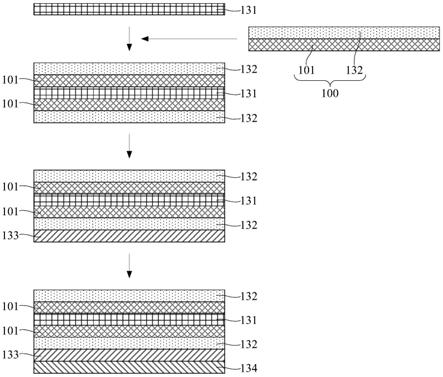
1.本技术涉及电子设备的技术领域,具体是涉及电子设备、壳体及其制作方法。
背景技术:2.随着电子装置的不断普及,电子装置已经成为人们日常生活中不可或缺的社交、娱乐工具,人们对于电子装置的要求也越来越高。以手机这类电子设备为例,用户也愈发关注手机的壳体(俗称“电池盖”或者“后盖”)的外观所带来的视觉体验。
技术实现要素:3.本技术实施例提供了一种壳体的制作方法,制作方法包括:对玻纤预浸料进行半固化处理;在玻纤预浸料的正面和反面分别贴设一纹理膜片;对玻纤预浸料和纹理膜片进行固化处理。
4.本技术实施例还提供了一种壳体,壳体由上述实施例所述的制作方法制得。
5.本技术实施例又提供了一种电子设备,电子设备包括显示模组和上述实施例所述的壳体,壳体与显示模组连接。
6.本技术的有益效果是:相较于相关技术中壳体的成型与纹理层的形成需要两个不同的工序,壳体的两侧形成纹理层也需要两个不同的工序,本技术提供的制作方法在同一工序中即可实现壳体的成型,并同时在壳体的正反两面分别形成一纹理层,极大地简化了壳体及其上纹理层的制作工序,提高生产效率,降低生产成本。
附图说明
7.为了更清楚地说明本技术实施例中的技术方案,下面将对实施例描述中所需要使用的附图作简单地介绍,显而易见地,下面描述中的附图仅仅是本技术的一些实施例,对于本领域普通技术人员来讲,在不付出创造性劳动的前提下,还可以根据这些附图获得其他的附图。
8.图1是本技术提供的电子设备一实施例的拆解结构示意图;
9.图2是本技术提供的壳体的制作方法一实施例的流程示意图;
10.图3是本技术提供的壳体在制作过程中不同工序所对应的结构示意图;
11.图4是本技术提供的壳体在制作过程中不同工序所对应的结构示意图;
12.图5是本技术提供的壳体在制作过程中不同工序所对应的结构示意图;
13.图6是本技术提供的成型模具一实施例的结构示意图;
14.图7是本技术提供的壳体在制作过程中不同工序所对应的结构示意图。
具体实施方式
15.下面结合附图和实施例,对本技术作进一步的详细描述。特别指出的是,以下实施例仅用于说明本技术,但不对本技术的范围进行限定。同样的,以下实施例仅为本技术的部
分实施例而非全部实施例,本领域普通技术人员在没有做出创造性劳动前提下所获得的所有其他实施例,都属于本技术保护的范围。
16.本技术中提及“实施例”意味着,结合实施例描述的特定特征、结构或特性可以包含在本技术的至少一个实施例中。本领域技术人员显式地和隐式地理解的是,本技术所描述的实施例可以与其他实施例相结合。
17.参阅图1,图1是本技术提供的电子设备一实施例的拆解结构示意图。
18.本技术中,电子设备10可以是手机、平板电脑、智能手表等便携装置。其中,本实施例以电子设备10为手机为例进行示例性的说明。
19.结合图1,电子设备10可以包括显示模组11、中框12和壳体13。其中,显示模组11和壳体13分别位于中框12相背的两侧,并可以通过胶接、卡接、焊接等组装方式中的一种或其组合与中框12装配连接,以使得三者组装之后形成显示模组11与壳体13一同夹持中框12的基本结构。进一步地,显示模组11与壳体13之间还可以形成一具有一定容积的腔体,该腔体可以用于设置摄像头模组14、主板15、电池16等结构件,以使得电子设备10能够实现相应的功能。其中,显示模组11、摄像头模组14等结构件可以通过柔性电路板(flexible printed circuit,fpc)分别与主板15、电池16等电性连接,以使得它们能够得到电池16的电能供应,并能够在主板15的控制下执行相应的指令。
20.进一步地,显示模组11的边缘可以朝向中框12弯曲,以使得显示模组11上显示的画面能够以类似于“瀑布”的形态从显示模组11的正面延伸至其侧面。如此设置,不仅能够减小甚至是隐藏显示模组11的黑边,以使得电子设备10能够为用户提供更大的显示视野,还能够使得显示模组11营造一种环绕显示的视觉效果,从而使得电子设备10给用户带来一种不同于刘海屏、水滴屏、挖孔屏、升降式摄像头、滑盖式摄像头等平板式全面屏的视觉体验,进而增加电子设备10的竞争力。相应地,壳体13的边缘也可以朝向中框12弯曲,以便于改善电子设备10的握持手感及外观美感。
21.下面,就壳体13的制作方法及其所制得的产品形态进行示例性的说明。
22.参阅图2,图2是本技术提供的壳体的制作方法一实施例的流程示意图。需要说明的是:为了便于描述,下文将以特定的顺序来描述某一壳体的制作步骤;但是,该壳体也可以按照不同顺序的步骤来制作,还可以增加额外的步骤或者减少(合并)某些步骤。
23.步骤s101:对玻纤预浸料进行半固化处理。
24.作为示例性地,壳体13中壳体基体131的材质可以为玻纤,其他诸如纹理层132、光学镀膜层133及盖底层134等膜层可以形成在壳体基体131上。其中,壳体基体131主要是用于满足壳体13的强度/硬度的结构需求,以抵抗外界的冲击;其他膜层主要是用于满足壳体13的绚丽多彩的外观需求。因此,壳体13应用于电子设备10时,其他膜层可以主要是位于壳体基体131朝向电子设备10内部的一侧,以免被刮掉。
25.一般地,玻纤可以具有预浸料、半固化料、固化料三种形态,本技术所述的制作方法将会充分利用玻纤的不同形态所对应的不同特性。具体而言,
26.预浸料:以玻璃纤维编织布为主体,通过浸润的方式在玻璃纤维编织布的内部填充树脂,进而形成具有一定厚度的单层料。其中,玻璃纤维编织布的形式可以有单向纤维布、方格布、斜纹布及多轴向布等,以满足玻纤的强度需求;树脂可以为环氧树脂、酚醛树脂,或者环氧树脂和酚醛树脂的混合物,以满足玻纤的定向、黏结需求。进一步地,玻璃纤维
编织布与树脂的质量比可以为40
‑
60%:40
‑
60%。值得注意是:为了使得诸如纹理层132、光学镀膜层133及盖底层134等膜层得以显现,壳体基体131的透光率可以大于或者等于80%;相应地,树脂可以优选透明料。
27.半固化料:预浸好的料(也即预浸料)通过低温(例如40℃
‑
80℃)固化,形成具有一定强度的单层板材料。此时,半固化料的结构强度还比较低,基本上是用于维持固体的基本状态,也相应地比较软,便于存储和运输。一般地,半固化料最薄可做到0.04mm,常用厚度为0.06mm。
28.固化料:半固化料经过高温(例如90℃
‑
180℃)并借助成型模具,形成特定的形状。此时,固化料具有良好的结构强度,可以满足相应的使用需求。
29.基于上述的相关描述,本技术所述的玻纤预浸料即为玻纤的预浸料。因此,对玻纤预浸料进行半固化处理可以指对玻纤的预浸料进行低温(例如40℃
‑
80℃)处理,使之形成具有一定强度的单层板材料。其中,玻纤预浸料可以多层层叠设置,使之进行半固化处理之后的厚度可以介于0.18mm与0.55mm之间,以使得最终制得的壳体13能够兼顾轻薄化与结构强度。例如:半固化料的厚度为0.3mm,玻纤预浸料采用4层;再例如:半固化料的厚度为0.4mm,玻纤预浸料采用5层。当然,在其他一些实施例中,半固化料也可以仅为一层,但一层半固化料的厚度即可为0.3mm或者0.4mm。
30.需要说明的是:基于壳体13的形状、大小等结构参数,玻纤预浸料可以在半固化处理之前或者半固化处理之后进行裁剪,并可以留有一定的余量。
31.步骤s102:在玻纤预浸料的正面和反面分别贴设一纹理膜片。
32.作为示例性地,玻纤预浸料半固化处理之后即可形成具有一定厚度、一定强度的半固化料。例如,半固化料的厚度为0.3mm或者0.4mm。此时,半固化料的正面和反面可以分别贴设以纹理膜片100,也即是两层纹理膜片100夹持玻纤的“三明治”叠层结构,以为后续的工序做好准备。其中,玻纤预浸料可以通过其自身树脂的黏性与纹理膜片100贴合,也可以借助额外的uv胶、oca胶等贴合胶与纹理膜片100贴合。
33.在一些实施例中,结合图3,图3是本技术提供的壳体在制作过程中不同工序所对应的结构示意图,纹理膜片100可以包括基材101以及形成在基材101上的纹理层132。其中,基材101可以为具有一定柔韧性的高分子材料制成的薄膜,具体的材质可以为聚对苯二甲酸乙二醇酯(polyethylene terephthalate,pet)、聚氯乙烯(polyvinyl chloride,pvc)、热塑性聚氨酯弹性体橡胶(thermoplastic polyurethanes,tpu)等,在此不作限制。基材101的厚度可以选择20μm、30μm、50μm、80μm、125μm等常用规格;经验证,保证后续涂布固化胶的情况下,基材101的厚度优选为50μm。纹理层132的材质可以为紫外光(ultraviolet,uv)固化胶,并可以通过转印工艺形成特定的纹理,以使得壳体13的外观更丰富。一般地,若纹理层132太薄,则所呈现出的纹理效果较差,而若纹理层132太厚,则会使纹理层132较脆,导致附着力较差。因此,纹理层132的厚度可以介于5μm与20μm之间,例如5μm、10μm、15μm、20μm等,具体可根据实际需求选择优选。此时,基材101可以与玻纤预浸料(也即壳体基体131)贴合。换言之,纹理层132相较于基材101更背离壳体基体131。当然,在其他一些实施例中,也可以是纹理层132与玻纤预浸料贴合。进一步地,本实施例中,基材101可以作为最终制得的壳体13的一部分而保留下来。
34.在其他一些实施例中,结合图4,图4是本技术提供的壳体在制作过程中不同工序
所对应的结构示意图,纹理膜片100可以包括基材101以及依次形成在基材101上的离型层102和纹理层132。其中,离型层102可以为石蜡类、聚乙烯类、有机硅类、酚类离型剂,以允许纹理层132与基材101分离。此时,纹理层132可以与玻纤预浸料(也即壳体基体131)贴合。换言之,纹理层132相较于基材101更靠近壳体基体131。进一步地,本实施例中,基材101可以仅用于承载纹理层132,并可以在壳体13的制作过程中被去除,例如步骤s103之后撕掉基材101,也即壳体13不具有基材101。当然,离型层102也会在壳体13的制作过程中被去除,例如撕掉基材101之后进一步清洗离型层102,以便于进行后续的工序。
35.在其他另一些实施例中,结合图5,图5是本技术提供的壳体在制作过程中不同工序所对应的结构示意图,壳体基体131的正面可以为图4所示的纹理膜片,反面可以为图3所示的纹理膜片。具体而言,壳体基体131的正面可以为纹理层132与玻纤预浸料贴合,基材101会被去除;壳体基体131的反面可以为基材101与玻纤预浸料贴合,纹理层132相较于基材101更背离壳体基体131。
36.需要说明的是:本技术所述的正面为壳体13背离显示模组11的一面,也即外表面;本技术所述的反面为壳体13朝向显示模组11的一面,也即内表面。进一步地,纹理膜片100可以单独加工,也可以采购。
37.步骤s103:对玻纤预浸料和纹理膜片进行固化处理。
38.作为示例性地,步骤s102所得的“三明治”叠层结构可以放到成型模具200内。其中,结合图6,图6是本技术提供的成型模具一实施例的结构示意图,成型模具200可以包括凹模201和凸模202,凸模202与凹模201合模之后形成一型腔203(也即是“三明治”叠层结构所在的空间区域)。如此,先将玻纤预浸料和纹理膜片置于凹模201内,再将凸模202与凹模201合模。其中,凹模201可以具有定位结构。此时,由于玻纤仍处于半固化状态,“三明治”叠层结构可以随型腔203的空间形态而变形。因此,可以在成型模具200内对玻纤预浸料和纹理膜片进行高温高压处理,玻纤预浸料中的树脂随即进一步固化,进而使得“三明治”叠层结构固化成型。其中,固化温度可以介于80℃与160℃之间,优选地介于100℃与110℃之间;固化压力可以为30mpa,保压时长可以介于5min与14min之间。
39.进一步地,壳体13的形态可以取决于成型模具200的型腔203。因此,结合图6,玻纤预浸料和纹理膜片在凸模202与凹模201合模之后可以部分位于凸模202的侧面,进而使得壳体13的形态呈2.5d或者3d。其中,凸模202与凹模201合模时可以先压住“三明治”叠层结构的边缘(俗称“压边”),以便于“三明治”叠层结构发生形变,压边则可以固化成型之后通过诸如cnc工艺去除。如此,壳体13的基本结构(例如三明治”叠层结构)、基本形态(例如2.5d或者3d)可以在同一工序中一次性形成,进而实现3d的正反纹理效果,增加壳体13的外观品质。当然,在其他一些实施例中,壳体13的基本形态也可以为平板状,而非诸如2.5d或者3d的弯曲状。
40.相关技术中,壳体的基本形态也可以为2.5d或者3d,其壳体基体的材质可以为复合板材(pc+pmma)或者玻璃。对于纹理层而言,相应的加工工艺一般可以分为如下两种:
41.第一种,复合板材(pc+pmma)多纹理加工工艺:复合板pc侧做转印纹理
→
光学镀膜
→
盖黑底油墨
→
高压成型
→
复合板pmma侧转印纹理。该加工工艺是先做一侧的纹理和效果,再在高压成型的2.5d或者3d结构上做另一侧的纹理,比较复杂。此时,壳体的总厚度一般为0.55mm。
42.第二种,玻璃多纹理加工工艺:玻璃热弯成型
→
正反面抛光
→
正面蚀刻纹理
→
背面贴合带纹理的膜片,膜片带纹理加工是单独在pet材上做转印纹理、光学镀膜和盖底。该加工工艺需要蚀刻纹理,也很复杂。此时,壳体的总厚度一般为0.6mm。
43.基于上述的相关描述,本技术利用玻纤的特性,以在同一工序中实现壳体(也即固化的玻纤预浸料)的成型,并同时在壳体的正反两面分别形成一纹理层。相较于相关技术中壳体的成型与纹理层的形成需要两个不同的工序,壳体的两侧形成纹理层也需要两个不同的工序,本技术提供的制作方法可以极大地简化壳体及其上纹理层的制作工序,提高生产效率,降低生产成本。
44.进一步地,结合图3至图5,步骤s103之后还可以在玻纤预浸料反面的纹理膜片(也即壳体13的内表面)上依次形成光学镀膜层133及盖底层134等膜层,以使得壳体13可以具有更加绚丽的外观品质。其中,对于图3至图5所示的壳体13而言,光学镀膜层133及盖底层134可以依次形成在纹理层132上。
45.光学镀膜层133可以包括氧化锆、氧化钛和氧化硅中的至少一者,并可以通过真空镀膜工艺成膜,使之具有高反射率,进而呈现高颜色叠加的外观效果。其中,光学镀膜层133与纹理层132配合,还可以使得纹理的反射效果更加绚丽,有利于增加视觉层次感。
46.在真空镀膜这一技术领域,一般根据膜厚对镀膜种类分为两类:膜厚大于200nm的可称为厚镀膜,膜厚小于200nm的可称为薄镀膜。其中,镀膜的反光色相依据膜层厚度可以有反光带蓝色、金黄色、粉红色等色相。值得注意的是:相较于薄镀膜,厚镀膜的反射波段宽、反射率高,视觉表现更炫更亮;但膜厚超过450nm后,由于镀膜应力和电子枪设备能力限制,膜层在测试过程中易失效,发生膜层脱落、开裂或uv老化变色等不良,限制了外观效果的进一步提升。
47.作为示例性地,在氧气氛围下,通过真空镀膜工艺在“三明治”叠层结构反面的纹理膜片100上沉积锆、钛、硅,以分别形成氧化锆、氧化钛和氧化硅的膜层,进而堆叠形成光学镀膜层133。基于上述的相关描述,光学镀膜层133既可以为薄镀膜,也可以为厚镀膜。由于光学镀膜层133在步骤s103之后形成,使之可以优选厚镀膜。基于此,光学镀膜层133可以由氧化锆打底,氧化钛和氧化硅以多层叠加组合的方式形成在氧化锆上。其中,光学镀膜层133的厚度可以介于200nm与450nm之间,例如200nm、300nm、450nm等,具体可根据实际需求选择;反射率可以为60%
‑
75%,例如60%、65%、70%、75%等,具体可根据实际需求选择优选。
48.盖底层134的材质可以为油墨,并可以通过丝印工艺形成在光学镀膜层133上,以衬托光学镀膜层133的颜色,并保护光学镀膜层133,以及满足壳体13的防火需求。具体而言,盖底层134可以包括主体颜色层和防火油墨层,前者一般为白色油墨或者黑色油墨,黑色主要是用于反射出光学镀膜层133的颜色,白色主要是用于显现出光学镀膜层133的透射颜色;后者一般为灰色油墨,并可以在其中加入防火填料,例如丙烯酸/异氰酸酯配成的聚氨酯固化体系,以改善壳体13的防火性能。其中,盖底层134的厚度可以介于5μm与20μm之间,例如5μm、10μm、15μm、20μm等,具体可根据实际需求选择优选;为了达到更好的阻燃和遮盖效果,一般需要丝印2
‑
3道防火油墨层。
49.作为示例性地,通过丝印工艺先在光学镀膜层133上形成主体颜色层,例如白色油墨或者黑色油墨;再在前述主体颜色层上形成防火油墨层,例如灰色油墨中加入防火填料,
前述防火填料可以为丙烯酸/异氰酸酯配成的聚氨酯固化体系,进而得到盖底层134。
50.结合图7,图7是本技术提供的壳体在制作过程中不同工序所对应的结构示意图,上述纹理层132、光学镀膜层133及盖底层134可以依次形成在基材101上,进而制得一光学膜片300,该光学膜片300再贴合在玻纤预浸料反面的纹理膜片(也即壳体13的内表面)上。
51.需要说明的是:对于壳体13内表面的纹理层132、光学镀膜层133而言,还可以根据实际的外观需求依次交替设置,例如纹理层132、光学镀膜层133、纹理层132、光学镀膜层133及盖底层134这种层叠结构。
52.基于上述的详细描述,本技术所述的制作方法所制得的壳体可以具有如下层叠结构:壳体反面实现单层纹理、单层光学镀膜、双层纹理、双层光学镀膜或其组合,壳体正面实现单层纹理。其中,相较于相关技术中复合板材壳体的总厚度为0.55mm和玻璃壳体的总厚度为0.6mm,本技术中技术方案“双层纹理+单层光学镀膜”即可实现类似的层叠结构,且壳体的总厚度可以更薄,即0.3mm壳体本体(固化后的玻纤预浸料)+10μm正面纹理层+10μm反面纹理层+200nm光学镀膜层+10μm盖底层=0.3302μm。不仅如此,玻纤的密度一般为1.9g/cm3,复合板材的密度一般为1.2g/cm3,玻璃的密度一般为2.5g/cm3,本技术提供的壳体在减薄的同时还有利于减轻重量,进而实现壳体的轻薄化设计。
53.以上所述仅为本技术的部分实施例,并非因此限制本技术的保护范围,凡是利用本技术说明书及附图内容所作的等效装置或等效流程变换,或直接或间接运用在其他相关的技术领域,均同理包括在本技术的专利保护范围内。