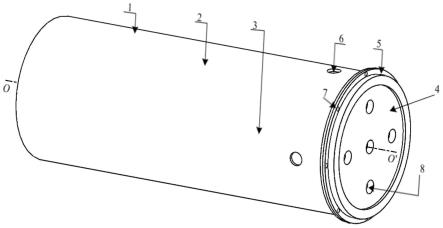
1.本发明属于一种破片威力测试装置及方法,特别涉及一种活性破片撞击侵彻及释能的综合毁伤威力测试装置及测试方法,更具体地,是涉及一种在密闭空间内利用金属开坑和结构变形性能对活性破片综合毁伤能力进行测试的装置及利用该装置对毁伤能力进行测试的方法。
技术背景
2.活性破片是一种含能的毁伤元,它突破了传统弹药破片(自然金属破片)仅靠动能进行毁伤的威力限制,是一种以动能侵彻为基础,并通过撞击引发反应并释放化学能的反应性亚稳态材料破片。活性破片在与目标撞击时,发生动能侵彻的同时,还通过一定速度的化学反应释放出能量,产生爆炸效果,对目标内部或后部进行更大程度破坏。活性材料的动态能量释放特性直接影响到其撞击反应和终点毁伤等性能,所以对其整体能量释放特性的表征及评估对于活性材料配方设计、毁伤效应和性能评估等方面具有重要意义。
3.传统的能量释放威力测试方法是在静态条件下起爆炸药后进行,而活性材料的能量释放威力高度依赖于撞击过程,因此2005年美国nswc的ames发明了一种冲击作用下活性材料动态能量释放特性的实验测量方法(ventedchambercalorimetry,vcc),即直接弹道实验,至今大部分研究活性材料释能特性的测试手段都是基于直接弹道实验,实验方法为在一个初始密封且一侧端盖为金属薄靶的圆柱形空腔内设置一固定的硬质砧板,活性材料弹丸以一定的速度穿透金属薄靶撞击至硬质砧板上,撞击过程后弹丸破碎成可在空气中持续燃烧的碎片群,碎片群持续反应放热使空腔内的空气温度升高,并通过压力传感器有源测量出空腔内的准静态压力值,从而分析出活性材料释放能量与该准静态压力的关系。
4.直接弹道实验可以较好地测试出活性材料反应释能参数,但活性破片作为毁伤元,其综合毁伤威力包括动能侵彻靶板时产生的开坑(或穿孔)、靶板运动、破碎反应释能等三个主要部分。直接弹道实验中由于硬质砧板是固定的,且通常使用坚硬材料制作以避免活性破片撞击后产生开坑影响对反应释能的测试,因此开坑(或穿孔)和靶板运动部分威力无法进行测试。另外,直接弹道实验中的测试,主要是依靠电学压力传感器对圆柱形容器内的空气热力学状态的变化进行测量,再分析换算得到活性材料的反应释能。由于测量是在密闭空间内进行测试,碰撞过程中产生的碎片颗粒(未反应或者反应不充分)会撞击到电学传感器敏感面上产生一定的寄生输出,导致综合毁伤威力测试结果不准确;同时反应过程中产生的振动和电磁干扰等也会对电学传感器的测量产生一定的影响,使得测量结果有偏差。
5.综上所述,若使用现有测试方法进行活性破片综合毁伤威力测试,则至少存在如下技术问题:
6.1.直接弹道实验忽略了硬质砧板的变形能和动能,导致无法准确测试出活性破片的综合毁伤威力。
7.2.直接弹道实验的电学测量系统易受空腔内环境影响,且需要进行热力学换算得
到反应释能,使得数据测量不准确、数据处理较繁琐。
8.实际上,要实现活性破片撞击侵彻及释能的综合毁伤威力的无源高精度测试,首先可以将无源测量结构设计得更加简易、可靠,提升测试系统的容错性,其次可以对活性破片的爆炸空间进行一定的约束,从而降低其动态能量的输出范围和对外热交换的能耗,提升测量系统的精度,最终通过设置可滑动式金属靶板和高灵敏度吸能构件将活性破片综合毁伤威力转变为可定量测量的不可逆吸能变形,提升测量系统灵敏度的同时既考虑了金属靶板的变形能和动能,又避免了电学测量仪器的使用,从而实现对活性破片动态释能威力的精准评价。常见的不可逆吸能变形过程包括塌陷、切削、扩径等,其中塌陷式吸能方式为冲击构件撞击材料过程中的塑性变形能耗、损伤能耗和摩擦发热能耗。
9.现有研究表明,受撞后金属靶板开坑的耗能情况可基于改进后的能量平衡模型进行表征,该能量平衡模型包括塌陷阻力功、塑性变形表面能和塑性变形体积能,虽然能量平衡模型是半经验公式,但已经广泛应用于工程问题中,可以用于金属靶板开坑所需能量的定量测量。此外,经过合理的设计,吸能构件材料的变形吸能和压缩过程中的应力也可以更加平稳控制,从而使得塌陷吸能与塌陷位移在准静态及动态加载下均有较好的线性关系,能够用于变形吸能的定量测量。
技术实现要素:10.本发明要解决的技术问题是提出一种活性破片撞击侵彻及释能的综合威力测试装置及方法,其综合威力包括活性破片动能侵彻金属靶板时产生的开坑、靶板运动、破碎反应释能等三个主要部分,解决现有活性破片释能测试方法中威力测试仅包括破片破碎后反应释能却未考虑硬质砧板的变形能和动能的局限性问题,从而能够精确测试出活性破片的综合毁伤威力,同时避免电学测量系统技术中因环境干扰导致的寄生输出以及数据处理较繁琐、布线复杂等问题。
11.本发明利用金属滑块和吸能构件将活性破片冲击碰撞释放的综合能量定量转化为金属滑块朝向活性破片侧面的凹陷变形量与吸能构件的塌陷位移量,从而实现在爆炸场活性破片释能威力的快速定量无源测试。
12.本发明测试装置由封装壳体、金属滑块、吸能构件、止位挡板、密封挡环、限位螺栓、固定螺栓组成。定义止位挡板和密封挡环所在的一端为本发明测试装置的右端,没有止位挡板和密封挡环的一端为左端。金属滑块、吸能构件、止位挡板按从左至右的顺序依次紧贴同轴嵌套于封装壳体内,金属滑块右端面紧贴吸能构件左端面,吸能构件右端面紧贴止位挡板左端面。金属滑块位于活性破片右侧,金属滑块在封装壳体内可自由滑动。密封挡环通过固定螺栓将止位挡板固定在封装壳体右侧,以防止金属滑块和吸能构件从封装壳体右端滑出。限位螺栓布置在封装壳体的外侧壁,要求位于吸能构件所处封装壳体的轴向段内,以限制吸能构件的径向位移。
13.封装壳体用于装载金属滑块、吸能构件和止位挡板,固定初始状态下的金属滑块和吸能构件。封装壳体为带一个端面的圆筒,封装壳体左端面中心o处挖有靶孔,没有右端面。封装壳体外直径d1满足0.3m《d1《0.6m,侧壁壁厚t1满足0.01m《t1《0.05m,左端面的壁厚等于t1,内直径d1满足d1=d
1-2t1,长度l1满足0.25m《l1《0.5m。封装壳体右端侧壁局部环向加厚形成加厚区域,以约束吸能构件径向位移,加厚区域侧壁的长度为满足0.01m≤
加厚区域内直径为满足加厚区域侧壁的厚度为加厚区域侧壁的厚度为因此长度为的左端侧壁厚度为t1,长度为的右端侧壁厚度为封装壳体最右端存在法兰带,法兰带通过固定螺栓与密封挡环紧密接触,用于限制密封挡环的轴向位移,使得封装壳体与密封挡环一体化,法兰带径向宽度b
12
满足1.5t1《b
12
《2.2t1,法兰带厚度t
12
满足t
12
=t1。距离封装壳体最右端为l6处,对称挖有4个直径为d6的侧孔,用于安装限位螺栓。封装壳体采用高强金属材料,要求材料满足:屈服强度σ1》100mpa,密度ρ1》1g/cm3,基本原则是在活性破片毁伤时产生的综合威力作用下不变形,即不吸收活性破片释放的能量,可以当作固壁。
14.靶孔是通孔,用于保证活性破片完整进入封装壳体内,外场测试时,活性破片以一定速度从左向右射入靶孔进入封装壳体,击中金属滑块进行毁伤。为确保活性破片毁伤区域是一个密闭环境(毁伤区域指活性破片与金属滑块左端面发生冲击碰撞释能的整个区域),所以靶孔尺寸不能太大,靶孔直径d9满足0.1d1《d9《0.2d1,若活性破片是圆柱体,靶孔直径d9还需满足d《d9《1.1d,其中d为活性破片横截面直径。基本原则是确保活性破片成功完整进入毁伤区域,并且尽量保证该区域的密闭性。
15.金属滑块是圆柱体,同轴置于封装壳体内部,用于当作靶板,承受活性破片撞击侵彻及释能所产生的综合毁伤载荷,同时可以在封装壳体内自由无摩擦滑动(金属滑块与封装壳体内壁之间的摩擦系数μ《0.05),将活性破片击中金属滑块所释放的能量转化为金属滑块自身的动能和变形能。金属滑块的直径d2满足0.7d1≤d2《d1,厚度l2满足0.05m《l2《0.10m,l2也可根据实际活性破片装药量进行调整(当装药量变大时,适当增加金属滑块的厚度l2);金属滑块的端面与封装壳体中心轴oo’垂直,活性破片发射轨迹沿着中心轴oo’朝向金属滑块左端面。金属滑块采用合金材料制成,具体要求材料满足:屈服强度σ2》200mpa,密度ρ2》2g/cm3,布氏硬度k2》300,基本原则是金属滑块在破片冲击碰撞作用下具有良好的塑性变形能力,在破片毁伤过程中不能被破片击穿。为计算受撞金属滑块的凹陷变形量,根据工程上毁伤冲击测试经验,需要事先预测活性破片的冲击毁伤范围,所以毁伤冲击测试前令金属滑块上的标点区域q为活性破片冲击毁伤金属滑块的预期毁伤区域,即为活性破片毁伤冲击测试后三维激光扫描仪测量的区域,标点区域q的直径dq满足0.3d2《dq《0.7d2,标点区域q中标点数量n2满足12≤n2≤50。金属滑块左端面与封装壳体左端面的右表面的初始距离为e2,满足0.2l1《e2《0.5l1。
16.吸能构件为圆柱型,用于将金属滑块的动能转化为金属滑块挤压自身所做的功,吸能构件的直径d3满足长度l3满足l3=l
1-t
1-e
2-l2。吸能构件采用蜂窝材料(或者任意具有线性吸能关系的吸能材料)制成,要求在综合毁伤威力作用下金属滑块对吸能构件进行挤压时,吸能构件可产生明显的塌陷变形,具体要求材料满足:屈服强度σ3《1000mpa,密度ρ3《10g/cm3。吸能构件位于金属滑块与封装壳体右端加厚区域之间,吸能构件左端面与金属滑块右端面刚性连接,吸能构件右端与加厚区域刚性连接以约束吸能构件径向位移。本发明试验过程中可以通过更换吸能构件,并通过改变吸能构件的材料和截面尺寸实现本发明对不同药量活性破片的测试。
17.止位挡板被密封挡环约束在封装壳体右端外侧,用于确保金属滑块、吸能构件限制在封装壳体右侧内部,在运输和安装时保证金属滑块和吸能构件不会从封装壳体右端滑出。止位挡板为圆形板,直径d4满足d4=d1,厚度t4满足0.9t1《t4《1.1t1。止位挡板采用硬质
合金制成,要求材料满足:屈服强度σ4》300mpa,密度ρ4》3g/cm3,基本原则是止位挡板受到综合毁伤威力作用时不产生塑性变形。在密封挡环的约束下,止位挡板左端面的四周边缘(即止位挡板左端面除去止位挡板与吸能构件的接触面剩余区域)紧贴封装壳体最右端的法兰带,止位挡板左端面中间区域紧贴吸能构件右端面。
18.止位挡板上挖有n4个泄气孔,泄气孔用于保证封装壳体中金属滑块右侧空间内的气体气压与外界气压一样,确保受压气体及时排出,避免活性破片毁伤释放的能量被金属滑块右侧空间内的受压气体做功消耗,可能导致释能威力测试结果偏低。泄气孔为圆形通孔,按照止位挡板中心o’布置1个泄气孔(令为中心泄气孔),以中心泄气孔为基点,以360
°
/(n
4-1)为基准角环向再布置n
4-1个泄气孔,泄气孔直径为d8=0.1d4,中心泄气孔与周围环向布置的泄气孔距离均为l8=6d8。可根据活性破片药量情况决定泄气孔数量n4,基本要求是止位挡板上布置的泄气孔保证破片爆炸后金属滑块右侧的受压气体能够从封装壳体内顺利排出,通常情况下泄气孔数量n4满足3≤n4≤8。描述了止位挡板和密封挡环的空间分布情况,止位挡板同轴嵌套于密封挡环的中间圆环处,止位挡板右端面紧贴于密封挡环的小圆环左端面,止位挡板左端面与密封挡环的大圆环左端面齐平。
19.密封挡环通过n5个固定螺栓固定在封装壳体右端法兰带外侧,保持左端面与法兰带右端面齐平,用于将止位挡板固定在封装壳体右端外侧,确保止位挡板不会脱离封装壳体,其中固定螺栓的数量n5需满足6≤n5≤12。密封挡环与止位挡板、封装壳体同轴排列,密封挡环为台阶式圆环,由大圆环、中间圆环和小圆环组成,大圆环外直径d
51
满足d1《d
51
《1.2d1,大圆环内直径d
51
满足d
51
=d4,以便完全套住止位挡板。小圆环外直径d
52
满足d
52
=d
51
+2b5,小圆环内直径d
52
尺寸略小于金属滑块直径,即d
52
满足0.8d2《d
52
《d2,由于中间圆环是大圆环与小圆环之间的过渡区域,所以中间圆环的外直径等于小圆环外直径d
52
,中间圆环的内直径等于大圆环内直径d
51
,大圆环和小圆环的厚度均为t5,其中t5满足0.3t1《t5《1.2t1,中间圆环的内外半径差为b5,其中b5满足b5=t5,为贴合并约束止位挡板,密封挡环轴向长度h5满足h5=t4+t5。密封挡环采用硬质合金制成,要求材料满足:屈服强度σ5》100mpa,密度ρ5》1g/cm3,基本原则是密封挡环受到综合毁伤威力作用时不产生塑性变形同时不会使止位挡板脱离封装壳体右端面。
20.限位螺栓用于限制吸能构件的径向位移,确保吸能构件始终沿着封装壳体进行轴向移动。4个限位螺栓分别穿过封装壳体抵住吸能构件,限位螺栓选用六角螺栓标准件,直径d6满足0.02l3≤d6≤0.05l3,螺栓长度螺栓中心线与止位挡板左端面距离l6(满足0.1l3≤l6≤0.3l3,限位螺栓采用硬质合金制成,要求材料满足:屈服强度σ6》100mpa,密度ρ6》1g/cm3,基本原则是限位螺栓受到综合毁伤威力作用时不产生塑性变形。
21.固定螺栓用于将止位挡板固定在封装壳体右端面,从而使得止位挡板紧贴于封装壳体右端面和吸能构件右端面。固定螺栓选用六角螺栓标准件,直径d7满足0.2(d
51-d
52
)≤d7≤0.5(d
51-d
52
),固定螺栓长度2.2t5≤l7≤3t5。固定螺栓采用硬质合金制成,要求材料满足:屈服强度σ7》200mpa,密度ρ7》1.5g/cm3,基本原则是当固定螺栓受到综合毁伤威力作用时不产生塑性变形。
22.活性破片为待测释能性能炸药,外观为圆柱体,横截面直径为d,圆柱体长度为l,密度为ρ,活性破片药量w=ρπd2l。活性破片的具体尺寸是由开展本发明测试所需的具体用药规模决定,为适应本发明装置尺寸要求,活性破片直径d需满足10mm≤d≤25mm,长度l需
满足10mm≤l≤20mm,ρ为活性破片密度,密度ρ满足2g/cm3≤ρ≤5g/cm3。活性破片材料的基本原则是保证活性破片在与金属滑块发生冲击碰撞时能够实现完全爆炸,同时活性破片不能击穿金属滑块。
23.采用本发明进行活性破片释能威力测试的方法是:
24.第一步,测试准备:将本发明测试装置与地面固定,保持测试装置整体与地面水平,将测试装置的止位挡板右端面紧贴墙壁,保持止位挡板竖直,确保金属滑块与吸能构件之间以及吸能构件与止位挡板之间均紧密接触。
25.第二步,借鉴能量平衡模型(周亮,姚英学,刘琦,基于能量平衡方法的压痕尺寸效应分析,硅酸盐学报,第35卷第11期,2007年11月第1478页-第1483页)(所谓能量平衡模型即为w
p
=a0+a1h
max
+a2a
p
+a
3vp
,其中w
p
为活性破片冲击金属滑块过程中金属滑块凹陷变形(开坑)所需的变形能,a0为测试系数误差和引起材料初始塑性变形所做的功,a1h
max
为活性破片克服其与金属滑块之间的阻力而做的功,h
max
为冲击过程中金属滑块内最大压深,a1为该阻力的相关系数;a2a
p
为金属滑块内生成新表面而需做的功,a
p
为金属滑块内发生塑性变形区域的面积,a2为该塑性变形面积的相关系数;a
3vp
为金属滑块内产生塑性变形体积而需做的功,v
p
为金属滑块内的发生塑性变形区域的体积,即为毁伤区域内凹坑体积和毁伤区域周围凸起体积之和,a3为该金属滑块材料的真实硬度值)标定测试装置中金属滑块凹陷变形所需变形能的各相关系数即a0(单位为kg
·
m2/s2)、a1(单位为kg
·
m/s2)、a2(单位为kg/s2)、a3(单位为kg
·
m-1
/s2),并借鉴霍普金森杆试验技术标定测试装置中吸能构件的能量灵敏度系数k(单位为kg
·
m/s2)。
26.第三步,利用标尺测量并记录金属滑块初始位置(即从金属滑块右端面至靶孔右端面距离)x1,利用三维激光扫描仪测量并记录毁伤冲击前金属滑块标点区域q内各标点的空间坐标集x1,其中标点区域q含有n2个标点,令测量得到的x1中第i个标点(i为任意一个标点序号,标点序号可以自由设定,1≤i≤n2)毁伤冲击前的空间坐标为x
1i
(x
1i
,y
1i
,z
1i
)。
27.第四步,毁伤冲击:通过发射装置将活性破片发射至封装壳体内,活性破片穿过靶孔冲击至金属滑块左端面,撞击侵彻及释能产生的综合威力一方面推动金属滑块,使得金属滑块压缩吸能构件,另一方面毁伤金属滑块左端面,使其标点区域q发生局部塑性变形并出现凹坑。
28.第五步,毁伤冲击结束后,利用标尺测量并记录金属滑块受冲击后位置(即从受冲击后的金属滑块右端面至靶孔右端面距离)x2,计算出固定在金属滑块上的吸能构件的压缩位移量为δx=x
2-x1;利用三维激光扫描仪测量并记录毁伤冲击后金属滑块标点区域q内各标点的空间坐标集x2,x2中第i个标点毁伤冲击后的空间坐标为x
2i
(x
2i
,y
2i
,z
2i
)。
29.第六步,对毁伤冲击前后区域q内的各标点的空间坐标集x1、x2进行数据处理,则最大压深取毁伤冲击后的金属滑块中任意相邻且不在同一条直线上的三个标点a’、b’、c’,假如三个点坐标分别是(x
2i
,y
2i
,z
2i
)、(x
2j
,y
2j
,z
2j
)、(x
2k
,y
2k
,z
2k
),则该三角形a’b’c’面积s
a'b'c'
为:
30.[0031][0032][0033][0034]
则金属滑块内发生塑性变形区域的面积a
p
即为毁伤冲击后标点区域内所有面积不重叠的三角形面积之和,即a
p
=∑s
a'b'c'
。取毁伤冲击前金属滑块中任意相邻且不在同一条直线上的三个标点a、b、c,再在取毁伤冲击后的金属滑块中任意相邻且不在同一条直线上的三个标点a’、b’、c’,将上述a、b、c、a’、b’、c’六个点相连形成一个棱台abcc’b’a’,由多面体体积的坐标计算法(韦进,三维空间任意多面体体积的一种坐标计算法,湖州师专学报,第19卷第5期,1997年5月第67页-第73页),该棱台abcc’b’a’体积为:
[0035][0036]
d(abb'a')=d(abb')+d(ab'a')
[0037]
d(aa'c'c)=d(aa'c')+d(ac'c)
[0038]
d(bcc'b')=d(bcc')+d(bc'b')
[0039]
其中d(acb)函数是求a、c、b坐标的行列式,且该行列式主序必须是a、c、b坐标的主顺序,假设a、c、b坐标分别是(x
1i
,y
1i
,z
1i
)、(x
1k
,y
1k
,z
1k
)、(x
1j
,y
1j
,z
1j
),则同理,d(a'b'c')是求a'、b'、c'坐标的行列式;d(abb'a')函数是求a、b、b'、a'坐标的行列式,一般会将d(abb'a')函数分解为两个行列式,即d(abb'a')=d(abb')+d(ab'a')=d(bb'a')+d(ba'a)=d(b'a'a)+d(b'ab)=d(a'ab)+d(a'bb')。d(aa'c'c)函数是求a、a'、c'、c坐标的行列式,d(bcc'b')是求b、c、c'、b'坐标的行列式,则金属滑块内的发生塑性变形区域的体积即为各个体积上不重叠的棱台体积之和,即v
p
=∑v
abcc'b'a'
。通过上述数据处理方式,可测得金属滑块内最大压深h
max
、金属滑块内发生塑性变形区域的面积a
p
、金属滑块内的发生塑性变形区域的体积v
p
。
[0040]
第七步,计算吸能构件的变形能e1=k
·
δx,即为金属滑块的动能;计算金属滑块的变形能e2=a0+a1h
max
+a2a
p
+a
3vp
,等于活性破片毁伤冲击金属滑块过程中金属滑块凹陷变形所需的变形能w
p
,即e2=w
p
。由于毁伤冲击时间短暂,爆炸毁伤产生的热量无法及时通过封装壳体与外界空气进行热交换,所以可将活性破片毁伤区域视为绝热环境,整个毁伤区域系统内的能量全部用于对金属滑块进行做功w,其中w为金属滑块的动能和变形能e2之和,并且金属滑块的动能最终转化为吸能构件的变形能e1,能量等式为w=e1+e2,从而实现活性破片撞击侵彻及释能的威力测试,得到的w即为活性破片毁伤释放的总能量。
[0041]
第八步,从本发明装置右端卸下止位挡板,更换新的金属滑块和吸能构件,实现本测量装置的循环使用。
[0042]
采用本发明可以达到以下技术效果:
[0043]
1.本发明通过测量金属滑块位置变化可读取吸能构件的压缩位移量δx,根据吸
能构件的能量灵敏度系数可方便得到吸能构件的变形能;再利用三维激光扫描仪测量毁伤冲击前后标点区域q内的各标点空间位置的变化,可快速计算出金属滑块内最大压深h
max
、金属滑块内发生塑性变形区域的面积a
p
、体积v
p
,再结合金属滑块能量平衡模型中各项相关系数,得到金属滑块的变形能。吸能构件的变形能和金属滑块的变形能之和即为活性破片毁伤释放的总能量,该方法完成活性破片毁伤释能的定量测量,并解决了现有活性破片释能测试方法中威力测试仅包括破片破碎后反应释能却未考虑硬质砧板的变形能和动能的局限性问题。
[0044]
2.本发明装置的吸能构件和金属滑块可选用不同材料、不同截面尺寸、不同厚度等多种规格的构型,此外可调整活性破片的装药量、活性破片的初始速度,以此实现本装置对不同强度爆炸综合威力的测试,从而适用于活性破片不同装药量、不同初速度的综合毁伤威力参数测量。
[0045]
3.本发明装置具有结构简单,布设使用方便,无需供电,结果数据处理方便,重复使用率高等特点,避免电学测量系统技术中因环境干扰导致的寄生输出以及数据处理较繁琐、布线复杂等问题。
附图说明
[0046]
图1是本发明测试装置总体结构立体示意图;
[0047]
图2是本发明测试装置结构部件空间分布示意图;
[0048]
图3是本发明测试装置总体结构透视图;
[0049]
图4是本发明测试装置中封装壳体1的轴向剖视图;
[0050]
图5是本发明测试装置中封装壳体1的结构示意图;图5(a)是本发明测试装置中封装壳体1的右视图,图5(b)是本发明测试装置中封装壳体1的立体示意图;
[0051]
图6是本发明测试装置中金属滑块2和吸能构件3的结构示意图;图6(a)是本发明测试装置中金属滑块2左视图,图6(b)是本发明装置中金属滑块2和吸能构件3的空间分布示意图;
[0052]
图7是本发明装置中止位挡板4的结构示意图;图7(a)是本发明测试装置中止位挡板4的右视图,图7(b)是本发明装置中止位挡板4和密封挡环5的空间分布示意图;
[0053]
图8是本发明测试装置中密封挡环5结构示意图;图8(a)是密封挡环5的右视图,图8(b)是密封挡环5的正视图;
[0054]
图9是本发明测试装置受活性破片撞击释能前的轴向剖视图;
[0055]
图10是本发明测试装置受活性破片撞击释能后的轴向剖视图;
[0056]
图11是本发明测试装置中金属滑块2受毁伤冲击前的任意相邻标点a、b、c以及该三个标点相连成的三角形区域abc;图11(a)是三角形区域abc在金属滑块2左视图中的位置,图11(b)是三角形区域abc在金属滑块2正视图中的位置;
[0057]
图12是本发明测试装置金属滑块2受毁伤冲击后的任意相邻标点a’、b’、c’;图12(a)是该三个相邻标点所连成的三角形区域a’b’c’;图12(b)是上述三个相邻标点a’、b’、c’和图11所示三个相邻标点a、b、c所连成的棱台区域abcc’b’a’。
具体实施方式
[0058]
如图1、图2和图3所示,本发明测试装置由封装壳体1、金属滑块2、吸能构件3、止位挡板4、密封挡环5、限位螺栓6、固定螺栓7组成。定义止位挡板4和密封挡环5所在的一端为本发明测试装置的右端,没有止位挡板4和密封挡环5的一端为左端。金属滑块2、吸能构件3、止位挡板4按从左至右的顺序依次紧贴同轴(指同中心轴oo’)嵌套于封装壳体1内,金属滑块2右端面紧贴吸能构件3左端面,吸能构件3右端面紧贴止位挡板4左端面。金属滑块2位于活性破片10右侧,金属滑块2在封装壳体1内可自由滑动。如图2、图7(b)所示,密封挡环5通过固定螺栓7将止位挡板4固定在封装壳体1右侧,以防止金属滑块2和吸能构件3从封装壳体1右端滑出。限位螺栓6布置在封装壳体1的外侧壁,要求位于吸能构件3所处封装壳体1的轴向(即沿着中心轴oo’的方向)段内,以限制吸能构件3的径向(即垂直中心轴oo’的竖直面方向)位移。
[0059]
如图1所示,结合图2,封装壳体1用于装载金属滑块2、吸能构件3和止位挡板4,固定初始状态下的金属滑块2和吸能构件3。如图4、图5所示,封装壳体1为带一个端面的圆筒,封装壳体1左端面中心o处挖有靶孔9,没有右端面。封装壳体1外直径d1满足0.3m《d1《0.6m,侧壁壁厚t1满足0.01m《t1《0.05m,左端面的壁厚等于t1,内直径d1满足d1=d
1-2t1,长度l1满足0.25m《l1《0.5m。封装壳体1右端侧壁局部环向加厚形成加厚区域11,以约束吸能构件3径向位移,加厚区域11侧壁的长度为满足加厚区域内直径为满足加厚区域11侧壁的厚度为因此长度为的左端侧壁厚度为t1,长度为的右端侧壁厚度为封装壳体1最右端存在法兰带12,法兰带12通过固定螺栓7与密封挡环5紧密接触(见图2和图3),用于限制密封挡环5的轴向位移,使得封装壳体1与密封挡环5一体化,法兰带12径向宽度b
12
满足1.5t1《b
12
《2.2t1,法兰带12厚度t
12
满足t
12
=t1。距离封装壳体1最右端为l6处,对称挖有4个直径为d6的侧孔,用于安装限位螺栓6。封装壳体1采用高强金属材料,要求材料满足:屈服强度σ1》100mpa,密度ρ1》1g/cm3,基本原则是在活性破片10毁伤时产生的综合威力作用下不变形,即不吸收活性破片10释放的能量,可以当作固壁。
[0060]
如图3所示,靶孔9是通孔,用于保证活性破片10完整进入封装壳体1内,外场测试时,活性破片10以一定速度从左向右射入靶孔9进入封装壳体1,击中金属滑块2进行毁伤。为确保活性破片10毁伤区域是一个密闭环境(毁伤区域指活性破片10与金属滑块2左端面发生冲击碰撞释能的整个区域),所以靶孔9尺寸不能太大,靶孔9直径d9满足0.1d1《d9《0.2d1,若活性破片10是圆柱体,靶孔9直径d9还需满足d《d9《1.1d,其中d为活性破片10横截面直径。基本原则是确保活性破片10成功完整进入毁伤区域,并且尽量保证该区域的密闭性。
[0061]
如图2和图3所示,金属滑块2是圆柱体,同轴置于封装壳体1内部,用于当作靶板,承受活性破片10撞击侵彻及释能所产生的综合毁伤载荷,同时可以在封装壳体1内自由无摩擦滑动(金属滑块2与封装壳体1内壁之间的摩擦系数μ《0.05),将活性破片10击中金属滑块2所释放的能量转化为金属滑块2自身的动能和变形能。如图6(a)和图6(b)所示,金属滑块2的直径d2满足0.7d1≤d2《d1,厚度l2满足0.05m《l2《0.10m,l2也可根据实际活性破片10装药量进行调整(当装药量变大时,适当增加金属滑块2的厚度l2);金属滑块2的端面与封装壳体1中心轴oo’垂直,活性破片10发射轨迹沿着中心轴oo’朝向金属滑块2左端面。金属滑
块2采用合金材料制成,具体要求材料满足:屈服强度σ2》200mpa,密度ρ2》2g/cm3,布氏硬度k2》300,基本原则是金属滑块2在破片冲击碰撞作用下具有良好的塑性变形能力,在破片毁伤过程中不能被破片击穿。为计算受撞金属滑块2的凹陷变形量,根据工程上毁伤冲击测试经验,需要事先预测活性破片10的冲击毁伤范围,所以毁伤冲击测试前令图6中金属滑块2上的标点区域q为活性破片10冲击毁伤金属滑块2的预期毁伤区域,即为活性破片10毁伤冲击测试后三维激光扫描仪测量的区域,如图6(a)所示,标点区域q的直径dq满足0.3d2《dq《0.7d2,标点区域q中标点数量n2满足12≤n2≤50。如图9所示,金属滑块2左端面与封装壳体1左端面的右表面的初始距离为e2,满足0.2l1《e2《0.5l1。
[0062]
如图2和图3所示,吸能构件3为圆柱型,用于将金属滑块2的动能转化为金属滑块2挤压自身所做的功,如图6(b)所示,吸能构件3的直径d3满足长度l3满足l3=l
1-t
1-e
2-l2。吸能构件3采用蜂窝材料(或者任意具有线性吸能关系的吸能材料)制成,要求在综合毁伤威力作用下金属滑块2对吸能构件3进行挤压时,吸能构件3可产生明显的塌陷变形,具体要求材料满足:屈服强度σ3《1000mpa,密度ρ3《10g/cm3。吸能构件3位于金属滑块2与封装壳体1右端加厚区域11之间,吸能构件3左端面与金属滑块2右端面刚性连接,吸能构件3右端与加厚区域11刚性连接以约束吸能构件3径向位移。本发明试验过程中可以通过更换吸能构件3,并通过改变吸能构件3的材料和截面尺寸实现本发明对不同药量活性破片10的测试。
[0063]
如图2和图7所示,止位挡板4被密封挡环5约束在封装壳体1右端外侧,用于确保金属滑块2、吸能构件3限制在封装壳体1右侧内部,在运输和安装时保证金属滑块2和吸能构件3不会从封装壳体1右端滑出。如图7(a)所示,止位挡板4为圆形板,直径d4满足d4=d1,厚度t4(如图7(b)所示)满足0.9t1《t4《1.1t1。止位挡板4采用硬质合金制成,要求材料满足:屈服强度σ4》300mpa,密度ρ4》3g/cm3,基本原则是止位挡板4受到综合毁伤威力作用时不产生塑性变形。如图3、图7(b)和图9所示,在密封挡环5的约束下,止位挡板4左端面的四周边缘(即止位挡板4左端面除去止位挡板4与吸能构件3的接触面剩余区域)紧贴封装壳体1最右端的法兰带12,止位挡板4左端面中间区域紧贴吸能构件3右端面。
[0064]
如图1和图7(a)所示,止位挡板4上挖有n4个泄气孔8,泄气孔8用于保证封装壳体1中金属滑块2右侧空间内的气体气压与外界气压一样,确保受压气体及时排出,避免活性破片10毁伤释放的能量被金属滑块2右侧空间内的受压气体做功消耗,可能导致释能威力测试结果偏低。泄气孔8为圆形通孔,按照止位挡板4中心o’布置1个泄气孔(令为中心泄气孔),以中心泄气孔为基点,以360
°
/(n
4-1)为基准角环向再布置n
4-1个泄气孔(图7(a)中n4=5),泄气孔8直径为d8=0.1d4,中心泄气孔与周围环向布置的泄气孔距离均为l8=6d8。可根据活性破片10药量情况决定泄气孔数量n4,基本要求是止位挡板4上布置的泄气孔8保证破片爆炸后金属滑块2右侧的受压气体能够从封装壳体1内顺利排出,通常情况下泄气孔数量n4满足3≤n4≤8。图7(b)描述了止位挡板4和密封挡环5的空间分布情况,止位挡板4同轴嵌套于密封挡环5的中间圆环53处,止位挡板4右端面紧贴于密封挡环5的小圆环52左端面,止位挡板4左端面与密封挡环5的大圆环51左端面齐平。
[0065]
如图1和图7(b)所示,密封挡环5通过n5个固定螺栓7(图7(b)中n5=8)固定在封装壳体1右端法兰带12外侧,保持左端面与法兰带12右端面齐平,用于将止位挡板4固定在封装壳体1右端外侧,确保止位挡板4不会脱离封装壳体1,其中固定螺栓7的数量n5需满足6≤
n5≤12。如图2、图7(b)和图8所示,密封挡环5与止位挡板4、封装壳体1同轴排列,如图8(b)所示,密封挡环5为台阶式圆环,由大圆环51、中间圆环53和小圆环52组成,大圆环51外直径d
51
满足d1《d
51
《1.2d1,大圆环51内直径d
51
满足d
51
=d4,以便完全套住止位挡板4。小圆环52外直径d
52
满足d
52
=d
51
+2b5,小圆环52内直径d
52
尺寸略小于金属滑块2直径,即d
52
满足0.8d2《d
52
《d2,由于中间圆环53是大圆环51与小圆环52之间的过渡区域,所以中间圆环53的外直径等于小圆环52外直径d
52
,中间圆环53的内直径等于大圆环51内直径d
51
,大圆环51和小圆环52的厚度均为t5,其中t5满足0.3t1《t5《1.2t1,中间圆环53的内外半径差为b5,其中b5满足b5=t5,为贴合并约束止位挡板4,密封挡环5轴向长度h5满足h5=t4+t5。密封挡环5采用硬质合金制成,要求材料满足:屈服强度σ5》100mpa,密度ρ5》1g/cm3,基本原则是密封挡环5受到综合毁伤威力作用时不产生塑性变形同时不会使止位挡板4脱离封装壳体1右端面。
[0066]
如图1、图4和图5所示,限位螺栓6用于限制吸能构件3的径向位移,确保吸能构件3始终沿着封装壳体1进行轴向移动。如图9所示,4个限位螺栓6分别穿过封装壳体1抵住吸能构件3,限位螺栓6选用六角螺栓标准件,直径d6满足0.02l3≤d6≤0.05l3,螺栓长度螺栓中心线与止位挡板4左端面距离l6(见图4)满足0.1l3≤l6≤0.3l3,限位螺栓6采用硬质合金制成,要求材料满足:屈服强度σ6》100mpa,密度ρ6》1g/cm3,基本原则是限位螺栓6受到综合毁伤威力作用时不产生塑性变形。
[0067]
如图1、图2和图7(b)所示,固定螺栓7用于将止位挡板4固定在封装壳体1右端面,从而使得止位挡板4紧贴于封装壳体1右端面和吸能构件3右端面。如图9所示,固定螺栓7选用六角螺栓标准件,直径d7满足0.2(d
51-d
52
)≤d7≤0.5(d
51-d
52
),固定螺栓7长度2.2t5≤l7≤3t5。固定螺栓7采用硬质合金制成,要求材料满足:屈服强度σ7》200mpa,密度ρ7》1.5g/cm3,基本原则是当固定螺栓7受到综合毁伤威力作用时不产生塑性变形。
[0068]
如图3所示,活性破片10为待测释能性能炸药,外观为圆柱体,横截面直径为d,圆柱体长度为l,密度为ρ,活性破片10药量w=ρπd2l。活性破片10的具体尺寸是由开展本发明测试所需的具体用药规模决定,为适应本发明装置尺寸要求,活性破片10直径d需满足10mm≤d≤25mm,长度l需满足10mm≤l≤20mm。活性破片10材料的基本原则是保证活性破片10在与金属滑块2发生冲击碰撞时能够实现完全爆炸,同时活性破片10不能击穿金属滑块2。
[0069]
采用本发明进行活性破片释能威力测试的方法是:
[0070]
第一步,测试准备:如图9所示,将本发明测试装置与地面固定,保持测试装置整体与地面水平,将测试装置的止位挡板4右端面紧贴墙壁,保持止位挡板4竖直,确保金属滑块2与吸能构件3之间以及吸能构件3与止位挡板4之间均紧密接触。
[0071]
第二步,借鉴能量平衡模型(周亮,姚英学,刘琦,基于能量平衡方法的压痕尺寸效应分析,硅酸盐学报,第35卷第11期,2007年11月第1478页-第1483页)(所谓能量平衡模型即为w
p
=a0+a1h
max
+a2a
p
+a
3vp
,其中w
p
为活性破片10冲击金属滑块2过程中金属滑块2凹陷变形(开坑)所需的变形能,a0为测试系数误差和引起材料初始塑性变形所做的功,a1h
max
为活性破片10克服其与金属滑块2之间的阻力而做的功,h
max
为冲击过程中金属滑块2内最大压深,a1为该阻力的相关系数;a2a
p
为金属滑块2内生成新表面而需做的功,a
p
为金属滑块2内发生塑性变形区域的面积,a2为该塑性变形面积的相关系数;a
3vp
为金属滑块2内产生塑性变形体积而需做的功,v
p
为金属滑块2内的发生塑性变形区域的体积,即为毁伤区域内凹坑体积和毁伤区域周围凸起体积之和,a3为该金属滑块2材料的真实硬度值)标定测试装置中
金属滑块2凹陷变形所需变形能的各相关系数即a0(单位为kg
·
m2/s2)、a1(单位为kg
·
m/s2)、a2(单位为kg/s2)、a3(单位为kg
·
m-1
/s2),并借鉴霍普金森杆试验技术标定测试装置中吸能构件3的能量灵敏度系数k(单位为kg
·
m/s2)。
[0072]
第三步,如图9所示,利用标尺测量并记录金属滑块2初始位置(即从金属滑块2右端面至靶孔9右端面距离)x1,利用三维激光扫描仪测量并记录毁伤冲击前金属滑块2标点区域q内各标点的空间坐标集x1,其中标点区域q含有n2个标点,令测量得到的x1中第i个标点(i为任意一个标点序号,标点序号可以自由设定,1≤i≤n2)毁伤冲击前的空间坐标为x
1i
(x
1i
,y
1i
,z
1i
)。
[0073]
第四步,毁伤冲击:如图9所示,通过发射装置将活性破片10发射至封装壳体1内,活性破片10穿过靶孔9冲击至金属滑块2左端面,撞击侵彻及释能产生的综合威力一方面推动金属滑块2,使得金属滑块2压缩吸能构件3,另一方面毁伤金属滑块2左端面,使其标点区域q发生局部塑性变形并出现凹坑。
[0074]
第五步,毁伤冲击结束后,如图10所示(图中金属滑块2’表示初始位置下的金属滑块),利用标尺测量并记录金属滑块2受冲击后位置(即从受冲击后的金属滑块2右端面至靶孔9右端面距离)x2,计算出固定在金属滑块2上的吸能构件3的压缩位移量为δx=x
2-x1;利用三维激光扫描仪测量并记录毁伤冲击后金属滑块2标点区域q内各标点的空间坐标集x2,x2中第i个标点毁伤冲击后的空间坐标为x
2i
(x
2i
,y
2i
,z
2i
)。
[0075]
第六步,对毁伤冲击前后区域q内的各标点的空间坐标集x1、x2进行数据处理,则最大压深如图12(a)所示,取毁伤冲击后的金属滑块2中任意相邻且不在同一条直线上的三个标点a’、b’、c’,假如三个点坐标分别是(x
2i
,y
2i
,z
2i
)、(x
2j
,y
2j
,z
2j
)、(x
2k
,y
2k
,z
2k
),则该三角形a’b’c’面积s
a'b'c'
为:
[0076][0077][0078][0079][0080]
则金属滑块2内发生塑性变形区域的面积a
p
即为毁伤冲击后标点区域内所有面积不重叠的三角形面积之和,即a
p
=∑s
a'b'c'
。在图11中取毁伤冲击前金属滑块2中任意相邻且不在同一条直线上的三个标点a、b、c(其中图11(a)、(b)中的虚线黑框都是指标点区域q中包括上述三个标点a、b、c的小区域),再在图12(a)中取毁伤冲击后的金属滑块2中任意相邻且不在同一条直线上的三个标点a’、b’、c’(其中图12(a)中的虚线黑框是指标点区域q中包括上述三个标点a’、b’、c’的小区域),将上述a、b、c、a’、b’、c’六个点按图12(b)所示相连形成一个棱台abcc’b’a’(其中图12(b)中的虚线黑框是指图12(a)中三个相邻标点a’、b’、c’和图11(b)中三个相邻标点a、b、c相连所形成的棱台区域abcc’b’a’),由多面体体积的坐
标计算法(韦进,三维空间任意多面体体积的一种坐标计算法,湖州师专学报,第19卷第5期,1997年5月第67页-第73页),该棱台abcc’b’a’体积为:
[0081][0082]
d(abb'a')=d(abb')+d(ab'a')
[0083]
d(aa'c'c)=d(aa'c')+d(ac'c)
[0084]
d(bcc'b')=d(bcc')+d(bc'b')
[0085]
其中d(acb)函数是求a、c、b坐标的行列式,且该行列式主序必须是a、c、b坐标的主顺序,假设a、c、b坐标分别是(x
1i
,y
1i
,z
1i
)、(x
1k
,y
1k
,z
1k
)、(x
1j
,y
1j
,z
1j
),则同理,d(a'b'c')是求a'、b'、c'坐标的行列式;d(abb'a')函数是求a、b、b'、a'坐标的行列式,一般会将d(abb'a')函数分解为两个行列式,即d(abb'a')=d(abb')+d(ab'a')=d(bb'a')+d(ba'a)=d(b'a'a)+d(b'ab)=d(a'ab)+d(a'bb')。则金属滑块2内的发生塑性变形区域的体积即为各个体积上不重叠的棱台体积之和,即v
p
=∑v
abcc'b'a'
。通过上述数据处理方式,可测得金属滑块2内最大压深h
max
、金属滑块2内发生塑性变形区域的面积a
p
、金属滑块2内的发生塑性变形区域的体积v
p
。
[0086]
第七步,计算吸能构件3的变形能e1=k
·
δx,即为金属滑块2的动能;计算金属滑块2的变形能e2=a0+a1h
max
+a2a
p
+a
3vp
,等于活性破片10毁伤冲击金属滑块2过程中金属滑块2凹陷变形所需的变形能w
p
,即e2=w
p
。由于毁伤冲击时间短暂,爆炸毁伤产生的热量无法及时通过封装壳体1与外界空气进行热交换,所以可将活性破片10毁伤区域视为绝热环境,整个毁伤区域系统内的能量全部用于对金属滑块2进行做功w,其中w为金属滑块2的动能和变形能e2之和,并且金属滑块2的动能最终转化为吸能构件3的变形能e1,能量等式为w=e1+e2,从而实现活性破片10撞击侵彻及释能的威力测试,得到的w即为活性破片毁伤释放的总能量。
[0087]
第八步,从本发明装置右端卸下止位挡板4,更换新的金属滑块2和吸能构件3,实现本测量装置的循环使用。