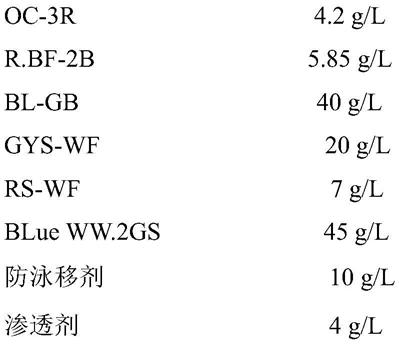
1.本发明涉及一种涤棉深色织物分散/活性染料一浴法染色工艺,属于纺织印染技术领域。
背景技术:2.随着科学技术的迅速发展,人类生活水平的不断提高,特别是生态环境保护受到了前所未有的重视。印染行业中,通过节水节能、降耗减排,减少对环境的污染,成了各企业的当务之急。
3.现涤棉深色面料采用活性/分散两浴法进行染色,该染色技术工艺流程长、生产效率低、水电汽等能耗大、生产成本高。在当前提倡节能减排、绿色制造的形式下,研究涤棉一浴法染色,实现涤棉面料的短流程连续染色加工,对于降低涤棉染色订单成本、提升生产效率和引领市场具有重要意义。
4.近年来,很多印染企业都在尝试深色涤棉面料的涤棉一浴染色法来代替涤棉两浴染色法,但都因为涤棉一浴染色法的染色牢度达不到要求、织物得色量低等问题得不到有效解决而放弃。
5.专利cn101392462a公开了一种涤棉织物分散、活性染料一浴特深染色工艺,其工艺选用ww系列分散染料和c系列活性染料,将纯棉织物放入染液中浸一次,然后用轧车轧一次,轧后预烘,预烘后焙烘,然后在汽蒸箱内汽蒸,汽蒸后水洗,水洗后皂洗,再经水洗、烘干,完成染色。该染色工艺对所用的染料为特定的染料,具有一定的局限性。
技术实现要素:6.本发明的目的是克服现有技术的不足,提供一种涤棉深色织物分散/活性染料一浴法染色工艺,其设计科学合理,工艺流程简单,生产稳定,有效降低涤棉染色面料的生产成本,染色牢度及深度高。
7.本发明所述的涤棉深色织物分散/活性染料一浴法染色工艺的制备方法,具体包括以下步骤:
8.将已经加工完前处理的织物浸轧染液
→
烘干
→
高温焙烘
→
浸轧固色液
→
汽蒸
→
清水洗
→
还原清洗剂清洗
→
皂洗
→
烘干。
9.使用还原清洗剂清洗时,溶液组成优选为:还原清洗剂gin:8~10g/l、naoh:2.5~3.5g/l,其余为水。
10.所述的还原清洗剂gin为一种不含硫、环保、具有分散功能的液体还原清洗剂。
11.使用还原清洗剂清洗时,优选的,溶液的ph值为8~9,水洗槽温度为90~95℃。
12.活性固色时高温皂洗时皂洗溶液优选为:皂洗剂isopon rss liq new:2~3g/l,其余为水。
13.所采用的皂洗剂isopon rss liq new为一种高浓分散防沾剂皂洗剂。
14.其中,优选的材料如下:
15.所述还原清洗剂redulit gin,上海佳和化学有限公司市售产品。
16.所述皂洗剂isopon rss liq new,天津市弘力元工贸有限公司市售产品。
17.本发明与现有技术相比,具有以下有益效果:
18.(1)本发明采用在活性固色时的水洗槽中加入还原清洗剂gin和naoh,在溶液ph值为8~9,温度为90~95℃的条件下,还原清洗剂gin所产生的氧化还原电位足以破坏大多数分散染料,但不足以破坏许多活性染料,在其较强的分散能力下,纤维表面吸附的未固着的分散染料被破坏后,其降解产物会被很好的分散在处理浴中,不会回沾在布面上,从而使织物获得更好的牢度;
19.(2)本发明活性固色的皂洗采用高浓分散防沾皂洗剂,能够有效去除未固着的染料,即使在染色中使用的盐类仍有一部分残留时,也能十分有效地去除浮色,使织物的牢度得到进一步的提升;
20.(3)本发明省略了轧干染色和分散固色两道流程,大大减少了废水的排放,实现了节能减排,环保降耗的目的。
具体实施方式
21.以下结合实施例对本发明作进一步描述。
22.实施例中用到的所有原料除特殊说明外,均为市购。
23.实施例1
24.采用涤棉混纺为原料,组织规格:cvc21*cvc21*118*58*58/59,织物组织:3/1s,具体工艺如下:
25.(1)织物预处理:将坯布依次经过烧毛、冷堆、煮练、漂白、干定型、丝光后,进行染色;
26.(2)浸轧染液:
27.染液配方:
[0028][0029][0030]
将染料溶于水并配制成染液,在均匀轧车上浸轧染液,浸轧染液后烘干。
[0031]
(3)高温焙烘:烘房温度:210℃,风量80%,焙烘时间:1.5min。
[0032]
(4)浸轧固色液:轧槽内轧液由烧碱、纯碱、元明粉、抗还原剂、渗透剂溶入水而成,其中烧碱10g/l,纯碱30g/l,元明粉225g/l,抗还原剂防染盐2g/l,渗透剂2g/l,轧液率62%。
2007,移染:日本大丸色泣法,耐酸汗渍色牢度:aatcc 15-2009。
[0052]
表1实施例1和对比例1的结果对比
[0053]
类型皂洗摩擦移染汗渍实施例1变色4级,沾色4级干摩4级,湿摩3级4级变色4级,沾色4.5级对比例1变色4级,沾色3级干摩4级,湿摩2.5级4级变色4级,沾色4级
[0054]
实施例1较对比例1,皂洗沾色高0.5级,湿摩擦牢度高0.5级,汗渍沾色高0.5级。充分说明本发明工艺处理后的面料,牢度明显提高。
[0055]
对比例2
[0056]
采用涤棉混纺为原料,组织规格:cvc21*cvc21*118*58*58/59,织物组织:3/1s,具体工艺如下:
[0057]
(1)织物预处理:将坯布依次经过烧毛、冷堆、煮练、漂白、干定型、丝光后,进行染色,具体步骤同实施例1;
[0058]
(2)浸轧分散染料染液
[0059]
染液配方:
[0060][0061][0062]
将染料溶于水并配制成染液,在均匀轧车上浸轧染液,浸轧染液后烘干。
[0063]
(3)高温焙烘:烘房温度:210℃,风量80%,焙烘时间:1.5min。
[0064]
(4)分散固色:轧槽内轧液由烧碱、剥色剂溶入水而成,其中烧碱:40g/l,剥色剂fn:40g/l,轧液率65%。
[0065]
(5)浸轧活性染料染液
[0066]
染液配方:
[0067][0068]
将染料溶于水并配制成染液,在均匀轧车上浸轧染液,浸轧染液后烘干。
[0069]
(6)浸轧固色液:轧槽内轧液由烧碱、纯碱、元明粉、抗还原剂、渗透剂溶入水而成,其中烧碱10g/l,纯碱30g/l,元明粉225g/l,抗还原剂防染盐2g/l,渗透剂2g/l,轧液率62%。
[0070]
(7)汽蒸:100℃*60s。
[0071]
(8)皂洗:7#8#9#水洗槽为皂洗剂溶液,其组成为皂洗剂raytexil wo-n:3g/l,其余为水,水洗槽温度95℃,烘干,完成染色。
[0072]
采用此工艺染成的织物色牢度为:皂洗变色4级,沾色4级,干摩4级,湿摩3级,移染4级,耐酸汗渍变色4级,沾色4.5级。
[0073]
注:色牢度测试方法:耐洗色牢度:aatcc 61-2010 2a,耐摩擦色牢度:aatcc 8-2007,移染:日本大丸色泣法,耐酸汗渍色牢度:aatcc 15-2009。
[0074]
表2实施例1和对比例2的结果对比
[0075]
类型皂洗摩擦移染汗渍实施例1变色4级,沾色4级干摩4级,湿摩3级4级变色4级,沾色4.5级对比例2变色4级,沾色4级干摩4级,湿摩3级4级变色4级,沾色4.5级
[0076]
实施例1较对比例2,各项牢度相当,充分说明本发明所采用的涤棉一浴染色工艺处理后的面料,牢度可以达到涤棉两浴染色工艺的水平,同时本发明所采用的工艺省略了轧干染色和分散固色两道流程,大大减少了废水的排放,实现了节能减排,环保降耗的目的。
[0077]
实施例2
[0078]
采用涤棉混纺为原料,组织规格:t/c45*t/c45*116*76*58/59,织物组织:1/1平纹,具体工艺如下:
[0079]
(1)织物预处理:将坯布依次经过烧毛、退浆、煮练、干定型、漂白、丝光;
[0080]
(2)浸轧染液:
[0081]
染液配方:
[0082][0083]
将染料溶于水并配制成染液,在均匀轧车上浸轧染液,浸轧染液后烘干。
[0084]
(3)高温焙烘:烘房温度:210℃,风量80%,焙烘时间:1.5min。
[0085]
(4)浸轧固色液:轧槽内轧液由烧碱、纯碱、元明粉、抗还原剂、渗透剂溶入水而成,其中烧碱10g/l,纯碱30g/l,元明粉225g/l,抗还原剂防染盐2g/l,渗透剂2g/l,轧液率62%。
[0086]
(5)汽蒸:100℃*60s。
[0087]
(6)还原清洗剂清洗:共12节水洗槽,3#4#水洗槽为还原清洗剂溶液,其组成为还原清洗剂gin:10g/l、naoh:2.8g/l,其余为水,水洗槽ph值为8.2,温度为90℃;
[0088]
(7)皂洗:7#8#9#水洗槽为皂洗剂溶液,其组成为高浓分散防沾剂isopon rss liq new:3g/l,其余为水,水洗槽温度95℃。
[0089]
采用此工艺染成的织物色牢度为:皂洗变色4级,沾色4级,干摩4级,湿摩3级,移染
4.5级,耐酸汗渍变色4.5级,沾色4.5级,耐碱汗渍变色4.5级,沾色4.5级。
[0090]
注:色牢度测试方法:耐洗色牢度:gb/t 3921-2008,耐摩擦色牢度:gb/t 3920-2008,移染:日本大丸色泣法,耐酸汗渍色牢度:gb/t 3922-1995,耐碱汗渍色牢度:gb/t 3922-1995。
[0091]
对比例3
[0092]
采用涤棉混纺为原料,组织规格:t/c45*t/c45*116*76*58/59,织物组织:1/1平纹,具体工艺如下:
[0093]
(1)织物预处理:将坯布依次经过烧毛、退浆、煮练、干定型、漂白、丝光,进行染色,具体步骤同实施例2;
[0094]
(2)浸轧染液:
[0095]
染液配方:
[0096][0097]
将染料溶于水并配制成染液,在均匀轧车上浸轧染液,浸轧染液后烘干。
[0098]
(3)高温焙烘:烘房温度:210℃,风量80%,焙烘时间:1.5min。
[0099]
(4)浸轧固色液:轧槽内轧液由烧碱、纯碱、元明粉、抗还原剂、渗透剂溶入水而成,其中烧碱10g/l,纯碱30g/l,元明粉225g/l,抗还原剂防染盐2g/l,渗透剂2g/l,轧液率65%。
[0100]
(5)汽蒸:100℃*60s。
[0101]
(6)还原清洗剂清洗:共12节水洗槽,3#4#水洗槽为还原清洗剂溶液,其组成为还原清洗剂gin:10g/l、naoh:2.8g/l,其余为水,水洗槽ph值为8.2,温度为90℃;
[0102]
(7)皂洗:7#8#9#水洗槽为皂洗剂溶液,其组成为raytexil wo-n:3g/l,其余为水,水洗槽温度95℃。
[0103]
采用此工艺染成的织物色牢度为:皂洗变色4级,沾色3级,干摩4级,湿摩2.5级,移染4级,耐酸汗渍变色4.5级,沾色4级,耐碱汗渍变色4.5级,沾色4级。
[0104]
注:色牢度测试方法:耐洗色牢度:gb/t 3921-2008,耐摩擦色牢度:gb/t 3920-2008,移染:日本大丸色泣法,耐酸汗渍色牢度:gb/t 3922-1995,耐碱汗渍色牢度:gb/t 3922-1995。
[0105]
表3实施例2和对比例3的结果对比
[0106][0107][0108]
实施例2较对比例3,皂洗沾色高1级,湿摩擦牢度高0.5级,耐酸汗渍沾色高0.5级,耐碱汗渍沾色高0.5级。充分说明本发明工艺处理后的面料,牢度明显提高。
[0109]
对比例4
[0110]
采用涤棉混纺为原料,组织规格:t/c45*t/c45*116*76*58/59,织物组织:1/1平纹,具体工艺如下:
[0111]
(1)织物预处理:将坯布依次经过烧毛、退浆、煮练、干定型、漂白、丝光,进行染色,具体步骤同实施例2;
[0112]
(2)浸轧分散染料染液
[0113]
染液配方:
[0114][0115]
将染料溶于水并配制成染液,在均匀轧车上浸轧染液,浸轧染液后烘干。
[0116]
(3)高温焙烘:烘房温度:210℃,风量80%,焙烘时间:1.5min。
[0117]
(4)分散固色:轧槽内轧液由烧碱、剥色剂溶入水而成,其中烧碱:40g/l,剥色剂fn:40g/l,轧液率65%。
[0118]
(5)浸轧活性染料染液
[0119]
染液配方:
[0120][0121]
将染料溶于水并配制成染液,在均匀轧车上浸轧染液,浸轧染液后烘干。
[0122]
(6)浸轧固色液:轧槽内轧液由烧碱、纯碱、元明粉、抗还原剂、渗透剂溶入水而成,其中烧碱10g/l,纯碱30g/l,元明粉225g/l,抗还原剂防染盐2g/l,渗透剂2g/l,轧液率65%。
[0123]
(7)汽蒸:100℃*60s。
[0124]
(8)皂洗:7#8#9#水洗槽为皂洗剂溶液,其组成为皂洗剂raytexil wo-n:3g/l,其余为水,水洗槽温度95℃,烘干,完成染色。
[0125]
采用此工艺染成的织物色牢度为:皂洗变色4级,沾色4级,干摩4级,湿摩3级,移染4.5级,耐酸汗渍变色4级,沾色4.5级,耐碱汗渍变色4级,沾色4.5级。
[0126]
注:色牢度测试方法:耐洗色牢度:gb/t 3921-2008,耐摩擦色牢度:gb/t 3920-2008,移染:日本大丸色泣法,耐酸汗渍色牢度:gb/t 3922-1995,耐碱汗渍色牢度:gb/t 3922-1995。
[0127]
表4实施例2和对比例4的结果对比
[0128][0129]
实施例2较对比例4,各项牢度相当,充分说明本发明所采用的涤棉一浴染色工艺处理后的面料,牢度可以达到涤棉两浴染色工艺的水平,同时本发明所采用的工艺省略了轧干染色和分散固色两道流程,大大减少了废水的排放,实现了节能减排,环保降耗的目的。
[0130]
实施例3
[0131]
采用涤棉混纺为原料,组织规格:t/c33/2*t/c33/2*97*56*61/62,织物组织:1/1+2并格子,具体工艺如下:
[0132]
(1)织物预处理:将坯布依次经过烧毛、退浆、煮练、干定型、漂白、丝光;
[0133]
(2)浸轧染液:
[0134]
染液配方:
[0135][0136][0137]
将染料溶于水并配制成染液,在均匀轧车上浸轧染液,浸轧染液后烘干。
[0138]
(3)高温焙烘:烘房温度:210℃,风量80%,焙烘时间:1.5min。
[0139]
(4)浸轧固色液:轧槽内轧液由烧碱、纯碱、元明粉、抗还原剂、渗透剂溶入水而成,其中烧碱10g/l,纯碱30g/l,元明粉225g/l,抗还原剂防染盐2g/l,渗透剂2g/l,轧液率65%。
[0140]
(5)汽蒸:100℃*60s。
[0141]
(6)还原清洗剂清洗:共12节水洗槽,3#4#水洗槽为还原清洗剂溶液,其组成为还原清洗剂gin:8g/l、naoh:3g/l,其余为水,水洗槽ph值为8,温度为95℃;
[0142]
(7)皂洗:7#8#9#水洗槽为皂洗剂溶液,其组成为高浓分散防沾剂isopon rss liq new:2g/l,其余为水,水洗槽温度95℃。
[0143]
采用此工艺染成的织物色牢度为:皂洗变色4级,沾色4级,干摩4级,湿摩3级,移染4级,耐酸汗渍变色4.5级,沾色4.5级,耐碱汗渍变色4.5级,沾色4.5级。
[0144]
注:色牢度测试方法:耐洗色牢度:jis l 0844:2011,耐摩擦色牢度:jis l 0849:2013,移染:日本大丸色泣法,耐酸汗渍色牢度:jis l 0848:2004,耐碱汗渍色牢度:jis l 0848:2004。
[0145]
对比例5
[0146]
采用涤棉混纺为原料,组织规格:t/c33/2*t/c33/2*97*56*61/62,织物组织:1/1+2并格子,具体工艺如下:
[0147]
(1)织物预处理:将坯布依次经过烧毛、退浆、煮练、干定型、漂白、丝光;
[0148]
(2)浸轧染液:
[0149]
染液配方:
[0150][0151]
将染料溶于水并配制成染液,在均匀轧车上浸轧染液,浸轧染液后烘干。
[0152]
(3)高温焙烘:烘房温度:210℃,风量80%,焙烘时间:1.5min。
[0153]
(4)浸轧固色液:轧槽内轧液由烧碱、纯碱、元明粉、抗还原剂、渗透剂溶入水而成,其中烧碱10g/l,纯碱30g/l,元明粉225g/l,抗还原剂防染盐2g/l,渗透剂2g/l,轧液率65%。
[0154]
(5)汽蒸:100℃*60s。
[0155]
(6)还原清洗剂清洗:共12节水洗槽,3#4#水洗槽为还原清洗剂溶液,其组成为还原清洗剂gin:8g/l、naoh:3g/l,其余为水,水洗槽ph值为8,温度为70℃;
[0156]
(7)皂洗:7#8#9#水洗槽为皂洗剂溶液,其组成为高浓分散防沾剂isopon rss liq new:2g/l,其余为水,水洗槽温度95℃。
[0157]
采用此工艺染成的织物色牢度为:皂洗变色4级,沾色3级,干摩4级,湿摩2.5级,移染3.5级,耐酸汗渍变色4.5级,沾色3.5级,耐碱汗渍变色4.5级,沾色3.5级,。
[0158]
注:色牢度测试方法:耐洗色牢度:jis l 0844:2011,耐摩擦色牢度:jis l 0849:2013,移染:日本大丸色泣法,耐酸汗渍色牢度:jis l 0848:2004,耐碱汗渍色牢度:jis l 0848:2004。
[0159]
表5实施例3和对比例5的结果对比
[0160][0161]
实施例3较对比例5,皂洗沾色高1级,湿摩擦牢度高0.5级,移染高0.5级,耐酸汗渍沾色高1级,耐碱汗渍沾色高1级。充分说明本发明工艺处理后的面料,牢度明显提高。
[0162]
对比例6
[0163]
采用涤棉混纺为原料,组织规格:t/c33/2*t/c33/2*97*56*61/62,织物组织:1/1+2并格子,具体工艺如下:
[0164]
(1)织物预处理:将坯布依次经过烧毛、退浆、煮练、干定型、漂白、丝光;
[0165]
(2)浸轧染液:
[0166]
染液配方:
[0167][0168]
将染料溶于水并配制成染液,在均匀轧车上浸轧染液,浸轧染液后烘干。
[0169]
(3)高温焙烘:烘房温度:210℃,风量80%,焙烘时间:1.5min。
[0170]
(4)分散固色:轧槽内轧液由烧碱、剥色剂溶入水而成,其中烧碱:40g/l,剥色剂fn:40g/l,轧液率65%。
[0171]
(5)浸轧活性染料染液
[0172]
染液配方:
[0173][0174]
将染料溶于水并配制成染液,在均匀轧车上浸轧染液,浸轧染液后烘干。
[0175]
(6)浸轧固色液:轧槽内轧液由烧碱、纯碱、元明粉、抗还原剂、渗透剂溶入水而成,其中烧碱10g/l,纯碱30g/l,元明粉225g/l,抗还原剂防染盐2g/l,渗透剂2g/l,轧液率65%。
[0176]
(5)汽蒸:100℃*60s。
[0177]
(7)皂洗:7#8#9#水洗槽为皂洗剂溶液,其组成为皂洗剂raytexil wo-n:3g/l,其
余为水,水洗槽温度95℃。
[0178]
采用此工艺染成的织物色牢度为:皂洗变色4级,沾色4级,干摩4级,湿摩3级,移染4级,耐酸汗渍变色4.5级,沾色4.5级,耐碱汗渍变色4.5级,沾色4.5级,。
[0179]
注:色牢度测试方法:耐洗色牢度:jis l 0844:2011,耐摩擦色牢度:jis l 0849:2013,移染:日本大丸色泣法,耐酸汗渍色牢度:jis l 0848:2004,耐碱汗渍色牢度:jis l 0848:2004。
[0180]
表6实施例3和对比例6的结果对比
[0181][0182]
实施例3较对比例6,各项牢度相当,充分说明本发明所采用的涤棉一浴染色工艺处理后的面料,牢度可以达到涤棉两浴染色工艺的水平,同时本发明所采用的工艺省略了轧干染色和分散固色两道流程,大大减少了废水的排放,实现了节能减排,环保降耗的目的。