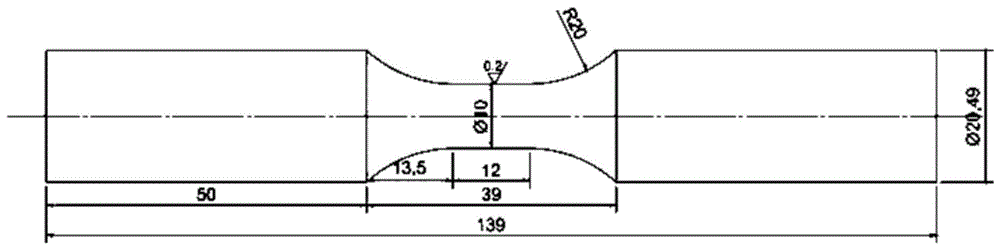
本发明涉及对含缺口的结构进行低周疲劳预测的问题,具体涉及一种基于总应变能密度的疲劳评估方法。
背景技术:
:疲劳失效是材料在低于正常强度的情况下经过若干周期的循环载荷作用发生破坏的现象。在当今众多行业如车辆、航空、航海、桥梁、冶金、电力等,主要结构都会承受各种复杂的循环变化载荷,疲劳失效是这些机械零件最主要的失效形式之一。由于疲劳失效的裂纹萌生期时间长,在快速扩展前难以发现,每年都会因此发生重大的事故,造成巨大的经济损失,这使得人们对材料疲劳失效问题的研究给予了高度的关注。在结构设计中,难免会出现台阶,圆孔,凹槽等结构,将这些结构统称为缺口。缺口结构会导致构件在受载时出现局部的应力集中,这些薄弱环节会成为疲劳裂纹的萌生源,大大降低整体的强度。在装备大型化发展的今天,以压力容器为例,常常每天只受到几个循环的载荷,为保证装备在服役期间能安全工作,低周疲劳问题的研究备受关注。目前对含缺口结构的疲劳寿命进行研究通常包含材料标准试样的疲劳试验,缺口件的疲劳试验和有限元数值模拟,已发展出了多种疲劳预测方法如局部应力应变法,临界距离法,应力场强法等等,这些方法有各自的适用范围,繁多的预测方法并没有统一。材料在每个循环载荷内由于变形产生的能量累积达到一定程度时会发生失效破坏,以此原理发展出了基于应变能的疲劳预测方法。材料在每次循环产生的弹性变形和塑性变形能量之和为总应变能密度,通过计算缺口件根部的最大总应变能密度并与材料标准件的试验结果进行对比可以进行疲劳寿命的预测。但是最初该方法进行预测由于只考虑缺口根部一点的能量,未考虑缺口周围的应力分布情况,对高周疲劳的预测具有较好的应用,但在局部发生较大塑性变形时,预测效果会过于保守,对低周疲劳问题的预测效果尚不理想。技术实现要素:为了克服使用总应变能密度对缺口件低周疲劳预测过于保守的问题,本发明提出了一种根据弹塑性能量之比来对总应变能密度进行修正的疲劳寿命评估方法,可得到准确的疲劳预测结果。本发明通过以下技术方案实现:一种总应变能密度修正的缺口件低周疲劳预测方法,其特征在于,所述方法包括如下步骤:(1)进行标准件的拉伸性能试验,得到材料的杨氏模量,拉伸特性曲线,屈服强度;(2)进行标准件的疲劳性能试验,提取稳态时的应力应变响应,计算得到循环应力应变曲线,分别计算塑性和弹性的应变能密度,建立材料的总应变能密度与疲劳寿命的方程;其中,循环应力应变曲线通过ramberg-osgood公式进行拟合:其中εa、σa分别为应变幅和应力幅,由标准件的疲劳性能试验得到,e为杨氏模量,由步骤(1)材料的拉伸试验得到,k′为循环强度系数,n′为循环应变硬化指数,为待拟合的材料参数;根据材料稳态时的应力应变滞回曲线面积计算塑性应变能密度:δwp=∫|σ|dε(2)其中σ为应力,ε为应变。根据材料稳态时的应力应变变程计算弹性应变能密度,公式为:δwe=δσδεe(3)其中δσ为应力变程,δεe为弹性应变变程;总应变能密度包括弹性和塑性应变能密度两部分,相加得到总应变能密度与疲劳寿命的方程:其中a与α为材料的塑性疲劳参数,为待拟合的材料参数;b与b为材料的弹性疲劳参数,为待拟合的材料参数;nf为疲劳破坏时的寿命;(3)建立缺口件的有限元模型,施加循环载荷,获得缺口件在不同时刻的应力分布;(4)选取缺口根部最大应力点作为疲劳危险点,根据载荷作用方向提取不同时刻的应力数据得到危险点处的应力变程δσ:根据对疲劳的贡献度最大的与载荷作用方向相同的应力,分别提取载荷最大最小时的应力数据,两者相减可得到应力变程δσ;(5)分别计算危险点的弹性应变能密度与塑性应变能密度,根据修正系数对危险点的总应变能密度进行修正;其中,缺口根部的塑性应变能密度经ramberg-osgood公式的化简后通过应力变程δσ计算得到:缺口根部的弹性应变能密度通过应力变程δσ计算:弹性和塑性两部分相加得到缺口危险点的总应变能密度δwt,root。对危险点的总应变能密度进行修正如下:其中k为材料常数,通过缺口件试验数据线性拟合得到;(6)将修正得到的总应变能密度带入材料的总应变能密度与疲劳寿命方程中得到寿命预测结果。与现有方法相比,本发明具有以下益处:1.有效解决基于总应变能密度对低周疲劳问题进行评估时过于保守的问题。2.对有限元建模的网格划分要求低,节省求解时间。3.计算公式简便,便于使用,预测精度高,稳定性好。附图说明图1(a)为标准圆棒试件,图1(b)为缺口半径为2mm的平板件,图1(c)为缺口半径为4mm的平板件,图1(d)为缺口半径为8mm的平板件。图2为两批304不锈钢拉伸性能曲线。图3为两批304不锈钢的总应变能密度寿命曲线。图4(a)为循环载荷示意图,图4(b)为有限元模型受力与网格划分图5为修正前后缺口件预测效果图具体实施方式下面通过实例结合附图对本发明做进一步的描述。本发明选用304不锈钢作为研究材料,304不锈钢作为一种常见的工程材料,广泛用于各种行业。考虑到生产工艺造成材料的性能差异,试验研究两批304不锈钢试件,这里记为a组和b组,使用图1(a)的标准圆棒试件进行拉伸试样和疲劳试验,设计了3种带缺口的平板件并进行疲劳试验,缺口根部的半径不同,在受相同载荷时应力集中的程度也不同,试验试件的尺寸如图1(b)、(c)、(d)。所有缺口平板件的疲劳试验采用应力控制,应力比为0,a组缺口件分别进行了应力幅150mpa和180mpa的疲劳试验;b组缺口件分别进行了应力幅180mpa和210mpa的疲劳试验。所有缺口件的试验结果小于10^5周期,属于低周疲劳的范畴。具体步骤如下:(1)进行标准件的拉伸性能试验,得到材料的杨氏模量,拉伸特性曲线,屈服强度。试验得出两批304不锈钢拉伸特性如图2所示,这两批304不锈钢有性能上的差异,它们具有相似的弹性性能和差异较大的塑性性能。(2)进行标准件的疲劳性能试验,提取稳态时的应力应变响应,计算得到循环应力应变曲线,分别计算塑性和弹性的应变能密度,建立材料的总应变能密度与疲劳寿命的方程。开展多组应力控制和应变控制的疲劳试验,取每组1/2寿命处的应力应变来进行循环应力应变曲线参数的计算,杨氏模量取200gpa,得出式(1)的参数如下表1。分别计算弹性和塑性应变能密度,得到两组材料的总应变能密度寿命的曲线如图3所示。表1循环应力应变曲线参数组别k′/mpan′a2732.30.387b1264.10.247(3)建立缺口件的有限元模型,施加循环载荷,获得缺口件在不同时刻的应力分布。使用有限元软件ansys对缺口件进行建模,由于缺口件为平板,因此选择plane183高阶二维八节点单元,根据缺口件的对称性建立1/2模型。材料属性使用kinh多线性随动硬化模型,为保证最大的应力结果低于材料的定义值,延长循环应力应变曲线进行取值。为保证结果的精确,使用映射网格对缺口件进行划分,在缺口处对网格进行细分。设置对称边界条件,按照试验载荷设置载荷步,进行模拟求解,施加的循环载荷如图4(a),有限元的受载和网格划分如图4(b)。模拟结果表明缺口根部受力最为严重,是疲劳破坏的危险点,这与试验结果相一致。(4)选取缺口根部最大应力点作为疲劳危险点,根据载荷作用方向提取不同时刻的应力数据得到危险点处的应力变程δσ。由于该实验中轴向应力对疲劳贡献度最大,绘制轴向应力的有限元模拟云图,分别提取危险点在载荷最大最小时的轴向应力,计算应力变程δσ。(5)分别计算危险点的弹性应变能密度与塑性应变能密度,根据修正系数对危险点的总应变能密度进行修正。根据式(5)和式(6)计算缺口根部的塑性应变能密度和弹性应变能密度,得到具体数值如下表2所示。表2试验应变能密度计算结果所有模拟结果中塑性应变能密度均大于弹性应变能密度,说明在低周疲劳中塑性应变占主导地位。塑性变形越大,塑性应变能密度也就越大,对总应变能密度的修正效果就越大。经过线性拟合得到a组材料的k=1.5658,b组材料的k=1.6265。根据式(7)可对两组缺口件的总应变能密度进行修正。(6)将修正得到的总应变能密度带入材料的总应变能密度与疲劳寿命方程中得到寿命预测结果。分别将修正前后的总应变能密度带入步骤(2)中的疲劳寿命曲线,得到预测结果如图5所示,图中横坐标为试验寿命,纵坐标为预测寿命,采用双对数坐标系,黑线为预测寿命与试验寿命完全相等,虚线为2倍因子区,在虚线内的结果可认为预测效果良好,若超出左上角为预测结果过于危险,若超出右下角为预测结果过于保守。试验结果同时也列出如下表3。表3试验疲劳寿命预测结果可以发现进行修正前的总应变能密度过大,使得修正前预测结果大部分偏小,过于保守;而经过修正的预测结果都能较好地位于2倍因子区内,本发明提出的寿命预测方法具有较好的准确性。当前第1页12