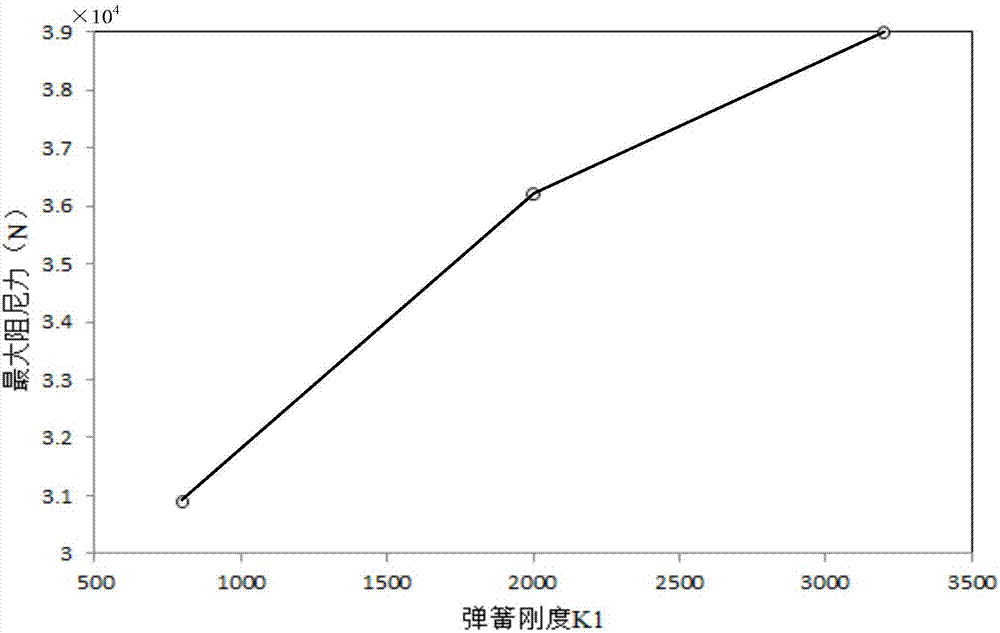
本发明涉及减振装置
技术领域:
,尤其涉及一种非线性的抗蛇形减振器的结构参数优化设计方法。
背景技术:
:目前,现在的高速铁道车辆的运营速度已经达到350km/h,但这也会使得运行工况比低速时更为恶劣,振动冲击也要更大。在保证车辆动力学性能的条件下为了获得更高的速度,许多新技术应用于高速铁路中,比如车辆轻量化技术,高平顺和高稳定性的无砟轨道。这些技术的应用都会导致车辆悬挂部件工作状况发生改变:一是悬挂部件和车辆之间相对位移振幅的降低;二是悬挂部件和车辆之间相对运动频率的增加。为了保障车辆安全及平稳运行,这就对车辆悬挂性能提出更高要求。铁道车辆的悬挂系统可以吸收和缓和道路不平顺等引起的振动和冲击,其性能的好坏将直接影响车辆的平稳性、舒适性、车辆部件的使用寿命和行车安全性。悬挂系统各元件的工作特性具有很强的非线性特征,它们对车辆运行的稳定性有着重要作用。车辆悬挂系统的非线性特性是指空气弹簧、液压减振器、抗蛇行减振器、转臂定位刚度等悬挂元件的非线性特性。悬挂系统的非线性特性中抗蛇行减振器特性参数、转臂定位刚度对铁道车辆动力学的影响相对较大。在车辆运行正常的大部分情况下,它们的工作特性可以用线性来近似描述。当然在铁道车辆通过道岔区或其它复杂工况的区间,产生较为剧烈的运动时,悬挂系统的非线性特性会影响到铁道车辆系统的动力学特性。其中非线性的抗蛇行减振器的工作会导致hopf分叉改变,通过选择合适的抗蛇行减振器后,带有大幅值的振荡会被抑制而达到更高的临界速度。液压减振器的阻尼特性是用减振力与活塞速度间的关系里描述的,因此建立的液压减振器数值模型应该尽可能准确地表达出这种关系。现在有三种建模方法:1.基于大量实验数据而建立数值模型,这种方法也称为非参数化模型。它不用考虑减振器内部结构和工作原理,仅采用图描述阻尼力与位移、速度、加速度、频率等状态变量的关系,在实际的计算时,只需查图或简单插值即可,运算速度很快。非参数化模型重点研究减振器在随机、简谐、等速和高频等各种激振方法下,其恢复力曲面使用速度.位移或是使用加速度—速度作为状态变量的准确性,目的是想在有限试验条件下能更精确地描述减振器在宽频带内的阻尼特性。2.基于减振器物理结构参数建立模型,如压力腔的体积、阀的特性、活塞截面等。这种方法的优点是模型可以应用于不同的减振器,可以修改不同物理结构参数。结果是调节模型所需的试验次数能降到最低。3.等效参数化建模。它将减振器抽象成一些如阻尼元件、弹性元件、摩擦元件、间隙元件等具有某种力学特性的典型物理元件的组合系统,通常只包括(但不仅限于)1-10个参数,在实际的计算中能保证很高的效率。为了提高减振器的性能这就需要对减振器动力学特性进行更加深入的研究,减振器结构参数的影响就是一个重要的方向。减振器性能设计的一个重要手段就是通过调整内部结构参数来实现的。液压减振器虽然结构各不相同,但基本结构参数主要是节流阀相关的初始节流孔、可变节流孔、弹簧的刚度和弹簧预压力,活塞杆的直径、减振器的两端刚度等。在现有技术中,建立非参数化模型需要进行大量的试验以获得一个精确的模型。这些试验必须要能描述减振器有可能工作时的所有操作范围。而这种情况下常常会出现减振器所产生的阻尼力不仅仅与当前的速度和位置有关,还与前面时刻的速度和位置有关。对于一些减振器来说,当不同压力腔内的压力差并没有达到一定的数值的时候油液是不会流动的,而这个时候,减振器产生的力是与零速度和位移时的零状态是不同的。这种现象就无法使用这种模型进行描述了。同时基于试验结果的模型也需要大量的结果分析,而这也是难以重复获得的,因为减振器模型会随着结构参数的变化而产生变化。建立基于减振器物理结构参数的模型,这种模型太过于复杂,而如果模型过于复杂会使得进行动力学仿真的时候效率下降,甚至会出现结果发散的现象。建立等效参数化模型,能够将减振器抽象成一些如阻尼元件、弹性元件、摩擦元件、间隙元件等具有某种力学特性的典型物理元件的组合系统,在实际的计算中能保证很高的效率,但是它的缺点在于参数的物理属性难以确定,分析结果不能应用于减振器的优化设计中。技术实现要素:针对上述问题中的至少之一,本发明提供了一种非线性的抗蛇形减振器的结构参数优化设计方法,通过从抗蛇行减振器的内部结构入手,对各种阀、活塞、油腔等元件依据流体力学的原理建立描述准确且计算高效率的抗蛇行减振器非线性液压模型。该模型可以应用于不同的减振器,可以修改不同物理结构参数。调节模型所需的试验次数能降到最低,同时还解决了模型复杂、动力学仿真时效率低甚至会出现结果发散的缺点。此外,通过在抗蛇行减振器的结构元件中选取各个元件的相关参数作为优化变量,包括节流阀的阻尼孔径、通流孔径、弹簧刚度、弹簧预紧力、活塞单向阀孔径、底阀单向阀孔径、活塞杆直径、节点刚度等,将抗蛇行减振器的非线性液压数值模型与车辆动力学模型结合,使用联合仿真的方法来分析这些结构参数对高速铁道车辆非线性稳定性的影响,从而得到最优参数。为实现上述目的,本发明提供了一种非线性的抗蛇形减振器的结构参数优化设计方法,包括:以抗蛇形减振器的阻尼调节阀、活塞单向阀和底阀建立抗蛇形减振器的非线性液压模型;采用多组不同的活塞速度分别对非线性液压模型进行动态仿真和试验,根据动态仿真和试验得出的阻尼力数据,判断非线性液压模型的精确性是否符合要求;将车辆的动力学模型中的抗蛇形减振器替换为可设定作用力和状态变量的阻尼力元件;将动力学模型中的状态变量与非线性液压模型中的作用力建立动态链接,形成联合仿真模型;对车辆进行试验,将试验的试验数据与联合仿真模型的仿真数据分别进行时域范围和频域范围的对比;根据试验数据与仿真数据的对比结果,判断联合仿真模型是否符合要求;若判定联合仿真模型符合要求,则分别对非线性液压模型中阻尼调节阀、活塞单向阀和底阀的结构参数进行调整,确定不同的结构参数对联合仿真模型的非线性稳定性的影响曲线;根据结构参数与联合仿真模型的影响曲线,确定各个结构参数的最优参数值。在上述技术方案中,优选地,所述根据动态仿真和试验得出的阻尼力数据,判断所述非线性液压模型的精确性是否符合要求具体包括:分别对非线性液压模型中阻尼调节阀、活塞单向阀和底阀的结构参数进行调整,得到不同的结构参数对非线性液压模型的阻尼特性的影响曲线,并确定结构参数对非线性液压模型的影响特性;以阻尼调节阀和活塞单向阀的结构参数为影响因素,以抗蛇形减振器的阻尼力最大值作为试验指标,在试验范围内选取三种因素进行正交试验;对正交试验的试验结果进行分析,确定各影响因素的水平变化趋势,并确定各影响因素的优选数据;在上述技术方案中,优选地,所述阻尼调节阀包括节流阀、常通孔、弹簧,所述抗蛇形减振器还包括活塞;所述阻尼调节阀、所述活塞单向阀和所述底阀的结构参数包括:所述节流阀的阻尼孔径、所述弹簧的弹簧刚度、所述弹簧的预紧力、所述常通孔的通流孔径,所述活塞单向阀的孔径、所述底阀的底阀单向阀孔径、所述活塞的活塞杆直径以及所述抗蛇形减振器与车辆车体的相连节点的节点刚度。在上述技术方案中,优选地,所述正交试验的影响因素包括所述节流阀的阻尼孔径、所述常通孔的通流孔径、所述弹簧的弹簧刚度、所述弹簧的预紧力和所述活塞单向阀的孔径。在上述技术方案中,优选地,所述对所述正交试验的试验结果进行分析,确定各影响因素的水平变化趋势,并确定各影响因素的优选数据具体包括:将每个影响因素按照不同水平确定试验组;计算每个影响因素下不同试验组的所述抗蛇形减振器的阻尼力最大值之和,以及所有试验组的阻尼力最大值的总和;计算每个影响因素下不同试验组中阻尼力最大值之和之间的极差,并根据所述极差值确定各影响因素的影响主次顺序;根据所述每个影响因素的不同试验组中阻尼力最大值之和,确定各影响因素的优选数据。在上述技术方案中,优选地,所述将车辆的动力学模型中的抗蛇形减振器替换为可设定作用力和状态变量的阻尼力元件,将所述动力学模型中的所述状态变量与所述非线性液压模型中的所述作用力建立动态链接,形成联合仿真模型具体包括:将adams仿真软件中车辆动力学模型的所述抗蛇形减振器替换为阻尼力元件,添加所述抗蛇形减振器两端的位移和所述抗蛇形减振器两端的相对速度作为系统状态变量,添加所述抗蛇形减振器的作用力;将所述车辆动力学模型的系统状态变量和作用力与easy5仿真软件中的所述非线性液压模型的抗蛇形减振器位移、速度和阻尼力进行动态链接,形成联合仿真模型;将所述联合仿真模型生成动态链接库文件。在上述技术方案中,优选地,所述对所述车辆进行试验,将所述试验的试验数据与所述联合仿真模型的仿真数据分别进行时域范围和频域范围的对比具体包括:采集所述车辆的试验数据和所述联合仿真模型的仿真数据;将所述试验数据与所述仿真数据中的车体和构架的振动加速度在时域范围内进行对比;计算并对比所述试验数据的均方根值与所述仿真数据的均方根值;将所述试验数据与所述仿真数据进行psd变换到频域范围;将所述试验数据与所述仿真数据中车体的振动加速度在频域范围内进行对比。与现有技术相比,本发明的有益效果为:通过从抗蛇行减振器的内部结构入手,对各种阀、活塞、油腔等元件依据流体力学的原理建立描述准确且计算高效率的抗蛇行减振器非线性液压模型。该模型可以应用于不同的减振器,可以修改不同物理结构参数。调节模型所需的试验次数能降到最低,同时还解决了模型复杂、动力学仿真时效率低甚至会出现结果发散的缺点。此外,通过在抗蛇行减振器的结构元件中选取各个元件的相关参数作为优化变量,包括节流阀的阻尼孔径、通流孔径、弹簧刚度、弹簧预紧力、活塞单向阀孔径、底阀单向阀孔径、活塞杆直径、节点刚度等,将抗蛇行减振器的非线性液压数值模型与车辆动力学模型结合,使用联合仿真的方法来分析这些结构参数对高速铁道车辆非线性稳定性的影响,从而得到最优参数。附图说明图1为本发明一种实施例公开的非线性的抗蛇形减振器的结构参数优化设计方法的流程示意图;图2为本发明一种实施例公开的典型的非线性液压减振器的工作原理图;图3为本发明一种实施例公开的阻尼调节阀工作原理示意图;图4为本发明一种实施例公开的阀片的结构示意图;图5为本发明一种实施例公开的阀片的有限元模型示意图;图6为本发明一种实施例公开的减振器数值液压模型示意图;图7为本发明一种实施例公开的不同速度的仿真示功图;图8为本发明一种实施例公开的不同速度的试验示功图;图9为本发明一种实施例公开的节流阀阻尼孔径水平变化趋势图;图10为本发明一种实施例公开的常通孔径水平变化趋势图;图11为本发明一种实施例公开的活塞单向阀孔径水平变化趋势图;图12为本发明一种实施例公开的弹簧刚度水平变化趋势图;图13为本发明一种实施例公开的弹簧的预紧力水平变化趋势图;图14为本发明一种实施例公开的修改后的车辆动力学模型示意图;图15为本发明一种实施例公开的抗蛇行减振器数值液压模型的车辆动力学联合仿真模型示意图;图16为本发明一种实施例公开的车体的振动加速度时域范围对比示意图;图17为本发明一种实施例公开的构架的振动加速度时域范围对比示意图;图18为本发明一种实施例公开的车体的振动加速度频域范围对比示意图;图19为本发明一种实施例公开的节流阀阻尼孔径对动态阻尼率的影响示意图;图20为本发明一种实施例公开的节流阀阻尼孔径对车辆临界速度的影响示意图;图21为本发明一种实施例公开的节流阀阻尼孔径对车辆平稳性指数的影响示意图;图22为本发明一种实施例公开的节流阀常通孔径对动态阻尼率的影响示意图;图23为本发明一种实施例公开的节流阀常通孔径对车辆临界速度的影响示意图;图24为本发明一种实施例公开的节流阀常通孔径对车辆平稳性指数的影响示意图;图25为本发明一种实施例公开的节流阀弹簧刚度对动态阻尼率的影响示意图;图26为本发明一种实施例公开的节流阀弹簧刚度对车辆临界速度的影响示意图;图27为本发明一种实施例公开的节流阀弹簧刚度对车辆平稳性指数的影响示意图;图28为本发明一种实施例公开的弹簧预紧力对动态阻尼率的影响示意图;图29为本发明一种实施例公开的弹簧刚度对车辆临界速度的影响示意图;图30为本发明一种实施例公开的弹簧刚度对车辆平稳性的影响示意图;图31为本发明一种实施例公开的活塞单向阀孔径对动态阻尼率的影响示意图;图32为本发明一种实施例公开的活塞单向阀孔径对车辆临界速度的影响示意图;图33为本发明一种实施例公开的活塞单向阀孔径对车辆平稳性指数的影响示意图;图34为本发明一种实施例公开的底阀孔径对车辆临界速度的影响示意图;图35为本发明一种实施例公开的底阀孔径对车辆平稳性指数的影响示意图;图36为本发明一种实施例公开的节点刚度对动态阻尼率的影响示意图;图37为本发明一种实施例公开的节点刚度对动态刚度的影响示意图;图38为本发明一种实施例公开的节点刚度对车辆临界速度的影响示意图;图39为本发明一种实施例公开的节点刚度对车辆平稳性指标的影响示意图。具体实施方式为使本发明实施例的目的、技术方案和优点更加清楚,下面将结合本发明实施例中的附图,对本发明实施例中的技术方案进行清楚、完整地描述,显然,所描述的实施例是本发明的一部分实施例,而不是全部的实施例。基于本发明中的实施例,本领域普通技术人员在没有做出创造性劳动的前提下所获得的所有其他实施例,都属于本发明保护的范围。下面结合附图对本发明做进一步的详细描述:如图1所示,根据本发明提供的一种非线性的抗蛇形减振器的结构参数优化设计方法,包括:步骤s101,以抗蛇形减振器的阻尼调节阀、活塞单向阀和底阀建立抗蛇形减振器的非线性液压模型;步骤s102,采用多组不同的活塞速度分别对非线性液压模型进行动态仿真和试验,根据动态仿真和试验得出的阻尼力数据,判断非线性液压模型的精确性是否符合要求;步骤s103,将车辆的动力学模型中的抗蛇形减振器替换为可设定作用力和状态变量的阻尼力元件;步骤s104,将动力学模型中的状态变量与非线性液压模型中的作用力建立动态链接,形成联合仿真模型;步骤s105,对车辆进行试验,将试验的试验数据与联合仿真模型的仿真数据分别进行时域范围和频域范围的对比;步骤s106,根据试验数据与仿真数据的对比结果,判断联合仿真模型是否符合要求;步骤s107,若判定联合仿真模型符合要求,则分别对非线性液压模型中阻尼调节阀、活塞单向阀和底阀的结构参数进行调整,确定不同的结构参数对联合仿真模型的非线性稳定性的影响曲线;步骤s108,根据结构参数与联合仿真模型的影响曲线,确定各个结构参数的最优参数值。在上述实施例中,优选地,阻尼调节阀包括节流阀、常通孔、弹簧,抗蛇形减振器还包括活塞;阻尼调节阀、活塞单向阀和底阀的结构参数包括:节流阀的阻尼孔径、弹簧的弹簧刚度、弹簧的预紧力、常通孔的通流孔径,活塞单向阀的孔径、底阀的底阀单向阀孔径、活塞的活塞杆直径以及抗蛇形减振器与车辆车体的相连节点的节点刚度。在上述实施例中,优选地,正交试验的影响因素包括节流阀的阻尼孔径、常通孔的通流孔径、弹簧的弹簧刚度、弹簧的预紧力和活塞单向阀的孔径。在上述实施例中,优选地,上述对正交试验的试验结果进行分析,确定各影响因素的水平变化趋势,并确定各影响因素的优选数据具体包括:将每个影响因素按照不同水平确定试验组;计算每个影响因素下不同试验组的抗蛇形减振器的阻尼力最大值之和,以及所有试验组的阻尼力最大值的总和;计算每个影响因素下不同试验组中阻尼力最大值之和之间的极差,并根据极差值确定各影响因素的影响主次顺序;根据每个影响因素的不同试验组中阻尼力最大值之和,确定各影响因素的优选数据。在上述实施例中,优选地,上述将车辆的动力学模型中的抗蛇形减振器替换为可设定作用力和状态变量的阻尼力元件,将动力学模型中的状态变量与非线性液压模型中的作用力建立动态链接,形成联合仿真模型具体包括:将adams仿真软件中车辆动力学模型的抗蛇形减振器替换为阻尼力元件,添加抗蛇形减振器两端的位移和抗蛇形减振器两端的相对速度作为系统状态变量,添加抗蛇形减振器的作用力;将车辆动力学模型的系统状态变量和作用力与easy5仿真软件中的非线性液压模型的抗蛇形减振器位移、速度和阻尼力进行动态链接,形成联合仿真模型;将联合仿真模型生成动态链接库文件。在上述实施例中,优选地,上述对车辆进行试验,将试验的试验数据与联合仿真模型的仿真数据分别进行时域范围和频域范围的对比具体包括:采集车辆的试验数据和联合仿真模型的仿真数据;将试验数据与仿真数据中的车体和构架的振动加速度在时域范围内进行对比;计算并对比试验数据的均方根值与仿真数据的均方根值;将试验数据与仿真数据进行psd变换到频域范围;将试验数据与仿真数据中车体的振动加速度在频域范围内进行对比。在上述实施例中,对抗蛇形减振器的非线性液压模型的建立方法具体如下:如图2所示为典型非线性液压减振器的工作原理示意图。当减振器拉伸时,活塞上的单向阀关闭,底阀上的单向阀开启,活塞上部拉伸腔相当于体积为a的油液经节流孔流到储油缸,同时储油缸中相当于(a+b)的油液经底阀流到活塞下部压缩腔中。当减振器压缩时,底阀上的单向阀关闭,活塞上的单向阀开启,压缩腔相当于体积(a+b)的油液经单向阀流到拉伸腔,其中体积a的油液留在拉伸腔,而体积为b的油液经阻尼孔流到储油缸中。在建立减振器的非线性液压模型时,为了使模型简单又不影响计算精度,要进行一些假设简化:忽略一些结构辅助孔、节流能力小的孔;忽略因压力变化而引起的系统刚性构件的弹性变形和温度变化而引起的系统构件的变形;忽略系统刚性构件的弹性变形情况;忽略油液的自重;忽略活塞与工作缸之间、活塞杆与导向座之间的油液泄漏;忽略减振器在工作时引起工作油液温度的变化。液压减振器的数值液压模型中有三个主要的元件,分别为阻尼调节阀、活塞单向阀和底阀,下面分别介绍它们的建模。(1)阻尼调节阀建模如图3所示为阻尼调节阀的工作原理示意图。阻尼调节阀中,弹簧预紧力可改变减振阻力的大小和特性。图3中a点与拉伸腔相通,而b点与储油腔相通,当拉伸腔与储油腔的压力差不足以推动已预紧弹簧时,油液从常通小孔流动(q1);当拉伸腔与储油腔的压力差可以推动已预紧弹簧时,油液从常通小孔(q1)和侧隙流动(q2)。在easy5仿真软件中使用常通孔、单向阀和节流阀组合实现阻尼调节阀的功能,其中弹簧的刚度取为8.1×104n/m。(2)活塞单向阀与底阀如图4所示为阀片的结构示意图。活塞单向阀和底阀的结构相似,工作时都是利用阀片挡住液流,产生阻力。如图5所示为阀片有限元模型的示意图。按照阀片的尺寸建立有限元模型,通过有限元受力分析,得到等效刚度,其中活塞单向阀阀片刚度为4.63×103n/m,底阀阀片刚度为1.65×103n/m。表1为减振器参数。表1减振器参数如图6为减振器的数值液压模型示意图。在easy5仿真软件中根据阻尼调节阀、活塞单向阀和底阀的工作原理,建立减振器的液压模型。在easy5仿真软件中,对于活塞不同的速度(5mm/s,10mm/s,20mm/s,30mm/s,40mm/s,50mm/s,60mm/s)下进行动态仿真,其仿真示功图线如图7所示。同时减振器的试验示功图如图8所示。试验数据与减振器仿真数据相对比如表2所示。表2减振器试验与仿真数据对比表由表2可以得出,仿真阻尼力和试验阻尼力相对误差很小,最大为6.67%,最小仅为0.70%,这说明建立的easy5模型比较精确,符合建模要求。在上述实施例中,对于抗蛇形减振器结构参数对减振器特性的影响的分析方法如下:在抗蛇行减振器的结构元件中,减振器各个元件的相关参数、活塞杆直径、节点刚度都对减振器的工作特性有重要的影响。虽然各个元件的结构不相同,但它们的主要参数都包括初始节流孔径,可变节流孔径,弹簧的刚度和弹簧的预紧力等。本发明选取节流阀的阻尼孔径d1、通流孔径d2、弹簧刚度k1、预紧力f1、活塞单向阀孔径d3,底阀单向阀孔径d4,活塞杆直径d,节点刚度k2为研究对象,讨论它们对减振器工作特性的影响。试验时,采用相同的速度及位移激励,参数值的选取方法是在原始参数值左右较小范围内取值,参数设计试验表如表3,表中0代表所建减振器模型的初始值,“+”、“.”分别表示在初始值上加、减。表3减振器数字试验参数值在上述实施例中,对抗蛇形减振器的工作特性的正交试验分析方法具体如下:(1)正交试验表设定在进行正交试验的时候,选择节流阀阻尼孔径、常通孔径、弹簧刚度、弹簧的预紧力、活塞单向阀孔径作为影响因素。在试验范围内各选三种因素,因素水平如表4所示,而将减振器阻尼力最大值作为试验指标。表4因素-水平表10.750.051.180010020.950.11.5200020031.150.151.93200300本试验是五因素三水平,因此选择l18(37)正交表进行试验。按照因素顺序上列水平对号入座,确定试验方案如表5所示。表5试验方案表11(0.75)1(0.05)1(1.1)1(800)1(100)21(0.75)2(0.1)2(1.5)2(2000)2(200)31(0.75)3(0.15)3(1.9)3(3200)3(300)42(0.95)1(0.05)1(1.1)2(2000)2(200)52(0.95)2(0.1)2(1.5)3(3200)3(300)62(0.95)3(0.15)3(1.9)1(800)1(100)73(1.15)1(0.05)2(1.5)1(800)3(300)83(1.15)2(0.1)3(1.9)2(2000)1(100)93(1.15)3(0.15)1(1.1)3(3200)2(200)101(0.75)1(0.05)3(1.9)3(3200)2(200)111(0.75)2(0.1)1(1.1)1(800)3(300)121(0.75)3(0.15)2(1.5)2(2000)1(100)132(0.95)1(0.05)2(1.5)3(3200)1(100)142(0.95)2(0.1)3(1.9)1(800)2(200)152(0.95)3(0.15)1(1.1)2(2000)3(300)163(1.15)1(0.05)3(1.9)2(2000)3(300)173(1.15)2(0.1)1(1.1)3(3200)1(100)183(1.15)3(0.15)2(1.5)1(800)2(200)(2)正交试验结果分析a)计算各因素的ⅰ、ⅱ、ⅲ和总和t为了更清楚反映各因素水平的差异,在本试验结果中把各因素各水平所对应的指标加起来,填在表6中。其中ⅰ=因素所在的列中数码“1”所对应的指标值之和;ⅱ=因素所在的列中数码“2”所对应的指标值之和;ⅲ=因素所在的列中数码“3”所对应的指标值之和。最后将全部试验数据累加,记为t,可以通过它检查同一因素的ⅰ、ⅱ、ⅲ计算无差错。b)计算因素的极差r通过计算极差可以确定因素影响的主次顺序。每个因素的极差r=该因素的ⅰ、ⅱ、ⅲ中最大的与最小的之差。从计算的各因素极差值r中,可知各结构参数对阻尼力影响的主次顺序可排列为节流阀阻尼孔径、弹簧刚度、弹簧的预紧力、活塞单向阀孔径、常通孔径(从主到次的顺序)。c)选取较优生产条件根据ⅰ、ⅱ、ⅲ的结果,选取ⅰ、ⅱ、ⅲ中最大者作为对应水平即对于最大阻尼力的各因素最优组合是节流阀阻尼孔径(试验1)、弹簧刚度(试验3)、弹簧的预紧力(试验3)、活塞单向阀孔径(试验1)、常通孔径(试验2)。表6试验结果表d)趋势图对于每个因素,以水平位横坐标,相应的ⅰ、ⅱ、ⅲ为纵坐标,在坐标图上描点,便得该因素的趋势图。节流阀阻尼孔径、常通孔径、活塞单向阀孔径、弹簧刚度、弹簧的预紧力所对应的趋势图分别为图9、图10、图11、图12、图13所示。在上述实施例中,以联合仿真模型分析抗蛇形减振器的内部结构参数对车辆速度和稳定性的影响,从而实现抗蛇形减振器结构参数的优化设计方法具体如下:(1)联合仿真模型a)车辆动力学模型的建立在adams/rail中建立某型crh动车组车辆动力学模型。同时为了建立联合仿真模型,对于前转向架把抗蛇行减振器去除,添加两个作用力damper_force_left和damper_force_right以及6个系统状态变量,其中damper_xx_act_extension表示减振器两端的位移,damper_xx_act_rate表示减振器两端的相对速度,damper_force_xx表示减振器的作用力,设置如表7所示,修改后的部分模型如图14所示。同理对后转向架进行相同的处理,设定好各种变量。最后利用adams/control模块导出控制的plant文件。表7状态变量b)联合仿真模型的建立针对每一个减振器的输入/输出变量控制plant建立一个联合仿真模型。现以前转向架左侧抗蛇行减振器的输入/输出控制变量pout_left_1/pin_left_1为例,介绍如何建立联合仿真模型。在easy5的元件库中选择extensions扩展库,在msc.software元件库中选择“adamsmechanism”元件,把元件拖入模型区。设置元件的属性为adams/view导出的plant文件,选择“co.simulation”方式,并如图15中连接easy5模型中的元件,使得damper_left_act_extension_1,damper_left_act_rate_1分别与cd元件的位移和速度连接,damper_force_mag_1与cd元件的阻尼力连接。最后把联合仿真模型导出为adamsexternalsystemlibrary,系统生成动态链接库文件,供adams/control调用。c)联合仿真模型的验证联合仿真模型的验证时使用的轨道为中国高速铁轨chn60,轨道不平顺使用武广高速铁路联调联试测得不平顺,全长为7000m,中间1960m到3560为曲线,曲线具体工况见表8。表8验证模型的轨道曲线工况曲线半径r(m)圆曲线外轨超高h(mm)均衡速度(km/h)实际通过速度(km/h)9000128312km/h345km/h时域范围的模型验证:在时域范围内,对车体和构架振动加速度的试验数据和仿真数据进行比较,比较结果如图16、图17所示。从图16、图17可以看出,车体和构架在时域范围横向和垂向的试验数据和仿真计算数据的加速度振动基本是一致的,振动的最大值也基本吻合。表9为试验结果与adams/rail仿真结果的对比,这里rms(rootmeansquare)为均方根值,如式1所示。表9实测数据和仿真计算结果rms比较比较项实测rms仿真计算rms误差构架横向加速度(m/s^2)1.0791.29019.5%构架垂向加速度(m/s^2)1.1981.02314.6%车体横向加速度(m/s^2)0.087260.0712018.4%车体垂向加速度(m/s^2)0.12780.11589.39%从表9可以看出,车辆动力学联合仿真模型的仿真结果与试验结果在时域范围是基本一致的(误差范围小于20%)。说明建立的联合仿真模型在时域范围的仿真结果是可靠的,可以在工程实践的使用。频域范围的模型验证:图18所示为车体和构架的试验数据和仿真数据进行psd变换到频域范围的比较。从图18可以看出,用联合仿真计算的结果和试验的结果在频域范围内大致趋势一致。其中车体振动加速度psd比较可以看出,试验车体横向振动振动加速度的主频在2.3hz左右,垂向振动加速度主频在0.8hz左右;仿真车体横向振动加速度主频在2.7hz左右,垂向振动加速度主频在0.75hz左右。试验和仿真的车体横向、垂向振动主频比较接近,可以认为在合理的误差范围。构架的振动加速度psd比较可以看出,试验结果和仿真结果在0—20hz频率范围内的频率分布基本相同。综上所述,分析时域和频率的结果比较,此动力学联合仿真模型是基本符合实际要求,可以使用此模型进行研究。(2)结构参数优选a)节流阀阻尼孔通过改变抗蛇行减振器的节流阀阻尼孔径,常通孔径,弹簧刚度和弹簧预紧力,分析车辆运行的稳定性和平稳性,结果如图19至图21所示。在图19中可以看出随着节流阀阻尼孔径增加抗蛇行减振器的动态阻尼率单调下降,孔径从0.75cm增加到1.15cm,动态阻尼率降低了34%。随着动态阻尼率的下降,车辆的临界速度也不断减小。在图20中,当节流阀阻尼孔径小于时,随着节流阀阻尼孔径增加,车辆的临界速度变化很小,但是当阻尼孔的直径大于后,车辆的临界速度开始快速下降。在图21中,车辆垂向平稳性指标wzz变化平缓,而横向平稳性指标wzy会有所变化,但是当阻尼孔的直径大于0.9cm后wzy会快速变大,横向平稳性下降。b)节流阀常通孔通过改变抗蛇行减振器的节流阀常通孔径,分析车辆运行的稳定性和平稳性,结果如图22至图24所示。在图22中可以看出随着节流阀阻尼孔径增加抗蛇行减振器的动态阻尼率单调下降,孔径从0.02cm增加到0.22cm,动态阻尼率降低了22%,当节流阀常通孔径大于后,动态阻尼率快速下降。在图23和图24中,当节流阀常通孔径低于0.1cm后,车辆的临界速度急速下降,而节流阀常通孔径对车辆垂向平稳性指标wzz影响不大,而随常通孔径增加,横向平稳性指标wzy会单调增加,横向平稳性下降。c)节流阀弹簧刚度通过改变抗蛇行减振器的节流阀弹簧刚度,分析车辆运行的稳定性和平稳性,结果如图25至图27所示。在图25中可以看出随着节流阀弹簧刚度增加,抗蛇行减振器的动态阻尼率单调上升,但是弹簧刚度超过2000n/cm后,动态阻尼率变化趋于平缓。从图26和图27中也能看到这种变化,当节流阀弹簧刚度超过2000n/cm后,车辆的临界速度变化很小,横向平稳性指标wzy也会变化趋缓。节流阀弹簧刚度对车辆垂向平稳性指标wzz影响不大。d)节流阀弹簧的预紧力通过改变抗蛇行减振器的节流阀弹簧预紧力,分析车辆运行的稳定性和平稳性,结果如图28至图30所示。在图28中可以看出随着节流阀弹簧的预紧力增加抗蛇行减振器的动态阻尼率单调增加,动态阻尼率从9452n·s/m到13216.58n·s/m,增加了40%。在图29和图30中可以看出随着节流阀弹簧的预紧力增加,车辆临界速度单调上升,但是弹簧的预紧力超过200n后,它的变化趋于平缓,横向平稳性指标wzy也会变化趋缓。节流阀弹簧的预紧力对车辆垂向平稳性指标wzz影响不大。e)活塞单向阀通过改变抗蛇行减振器的活塞单向阀孔径,分析车辆运行的稳定性和平稳性,结果如图31至图33所示。在图31中可以看出随着活塞单向阀孔径增加,抗蛇行减振器的动态阻尼率单调下降,但是孔径超过1.5cm后,动态阻尼率变化趋于平缓。在图32中,随着活塞单向阀孔径增加,车辆的临界速度降低,但是当活塞单向阀孔径大于1.5cm后,车辆的临界速度变化平缓;在图33中,车辆垂向平稳性指标wzz和横向平稳性指标wzy变化平缓。f)底阀通过改变抗蛇行减振器的底阀孔径,分析车辆运行的稳定性和平稳性,结果如图34和图35所示。在图34中,当底阀孔径过小的时候,抗蛇行减振器的阻尼特性会出现畸变,进而影响车辆的临界速度。提高底阀孔径可以提高车辆的临界速度,但是当底阀孔径大于2.5cm后,车辆的临界速度不再提高;在图35中,车辆垂向平稳性指标wzz变化平缓,而横向平稳性指标wzy会随着底阀孔径增加变小,当底阀孔径大于2.5cm后,wzy不再减小。g)端部节点刚度仿真计算时候,将抗蛇行减振器端部节点刚度看做线性逐渐增大,减振器其他参数保持不变,抗蛇行减振器端部节点刚度对减振器的动态阻尼率和动态刚度影响很大。如图36和图37所示。从图36、图37中可以发现在端部节点刚度小于18mn/m时,减振器的动态阻尼率随着端部节点刚度的增加而减小,动态刚度则相反;但是在端部节点刚度大于18mn/m后,这种变化趋势变缓,处于缓慢增加和减小的状态。这种变化趋势也在车辆临界速度上有相类似的体现,如图38所示。在图38中的仿真结果显示,随着端部节点刚度的增加,车辆的临界速度明显上升,并且在刚度小于18mn/m时增加的较快,而当节点刚度大于20mn/m后增加速率开始减小,并且有下降的趋势。而图39中显示端部节点刚度对于平稳性的影响主要是对横向稳定性wzy有一定的影响,横向平稳性的指标随着节点刚度的增大而有所减少,说明横向平稳性提高,但是当节点刚度增大到一定值后,横向平稳性指标变化不大。节点刚度对垂向平稳性wzz影响不大,随着节点刚度的增大,垂向平稳性几乎不变。从仿真结果来看,提高抗蛇行减振节点刚度对车辆临界速度和稳定性都有作用,应该选用尽量大一些轴向刚度,但是还要考虑橡胶堆的工艺情况与实际运用情况来选择合适的刚度。以上所述为本发明的实施方式,考虑到现有技术中模型复杂不稳定、仿真效率低、参数属性不确定的技术问题,本发明提出了一种非线性的抗蛇形减振器的结构参数优化设计方法,以抗蛇形减振器内部结构的流体力学原理建立非线性液压模型,将非线性液压模型与车辆动力学模型结合为联合仿真模型,以联合仿真模型分析抗蛇形减振器的内部结构参数对车辆速度和稳定性的影响,从而实现抗蛇形减振器结构参数的优化设计。通过本发明的技术方案,简化了模型、提高了参数选取的合理性、提高了仿真时的效率,提高了模型的精确性,使得出的参数更加优化。以上所述仅为本发明的优选实施例而已,并不用于限制本发明,对于本领域的技术人员来说,本发明可以有各种更改和变化。凡在本发明的精神和原则之内,所作的任何修改、等同替换、改进等,均应包含在本发明的保护范围之内。当前第1页12