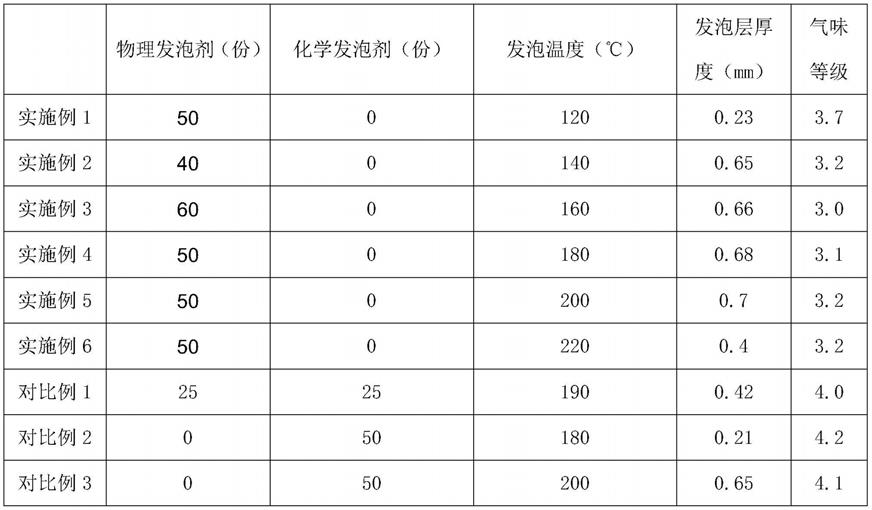
1.本发明涉及人造革制备领域,具体涉及一种新型物理发泡剂及其用途。
背景技术:2.随着国内汽车行业的发展,对于汽车内饰的材料需求也来越大。为了保护生态环境,促进人与自然和谐相处,汽车内饰逐渐使用人造革见图1取代真皮。随着生活质量的提高,人们在车辆的舒适性上,对人造革的气味要求也是越来越高。根据气味测试方法pv3900 c3气味等级达到4或以上,即有明显气味且让人感觉不适。
3.传统pvc人造革主要采用adc化学发泡的方式进行发泡,其主要发泡原料偶氮二甲酰胺在高温下分解产生气体,从而形成泡孔,见图2。此方法存在生产温度高,泡孔不均匀,pvc的手感偏硬,弹性低,舒适感差等局限性。
4.偶氮二甲酰胺在高温分解时会伴随副反应的发生,产生氨气存在于发泡层中。pvc人造革中残留有刺激性气味的物质(尿素,胺味等),在车内会持续的释放,影响乘客用车体验。
5.中国发明专利cn107574678公开了一种环保型发泡人造革及制备方法,通过将塑料颗粒、稳定剂和发泡剂等研磨后预热冲入气体形成气溶胶,然后平铺在离型纸上,在高温下穿过喷涂容器并且分解出气体形成发泡层,最后通过粘合剂和基布粘合制得发泡人造革。这种方法需要对发泡剂进行研磨,充气形成气溶胶,步骤较为繁琐。同时物理发泡剂是在高温下分解出气体形成泡孔,泡孔结构的规整性差,导致pvc人造革回弹性差。
技术实现要素:6.为解决现有技术存在的不足,本发明提供了一种新型物理发泡剂,通过使用该物理发泡剂,其在受热膨胀后,可以到达发泡的目的,泡孔均匀度较高,产品会弹效果好。同时使用本物理发泡剂制备的人造革,相比传统的adc发泡,大大降低了汽车内饰人造革的气味等级,满足了高度汽车对人造革气温等级的要求;使用此种发泡剂,发泡窗口更宽,降低了对发泡工艺的要求。
7.本发明的技术方案为:
8.一种新型发泡剂,包括新型物理发泡剂40
‑
60份、邻苯类增塑剂40
‑
60份,所述邻苯类增塑剂包括邻苯二甲酸二辛酯,邻苯二甲酸二丁酯,邻苯二甲酸二甲酯和邻苯二甲酸二异辛酯,所述新型物理发泡剂由热塑性树脂包裹烷烃类物质形成的壳核结构,整体粒径为20
‑
60μm,球体壁厚为2
‑
6μm。
9.优选地,所述壳核结构粒径为20μm,球体壁厚为2μm。
10.优选地,所述壳核结构粒径为60μm,球体壁厚为6μm。
11.优选地,所述壳核结构粒径为45μm,球体壁厚为4.5μm。
12.一种使用新型发泡剂制造的人造革,包括处理剂层、表皮层、新型发泡层、胶水粘结层和基布层,所述基布层上端涂有所述胶水层,所述胶水层上端设有所述pvc发泡层,所
述pvc发泡层上设有所述pvc表皮层,所述pvc表皮层上侧设有所述表面处理层,所述新型发泡层包括pvc粉80
‑
100份、增塑剂 50
‑
100份、热稳定剂1
‑
10份、阻燃剂1
‑
20份和新型发泡剂1
‑
20份。
13.优选地,所述新型发泡层包括pvc粉80份、增塑剂60份、热稳定剂2 份、阻燃剂6份和新型发泡剂6份。
14.优选地,所述新型发泡层包括pvc粉100份、增塑剂75份、热稳定剂 10份、阻燃剂5份和新型发泡剂3份。
15.优选地,所述新型发泡层包括pvc粉100份、增塑剂80份、热稳定剂10份、阻燃剂2份和新型发泡剂8份。
16.一种使用新型发泡剂制造的人造革的方法,包括:
17.表皮层制备:pvc粉,增塑剂,稳定剂,混合,在1000rpm条件下,分散搅拌10min,将搅拌好的浆液经过150目筛网过滤,之后在
‑
0.1mpa、300rpm 条件下真空脱泡搅拌1h,即得到表皮层浆料;
18.发泡层制备:pvc粉,增塑剂,钙锌类稳定剂,新型物理发泡剂,阻燃剂,混合,搅拌分散即得到发泡层浆料;
19.胶水层制备:pvc粉,增塑剂,钙锌类稳定剂,混合,在1200rpm条件下,分散搅拌30min,即得到胶水层浆料;
20.涂布:采用离型纸涂覆法,将表皮层、发泡层、胶水和基布按照顺序排布制备得到pvc人造革半成品;
21.印刷/压花:对pvc人造革半成品用表面处理剂进行涂覆,再经压花,即得到所述的常规车用人造革产品。
22.裁剪/入库:按照一定的门幅尺寸裁剪,即可得到合格的人造革成品。
23.本发明所达到的有益效果为:
24.本发明以新型发泡剂,以物理发泡的形式代替传统adc化学发泡的形式,使制备的人造革的泡孔更加均匀,制备的人造革的回弹性能也比较好,大大提高了人造革的性能;
25.使用新型发泡剂,可以明显扩大新型发泡剂的发泡工艺窗口,降低了工艺生产参数;
26.由于是使用物理发泡剂,可以明显降低人造革成品的气味等级,满足了高端车内饰对人造革的气味要求。
附图说明
27.图1是人造革的结构示意图。
28.图2是传统的化学发泡剂的发泡原理示意图。
29.图3是使用传统化学发泡剂制备的发泡层的剖面图。
30.图4是使用本发明中的发泡剂制备的发泡层的剖面图。
具体实施方式
31.为便于本领域的技术人员理解本发明,下面结合附图说明本发明的具体实施方式。
32.一种新型发泡剂,包括新型物理发泡剂40
‑
60份、邻苯类增塑剂40
‑
60份,所述邻苯类增塑剂包括邻苯二甲酸二辛酯,邻苯二甲酸二丁酯,邻苯二甲酸二甲酯和邻苯二甲酸二异辛酯,所述新型物理发泡剂由热塑性树脂包裹烷烃类物质形成的壳核结构,整体粒径为20
‑
60μm,球体壁厚为2
‑
6μm。
33.在本实施例中,所述壳核结构粒径为20μm,球体壁厚为2μm。
34.在本实施例中,所述壳核结构粒径为60μm,球体壁厚为6μm。
35.在本实施例中,所述壳核结构粒径为45μm,球体壁厚为4.5μm。
36.一种使用新型发泡剂制造的人造革,包括处理剂层、表皮层、新型发泡层、胶水粘结层和基布层,所述基布层上端涂有所述胶水层,所述胶水层上端设有所述pvc发泡层,所述pvc发泡层上设有所述pvc表皮层,所述pvc表皮层上侧设有所述表面处理层,所述新型发泡层包括pvc粉80
‑
100份、增塑剂 50
‑
100份、热稳定剂1
‑
10份、阻燃剂1
‑
20份和新型发泡剂1
‑
20份。
37.在本实施例中,所述新型发泡层包括pvc粉80份、增塑剂60份、热稳定剂2份、阻燃剂6份和新型发泡剂6份。
38.在本实施例中,所述新型发泡层包括pvc粉100份、增塑剂75份、热稳定剂10份、阻燃剂5份和新型发泡剂3份。
39.在本实施例中,所述新型发泡层包括pvc粉100份、增塑剂80份、热稳定剂10份、阻燃剂2份和新型发泡剂8份。
40.一种使用新型发泡剂制造的人造革的方法,包括:
41.表皮层制备:pvc粉,增塑剂,稳定剂,混合,在1000rpm条件下,分散搅拌10min,将搅拌好的浆液经过150目筛网过滤,之后在
‑
0.1mpa、300rpm 条件下真空脱泡搅拌1h,即得到表皮层浆料;
42.发泡层制备:pvc粉,增塑剂,钙锌类稳定剂,新型物理发泡剂,阻燃剂,混合,搅拌分散即得到发泡层浆料;
43.胶水层制备:pvc粉,增塑剂,钙锌类稳定剂,混合,在1200rpm条件下,分散搅拌30min,即得到胶水层;
44.涂布:采用离型纸涂覆法,将表皮层、发泡层、胶水和基布按照顺序排布制备得到pvc人造革半成品;
45.印刷/压花:对pvc人造革半成品用表面处理剂进行涂覆,再经压花,即得到所述的常规车用人造革产品。
46.裁剪/入库:按照一定的门幅尺寸裁剪,即可得到合格的人造革成品。
47.实施例1:
48.(1)新型发泡剂的预混:取新型物理发泡剂50份,邻苯二甲酸二辛酯50份,混合,在1000rpm条件下分散搅拌30min。搅拌结束后将浆液经过150目筛网过滤,即得到物理发泡剂浆料。
49.(2)物理发泡层浆料的制备:取pvc树脂粉80份、增塑剂邻苯二甲酸二辛酯 60份、阻燃剂硼酸锌2份、物理发泡剂浆料6份、热稳定剂硬脂酸钙6份,混合,在1000rpm条件下,分散搅拌10min;随后在1200rpm条件下分散搅拌30min;将搅拌好的浆液经过100目筛网过滤,即得到物理发泡层浆料。
50.(3)pvc人造革的制备:将混合好的表皮层、物理发泡层和胶水层依次涂布在离型纸上得到涂布半成品,其中物理发泡层发泡温度设置为120℃。再对pvc人造革半成品用表面处理剂进行印刷和压花,最终得到汽车内饰人造革成品。
51.实施例2:
52.(1)物理发泡剂的预混:取物理发泡剂40份,邻苯二甲酸二丁酯40份,混合,在1000rpm条件下分散搅拌30min。搅拌结束后将浆液经过150目筛网过滤,即得到物理发泡剂浆料。
53.(2)物理发泡层浆料的制备:取pvc树脂粉100份、增塑剂邻苯二甲酸二丁酯 75份、阻燃剂氢氧化铝10份、物理发泡剂浆料5份、热稳定剂硬脂酸锌3份,混合,在1000rpm条件下,分散搅拌10min;随后在1200rpm条件下分散搅拌 30min;将搅拌好的浆液经过100目筛网过滤,即得到物理发泡层浆料。
54.(3)pvc人造革的制备:将混合好的表皮层、发泡层和胶水层依次涂布在离型纸上得到涂布半成品,其中发泡层发泡温度设置为140℃。再对pvc人造革半成品用表面处理剂进行印刷和压花,最终得到汽车内饰人造革成品。
55.实施例3:
56.(1)物理发泡剂的预混:取物理发泡剂60份,邻苯二甲酸二甲酯60份,混合,在1000rpm条件下分散搅拌30min。搅拌结束后将浆液经过150目筛网过滤,即得到物理发泡剂浆料。
57.(2)物理发泡层浆料的制备:取pvc树脂粉100份、增塑剂邻苯二甲酸二甲酯 80份、阻燃剂三氧化二锑10份、物理发泡剂浆料2份、热稳定剂硬脂酸锌8份,混合,在1000rpm条件下,分散搅拌10min;随后在1200rpm条件下分散搅拌 30min;将搅拌好的浆液经过100目筛网过滤,即得到物理发泡层浆料。
58.(3)pvc人造革的制备:将混合好的表皮层、发泡层和胶水层依次涂布在离型纸上得到涂布半成品,其中发泡层发泡温度设置为160℃。再对pvc人造革半成品用表面处理剂进行印刷和压花,最终得到汽车内饰人造革成品。
59.实施例4:
60.(1)物理发泡剂的预混:取物理发泡剂50份,邻苯二甲酸二异辛酯50份,混合,在1000rpm条件下分散搅拌30min。搅拌结束后将浆液经过150目筛网过滤,即得到物理发泡剂浆料。
61.(2)物理发泡层浆料的制备:取pvc树脂粉100份、增塑剂邻苯二甲酸二异辛酯75份、阻燃剂氢氧化铝10份、物理发泡剂浆料4份、热稳定剂硬脂酸钙3 份,混合,在1000rpm条件下,分散搅拌10min;随后在1200rpm条件下分散搅拌30min;将搅拌好的浆液经过100目筛网过滤,即得到物理发泡层浆料。
62.(3)pvc人造革的制备:将混合好的表皮层、发泡层和胶水层依次涂布在离型纸上得到涂布半成品,其中发泡层发泡温度设置为180℃。再对pvc人造革半成品用表面处理剂进行印刷和压花,最终得到汽车内饰人造革成品。
63.实施例5:
64.(1)物理发泡剂的预混:取物理发泡剂50份,邻苯二甲酸二丁酯50份,混合,在1000rpm条件下分散搅拌30min。搅拌结束后将浆液经过150目筛网过滤,即得到物理发泡剂
浆料。
65.(2)物理发泡层浆料的制备:取pvc树脂粉100份、增塑剂邻苯二甲酸二丁酯 65份、阻燃剂三氧化二锑10份、物理发泡剂浆料3份、热稳定剂异辛酸锌3份,混合,在1000rpm条件下,分散搅拌10min;随后在1200rpm条件下分散搅拌 30min;将搅拌好的浆液经过100目筛网过滤,即得到物理发泡层浆料。
66.(3)pvc人造革的制备:将混合好的表皮层、发泡层和胶水层依次涂布在离型纸上得到涂布半成品,其中发泡层发泡温度设置为200℃。再对pvc人造革半成品用表面处理剂进行印刷和压花,最终得到汽车内饰人造革成品。
67.实施例6:
68.(1)物理发泡剂的预混:取物理发泡剂50份,邻苯二甲酸二丁酯50份,混合,在1000rpm条件下分散搅拌30min。搅拌结束后将浆液经过150目筛网过滤,即得到物理发泡剂浆料。
69.(2)物理发泡层浆料的制备:取pvc树脂粉100份、增塑剂邻苯二甲酸二丁酯 70份、阻燃剂硼酸锌10份、物理发泡剂浆料3份、热稳定剂异辛酸锌4份,混合,在1000rpm条件下,分散搅拌10min;随后在1200rpm条件下分散搅拌30min;将搅拌好的浆液经过100目筛网过滤,即得到物理发泡层浆料。
70.(3)pvc人造革的制备:将混合好的表皮层、发泡层和胶水层依次涂布在离型纸上得到涂布半成品,其中发泡层发泡温度设置为220℃。再对pvc人造革半成品用表面处理剂进行印刷和压花,最终得到汽车内饰人造革成品。
71.对比例1:
72.(1)发泡剂的预混:取物理发泡剂25份、偶氮二甲酰胺25份、邻苯二甲酸二丁酯50份,混合,在1000rpm条件下分散搅拌30min。搅拌结束后将浆液经过 150目筛网过滤,即得到发泡剂浆料。
73.(2)发泡层浆料的制备:取pvc树脂粉100份、增塑剂邻苯二甲酸二丁酯70 份、阻燃剂硼酸锌10份、发泡剂浆料4份、热稳定剂硬脂酸钙3份,混合,在 1000rpm条件下,分散搅拌10min;随后在1200rpm条件下分散搅拌30min;将搅拌好的浆液经过100目筛网过滤,即得到发泡层浆料。
74.(3)pvc人造革的制备:将混合好的表皮层、发泡层和胶水层依次涂布在离型纸上得到涂布半成品,其中发泡层烘烤温度设置为190℃。再对pvc人造革半成品用表面处理剂进行印刷和压花,最终得到汽车内饰人造革成品。
75.对比例2:
76.(1)化学发泡剂的预混:偶氮二甲酰胺50份、邻苯二甲酸二甲酯50份,混合,在1000rpm条件下分散搅拌30min。搅拌结束后将浆液经过150目筛网过滤,即得到物理发泡剂浆料。
77.(2)化学发泡层浆料的制备:取pvc树脂粉100份、增塑剂邻苯二甲酸二甲酯 70份、阻燃剂三氧化二锑10份、化学发泡剂浆料4份、热稳定剂硬脂酸锌3份,混合,在1000rpm条件下,分散搅拌10min;随后在1200rpm条件下分散搅拌 30min;将搅拌好的浆液经过100目筛网过滤,即得到化学发泡层浆料。
78.(3)pvc人造革的制备:将混合好的表皮层、发泡层和胶水层依次涂布在离型纸上
得到涂布半成品,其中发泡层烘烤温度设置为180℃。再对pvc人造革半成品用表面处理剂进行印刷和压花,最终得到汽车内饰人造革成品。
79.对比例3:
80.(1)化学发泡剂的预混:偶氮二甲酰胺50份、邻苯二甲酸二甲酯50份,混合,在1000rpm条件下分散搅拌30min。搅拌结束后将浆液经过150目筛网过滤,即得到物理发泡剂浆料。
81.(2)化学发泡层浆料的制备:取pvc树脂粉100份、增塑剂邻苯二甲酸二甲酯 70份、阻燃剂三氧化二锑10份、化学发泡剂浆料4份、热稳定剂硬脂酸锌3份,混合,在1000rpm条件下,分散搅拌10min;随后在1200rpm条件下分散搅拌 30min;将搅拌好的浆液经过100目筛网过滤,即得到化学发泡层浆料。
82.(3)pvc人造革的制备:将混合好的表皮层、发泡层和胶水层依次涂布在离型纸上得到涂布半成品,其中发泡层烘烤温度设置为200℃。再对pvc人造革半成品用表面处理剂进行印刷和压花,最终得到汽车内饰人造革成品。
83.性能测试与评价:
84.1.厚度测试
85.采用游标卡尺对实施例和对比例中的产品进行厚度测量。
86.2.气味等级测试
87.按照德国大众公司的pv3900标准对实施例和对比例中的产品进行气味等级测试。
88.通过上述实施例和对比例得到的pvc人造革,经过上述测试,结果如表 1.
89.表1为各种pvc发泡组分配比发泡温度及测试结果
[0090][0091]
由表1的测试结果可以看出,本发明的配料对发泡温度和pvc人造革气味的影响。比较实施例3
‑
4和对比例3,可以看出,使用新型物理发泡剂能够有效降低pvc人造革的气味等级,说明使用本发明的物理发泡剂制备的人造革在降低气味方面效果明显。相较于化学发泡剂热分解产生气体形成泡孔,会伴随着氨气等刺激性气体的产生,物理发泡剂能够有效克服这一弊端。
[0092]
比较实施例1
‑
6和对比例1
‑
3,可以看出,相较于化学发泡剂较高的发泡温度(200℃),物理发泡温度在140~200℃范围内均可到达同样的发泡厚度,物理发泡剂温蒂更低,发泡范围更宽,降低了发泡的生产工艺要求。
[0093]
比较实施例3和对比例3,结合图3和图4可以看出,物理发泡的泡孔比化学发泡的泡孔更加均匀,规整性好。物理新型物理发泡剂在热时,热塑性树脂逐步软化,烷烃类物质受热分解释放出气体,热塑性树脂逐渐膨胀变大,起到发泡的作用,当受热一定时间后,由于气体的持续释放,热塑性树脂壳体被撑破,降温后泡孔成型。由于热塑性树脂和烷烃类的物质分量比较固定,因此发泡时形成的泡孔尺寸也就比较均匀。而化学发泡的泡孔大小不一,规整性较差,影响人造革的恢复能力。
[0094]
以上所述的本发明实施方式,并不构成对本发明保护范围的限定。任何在本发明的精神和原则之内所作的修改、等同替换和改进等,均应包含在本发明的权利要求保护范围之内。