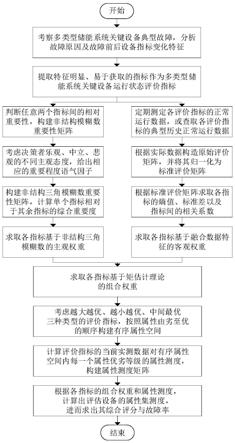
1.本发明属于多类型储能系统检修优化领域,更具体地,涉及一种基于关键设备状态评价体系的多类型储能检修优化方法。
背景技术:2.储能技术作为促进可再生能源大规模消纳和改善电网运行环境的重要手段,受到了学术界和工业界越来越广泛的关注。随着国家政策的大力扶持和储能技术及市场的不断成熟完善,多类型储能系统正逐渐由示范应用走向商业推广,储能系统在电网中渗透比例的不断提高已是大势所趋。在储能系统正常运行周期内,不可避免地会由于多种外界环境影响或自身老化等因素,导致储能系统功能恶化甚至出现故障,影响储能系统甚至电网的安全稳定运行,因此需要对储能系统的运行状态进行评价,根据状态评价结果制定科学合理的储能系统运维检修计划,以保障储能系统安全稳定运行和可持续健康发展。
3.然而,现有的储能系统运行状态评价方法普遍集中于单类型储能系统关键设备的故障分析及运行状态评价,未见有综合考虑多类型储能系统的运行状态评价方法;现有的检修优化方法大多侧重于传统电网设备的检修优化,面向多类型储能系统及其关键设备的检修优化方法仍较为少见,且对于检修过程中待检修设备运行状态较为恶劣时可能造成的风险因素考虑得不够充分。
技术实现要素:4.针对现有技术的缺陷,本发明的目的在于提供一种基于多类型储能系统关键设备运行状态评价体系,并综合考虑检修周期中的风险成本与实际成本的多类型储能系统检修优化方法。
5.为实现上述目的,本发明提供了一种基于关键设备状态评价体系的多类型储能检修优化方法,包括以下步骤:
6.步骤a:从关键设备的典型故障出发,分析故障原因及故障前后设备指标的变化特征,从中挖掘出特征明显且易于获取的设备指标作为表征关键设备运行状态的评价指标。进而,采用主客观权重组合赋权法对选取的评价指标进行赋权,确定各指标对表征设备总体运行状态的相对重要程度。最后,采用基于属性识别模型的综合评价法对设备总体运行状态进行综合评分,并根据该评分指导后续检修工作的开展。
7.步骤b:构建多类型储能系统检修优化模型,该模型以检修周期内的检修风险成本与检修实际成本之和最小为优化目标,计及检修计划约束、系统运行约束、常规机组运行约束、储能系统运行约束等条件。
8.步骤c:将多类型储能系统关键设备运行状态评价体系输出结果作为检修优化模型的输入参数,并输入常规机组运行参数、储能系统运行参数、风电出力预测数据、负荷预测数据等参数,求解模型得到满足优化目标的检修安排计划以及常规机组、储能系统的运行调度结果。
9.其中,多类型储能系统包括抽水蓄能(pumped storage,ps)系统、压缩空气储能(compressed air energy storage,caes)系统、电池储能(battery energy storage,bes)系统三大类,其中bes系统包括铅蓄电池储能(pb
‑
bes)系统和锂电池储能(li
‑
bes)系统。
10.多类型储能系统的关键设备运行状态评价指标如下:
11.ps系统的关键设备是水泵水轮机,水泵水轮机的运行状态评价指标如表1所示。
12.表1
[0013][0014][0015]
caes系统的关键设备是压缩机和膨胀机,压缩机的运行状态评价指标如表2所示,膨胀机的运行状态评价指标如表3所示。
[0016]
表2
[0017][0018]
表3
[0019][0020]
pb
‑
bes系统和li
‑
bes系统的关键设备均为各自类型的电池簇,电池簇的运行状态评价指标如表4所示。
[0021]
表4
[0022][0023]
步骤a中,基于非结构三角模糊数的主观赋权法实施过程如下:
[0024]
(1)假设某一设备存在a1,a2,...,a
n
共n个评价指标,决策者根据自身工作经验与专业知识对它们进行相对重要性判断,得到非结构模糊数重要性矩阵f:
[0025][0026][0027]
上述两式体现了非结构模糊数赋权过程。
[0028]
(2)在此基础上,当决策者分别处于乐观、中立、悲观态度时,可以判断指标间相对重要性的大小,决策者可按表5给出语气因子,并进一步转化为定量标度。
[0029]
表5
[0030][0031][0032]
由此可得非结构三角模糊数重要性矩阵g:
[0033][0034]
上式中,opt、neu、pes分别代表乐观、中立、悲观三种主观态度;为决策者分别处于乐观、中立、悲观态度时给出的a
i
与a
j
间相对重要性的语气因子定量标度。
[0035]
(3)对g矩阵中每个子阵元素按行求和得到非结构三角模糊数综合重要性矩阵h:
[0036][0037]
上式中,为决策者分别处于乐观、中立、悲观态度时指标a
i
相对于其他指标的重要性的加和。
[0038]
(4)按h矩阵给出的综合重要度分配权重,得到主观权重矩阵w
s
:
[0039]
[0040][0041]
上式中,为决策者的主观态度为k时指标a
i
的主观权重。
[0042]
步骤a中,基于融合数据特征的客观赋权法实施过程如下:
[0043]
(1)假设某一设备存在a1,a2,...,a
n
共n个评价指标,并且对这n个指标定期测定得到m组数据,这些数据构成了原始评价矩阵x:
[0044][0045]
(2)将x矩阵进行归一化,得到标准评价矩阵y:
[0046][0047][0048]
上式中,x
j,best
为指标a
j
的m个数据中最令人满意的数据,x
j,worst
为指标a
j
的m个数据中最令人失望的数据,若x
j,best
=x
j,worst
,则说明这m个数据相同,则有y
ij
=1,i=1,...,m。
[0049]
(3)根据y矩阵,可以求得各指标的熵值:
[0050][0051]
规定:若y
ij
=0,则上式中,e
j
为指标a
j
的熵值。
[0052]
(4)根据y矩阵和指标的熵值,可以求得客观权重矩阵w
o
:
[0053][0054][0055]
上式中,σ
i
为[y
1i
…
y
mi
]
t
的标准差,r
ij
为[y
1i
…
y
mi
]
t
与[y
1j
…
y
mj
]
t
之间的相关系数,为指标a
j
的客观权重。
[0056]
步骤a中,基于矩估计理论的组合赋权法实施过程如下:
[0057]
得到主客观权重后,采用基于矩估计理论的组合赋权法,可得到组合权重矩阵w
c
:
[0058][0059][0060][0061][0062]
上式中,为决策者的主观态度为k时指标a
i
的组合权重,α
k,i
为决策者的主观态度为k时指标a
i
的主观权重的相对重要程度,β
k,i
为决策者的主观态度为k时指标a
i
的客观权重的相对重要程度。
[0063]
步骤a中,基于属性识别模型的综合评价法实施过程如下:
[0064]
(1)构建有序属性空间
[0065]
假设某一设备存在a1,a2,...,a
n
共n个评价指标,指标类型有越小越好、越大越好、中间最优三种,由此进一步假设分别属于上述三种指标类型,且满足:
[0066][0067]
上述n个指标可按照p个属性优劣等级升序排列方式构成n
×
p有序属性空间ω:
[0068][0069][0070]
[0071][0072]
上式中,为越小越好型指标在属性优劣等级为j处的特征值;分别是越小越好型指标的极限值和最优值;为越大越好型指标在属性优劣等级为j处的特征值;分别是越大越好型指标的极限值和最优值;的极限值和最优值;分别为中间最优型指标在属性优劣等级为j处的特征下界和特征上界;分别是中间最优型指标的极限下界、极限上界、最优下界、最优上界。
[0073]
上式中,有序属性空间ω按照等间隔设置属性优劣等级的升序排列,将极限值与最优值之间分成p个优劣等级,j=1对应最劣值,即极限值,属性优劣等级最低,j=p对应最优值,属性优劣等级最高。上述指标极限值是设备发生故障的理论临界点、历史故障记录临界点或试验测定临界点,指标最优值是设备达到最优工作状态所需要的理论最优点或正常运行过程中实际所能达到的最优点。
[0074]
(2)计算设备各指标的属性测度
[0075]
属性测度是指设备某指标的实测值靠近于该指标的某个属性优劣等级的程度。假设某一设备某次测定后得到对应于指标a1,a2,...,a
n
的n个实测数据为x1,x2,...,x
n
,则任意指标a
i
的属性测度δ
ij
(i=1,...,n;j=1,...,p)计算情景及方法如下:
[0076]
1)a
i
为越小越好型指标
[0077]
①
[0078][0079]
②
[0080][0081]
③
[0082][0083]
2)a
i
为越大越好型指标
[0084]
①
[0085][0086]
②
[0087][0088]
③
[0089][0090]
3)a
i
为中间最优型指标
[0091]
①
或
[0092][0093]
②
[0094][0095]
③
[0096][0097]
④
[0098][0099]
最终形成该设备在实测数据集为{x1,x2,...,x
n
}、属性优劣等级分级数为p时的属性测度矩阵δ:
[0100][0101]
上式中,δ
ij
为该设备指标a
i
的实测数据x
i
靠近属性优劣等级j的程度,即指标a
i
的属性测度。
[0102]
(3)计算设备的属性集测度
[0103]
假设某一设备存在a1,a2,...,a
n
共n个评价指标,设备的每个指标均按等间隔设置了p个属性优劣等级,并且它们在有序属性空间ω中为升序排列。令同一属性优劣等级下的所有指标的特征值构成一个集合,这个集合就是一个属性集,有序属性空间ω包含了p个属性集,记为s
j
(j=1,...,p),则有序属性空间与属性集之间有如下关系:
[0104]
ω=[s
1 s2…
s
p
]
[0105]
假设设备某次测定后得到对应于指标a1,a2,...,a
n
的n个实测数据为x1,x2,...,x
n
,这些实测数据构成实测数据集x,则该设备的属性集测度为:
[0106][0107]
上式中,为决策者主观态度为k时,该设备所有指标的实测数据集x靠近属性优劣等级j的程度,即该设备的属性集测度。
[0108]
(4)计算设备的综合评分
[0109]
属性集测度仅能说明设备状态靠近每个属性优劣等级的程度,但无法准确表述设备具体处于哪一个等级,因此需要进一步计算设备的综合评分,用于指示该设备的运行状态。
[0110]
设有序属性空间ω的p个属性集为s
j
(j=1,...,p),对应每个属性集采用等间隔方式设置一组评分特征值q
e
:
[0111][0112]
上式中,为属性集s
j
的评分特征值。属性优劣等级j越大,属性集s
j
的指标特征值越好,评分特征值越大。
[0113]
设备根据当前实测数据集x得到的综合评分计算方法如下:
[0114][0115]
确定好设备综合评分后,需要明确各个属性优劣等级的评分范围。若设备综合评分q在某个范围内,则该设备的运行状态就属于该范围对应的属性优劣等级。评分范围计算方法如下:
[0116]
[0117][0118][0119][0120]
上式中,和分别是属性优劣等级j的评分下界和评分上界。若设备综合评分满足:
[0121][0122]
则该设备的属性优劣等级为j。
[0123]
步骤a中,基于设备综合评分的故障率计算方法如下:
[0124]
为将综合评分q应用于检修优化模型,需将其转化为设备故障率:
[0125][0126]
上式中,a、b为指数模型的形状参数;和分别是设备在整个评分范围内的综合评分最小边界值和最大边界值;和分别是设备在整个评分范围内使得设备故障率达到最值的综合评分最小临界值和最大临界值;p
fault,min
和p
fault,max
分别是设备在整个评分范围内的设备故障率最小值和最大值。
[0127]
步骤b中,所构建的多类型储能系统检修优化模型目标函数如下:
[0128]
minf=c
real
+c
risk
[0129]
上式中,c
real
、c
risk
分别是检修实际成本与检修风险成本。具体计算方法如下:
[0130]
(1)检修实际成本
[0131]
c
real
=c
maintain
+c
increment
[0132]
上式中,c
maintain
为设备进行检修所需的固定状态检修费用,c
increment
为在检修周期内因设备检修退出运行所带来的系统运行成本的增量。
[0133]
固定状态检修费用的计算方法如下:
[0134][0135]
上式中,n
maintain
为待检修设备总数;为待检修设备i状态检修费用与故障维修费用的比值;为待检修设备i的故障维修费用;为待检修设备i单位功率(或容量)故障维修费用;pe
i
为待检修设备i的额定功率或容量,若i为ps系统水泵水轮机、caes系统压缩机或膨胀机,则pe
i
代表功率,若i为pb
‑
bes系统或li
‑
bes系统电池簇,则pe
i
代表容量;p
fault
,i为待检修设备i的故障率;为待检修设备i单位功率(或容量)重置费用。
[0136]
系统运行成本增量的计算方法如下:
[0137]
c
increment
=c
g,run
+c
g,reserve
+c
g,start
[0138]
+c
g,environment
+c
w,waste
+c
ess,rm
‑
c
normal
[0139]
上式中,ess代表本发明所涉及的ps、caes、pb
‑
bes、li
‑
bes系统,下述ess均为此含义;c
g,run
、c
g,reserve
、c
g,start
、c
g,environment
分别为常规机组的运行成本、备用成本、开机成本、环境成本;c
w,waste
为系统弃风成本;c
ess,rm
为储能系统的运维成本;c
normal
为所有设备正常运行无退出时的系统最优运行成本。上式中各种成本的具体计算方法如下:
[0140][0141]
上式中,t为检修周期时长,设为一个自然日;n
g
为系统内常规机组数量;为常规机组i的购电成本系数;为常规机组i在t时段的出力;分别为常规机组i的正、负备用成本系数;分别为常规机组i在t时段的正、负备用容量;为常规机组i的开机成本;为常规机组i在t时段的运行状态,机组运行为1,机组停机为0;为常规机组i的环境成本系数;c
penalty
弃风成本系数;为风电机组t时段的预测出力;为风电机组t时段的实际出力;n
ess
为系统内储能系统数量;为储能系统i的单位功率日运维成本;为储能系统i的额定功率。
[0142]
关于c
normal
的计算方法,该值是以下式为目标函数,以本发明所述多类型储能系统检修优化模型中的系统运行约束、常规机组运行约束、ps系统运行约束、caes系统运行约束、bes系统运行约束为条件,并且没有设备退出运行时所计算出的最优解。
[0143]
minc
normal
=c
g,run
+c
g,reserve
+c
g,start
[0144]
+c
g,environment
+c
w,waste
+c
ess,rm
[0145]
(2)检修风险成本
[0146]
关于检修风险成本的计算,首先作出假设:
①
检修周期内待检修设备的故障情况为n
‑
1型故障;
②
同一时段最多仅有一台设备在检修。根据假设可知,在检修周期内有两类故障场景,一是没有设备进行检修的时段待检修设备i发生故障;二是设备j进行检修的时段待检修设备i发生故障。检修风险成本计算方法如下:
[0147][0148]
上式中,为t时段的检修风险成本期望值;为t时段仅有待检修设备i发生故障的概率;为t时段仅有待检修设备i发生故障所造成的本时段总成本增量。
[0149]
的计算方法如下:
[0150][0151]
上式中,为t时段待检修设备i的待检修状态,等待检修时为1,否则为0。此处用来实现故障率更新,当t时段i处于待检修状态时,说明i可能发生故障,则其故障率为p
fault,i
;当处于停机检修或检修完成状态时,认为i不会发生故障,则其故障率为0。
[0152]
的计算方法如下:
[0153][0154]
上式中,为待检修设备j在t时段的检修状态,正在检修为1,未在检修为0;分别为当t时段属于场景一、二时待检修设备i发生故障所导致的本时段总成本增量;分别为待检修设备i、j在整个检修周期均退出运行时的系统最优成本,除存在设备退出运行的情况外,其余计算方法与c
normal
相同;为待检修设备i和j在整个检修周期均退出运行时的系统最优成本,除存在设备退出运行的情况外,其余计算方法与c
normal
相同;此处用与实现故障场景控制,当t时段i处于检修中或检修完成状态时,认为i不会发生故障,当t时段i处于待检修状态并且其他设备未在检修时,当t时段i处于待检修状态并且j正在检修时,
[0155]
步骤b中,所构建的多类型储能系统检修优化模型约束条件如下:
[0156]
所构建的多类型储能系统检修优化模型约束条件主要包括检修计划约束、系统运行约束、常规机组运行约束、ps系统运行约束、caes系统运行约束、bes系统运行约束等,分别如下:
[0157]
(1)检修计划约束
[0158]
检修计划约束主要包括检修资源约束、检修时长约束、检修裕度约束、待检修状态
约束,分别如下:
[0159]
1)检修资源约束
[0160]
同一时段最多仅有一台设备在检修,如下式所示:
[0161][0162]
2)检修时长约束
[0163]
待检修设备i开始检修后应保持为检修状态直至检修完成。此外,检修状态持续时段数应等于i的检修时长,如下式所示:
[0164][0165][0166]
上式中,分别为待检修设备i的检修开始、完成时刻;为待检修设备i的检修时长。
[0167]
3)检修裕度约束
[0168]
考虑到一方面不同储能系统之间地理位置不同,另一方面检修过程中可能由于技术或资源问题而造成检修时间延长,需设置检修时间裕度,如下式所示:
[0169][0170]
上式中,ess
i
、ess
j
分别为待检修设备i、j所在的储能系统;为待检修设备i所在储能系统的检修时间裕度。上式说明,同一储能系统的不同待检修设备之间连续检修,不同储能系统的待检修设备之间存在最小等待时间,即检修时间裕度。
[0171]
4)待检修状态约束
[0172]
待检修设备i在开始检修前处于待检修状态,如下式所示:
[0173][0174]
(2)系统运行约束
[0175]
系统运行约束主要包括系统功率平衡约束、系统备用约束、风电出力约束,分别如下:
[0176]
1)系统功率平衡约束
[0177][0178]
上式中,分别为储能系统i在t时段的发电功率、用电功率;为t时段的系统负荷预测值。
[0179]
2)系统备用约束
[0180]
由于风电与负荷的预测存在一定的误差,为保证系统运行安全稳定,需要为系统预留一定量的正负备用容量,如下式所示:
[0181][0182]
上式中,分别为常规机组i在t时段的正、负备用容量;分别为常规机组i在t时段的正、负备用容量;分别为储能系统i在t时段的正、负备用容量;ε
load
、ε
wind
分别是负荷、风电的预测误差。
[0183]
3)风电出力约束
[0184]
系统弃风量不超过风电预测出力,如下式所示:
[0185][0186]
(3)常规机组运行约束
[0187]
常规机组运行约束主要包括出力上下限约束、备用容量约束、爬坡率约束、启停时间约束,分别如下:
[0188]
1)出力上下限约束
[0189][0190]
上式中,为常规机组i在t时段的运行状态,机组运行为1,机组停机为0;分别为常规机组i的出力上、下限。
[0191]
2)备用容量约束
[0192][0193]
3)爬坡率约束
[0194][0195]
上式中,分别为常规机组i的上、下爬坡率。
[0196]
4)启停时间约束
[0197][0198]
上式中,分别为常规机组i在t时段开、关机后的状态保持时间;分别为常规机组i的最小开、关机时间。
[0199]
(4)ps系统运行约束
[0200]
ps系统运行约束主要包括运行状态约束、功率约束、备用约束、库容约束、启停转
换约束,分别如下:
[0201]
1)运行状态约束
[0202]
ps系统内机组不能同时处于发电和抽水工况。
[0203][0204]
上式中,分别为t时段ps系统的发电、抽水工况状态;分别为t时段ps系统的发电、抽水工况状态;分别为t时段机组i的发电、抽水工况状态。
[0205]
若机组i的水泵水轮机为待检修设备,则有:
[0206][0207]
2)功率约束
[0208][0209]
上式中,分别为机组i的最大、最小发电功率;分别为机组i的最大、最小发电功率;分别为机组i的最大、最小抽水功率;分别为t时段机组i的发电、抽水功率。
[0210]
3)备用约束
[0211]
ps系统可以承担一部分旋转备用任务,从而减少常规机组的备用容量,减少燃料消耗,提高经济性。
[0212][0213]
式中,分别为t时段机组i的发电工况正、负备用容量;分别为t时段机组i的抽水工况正、负备用容量。
[0214]
4)库容约束
[0215]
在不考虑水库水量损失的情况下,可认为一天内上下水库水量总和不变,则上水库库容变化与下水库库容变化等效,可以仅考虑上水库库容约束。
[0216][0217]
上式中,v
t
为t时段上水库水量;v
max
、v
min
分别为上水库库容上、下限;v
t
分别为检修周期初始、结束时段上水库水量;k
ps
,g为发电工况水量
‑
功率转换系数;k
ps,p
为抽水工
况水量
‑
功率转换系数。上式说明,在检修周期内任意时段,上水库水量不能超过库容限值,且不能影响第二天使用。
[0218][0219]
上式说明,在考虑ps系统提供正负备用容量的情况下,上水库水量仍不能超过库容限值。
[0220]
5)启停转换约束
[0221]
过于频繁地启停一方面会对机组造成损害,另一方面会增加水头损失,因此需要对机组的日启停次数进行约束。
[0222][0223]
上式中,分别为检修周期内机组i的开、关机次数;为机组i的最大启停机次数。
[0224]
(5)caes系统运行约束
[0225]
caes系统运行约束主要包括运行状态约束、功率约束、备用约束、储气室气压约束,分别如下:
[0226]
1)运行状态约束
[0227]
caes系统不能同时处于发电工况和压缩工况。
[0228][0229]
上式中,分别为caes系统在t时段的发电、压缩工况状态。
[0230]
若caes系统的第i级压缩机为待检修设备,则有:
[0231][0232]
若caes系统的第i级膨胀机为待检修设备,则有:
[0233][0234]
2)功率约束
[0235]
[0236]
上式中,分别是caes系统的最小、最大发电功率;分别是caes系统的最小、最大发电功率;分别是caes系统的最小、最大压缩功率;分别是caes系统在t时段的发电、压缩功率。
[0237]
3)备用约束
[0238]
caes系统可以承担一部分旋转备用任务,从而减少常规机组的备用容量,减少燃料消耗,提高经济性。
[0239][0240]
上式中,分别是caes系统在t时段的发电工况正、负备用容量;分别是caes系统在t时段的压缩工况正、负备用容量。
[0241]
4)储气室气压约束
[0242][0243]
上式中,ap
t
为t时段储气室气压;ap
max
、ap
min
分别为储气室气压上限、下限;ap
t
分别为检修周期初始、结束时段储气室气压;k
caes,g
为发电工况气压
‑
功率转换系数;k
caes,c
为压缩工况气压
‑
功率转换系数。上式说明,在检修周期内任意时段,储气室气压不能超过气压限值,且不能影响第二天使用。
[0244][0245]
上式说明,在考虑caes系统提供正负备用容量的情况下,储气室气压仍不能超过气压限值。
[0246]
(6)bes系统运行约束
[0247]
pb
‑
bes系统与li
‑
bes系统的运行约束类似,在此统一说明。bes系统运行约束主要包括运行状态约束、功率约束、备用约束、能量约束、日吞吐量约束,分别如下:
[0248]
1)运行状态约束
[0249]
bes系统内电池簇不能同时处于放电和充电工况。
[0250]
[0251]
上式中,分别是t时段bes系统的充电、放电状态;分别是t时段bes系统的充电、放电状态;分别是t时段电池簇i的充电、放电状态。
[0252]
若电池簇i为待检修设备,则有:
[0253][0254]
2)功率约束
[0255][0256]
上式中,分别是t时段电池簇i的充电、放电功率;为电池簇i的最大充放电功率。
[0257]
3)备用约束
[0258]
bes系统可以承担一部分旋转备用任务,从而减少常规机组的备用容量,减少燃料消耗,提高经济性。
[0259][0260]
上式中,分别是t时段电池簇i的放电工况正、负备用容量;分别是t时段电池簇i的充电工况正、负备用容量。
[0261]
4)能量约束
[0262][0263]
上式中,n
bs
为bes系统内电池簇总数;为t时段电池簇i的能量;分别是电池簇i的能量最大、最小值;η为bes系统变流器转换效率;分别是检修周期初始、结束时段电池簇i的能量。上式说明,在检修周期内任意时段,电池簇能量不能超过能量限值,且不能影响第二天使用。
[0264][0265]
上式说明,在考虑bes系统提供正负备用容量的情况下,电池簇能量仍不能超过能量限值。
[0266]
5)日吞吐量约束
[0267]
日吞吐量是指bes系统日内充放电量总和,减小日吞吐量可以延长电池寿命。
[0268][0269]
上式中,分别为bes系统的日内充、放电量;为bes系统日最大吞吐量;δt为单位时段长度。
[0270]
步骤c中,所述模型求解结果如下:
[0271]
(1)常规机组的启停状态、出力调度计划、正负备用调度计划;
[0272]
(2)ps系统、caes系统、pb
‑
bes系统、li
‑
bes系统的运行工况状态、储能释能调度计划、正负备用调度计划;
[0273]
(3)风电出力调度计划;
[0274]
(4)储能系统待检修设备检修计划。
[0275]
通过本发明所构思的以上技术方案,与现有技术相比,能够取得以下有益效果:
[0276]
针对现有储能系统运行状态评价方法仅考虑单一类型储能系统的片面性问题,以及没有进一步与储能系统检修优化相结合的不实用问题,本发明所述储能系统运行状态评价方法充分考虑ps系统、caes系统、bes系统等多类型储能系统,首先,通过对多类型储能系统关键设备的典型故障分析,明确故障原因及故障前后设备指标的变化特征,从中挖掘出特征明显且易于获取的设备指标作为表征关键设备运行状态的评价指标;然后,采用基于非结构三角模糊数的主观赋权法和基于融合数据特征的客观赋权法对各指标分别进行主、客观权重分配,并采用基于矩估计理论的组合赋权法对主客观权重进行融合,得到各指标的组合权重;最后,采用基于属性识别模型的综合评价法对各关键设备进行运行状态评价,得出设备的综合评分、健康状态及故障率,并据此进一步指导后续检修优化方法的使用。
[0277]
针对目前电网设备检修优化方法大多针对线路、变压器等传统电网设备的现状,本发明所述检修优化方法侧重于对多类型储能系统展开,首先,计及检修计划约束、系统运行约束、常规机组运行约束、储能系统运行约束等条件,建立以检修周期内实际成本与风险成本之和最小为优化目标的多类型储能系统检修优化模型;然后,将获取的系统内各设备运行参数、负荷预测值、风电出力预测值、待检修设备检修参数输入至所述检修优化模型
中,求解该模型;最后,得出各待检修设备的检修计划安排,用于指导实际检修工作的开展。
[0278]
综上所述,本发明所述储能系统运行状态评价方法涉及到不同类型的储能系统,充分考虑多类型储能系统典型故障与运行指标的各异性与多样性,便于对区域电网内各种储能系统的运行状态进行统一评价与监测;该评价方法充分考虑主客观权重,避免了仅考虑主观权重时过于依赖专家经验而脱离实际数据的问题,以及仅考虑客观权重时不关心决策者主观偏好的问题;该评价方法可以充分响应电网中各类储能系统进行检修优化的需求,为实际检修工作的开展提供理论与数据支撑。本发明所述检修优化方法针对多类型储能系统展开,填补了储能系统检修优化方法的空缺;该检修优化方法充分考虑检修周期内的检修风险成本与检修实际成本,避免了仅考虑检修实际成本时,对健康状况较为恶劣设备的潜在故障风险因素有失考量的问题。
附图说明
[0279]
图1为本发明实施例1的多类型储能系统运行状态评价方法流程图;
[0280]
图2为本发明实施例2的改进ieee30节点系统结构图;
[0281]
图3为本发明实施例2的负荷与风电的典型日预测曲线;
[0282]
图4为本发明实施例2的对比方案一中各场景检修成本;
[0283]
图5为本发明实施例2的对比方案一中场景a检修计划;
[0284]
图6为本发明实施例2的对比方案一中场景b检修计划;
[0285]
图7为本发明实施例2的对比方案一中场景c检修计划;
[0286]
图8为本发明实施例2的对比方案一中各场景ps系统运行情况;
[0287]
图9为本发明实施例2的对比方案一中各场景caes系统运行情况;
[0288]
图10为本发明实施例2的对比方案二中各场景检修成本;
[0289]
图11为本发明实施例2的对比方案二中场景e检修计划;
[0290]
图12为本发明实施例2的对比方案二中场景f、g检修计划;
[0291]
图13为本发明实施例2的对比方案二中场景h、i检修计划。
具体实施方式
[0292]
为了使本发明的目的、技术方案及优点更加清楚明白,以下结合附图及实施例,对本发明进行进一步详细说明。应当理解,此处所描述的具体实施例仅仅用以解释本发明,并不用于限定本发明。此外,下面所描述的本发明各个实施方式中所涉及到的技术特征只要彼此之间不构成冲突就可以相互组合。
[0293]
实施例1:
[0294]
本实施例围绕本发明所述多类型储能系统运行状态评价方法展开,该方法流程示意图如图1所示。本实施例着重描述ps系统关键设备水泵水轮机的运行状态评价过程,其他类型储能系统的评价过程与之类似。本实施例按照如下步骤执行:
[0295]
步骤a:依照表1中水泵水轮机的运行状态评价指标,输入相应指标值的客观数据如表6所示。表中的最优值、极限值、实测值、典型历史测量值需要根据实际情况填入,其中最优情况可填入设备在试验过程中的最理想数据,或者理论上的最理想数据;极限情况可填入使设备容易发生故障的临界值;典型历史数值可填入单个设备正常工作时的定期监测
数据,或者投入时长相近的多个同类型设备的正常工作监测数据;实测值填入当前设备待评价状态下的监测数据。其中,中间最优型指标的最优值为最优上、下限,极限值为极限上、下限。
[0296]
表6
[0297][0298][0299]
步骤b:依照表1中水泵水轮机的运行状态评价指标,输入相应指标值的主观评价值如表7~8所示。表中,每组指标对下含有四个可选项,第一行可填入行指标比列指标“重要”、“不重要”或“同样”重要,第二行自左至右分别是决策者在悲观、中立、乐观态度下对行列两指标相对重要程度的具体判断;当两个指标同样重要时,四个可选项均为“同样”;任意两指标a和b,无论是哪种态度下,a比b重要的程度应和b比a不重要的程度相同;同一指标与自身相比永远是同样重要。
[0300]
表7
[0301][0302][0303]
表8
[0304][0305][0306]
步骤c:依照表5的主观评价量化法则,对表7~8的主观评价进行量化,结果如表9~10所示。
[0307]
表9
[0308][0309]
表10
[0310][0311]
步骤d:依照表9~10的主观评价量化值,求取各指标的主观权重,如表11所示。
[0312]
表11
[0313][0314][0315]
步骤e:依照表6中水泵水轮机运行指标的客观数据,求取各指标的熵值、标准差,以及指标之间的相关系数,如表12~13所示。
[0316]
表12
[0317]
指标熵值标准差x轴向位移/μm0.7686690.379749
y轴向位移/μm0.7022480.384363x轴向振动速率/(mm/s)0.7235740.402394y轴向振动速率/(mm/s)0.717890.367771z轴向振动速率/(mm/s)0.8048510.362942水导轴承温度/℃0.8431990.335703油冷却系统油温/℃0.8589860.357759油冷却系统油位/mm0.8425070.325864油冷却系统油质劣化程度/%0.735330.365499主轴密封磨损程度/mm0.8227250.396003供水系统温度/℃0.7471830.382281供水系统供水压力/bar0.8519890.351047
[0318]
表13
[0319][0320][0321]
步骤f:依照表12~13中水泵水轮机运行指标的熵值、标准差,以及指标之间的相关系数,求取各指标的客观权重,如表14所示。
[0322]
表14
[0323]
指标客观权重
x轴向位移/μm0.088665y轴向位移/μm0.146826x轴向振动速率/(mm/s)0.107183y轴向振动速率/(mm/s)0.110815z轴向振动速率/(mm/s)0.067355水导轴承温度/℃0.050462油冷却系统油温/℃0.050826油冷却系统油位/mm0.050755油冷却系统油质劣化程度/%0.097234主轴密封磨损程度/mm0.074858供水系统温度/℃0.090368供水系统供水压力/bar0.06465
[0324]
步骤g:依照表11中水泵水轮机运行指标主观权重,以及表14中水泵水轮机运行指标客观权重,求取组合权重,如表15所示。
[0325]
表15
[0326][0327]
步骤h:依照表6中水泵水轮机运行指标的客观数据,求取各指标的属性测度,如表16所示。其中,本实施例水泵水轮机运行状态的属性优劣等级设为“最劣”、“较劣”、“较优”、“最优”四级。
[0328]
表16
[0329][0330]
步骤i:依照表15中水泵水轮机运行指标组合权重,以及表16水泵水轮机运行指标属性测度,求取水泵水轮机的属性集测度,如表17所示。
[0331]
表17
[0332][0333]
步骤j:依照表17中水泵水轮机的属性集测度,求取水泵水轮机的综合评分及故障率,如表18所示。其中,各属性优劣等级的评分特征值与评分范围可预先设置,本实施例设置总分30分制。故障率计算公式如下式所示:
[0334][0335]
表18
[0336][0337]
综合实施例1的以上步骤,本发明所述多类型储能系统运行状态评价方法能合理且有效地将设备的运行指标实测数据转化为描述设备运行健康状况的综合评分及故障率,主客观权重组合赋权可以综合考虑决策者的主观偏好和实际数据的客观特征,为后续多类型储能系统检修工作的开展提供了理论与数据支撑,从而避免了检修工作单纯依照专家经验和设备运行时间可能导致的检修需求与工作开展不匹配的问题。
[0338]
实施例2:
[0339]
本实施例围绕本发明所述多类型储能系统检修优化方法展开,具体步骤如下:
[0340]
步骤a:计及多类型储能系统检修计划约束、电力系统运行约束、常规机组运行约束、各类储能系统运行约束等条件,以检修周期内检修实际成本与检修风险成本之和最小为优化目标,建立多类型储能系统检修优化模型。该模型的具体原理说明如下:
[0341]
(1)系统调度架构:包括交流输电网、常规火电机组、风电机组、ps电站、caes电站、pb
‑
bes电站、li
‑
bes电站等部分。
[0342]
(2)优化目标:本发明所述多类型储能系统检修优化方法以检修周期内的检修风险成本与检修实际成本之和最小为优化目标。检修风险成本是指待检修设备在检修周期内的等待检修时段,其发生故障所额外增加的设备故障维修费用和系统运行成本增量。检修风险成本是一个虚拟的成本,它受设备故障率和时间累积效应的影响,即设备故障率越大,等待检修时段越长,那么检修风险成本也应该越大。检修实际成本是指待检修设备进行停机检修时带来的状态检修费用和系统运行成本增量。检修实际成本是一个真实的成本,它是设备检修必然会造成的成本增量。
[0343]
(3)待检修设备的检修计划约束:检修资源约束,限制同时检修的设备数量;检修时长约束,待检修设备开始检修后应保持为检修状态直至检修完成,检修状态持续时段数应等于设定检修时长;检修裕度约束,考虑到一方面不同储能电站之间地理位置不同,另一方面检修过程中可能由于技术或资源问题而造成检修时间延长,需设置检修时间裕度;待检修状态约束,待检修设备在开始检修前处于待检修状态。
[0344]
(4)电力系统运行约束:功率平衡约束,电力系统运行首先应保证功率平衡;系统备用约束,由于风电与负荷的预测存在一定的误差,为保证系统运行安全稳定,需要为系统预留一定量的正负备用容量,以保证在功率波动或发生事故时能够安全运行。
[0345]
(5)常规机组运行约束:一般性约束,保证常规机组的安全稳定运行,包括出力上下限约束、备用容量约束、爬坡率约束、启停时间约束。
[0346]
(6)ps系统运行约束:运行状态约束,限制ps系统的运行工况及其转换过程;功率约束,限制ps系统在发电工况以及抽水工况的最大与最小功率;备用约束,ps系统可以承担部分旋转备用任务,从而减少常规机组备用容量,减少燃料消耗,提高经济性;库容约束,在检修周期内任意时段,上水库水量不能超过库容限值,并且当天结束时的上水库水量不能过低以至于影响第二天ps系统的正常工作;启停转换约束,过于频繁地启停一方面会对机组造成损害,另一方面会增加水头损失,因此需要对机组的日启停次数进行约束。
[0347]
(7)caes系统运行约束:caes系统运行约束主要包括运行状态约束、功率约束、备用约束、储气室气压约束,分别与ps系统的运行状态约束、功率约束、备用约束、库容约束类似,在此不再赘述。
[0348]
(8)pb
‑
bes系统运行约束:pb
‑
bes系统运行约束主要包括运行状态约束、功率约束、备用约束、soc约束、日吞吐量约束,其中前四种约束分别与ps系统的运行状态约束、功率约束、备用约束、库容约束类似,在此不再赘述。日吞吐量是指bes系统日内充放电量总和,减小日吞吐量可以延长电池寿命。
[0349]
(9)li
‑
bes系统运行约束:li
‑
bes系统运行约束主要包括运行状态约束、功率约束、备用约束、soc约束、日吞吐量约束,与pb
‑
bes系统类似,在此不再赘述。
[0350]
步骤b:本实施例的网架结构及参数设置如下。本实施例检修周期设为24小时,采用日前调度,单位调度时长为1h。本实施例采用改进ieee30节点系统进行分析,ps电站接入节点24,风电场和caes电站接入节点23,pb
‑
bes电站接入节点29,li
‑
bes电站接入节点10,系统结构图如图2所示。本实施例负荷及风电参数参考我国某地区典型日24h的负荷及风电数据,二者预测曲线如图3所示。本实施例常规机组的各类运行及成本参数如表19所示。本
实施例ps电站、caes电站、bes电站的的各类运行及成本参数如表20~22所示。本实施例设置有6个待检修储能系统关键设备,其综合评分及故障率均是通过本发明所述多类型储能系统运行状态评价方法生成的,相关检修参数如表23所示。本实施例需预先计算c
normal
、、等不同数量的待检修设备在整个检修周期内退出运行情况下的系统最优成本,如表24所示。除此之外,本实施例假设负荷预测和风力发电预测的最大误差分别为5%和40%,设置弃风成本系数为500$/mw。
[0351]
表19
[0352]
常规机组参数g1g2g3g4g5g6额定出力/mw350240200250350230最小技术出力/mw1003020505030购电成本系数a/($/mw
·
h)38.6449.1258.844642.3654.68购电成本系数b/($/mw
·
h)121.68111.4101.44114.04118.16105.72正备用成本系数/($/mw
·
h)37.6427.3217.430.2434.1621.68负备用成本系数/($/mw
·
h)31.223.2814.220.9223.618.52环境成本系数/($/mw
·
h)0.80.90.90.90.80.9开机成本/$15008905009001450720最小启停机时间/h422242爬坡率/(mw/min)2.34.58.24.62.77.9
[0353]
表20
[0354][0355][0356]
表21
[0357]
参数数值参数数值机组数量1储气室初始气压/bar50压缩机级数4发电工况气压
‑
功率转换系数/(bar/mw
·
h)0.008581膨胀机级数4压缩工况气压
‑
功率转换系数/(bar/mw
·
h)0.004826机组额定发电功率/mw80系统日运维成本/($/mw)5机组最小发电功率/mw32压缩机单位功率造价/($/mw)97500机组额定压缩功率/mw50膨胀机单位功率造价/($/mw)81250机组最小压缩功率/mw20压缩机检修时长(较优,较劣,最劣)/h(3,4,5)储气室最大气压/bar55膨胀机检修时长(较优,较劣,最劣)/h(3,4,5)储气室最小气压/bar40系统检修时间裕度/h2
[0358]
表22
[0359][0360]
表23
[0361][0362][0363]
表24
[0364]
退出的待检修设备编号系统最优成本/$退出的待检修设备编号系统最优成本/$无设备退出1123450.78(1,4)1156674.49711154960.255(1,5)或(1,6)1156671.1692或3或(2,3)1163594.832(2,4)或(3,4)1165300.26941124023.47(2,5)或(3,5)或(2,6)或(3,6)1165425.8635或61124044.103(4,5)或(4,6)1124606.074(1,2)或(1,3)1243068.407(5,6)1124624.358
[0365]
步骤c:为验证本发明所述多类型储能系统检修优化方法的合理性与有效性,本实施例设置两组对比方案。为凸显本发明所述多类型储能系统检修优化方法同时考虑检修风险成本和检修实际成本的优越性,对比方案一设置如下场景:场景a,优化目标仅考虑检修风险成本;场景b,优化目标仅考虑检修实际成本;场景c,优化目标同时考虑两种成本。上述
三种场景除对照条件外,其余参数保持不变且相同。
[0366]
图4为本实施例对比方案一中各场景的检修成本对比情况。分析图中数据可以发现,当检修优化目标为单一的检修风险成本(场景a)或者检修实际成本(场景b)时,其对应的目标成本确实会降低到三种场景下的最优值,然而其未考虑的另一种成本则会升至最高。从检修总成本的角度看,场景c作为一种折中方案,其检修总成本最小,分别比a、b减小了13.34%、10.90%,这说明可以综合考虑检修风险成本和实际成本,降低检修总成本。考虑到两种成本性质不同,可以将两种成本进行归一化求和,如下式所示:
[0367][0368]
式中,c
risk,max
、c
risk,min
、c
real,max
、c
real,min
分别为场景a~c中检修风险成本和检修实际成本的最大值和最小值。由上式计算可得场景a~c的归一化成本之和分别为1、1、0.3484,场景c比a、b均减小了65.16%,说明说明在相同的检修环境下,场景c更倾向于将两种成本降低到该环境下的最小值。
[0369]
图5~7为本实施例对比方案一中各场景的检修计划。由图5可知,若不考虑检修时间裕度,则相当于所有待检修设备连续检修,这符合检修风险成本的时间累积效应。由表23、24可知,图5中设备检修顺序是按照故障维修费用和故障后系统运行成本增量降序排列的,符合降低检修风险成本的目标。
[0370]
由图6及图3可知,ps系统设备的检修时间避开了一天内负荷的最高峰期、低谷期以及风电高发期,考虑到水泵水轮机可以进行抽水工况和发电工况的转换(称之为“双工况设备”),该检修计划避免了水泵水轮机的停机检修与电网的运行需求相违背,从而保证ps系统能够充分参与辅助系统供电、提供备用、提高风电消纳率等。caes系统的压缩机和膨胀机之间没有直接耦合关系,二者均只能工作于单一工况(称之为“单工况设备”),其检修具有特殊性,后续结合图9中caes系统运行情况给出具体分析。bes系统电池簇由于功率容量相对较小,其对于检修实际成本的影响较小,因此在场景b仅考虑检修实际成本的情况下,其检修计划制定时的优先级较低,一般将其安排在ps系统和caes系统检修计划制定完成之后。
[0371]
由图7可知,为保证检修风险成本尽可能降低,此时所有待检修设备在不考虑检修时间裕度的情况下仍是连续检修的,但顺序与图5有所不同。由图3可知,由于风电具有反调峰性,1
‑
6h为风电高发期和负荷低谷期,为提高风电消纳率,储能系统应在该时段吸收多余的风电。图5中,除ps系统机组1外,其他储能系统均可参与该任务;图7中,caes系统在其膨胀机检修时仍可以处于压缩工况,并且ps系统全部机组可用,因此与场景a相比,场景c对风电的消纳能力更强。
[0372]
图8、9分别为本实施例对比方案一中各场景下ps系统、caes系统的运行情况。将电网正常运行场景设置为场景d,即场景d中不考虑储能设备检修,场景d的ps系统及caes系统运行情况也分别绘制到图8、9中,其中发电功率为正,抽水或压缩功率为负;ps系统、caes系统在场景a~c中的运行情况与d相比的平均偏差程度如表25所示。鉴于bes系统的待检修设备功率远小于前二者,故此处不着重分析。对于ps系统,对比分析图8中四类场景的ps系统运行情况和表25中ps系统的运行情况平均偏差程度可知,场景b与场景d的运行情况最为接近,场景a与场景d的运行情况相差最大。对于caes系统,对比分析图9中四类场景的caes系
统运行情况和表25中caes系统的运行情况平均偏差程度,可以得到与ps系统相同的结论。这表明,仅考虑检修实际成本时储能系统的运行情况最接近电网正常运行即无设备检修时的储能系统运行情况,而仅考虑检修风险成本时则偏差最大,即储能系统的工作状况受影响较大。另一方面,分析表25可知,场景a~c中ps系统的运行情况平均偏差程度,均低于场景a~c中caes系统的运行情况平均偏差程度,这是由于ps系统待检修设备的功率仅占总系统的1/4,而对于caes系统而言,任一设备检修均会对总系统的运行工况造成影响。
[0373]
表25
[0374][0375]
ps系统与caes系统的能量日吞吐量如表26所示,该值可以反映储能系统参与电网运行的程度。分析表26可以看出,对于ps系统而言,其在场景c中的能量日吞吐量最大,其次是场景b,最后是场景a。由于ps系统一天内上水库的末时段水量需不小于初时段水量,ps系统参与电网运行就必须保证一定的抽水工况时间,由图8场景d可知,正常运行时抽水工况时段为1~4、6、8、22~24h,若检修工作大量占用抽水工况时段,则会降低ps系统的电网运行参与度。由图5~7可知,三种场景中ps系统1号机组的水泵水轮机检修时段占用抽水工况时段的比例由高到低依次为a、b、c,因此表26中三种场景的ps系统能量日吞吐量的大小关系为a<b<c。由于bes系统电池簇与ps系统水泵水轮机同为双工况设备,因此bes系统电池簇的检修也具有类似的规律。
[0376]
对于caes系统而言,其在场景b中的能量日吞吐量最大,场景a、c基本一致。caes系统的储能和释能设备检修时具有“互不影响”的特征,即当压缩机检修时,caes系统可处于发电工况或空闲状态,当膨胀机检修时,caes系统可处于压缩工况或空闲状态。则对于caes系统中同时存在压缩机和膨胀机需要检修的情况,最佳检修时段为负荷高峰期工况转换前后时段,例如图9中场景d的18~20h前后;对于caes系统中只存在储能或释能设备需要检修的情况,最佳检修时段为caes系统工作于该设备的互斥工况的时段,即压缩机的最佳检修时段为图9场景d的发电工况时段,膨胀机的最佳检修时段为图9场景d的压缩工况时段。由图5~7可知,场景b中caes系统待检修设备安排在16~21h,场景a、c安排在其他时段,因此表26中三种场景的caes系统能量日吞吐量大小关系为b>a≈c。
[0377]
表26
[0378][0379]
步骤d:为说明本发明所述多类型储能系统运行状态评价方法可以有效指导检修工作的开展,对比方案二设置场景e~i,不同场景中ps
‑
1号机组
‑
水泵水轮机的综合评分分别为14、15、16、17、18,其余参数保持不变且相同,优化目标均采用同时考虑两种成本。
[0380]
图10为本实施例对比方案二中各场景的检修成本对比情况,图11~13为本实施例
对比方案二中各场景的检修计划。由图10可知,各项检修成本随ps系统综合评分减小逐渐提高,但在评分由17变为16时检修风险成本降低,对比图12、13可知,这是因为此时检修计划将ps系统提前至检修周期初始时段开始检修,则ps系统不存在检修风险费用。由图11~13可知,随着综合评分的减小,ps
‑
1号机组
‑
水泵水轮机的检修时段逐步被提前,并且评分减小到一定程度检修时间也相应增加。因此,本发明所述多类型储能系统运行状态评价方法能有效指导检修计划的制定。
[0381]
综合实施例2的以上步骤,本发明所述多类型储能系统检修优化方法能综合考虑检修实际成本和检修风险成本,避免了仅考虑检修实际成本时可能造成的设备故障风险和仅考虑检修风险成本时可能造成的系统运行不经济等情况。并且,本发明所述多类型储能系统运行状态评价方法可以有效指导检修计划的制定,设备综合评分越低,检修计划中该设备的检修次序越靠前。
[0382]
本领域的技术人员容易理解,以上所述仅为本发明的较佳实施例而已,并不用以限制本发明,凡在本发明的精神和原则之内所作的任何修改、等同替换和改进等,均应包含在本发明的保护范围之内。