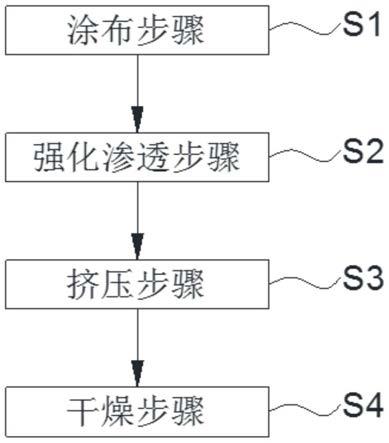
1.本发明涉及烟叶生产工艺领域,具体而言,涉及一种加热不燃烧再造烟叶的涂布方法和装置。
背景技术:2.加热不燃烧再造烟叶的生产过程是一个烟草物质的分离—重组过程,在生产过程中烟草原料通过提取分离技术分为溶剂可溶物和不可溶物两个部分,不可溶物通过制浆、抄造等工艺环节形成再造烟叶的中间产物——基片,可溶物经过精制、浓缩、调配等工艺形成另一中间产物——涂布液,将涂布液在基片上回填重组即可得到加热不燃烧再造烟叶。
3.常规涂布过程是将配置好的涂布液通过涂布上料系统送至涂布机,通过涂布辊将涂布液回填到基片中,多余的涂布液通过回收系统精制、调浓再次回到涂布上料系统,回填好的基片通过烘箱干燥即可形成再造烟叶。
4.常规涂布过程在生产加热不燃烧再造烟叶中存在以下问题:涂布液难以渗透至基片内部,而会在基片外部形成壳体,一旦吸湿再造烟叶将粘接在一起影响后续加工过程,最终产品断纸、涂布率不达标等现象时有发生。
技术实现要素:5.本发明的目的包括,例如,提供了一种加热不燃烧再造烟叶的涂布方法,其可提升涂布液对基片的渗透性避免粘黏、结块等不利于后续加工的现象发生,同时该工艺可以有效调节加热不燃烧再造烟叶的厚度改善其物理性能,提升加热不燃烧烟支的使用感受。
6.本发明的目的包括,例如,提供了一种加热不燃烧再造烟叶的涂布装置,其能够有效实现上述涂布方法,使得最终获得的加热不燃烧再造烟叶质量更佳,使用感受更佳。
7.本发明的实施例可以这样实现:
8.第一方面,实施例提供一种加热不燃烧再造烟叶的涂布方法,其包括:
9.将涂布液回填至基片上,获得烟叶半成品;
10.利用预设温度的蒸汽湿加热所述烟叶半成品;以及;
11.通过对加热后的所述烟叶半成品进行挤压以调节所述烟叶半成品的厚度。
12.在可选的实施方式中,利用涂布机构将所述涂布液回填至所述基片;
13.优选地,所述涂布机构包括相对设置且相向转动的第一涂布辊和第二涂布辊,所述第一涂布辊的硬度大于所述第二涂布辊的硬度;
14.优选地,所述第一涂布辊的硬度为20-40p&j;
15.优选地,所述第二涂布辊的硬度为120-140p&j;
16.优选地,所述涂布液的温度为55-80℃。
17.在可选的实施方式中,所述蒸汽的预设温度不低于80℃;优选为80-110℃;
18.优选地,所述蒸汽的压力为1-15bar;
19.优选地,利用蒸汽喷嘴对所述烟叶半成品进行湿加热;
20.优选地,所述蒸汽喷嘴与所述烟叶半成品之间的夹角为50
°-
70
°
;
21.优选地,所述蒸汽喷嘴与所述烟叶半成品之间的距离为30-50cm;
22.优选地,所述蒸汽喷嘴为多个且均匀分布于与所述烟叶半成品的运动方向垂直的方向上;
23.优选地,任意两个相邻的所述蒸汽喷嘴之间的间距为15-25cm;
24.优选地,在对加热后的所述烟叶半成品进行挤压之前,利用所述蒸汽喷嘴调节加热后的所述烟叶半成品的水分为15-30%。
25.在可选的实施方式中,利用压光机构对加热后的所述烟叶半成品进行挤压;
26.优选地,所述压光机构包括相对设置且相向转动第一压光辊和第二压光辊,所述第一压光辊的硬度大于所述第二压光辊的硬度;
27.优选地,所述第一压光辊的硬度为18-22p&j;
28.优选地,所述第二压光辊的硬度28-32p&j;
29.优选地,所述第一压光辊和所述第二压光辊之间的线压力为70-130kn/m。
30.在可选的实施方式中,所述加热不燃烧再造烟叶的涂布方法还包括在挤压所述烟叶半成品后进行干燥以脱除所述烟叶半成品中的水分;
31.优选地,采用烘箱组对挤压后的所述烟叶半成品进行烘干;
32.优选地,所述烘箱组包括多个依次排列的烘箱,且多个所述烘箱的温度从进料端至出料端的方向先升高后降低;
33.优选地,所述烘箱为10个,其中,靠近进料端的第一个烘箱的温度为83-87℃,风机频率为32-34%;第二个烘箱的温度为88-92℃,风机频率为29-31%;第三个烘箱的温度为98-102℃,风机频率为29-31%;第四个烘箱的温度为108-112℃,风机频率为29-31%;第五个烘箱的温度为123-127℃,风机频率为37-39%;第六个烘箱的温度为108-112℃,风机频率为37-39%;第七个烘箱的温度为98-102℃,风机频率为32-34%;第八个烘箱的温度为88-92℃,风机频率为35-36%;第九个烘箱的温度为88-92℃,风机频率为35-36%;靠近出料端的第十个烘箱的温度为88-92℃,风机频率为35-36%。
34.第二方面,实施例提供一种加热不燃烧再造烟叶的涂布装置,其用于实现如前述实施方式任一项所述的加热不燃烧再造烟叶的涂布方法,包括涂布机构、喷洒机构、压光机构以及第一传送机构;
35.所述涂布机构位于所述第一传送机构的进料端,所述压光机构位于所述第一传送机构的出料端,所述喷洒机构位于所述涂布机构和所述压光机构之间。
36.在可选的实施方式中,所述涂布机构包括相对设置且相向转动的第一涂布辊和第二涂布辊,所述第一涂布辊的硬度大于所述第二涂布辊的硬度。
37.在可选的实施方式中,所述喷洒机构包括蒸汽喷嘴。
38.在可选的实施方式中,所述压光机构包括相对设置且相向转动第一压光辊和第二压光辊,所述第一压光辊的硬度大于所述第二压光辊的硬度。
39.在可选的实施方式中,所述加热不燃烧再造烟叶的涂布装置还包括干燥机构和第二传送机构,所述压光机构位于所述第二传送机构的进料端,所述干燥机构位于所述第二传送机构的出料端;
40.优选地,所述干燥机构为烘箱组。
41.本发明实施例的有益效果包括,例如:
42.本申请实施例提供的一种加热不燃烧再造烟叶的涂布方法,其包括将涂布液回填至基片上,随后增加蒸汽湿加热的操作工艺,能够提升涂布液的流动相使其更好的向基片内部渗透,从而有效避免粘黏和结块的情况发生,接着增加对潮湿的烟叶半成品进行挤压以调节烟叶半成品的厚度的步骤,能够提升再造烟叶的紧度、挺度和抗张强度。该方法可提升涂布液对基片的渗透性,避免粘黏、结块等不利于后续加工的现象发生,同时该方法可以有效调节加热不燃烧再造烟叶的厚度改善其物理性能,提升加热不燃烧烟支的使用感受。对应的,本申请提供的加热不燃烧再造烟叶的涂布装置,其通过对不同工艺阶段的机构进行设置和排布,使得基片能够在该涂布装置上流水线作业,分别利用涂布机构、喷洒机构和压光机构实现对涂布液和基片的回填、湿加热和挤压操作,最终获得的烟叶的物理性能佳,使用感受佳。
附图说明
43.为了更清楚地说明本发明实施例的技术方案,下面将对实施例中所需要使用的附图作简单地介绍,应当理解,以下附图仅示出了本发明的某些实施例,因此不应被看作是对范围的限定,对于本领域普通技术人员来讲,在不付出创造性劳动的前提下,还可以根据这些附图获得其他相关的附图。
44.图1为本申请实施例提供的加热不燃烧再造烟叶的涂布装置的结构示意图;
45.图2为本申请实施例提供的加热不燃烧再造烟叶的涂布装置的蒸汽喷嘴与第一传送机构相互配合的结构示意图;
46.图3为本申请实施例提供的加热不燃烧再造烟叶的涂布装置的第一传送机构的结构示意图;
47.图4为本申请实施例提供的加热不燃烧再造烟叶的涂布装置的干燥机构的结构示意;
48.图5为本申请实施例提供的加热不燃烧再造烟叶的涂布方法的流程图。
49.图标:100-加热不燃烧再造烟叶的涂布装置;101-基片;110-涂布机构;111-第一涂布辊;112-第二涂布辊;113-涂布液上料口;120-喷洒机构;121-蒸汽喷嘴;130-第一传送机构;131-网状传送带;140-压光机构;141-第一压光辊;142-第二压光辊;150-第二传送机构;160-干燥机构;161-第一个烘箱;162-第二个烘箱;163-第三个烘箱;164-第四个烘箱;165-第五个烘箱;166-第六个烘箱;167-第七个烘箱;168-第八个烘箱;169-第九个烘箱;1610-第十个烘箱。
具体实施方式
50.为使本发明实施例的目的、技术方案和优点更加清楚,下面将结合本发明实施例中的附图,对本发明实施例中的技术方案进行清楚、完整地描述,显然,所描述的实施例是本发明一部分实施例,而不是全部的实施例。通常在此处附图中描述和示出的本发明实施例的组件可以以各种不同的配置来布置和设计。
51.因此,以下对在附图中提供的本发明的实施例的详细描述并非旨在限制要求保护的本发明的范围,而是仅仅表示本发明的选定实施例。基于本发明中的实施例,本领域普通
技术人员在没有作出创造性劳动前提下所获得的所有其他实施例,都属于本发明保护的范围。
52.应注意到:相似的标号和字母在下面的附图中表示类似项,因此,一旦某一项在一个附图中被定义,则在随后的附图中不需要对其进行进一步定义和解释。
53.在本发明的描述中,需要说明的是,若出现术语“上”、“下”、“内”、“外”等指示的方位或位置关系为基于附图所示的方位或位置关系,或者是该发明产品使用时惯常摆放的方位或位置关系,仅是为了便于描述本发明和简化描述,而不是指示或暗示所指的装置或元件必须具有特定的方位、以特定的方位构造和操作,因此不能理解为对本发明的限制。
54.此外,若出现术语“第一”、“第二”等仅用于区分描述,而不能理解为指示或暗示相对重要性。
55.需要说明的是,在不冲突的情况下,本发明的实施例中的特征可以相互结合。
56.本申请提供了一种加热不燃烧再造烟叶的涂布方法以及加热不燃烧再造烟叶的涂布装置100,为了便于后续对涂布方法的介绍,本申请中先对加热不燃烧再造烟叶的涂布装置100的结构进行说明。
57.请参阅图1,本申请提供的加热不燃烧再造烟叶的涂布装置100包括涂布机构110、喷洒机构120、第一传送机构130、压光机构140、第二传送机构150以及干燥机构160。
58.应理解,本申请中的基片101为长条状,其利用第一传送机构130和第二传送机构150不断进行传送,从而分别经过涂布机构110、喷洒机构120、压光机构140和干燥机构160,形成一完整的工业流程线。
59.涂布机构110位于第一传送机构130的进料端,压光机构140位于第一传送机构130的出料端,喷洒机构120位于涂布机构110和压光机构140之间。压光机构140位于第二传送机构150的进料端,干燥机构160位于第二传送机构150的出料端。
60.涂布机构110包括第一涂布辊111、第二涂布辊112以及用于将涂布液挤出至基片101上的涂布液上料口113,本申请中第一涂布辊111和第二涂布辊112相对设置且相向转动,通过第一涂布辊111和第二涂布辊112的相向转动实现对涂布液和基片101进行挤压回填,本申请中,第一涂布辊111的硬度大于第二涂布辊112的硬度。喷洒机构120包括蒸汽喷嘴121。压光机构140包括相对设置且相向转动第一压光辊141和第二压光辊142,第一压光辊141的硬度大于第二压光辊142的硬度。干燥机构160为烘箱组,具体到本申请中,请参阅图4,烘箱组包括10个烘箱,分别为第一个烘箱161、第二个烘箱162、第三个烘箱163、第四个烘箱164、第五个烘箱165、第六个烘箱166、第七个烘箱167、第八个烘箱168、第九个烘箱169和十个烘箱。本申请按照上述工艺设置相互独立的10个烘箱,能够保证每个烘箱的温度和风机频率可单独控制,以便实现更好的对烟叶半成品进行干燥。
61.此外,本申请中,第一传送机构130和第二传送机构150均为传动带形式,具体到本实施例中,请参阅图3,第一传送机构130的传送带为网状传送带131,其网状结构有利于喷洒机构120喷出的热蒸汽渗透,从而带动涂布液进一步渗透至基片101的内部,渗透效果更佳。
62.其中,涂布机构110、喷洒机构120、压光机构140以及干燥机构160的具体结构设计以及参数设计将再下文对涂布方法的描述中进一步详细的描述,这里不再赘述。应理解,本申请中的加热不燃烧再造烟叶的涂布方法和加热不燃烧再造烟叶的涂布装置100的对于各
个机构的设计以及参数是可以相互结合的。
63.本申请提供的加热不燃烧再造烟叶的涂布方法,其包括以下步骤(请参阅图5):
64.s1、涂布步骤:将涂布液回填至基片101上,获得烟叶半成品。
65.具体地,本申请中,利用涂布机构110将涂布液回填至基片101,该涂布机构110包括相对设置且相向转动的第一涂布辊111和第二涂布辊112,第一涂布辊111的硬度大于第二涂布辊112的硬度。本申请中选择双棍进行涂布,且第一涂布辊111和第二涂布辊112的硬度不一样,其中,第一涂布辊111为硬辊,第二涂布辊112为软辊。硬辊和软辊相配合的方式能够保证在涂布过程中,基片101与涂布液呈弧面接触,相较于两个硬辊进行涂布(此时基片101与涂布液呈线接触),涂布更加均匀。
66.优选地,第一涂布辊111的硬度为20-40p&j;第二涂布辊112的硬度为120-140p&j。其中,“p&j”表示勃氏硬度,其英文名称为:pusey&jones,简写代号为“p&j”或“p
·
j”,也可以称之为赵氏或普氏硬度。其数值越大,硬度越小。
67.优选地,本申请的涂布液的温度为55-80℃,通过预先对涂布液进行升温,能够提升涂布液的流动性,有利于涂布液快速渗透至基片101内。
68.s2、强化渗透步骤:利用预设温度的蒸汽湿加热烟叶半成品。
69.经发明人研究发现,现有技术中,发烟剂和涂布液中大分子组分粘度较高,流动性较差,很难渗透到基片101内部,而会在基片101外部形成壳体,一旦吸湿再造烟叶将粘接在一起影响后续加工过程,而单独增加涂布液的温度,无法较好的改善其粘度和流动性,此外,单纯的增加涂布液的温度,会导致涂布液中含水量进一步降低,难以涂布至基片101上。
70.本申请中,通过采用热蒸汽(不低于80℃;优选为80-110℃)喷洒至烟叶半成品上,不仅仅能够提高涂布液的流动性,同时补充了部分水分,稀释了涂布液,进而使得涂布液能够更好的渗透到基片101内,有效避免出现粘黏、结块的现象。
71.优选地,蒸汽的压力为1-15bar;蒸汽压力例如包括1、2、3、4、5、6、7、8、9、10、11、12、13、14和15bar中的任一项或者任意两项之间的范围值。
72.优选地,请参阅图2,利用蒸汽喷嘴121对所述烟叶半成品进行湿加热;蒸汽喷嘴121与烟叶半成品之间的夹角为50
°-
70
°
;蒸汽喷嘴121与烟叶半成品之间的距离为30-50cm;蒸汽喷嘴121成一定角度喷入蒸汽,能够推动涂布液在基片101上流动并渗透进入基片101内部,使得涂布液均匀地渗透至基片101内。而蒸汽喷嘴121与烟叶半成品之间的间距保证了蒸汽喷出后呈扇形喷洒,喷洒面积更广,加热更均匀。
73.优选地,蒸汽喷嘴121为多个且均匀分布于与烟叶半成品的运动方向垂直的方向上;任意两个相邻的蒸汽喷嘴121之间的间距为15-25cm;本申请中,通过设置多个蒸汽喷嘴121,能够使蒸汽喷雾更均匀,实现对烟叶半成品的宽度方向上同步均匀地喷洒。
74.本申请中通过调节蒸汽喷嘴121的出气量以及烟叶半成品的运行速度,以控制烟叶半成品在进行挤压之前的水分保持在15-30%之间,有利于后续的挤压工序。
75.s3、挤压步骤:通过对加热后的烟叶半成品进行挤压以调节烟叶半成品的厚度。
76.具体地,本申请中利用压光机构140对加热后的烟叶半成品进行挤压;通过挤压可以对烟叶半成品的厚度进行调节,从而提升再造烟叶的紧度、挺度和抗张强度。
77.优选地,本申请中,压光机构140包括相对设置且相向转动第一压光辊141和第二压光辊142,第一压光辊141的硬度大于第二压光辊142的硬度;其中,第一压光辊141的硬度
为18-22p&j;第二压光辊142的硬度28-32p&j。同样的,本申请中采用硬度不同的压光辊实现在第一压光辊141和第二压光辊142接触时以弧面接触的方式进行接触,从而提升第一压光辊141和第二压光辊142对于烟叶半成品的挤压均匀度。
78.进一步地,第一压光辊141和第二压光辊142之间的线压力为70-130kn/m,并且该线压力的大小可调节,也即是,第一压光辊141和第二压光辊142之间可调节偏压,从而可依据输送过来的烟叶半成品的厚度来调节第一压光辊141和第二压光辊142的偏压,以确保从第一压光辊141和第二压光辊142之间输出的烟叶半成品的厚度均匀。
79.s4、干燥步骤:在挤压烟叶半成品后进行干燥以脱除烟叶半成品中的水分。
80.具体地,干燥的方式有多种,例如真空干燥、微波干燥和烘箱干燥等等。本申请中优选选择烘箱干燥,即采用烘箱组对挤压后的所述烟叶半成品进行烘干。具体到本实施例中,烘箱组包括多个依次排列的烘箱,且多个烘箱的温度从进料端至出料端的方向先升高后降低;通过升高温度随后降温的方式能够保证烟叶半成品的干燥效果更佳。
81.进一步地的,本申请中,烘箱为10个,其中,靠近进料端的第一个烘箱161的温度为83-87℃,风机频率为32-34%;第二个烘箱162的温度为88-92℃,风机频率为29-31%;第三个烘箱163的温度为98-102℃,风机频率为29-31%;第四个烘箱164的温度为108-112℃,风机频率为29-31%;第五个烘箱165的温度为123-127℃,风机频率为37-39%;第六个烘箱166的温度为108-112℃,风机频率为37-39%;第七个烘箱167的温度为98-102℃,风机频率为32-34%;第八个烘箱168的温度为88-92℃,风机频率为35-36%;第九个烘箱169的温度为88-92℃,风机频率为35-36%;靠近出料端的第十个烘箱1610的温度为88-92℃,风机频率为35-36%。
82.可以看出,本申请中从第一个烘箱161到第五个烘箱165的温度逐渐上升,在这一过程中充分将烟叶半成品进行干燥,而后进行逐渐降温,能够保持烟叶半成品的干燥情况,并逐步将烟叶半成品内部的水分进行烘干,在第八个烘箱168至第四个烘箱164时,其温度基本保持不变,在一恒定的温度下能够更好的维持烟叶半成品处于恒定温度下,保证烟叶半成品的内外温度恒定,受热更均匀,避免发生局部受热过多的情况。
83.此外,本申请中,不仅仅控制了各个烘箱的加热温度,同时还控制了各个烘箱内的风机频率,风机频率越高,风量越大,通过温度和频率的配合,能够实现更好的干燥效果。其中,第一个烘箱161作为初始烘箱,其风量适中(风机频率为32-34%),能够尽可能风干烟叶半成品中的大部分表面的水分,随后第二个烘箱162至第四个烘箱164的风机频率(风机频率为29-31%)略小于第一个烘箱161的风机频率,能够保证在高温缓慢烘干,而后在第五个烘箱165时,温度最高,风机频率也最高,此时通过高温大风量进行充分的烘干,以保证烟叶半成品内的水分的干燥程度,随后降低温度但不降低风机频率的第六个烘箱166中继续加热,能够保证表面干燥的同时内部温度继续升高,接着降低温度并降低风机频率,能够以小风量对烟叶半成品进行干燥,而后继续降低温度,并提高风机频率,使得烟叶半成品逐步降温,利用余温对剩余水分进行干燥,保证烟叶半成品的内外温度恒定,受热更均匀,避免发生局部受热过多的情况。
84.本申请利用硬度不同的双棍将涂布液回填至基片101上,两个辊的接触面积更大,能够保证涂布液回填更均匀,随后增加蒸汽湿加热的操作工艺,能够提升涂布液的流动相使其更好的向基片101内部渗透,从而有效避免粘黏和结块的情况发生,接着增加硬度不同
的压光辊对潮湿的烟叶半成品进行挤压以调节烟叶半成品的厚度,进而提升再造烟叶的紧度、挺度和抗张强度,最后使用烘箱进行干燥脱除再造烟叶中残余的水分。该工艺可提升涂布液对基片101的渗透性避免粘黏、结块等不利于后续加工的现象发生,同时该工艺可以有效调节加热不燃烧再造烟叶的厚度改善其物理性能,提升加热不燃烧烟支的使用感受。
85.接下来,本申请例举实例对本申请提供的加热不燃烧再造烟叶的涂布方法的效果进行说明:
86.实施例1
87.本申请提供了一种加热不燃烧再造烟叶的涂布方法,其包括:
88.s1、涂布步骤。
89.在涂布过程中,控制涂布液的温度为60℃,基片101定量55g/m2,第一涂布辊111的硬度为30p&j;第二涂布辊112的硬度为130p&j。涂布辊线压力10kn/m,涂布液上料量6.5吨/小时,涂布液回流量3.5吨/小时。纸机幅宽3m、纸机车速170m/min、涂布液浓度55%
±
2%。
90.s2、强化渗透步骤。
91.本申请中,利用多个蒸汽喷嘴121对烟叶半成品进行湿加热;多个蒸汽喷嘴121均匀分布于与烟叶半成品的运动方向垂直的方向上;任意两个相邻的蒸汽喷嘴121之间的间距为20cm。蒸汽喷嘴121与烟叶半成品之间的夹角为60
°
;蒸汽喷嘴121与烟叶半成品之间的距离为40cm;热蒸汽的温度为110℃,蒸汽的压力为1bar。在进行挤压之前控制烟叶半成品的水分保持在30%。
92.s3、挤压步骤。
93.第一压光辊141的硬度为20p&j;第二压光辊142的硬度30p&j。第一压光辊141和第二压光辊142之间的线压力为80kn/m。
94.s4、干燥步骤。
95.干燥过程使用的烘箱为10个,其中,靠近进料端的第一个烘箱161的温度为85℃,风机频率为33%;第二个烘箱162的温度为90℃,风机频率为30%;第三个烘箱163的温度为100℃,风机频率为30%;第四个烘箱164的温度为110℃,风机频率为30%;第五个烘箱165的温度为125℃,风机频率为38%;第六个烘箱166的温度为110℃,风机频率为38%;第七个烘箱167的温度为100℃,风机频率为33%;第八个至第十个烘箱1610的温度均为90℃,风机频率均为35%。
96.实施例2
97.本申请提供了一种加热不燃烧再造烟叶的涂布方法,其包括:
98.s1、涂布步骤。
99.在涂布过程中,控制涂布液的温度为55℃,基片101定量55g/m2,第一涂布辊111的硬度为20p&j;第二涂布辊112的硬度为120p&j。涂布辊线压力10kn/m,涂布液上料量6.5吨/小时,涂布液回流量3.5吨/小时。纸机幅宽3m、纸机车速170m/min、涂布液浓度55%
±
2%。
100.s2、强化渗透步骤。
101.本申请中,利用多个蒸汽喷嘴121对烟叶半成品进行湿加热;多个蒸汽喷嘴121均匀分布于与烟叶半成品的运动方向垂直的方向上;任意两个相邻的蒸汽喷嘴121之间的间距为15cm。蒸汽喷嘴121与烟叶半成品之间的夹角为50
°
;蒸汽喷嘴121与烟叶半成品之间的距离为30cm;热蒸汽的温度为80℃,蒸汽的压力为5bar。在进行挤压之前控制烟叶半成品的
水分保持在15%之间。
102.s3、挤压步骤。
103.第一压光辊141的硬度为18p&j;第二压光辊142的硬度28p&j。第一压光辊141和第二压光辊142之间的线压力为75kn/m。
104.s4、干燥步骤。
105.干燥过程使用的烘箱为10个,其中,靠近进料端的第一个烘箱161的温度为83℃,风机频率为32%;第二个烘箱162的温度为88℃,风机频率为29%;第三个烘箱163的温度为98℃,风机频率为29%;第四个烘箱164的温度为108℃,风机频率为29%;第五个烘箱165的温度为123℃,风机频率为37%;第六个烘箱166的温度为108℃,风机频率为37%;第七个烘箱167的温度为98℃,风机频率为32%;第八个至第十个烘箱1610的温度均为88℃,风机频率均为35%。
106.实施例3
107.本申请提供了一种加热不燃烧再造烟叶的涂布方法,其包括:
108.s1、涂布步骤。
109.在涂布过程中,控制涂布液的温度为75℃,基片101定量55g/m2,第一涂布辊111的硬度为40p&j;第二涂布辊112的硬度为140p&j。涂布辊线压力10kn/m,涂布液上料量6.5吨/小时,涂布液回流量3.5吨/小时。纸机幅宽3m、纸机车速170m/min、涂布液浓度55%
±
2%。
110.s2、强化渗透步骤。
111.本申请中,利用多个蒸汽喷嘴121对烟叶半成品进行湿加热;多个蒸汽喷嘴121均匀分布于与烟叶半成品的运动方向垂直的方向上;任意两个相邻的蒸汽喷嘴121之间的间距为25cm。蒸汽喷嘴121与烟叶半成品之间的夹角为70
°
;蒸汽喷嘴121与烟叶半成品之间的距离为50cm;热蒸汽的温度为110℃,蒸汽的压力为15bar。在进行挤压之前控制烟叶半成品的水分保持在25%之间。
112.s3、挤压步骤。
113.第一压光辊141的硬度为22p&j;第二压光辊142的硬度32p&j。第一压光辊141和第二压光辊142之间的线压力为125kn/m。
114.s4、干燥步骤。
115.干燥过程使用的烘箱为10个,其中,靠近进料端的第一个烘箱161的温度为87℃,风机频率为34%;第二个烘箱162的温度为92℃,风机频率为31%;第三个烘箱163的温度为102℃,风机频率为31%;第四个烘箱164的温度为112℃,风机频率为31%;第五个烘箱165的温度为127℃,风机频率为39%;第六个烘箱166的温度为112℃,风机频率为39%;第七个烘箱167的温度为102℃,风机频率为34%;第八个至第十个烘箱1610的温度均为92℃,风机频率均为36%。
116.对比例1
117.对比例1提供了一种常规涂布工艺,具体操作方法为:采用两条硬辊(硬度为20p&j)作为涂布辊,将涂布液回填至基片101上,随后进行干燥操作,其中涂布过程和干燥过程的具体参数可参阅实施例1。
118.对比例2
119.其省略了实施例1中的强化渗透步骤和挤压步骤。
120.对比例3
121.其省略了实施例1中的强化渗透步骤。
122.对比例4
123.其省略了实施例1中的挤压步骤。
124.将上述实施例1-3以及对比例1-4生产的样品进行检测,测试项目包括厚度、定量、松厚度、抗张指数和柔软度,检测结果如表1所示:
125.表1.实施例1-3以及对比例1-4生产的样品的性能检测
[0126] 厚度(mm)定量(g/m2)松厚度(cm3/g)抗张指数柔软度(mn)实施例10.181301.387.5941实施例20.201061.897.1945实施例30.151281.177.8949对比例10.221121.966.21062对比例20.2613026.51121对比例30.191301.467.01069对比例40.251301.926.61071
[0127]
如上表所示,本申请实施例1提供的涂布工艺所制备的造纸法加热不燃烧样品,紧度(松厚度的倒数)、抗张指数、柔软度均优于对比例1提供的工艺涂布生产样品。
[0128]
将上述实施例1-3以及对比例1-4生产的样品上线制备成加热不燃烧卷烟,并对其进行检测分析,具体结果如表2所示。
[0129]
表2.实施例1-3以及对比例1-4生产的样品制备的加热不燃烧卷烟的性能检测
[0130] 重量(g)圆周(mm)圆度(mm)加热段长度(mm)吸阻(pa)衰减口数实施例10.70124.320.7211.99105312实施例20.69924.350.7212.00112210实施例30.70024.220.7212.00119311对比例10.65224.470.7212.0111668对比例20.70224.390.7211.99133110对比例30.70124.210.7211.99116011对比例40.69924.410.7212.01129010
[0131]
如上表所示,实施例1获得的烟支的圆周、圆度、加热段长度与对比例1基本一致,而烟支重量实施例1高于对比例1,说明在相同的烟支中可以装入更多的实施例1提供的加热不燃烧再造烟叶;进行抽吸测试显示,对比例1的烟支的吸阻要高于实施例1,说明使用实施例1加热不燃烧再造烟叶的烟支使用感受更好,同时实施例1烟支装入了更多的加热不燃烧再造烟叶使其烟气、烟雾的持续释放效果更好,抽吸体验更好。
[0132]
综上所述,本申请实施例提供了一种加热不燃烧再造烟叶的涂布方法,其利用硬度不同的双棍将涂布液回填至基片101上,两个辊的接触面积更大,能够保证涂布液回填更均匀,随后增加蒸汽湿加热的操作工艺,能够提升涂布液的流动相使其更好的向基片101内部渗透,从而有效避免粘黏和结块的情况发生,接着增加硬度不同的压光辊对潮湿的烟叶半成品进行挤压以调节烟叶半成品的厚度,进而提升再造烟叶的紧度、挺度和抗张强度,最后使用烘箱进行干燥脱除再造烟叶中残余的水分。该工艺可提升涂布液对基片101的渗透
性避免粘黏、结块等不利于后续加工的现象发生,同时该工艺可以有效调节加热不燃烧再造烟叶的厚度改善其物理性能,提升加热不燃烧烟支的使用感受。对应的,本申请提供的加热不燃烧再造烟叶的涂布装置100,其通过对不同工艺阶段的机构进行设置和排布,使得基片101能够在该涂布装置上流水线作业,分别利用涂布机构110、喷洒机构120和压光机构140实现对涂布液和基片101的回填、湿加热和挤压操作,最终获得的烟叶的物理性能佳,使用感受佳。
[0133]
以上所述,仅为本发明的具体实施方式,但本发明的保护范围并不局限于此,任何熟悉本技术领域的技术人员在本发明揭露的技术范围内,可轻易想到的变化或替换,都应涵盖在本发明的保护范围之内。