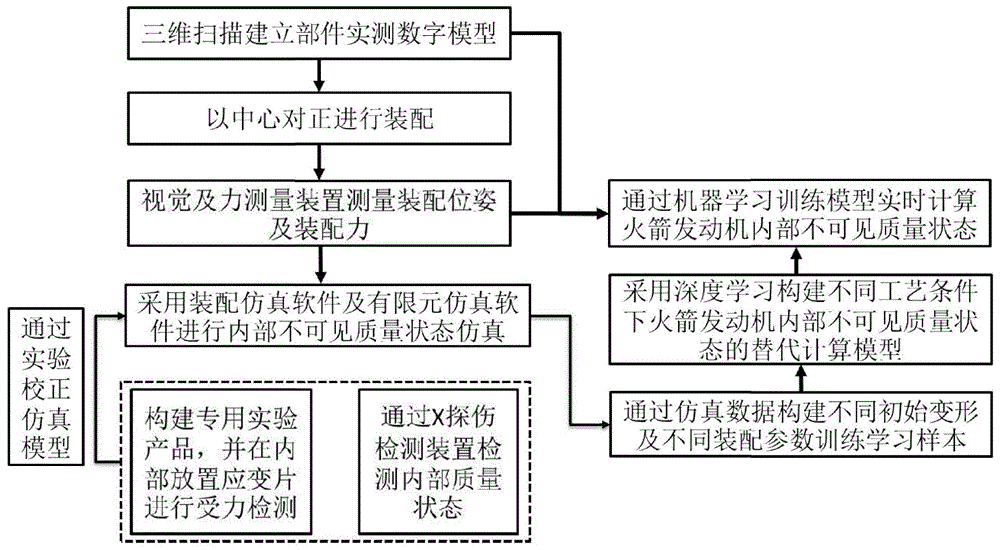
本发明属于火箭发动机数字孪生对接总装领域,具体的说是提供一种针对多级轴孔配合对接的火箭发动机内部不可测装配质量数字孪生建模与追溯方法。技术背景火箭发动机装配是缩短制造周期、保证产品质量的最关键环节,装配过程通过多级轴孔冗余定位配合提高受力特性及产品密封性能,装配质量保证的特点及难点在于内插式多台阶高精度不可见装配。由于其尺寸重量大、制造误差大、薄壁壳体易变形,导致绝热件、密封圈等内部不可见装配过程容易磕碰、剪切、挤压变形受损,质量状态不可知,存在较大的安全风险及隐患。装配变形示意图如图2a~图2c所示,给装配过程的质量监测提出了极高难点。主要在于:1)制造误差及重力变形导致多级台阶之间的基准关系发生无规律变化,仅依靠测量最外部基准进行对接时内部精密配合台阶会发生干涉,但内部干涉情况在物理空间不可见、不可测,质量状态无法精准控制;2)高技能工人依靠长期的经验与感觉缓慢谨慎调整才能完成装配对接,无法记录装配过程,导致产品后期如果出现质量问题,无法进行追溯。利用数字孪生技术进行装配质量的控制与追溯,目前可查的公开资料较少。本发明着重针对多级轴孔配合对接的火箭发动机内部不可测装配质量数字孪生建模与追溯,并采用数字孪生、人工智能等新一代信息技术解决其装配过程质量控制和追溯的难题,属于全新的技术方法。技术实现要素:本发明的物理设备组成如图3所示,主要由舱段位置姿态调整装置、三维扫描重建装置、视觉位置姿态测量装置和拧紧力/力矩测量装置组成,物理装置各部分均为成熟技术。其中舱段位置姿态调试装置为6自由度并联平台,通称stewart平台,是通用设备;三维扫描重建设备为三维信技测量技术(苏州)有限公司英文3dinfotech(suzhou)co.,ltd.的umasmartcell扫描装置;视觉位置姿态测量装置为双目视觉测量装置;拧紧力/力矩传感装置安装在拧紧机构后方,可实现拧紧扭矩及与轴线垂直平面内附加侧向力的实时检测,力/力矩传感器为德国me公司的六分量力传感器,型号为k6d175,力的测量量程为50kn,力矩测量量程为5knm。数字孪生模型构建仿真软件为西门子设计软件nx及装配仿真软件processsimulate,是通用的商业软件。本发明为实现上述目的所采用的技术方案是:火箭发动机内部不可测装配质量数字孪生建模与追溯方法,包括以下步骤:步骤1:构建基于实测数据的数字孪生模型,用于多级轴孔配合对接的火箭发动机内部不可测装配质量追溯提供模型;步骤2:利用视觉及力测量装置对火箭发动机装配位姿及装配力进行测量,通过数字空间与物理空间的虚实实时交互实现火箭发动机装配过程在数字空间中的映射;步骤3:采用深度神经网络构建含有火箭发动机装配位姿及装配力的不同工艺条件下火箭发动机内部不可见质量状态的替代计算模型;步骤4:通过替代计算模型实时计算火箭发动机内部不可见质量状态,通过数字空间与物理空间的虚实实时交互实现火箭发动机装配过程虚实交互控制执行。所述步骤1包括以下步骤:步骤1.1:在两对接装配件上设置用于表示舱段的空间位姿的外部测量基准;步骤1.2:在装配调整设备上设置用于表示火箭发动机的空间位姿的设备基准点;步骤1.3:采用三维扫描测量装置对火箭发动机内部舱段变形后的多台阶装配接口、外设测量基准进行测量,形成测量点云数据;步骤1.4:将测量点云数据转换为仿真软件可识别的cad模型;步骤1.5:将cad模型通过装配仿真软件,并根据实测外部测量基准与设备基准点,建立火箭发动机舱段模型作为数字孪生模型,以及其与火箭发动机舱段位置姿态调整设备之间的坐标关系,以保证数字的舱段模型与真实物理状态一致。所述步骤2包括以下步骤:步骤2.1:将火箭发动机装配零件中心对正,进行实体装配;步骤2.2:视觉测量装置实时对外部测量基准进行舱段位置姿态测量,并将实际视觉测量信息反馈至数字空间的装配仿真软件中,建立装配位姿仿真模型;步骤2.3:装配仿真软件根据实际视觉测量信息同步调整数字空间中舱段的位置姿态,装配仿真软件同时进行对接调整偏差判定,得到装配零件在数字空间中的位置姿态和几何偏差;步骤2.4:力/力矩传感器实时测量拧紧力矩与附加侧向分力,并将实际力/力矩测量信息反馈至数字空间的有限元仿真软件中,建立装配力仿真模型;步骤2.5:有限元仿真软件根据实际力/力矩测量信息同步调整数字空间中装配过程力/力矩的大小,同时进行装配力和方向调整偏差判定,得到装配零件在数字空间中的力/力矩和偏差数据;步骤2.6:构建实验产品模拟火箭发动机装配过程,在实验产品对接表面放置应变片进行受力检测,通过模拟装配实验校正装配力仿真模型;步骤2.7:通过x探伤检测装置检测实验产品在装配过程中的内部质量状态。所述内部质量状态包括装配间隙,装配干涉,密封圈剪切力,密封圈挤压量。所述步骤3包括以下步骤:步骤3.1:通过步骤2中得到的所有仿真数据构建训练学习样本,以不同初始变形及含有装配力、装配位姿、零部件初始偏差状态的不同装配参数作为深度神经网络模型的输入,不同的内部质量状态作为深度神经网络模型的输出;步骤3.2:把输入数据归一化;步骤3.3:针对火箭发动机内部不可见的装配间隙,装配干涉,密封圈剪切力,密封圈挤压量预测计算问题,构建深度神经网络模型,对步骤3.1得到学习样本进行训练,学习权重参数,得到最终深度神经网络模型作为替代计算模型。所述步骤4包括以下步骤:步骤4.1:基于实测数据的数字孪生模型,利用视觉及力测量装置获取火箭发动机装配位姿及装配力,输入到替代计算模型,得到火箭发动机内部不可见质量状态的仿真结果;步骤4.2:装配调整设备中的平台控制器根据数字空间内部不可见质量状态的仿真结果,调整装配位姿及装配力,分解成平台各驱动电机的控制指令,控制物理空间的装配过程,并将偏差信息反馈至装配调整设备;步骤4.3:装配调整设备根据数字空间的偏差反馈信息进行闭环控制调整,实现对接装配。本发明的优点与积极效果为:1.本发明通过采用激光三维扫描方法实测火箭发动机装配过程及装配接口与引入的外部基准的精确坐标对应关系,并将火箭发动机装配过程以及可能变形后的接口及其外部基准在数字空间中的装配仿真软件中建立高精度实测装配位姿仿真模型;通过力/力矩传感器实时测量拧紧力矩与附加侧向分力,并将实际测量信息反馈至数字空间的有限元仿真软件中,建立装配力仿真模型;最终形成实时展现装配过程的高精度数字孪生模型。2.本发明基于产品装配过程数据样本集进行离线学习和训练,研究基于卷积神经网络的网络结构和训练策略设计方法,构造产品装配过程深度神经网络模型,利用深度神经网络强大的特征提取和预测能力实现对机理仿真模型计算过程和结果的全部或部分逼近,通过封装后的深度神经网络模型正向计算代替机理模型的海量计算,实现仿真计算的加速,减少计算时间和内存占用,满足产品装配过程中虚实交互的实时性要求,达到装配质量的快速精准预测的目的。3.本发明开发虚实交互接口实现仿真软件与实际物理设备的信息交互,通过视觉和力测量装置测量外部基准得到物理空间装配过程的实时状态,并将其反馈至数字空间的装配仿真软件中;同时,将利用机器学习方法建立模型生成的仿真质量结果可视化呈现,并传输至设备控制系统,驱动设备进行实时装配控制和调整,改善装配质量。本发明通过数字孪生技术可视化、持久化的记录装配过程,如何产品后期如果出现质量问题,可实现装配全过程质量追溯。附图说明图1是火箭发动机内部不可测装配质量数字孪生建模流程图;图2a是火箭发动机装配过程多级台阶轴孔的变形状态图;图2b是火箭发动机装配过程多级台阶轴孔的变形状态图;图2c是火箭发动机装配过程多级台阶轴孔的变形状态图;图3是本发明的物理设备组成图;图4是引入的舱段外部测量基准点及设备标识基准点图;图5是深度神经网络训练计算代替机理模型流程图。其中,3-1舱段位置姿态调整设备、3-2三维扫描重建设备、3-3视觉位置姿态测量设备、3-4舱段1、3-5舱段2、4-1舱段1的外部基准,4-2舱段2的外部基准、4-3舱段位置姿态调整设备3-1的标识基准点。具体实施方式下面结合附图和实施例对本发明做进一步说明。数字孪生技术为解决针对多级轴孔配合对接的火箭发动机内部不可测装配过程质量问题发现和追溯的难题提供了新手段。通过在物理空间实测火箭发动机装配过程中多级轴孔变形后真实形状,并设置外部基准,在数字空间进行发动机装配模型及其与外部可见基准的重建,在数字仿真环境中实现不可见装配过程的可视化,为物理空间装配对接调整提供闭环反馈信息。在数字化空间通过装配仿真软件及有限元仿真软件进行内部不可见质量状态仿真,借助实验对内部装配受力和质量状态进行数字空间映射,并仿真模型进行校正。为实现数字空间对火箭发动机装配过程内部不可见部分和质量状态进行快速可视化重建,采用深度神经网络等机器学习方法在数字仿真环境中构建不同工艺条件下火箭发动机内部不可见质量状态的替代计算模型,通过仿真数据构建不同初始变形及不同装配参数的初始学习训练样本。从而在对火箭发动机装配件外部三维扫描以及通过视觉及力测量装置测量对装配位姿及装配力的基础上,通过数字空间与物理空间的虚实实时交互实现火箭发动机装配过程在数字空间中的映射,实现装配过程内部不可测装配质量问题发现和可视化追溯,保证产品的质量性能。如图1所示,本发明包括以下步骤:步骤1:构建基于实测数据的高精度数字孪生模型,为针对多级轴孔配合对接的火箭发动机内部不可测装配质量建追溯提供高精度数字孪生模型。步骤1.1:在两对接装配件上设置外部测量基准,如图5所示;步骤1.2:在对接调整设备上设置基准点,如图5所示;步骤1.3:采用三维扫描测量装置对火箭发动机内部舱段变形后的多台阶装配接口、外设测量基准进行测量,形成测量点云数据;步骤1.4:在西门子三维设计软件nx中,利用pointcloud模块将点云数据转换为仿真软件可识别的cad模型;步骤1.5:将重建的cad模型导入西门子processsimulate,并根据实测的步骤1.1中的火箭发动机舱段外部基准与步骤1.2中的设备基准点,设置火箭发动机舱段模型与调整设备之间的坐标关系,保证数字模型与真实物理状态一致。步骤2:利用视觉及力测量装置对火箭发动机装配位姿及装配力进行测量,通过数字空间与物理空间的虚实实时交互实现火箭发动机装配过程在数字空间中的映射。步骤2.1:将火箭发动机装配零件中心对正,进行实体装配;步骤2.2:视觉测量装置实时对步骤1.1中构建的外部基准进行舱段位置姿态进行测量,并将实际测量信息反馈至数字空间的装配仿真软件中,建立装配位姿仿真模型;步骤2.3:仿真软件根据实际测量信息同步调整数字空间中舱段的位置姿态,并利用装配仿真软件自带的间隙测量及干涉检测功能,进行对接调整偏差判定;步骤2.4:力/力矩传感器实时测量拧紧力矩与附加侧向分力,并将实际测量信息反馈至数字空间的有限元仿真软件中,建立装配力仿真模型;步骤2.5:仿真软件根据实际测量信息同步调整数字空间中装配过程力/力矩的大小,并利用有限元仿真软件自带的间隙测量及干涉检测功能,进行装配力和方向调整偏差判定;步骤2.6:构建实验产品模拟火箭发动机装配过程,在实验产品内部放置应变片进行受力检测,通过模拟装配实验校正步骤2.4装配力仿真模型;步骤2.7:通过x探伤检测装置检测实验产品在装配过程中的内部质量状态,包括平均装配间隙,平均装配干涉,密封圈剪切力,密封圈挤压量。步骤3:如图5所示,采用深度神经网络构建装配力,装配位置姿态,零部件初始偏差状态等不同工艺条件下火箭发动机内部不可见质量状态的替代计算模型;步骤3.1:通过仿真数据构建训练学习样本,以不同初始变形及不同装配参数为输入,不同的内部质量状态为输出;步骤3.2:把输入数据各个维度都中心化为零,把样本的中心拉回到坐标系原点上;将幅度归一化到同样的范围,减少各维度数据取值范围的差异而带来的干扰;步骤3.3:针对火箭发动机内部不可见的平均装配间隙,平均装配干涉,密封圈剪切力,密封圈挤压量预测计算问题,设计二维卷积神经网络结构,对步骤3.1得到数据集进行训练,学习权重参数;步骤3.3.1:以随机小数矩阵的形式初始化卷积核,进行卷积运算,在网络的训练过程中卷积核将学习得到合理的权值;步骤3.3.2:通过激活函数f对卷积神经网络进行激活,把卷积层输出结果做非线性映射,;步骤3.3.3:为减少了特征数和参数,进而简化了卷积网络计算时的复杂度,将输入的特征图通过卷积层后我们得到了它的特征图进行子采样,交替使用均值子采样和最大值子采样这两种采用方式以降低特征提取误差;步骤3.3.4:把卷积层和池化层的输出展开成一维形式,构建一个全连接的多层感知机回归网络和分类网络,将学到的分布式特征表示映射到样本标记空间;根据任务不同,分为分类任务和回归任务;分类任务采用柔性最大损失函数(softmaxloss),用于保证每个分类概率总和为1;回归任务可以采用均方误差函数(meansquareerror);步骤3.4:深度神经网络模型的评估和改进;步骤3.4.1:基于分类准确率/预测误差等指标,对上述深度神经网络模型的性能进行评估;步骤3.4.2:通过调整网络超参数(例如,层数、卷积核数量、非线性激活函数类型、学习率等),重新训练模型,并评估其性能;步骤3.4.3:根据上述评估结果,优选兼顾分类准确率/预测误差和网络复杂度(参数量和计算量)的模型作为最终模型。步骤4:通过替代计算模型实时计算火箭发动机内部不可见质量状态,通过数字空间与物理空间的虚实实时交互实现火箭发动机装配过程虚实交互控制执行。步骤4.1:在基于实测数据的高精度数字孪生模型,利用视觉及力测量装置获取火箭发动机装配位姿及装配力,输入到替代计算模型,得到火箭发动机内部不可见质量状态的仿真结果;步骤4.2:stewart平台控制器根据数字空间内部不可见质量状态的仿真结果,调整装配位姿及装配力,分解成平台各驱动电机的控制指令,控制物理空间的装配过程,并将偏差信息反馈至物理空间设备;步骤4.3:物理空间stewart平台根据数字空间的偏差反馈信息进行闭环控制调整,直至完成高精度对接装配。本发明的物理设备组成如图3所示,主要由舱段位置姿态调整设备3-1、三维扫描重建设备3-2、视觉位置姿态测量设备3-3、舱段3-4及舱段3-5组成,物理设备均采用成熟技术。其中舱段位置姿态调试设备3-1为6自由度并联平台,通称stewart平台,是通用设备;三维扫描重建设备3-2为三维扫描重建设备为三维信技测量技术(苏州)有限公司英文3dinfotech(suzhou)co.,ltd.的umasmartcell扫描装置;视觉位置姿态测量装置3-3为双目视觉测量装置。数字孪生模型构建仿真软件为西门子设计软件nx及装配仿真软件processsimulate,是通用的商业软件。实施例:本发明具体为:步骤1:构建基于实测数据的高精度数字孪生模型,为针对多级轴孔配合对接的火箭发动机内部不可测装配过程提供高精度模型,为后面的质量预测打下基础。步骤1.1:在火箭发动机装配过程上设置外部测量基准,如图4所示,4-1为舱段1的外部基准,4-2为舱段2的外部基准,基准为三个柱形装置,可代表舱段的空间位置姿态;步骤1.2:在装配调整设备上设置基准标识点,如图4所示,4-3为装配调整设备标识基准点,基准为三个柱形装置,可代表火箭发动机的空间位置姿态。步骤1.3:采用三维扫描测量装置3-2对火箭发动机变形后的舱段及多台阶装配接口3-4、3-5及外设测量基准4-1及4-2进行测量,形成测量点云数据;步骤1.4:在西门子三维设计软件nx中,利用pointcloud模块将火箭发动机3-4、3-5及外部基准3-1及3-2的点云数据转换为仿真软件可识别的cad模型;步骤1.5:将重建的火箭发动机接口3-4、3-5及外部基准4-1及4-2模型导入西门子processsimulate,并根据实测的步骤1.1中的舱段外部基准4-1、4-2与步骤1.2中的设备基准标识点4-3坐标关系,设置火箭发动机装配模型与调整设备之间的坐标关系,保证数字模型与真实物理状态一致。步骤2.1:将火箭发动机装配零件中心对正,进行实体装配;步骤2.2:视觉测量装置实时对步骤1.1中构建的外部基准进行舱段位置姿态进行测量,并将实际测量信息反馈至数字空间的装配仿真软件中,建立装配位姿仿真模型;步骤2.3:仿真软件根据实际测量信息同步调整数字空间中舱段的位置姿态,并利用装配仿真软件自带的间隙测量及干涉检测功能,进行对接调整偏差判定;步骤2.4:力/力矩传感器实时测量拧紧力矩与附加侧向分力,并将实际测量信息反馈至数字空间的有限元仿真软件中,建立装配力仿真模型;步骤2.5:仿真软件根据实际测量信息同步调整数字空间中装配过程力/力矩的大小,并利用有限元仿真软件自带的间隙测量及干涉检测功能,进行装配力和方向调整偏差判定;步骤2.6:构建实验产品模拟火箭发动机装配过程,在实验产品内部放置应变片进行受力检测,通过模拟装配实验校正步骤2.4装配力仿真模型;步骤2.7:通过x探伤检测装置检测实验产品在装配过程中的平均装配间隙,平均装配干涉,密封圈剪切力,密封圈挤压量等内部质量状态。步骤3:采用深度神经网络构建装配力,装配位置姿态,零部件初始偏差状态等不同工艺条件下火箭发动机内部不可见质量状态的替代计算模型;步骤3.1:通过仿真数据构建训练学习样本,以不同初始变形及不同装配参数为训练输入,如表1所示;不同的内部质量状态为训练输出,如表2所示;表1训练输入:不同初始变形及不同装配参数表2训练输出:不同的内部质量状态平均装配间隙平均装配干涉密封圈剪切力密封圈挤压量10.36mm1.72mm2.41kg·m/s20.17mm20.49mm2.14mm3.26kg·m/s20.19mm30.21mm0.84mm2.59kg·m/s20.22mm40.36mm1.21mm2.68kg·m/s20.25mm50.84mm1.57mm3.17kg·m/s20.16mm60.47mm0.99mm4.06kg·m/s20.19mm……………步骤3.2:把输入数据各个维度都中心化为零,把样本的中心拉回到坐标系原点上;将幅度归一化到同样的范围,减少各维度数据取值范围的差异而带来的干扰;步骤3.3:针对火箭发动机内部不可见的装配间隙,装配干涉,密封圈剪切力,密封圈挤压量预测计算问题,设计二维卷积神经网络结构如表3所示;表3cnn网络体系结构步骤3.4:深度神经网络模型的评估和改进;步骤3.4.1:基于分类准确率/预测误差等指标,对上述深度神经网络模型的性能进行评估;步骤3.4.2:通过调整网络超参数(例如,层数、卷积核数量、非线性激活函数类型、学习率等),重新训练模型,并评估其性能;步骤3.4.3:根据上述评估结果,优选兼顾分类准确率/预测误差和网络复杂度(参数量和计算量)的模型作为最终模型。表4模型的分类结果数据集大小1%2%3%4%训练集准确率1111测试集准确率0.8210.8620.9360.979步骤4:通过替代计算模型实时计算火箭发动机内部不可见质量状态,通过数字空间与物理空间的虚实实时交互实现火箭发动机装配过程虚实交互控制执行。步骤4.1:在基于实测数据的高精度数字孪生模型,利用视觉及力测量装置获取火箭发动机装配位姿及装配力,输入到替代计算模型,得到火箭发动机内部不可见质量状态的仿真结果;步骤4.2:stewart平台控制器根据数字空间内部不可见质量状态的仿真结果,调整装配位姿及装配力,分解成平台各驱动电机的控制指令,控制物理空间的装配过程,并将偏差信息反馈至物理空间设备;步骤4.3:物理空间stewart平台根据数字空间的偏差反馈信息进行闭环控制调整,直至完成高精度对接装配。当前第1页12