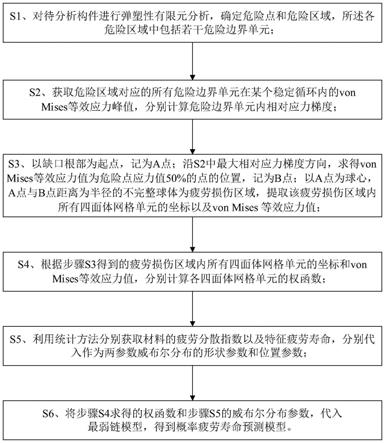
1.本发明属于特种车辆结构完整性与可靠性评估领域,特别涉及一种缺口结构概率疲劳的寿命预测技术。
背景技术:2.科学技术的进步,为现代武器装备工业注入了大量的新鲜血液,刺激着军工制造业的飞速发展,特种车辆作为联合作战中基本的要素和重要的力量,在过去和未来的战场中有着不可替代的作用。特种车辆在研发与制造时,都要求操作系统操作便捷、工作稳定、安全可靠,并且能够适应在远距离、全天候和全地形的作战环境。在恶劣的工作环境和高工作强度下,对其核心部件进行结构完整性与可靠性评估十分必要。钛合金因其高强度、高韧性等优良性能,被应用于各类武器装备中,且钛合金重量相比钢较轻,一直被认为是完美的特种车辆装甲材料。用钛合金作为装甲材料,能达到增强防护力又减重的良好效果。近年来,随着新技术、新工艺的使用,钛合金装甲的价格大幅下降,制造成本不断降低,国内外新型特种车辆的结构框架和部分装甲逐渐使用钛合金制造,以满足更加现代化的特种车辆发展需要。随着我国兵器装备集团在钛合金大型零部件制造、焊接、机加工等方面的高速发展,未来大量钛合金将被广泛应用于特种车辆的基本结构制造。
3.随着现代军事科技的迅速发展进步,现代各类武器装备诸如特种车辆的核心部件设计制造愈发复杂,使用环境愈发恶劣,使用要求不断提高,从而对结构完整性和可靠性产生更高的要求。以特种车辆核心部件发动机为例,在其的结构设计中,为了满足包括冷却、装配、和减重等要求,新提出的设计方案中的部件截面变得愈加复杂,从而导致在外部载荷的作用下在某些位置不可避免的出现应力集中。而应力集中又会促使裂纹萌生,进而导致疲劳损伤和裂纹扩展,因此成为了当前结构完整性和疲劳寿命研究领域的热点问题。各种核心部件的复杂形状导致了在循环载荷作用下的多轴应力-应变状态的出现,因此,基于实验室试样建立的模型不能满足现今对部件疲劳分析的要求,缺口效应的研究还不够完善,有待进一步深入地探讨。此外,尺寸效应也是结构机械完整性设计的关键因素。基于对结构强度和疲劳分析越来越迫切的需求,为了保证装甲车辆核心组件的结构完整性,概率疲劳寿命预测模型以及考虑尺寸和缺口效应的方法的发展备受期待。
4.迄今为止,在缺口构件疲劳寿命预测的研究上已有较深的积累,研究者期望找到一种能够较为合理地表征复杂结构在循环载荷作用下的疲劳失效方法,目前的模型主要基于应力、应变、能量、临界平面以及耦合能量和临界面等四种思路建立,其中基于应力的方法基于疲劳试验中疲劳寿命和应力水平的关系实际建立,在实际预测疲劳寿命操作简便,被认为是缺口疲劳分析最直接的方法。而对缺口效应而言,由于存在应力集中的作用,缺口表面位置处的局部应力水平往往偏高,但是随着往内部的深入,应力迅速下降,未屈服部分对危险部位的屈服部分仍然起着支撑作用,故而仅仅将危险点处的应力应变作为整体疲劳和失效的判据是不合理的,针对此问题,研究者提出了名义应力法、局部应力应变法、应力场强法和临界距离理论等方法;但是名义应力法和局部应力应变法未考虑缺口处的应力集
中,预测结果误差大;应力场强法和临界距离理论所需参数获取困难。
技术实现要素:5.为解决上述技术问题,基于综合考虑缺口效应以及尺寸效应作用的需要,本发明在最弱链模型法的基础上耦合应力场强法权函数来表征缺口支撑效应的影响,提出了一种计算简单且能同时考虑尺寸效应和缺口效应作用的疲劳寿命预测方法。
6.本发明采用的技术方案为:一种加权耦合最弱链模型的缺口结构概率疲劳寿命预测方法,采用基于应力场强法权函数来对不同位置的材料疲劳失效概率进行修正,在最弱链模型的基础上,得到概率疲劳寿命预测模型,基于概率疲劳寿命预测模型进行缺口结构概率疲劳寿命预测。
7.得到概率疲劳寿命预测模型的过程为:
8.s1、对待分析构件进行弹塑性有限元分析,确定危险点和危险区域,所述各危险区域中包括若干危险边界单元;
9.s2.获取危险区域对应的所有危险边界单元在某个稳定循环内的von mises等效应力峰值,分别计算危险边界单元内相对应力梯度;
10.s3.以缺口根部为起点,记为a点;沿s2中最大相对应力梯度方向,求得von mises等效应力值为危险点应力值50%的点的位置,记为b点;以a点为球心,a点与b点距离为半径的不完整球体为疲劳损伤区域,提取该疲劳损伤区域内所有四面体网格单元的坐标以及von mises等效应力值;
11.s4.根据步骤s3得到的疲劳损伤区域内所有四面体网格单元的坐标和von mises等效应力值,分别计算各四面体网格单元的权函数;
12.s5.利用统计方法分别获取材料的疲劳分散指数kn以及特征疲劳寿命n
*
,分别代入作为两参数威布尔分布的形状参数和位置参数;
13.s6.将步骤s4求得的权函数和步骤s5的威布尔分布参数,代入最弱链模型,得到概率疲劳寿命预测模型。
14.步骤s1所述危险区域包括所有发生局部应力集中的区域。
15.步骤s5获取材料的疲劳分散指数kn以及特征疲劳寿命n
*
的过程为:首先将同一应力水平下的不用疲劳寿命按数值大小顺序排列,分别计算各疲劳寿命对应下的失效概率,对疲劳寿命与失效率进行线性拟合获得该应力水平下的kn和n
*
;求解不同应力水平下的分布参数kn和n
*
,最终kn取所有应力水平下疲劳寿命指数的均值,并且拟合疲劳特征寿命n
*
和应力水平σ
max
的basquin公式:σ
max
=a(n
*
)b;
16.其中,a、b为材料常数。
17.所述a、b在拟合疲劳特征寿命n
*
同时获得。
18.步骤s6所述概率疲劳寿命预测模型表达式为:
[0019][0020]
其中,nf为疲劳寿命,v(i)为第i个四面体网格单元的体积,v
ω
为疲劳损伤区域的体
积,n
*
和kn分别威布尔位置参数和形状参数,为第i个四面体网格单元的权函数,第i个四面体网格单元的von mises等效应力幅值,r(i)第i个四面体网格单元到缺口根部的距离,θ(i)第i个四面体网格单元与最大应力梯度方向的偏离角。
[0021]
根据步骤s6的概率疲劳寿命预测模型,求解构件在不同寿命下的失效概率,获得构件疲劳试验寿命分散性量化结果,以50%失效概率时构件的疲劳寿命作为预测结果。
[0022]
步骤s4所述的四面体网格单元的权函数表达式为:
[0023][0024]
其中,σ
a,max
为构件最大von mises等效应力,r为疲劳损伤区域的半径。
[0025]
本发明的有益效果:本发明的方法,在最弱链模型的计算失效概率的初始公式的基础上,引入应力场强法权函数的来对缺口效应进行修正,最后得到一个新的最弱链模型失效概率计算公式;具有以下优点:
[0026]
(1)通过结合适用于尺寸效应的最弱链模型和用于表征缺口效应的应力场强法权函数,将尺寸效应和缺口效应有机的结合了起来了,既能体现疲劳试验中疲劳强度通常随试样尺寸增大而降低的实际,又能反应缺口不均匀应力分布对疲劳强度的影响,综合考虑了两者对疲劳寿命的影响;
[0027]
(2)新提出了一种疲劳损伤区域定义,该定义下的疲劳损伤区域会随试样尺寸增大而增大,能更好体现尺寸效应对疲劳寿命的影响,且所定义疲劳损伤区域可直接通过有限元分析确定,无需通过反复试验获取;
[0028]
(3)新提出了一种基于单元位置和应力水平的权函数,提取计算操作简便,材料常数kn,n
*
,a和b的拟合简便,修正公式简洁;经过权函数修正的最弱链模型,预测结果分散性小,准确度高,且能用于任何尺寸的缺口构件概率疲劳寿命预测,更具普适性。
附图说明
[0029]
图1为本发明实施例提供的tc4合金疲劳试验试件尺寸;
[0030]
其中,图1(a)为tc4应力集中系数k
t
=3的缺口试件尺寸,图1(b)为tc4应力集中系数k
t
=5的缺口试件尺寸;
[0031]
图2本发明实施例提供的方案流程图;
[0032]
图3为本发明的方法应用于钛合金tc4缺口件疲劳寿命分散性量化的结果图;
[0033]
其中,图3(a)为tc4应力集中系数k
t
=3的缺口试件疲劳寿命分布图,图3(b)为tc4应力集中系数k
t
=5的缺口试件疲劳寿命分布图;
[0034]
图4为本发明方法对tc4的预测寿命与试验寿命比较。
具体实施方式
[0035]
为便于本领域技术人员理解本发明的技术内容,下面结合附图对本发明内容进一步阐释。
[0036]
本发明通过tc4材料的疲劳试验数据对该模型进行了验证,具体包括理论应力集
中系数k
t
=3、5的tc4试件,其中tc4试件的试验在常温下进行,k
t
=3和5的缺口试件尺寸如图1中的(a)、(b)所示,图1中d为试样夹持端直径,d为试样标距段的直径,r为缺口半径,θ为缺口张开角。目前仅以tc4材料作为实施例进行说明,材料参数和试验数据详见表1、表2。危险点是指局部应力最大的位置,危险点附近的区域为危险区域,危险区域内包含若干危险边界单元;
[0037]
如图2所示为本技术的方案流程图,本发明的技术方案为:一种加权耦合最弱链模型的缺口结构概率疲劳寿命预测方法,包括:
[0038]
s1.对待分析构件进行弹塑性有限元分析,确定其应力应变分布以及可能发生疲劳失效的危险区域,所述危险区域中含若干危险边界单元;如表1所示,首先确定tc4材料的疲劳特性;然后在有限元分析软件中添加tc4材料静态参数并根据单轴疲劳参数计算和添加多线性随动硬化(kinh,the multilinear kinematic hardening)本构模型中的应力应变数据点,应力应变数据点可以通过ramberg-osgood方程得到;对tc4金属试件或者构件进行有限元分析,通过应力应变分布确定其危险区域,因为存在缺口效应的影响,仅仅取应力或应变最大位置不合理,所以应将所有发生局部应力集中的区域均囊括在内,并据此确定若干危险边界单元。
[0039]
步骤s1中所述的对待分析构件进行弹塑性有限元分析,是根据待分析构件实际加载进行弹塑性有限元分析,确定危险点和危险区域。
[0040]
s2.获取各危险区域对应的所有危险边界单元在某个稳定循环内的von mises等效应力峰值,根据危险点附近危险边界单元内的von mises等效应力的分布,计算危险边界单元内归一化相对应力梯度χ
elem
,归一化处理的具体操作为:将危险边界单元内相对应力梯度χ
elem
除以危险点von mises等效应力峰值σ
a,max
,得到各单元归一化的相对应力梯度χ
nor
;
[0041]
s3.以缺口根部为起点,沿着步骤s2得到最大相对应力梯度方向定义一条过危险点的路径来获得危险点附近危险边界单元内von mises等效应力的分布,进而求得von mises等效应力值为危险点(缺口根部)50%的点的位置;以危险点为球心,上述两点距离为半径的不完整球体为疲劳损伤区域,提取该疲劳损伤区域内所有四面体网格单元的坐标以及von mises等效应力峰值,分别记为x(i),y(i),z(i),σ
a(i)
,i为单元编号;疲劳损伤区域内的四面体网格单元,针对如图1所示的试样尺寸,本实施例中网格尺寸0.025mm,一个四面体网格单元中有十个节点,这十个节点的坐标和von mises应力值取平均值后即为该四面体网格单元的坐标和von mises应力值。
[0042]
在实际应用中网格的尺寸可以根据实际情况进行取值,试样尺寸越大,则网格分网尺寸取值越大,不同分网尺寸,应保证各自得到的最终疲劳寿命计算结果误差保持在3%以内。
[0043]
s4.根据步骤s3得到的疲劳损伤区域内所有单元的坐标和von mises等效应力值,分别计算各单元权函数,并代入最弱链模型中;
[0044]
s5.利用统计方法分别获取材料的疲劳分散指数以及疲劳分布指数,分别代入作为两参数威布尔分布的形状参数和位置参数。所述材料疲劳分布指数kn和特征疲劳寿命n
*
的确定过程为:首先将同一应力水平下的不用疲劳寿命按数值大小顺序排列,分别计算各疲劳寿命对应下的失效概率,对疲劳寿命与失效率进行线性拟合获得该应力水平下的kn和n*
;求解不同应力水平下的分布参数kn和n
*
,最终kn取所有应力水平下疲劳寿命指数的均值,并且拟合疲劳特征寿命n
*
和应力水平σ
max
的basquin公式,式中a、b为材料常数,可在拟合疲劳特征寿命n
*
同时获得:
[0045]
σ
max
=a(n
*
)b[0046]
s6.根据s4和s5步骤求得的权函数和威布尔分布参数,求解构件在不同寿命下的失效概率,获得构件疲劳试验寿命分散性量化结果,以50%失效概率时构件的疲劳寿命作为预测结果。
[0047]
步骤s6的实现过程为:
[0048]
a1、基于最弱链模型的疲劳寿命预测初始公式为:
[0049][0050]
其中,nf为疲劳寿命,v0为参考试样体积,n
*
和kn分别威布尔位置参数和形状参数,根据材料的不同有不同的取值;
[0051]
a3.分别计算疲劳损伤区域内各单元的权函数,计算公式为:
[0052][0053]
其中为第i个单元的权函数,r(i),θ(i)分别为第i个单元的von mises等效应力幅值、到缺口根部的距离、与最大应力梯度方向的偏离角,σ
a,max
为构件最大vonmises等效应力,r为疲劳损伤区域的半径,可由步骤s3可获得。
[0054]
a3.基于步骤a1中的式子,结合a2得到的疲劳损伤区域点各单元的权函数数值对缺口效应的影响进行修正,得到的新的概率疲劳寿命预测的公式为:
[0055][0056]
其中,v(i)为第i个四面体网格单元的体积,v
ω
为疲劳损伤区域的体积。
[0057]
一般来说,在基于应力分布和最弱链模型计算构件疲劳失效概率时是不需要考虑各单元的位置对单元失效概率的影响,而发明人发现各种疲劳试验现象表明:同一应力水平的单元,位置越靠近危险点,失效概率越大,在此发明中基于各单元的位置对其失效概率进行加权修正,就能将基于应力场强法的权函数的适用面拓宽,让其在对任意的几何形状的应力集中/缺口构件进行结构完整性和可靠性分析时具有普遍适用性。
[0058]
如图3所示为本发明的方法应用于钛合金tc4缺口件疲劳寿命分散性量化的结果图,从图3可以看出,本发明提供的方法较好的表征了疲劳寿命的分散性,试验结果基本在10%和90%存活率的概率分散带内;图4为本发明的方法对tc4的预测寿命与试验寿命对比图,可以看出,绝大部分寿命预测结果在两倍误差带以内,证明本技术所提出的寿命预测模型取得了较好的预测效果,tc4的材料性能参数以及疲劳试验数据如表1、2所示:
[0059]
表1 tc4的材料性能参数
[0060][0061]
表2对称载荷下tc4的疲劳试验数据
[0062]
no.k
t
σ
max
(mpa)n
t
(cycles)no.k
t
σ
max
(mpa)n
t
(cycles)1349516063031502622182349517463131503297893349519553231503892684349521303352753451534952707345275548163395450735527560427339550543652758975833955276375275100149339557383851958462103395608939519517566113260236614051951885912326025732415195278991332602921542519533968143260309384351652603915326034203445165287031632604045445516536914173180107629465165540571831801490344751656952119318018936748516576632203180209348495951043152131802309635059512908322318025848851595139996233170269842525951590842431608842653595175357253160218544545952223402631603152665559528248427316039006656585343926
28315013481057585443210293150200539
ꢀꢀꢀꢀ
[0063]
本领域的普通技术人员将会意识到,这里所述的实施例是为了帮助读者理解本发明的原理,应被理解为本发明的保护范围并不局限于这样的特别陈述和实施例。对于本领域的技术人员来说,本发明可以有各种更改和变化。凡在本发明的精神和原则之内,所作的任何修改、等同替换、改进等,均应包含在本发明的权利要求范围之内。