内将温度降至150-170℃,然后自然冷却至室温得到合金;步骤六,加工将步骤五所制得的合金进行切割加工制得所需形状的线圈。该实施例的优选合金的配比为:(fe0.6co0.4)50(ni0.65al0.3ce0.05)35cu3b6si3cr3;更加优选该合金的结构为:该合金形成了α-fe相、掺杂co的α-fe相和非晶相组成,其中α-fe相和掺杂co的α-fe相组成第一相,第一相中α-fe相和掺杂co的α-fe相的颗粒尺寸在1-15nm之间,第一相与非晶相之间形成了一个界面相,其中第一相的饱和磁化强度约为1.52t,相界面为一个厚度为1-1.5nm的界面,其中ni在第一相中的含量为在非晶相中的含量的1.5倍。步骤一中,优选的球磨时间为152h。步骤五中更加优选,将步骤四淬火得到的基础合金置于氩气气氛的退火炉中,首先加热至455℃,保温1.5h,之后再次加热至530℃,保温2.5h,然后加热到720℃,保温3.5h,停止加热,在30-40min内将温度降至150-170℃,然后自然冷却至室温得到合金。实施例1如图1、图2、图3和图5~图7所示,一种手写输入装置,包括显示组件801,设置在显示组件801上任意位置的磁信号感应组件,与磁信号感应组件对应设置的磁信号输出件,上述所有部件均设置在外壳中,外壳内还设有主板;其中,磁信号感应组件包括感应元件100和连接感应元件的检测控制电路10,感应元件100透过连接器插接或直接热压焊接到检测控制电路,感应元件100包括:水平编码阵列1010与水平编码阵列1010垂直设置的垂直编码阵列1011,水平编码阵列1010与垂直编码阵列1011均由磁信号感应线圈单元组成。优选地,磁信号感应线圈单元(图3)由至少两个磁感应线圈101通过差分线102串联而成。磁信号感应线圈101由1圈到10圈连续环形导线构成;磁信号感应线圈单元(图3)的磁感应线圈101之间的差分线102设置在磁感应定位有效区118内。优选地,检测控制电路10包括多选一阵列开关103、前级信号放大器104、可控增益放大器105、带通放大器106、交直流变换器107、积分电路108、直流放大器109、充放电开关112和处理器110;其中,多选一阵列开关103一侧分别与水平磁感应线圈单元1010和垂直磁感应线圈单元1011连接,多选一阵列开关103另一侧与前级放大器104连接,前级放大器104与可控增益放大器105连接;可控增益放大器105一端通向处理器110,可控增益放大器105另一端通向带通放大器106,带通放大器106通过交直流变换器107与积分电路108连接;积分电路108一端通过直流放大器109通向处理器110,积分电路108另一端通向充放电开关112,处理器110分别通向多选一阵列开关103和充放电开关112;所述检测控制电路10依次扫描接入水平编码阵列1000和垂直编码阵列1001的水平磁信号感应线圈单元1010和垂直磁信号感应线圈单元1011,对磁信号感应线圈单元的磁互感信号依次进行限幅限频放大,对最终放大信号进行交直流变换。变换后的直流电平受控制对积分电路108进行定期放电和充电,单位时间内对积分电路108充电的有无与高低,直接对应判定磁信号感应线圈单元101的磁互感信号的有无与强弱,越强判定越靠近交变磁信号源117。优选地,显示组件801与磁信号感应组件之间还设有中间件803。显示组件801设置在靠近使用者一端,磁信号感应组件设置在远离使用者一端,中间件803可以不设置,或者设置任意不整面导电的金属结构件。优选地,磁信号输出件为电磁触控笔802,电磁触控笔802首端设有交变电磁信号源117。优选地,设置在水平编码阵列1010中的磁信号感应线圈101与垂直编码阵列1011中的磁信号感应线圈101相互交叉排列组合设置。优选地,排列组合设置为:同一磁信号感应线圈单元(图3)上任意位置的磁信号感应线圈101与相邻前或相邻后其它与之串联的磁信号感应线圈101的两两排列组合不与其它位置上的两两排列组合重复。并同时遵循同一串联磁信号感应线圈单元(图3)上的磁感应线圈101在任意位置不连续出现参与两两排列组合。优选地,在水平编码阵列1010中和垂直编码阵列1011中任意相邻的两个磁感应线圈101的两两排列组合在同一阵列里是唯一的;水平编码阵列1010和垂直编码阵列1011相邻磁感应线圈101的两两排列组合可以一样。所述磁感应线圈的材质为合金材料,该合金材料由以下质量配比的合金制成:(fexcol-x)a(nil-y-zalycez)bcucbdsiecrf,其中a=30-60,b=30-55,c=1-5,d=1-8,e=1-5,f=1-5,x=0.1-0.8,y=0.1-0.5,z=0.01-0.08;该合金的制备方法包括以下步骤:步骤一,纳米合金粉体的制备:采用铁粉、镍粉、铬粉和铜粉作为基础粉体;所采用的铁粉的颗粒度60~100μm,纯度≥99%;镍粉的颗粒度为3~6μm,纯度>99%;铬粉的颗粒度80~120μm,纯度≥99.9%;铜粉的颗粒度为50~130μm,纯度≥99.9%;所述铁粉、镍粉、铬粉和铜粉的质量比为20-40∶15-30∶1-6∶1-5,配置成混合粉末,加入无水乙醇搅拌均匀,放入密封罐后,在行星式球磨机上于常温下进行星式球磨,球磨时间为100-190h,获得颗粒尺寸为1-10nm的fe-ni-cu-cr纳米合金粉末,所述基础粉体与无水乙醇的质量比为1-2∶0.5-3;步骤二,合金粉体基体的制备按照合金的质量配比将步骤一所得到的纳米合金粉体进行干燥后加入粉体si、al、co、ce和b,将上述原料放入真空感应炉中,在1000-1500℃下进行熔炼,反复熔炼2-4次,每次熔炼30-120min,熔炼完毕后,在氦气的保护下进行铸坯,冷却后得到合金铸锭,将冷却后的合金铸锭,放入密封罐后,在行星式球磨机上于常温下进行星式球磨,球磨的时间为50-200h,球磨得到粒度为小于15nm的合金粉体基体;所述si,al,co,ce和b的纯度达到99.8%以上,si粒径为粒径为10-100μm,al的粒径为10-80μm,co的粒径为10-120μm,ce的粒径为10-90μm,b的粒径为10-110μm;步骤三,烧结将步骤二所制得的合金粉体基体在氩气气氛烧结炉中烧结成型,在烧结过程,首先以10-15℃/min的升温速率在400-500℃预烧1-3h,然后以30-40℃/min的升温速率在1250-1350℃烧结5-8h得到基础合金;步骤四,淬火将步骤三烧结的基础合金置于淬火炉内进行淬火处理,首先在淬火温度为1100-1200℃保温时间15-25min,之后在5-10min内降温至50-80℃保温时间30-40min;步骤五,退火处理将步骤四淬火得到的基础合金置于氩气气氛的退火炉中,首先加热到450-455℃,保温1-2h,再次加热到525-535℃,保温2-3h,然后加热到720℃,保温3-4h,停止加热,在30-40min内将温度降至150-170℃,然后自然冷却至室温得到合金;步骤六,加工将步骤五所制得的合金进行切割加工制得所需形状的线圈。该实施例的优选合金的配比为:(fe0.6co0.4)50(ni0.65al0.3ce0.05)35cu3b6si3cr3;更加优选该合金的结构为:该合金形成了α-fe相、掺杂co的α-fe相和非晶相组成,其中α-fe相和掺杂co的α-fe相组成第一相,第一相中α-fe相和掺杂co的α-fe相的颗粒尺寸在1-15nm之间,第一相与非晶相之间形成了一个界面相,其中第一相的饱和磁化强度约为1.52t,相界面为一个厚度为1-1.5nm的界面,其中ni在第一相中的含量为在非晶相中的含量的1.5倍。步骤一中,优选的球磨时间为152h。步骤五中更加优选,将步骤四淬火得到的基础合金置于氩气气氛的退火炉中,首先加热至455℃,保温1.5h,之后再次加热至530℃,保温2.5h,然后加热到720℃,保温3.5h,停止加热,在30-40min内将温度降至150-170℃,然后自然冷却至室温得到合金。【性能测试】(一)步骤一所制得的纳米合金粉体采用日本rikendenshi公司modeibhv-525型振动样品磁强计(vsm)测量样品的磁性能。1、通过研究球磨后的xrd谱线发现,在球磨至一段时间后ni、cr和cu的衍射峰将出现基本消失的情形,这是由于随着球磨时间的增加,fe形成过饱和固溶体,晶体的完整性受到破坏,使得参与衍射的晶粒减少而导致峰高逐渐降低,ni、cr和cu的衍射峰降低直至基本消失,说明ni、cr和cu固溶于fe中,形成fe的过饱和固溶体,研究还发现这种情形的出现,对于cr含量和球磨时间是成反比的;但是球磨后期的颗粒硬化,内应力增大,当达到弹性极限时,颗粒开始碎化,在粉末不断细化的同时,伴随着粉末团聚现象的产生,这是由于球磨过程中,形成了很多纳米级粉末,而尺寸达到纳米级的粉末的表面能和吸附能增加,从而造成团聚现象,因此该在该配比下最佳的球磨时间为152h;2、如表1所述随着cr含量的上升fe-ni-cu-cr的合金的饱和磁化强度先上升后下降,在cr含量为3-6%时达到最大值,5%时达到最大值172(σs/a·m2·kg-1);这是因为,当cr含量增加,会导致合金中长程有序铁磁性相增加,但是cr元素不具有磁矩,所以比饱和磁化强度随着cr含量的增加先上升后下降的情形;随着cr含量的上升该合金的磁导率变化量实现先上升后下降的趋势,得到含量为5%时为饱和磁化强度与磁导率最优的配比。表1纳米合金粉体的性能测试cr含量饱和磁化强度(σs/a·m2·kg-1)磁导率增长量0%1240%1%1471%3%1512%5%1723%7%1501.5%9%131-1%(二)(1)制备过程中加入了铈,使得合金中含有ce元素对ni进行了掺杂,研究发现由于合金中同时含有cr、ni等大原子,当大原子与小原子组合形成合金时候,则能够生成一种金属间化合物laves相,它的不同尺寸原子以最致密的方式堆垛在晶胞中,其硬度较高,有显著的强化作用,随着ce元素的增加,合金中硬质相增加,促使合金中的固溶体组织均匀细化,导致合金在外力的作用下不易折断和剥落,研究发现含有ce的合金经过摩擦后合金表面显得光滑平整,说明摩擦基体对硬质相的支持保护作用加大,硬相不易剥离和脱落,因而提高了抗磨损的能力,磨损量减少,耐磨性比未加ce的合金提高20%~30%以上,并且增加ce的含量引起合金体中的奥氏体含量降低,能够有效改善合金表面的微观结构,从而提高合金的耐腐蚀性能;但是还发现随着ce含量的增加至一定程度后,合金中的耐摩擦性能和耐腐蚀性能增强,但是磁导率呈现下降的趋势,这是由于ce增加到一定程度后对于合金的晶粒大小的细化作用减小达到瓶颈,因此随着ce含量的增加对于耐摩擦性能增长变缓,如表2所述当ce含量为1.75%时候为最佳配比,其中合金的配比为(fe0.6co0.4)50(ni0.65al0.3ce0.05)35cu3b6si3cr3。磨损试验:在rrt2iii型往复式摩擦磨损机上进行,磨损试验试样的对偶件为70mm×1317mm×10mm白刚玉砂条,粒度为200目,试样表面粗糙度在018~014μm之间。测试速度150r/s,测试压力28mpa,测试时间10min,每个试样测试次数1600-1800次,测试行程75m,室温20-25℃,湿度23-26%,无润滑干摩擦试验,磨损量用万用电子分析天平测试。未添加ce的合金磨损量为0.019/mg;腐蚀试验:腐蚀介质选取h2so4(5%)、hcl(5%)和naoh(5%),试样均在微沸状态下腐蚀24h,采用失重法进行腐蚀试验,试样先要打磨抛光,在腐蚀前后用丙酮浸泡、酒精清洗、吹风机吹干后用万分之一天平称腐蚀前后的重量,腐蚀率。表2合金性能测试(三)步骤三中经过二次加热处理进行烧结,首先进行预热之后升温进行正式烧结。经过研究发现二次加热处理后的初始磁导率要比一次预热处理后的初始磁导率要好,其磁导率要高于单次加热的合金5-10%,,随温度的升高,合金发生结构驰豫,向稳定的低内能状态转变。并且二次加热工艺的加热速率也需要远远高于第一次预热工艺的加热速率:“首先以10-15℃/min的升温速率在400-500℃预烧1-3h,然后以30-40℃/min的升温速率在1250-1350℃烧结5-8h”优选“首先以12℃/min的升温速率在400-500℃预烧2h,然后以35℃/min的升温速率在1250-1350℃烧结7h”,第二次加热速率几乎三倍于第一次的加热速率,通过研究发现由于之前的预热已经使得合金体具有一定的适应能力,通过快速升温,使得材料的合金迅速且结晶更加充分,晶粒间的耦合作用更强,从而材料的有效各向异性常数更低,初始磁导率更高。经过实验得知,采用二次加热处理进行烧结后的合金初始磁导率要高于单次加热处理进行烧结后的合金初始磁导率3-7%,采用第二次加热速率三倍于第一次的加热速率后得到的合金的初始磁导率相较于普通二次加热处理进行烧结后的合金初始磁导率提高4-8%;(四)本发明中的淬火步骤中的第二阶段采用了快速的淬火步骤,通过研究发现,采用了快速的淬火步骤能够使得合金的性能更加优质,能提高合金的冲击韧性值及硬度值,且对于磁性能并无影响,该合金在急冷过程中,其材料的内部结构发生相变增韧,ce元素能够部分熔解,使得在粘结相中的ce在急冷情况下来不及析出,起到了固熔强化的作用,能大幅度提高了该合金的冲击韧性及硬度值。冲击韧性能够达到0.72-0.89mj/m2,其中经过综合考虑当合金材料的配比为:其中合金的配比为(fe0.6co0.4)50(ni0.65al0.3ce0.05)35cu3b6si3cr3,时ce含量约为1.75%时的冲击韧性以及各项性能达到最佳,冲击韧性为0.85mj/m2,洛氏硬度值为38hrc。(五)经过退火步骤后该合金形成了α-fe相、掺杂co的α-fe相和非晶相组成,其中α-fe相和掺杂co的α-fe相组成第一相,第一相中α-fe相和掺杂co的α-fe相的颗粒尺寸在1-15nm之间,第一相与非晶相之间形成了一个界面相,其中第一相的饱和磁化强度约为1.52t,相界面为一个厚度为1-1.5nm的界面,其中ni在第一相中的含量为在非晶相中的含量的1.5倍;本发明创造性的首先制备纳米合金粉体,之后加入金属进行熔炼,这样使得ni能够进入至由α-fe相和掺杂co的α-fe相组成的第一相中,经过研究发现当ni在第一相中的含量为在非晶相中的含量的1.5倍时该合金的饱和磁化强度最大,其合金的饱和磁化强度约为1.57t。(1)步骤五中的退火温度对于合金的晶粒直径有一定影响。在合金加热过程中,由于存在不同的金属元素,经过研究发现首先加热至455℃,保温1.5h,先使得第一相中的元素优先成核,之后再次加热至530℃,保温2.5h,然后加热到720℃,保温3.5h,使得非晶相此时能够得到均匀细小纳米结构。如果再次升温后发现当温度升高到750℃时,晶粒尺寸急剧长大,其使磁各向异性增加,同时大晶粒对畴壁的位移、磁矩转动起阻碍作用。因此本发明采用最佳的退火温度为“首先加热至455℃,保温1.5h,先使得第一相中的元素优先成核,之后再次加热至530℃,保温2.5h,然后加热到720℃,保温3.5h”。(2)研究发现在进行退火的过程中需要进行保温程序,但是保温的时间与本发明合金的磁性能具有很大的关系,随着保温时间的延长,磁性能下降。由于在合金的内部存在很大的内应力,且不同部位固化推进方式不同而形成区域应力场,在720℃保温3-4h后(最佳保温时间为3.5h),合金的内应力可以达到充分的释放,磁晶各相异性能降低,合金内部的亚稳定结构趋于稳定,而使合金表现出优良的软磁性能。但在720℃保温超过4h后,由于出现了恶化磁性能的析出相,导致合金磁性能下降。实施例2参照图1、图2、图4和图8~图11,与实施例的不同之处在于,差分线102设置在磁信号定位有效区118外,磁感应线圈2为透明或者不透明导电材质,材质和实施例1中的材质相同,水平编码阵列1010与水平编码阵列1011的磁感应线圈101设置在不同的装置内。显示组件801设置在远离使用者一端,磁信号感应组件的感应元件100的书写背面,两者中间件为任意透明构件,有利于磁信号感应组件的感应元件100设置在显示组件801的正前面。工作原理如下:参照图7和图10,电磁触控笔上的交变磁信号源117,靠近磁信号感应组件中的水平编码阵列1010,水平编码阵列1010中靠近交变磁信号源117的几个相邻磁感应线圈101,例如:x1、x5、x7与交变磁信号源117互感产生磁互感信号。产生此磁互感信号的几个相邻水平磁感应线圈101,如x1、x5、x7的组合编码为x5x1、x5x7、x7x5、x1x5x7或x7x5x1,该组合编码为当前交变磁信号源117在水平编码阵列1010核磁信号定位有效区118中的水平坐标编码,产生磁互感信号越强的磁感应线圈101判定越靠近交变磁信号源117。同理,交变磁信号源117靠近垂直编码阵列1011,垂直垂直编码阵列1011中靠近交变磁信号源117的几个相邻的磁感应线圈单元(图3),例如y6、y2、y4与交变磁信号源117互感产生磁互感信号。产生此磁互感信号的几个相邻的磁感应线圈101如y6、y2、y4的组合编码为y6y2,y2y6,y2y4,y4y2,y6y2y4或y4y2y6,该组合编码为当前交变磁信号源117在垂直编码阵列1011和磁信号定位有效区118中的垂直坐标编码,产生磁互感信号越强的磁感应线圈101判定越靠近交变磁信号源117。靠近交变磁信号源117的几个相邻磁感应线圈101的x1、x5、x7或y6、y2、y4的组合编码x1x5,x5x1,x5x7,x7x5,x1x5x7或x7x5x1和y6y2,y2y6,y2y4,y4y2,y6y2y4或y4y2y6,代表交变磁信号源117在感应元件100的检测磁信号定位有效区118水平方向和垂直方向的大致绝对坐标位置。交变磁信号源117判定在大致绝对坐标位置处磁互感信号最强那个磁感应线圈101,如x1x5x7的x5和y6y2y4的y2位置,再根据最强磁感应线圈两侧的磁感应线圈的感应磁互感信号强度的比值判定交变磁信号源117在最强磁感应线圈x1x5x7的x5和y6y2y4的y2通道所在区域内相对两侧磁感应线圈101的精细相对位置。最强磁感应线圈x5和y2两侧的磁感应线圈x1,x7和y6,y4磁互感信号强度的比值为1∶1代表交变磁信号源117在最强磁感应线圈x5和y2通道的中心位置,大于1∶1则判定交变磁信号源117在最强磁感应线圈x5和y2通道所在区域内并偏向一侧的次强磁感应线圈,偏移的距离跟这个比值成正比,小于1∶1则判定交变磁信号源117在最强磁感应线圈x5和y2通道所在区域内并偏向另一侧的次强磁感应线圈单元,偏移的距离跟这个比值成反比。精准的定位信息从磁信号感应组件通过主板传递到显示组件上进行显示,可以对使用者通过电磁触控笔所表达出来的位置信息进行精准的表达。所述磁感应线圈的材质为合金材料,该合金材料由以下质量配比的合金制成:(fexco1-x)a(ni1-y-zalycez)bcucbdsiecrf,其中a=30-60,b=30-55,c=1-5,d=1-8,e=1-5,f=1-5,x=0.1-0.8,y=0.1-0.5,z=0.01-0.08;该合金的制备方法包括以下步骤:步骤一,纳米合金粉体的制备:采用铁粉、镍粉、铬粉和铜粉作为基础粉体;所采用的铁粉的颗粒度60~100μm,纯度≥99%;镍粉的颗粒度为3~6μm,纯度>99%;铬粉的颗粒度80~120μm,纯度≥99.9%;铜粉的颗粒度为50~130μm,纯度≥99.9%;所述铁粉、镍粉、铬粉和铜粉的质量比为20-40∶15-30∶1-6∶1-5,配置成混合粉末,加入无水乙醇搅拌均匀,放入密封罐后,在行星式球磨机上于常温下进行星式球磨,球磨时间为100-190h,获得颗粒尺寸为1-10nm的fe-ni-cu-cr纳米合金粉末,所述基础粉体与无水乙醇的质量比为1-2∶0.5-3;步骤二,合金粉体基体的制备按照合金的质量配比将步骤一所得到的纳米合金粉体进行干燥后加入粉体si、al、co、ce和b,将上述原料放入真空感应炉中,在1000-1500℃下进行熔炼,反复熔炼2-4次,每次熔炼30-120min,熔炼完毕后,在氦气的保护下进行铸坯,冷却后得到合金铸锭,将冷却后的合金铸锭,放入密封罐后,在行星式球磨机上于常温下进行星式球磨,球磨的时间为50-200h,球磨得到粒度为小于15nm的合金粉体基体;所述si,al,co,ce和b的纯度达到99.8%以上,si粒径为粒径为10-100μm,al的粒径为10-80μm,co的粒径为10-120μm,ce的粒径为10-90μm,b的粒径为10-110μm;步骤三,烧结将步骤二所制得的合金粉体基体在氩气气氛烧结炉中烧结成型,在烧结过程,首先以10-15℃/min的升温速率在400-500℃预烧1-3h,然后以30-40℃/min的升温速率在1250-1350℃烧结5-8h得到基础合金;步骤四,淬火将步骤三烧结的基础合金置于淬火炉内进行淬火处理,首先在淬火温度为1100-1200℃保温时间15-25min,之后在5-10min内降温至50-80℃保温时间30-40min;步骤五,退火处理将步骤四淬火得到的基础合金置于氩气气氛的退火炉中,首先加热到450-455℃,保温1-2h,再次加热到525-535℃,保温2-3h,然后加热到720℃,保温3-4h,停止加热,在30-40min内将温度降至150-170℃,然后自然冷却至室温得到合金;步骤六,加工将步骤五所制得的合金进行切割加工制得所需形状的线圈。该实施例的优选合金的配比为:(fe0.6co0.4)50(ni0.65al0.3ce0.05)35cu3b6si3cr3;更加优选该合金的结构为:该合金形成了α-fe相、掺杂co的α-fe相和非晶相组成,其中α-fe相和掺杂co的α-fe相组成第一相,第一相中α-fe相和掺杂co的α-fe相的颗粒尺寸在1-15nm之间,第一相与非晶相之间形成了一个界面相,其中第一相的饱和磁化强度约为1.52t,相界面为一个厚度为1-1.5nm的界面,其中ni在第一相中的含量为在非晶相中的含量的1.5倍。步骤一中,优选的球磨时间为152h。步骤五中更加优选,将步骤四淬火得到的基础合金置于氩气气氛的退火炉中,首先加热至455℃,保温1.5h,之后再次加热至530℃,保温2.5h,然后加热到720℃,保温3.5h,停止加热,在30-40min内将温度降至150-170℃,然后自然冷却至室温得到合金。【性能测试】(一)步骤一所制得的纳米合金粉体采用日本rikendenshi公司modeibhv-525型振动样品磁强计(vsm)测量样品的磁性能。1、通过研究球磨后的xrd谱线发现,在球磨至一段时间后ni、cr和cu的衍射峰将出现基本消失的情形,这是由于随着球磨时间的增加,fe形成过饱和固溶体,晶体的完整性受到破坏,使得参与衍射的晶粒减少而导致峰高逐渐降低,ni、cr和cu的衍射峰降低直至基本消失,说明ni、cr和cu固溶于fe中,形成fe的过饱和固溶体,研究还发现这种情形的出现,对于cr含量和球磨时间是成反比的;但是球磨后期的颗粒硬化,内应力增大,当达到弹性极限时,颗粒开始碎化,在粉末不断细化的同时,伴随着粉末团聚现象的产生,这是由于球磨过程中,形成了很多纳米级粉末,而尺寸达到纳米级的粉末的表面能和吸附能增加,从而造成团聚现象,因此该在该配比下最佳的球磨时间为152h;2、如表1所述随着cr含量的上升fe-ni-cu-cr的合金的饱和磁化强度先上升后下降,在cr含量为3-6%时达到最大值,5%时达到最大值172(σs/a·m2·kg-1);这是因为,当cr含量增加,会导致合金中长程有序铁磁性相增加,但是cr元素不具有磁矩,所以比饱和磁化强度随着cr含量的增加先上升后下降的情形;随着cr含量的上升该合金的磁导率变化量实现先上升后下降的趋势,得到含量为5%时为饱和磁化强度与磁导率最优的配比。表1纳米合金粉体的性能测试cr含量饱和磁化强度(σs/a·m2·kg-1)磁导率增长量0%1240%1%1471%3%1512%5%1723%7%1501.5%9%131-1%(二)(1)制备过程中加入了铈,使得合金中含有ce元素对ni进行了掺杂,研究发现由于合金中同时含有cr、ni等大原子,当大原子与小原子组合形成合金时候,则能够生成一种金属间化合物laves相,它的不同尺寸原子以最致密的方式堆垛在晶胞中,其硬度较高,有显著的强化作用,随着ce元素的增加,合金中硬质相增加,促使合金中的固溶体组织均匀细化,导致合金在外力的作用下不易折断和剥落,研究发现含有ce的合金经过摩擦后合金表面显得光滑平整,说明摩擦基体对硬质相的支持保护作用加大,硬相不易剥离和脱落,因而提高了抗磨损的能力,磨损量减少,耐磨性比未加ce的合金提高20%~30%以上,并且增加ce的含量引起合金体中的奥氏体含量降低,能够有效改善合金表面的微观结构,从而提高合金的耐腐蚀性能;但是还发现随着ce含量的增加至一定程度后,合金中的耐摩擦性能和耐腐蚀性能增强,但是磁导率呈现下降的趋势,这是由于ce增加到一定程度后对于合金的晶粒大小的细化作用减小达到瓶颈,因此随着ce含量的增加对于耐摩擦性能增长变缓,如表2所述当ce含量为1.75%时候为最佳配比,其中合金的配比为(fe0.6co0.4)50(ni0.65al0.3ce0.05)35cu3b6si3cr3。磨损试验:在rrt2iii型往复式摩擦磨损机上进行,磨损试验试样的对偶件为70mm×1317mm×10mm白刚玉砂条,粒度为200目,试样表面粗糙度在018~014μm之间。测试速度150r/s,测试压力28mpa,测试时间10min,每个试样测试次数1600-1800次,测试行程75m,室温20-25℃,湿度23-26%,无润滑干摩擦试验,磨损量用万用电子分析天平测试。未添加ce的合金磨损量为0.019/mg;腐蚀试验:腐蚀介质选取h2so4(5%)、hcl(5%)和naoh(5%),试样均在微沸状态下腐蚀24h,采用失重法进行腐蚀试验,试样先要打磨抛光,在腐蚀前后用丙酮浸泡、酒精清洗、吹风机吹干后用万分之一天平称腐蚀前后的重量,腐蚀率。表2合金性能测试(三)步骤三中经过二次加热处理进行烧结,首先进行预热之后升温进行正式烧结。经过研究发现二次加热处理后的初始磁导率要比一次预热处理后的初始磁导率要好,其磁导率要高于单次加热的合金5-10%,,随温度的升高,合金发生结构驰豫,向稳定的低内能状态转变。并且二次加热工艺的加热速率也需要远远高于第一次预热工艺的加热速率:“首先以10-15℃/min的升温速率在400-500℃预烧1-3h,然后以30-40℃/min的升温速率在1250-1350℃烧结5-8h”优选“首先以12℃/min的升温速率在400-500℃预烧2h,然后以35℃/min的升温速率在1250-1350℃烧结7h”,第二次加热速率几乎三倍于第一次的加热速率,通过研究发现由于之前的预热已经使得合金体具有一定的适应能力,通过快速升温,使得材料的合金迅速且结晶更加充分,晶粒间的耦合作用更强,从而材料的有效各向异性常数更低,初始磁导率更高。经过实验得知,采用二次加热处理进行烧结后的合金初始磁导率要高于单次加热处理进行烧结后的合金初始磁导率3-7%,采用第二次加热速率三倍于第一次的加热速率后得到的合金的初始磁导率相较于普通二次加热处理进行烧结后的合金初始磁导率提高4-8%;(四)本发明中的淬火步骤中的第二阶段采用了快速的淬火步骤,通过研究发现,采用了快速的淬火步骤能够使得合金的性能更加优质,能提高合金的冲击韧性值及硬度值,且对于磁性能并无影响,该合金在急冷过程中,其材料的内部结构发生相变增韧,ce元素能够部分熔解,使得在粘结相中的ce在急冷情况下来不及析出,起到了固熔强化的作用,能大幅度提高了该合金的冲击韧性及硬度值。冲击韧性能够达到0.72-0.89mj/m2,其中经过综合考虑当合金材料的配比为:其中合金的配比为(fe0.6co0.4)50(ni0.65al0.3ce0.05)35cu3b6si3cr3,时ce含量约为1.75%时的冲击韧性以及各项性能达到最佳,冲击韧性为0.85mj/m2,洛氏硬度值为38hrc。(五)经过退火步骤后该合金形成了α-fe相、掺杂co的α-fe相和非晶相组成,其中α-fe相和掺杂co的α-fe相组成第一相,第一相中α-fe相和掺杂co的α-fe相的颗粒尺寸在1-15nm之间,第一相与非晶相之间形成了一个界面相,其中第一相的饱和磁化强度约为1.52t,相界面为一个厚度为1-1.5nm的界面,其中ni在第一相中的含量为在非晶相中的含量的1.5倍;本发明创造性的首先制备纳米合金粉体,之后加入金属进行熔炼,这样使得ni能够进入至由α-fe相和掺杂co的α-fe相组成的第一相中,经过研究发现当ni在第一相中的含量为在非晶相中的含量的1.5倍时该合金的饱和磁化强度最大,其合金的饱和磁化强度约为1.57t。(1)步骤五中的退火温度对于合金的晶粒直径有一定影响。在合金加热过程中,由于存在不同的金属元素,经过研究发现首先加热至455℃,保温1.5h,先使得第一相中的元素优先成核,之后再次加热至530℃,保温2.5h,然后加热到720℃,保温3.5h,使得非晶相此时能够得到均匀细小纳米结构。如果再次升温后发现当温度升高到750℃时,晶粒尺寸急剧长大,其使磁各向异性增加,同时大晶粒对畴壁的位移、磁矩转动起阻碍作用。因此本发明采用最佳的退火温度为“首先加热至455℃,保温1.5h,先使得第一相中的元素优先成核,之后再次加热至530℃,保温2.5h,然后加热到720℃,保温3.5h”。(2)研究发现在进行退火的过程中需要进行保温程序,但是保温的时间与本发明合金的磁性能具有很大的关系,随着保温时间的延长,磁性能下降。由于在合金的内部存在很大的内应力,且不同部位固化推进方式不同而形成区域应力场,在720℃保温3-4h后(最佳保温时间为3.5h),合金的内应力可以达到充分的释放,磁晶各相异性能降低,合金内部的亚稳定结构趋于稳定,而使合金表现出优良的软磁性能。但在720℃保温超过4h后,由于出现了恶化磁性能的析出相,导致合金磁性能下降。以上所述仅为本发明的优选实施例,并非因此限制本发明的专利范围,凡是在本发明的发明构思下,利用本发明说明书及附图内容所作的等效结构变换,或直接/间接运用在其他相关的
技术领域:
均包括在本发明的专利保护范围内。当前第1页12