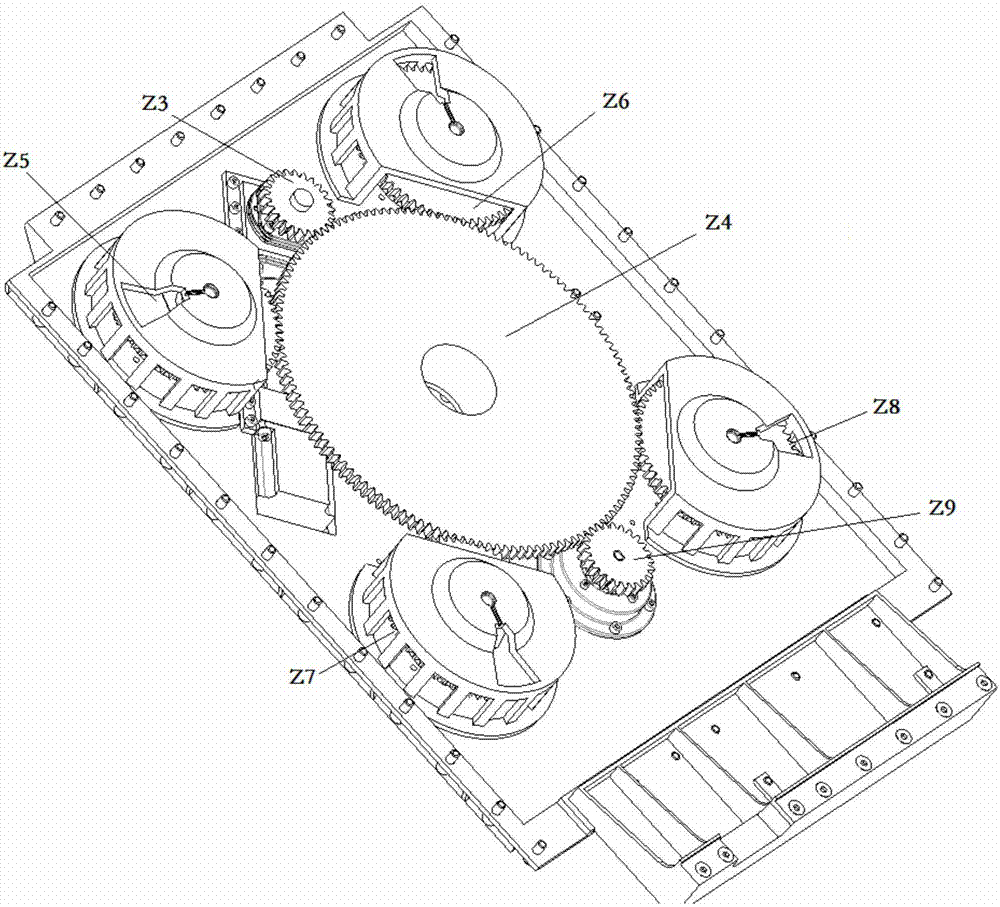
本发明涉及机械产品装配
技术领域:
,具体地说是一种自动锁紧释放机构传动链精度分析方法。
背景技术:
:传动链精度分析技术在机械产品制造装配领域中具有重要的应用意义,合理而经济的精度设计方案不仅能够显著提高产品的综合性能,同时能够减少浪费。目前,企业内的零部件精度设计方案,主要是以经验为基础,但对于形成标准的系列产品,公差设计经验在不断地积累和修改而得以完善,而对于产品的更新换代或新产品的生产,原有经验可能会偏离于实际需求,不可避免地面临诸如产品的可制造性、可装配性和经济性等相关性能指标的失效。传动链误差分析是一项产品质量控制与预测相关的技术,不同误差环节对于产品的相关性能指标具有不同的影响,如何找到这些因素,并加以合理的控制,从而设计出经济合理而且性能水平优良的产品是一项及其有意义的工作。如图1~2所示,在一种自动锁紧释放机构中,包括驱动电机、传动齿轮组和多个丝杠,且所述多个丝杠通过所述驱动电机驱动同步转动,所述驱动电机通过传动齿轮组传递转矩,其中各个丝杠能否同步转动对于整个机构工作精度而言十分关键,但由于该机构包含的传动元件数量较多,如果按照传统方法很难确定出造成丝杠不同步的因素,只能依靠长时间经验累积后获得,这显然无法满足企业要求。技术实现要素:本发明的目的在于提供一种自动锁紧释放机构传动链精度分析方法,能够分析出自动锁紧释放机构中对于丝杠不同步影响的显著因素,并可以据此优化设计方案,大大提高了设计效率。本发明的目的是通过以下技术方案来实现的:一种自动锁紧释放机构传动链精度分析方法,所述自动锁紧释放机构包括传动齿轮组和多个同步转动的丝杠,包括如下步骤:步骤一:根据传动误差关系确定影响丝杠同步转动精度的传动元件;步骤二:根据步骤一中确定的传动元件传动误差成因确定传动误差影响因素;步骤三:进行传动误差建模;步骤四:对步骤二中确定的传动误差影响因素进行技术参数分析,并对技术参数初始化;步骤五:对传动误差影响因素精度进行水平划分,细化为多个方面因素,并根据步骤四中初始化后的数值通过步骤三中公式,得出各个方面因素的传动链输出精度标准差估算值σ数据;步骤六:根据步骤五的结果,通过极差分析获得极差结果作为各个方面因素的敏感度分析结果,此外对于方面因素的敏感度分析的可靠性通过方差分析进行验证。步骤一中确定的影响丝杠同步精度的传动元件包括中心传动齿轮、与所述中心传动齿轮啮合的锁紧端齿轮以及与所述锁紧端齿轮固连的丝杠。步骤二中,确定的传动误差影响因素包括齿轮单项传动误差、齿轮间空程误差和丝杠传动误差。所述齿轮单项传动误差包括齿轮切向综合总偏差fi’;所述齿轮间空程误差包括齿轮的齿厚偏差导致的圆周侧隙j1、齿轮间中心距偏差导致的圆周侧隙j2和轴承游隙导致的圆周侧隙j3;所述丝杠传动误差包括丝杠本身制造装配产生的轴向运动误差和累积于与所述丝杠对应的锁紧端齿轮的周节误差。步骤三中,传动误差模型为各传动元件相互作用关系,表示为:上式中,δl为传动链输出误差;δl为丝杠自身轴向运动误差;d为锁紧端齿轮分度圆直径;s为丝杠导程;k1、k2分别为相互啮合齿轮1,2的单项传动误差,j1为齿厚偏差导致的圆周侧隙,j2为中心距导致的圆周侧隙,j3为轴承游隙导致的圆周侧隙;并由上式得出传动链输出误差的均值和方差;均值公式为:e表示对误差量求取均值;方差公式为:d表示对误差量求取方差。。步骤四中,传动误差影响因素的技术参数包括:齿轮公称参数、齿厚公差参数、切向公差参数、轴承游隙公差参数、中心距公差参数和丝杠轴向公差参数。步骤五中,对传动误差影响因素进行水平划分,具体细化为五个方面因素:中心传动齿轮z4精度等级、锁紧端齿轮精度等级、齿轮支撑轴承精度等级、中心驱动齿轮z4的轴间距和丝杠轴向制造公差。所述齿轮支撑轴承精度等级体现于轴承径向游隙。还包括步骤七:根据步骤六的分析结果调整中心传动齿轮、锁紧端齿轮和丝杠。本发明的优点与积极效果为:1、本发明能够分析出自动锁紧释放机构中对于丝杠不同步影响的显著因素,并可以据此优化设计方案,大大提高了设计效率。2、本发明不用依靠长时间经验累积后才获得相关数据,根据分析结构进行设计改进,充分满足企业要求。附图说明图1为本发明所要分析的机构结构示意图,图2为图1中机构的传动齿轮组结构示意图,图3为图1中从电机到丝杠的转矩传递过程示意图,图4为图1中从电机到丝杠的转矩传递流程框图,图5为本发明的分析结果示意图。具体实施方式下面结合附图对本发明作进一步详述。如图1~4所示,本发明所要分析的自动锁紧释放机构包括电机q、传动齿轮组和四个丝杠,所述传动齿轮组中包括锥齿轮z1、从动锥齿轮z2、驱动齿轮z3、中心传动齿轮z4和四个锁紧端齿轮,其中锥齿轮z1安装在电机q的输出轴上,从动锥齿轮z2与所述锥齿轮z1啮合,所述从动锥齿轮z2和驱动齿轮z3同轴,所述驱动齿轮z3与所述中心传动齿轮z4啮合,在所述中心传动齿轮z4四周沿着圆周方向均布四个锁紧端齿轮,其中锁紧端齿轮一z5与丝杠一s1固连,锁紧端齿轮二z6与丝杠二s2固连,锁紧端齿轮三z7与丝杠三s3固连,锁紧端齿轮四z8与丝杠四s4固连,所述驱动齿轮z3设置于所述中心传动齿轮z4一侧,且设置于锁紧端齿轮一z5和锁紧端齿轮二z6之间,所述中心传动齿轮z4另一侧与一个计数齿轮z9啮合。本发明主要分析四个丝杠不同步的因素影响,并据此改进工艺。具体如下:一、传动误差关系分析,确定影响丝杠同步精度的传动元件包括中心传动齿轮z4、锁紧端齿轮及其对应的丝杠,也即图4中虚线方框内的部分。如图3所示,从电机q开始到中心传动齿轮4这一段传动链尽管也存在传动误差,但由于对各个丝杠误差作用是相同的,因此对于各个丝杠同步精度没有影响。二、对步骤一中确定的中心传动齿轮z4、锁紧端齿轮和丝杠的传动误差进行分析,影响中心传动齿轮z4、锁紧端齿轮和丝杠传动误差的因素包括齿轮单项传动误差、齿轮间空程误差和丝杠传动误差。1、齿轮单项传动误差:齿轮单项传动误差k主要为齿轮切向综合总偏差fi’,可表示为:k=f′i1)1)式中,fi’可具体表示为:fi'=fp+fi'2)2)式中:fp为齿距累积总偏差(包括不同精度等级的上下偏差);fi’为单齿切向综合偏差(包括不同精度等级的上下偏差)。2、齿轮间空程误差:包括齿轮的齿厚偏差导致的圆周侧隙j1、中心距偏差导致的圆周侧隙j2和轴承游隙导致的圆周侧隙j3,从而导致传动的空程误差。其中:齿厚偏差导致的圆周侧隙j1包括相啮合中心传动齿轮z4和锁紧端齿轮的齿厚的周节偏差和啮合后形成的侧隙,二者的随机性特点不同,前者形成于制造阶段,后者形成于装配阶段,所以误差分布的特性不一定相同。齿厚偏差导致的圆周侧隙j1可表示为:j1=es1+es23)3)式中:es1和es2分别为相互啮合两齿轮的齿厚的偏差值,包含不同精度等级的齿厚公差tsn、上偏差esns和下偏差esni。中心距导致的圆周侧隙j2可表示为:j2=2fatanα4)4)式中:fa为中心距偏差值(包括不同精度等级的上下偏差),α为啮合齿轮压力角。轴承游隙导致的圆周侧隙j3为:j3=2(u1+u2)tanα5)5)式中,u1、u2分别为相啮合的中心传动齿轮z4和锁紧端齿轮支撑轴承的径向游隙(包括不同精度等级上下偏差),α为啮合齿轮压力角。3、丝杠传动误差:作为传动链的末端,丝杠传动误差包括两个方面:一是丝杠本身制造装配所导致的轴向运动误差;二是前向传动链累积于与所述丝杠对应的锁紧端齿轮的周节误差,从而引起的丝杠轴向运动误差。三、步骤二中明确影响中心传动齿轮z4、锁紧端齿轮和丝杠传动误差的因素后,进行传动误差建模,中心传动齿轮z4、锁紧端齿轮和丝杠所形成的传动链相互作用几何关系可以表示为:6)式中,δl为传动链输出误差;δl为丝杠自身轴向运动误差;d为锁紧端齿轮分度圆直径;s为丝杠导程。考虑到各环节传动误差作为随机变量,不具有相关性,由式6)可得传动链输出误差的均值和方差公式为:四、对步骤二中确定的齿轮单项传动误差、齿轮间空程误差和丝杠传动误差进行技术参数分析和初始化,影响各误差的技术参数包括:齿轮公称参数、齿厚公差参数、切向公差参数、轴承游隙公差参数、中心距公差参数和丝杠轴向公差参数,对这些技术参数在精度合理范围进行初始化,为进一步基于试验设计理论的敏感度分析提供基础条件。五、对传动误差影响因素精度进行水平划分,细化为多个方面因素,并实施基于试验设计理论的传动精度分析,也即将步骤四中初始化后的数据代入步骤三中的公式中计算。首先由步骤一可知影响因素包括:中心传动齿轮z4和锁紧端齿轮制造精度和装配精度以及丝杠副制造精度,在步骤五水平划分时具体可以细化为五个方面的因素:1、中心传动齿轮z4精度等级、2、锁紧端齿轮精度等级、3、齿轮支撑轴承精度等级(体现于轴承径向游隙)、4、中心驱动齿轮z4的轴间距和5、丝杠轴向制造公差。齿轮和丝杠属于标准传动件,参数公差是离散的,通过技术参数精度等级初始化,可以获得不同精度等级具体的传动件参数误差。根据步骤三中式6)~8),将各传动件精度等级输入,初步采用传动链末端误差标准差作为试验目标进行估算,得到不同精度等级传动条件配合下的输出误差,六、通过极差分析,初步得出不同因素对丝杠同步输出影响的敏感度,并对此通过方差分析进行验证,从而找出中心传动齿轮z4、锁紧端齿轮和丝杠传动链中对于丝杠输出精度造成显著影响的因素,并提出可能的优化方案。下面列举一个实施例进行进一步说明。由上述可知,在传动链结构中,与齿轮,丝杠传动精度相关的制造和装配公差参数较多,在步骤四的技术参数分析中,确定这些技术参数包括齿轮公称参数、齿厚公差参数、齿轮切向公差参数、轴承游隙公差参数、中心距公差参数和丝杠轴向公差参数。a、首先初始化确定各个参数,具体如下:1、确定齿轮公称参数。本实施例中的中心传动齿轮z4和锁紧端齿轮的公称参数如表1所示。表1的参数是根据闻邦椿主编《机械设计手册》第5版第2卷表8.2-4(pp:8-11)查表所得到。表1齿轮结构参数公称值由表1可得中心传动齿轮z4和锁紧端齿轮啮合的理论中心距为(264+120)/2=192mm。2、确定齿厚公差参数。(1)、确定切齿径向刀具进给公差br本实施例中的中心传动齿轮z4和锁紧端齿轮的切齿径向刀具进给公差br如表2所示。表2的参数根据闻邦椿主编《机械设计手册》第5版第2卷表8.2-119(pp:8-116)查表得到。表2切齿径向刀具进给公差br4级5级6级7级8级中心传动齿轮z4/μm65.5281102.06130163.8锁紧端齿轮/μm44.15468.0487109.62(2)、确定径向圆跳动公差fr。本实施例中的中心传动齿轮z4和锁紧端齿轮的径向圆跳动公差fr如表3所示。表3根据闻邦椿主编《机械设计手册》第5版第2卷表8.2-114(pp:8-113),查表得到。表3径向圆跳动公差fr4级5级6级7级8级中心传动齿轮z4/μm13.619.22839.255.2锁紧端齿轮/μm10.414.420.829.641.6(3)、确定齿厚公差tsn。本实施例中的中心传动齿轮z4和锁紧端齿轮的齿厚公差tsn如表4所示。表4根据闻邦椿主编《机械设计手册》第5版第2卷公式(8.2-50)(pp:8-116)计算得到。表4齿厚公差tsn4级5级6级7级8级中心传动齿轮z4/μm47.7660.5977.0498.84125.83锁紧端齿轮/μm32.9840.6851.7966.8985.35(4)、确定齿厚偏差参数。本实施例中的中心传动齿轮z4和锁紧端齿轮的齿厚偏差参数如表5所示。齿厚偏差参数计算根据闻邦椿主编《机械设计手册》第5版第2卷公式(8.2-51)(pp:8-116)将表2~表4数据代入计算得到。表5齿厚偏差参数3、确定齿轮切向公差参数。(1)、确定齿轮重合度εr。齿轮重合度εr包括两部分,端面重合度εα和纵向重合度εβ,自本发明所要分析的锁紧机构背板上驱动齿轮z3、中心传动齿轮z4和锁紧端齿轮均为直齿圆柱齿轮,齿轮螺旋角β为零,故纵向重合度εβ为零,端面重合度εα需要根据齿数查表来确定,具体如表6所示。表6根据闻邦椿主编《机械设计手册》第5版第2卷图8.2-7(pp:8-26)和表8.2-16(pp:8-24)查询得到。表6齿轮重合度εr计算结果(2)、确定等效系数k(用于确定单齿单齿切向综合偏差fi’)。等效系数k计算值根据闻邦椿主编《机械设计手册》第5版第2卷表8.2-103(pp:8-95)查表得到。表7等效系数k计算值(3)、确定单齿切向综合偏差fi’。单齿切向综合偏差fi’根据闻邦椿主编《机械设计手册》第5版第2卷表8.2-103(pp:8-95)查表得到。表8单齿切向综合偏差fi’(4)、计算齿轮切向公差参数,将表5代和表8入公式1)~公式4)中计算得到下表9的齿轮切向公差参数。表9齿轮切向公差参数4、确定轴承游隙公差参数。根据所述自动锁紧释放机构设计方案,支撑中心传动齿轮z4轮轴采用深沟球轴承,所述深沟球轴承具有径向游隙,而各个锁紧端齿轮的支撑轴承为角接触轴承(gb/t292-94),在部件装配过程中其径向游隙可以控制到很小,因此在本实施例的传动误差研究中可设置为零,参见下表10。表10根据闻邦椿主编《机械设计手册》第5版第3卷表14.2-13,pp:14-61查询得到。表10中心传动齿轮z4支撑轴承游隙等级参数(gb/t276-94)5、确定齿轮中心距公差参数。齿轮中心距单向公差fa如下表11所示。表11根据闻邦椿主编《机械设计手册》第5版第2卷表8.2-129(pp:8-121)查表得到。表11齿轮中心距单向公差fa6、丝杠轴向公差参数本实施例中丝杠的最大行程大于65mm,设定锁紧和释放的行程范围为40~75mm,丝杠的轴向误差通过插值计算如表12所示。表12根据于源.机床梯形螺纹丝杠、螺母精度的特点[j],机械工人.冷加工,1997,3,pp:13-16表1和表2,查询得到。表12丝杠轴向公差δl(jb2886—92)b、参数确定后,进行步骤五的试验设计水平安排,对传动误差影响因素精度进行水平划分,包括1、中心传动齿轮z4精度等级、2、锁紧端齿轮精度等级、3、齿轮支撑轴承精度等级(体现于轴承径向游隙)、4、中心驱动齿轮z4的轴间距和5、丝杠轴向制造公差。传动误差影响因素总体上可分为4级,对于因素4(中心驱动齿轮的轴间距)总共有3个等级,可以考虑采用拟水平方法作以补充,划分后的因素水平如表13(根据上述表10、11、12代入得到)所示。表13主要影响因素的水平安排根据水平划分的等级,选择l16(45)正交表能够满足要求,以步骤二中确立的五项因素作为输入,并以传动链输出精度的标准差作为试验响应,可以得到如表14所示的分析表。表14是根据上述表1~表13数据,代入到上述公式2)~公式6)计算得到最后一列传动链输出精度标准差估算值σ的数据。表14含拟水平正交表l16(45)根据表14得到的试验结果,通过极差分析(如表15所示)获得极差结果作为不同因素的敏感度分析结果,如图5所示。此外对于敏感度关系的分析可靠性还需要进行方差分析进行验证,如表16所示,最后可以根据敏感度关系对方案进行适度优化。表15和16根据根据李云雁,胡传荣编著.实验设计与数据处理[m],化学工业出版社得出。表15含拟水平正交表l16(45)极差分析k14.6954.7244.7684.7482.750k24.7564.7474.78689.5583.480k34.78274.7964.7744.7965.525k44.86794.8354.774——7.346k11.1741.1811.1921.1870.687k21.1891.1871.1971.1950.870k31.1961.1991.1931.1991.381k41.2171.2091.193——1.836r0.0430.0280.0050.0121.149表16方差分析表从f分布表中查得f0.05(3,1)=215.7,f0.025(3,1)=864.2,f0.01(3,1)=5403,f0.005(3,1)=21615。通过方差分析,影响传动链精度的五项因素的显著性与如图5所示的极差分析得到的结果一致,可知丝杠的轴向精度对于传动链输出精度的影响最为显著,其他因素与之相比,不具有显著性。c、方案的优化根据精度敏感度分析结果,在“中心传动齿轮z4—锁紧端齿轮—丝杠”这部分传动链中,将齿轮精度等级选择降到最低,即中心传动齿轮z4和锁紧端齿轮选择为7级精度,中心传动齿轮z4的深沟球轴承等级选择为第4组,啮合齿轮的轴间距精度等级选择为9~10级。根据式8)可得,齿轮周节误差对丝杠轴线方向误差的贡献为±1.776μm,如果丝杠为5级精度(轴向运动误差为±2.08μm),传动链输出误差,即四根丝杠不同步偏差为±2.738μm;如果丝杠为6级精度(轴向运动误差为±3.83μm),四根丝杠不同步偏差为±4.225μm;如果丝杠为7级精度(轴向运动误差为±5.28μm),4根丝杠不同步偏差为±5.57μm。本例分析传动链结构及其影响因素,从试验设计的敏感度分析结果可以看出,在整个传动链系统中,作为传动链末端环节的丝杠制造精度对于传动链的输出精度的影响最为显著,其余因素对于传动链输出精度影响不显著。如果对该机构的输出精度要求过高,可以考虑更换较高精度等级的丝杠;如果该机构的输出精度足够满足要求,可以考虑适当放宽中心传动齿轮z4和锁紧端齿轮z5、z6、z7和z8,以及支撑轴承的精度等级,以节约成本。对于类似的实际机构,在保证传动精度达标同时,还需要降低相关非传动部件的定位误差,由于结构零部件较多,其装配过程的定位误差需要严格控制,确保结构末端定位精度满足设计要求。当前第1页12