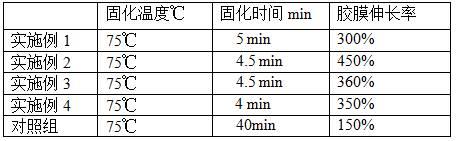
1.本发明属于静电植绒面料领域,具体涉及一种热塑性静电植绒面料及其制备方法和应用。
背景技术:2.汽车脚垫的主要功能是保护原车毯,要有安全、健康、舒适、美观的综合性能,人们通过不断的技术研发和实用经验积累,总结出脚垫材料的最佳选择是地毯类材料。然而由于地毯类材料制造工艺的原因,不具备热塑成型条件,只能用于平垫,而平垫对原车毯的防护区域有限,从而致使诸多使用者放弃了最佳选择。另外地毯类材料不易打理,也给使用者带来了不良体验。静电植绒面料最大的特点是绒面由直立的单纤构成,通过绒毛胶水与基层面料结合,形成绒面材料,单纤不同于纱线,其形成的毯面没有夹持能力,其结果是易打理易清洁,非常适合用于汽车脚垫制造领域。目前尚未发现制绒技术汽车地毯脚垫领域应用。
3.应用热塑性发泡片材(tpe、xpe、eva等)热拉成型,用于嵌入式汽车脚垫的产品技术得到广泛应用。由于该类材料的力学特性,并不能直接使用,为解决这一问题,目前有三种方法:1)成型后粘贴,其方法是先将片材热拉成型,然后用胶水将手工缝制的其它脚垫材料粘贴上,达到可以使用的要求;2)粘贴后成型,其方法是先将片材与其它热塑性材料复合,然后热拉成型,可以直接使用。所用到的材料一般为人造革类,复合后改进了成型体的表面强度,通过选用不同表面风格的革材,也提升了美观度;3)复合后成型,利用热塑性发泡片材的特性,热复合上无纺材料,所选用的材料经过拉绒处理,成型产品在改善了发泡片材表面强度的基础上,提升了产品的舒适性。
4.静电植绒产品技术在我国已有数十年的发展,随着该技术的不断进步,产品在服装、装饰、家居、包装、地毯等领域得到广泛应用。将静电植绒产品技术应用到热拉成型汽车脚垫产品,要求植绒面料有较好的热塑性,常规的植绒面料不具备这一要求。常规植绒面料,基布、胶水的选用差异,其弹性形变一般在8%—20%之间,在热态(150℃—170℃)下,没有塑性形变,在外力下只能产生破坏性变形。
5.因此,研发一种可适用于热拉成型工艺的植绒面料,并应用于汽车地毯脚垫领域具有重要意义。
技术实现要素:6.针对现有技术中存在的静电植绒面料热塑性差,没有塑形形变的问题,本发明提供了及一种热塑性植绒面料及其制备方法和应用,制备的静电植绒面料在常温下具有较好的尺寸稳定性,弹性伸长率为5~8%,热态(150
‑
170℃)下,可发生塑性形变,且塑性变形均匀、无撕裂、龟裂现象。
7.本发明通过以下技术方案实现:一种热塑性静电植绒面料,由面层、中间层和底层构成;所述的面层为纤维绒毛,
中间层为胶水固化层,底层为基布;所述的胶水固化层为静电植绒胶,由以下重量份的组分构成:混合单体80
‑
120份,乳化剂3
‑
4份,引发剂0.4
‑
0.5份,交联剂3
‑
5份,水120~150份;所述的混合单体包括甲基丙烯酸甲酯10
‑
20份,马来酸二丁酯 8
‑
15份,丙烯酸丁酯35
‑
50份,丙烯酸乙酯10
‑
20份,环氧树脂10
‑
20份。
8.进一步地,所述纤维绒毛的绒毛成分为pa、pet、pp化学纤维材料,绒毛纤度为10
‑
50d,绒毛长度为2
‑
6mm;所述的胶水固化层的厚度为0.8~1.2mm;所述的基布为针刺涤纶无纺布,200
‑
400g/
㎡
。
9.进一步地,所述的乳化剂为op
‑
10烷基酚聚氧乙烯醚;所述的引发剂为过硫酸钾;所述的交联剂为n
‑
羟甲基丙烯酰胺。
10.进一步地,所述的静电植绒胶通过以下方法制备得到:(1)将乳化剂和水混合搅拌,搅拌后加入混合单体,继续搅拌均匀,得预乳液;(2)将交联剂在水中溶解,溶解后的交联剂溶液待用;(3) 将引发剂在水中溶解,溶解后的引发剂溶液待用;(4)将步骤(1)中部分预乳液取出,向剩余的预乳液中加入部分引发剂溶液,在100
‑
200r/min的搅拌速率下升温至40
‑
50℃,反应50~80min,升温至70
‑
90℃,搅拌速率增长为300
‑
400r/min,然后将剩余的预乳液和剩余的引发剂溶液、交联剂溶液缓慢加入,搅拌速率为200
‑
300r/min,加入完毕后70
‑
90℃下静置1.5~2.5h,冷却至室温,过滤得静电植绒胶。
11.进一步地,所述的引发剂溶液的浓度为0.02
‑
0.045g/ml;所述的交联剂溶液的浓度为0.4
‑
0.5g/ml。
12.本发明中,所述的热塑性静电植绒面料的制备方法为:设置底层基布,通过机械发泡的方式将静电植绒胶涂覆在底层基布上,然后利用静电植绒的方式植入纤维绒毛作为面层,最后烘干、刷毛制得热塑性静电植绒面料。
13.进一步地,所述的机械发泡率为150
‑
300%,上胶量为500
‑
1000g/
㎡
;所述的静电植绒投绒量为200
‑
600g/
㎡
;所述的烘干时一区温度为100
‑
110℃,二区温度为130
‑
160℃,三区温度为150
‑
170℃,四区温度为常温加水冷。
14.进一步地,所述的机械发泡时向静电植绒胶中加入3~5wt%的增稠剂se
‑
60。本发明中,所述的热塑性静电植绒面料在绒面弹性复合材料中的应用。
15.进一步地,所述的绒面弹性复合材料为汽车地毯脚垫。
16.本发明在热塑性静电植绒面料制备工艺中,静电植绒胶涂布后会沿基布纹理渗透,所形成的复合结构稳定,有利于提高面料的屈服形变,静电植绒胶机械发泡后,增加了粘稠度,当粘稠度达到18000mpa
·
s时,屈服形变>40%,满足产品成型需要。
17.本发明中使用静电植绒胶作为静电植绒面料的中间层,与现有的乳液型静电植绒胶相比,在固化温度相同的情况下,所需烘干时间被大大缩短,节省了相关生产工艺流程所需的时间和物力资源,在增稠剂(se
‑
60)机械转速相同的情况下,起泡倍率高。
18.利用本发明中的静电植绒胶制备热塑性静电植绒面料,该面料在常温时具有较好的尺寸稳定性,热态(150
‑
170℃)下,可发生塑性形变,且塑性变形均匀、无撕裂、龟裂现象,可与热塑性发泡片材(tpe、xpe、eva等)复合成型,成型产品在改善了发泡片材表面强度的基础上,提升了产品的舒适性,可应用于嵌入式汽车地毯脚垫所需的新材料。
19.有益效果
(1)本发明制备的静电植绒胶固化温度低,成膜后胶膜伸长率高达300
‑
450%,胶膜柔软,应用于制备热塑性静电植绒面料时静电植绒胶涂布后会沿基布纹理渗透,所形成的复合结构稳定,有利于提高面料的屈服形变,机械发泡后,粘度高达18000
‑
24000mpa
·
s时,屈服形变>40%,满足产品成型需要;(2)本发明制备的静电植绒面料在常温下具有较好的尺寸稳定性,弹性伸长率为5~8%,热态(150
‑
170℃)下,可发生塑性形变,且塑性变形均匀、无撕裂、龟裂现象,可应用于嵌入式汽车地毯脚垫所需的新材料。
具体实施方式
20.为了进一步理解本发明,下面结合实施例对本发明优选实施方案进行描述,但是应当理解,这些描述只是进一步说明本发明的特征及优点,而不是对本发明进行限制。
21.下列实施例1
‑
4所述的引发剂为过硫酸钾;下列实施例5~8制备热塑性静电植绒面料:面层为尼龙纤维绒毛,绒毛成分为(尼龙)、绒毛纤度为10d—50d,绒毛长度为2mm
‑
6mm;中间层为静电植绒胶(实施例1
‑
4制备的静电植绒胶)固化层;下层基布为针刺涤纶无纺基布,(克重为)300g/
㎡
。
22.实施例1(1)在装有搅拌器、回流冷凝管、橡皮塞和温度计的四颈瓶中加入op
‑
10 9g和去离子水252ml,进行搅拌,搅拌速度为1800r/min,搅拌15min后,滴入混合单体300g(甲基丙烯酸甲酯45g,马来酸二丁酯 30g,丙烯酸丁酯120g,丙烯酸乙酯45g,环氧树脂60g),然后继续以2000r/min速度搅拌至混合均匀,得预乳液;(2)将引发剂1 .35g溶解于35ml去离子水中得引发剂溶液,将交联剂n
‑
羟甲基丙烯酰胺4g溶于10ml去离子水中得交联剂溶液,将步骤(1)中制备的预乳液分离出2/3备用,向步骤(1)中剩余的1/3预乳液中加入20ml引发剂溶液,边搅拌边升温,搅拌速度为150r/min,45℃条件下反应1h,然后使温度缓慢升至80℃时,此时增加搅拌速率至350r/min,然后将分离出的2/3预乳液匀速滴入四颈瓶中,剩余的引发剂溶液和和交联剂溶液分四次随剩余的预乳液加入至四颈瓶中,以250r/min的速度继续搅拌,等全部滴加完后在80℃恒温状态下静置2h,最后自然冷却至室温,过滤即得低温丙烯酸静电植绒胶,制备的低温丙烯酸静电植绒胶的固含量为51%,25℃下黏度为3500mpas。
23.实施例2(1)在装有搅拌器、回流冷凝管、橡皮塞和温度计的四颈瓶中加入op
‑
10 1.2g和去离子水298ml,进行搅拌,搅拌速度为1800r/min,搅拌15min后,滴入混合单体345g(甲基丙烯酸甲酯52g,马来酸二丁酯 35g,丙烯酸丁酯139g,丙烯酸乙酯50g,环氧树脂69g),然后继续以2000r/min速度搅拌至混合均匀,得预乳液;(2)将引发剂1.55g溶解于35ml去离子水中得引发剂溶液,将交联剂n—羟甲基丙烯酰胺5g溶于10ml去离子在水中得交联剂溶液,将步骤(1)中制备的预乳液分离出2/3备用,向步骤(1)中剩余1/3预乳液中加入20ml引发剂溶液,边搅拌边升温,搅拌速度为150r/min,45℃条件下反应1h,然后使温度缓慢升至80℃时,此时增加搅拌速率至350r/min,然后将分离出的2/3预乳液匀速滴入四颈瓶中,剩余的引发剂溶液和和交联剂溶液分四次随剩余的预乳液加入至四颈瓶中,以250r/min的速度继续搅拌,等全部滴加完后在80℃恒温状
态下静置2h,最后自然冷却至室温,过滤即得低温丙烯酸静电植绒胶,制备的低温丙烯酸静电植绒胶的固含量为50%,25℃下黏度为2800mpas。
24.实施例3(1)在装有搅拌器、回流冷凝管、橡皮塞和温度计的四颈瓶中加入op
‑
10 0.72g和去离子水172ml,进行搅拌,搅拌速度为1800r/min,搅拌15min后,滴入混合单体180g(甲基丙烯酸甲酯18g,马来酸二丁酯 27g,丙烯酸丁酯61g,丙烯酸乙酯36g,环氧树脂38g),然后继续以2000r/min速度搅拌至混合均匀,得预乳液;(2)将引发剂0.72g溶解于35ml去离子水中得引发剂溶液,将交联剂n
‑
羟甲基丙烯酰胺4g溶解于10ml去离子水中得交联剂溶液,将步骤(1)中制备的预乳液分离出2/3备用,向步骤(1)中剩余1/3预乳液中加入20ml引发剂溶液,边搅拌边升温,搅拌速度为150r/min,45℃条件下反应1h,然后使温度缓慢升至80℃时,此时增加搅拌速率至350r/min,然后将分离出的2/3预乳液匀速滴入四颈瓶中,剩余的引发剂溶液和交联剂溶液分四次随剩余的预乳液加入至四颈瓶中,以250r/min的速度继续搅拌,等全部滴加完后在80℃恒温状态下静置2h,最后自然冷却至室温,过滤即得低温丙烯酸静电植绒胶,制备的低温丙烯酸静电植绒胶的固含量为46%,25℃下黏度为2600mpas。
25.实施例4(1)在装有搅拌器、回流冷凝管、橡皮塞和温度计的四颈瓶中加入op
‑
10 0.92g和去离子水223ml,进行搅拌,搅拌速度为1800r/min,搅拌15min后,滴入混合单体248g(甲基丙烯酸甲酯49g,马来酸二丁酯 37g,丙烯酸丁酯74g,丙烯酸乙酯37g,环氧树脂51g),然后继续以2000r/min速度搅拌至混合均匀,得预乳液;(2)将引发剂0.99g溶解于35ml去离子水中得引发剂溶液,将交联剂n
‑
羟甲基丙烯酰胺4g溶解于10ml去离子水中得交联剂溶液,将步骤(1)中制备的预乳液分离出2/3备用,向步骤(1)中剩余的1/3预乳液中加入20ml引发剂溶液,边搅拌边升温,搅拌速度为150r/min,45℃条件下反应1h,然后使温度缓慢升至80℃时,此时增加搅拌速率至350r/min,然后将分离出的2/3预乳液匀速滴入四颈瓶中,剩余的引发剂溶液和交联剂溶液分四次随剩余的预乳液加入至四颈瓶中,以250r/min的速度继续搅拌,等全部滴加完后在80℃恒温状态下静置2h,最后自然冷却至室温,过滤即得低温丙烯酸静电植绒胶,制备的低温丙烯酸静电植绒胶的固含量为48.6%,25℃下黏度为3300mpas。
26.静电植绒胶性能进行测试:以商业购买的乳液型静电植绒胶作为对照组,将实施例1~4制备的静电植绒胶和对照组乳液型静电植绒胶分别倾倒于玻璃板上,在75℃下进行固化,记录固化时间,待形成胶膜后使用胶膜拉伸机测试胶膜的胶膜伸长率,结果如下表1所示。由表1可知,本发明制备的静电植绒胶与现有乳液型静电植绒胶相比,在固化温度相同情况下,固化时间明显缩短,即所需烘干时间大大被缩短,节省相关生产工艺流程所需时间和物力资源,在本专利静电植绒胶与现有乳液型丙烯酸植绒胶在添加增稠剂(se—60)增加粘度至18000mpas情况下,达到植绒所需粘度的条件,机械转速相同,烘箱温度与时间一样的情况下,本专利静电植绒胶明显优于现有乳液型丙烯酸静电植绒胶。
27.表1 静电植绒胶性能测试结果
实施例5应用实施例1制备的静电植绒胶作为中间层(胶水固化层)制备热塑性静电植绒面料:热塑性静电植绒面料由面层、中间层和底层构成,面层为尼龙纤维绒毛,中间层为静电植绒胶固化层,底层为针刺涤纶无纺基布;热塑性静电植绒面料的生产工艺为:进料
→
上胶
→
植绒
→
烘干
→
刷毛
→
成品;(1)进料:表面平整的涤纶水刺无纺布作为底层基布架放到放布架上面,同时给予一定的张力进行张紧定型;(2)上胶:底层基布以一定的速率(8m/min)通过开花辊喂入到浆台,通过刮刀和布面之间的间隙将机械发泡后的静电植绒胶(静电植绒胶的机械发泡倍率为1.5倍,在机械发泡的同时加入se
‑
60(25g/
㎡
),发泡后静电植绒胶的黏度为18000mpas)均匀挤出,再通过毛刷盘和压盘作用将底布固定到植绒生产线两边的针板上以防止底布的上下震动和左右移动;(3)植绒:植绒机将涂覆好的底层基布喂入到植绒区域,绒毛通过正负电荷作用,产生净负电荷,使绒毛在电场中具有很大的伸直度和飞翔性,以较高的速度垂直下落到涂有静电植绒胶的涤纶水刺无纺基布上;(4)烘干:在植绒结束后,进入四项烘箱进行烘干(一区温度为105℃,二区温度为150℃,三区温度为160℃,四区温度为常温加水冷),使胶水凝固,绒毛固定在底层基布上;(5)刷毛:植绒后虽吸去浮绒,但在绒毛间隙中还有残留绒毛,一般采用毛刷逆基布运动走向的方式,进行一次刷毛清理,并用吹风装置将刷掉的绒毛进行收集;(6)成品:将刷完毛的植绒面料经过储布架进行打卷,通过纠偏使植绒卷轴整齐,最终产品达到上胶量500g/
㎡
,上毛量达到320g/
㎡
。
28.实施例6应用实施例2制备的静电植绒胶作为中间层(胶水固化层)制备热塑性静电植绒面料:热塑性静电植绒面料由面层、中间层和底层构成,面层为尼龙纤维绒毛,中间层为静电植绒胶固化层,底层为针刺涤纶无纺基布;热塑性静电植绒面料的生产工艺为:进料
→
上胶
→
植绒
→
烘干
→
刷毛
→
成品;(1)进料:以表面平整的涤纶水刺无纺布为底层基布,放到放布架上面,同时给予一定的张力进行张紧定型;(2)上胶:底层基布以一定的速率(8m/min)通过开花辊喂入到浆台,通过刮刀和布面之间的间隙将机械发泡后的静电植绒胶(静电植绒胶的机械发泡倍率1.5倍,在机械发泡的同时加入se
‑
60(30g/
㎡
),发泡后静电植绒胶的黏度为18000mpas)均匀挤出,再通过毛刷盘和压盘作用将底层基布固定到植绒生产线两边的针板上以防止底层基布的上下震动和左右移动;
(3)植绒:植绒机将涂覆好的底层基布喂入到植绒区域,绒毛通过正负电荷作用,产生净负电荷,使绒毛在电场中具有很大的伸直度和飞翔性,以较高的速度垂直下落到涂有静电植绒胶的底层基布上;(4)烘干:在植绒结束后,进入四项烘箱进行烘干(一区温度为105℃,二区温度为150℃,三区温度为160℃,四区温度为常温加水冷),使胶水凝固,绒毛固定在底层基布上;(5)刷毛:植绒后虽吸去浮绒,但在绒毛间隙中还有残留绒毛,一般采用毛刷逆基布运动走向的方式,进行一次刷毛清理,并用吹风装置将刷掉的绒毛进行收集;(6)成品:将刷完毛的植绒面料经过储布架进行打卷,通过纠偏使植绒卷轴整齐,最终产品达到上胶量600g/
㎡
,上毛量达到380g/
㎡
。
29.实施例7应用实施例3制备的静电植绒胶作为中间层(胶水固化层)制备热塑性静电植绒面料:热塑性静电植绒面料由面层、中间层和底层构成,面层为尼龙纤维绒毛,中间层为静电植绒胶固化层,底层为针刺涤纶无纺基布;热塑性静电植绒面料的生产工艺为:进料
→
上胶
→
植绒
→
烘干
→
刷毛
→
成品;(1)进料:以表面平整的涤纶水刺无纺布作为底层基布,放到放布架上面,同时给予一定的张力进行张紧定型;(2)上胶:下层基布以一定的速率(8m/min)通过开花辊喂入到浆台,通过刮刀和布面之间的间隙将机械发泡后的静电植绒胶(静电植绒胶的机械发泡倍率1.5倍,在机械发泡的同时加入se
‑
60(35g/
㎡
),发泡后静电植绒胶的黏度为18000mpas)均匀挤出,再通过毛刷盘和压盘作用将底层基布固定到植绒生产线两边的针板上以防止底层基布的上下震动和左右移动;(3)植绒:植绒机将涂覆好的底层基布喂入到植绒区域,绒毛通过正负电荷作用,产生净负电荷,使绒毛在电场中具有很大的伸直度和飞翔性,以较高的速度垂直下落到涂有静电植绒胶的底层基布上;(4)烘干:在植绒结束后,进入四项烘箱进行烘干(一区温度为105℃,二区温度为150℃,三区温度为160℃,四区温度为常温加水冷),使胶水凝固,绒毛固定在底层基布上;(5)刷毛:植绒后虽吸去浮绒,但在绒毛间隙中还有残留绒毛,一般采用毛刷逆基布运动走向的方式,进行一次刷毛清理,并用吹风装置将刷掉的绒毛进行收集;(6)成品:将刷完毛的植绒面料经过储布架进行打卷,通过纠偏使植绒卷轴整齐,最终产品达到上浆量700g/
㎡
,上毛量达到450g/
㎡
。
30.实施例8应用实施例4制备的静电植绒胶作为中间层(胶水固化层)制备热塑性静电植绒面料:热塑性静电植绒面料由面层、中间层和底层构成,面层为尼龙纤维绒毛,中间层为静电植绒胶固化层,底层为针刺涤纶无纺基布;热塑性静电植绒面料的生产工艺为:进料
→
上胶
→
植绒
→
烘干
→
刷毛
→
成品;(1)进料:以表面平整的涤纶水刺无纺布作为底层基布,放到放布架上面,同时给予一定的张力进行张紧定型;(2)上胶:基布以一定的速率(8m/min)通过开花辊喂入到浆台,通过刮刀和布面之间的间隙将机械发泡后的静电植绒胶(静电植绒胶的机械发泡倍率1.5倍,在机械发泡的同
时加入se
‑
60 (37.5g/
㎡
),发泡后静电植绒胶的黏度为18000mpas)均匀挤出,再通过毛刷盘和压盘作用将基布固定到植绒生产线两边的针板上以防止底层基布的上下震动和左右移动;(3)植绒:植绒机将涂覆好的底层基布喂入到植绒区域,绒毛通过正负电荷作用,产生净负电荷,使绒毛在电场中具有很大的伸直度和飞翔性,以较高的速度垂直下落到涂有静电植绒胶的底层基布上;(4)烘干:在植绒结束后,进入四项烘箱进行烘干(一区温度为105℃,二区温度为150℃,三区温度为160℃,四区温度为常温加水冷),使胶水凝固,绒毛固定在底层基布上;(5)刷毛:植绒后虽吸去浮绒,但在绒毛间隙中还有残留绒毛,一般采用毛刷逆基布运动走向的方式,进行一次刷毛清理。并用吹风装置将刷掉的绒毛进行收集;(6)成品:将刷完毛的植绒面料经过储布架进行打卷,通过纠偏使植绒卷轴整齐,最终产品达到上胶量750g/
㎡
,上毛量达到520g/
㎡
。
31.热塑性静电植绒面料热塑性研究以市场购买的静电植绒面料作为对照组,对实施例5
‑
8制备的热塑性静电植绒面料和对照组的静电植绒面料进行性能表征,测量其在常温和170℃条件下的弹性伸长率(热塑性),结果如下表2所示。由表2可知,利用本发明中的静电植绒胶制备的热塑性静电植绒面料在常温时具有较好的尺寸稳定性,热态下(170℃),可发生塑性形变,且塑性变形均匀、无撕裂、龟裂现象。因此可与热塑性发泡片材((tpe、xpe、eva等)复合成型,成型产品在改善了发泡片材表面强度的基础上,提升了产品的舒适性,可应用于嵌入式汽车地毯脚垫所需的新材料。
32.表2 本发明制备的热塑性静电植绒面料的热塑性研究应用实施例:利用实施例5~8制备的热塑性静电植绒面料制备绒面弹性复合材料:1)所需的材料:实施例5
‑
8制备的静电植绒面料;2)韧性发泡材料:其材料成分为xpe,材料密度0.25g/cm
³
,材料厚度5mm,材料硬度30a(邵氏硬度);3)针刺无纺布,材料成分为pet,规格为280g/
㎡
。
33.4)实施设备为火焰式复合机,实施工艺分两步进行:第一步发泡材料与针刺无纺
布复合,将发泡材料xpe通过火焰复合机将一面融化,然后将无纺布或毛刺布一起通过滚筒压合冷却得第一生产品,第二步将第一步得到的第一生产品与植绒面料复合,将第一生产品反面通过火焰复合机,将反面融化后与植绒面料通过滚筒压合,然后冷却得到成品;复合成型的绒面弹性复合材料在常温下有较好的尺寸稳定性,弹性伸长率为5%—8%,热态(150℃—170℃)下,塑性变形均匀、无撕裂、龟裂现象,可用于嵌入式汽车地毯脚垫所需的新材料。