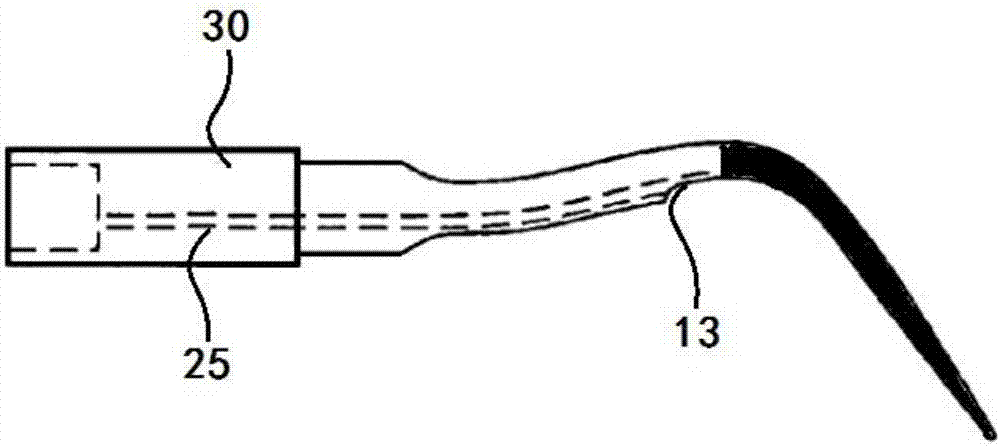
本发明涉及牙科医疗器械的
技术领域:
,更具体地说,本发明涉及一种超声洁牙装置及其制备方法。
背景技术:
:口腔卫生以及牙齿健康是人体健康的重要组成部分,是维系和提高生命质量的重要因素。现代研究证明,牙病可以引发或加重冠心病、糖尿病等全身性疾病。随着时间的推移,牙齿上会形成各种沉积物,例如色斑、菌斑、牙垢以及牙结石等沉积物,这些沉积物一般很难通过日常的刷牙清洗,而这些沉积物不仅形成牙齿表面而且可能深入牙龈线以下到达牙龈内部,因此为了保持口腔清洁以及牙齿和牙龈健康,应定期地进行专业地洁牙。为了专业地洁牙,现有技术中已经开发了多种洁牙装置,而目前超声波洁牙装置和方法成为主流的洁牙装置。超声洁牙装置一般由包括带适配器的电源、超声换能器以及工作尖头等组成,给超声波换能器施加电能后生成超声波进而带动工作尖端进行刮、磨、钻等治疗操作。在现有技术中通常采用涂布有氮化钛、碳化钛或二氧化碳钛涂层的不锈钢制工作尖头,由于通过常规pvd或cvd方法形成的氮化钛、碳化钛或二氧化碳钛涂层较薄,耐久性较差,从而导致工作尖头的使用寿命较短,需要频繁地更换工作尖头。技术实现要素:为了解决现有技术中的上述技术问题,本发明的目的在于提供一种超声洁牙装置及其制备方法。一种超声洁牙装置,包括内部设置有超声换能器的手持件以及工作尖端,其特征在于:所述工作端可拆卸地连接至所述手持件。其中,所述工作端包括中空的颈部以及弯曲尖头,所述颈部与所述手持件可拆卸地连接,并且所述颈部与所述弯曲尖头的结合处设置有出水口,并且所述出水口的开口方向朝向所述弯曲尖头的方向。其中,所述手持件内部为空腔结构,所述超声换能器设置在所述空腔结构中,并且所述空腔结构中还设置有导流管,并且所述导流管延伸至所述中空的颈部内。其中,所述超声换能器为压电陶瓷超声换能器或磁致伸缩超声换能器。其中,所述工作端由不锈钢加工而成,并且所述工作端的弯曲尖头上涂覆有铜铬合金层,并且所述铜铬合金层上设置有耐磨工作层。其中,所述铜铬合金层中,铬的含量为12~35at%,余量为铜。其中,所述铜铬合金层的厚度为0.05~1.0μm;所述耐磨工作层为厚度为2.5~20μm的碳氮化硅膜层。其中,所述耐磨工作层在氮气气氛中进行退火热处理,热处理温度为400℃。其中,所述碳氮化硅膜层采用等离子增强化学气相沉积方法得到,并且以xps测量的硅:氮:碳的摩尔比为1:1.05~1.82:0.12~0.95。其中,所述碳氮化硅膜层采用等离子增强化学气相沉积方法得到,并且以xps测量的硅:氮:碳的摩尔比为1:1.25~1.80:0.32~0.60。本发明的超声洁牙装置具有以下有益效果:本发明的超声洁牙装置结构简单,工作端的工作尖头设置有硬质耐磨工作层,耐久性好,可重复使用,而且工作端拆卸更换方便。附图说明图1为本发明的超声洁牙装置的整体结构示意图。图2为工作尖端与手持件配合部的放大结构示意图。具体实施方式以下将结合具体实施例对本发明所述的超声洁牙装置做进一步的阐述,以帮助本领域的技术人员对本发明的发明构思、技术方案有更完整、准确和深入的理解。如图1所示,本发明的超声洁牙装置,包括内部设置有超声换能器的手持件20以及工作尖端10,所述工作尖端10包括中空的颈部11以及弯曲尖头12,所述颈部与所述手持件可拆卸地连接,并且所述颈部与所述弯曲尖头的结合处设置有出水口13,并且所述出水口13的开口方向朝向所述弯曲尖头的方向,从而可以使得在洁牙时流水根据吸附原理能够顺着弯曲尖头流到正在清洁的牙齿部分。如图2所示,所述手持件20内部为空腔结构30,所述超声换能器设置在所述空腔结构中(图中未示出),并且所述空腔结构中还设置有导流管25,并且所述导流管25延伸至所述中空的颈部内,为了方便调节导流管中的水流流量,所述空腔结构中还可设置有一个小的储水槽(图中虚线方框中所示)。在手持件20的外端面上可设置有用于调节功率以及水流量的旋钮,并且所述手持件通过导线连接至一带有电源适配器的电源和控制器,所述带有电源适配器的电源和控制器等通常设置在盒体内一般称为主机(图中未示出);并且手持件20还通过一导管连接至供水源(所述供水源一般为去离子水、蒸馏水,并且根据需要可以添加口腔治疗用的药剂),在现有技术中所述供水源也可以集成在盒体中,此时所述导线与导管也可以集成一根软管中。在本发明中,所述超声换能器为压电陶瓷超声换能器或磁致伸缩超声换能器。在本发明中,所述工作端由不锈钢加工而成,由于工作端的弯曲尖端表面会与洁牙者的牙齿接触,从而使得弯曲尖端在超声振动下会与钙化的牙结石以及超硬牙釉质等接触,因而在清洁操作下弯曲尖头会经受持续的磨损,为了提高弯曲尖头的耐久性,通常会在弯曲尖头上涂覆耐磨硬质涂层,作为耐磨硬质涂层的例子,例如可以涂覆钛、铬、锆、镍、铝等的碳化物、氮化物、硼化物或碳氮化物等,在现有技术中通常采用tic、ticn、tialcn、tin、tio2、crn等涂层,由于其可镀的厚度较薄,导致镀层的耐磨耐久性不佳,需要经常更换工作端,而金刚石膜层具有已知最高的硬度和耐磨性,因而期望结合金刚石膜层或类金刚石膜层来提高弯曲尖头的耐磨损性能和耐久性。然而不锈钢基材与金刚石之间的热膨胀系数差异大,导致二者之间的结合强度较差,另外铁基材料形成的类金刚石膜层中石墨含量高,得到的类金刚石膜层的质量较差。为了提高不锈钢的弯曲尖端与耐磨工作层之间的结合强度,在本发明中首先在弯曲尖头上涂覆形成铜铬合金层。在本发明中,所述不锈钢优选为奥氏体不锈钢或马氏体不锈钢,并且通过机械加工例如冲压、压延等工艺形成工作端。在涂覆形成铜铬合金层之前,首先对工作端进行清洗,所述清洗例如可以包括碱洗和水洗,以去除表面的氧化膜和杂质等,从而提高不锈钢工作端与设置的铜铬合金层之间的粘结性。然后,在真空镀膜设备中,在工作端的弯曲尖端表面上沉积铜铬合金层,所述铜铬合金层的厚度为0.05~1.0μm,优选为0.10~0.50μm,所述铜铬合金层中,铬的含量为12~35at%,余量为铜;更优选地所述铬的含量为15~25at%。在真空镀膜设备中沉积铜铬合金层的方法可采用蒸镀、溅射、离子镀等pvd镀膜方法,为了保证涂层的均匀性,在镀膜时所述工作端可以设置在带旋转设备的基座上。在本发明中,所述耐磨工作层为厚度为2.5~20μm的碳氮化硅膜层,优选地,所述碳氮化硅膜层的厚度为5.0~15μm。并且所述碳氮化硅膜层中以xps测量的硅:氮:碳的摩尔比为1:1.05~1.82:0.12~0.95。所述碳氮化硅膜层是以硅烷、氮气以及乙炔气体作为si源、n源以及c源的供给气体。本发明的碳氮化硅膜层优选通过等离子增强化学气相沉积方法制备得到。具体来说,所述的碳氮化硅膜层在等离子体增强化学气相沉积装置中制备得到,所述的装置通常包括带有基座的反应腔室、真空系统、反应气体气路系统以及等离子发生装置,为了提高膜层的均匀性,所述工作端的弯曲尖头(预先涂覆有铜铬合金层)在镀膜过程中处于旋转状态,并且在工件上施加负偏压,所述负偏压可设置为-500v。在镀覆碳氮化硅膜层之前预先镀覆铜铬合金层,然后组装在基座上放入反应腔室之后进行抽真空,并使得反应腔室的本底真空度应维持在10-5pa或以上的水平。本发明采用等离子增强化学气相沉积方法,工件温度可以在250~350℃的较低温度范围进行沉积。本发明的方法中,首先在工作端的弯曲尖头上镀覆铜铬合金层。作为示例性地首先对工作端进行清洗并干燥,接着将所述工作端放置在镀膜腔室中,并对镀膜腔室进行抽真空,使得镀膜腔室内的真空度为5×10-3pa以下,然后通入20~50sccm的氩气,并施加300~500v的直流电压以产生氩等离子进行预溅射以去除工作端的不锈钢层表面的氧化膜层。然后在设置有铬靶和铜靶的真空镀膜腔室中在工作端的弯曲尖头沉积铜铬合金层(颈部可以通过掩膜遮盖),在真空镀膜室中导入50~100sccm的氩气,并施加400v的直流电压以产生氩等离子体,设置铬靶和铜靶电离电压为30~100v,电离电流为10~50a,从而可以在工作端的弯曲尖头上镀覆铜铬合金层,通过调节铬靶和铜靶的电离电压和电流可以调节铜铬合金层中铜和铬的含量,而通过时间控制可以控制膜层的厚度。然后,在铜铬合金层上镀覆碳氮化硅膜层。作为示例性地,在安装有远程等离子体发生器的等离子增强化学气相沉积装置中,采用的射频电源的频率为13.56mhz,功率为500w。将镀覆有铜铬合金层的工作端放入反应腔室之后进行多级抽真空至10-5pa,然后通入100~200sccm的氩气,并施加400v的直流电压以产生氩等离子进行预溅射10~15分钟。镀覆时,氩气的流量为50~100sccm,硅烷的流量为30~100sccm,氮气的流量为25~100sccm,乙炔的流量为12~30sccm,沉积温度为300℃,对安装镀覆有铜铬合金层的工作端的基座施加-400v的偏压;沉积后在氮气气氛中进行退火热处理,热处理温度为400℃,时间为30分钟。通过调节各前体的流量,以及镀膜时间等参数可以调节得到的碳氮化硅膜层中的si、c和n的摩尔比以及膜层的厚度。表1示出了不同厚度和组成(通过x射线光电子能谱xps分析)的实施例和对比例。表1对比例5中1:1.27为si与n的原子比;对比例8中1:0.96为si与c的原子比。采用nanotest600测试硬度(berkovitch型锥型金刚石压头),参照德国工程师手册(vdi3198)压入法测量膜层的结合强度,参照标准dinen1071-6:2006-01测量膜层的耐磨性,其结果如表2所示。表2硬度(gpa)结合强度磨损量(m3m-1n-110-15)实施例115hf1~20.53实施例218hf1~20.57实施例325hf10.23实施例421hf10.37实施例516hf1~20.63实施例615hf1~20.61实施例727hf1~20.49实施例823hf10.19实施例915hf1~20.83实施例1017hf1~20.81对比例123hf3~4>10对比例225hf3~4>10对比例322hf3~4>10对比例423hf3~4>10对比例521hf3~4>20对比例615hf1~2>10对比例712hf1~2>10对比例825hf3~4>20对于碳氢膜层(例如类金刚石膜层)通常在不锈钢基体上可设置铬膜层来改进结合强度,但是对于本发明中的碳氮化硅而言,其在热处理后表现出的结合强度反而较差,而通过镀覆铜铬合金(铬含量为15~25at%)热处理后则可以获得良好的结合强度,这可能与热处理时铜铬合金与不锈钢以及碳氮化硅良好的匹配有关,而且通过添加适量的铬有利于碳氮化硅膜层与铜铬合金膜层的化学键合,在本申请中结合强度通过vdi3198测量,该结合强度反映的是膜层整体结合性能,对膜层的耐磨性有直接的影响。另外,碳氮化硅膜层中硅/氮比以及硅/碳比不仅影响到膜层的硬度,而且也会影响到碳氮化硅膜层与不锈钢之间的结合强度。所述碳氮化硅膜层中以xps测量的硅:氮:碳的摩尔比为1:1.25~1.80:0.32~0.60的范围时能够获得更高的硬度(18~27gpa)以及更好的耐磨性(0.15~0.50×m3m-1n-110-15),因而是优选地。对于本领域的普通技术人员而言,具体实施例只是对本发明进行了示例性描述,显然本发明具体实现并不受上述方式的限制,只要采用了本发明的方法构思和技术方案进行的各种非实质性的改进,或未经改进将本发明的构思和技术方案直接应用于其它场合的,均在本发明的保护范围之内。当前第1页12