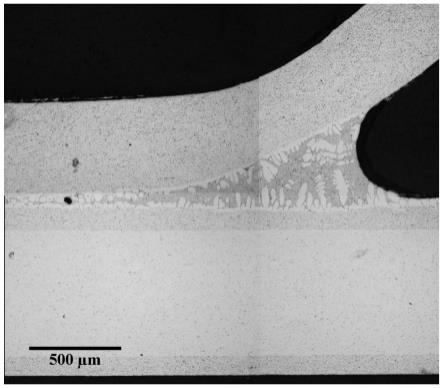
1.本发明涉及铝合金复合板技术领域,尤其涉及一种铝合金复合板材。
背景技术:2.铝合金具有高强质比、耐腐蚀性好,传热系数高和易于加工等优异性能,广泛应用于热传输领域。市场上的热交换器材料广泛采用3系铝合金,由于mn在铝合中具有较好的弥散强化作用和固溶强化作用,使得钎焊工件在高温条件下不易变形,其钎焊后屈服强度一般在40-55mpa,热导率在154-170w/m
·
k,常常作为热交换器用钎焊铝合金使用,最典型的代表是aa3003铝合金。
3.但是随着交通运输行业逐渐加快绿色低碳科技革命,更多的新能源车量融入到普通民众的生活中,而每辆新能源汽车中所需的换热器为传统汽车的两倍,这就促使新能源车辆中的热交换器朝着轻量化,为实现轻量减薄,需要提高材料的强度(屈服强度要求≥80mpa),新能源汽车以电池为动力,电池包工作时会产生大量的热能,因此,对材料还有高导热率的要求(导热率大于170w/m
·
k)、长寿命等方向发展。
4.由此可见,传统交换器用钎焊铝合金3系在强度和导热性能上已无法满足未来市场需求,开发高强度、更轻更薄、高导热的铝合金换热器材料成为了重要的研究方向。
5.在高强度改性方面,例如专利cn106827712a和cn101443188a中,往3系合金中添加高于0.6wt%cu,高于0.6wt%si,把mn的添加量上限提高到1.6wt%-1.9wt%,甚至添加低于0.2wt%的mg元素,相较于传统的3系铝合金,在钎焊后的屈服强度最高可达104mpa。然而我们发现体系中含有大量mn元素会导致钎焊后的热导率会显著降低,无法兼顾高强、高导热的综合性能目标。
6.传统热交换器领域,往往采用自然时效的方法来提高材料的力学性能,而钎焊后只进行自然时效的方式,或者欠时效方式时,合金中的强化相只会处于原子团簇或gp区阶段,导致电子散射显著,6系材料的热导率会降低17-25%,而且强度提升有限,所以综合性能没有3系合金中添加si、mn性能的好,钎焊领域中通常不使用6系铝合金芯层的热交换器。
7.而传统的铝合金材料,为了提高热导率,往往在铝基体中添加稀有金属元素或者纳米结构材料。cn108866396a向合金中加入纳米级al3bc晶种合金,以提高4系铝合金的导热率。cn112176232a向6系铝合金中加入mo、nb、ce、pr、yb元素,通过多元素的协同作用进而提高了高导热铝合金的屈服强度、拉伸强度。但是特殊的纳米晶种和稀有金属元素价格昂贵且不利于铝合金的回收再利用。
8.因此,开发一种钎焊后具有高强、高导热率铝合金复合材料已成为当前热交换器制造领域的发展方向。
技术实现要素:9.鉴于现有技术中存在的问题,本发明提供一种铝合金复合板材,即提供一种钎焊铝合金复合板材,在提高铝合金复合材料钎焊后力学性能的同时,使其具有优良热导率。
10.为达此目的,本发明采用以下技术方案:
11.本发明提供一种铝合金复合板材,所述铝合金复合板材依次包括外侧阻挡层、芯层、中间阻挡层和皮层;所述芯层的材料为6系铝合金,所述6系铝合金中含有si和mg元素的质量百分比至少形成理论值0.49wt%的mg2si,并且还含有0.2~0.3wt%的过量si;所述6系铝合金中含有≤0.4wt%的cu;其余为al和小于0.15wt%的不可避免杂质;所述芯层中si、mg元素基本以强化相β"和β'相的状态存在。
12.所述6系铝合金中除mg2si外还含有0.2~0.3wt%的过量si,例如可以是0.2wt%、0.21wt%、0.22wt%、0.23wt%、0.24wt%、0.25wt%、0.28wt%或0.3wt%等;所述6系铝合金中含有≤0.4wt%的cu,cu含量例如可以是0.4wt%、0.38wt%、0.35wt%、0.34wt%、0.3wt%、0.28wt%、0.25wt%或0.2wt%等;所述6系铝合金中mn≤0.6wt%;其中mn含量例如可以是0.6wt%、0.4wt%、0.32wt%、0.2wt%、0.17wt%、0.16wt%或0.1wt%等。
13.本发明提供的铝合金复合板材中si元素可以与mg元素结合,钎焊时效后可以形成基本以强化相β"和β'相的状态存在的镁硅化合物沉淀相(如图1),显著提升芯层合金的力学性能。在合金设计时,采用较少的si过剩(控制在0.2-0.3wt%)是有利于促进时效初期原子团簇数量密度的增加,而该原子团簇随着时效处理的过程,会演变为强化相β"和β'相,β"和β'相对合金强度提高的贡献远远高于原子团簇或gp区等相形态,对si含量的准确控制而使得β"和β'相的析出密度增加,进而影响合金强度。
14.所述6系铝合金中含有si和mg元素形成至少0.49wt%的mg2si是指,合金中si和mg的添加量理论上可以形成至少0.49wt%的mg2si,当mg2si理论含量过少时,亦无法形成足够多的β"和β'相,严重影响芯材合金的机械强度。
15.当合金体系中过剩si《0.2%时,不利于时效初期的原子团簇均匀细小的弥散析出,进而不利于形成充分多的强化相β"和β'相,严重影响芯材合金的机械强度;当过剩si超过0.3wt%,导致合金中形成单质si相,当单质si固溶到合金中还会导致热导率下降。应理解的是所述体系中si过剩0.2-0.3wt%,并不是意味着存在单质si的过剩,由于mg、si之间会形成化合物,其配比存在一定的关系,这种关系随着相态的变化而变化,我们在描述合金体系中mg、si含量控制时,通常以稳定相mg2si为基准,再定义mg或si相对mg2si理论值下的过剩值,因此,本技术所述的si过剩实质相对于体系中总的si含量扣除形成理论值mg2si中的si含量还剩余的si的含量。当合金中si含量在0.2wt%-0.3wt%时,峰值时效状态下,β"和β'相的数量密度多,而且并未发现合金中存在单质si,这是因为β"和β'相中的成分和结构与过时效产生的mg2si稳定相不同,β"相的化学成分比较接近mg5si6、β'相的化学成分比较接近mg9si5,导致mg:si摩尔数《2,所以需要硅过剩情况,性能较高。
16.芯层中cu元素的存在会显著降低材料的熔点,在本体系中,当cu含量》0.4wt%,就会导致合金的熔点显著降低,使得合金钎焊后容易发生过烧,进而影响材料的机械强度。
17.在6系合金中添加mn元素并不会帮助性能的提高,反而,mn元素会明显影响材料的热导率,需要严格控制mn元素的含量mn≤0.6wt%。优选地,所述6系铝合金中含有≤0.2wt%的mn元素,获得的机械性能更加。
18.优选地,所述6系铝合金中含有si和mg元素的质量百分比形成理论值达0.49~1.5wt%的mg2si。
19.当mg2si的添加量过高时,si含量较高,一方面容易导致过烧,致使性能严重下降,
另一方面,过多的mg含量,使得其需要复配更厚的阻挡层,否则将导致mg元素扩散到表面。
20.优选地,所述6系铝合金中还含有0.2~0.4wt%的cu。
21.cu元素钎焊后可以固溶到铝基体中,提高钎焊后的力学性能,并通过人工时效析出al2cu沉淀相,进一步提高时效后的性能,因此,在制备高性能铝合金时,通常会优选在芯层中添加约至少0.2wt%的cu元素。
22.优选地,所述6系铝合金中还含有0.07~0.25wt%的zr,例如可以是0.07wt%、0.1wt%、0.12wt%、0.15wt%、0.25wt%等。
23.优选zr的加入主要是为了形成al3zr弥散相,通过弥散强化进一步提高合金的力学性能,同时,al3zr相有抑制再结晶晶粒长大,使芯材合金钎焊后的晶粒组织均匀性提高,避免粗晶的出现,改善合金的成形性。此外,al3zr是弥散形式存在,对合金的导热率影响小。
24.优选地,所述外侧阻挡层和中间阻挡层的组分包括1.2~1.8wt%的mn,0.44~0.50倍mn含量的si,其余为al和不可避免杂质,其中mn含量例如可以是1.2wt%、1.25wt%、1.3wt%、1.4wt%、1.5wt%、1.6wt%、1.7wt%或1.8wt%等。si含量例如可以是mn含量的0.44倍、0.45倍、0.46倍、0.47倍、0.48倍或0.50倍等。
25.优选地,所述外侧阻挡层和中间阻挡层为材质相同的铝合金。
26.3系铝合金中,加入si可以使得铸锭在均质过程中,基体中产生大量的almnsi弥散相,固定mn元素,后期在钎焊过程中,almnsi弥散相可以有效防止mn元素回溶到基体中,进而防止3系铝合金的热导率大量降低,同时弥散相也具有强化作用。
27.由于almnsi相中的mn/si质量比为2:1;所以尽量控制硅的添加量为锰添加量的0.44~0.50,有利于合金中最大程度的形成almnsi弥散相。如果si含量低于0.44
×
wt.%mn,almnsi相析出量少,导致大量的mn固溶到铝基体中,合金的热导率下降明显;当si含量高于0.50
×
wt.%mn时,会导致si元素过剩,进而会使得多余的si元素钎焊过程中固溶在铝基体中,不利于热导率的提高。并不能一味的增加mn元素而伴随着增加si元素,否则容易导致钎焊时过烧,反而致使性能下降。
28.由于芯材中含有大量mg元素,在钎焊时会扩散到铝合金表面,mg元素会与钎剂反应,而导致钎剂失效;因此对于有钎焊需求的6系铝合金通常需要设置阻挡层,来阻挡mg元素扩散到钎焊表面。由于阻挡层合金的机械性能不如芯材合金,在相同的芯材合金下,阻挡层的复合比越大,复合材料的力学性能越差,因此期望在有效避免mg元素扩散至材料表面的情况下,减小阻挡层的厚度。
29.阻挡层合金中通过加入mn,可以提高合金钎焊后的强度,但是mn会显著降低合金的热导率。本发明通过在阻挡层中加入较大量的si形成almnsi弥散相,经实验研究,将mn元素转化为almnsi弥散相,可以减弱mn对热导率的影响。
30.优选地,所述外侧阻挡层和中间阻挡层的组分中还含有2.3~2.7wt%的zn,例如可以是2.3wt%、2.4wt%、2.5wt%、2.6wt%或2.7wt%等。
31.优选采用含zn的阻挡层,通过合理调控zn含量,使阻挡层的电化学电位与芯材合金匹配良好,可以提高复合材料的耐腐蚀性能。
32.优选地,所述铝合金复合板材中上下两侧阻挡层的厚度大于芯层中mg元素向两侧的扩散深度。
33.优选地,所述6系铝合金中含有si和mg元素形成1.21~1.5wt%的mg2si。
34.优选地,所述铝合金复合板材中间阻挡层的复合比例为7.5~12.5wt%,例如可以是7.5wt%、8wt%、8.5wt%、9wt%、9.5wt%、10wt%、11wt%或12.5wt%等。
35.优选地,所述铝合金复合板材中外侧阻挡层的复合比例为7.5~12.5wt%,例如可以是7.5wt%、8wt%、8.5wt%、9wt%、9.5wt%、10wt%、11wt%或12.5wt%等。
36.本发明中的阻挡层优选7系的无镁铝合金,既可以防止芯材中的mg扩散到铝合金的表面影响钎焊性能和焊后板材的美观性,同时又作为牺牲层合理的保护芯材合金材料。
37.优选地,所述皮层为4系铝合金。
38.优选地,所述皮层的组分中si含量为6.8~8.2wt%,例如可以是6.8wt%、6.9wt%、7.0wt%、7.2wt%、7.3wt%、7.4wt%、7.5wt%、7.8wt%、8.0wt%或8.2wt%等。
39.优选地,所述铝合金复合板材中皮层的复合比例为7.5~10wt%,例如可以是7.5wt%、7.8wt%、8.0wt%、8.5wt%、9.0wt%、9.5wt%或10.0wt%等。
40.优选地,所述铝合金复合板材的厚度为1.0~2.0mm,例如可以是1.0mm、1.2mm、1.5mm、1.8mm或2.0mm等。
41.与现有技术相比,本发明至少具有以下有益效果:
42.(1)本发明提供的铝合金复合板材使用所述6系铝合金替代传统的3系铝合金用作热交换器用铝合金复合材料的芯材,经钎焊时效后,材料的力学性能和热导率大幅提升,材料的机械性能和热导率优于传统的3系材料;
43.(2)本发明提供的铝合金复合板材钎焊时效后的屈服强度≥101mpa,抗拉强度≥170mpa,导热率高于170w/m
·
k,延伸率≥9%;
44.(3)本发明提供的铝合金复合板材的制备方法流程简单,易于工业化生产,能够得到性能优良的铝合金复合板材。
附图说明
45.图1为实施例5板材钎焊后经过170℃保温12h时效,并且达到峰值强度的沉淀相形貌图。
46.图2为对比例7材钎焊后在室温下经过两周自然时效后的析出相形貌图。
47.图3为实施例15的1mm厚板材经高温钎焊后的金相图片。
48.图4为实施例15板材制造的水冷板产品实物图。
49.图5为实施例15板材制造的水冷板产品局部钎焊后的放大图。
具体实施方式
50.下面结合附图并通过具体实施方式来进一步说明本发明的技术方案。
51.下面对本发明进一步详细说明。但下述的实例仅仅是本发明的简易例子,并不代表或限制本发明的权利保护范围,本发明的保护范围以权利要求书为准。
52.铝合金复合板材的制备
53.芯层铸锭先经均匀化处理,然后按照外侧阻挡层、芯层、中间阻挡层和皮层依次经热轧、复合热轧、冷精轧和退火处理,得到所述铝合金复合板材;
54.所述芯层铸锭、外侧阻挡层铸锭、中间阻挡层铸锭、皮层铸锭通过常规工艺获得,
在本实施例中使用半连续铸造的方式制备,浇铸铸锭的尺寸为8000*1500*330mm3;浇铸完成后对铸锭合金成分进行测定,确保合金成分在实验设定的范围内;其中,皮材为常规的aa4343合金,si含量为7.5wt%,记为a1合金;阻挡层合金成分见表1,记为b合金;芯层合金成分见表2,记为c合金;将芯层铸锭、外侧阻挡层铸锭、中间阻挡层铸锭、皮层铸锭分别按照复合比(见表3)轧制成一定厚度,轧制后芯层铸锭、外侧阻挡层铸锭、中间阻挡层铸锭、皮层铸锭的总厚度为120mm。
55.上述工艺中均匀化处理工艺、热轧、冷精轧及退火工艺均为常规的加工工艺;其中,均匀化处理工艺应选用适宜的工艺以确保合金材料不产生过烧且mg2si结晶相溶解充分,例如可以设定为均匀化处理的温度500~570℃,均匀化处理中升温速率为65~100℃/h,均匀化处理的保温时间4~6h;所述的热轧、冷精轧工艺没有特殊限制,可采用本领域技术人员熟知的任何可用于热轧、冷精轧的装置和方式,也可根据实际工艺进行调整,其工艺的调整以实现多层复合板的粘合和轧至预设目标厚度为准,所述热轧的最终厚度例如可以是10mm、7mm、5mm等,本实施例、对比例中复合板热轧的最终厚度均为6mm;所述精冷轧的最终厚度例如可以是1mm、1.5mm、2mm等,本实施例、对比例中复合板热轧的最终厚度均为1mm;所述的退火工艺应选择为能够实现铝合金芯材完全再结晶的加工工艺,例如可以设定为退火的升温速率为90~110℃/h;退火中铝合金复合板材随炉升温至360~410℃;退火的保温时间为2~3h。
56.上述步骤中各样品的具体加工条件为按照表3的条件对应于表4进行。
57.对实施例和对比例获得的样品进行钎焊处理和时效处理,具体过程为:将退火后的复合板材沿纵向切割成相应测试标准尺寸(长度为240mm,宽度为20mm),在钎焊炉中随炉升温到603℃保温10min,开炉门随炉冷却至100℃(冷却速度为40℃/min),移出复合板材在空气中冷却至室温,完成钎焊处理,在钎焊处理后的24h内,进行相应的人工时效或者自然时效。
58.测定时效后样品中芯层析出相的演变形态,具体为采用美国fei生产的tecnai型号透射电子显微镜,操作电压为200kv。芯材的透射样品在30vol.%硝酸+70vol.%甲醇的电解液中进行双喷减薄,电解液温度控制为约-30℃。观测析出相时,不同样品均在同一放大倍数下进行图片的拍摄。
59.下列表格中
“‑”
表示含量为0.01wt%以下。
60.阻挡层的合金b1~b7组成如表1所示。
61.表1
[0062][0063]
芯层的合金c1~c16组成如表2所示,其中δsi表示si的过剩量。
[0064]
表2
[0065][0066]
复合板材的具体加工条件如表3所示,其中p1~p7表示不同的工艺条件。
[0067]
表3
[0068][0069]
本发明中各实施例的铝合金复合板的组成、工艺以及性能如表4所示。
[0070]
表3、4、5中铝合金复合板a/b/c/b是指依次叠放的皮层、中间阻挡层、芯层、外侧阻挡层。
[0071]
表4
[0072][0073]
综合实施例1~20可以看出,本发明提供的铝合金复合板材性能优良,钎焊时效后的屈服强度≥101mpa,抗拉强度≥170mpa,延伸率≥9%,热导率高于170w/m
·
k,可满足热交换器用铝合金复合材料的需求。
[0074]
具体从实施例15图3的金相图片可以看出,焊角饱满无缺陷,熔蚀深度只有30μm。从实施例15制造的水冷板产品实物图4可以看出,经工业钎焊后冶金结合紧实,表面美观度好;图5则能示出其焊接性能良好。
[0075]
各对比例的铝合金复合板的组成、工艺如表5所示。
[0076]
表5
[0077][0078][0079]
1.导热性能
[0080]
在如下具体的实施方式中,使用qetrud型导热仪对钎焊后峰值时效的板材在室温中测量导热系数。
[0081]
热导率的下降,根源在于晶格的畸变对电子平均自由程的阻碍,从而降低合金的热导率,发明人分别研究了mn、si、cu固溶单质相因素以及mg2si强化相的相形态以及量对热导率的影响。
[0082]
①
芯层中mn元素对复合板热导率的影响
[0083]
实施例6(a/b1/c6/b1,p1)、实施例7(a/b1/c7/b1,p1)、实施例8(a/b1/c8/b1,p1)、实施例9(a/b1/c9/b1,p1),与对比例1(a/b1/c13/b1,p1)为一组比对实验,研究芯材中mn含量对铝合金复合板导热性的影响,其区别在于芯材中的mn含量分别为0、0.2wt%、0.4wt%、0.6wt%、0.8wt%;测得的热导率分别为192w/k
·
m、190w/k
·
m、182w/k
·
m、173w/k
·
m、162.5w/k
·
m;可见,当芯材中高于0.2wt.%的mn元素导致材料的热导率下降,当mn含量高于0.6wt.%时,热导率不符合要求。
[0084]
②
芯层中si元素对复合板热导率的影响
[0085]
实施例20(a/b1/c16/b1,p1),与对比例3(a/b1/c15/b1,p1)为一组比对实验,研究芯材层相对过剩硅δsi》0.30wt.%对铝合金复合板导热性的影响;其δsi分别为0.3wt.%和0.35wt.%,通过扫描电镜观察,当δsi为0.35wt.%时存在单质si,测定实施例20与对比例3的热导率分别为185.6w/k
·
m和165.2w/k
·
m。
[0086]
③
阻挡层中mn、si元素对复合板热导率的影响
[0087]
实施例7(a/b1/c7/b1,p1),与实施例19(a/b5/c7/b5,p1)、对比例2(a/b7/c7/b7,p1)、对比例4(a/b6/c7/b6,p1)为一组比对实验,研究阻挡层材料组分对铝合金复合板导热性的影响,所述阻挡层中均含有mn元素,其区别在于阻挡层中si/mn比分别为0.44、0.5、0.6、0;测得的热导率分别为190w/k
·
m、185.3w/k
·
m、163.2w/k
·
m、168.2w/k
·
m;这是由于当si/mn比在一定范围时,使用扫描电镜可以观察到单质si和单质mn形成almnsi相而析出,不会有大量的mn、si固溶到铝基体中,减缓了单质固溶所导致的晶格的畸变,减弱了阻挡层中引入mn元素导致的对导热性的影响,由于阻挡层较薄,通过复配合理的si元素,引入1.2~1.8wt%的mn并不会显著的影响材料的整体热导率,相比于不含mn中间层更有利于整体性能的提升。
[0088]
④
镁硅化合物对热导率的影响
[0089]
实施例5(a/b1/c5/b1,p1),与对比例7(a/b1/c5/b1,p7)为一组对比试验,研究相同组成的铝合金获得的不同mg2si相态下材料对热导率的影响;经不同的工艺处理使得实施例5的mg2si相态为β’以及β”相(图1),从图1可以发现材料的基材比较白;而对比例7的mg2si相态呈gp状态区(图2),材料的基材发暗,而且以析出相还处于gp区,不同mg2si相态的材料获得的热导率不同,实施例5中热导率为194w/k
·
m,而对比例7中热导率测得仅为161w/k
·
m。
[0090]
2.力学性能
[0091]
在如下具体的实施方式中,按照gb/t228.1-2010《金属材料拉伸试验第1部分:室温试验方法》公开的方法对复合板材(复合板材经过钎焊处理和时效处理)进行机械性能测试,测试仪器为zwick万能材料试验机,测试指标为规定屈服强度rp
0.2
、抗拉强度rm、断后延伸率a
50
。
[0092]
mg元素扩散深度,使用hitachi电子探针设备,对复合板材(复合板材经过钎焊处理和时效处理)纵截面的mg元素进行定量线扫描分析,确定板材纵截面不同位置处的mg元素含量变化,从而确定mg元素的扩散深度。
[0093]
①
mg2si相态对性能的影响
[0094]
实施例5(a/b1/c5/b1,p1),与对比例7(a/b1/c5/b1,p7)为一组对比试验,研究相同组成的铝合金获得的不同mg2si相态对材料性能的影响;经不同的工艺处理使得实施例5的mg2si相态呈为β’以及β”相(图1),从图1可以发现材料的基材比较白,而里面的析出相基本为β’以及β”相;而对比例7的mg2si相态呈gp区(图2),材料的基材发暗,而且以析出相还处于gp区状态,不同mg2si相态的材料性能不同,实施例5中屈服强度为229.6mpa、抗拉强度为258.6mpa、延伸率为11.5%;而对比例7中屈服强度为116mpa、抗拉强度为202.3mpa、延伸率为14%。
[0095]
②
芯材中mg、si元素对性能的影响
[0096]
实施例1(a/b1/c1/b1,p1)、实施例7(a/b1/c7/b1,p1)、对比例6(a/b1/c14/b1,p1)、对比例8(a/b1/c10/b1,p1)为一组比对实验,研究不同芯材成分下mg2si元素的变化,对复合板材的力学性能,实施例1、7与对比例6、8的mg2si理论值分别为0.49wt.%、1.5wt.%、1.6wt.%和0.31wt.%,mg2si过少或者过多都会导致性能的严重下降,过少的mg2si导致强化相不足,过多的mg2si导致合金发生过烧并且mg元素扩散到表面。
[0097]
实施例1(a/b1/c1/b1,p1),与对比例9(a/b1/c11/b1,p1)为一组比对实验,研究不同芯材成分下δsi含量的减少,对强度的影响,实施例1与对比例9的芯材中,δsi分别为0.2wt.%和0.1wt.%,导致对比例9中力学性能比实施例1降低,其中对比例9中的抗拉强度仅为168mpa、屈服强度仅为98mpa。
[0098]
③
芯材中cu元素对复合板机械性能的影响
[0099]
实施例7(a/b1/c7/b1,p1)与对比例5(a/b1/c12/b1,p1),芯材中cu含量为0.6,超过0.4,导致合金的熔点为582℃,合金发生过烧现象,所以对比例5力学性能和热导率均比实施例7降低,对比例5中抗拉强度仅为158.0mpa、屈服强度仅为98mpa,延伸率下降至2.5%,热导率仅为167.3w/k
·
m。
[0100]
本发明通过上述实施例来说明本发明的详细结构特征,但本发明并不局限于上述详细结构特征,即不意味着本发明必须依赖上述详细特征才能实施。所属技术领域的技术人员应该明了,对本发明的任何改进,对本发明所选用材料的等效替换以及辅助材料的增加、具体方式的选择等,均落在本发明的保护范围和公开范围之内。