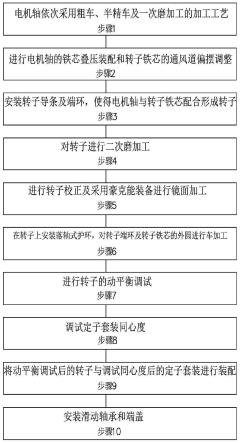
1.本发明涉及一种降低电机轴径向位移的加工及装配工艺,属于轴承加工领域。
背景技术:2.随着国民经济的高速发展,大中型电机的应用范围越来越广泛,很多行业对电机质量稳定性的依赖越来越高。压缩机是采矿业、化学工业、机械制造业、制冷与气体分离工程及国防等工业必不可少的机械,某些行业对压缩机质量稳定性要求特别高,电机作为压缩机工作的核心驱动设备必然要长期稳定地运行才能满足市场需求。
3.压缩机上使用的电机转速一般较高,一些大型的压缩机通常使用高速大中型滑动轴承结构电机作为驱动设备,大多数的压缩机企业要求监控电机工作状态的轴径向位移,为了更及时地监控并保障压缩机的运行稳定性,某些压缩机企业规定电机高速运行时的轴径向位移标准远远高于国标,现场运行的压缩机经常出现因为轴径向位移超标的故障而被迫停机,很多电机厂因为电机质量不过关频繁遭到投诉。
4.大多数的客户使用电涡流传感器检测电机的轴径向位移。电机制造过程中轴位移的大小主要与转子轴加工精度、铁芯叠压质量、动平衡精度及装配质量等因素有关。高速电机因其转速过高而容易出现轴径向位移超标现象,进而影响使用品质及寿命,如何降低电机轴径向位移成为许多企业面临的难题。因此需要设计一种降低电机轴径向位移的加工及装配工艺。
技术实现要素:5.本发明的目的在于克服上述不足之处,通过科学合理的加工及装配工艺降低电机运行时的轴径向位移,提高电机质量稳定性,延长电机的使用寿命。
6.按照本发明提供的技术方案,一种降低电机轴径向位移的加工及装配工艺,包括以下步骤:
7.步骤1,电机轴依次采用粗车、半精车及一次磨加工的加工工艺;
8.步骤2,在电机轴一次磨加工后,进行电机轴的铁芯叠压装配和转子铁芯的通风道偏摆调整;
9.步骤3,在通风道偏摆调整后,安装转子导条及焊接端环,使得电机轴与转子铁芯配合形成转子;
10.步骤4,转子导条及焊接转子端环焊接后,对转子进行二次磨加工;
11.步骤5,转子二次磨加工后,进行转子校正及采用豪克能装备进行镜面加工;
12.步骤6,在转子镜面加工后,在转子上安装落轴式护环,转子端环及转子铁芯的外圆进行车加工;
13.步骤7,转子端环及转子铁芯的外圆转进行车加工后,进行转子的动平衡调试;
14.步骤8,调试定子套装同心度;
15.步骤9,将动平衡调试后的转子与调试同心度后的定子套装进行装配;
16.步骤10,在步骤9中得到的转子与定子套装的装配体上安装滑动轴承与端盖。
17.作为本发明的进一步改进,所述所述步骤1中,电机轴在粗车后至半精车前,在电机轴的轴承档处用精车的车刀加工一个基准线。
18.作为本发明的进一步改进,所述步骤2中,在电机轴的配合档进行转子铁芯叠压装配,其叠压压力高于图纸要求5%以内;转子铁芯锁紧后再次测试压力必须高于图纸要求的5%范围内,确保压力高于图纸要求的5%范围内。
19.作为本发明的进一步改进,所述步骤3中,在一次磨加工后,使用千分表检查各档位的跳动值,所述跳动值包括形位公差,检测形位公差时需注意两端跳动高点方向是否一致,若不一致则两端跳动累计值应≤0.008mm;另外检测跳动时,同一个圆截面上出现两个或两个以上高点,将中心孔重新修正后再进行磨加工。
20.作为本发明的进一步改进,所述步骤4,将转子固定在磨床上,二次磨加工轴伸档、轴承档、内密封档和外密封档。
21.作为本发明的进一步改进,所述步骤9中,根据转子的重量及轴径选择穿装转子的方式及起吊位置,穿入定子套装;电机轴中心高≤630mm时,使用单臂吊穿装转子,穿装时根据轴径大小选择合适的铜套筒,其套筒直径与电机轴的轴径差≤10mm,起吊位置选择轴承档和配合档之间的空档处;电机轴中心高≥710mm,使用穿装管抬穿转子,穿装时根据轴径大小选择合适的铜套筒,套筒直径与轴径差≤10mm,转子两端需要使用5mm橡皮垫包裹,起吊位置选择两个轴承档的位置。
22.作为本发明的进一步改进,所述步骤10中,在拧紧滑动轴承的上轴承座之前,采用行车盘转动转子5~6圈,滑动轴承自找正后再拧紧滑动轴承的上轴承座。
23.本发明的有益效果在于:
24.本发明通过合理化加工及装配顺序,多方面降低电机轴振动风险,以及减少轴径向位移,提高电机运行稳定性,延长电机的使用寿命。
附图说明
25.图1为本发明的装配步骤图。
26.图2为本发明的电机轴示意图。
27.图3为本发明的转子示意图。
28.图4为本发明的转子吊装示意图。
29.图5为本发明中转子及定子装配后总图。
30.附图标记说明:1、轴承档;2、配合档;3、转子铁芯;4、检测铁芯通风道;5、转子导条;6、转子端环;7、落轴式护环;8、轴伸档;9、内密封档;10、外密封档;11、单臂吊;12、铜套筒;13、穿装管;14、橡皮垫;15、端盖;16、滑动轴承。
具体实施方式
31.下面本发明将结合附图中的实施例作进一步描述:
32.如图所示,一种降低电机轴径向位移的加工及装配工艺,包括以下步骤:
33.步骤1,电机轴采用粗车、半精车及一次磨加工的加工工艺;
34.首先固定电机轴,电机轴粗车加工,尽可能去除多余材料提高加工效率,然后半精
车保证工件的精度,达到工艺的参数要求,无论电机轴轴材料加工余量多与少都要按照上述过程执行,一方面可以保证适当的加工效率,另一方面可以减少加工应力,降低轴的加工应力变形,提高加工精度,增加转子运行的稳定性,降低电机运转时的轴径向位移。
35.为了提高加工效率,粗车后轴在自由状态下静置24小时降低粗车时产生的内应力(因粗车后再精车会大幅降低加工时间,静置时间仅影响装配效率,在此不做赘述),上车床半精车转轴,然后在电机轴的轴承档1处用精车的车刀加工一个基准线,为后续各道工序加工提供基准,最后上磨床第一次磨加工电机轴与转子铁芯的配合档2。
36.其中电机轴的磨加分两次完成,二次磨加工前,需要先一次磨加工轴伸档8、轴承档1、内外密封档,待转子铁芯3叠压、转子端环6焊接后再二次磨加工。
37.步骤2,电机轴的铁芯叠压装配和铁芯的通风道偏摆调整;在电机轴的配合档进行转子铁芯3的叠压装配,其叠压压力高于图纸要求5%以内;转子铁芯3锁紧后再次测试压力必须高于图纸要求的5%范围内,确保压力高于图纸要求的5%范围内,进行通风道偏摆调整;
38.按照图纸要求叠片,用c型卡规控制铁芯每组冲片偏差在
±
0.5mm,根据图纸长度采用合理的预压次数,转子铁芯3加压压力高于图纸要求5%以内,在保压状态下锁紧转子铁芯3上下压板的连接螺杆,螺杆锁紧后要检查压机的压力,确保压力高于图纸要求的5%范围内。在进行通风道偏摆调整前,复测转子铁芯3圆周,选取四个点的长度尺寸测出偏差,将偏差控制在1mm范围内,然后转子铁芯3加热套轴固定;紧接着进行转子铁芯3的通风道偏摆调整,因为转子冲片毛刺、冲片变形,通风槽板变形等因素存在,转子叠压后容易出现通风道偏摆过大的情况,导致转子运行时不稳定因素增加,铁芯通风道偏摆必须控制在2mm以内。
39.步骤3,安装转子导条5及焊接转子端环6;铁芯通风道4的偏摆校正后,安装转子导条5及焊接转子端环6;转子端环6与转子导条5之间使用银铜焊条进行中频焊接,减小焊接热影响区。转子端环6上加工焊接槽,焊接时保证笼条与端环焊缝饱满,保证焊接处的牢固性,增加转子高速旋转时的稳定性,使得电机轴与转子铁芯3配合形成转子;
40.步骤4,对转子进行二次磨加工;转子导条5及焊接转子端环6焊接后,将转子固定在磨床上,以精车时预留的基准线为基准,磨加工轴伸档8、轴承档1、内密封档9、外密封档10。磨加工后需要使用千分表检查各档位的跳动,检查跳动时要搭在各档位的靠边处,防止因砂轮边角残缺产生的不良跳动漏检,检测形位公差时需注意两端跳动高点方向是否一致(指两端高点位置在圆周方向的角度要在45
°
以内),若不一致则两端跳动累计值应≤0.008mm;另外检测跳动时,同一个圆截面上不能出现两个及两个以上高点,若出现两个或两个以上高点,则说明中心孔有问题,必须将中心孔重新修正后再进行磨加工。
41.转子再上磨床检查各档位的同心度,如无异常磨加工转轴轴伸档、轴承档、内外密封档。转子叠压或是转运过程中有可能造成轻微的轴变形及加工面粗糙度降低,转子叠压后再磨加工过程中可以避免上述问题,提高转子表面粗糙度及形位公差,提高转子运行时稳定性,降低振动和轴径向位移。
42.步骤5,转子校正及采用豪克能装备进行镜面加工;仔细检查清理轴承档1、内密封档9、外密封档10并确保清理干净,转子上车床校正,保证转子各加工档位跳动在0.02mm以内;装上豪克能加工设备进行镜面加工,金属表面性能得以有效的改善,据相关试验可知利
用豪克能加工过的金属表面可以有效地提高金属表面的显微硬度、耐磨性及疲劳强度和疲劳寿命。通过金属试样的测试发现豪克能加工后的加工面与未加工面有明显区别,加工后的表面粗糙度有明显提高,豪克能加工后工件表面粗糙度由ra值0.8提高至ra值0.15(保证加工后的粗糙度值在ra0.2以下)。豪克能加工后金属表面的硬度由120提升至160(维氏硬度hv0.2)。粗糙度的降低可以有效降低轴径向位移,轴表面性能的提升可以延长轴使用寿命,产品质量稳定性也得以提升。
43.步骤6,在转子的护环固定键槽上安装落轴式护环,转子端环6及转子铁芯3的外圆进行车加工;加工转子的轴承档1及内外密封档后,清理轴上护环固定键槽,安装护环固定键,考虑热变形因素护环与轴之间留有一定的间隙,护环安装后需要检查键与护环的间隙符合要求,安装落轴式护环,对转子端环6及转子铁芯3的外圆转进行车加工,其具体过程如下:
44.转子端环6及转子铁芯3外圆留有加工余量,需要车加工转子端环6及转子铁芯3外圆,车加工时要加持轴伸档8,车床卡爪下垫铜片防止卡爪夹伤轴伸档8,按照图纸要求尺寸加工转子端环6及转子铁芯3外圆;车加工转子端环5及外圆可以降低相关部件偏心引起的不平衡量,降低动平衡的难度,增加转子稳定性并降低电机的振动。转子外圆加工后可以更好地保证气隙的均匀度,提高转子运转的稳定性,降低转子轴径向位移。
45.步骤7,转子的动平衡调试;转子端环6及转子铁芯3的外圆转进行车加工后,在转子上安装动平衡连接器,进行全速转子动平衡调试;一般来讲转子在低速下平衡就可以保证电机转轴旋转平稳,电机振动在较小的水平,但是现在机器设计日趋向高速化发展,比如压缩机用高速电机工作转速超过一阶临界转速,转子在工作转速下运行时除了不平衡产生的离心力还有转子挠曲变形产生的反力,这类转子需要在高速平衡机上通过多平面影响系数法或振型平衡法进行平衡,使转子在工作转速下旋转平稳,转子振动最小,进而控制轴径向位移在较低水平;具体过程为转子上安装动平衡连接器,转子使用高速动平衡机进行额定转速动平衡。按照国际标准化组织颁布的相关要求该类型电机转子动平衡精度等级为g2.5,但根据实际工作经验,该类转子采用双面平衡,单面剩余不平衡量按照10g以内控制振动才能达到理想的设计和使用要求。对于刚性转子可以在低速时平衡,高速时检查剩余不平衡量在要求范围即可。对于挠性转子需要通过伯德图判定一阶临界转速,一阶临界转速时速度位移值需要控制在1.5μm范围内。
46.步骤8,调试定子套装同心度;电机气隙均匀度越高,转子旋转时就越平稳,轴径向位移就越小,根据经验,保证定子套装后的同心度≤0.2mm。电机气隙不均匀时电机振动、噪音会变大,严重时还可能造成轴承过早失效。改善气隙的均匀度,降低单边磁拉力,有助于改善转子运行的平稳性,降低电机轴径向位移,降低电机振动。
47.为了达到上述目的,转子与定子套装前(定子、机座和电机外壳组装为一体),在零部件加工方面将加工公差带收紧,机座和定子铁芯理论配合间隙在0-0.15mm,可以按照上述数值选择合理的公差配合。机座、定子铁芯加工后必须在翻转机、木质或是橡胶等软表面平台上翻身,减小翻身冲击力造成的工件变形。电机装配前需要检查定子套装同心度,如果定子同心度超过0.2mm可以通过车加工定子内圆或是调整定子与机座配合间隙的方式处理;定子机座加工、吊运过程需要特别关注防变形措施,通过零部件质量控制水平的提高改善电机气隙的均匀度。
48.步骤9,转子与定子套装的装配;根据转子的重量及轴径选择穿装转子的方式及起吊位置,穿入定子套装;根据多年经验摸索,起吊方式及起吊位置不合适有可能造成轴形位公差变化,增加轴跳动量。当电机重量较轻时,电机轴中心高≤630mm时可以选择使用单臂吊11穿装转子,起吊位置选择轴承档1和配合档2之间的空档处,如附图4所示起吊位置;当转子较重时,电机轴中心高≥710mm,须使用穿装管13抬的方式穿装转子,转子穿装时根据轴径大小选择合适的铜套筒12,套筒直径与轴径差≤10mm,转子两端需要使用5mm橡皮垫14包裹,起吊位置选择两个轴承档1的位置,穿装管13与起吊点的间隙需要符合要求,减小起吊造成的轴变形。
49.步骤10,转子与定子穿装结束后,先将滑动轴承16的下轴承座与端盖15装配在一起,然后安装端盖15,端盖15安装到位后再安装滑动轴承16,拧紧滑动轴承16的上轴承座;其具体过程如下:将滑动轴承16的下轴承座与端盖15装配在一起,检查下轴承座下方与端盖之间的间隙小于0.03mm,如果不满足要求需要检查处理。滑动轴承16上下瓦需要根据轴表面的实际状态配研并修正轴瓦接触角,着色剂使用红丹粉,对于转速大于2500r/min电机要求研瓦后接触角平分线向两侧各30~35
°
范围内,接触面积应达到75%以上,并在轴承档轴向全长范围内接触。转速小于2500r/min电机要求接触角平分线向两侧各35~45
°
范围内有较均匀接触,轴承档轴向全长范围内接触且连续不间断,若不符合上述要求需要刮瓦。上述处理结束后,拆分端盖15和滑动轴承16,安装端盖15安装到定子上,端盖15安装到位后再安装滑动轴承16安装到端盖15上,滑动轴承16安装后上轴承座不要把紧,用行车盘转子5~6圈,滑动轴承16自找正后再拧紧上轴承座,电机装配结束。
50.滑动轴承16装配时需要配研及修正接触角。因滑动轴承16加工设备精度及轴承档1表面实际工作状态的影响,轴承与轴的实际接触面往往达不到应用要求,这就要求轴承装配时需要配研及修正接触角,达到电机运行时轴瓦与轴的良好接触,改善润滑条件提高轴运行的稳定性,降低轴径向位移。