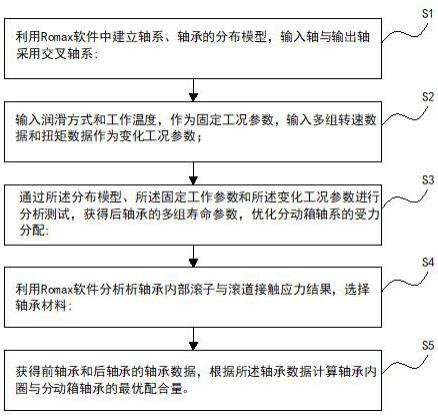
1.本发明涉及轴承设计技术领域,尤其涉及一种分动箱轴承最优配合参数设计方法。
背景技术:2.所谓分动箱,就是将发动机的动力进行分配的装置,目前分动箱已经进入大功率、大扭矩的时代,所采用的齿轮模数越来越大、体积也就越来越大,占据了较大空间,壳体内齿轮运转所散出的热量较大,在分动箱箱体内会形成高温,因此对齿轮和轴承的寿命带来不良影响。
3.目前在轴承最优配合量的研究方面,往往通过经验来确定轴承配合量,没有考虑轴系的受力分配,导致轴承的使用寿命缩短。
技术实现要素:4.本发明的目的在于提供一种分动箱轴承最优配合参数设计方法,旨在解决现有技术中在轴承最优配合量的研究方面,往往通过经验来确定轴承配合量,没有考虑轴系的受力分配,导致轴承的使用寿命缩短的技术问题。
5.为实现上述目的,本发明提供了一种分动箱轴承最优配合参数设计方法,包括如下步骤:
6.利用romax软件中建立轴系、轴承的分布模型,输入轴与输出轴采用交叉轴系;
7.输入润滑方式和工作温度,作为固定工况参数,输入多组转速数据和扭矩数据作为变化工况参数;
8.通过所述分布模型、所述固定工作参数和所述变化工况参数进行分析测试,获得后轴承的多组寿命参数,优化分动箱轴系的受力分配;
9.利用romax软件分析析轴承内部滚子与滚道接触应力结果,选择轴承材料;
10.获得前轴承和后轴承的轴承数据,根据所述轴承数据计算轴承内圈与分动箱轴承的最优配合量。
11.其中,在利用romax软件中建立轴系、轴承的分布模型,输入轴与输出轴采用交叉轴系的步骤中:
12.输入轴和输出轴之间的传动方式采用螺旋线锥齿轮传动,输入轴的前支撑轴承和后支撑轴承均采用分动惯用的圆锥滚子轴承。
13.其中,在利用romax软件中建立轴系、轴承的分布模型,输入轴与输出轴采用交叉轴系的步骤中:
14.输出轴的后支撑轴承采用32909标准型结构轴承。
15.其中,在输入润滑方式和工作温度,作为固定工况参数,输入多组转速数据和扭矩数据作为变化工况参数的步骤中:
16.润滑方式采用90w变速箱油进行润滑,工作温度为90℃。
17.其中,在输入润滑方式和工作温度,作为固定工况参数,输入多组转速数据和扭矩数据作为变化工况参数的步骤中:
18.所述变化工况参数包括第一工况、第二工况和第三工况;所述第一工况的转速为430r/min,扭矩为72nm;所述第二工况的转速为156r/min,扭矩为1900nm;所述第三工况的转速为480r/min,扭矩为600nm。
19.其中,在通过所述分布模型、所述固定工作参数和所述变化工况参数进行分析测试,获得后轴承的多组寿命参数,优化分动箱轴系的受力分配的步骤中:
20.romax软件软件分析的理论依据为iso281和ts16281国际标准的轴承寿命计算方法。
21.其中,在通过所述分布模型、所述固定工作参数和所述变化工况参数进行分析测试,获得后轴承的多组寿命参数,优化分动箱轴系的受力分配的步骤中:
22.将所述变化工况参数分别带入iso281和ts16281国际标准进行分析得到后轴承的寿命;第一工况的后轴承寿命为5880h,第二工况的后轴承寿命为3.8h,第三工况的后轴承寿命为826h。
23.其中,在利用romax软件分析析轴承内部滚子与滚道接触应力结果,选择轴承材料的步骤中;
24.对不同轴承钢材料的接触疲劳寿命及寿命离散度进行评估,分析轴承材料的冶炼质量对轴承性能和寿命的影响,从而选择轴承材料。
25.其中,在获得前轴承和后轴承的轴承数据,根据所述轴承数据计算轴承内圈与分动箱轴承的最优配合量的步骤中:
26.通过在几何建模软件proe/e中建立主轴系统的实体模型,并对输入轴和输出轴实体模型进行模型简化;所述轴承数据包括轴承内圈材料的密度,轴承的旋转角速度、轴承内圈材料的弹性模量、轴承的内圈半径、轴承的外圈半径、工作温度、摩擦热和润滑剂粘度。
27.其中,在获得前轴承和后轴承的轴承数据,根据所述轴承数据计算轴承内圈与分动箱轴承的最优配合量的步骤中:
28.根据轴承的工作温度、摩擦热、润滑剂粘度计算轴承的稳态温度场,根据轴承内圈材料的密度,轴承的旋转角速度、轴承内圈材料的弹性模量、轴承的内圈半径、轴承的外圈半径计算轴承的迭代初值,将所述稳态温度场和所述迭代初值带入proe/e中建立主轴系统的实体模型,得到最优配合量。
29.本发明的一种分动箱轴承最优配合参数设计方法,利用romax软件中建立轴系、轴承的分布模型,输入轴与输出轴采用交叉轴系;输入润滑方式和工作温度,作为固定工况参数,输入多组转速数据和扭矩数据作为变化工况参数;通过所述分布模型、所述固定工作参数和所述变化工况参数进行分析测试,获得后轴承的多组寿命参数,优化分动箱轴系的受力分配;利用romax软件分析析轴承内部滚子与滚道接触应力结果,选择轴承材料;获得前轴承和后轴承的轴承数据,根据所述轴承数据计算轴承内圈与分动箱轴承的最优配合量,通过上述方法,优化分动箱轴系受力分配,调整齿轮和轴承的位置以及齿轮结构,合理分配前、后轴承的承载,更改后轴承的尺寸型号或内部结构参数,使后轴承具有更高的轴向承载能力,从而提高轴承的使用寿命;避免了传统方法利用经验来确定轴承配合量所带来的问题,使轴承配合参数设计更加合理。
附图说明
30.为了更清楚地说明本发明实施例或现有技术中的技术方案,下面将对实施例或现有技术描述中所需要使用的附图作简单地介绍,显而易见地,下面描述中的附图仅仅是本发明的一些实施例,对于本领域普通技术人员来讲,在不付出创造性劳动的前提下,还可以根据这些附图获得其他的附图。
31.图1是本发明提供的一种分动箱轴承最优配合参数设计方法的步骤流程图。
具体实施方式
32.下面详细描述本发明的实施例,所述实施例的示例在附图中示出,其中自始至终相同或类似的标号表示相同或类似的元件或具有相同或类似功能的元件。下面通过参考附图描述的实施例是示例性的,旨在用于解释本发明,而不能理解为对本发明的限制。
33.请参阅图1,本发明提供一种分动箱轴承最优配合参数设计方法,包括如下步骤:
34.s1:利用romax软件中建立轴系、轴承的分布模型,输入轴与输出轴采用交叉轴系;
35.s2:输入润滑方式和工作温度,作为固定工况参数,输入多组转速数据和扭矩数据作为变化工况参数;
36.s3:通过所述分布模型、所述固定工作参数和所述变化工况参数进行分析测试,获得后轴承的多组寿命参数,优化分动箱轴系的受力分配;
37.s4:利用romax软件分析析轴承内部滚子与滚道接触应力结果,选择轴承材料;
38.s5:获得前轴承和后轴承的轴承数据,根据所述轴承数据计算轴承内圈与分动箱轴承的最优配合量。
39.其中,在步骤s1中,利用romax软件中建立轴系、轴承的分布模型,输入轴与输出轴采用交叉轴系,输入轴和输出轴之间的传动方式采用螺旋线锥齿轮传动,输入轴的前支撑轴承和后支撑轴承均采用分动惯用的圆锥滚子轴承;输出轴的后支撑轴承采用32909标准型结构轴承,为易失效齿轮,加快实验速度。
40.在步骤s2中,输入润滑方式和工作温度,作为固定工况参数,输入多组转速数据和扭矩数据作为变化工况参数,润滑方式采用90w变速箱油进行润滑,工作温度为90℃;由输入轴左侧施加扭矩载荷,分别输入三组转速数据和扭矩数据,分别进行三个工况的模拟;第一工况为转速430r/min,扭矩72nm,第二工况为转速156r/min,扭矩1900nm,第三工况为转速480r/min,扭矩600nm。
41.在步骤s3中,通过所述分布模型、所述固定工作参数和所述变化工况参数进行分析测试,获得后轴承的多组寿命参数,优化分动箱轴系的受力分配,从轴承的总体寿命总结结果来看,前轴承可以满足试验工况要求;后轴承寿命较短,不能达到600h试验寿命的要求。首先,试验工况的模拟并不能完全代表车辆实际运行的工况,试验工况往往设计偏于保守,这就导致了轴承在使用过程中未必如分析一般显现的失效的概率;
42.其次,romax软件分析的理论依据为iso281和ts16281国际标准的轴承寿命计算方法,可得到在iso281的标准下:后轴承的寿命为31h,前轴承的寿命为1462h;在ts16281的标准下:后轴承的寿命为51h,前轴承的寿命为1717h;分析结果侧面反映了车辆在实际运行工作过程中将存在分动器后轴承疲劳失效的风险;
43.将三个工况带入软件进行分析得到后轴承的寿命,在iso281标准下,第一工况的
寿命为1880h,第二工况为3.8h,第三工况为178h;在ts16281的标准下,第一工况的寿命为5880h,第二工况为3.8h,第三工况为826h;轴承只起到承载轴重并提供转动的能力,其本身是不直接承载扭矩的,因此,输入扭矩所导致的轴系受力必将是后轴承不能满足要求的主要原因,通过上述数据,可选取第一工况的扭矩数据对分动箱轴系的受力分配进行优化,增大工况测试量,可进一步进行优化。
44.在步骤s4中,利用romax软件分析析轴承内部滚子与滚道接触应力结果,选择轴承材料,根据gb/t4662《滚动轴承额定静负荷》的规定,圆锥滚子轴承的额定静负荷应力果,对不同轴承钢材料的接触疲劳寿命及寿命离散度进行评估,分析轴承材料的冶炼质量对轴承性能和寿命的影响,选择性能优良的材料。
45.在步骤s5中,在几何建模软件proe/e中建立主轴系统的实体模型,并对输入轴和输出轴实体模型进行模型简化,删除小于1mm的阶梯,删除输出轴和输入轴上的螺纹及螺纹孔,删除倒角和圆角;分别获得前轴承和后轴承的轴承数据,根据所述轴承数据计算轴承内圈与分动箱轴承的最优配合量;所述轴承数据包括轴承内圈材料的密度,轴承的旋转角速度、轴承内圈材料的弹性模量、轴承的内圈半径、轴承的外圈半径、工作温度、摩擦热和润滑剂粘度,考虑轴承与轴承内圈离心膨胀的影响,通过公式:
[0046][0047]
进行计算,其中δ1为迭代初值,ρ为轴承内圈材料密度,ω为轴承的旋转角速度,e为轴承内圈材料的弹性模量,r1为轴承的内圈半径,r2为轴承的外圈半径;根据轴承的工作温度、摩擦热、润滑剂粘度计算轴承的稳态温度场将所述稳态温度场和所述迭代初值带入proe/e中建立主轴系统的实体模型,得到最优配合量。
[0048]
利用romax软件中建立轴系、轴承的分布模型,输入轴与输出轴采用交叉轴系;输入润滑方式和工作温度,作为固定工况参数,输入多组转速数据和扭矩数据作为变化工况参数;通过所述分布模型、所述固定工作参数和所述变化工况参数进行分析测试,获得后轴承的多组寿命参数,优化分动箱轴系的受力分配;利用romax软件分析析轴承内部滚子与滚道接触应力结果,选择轴承材料;获得前轴承和后轴承的轴承数据,根据所述轴承数据计算轴承内圈与分动箱轴承的最优配合量,通过上述方法,优化分动箱轴系受力分配,调整齿轮和轴承的位置以及齿轮结构,合理分配前、后轴承的承载,更改后轴承的尺寸型号或内部结构参数,使后轴承具有更高的轴向承载能力,从而提高轴承的使用寿命;避免了传统方法利用经验来确定轴承配合量所带来的问题,使轴承配合参数设计更加合理。
[0049]
以上所揭露的仅为本发明一种较佳实施例而已,当然不能以此来限定本发明之权利范围,本领域普通技术人员可以理解实现上述实施例的全部或部分流程,并依本发明权利要求所作的等同变化,仍属于发明所涵盖的范围。