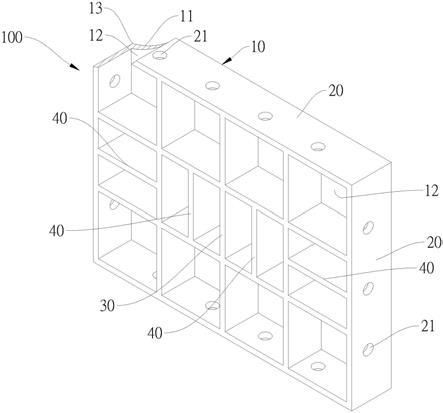
1.本实用新型是有关于一种碳纤维材料的技术领域,特别是有关于一种碳纤维模板及其制造系统。
背景技术:2.在各种营建工程中,完成钢筋结构之后,接着在钢筋结构的外部进行混凝土的灌浆作业,而混凝土的定型是预先在钢筋结构外部建构模板,模板建构出的形状对应于建筑物中各种结构,然后混凝土灌入模板,最后混凝土凝固成型。
3.在现有技术中,模板有用木材或钢材等制作,木材虽然容易裁切,但是有一定的使用寿命,而钢材虽然使用寿命长,但是其不易裁切而且重量较重,因此组装相当不容易且组装速度慢,而且回收性差及重制速度慢。
技术实现要素:4.有鉴于此,本实用新型所要解决的技术问题在于:提供一种碳纤维制作的模板,其兼具质轻极容易裁切的特性,而且组装速度快,以及回收重制速度快。
5.本实用新型所采用的技术手段如下。本实用新型的碳纤维模板包括一板体、复数个突缘以及复数个加强肋。该板体具有一第一表面、一第二表面以及复数个侧边,该第一表面与该第二表面相对设置,该侧边连接该第一表面与该第二表面。复数个突缘,连接于该侧边,且从该第一表面朝该第二表面的方向延伸。复数个加强肋,设置在该第二表面且连接于该突缘。其中,该板体、该突缘及该加强肋是以一碳纤维复合材料制成。
6.在另一实施例中,该碳纤维复合材料是由复数根碳纤维分布于热可塑性树脂所构成的一热塑性基材中所构成。
7.在另一实施例中,该碳纤维复合材料是由复数根该碳纤维与复数根热可塑性纤维彼此相互缠绕成无方向性分布的一碳纤维复合材料预成型体,之后再将该碳纤维复合材料预成型体经由热压所构成该碳纤维复合材料。
8.在另一实施例中,复数根该热可塑性纤维是全部热熔形变彼此粘合而构成该热塑性基材,或者复数根该热可塑性纤维是只有一部分该热可塑性纤维热熔形变与另一部分维持纤维形状的该热可塑性纤维彼此粘合而构成该热塑性基材。
9.在另一实施例中,其中所述无方向性分布是为将该碳纤维复合材料或该碳纤维复合材料预成型体投影于一个二维平面,而复数根该碳纤维于该二维平面上的投影是杂乱或随机地以各方向延伸,该碳纤维是不连续的碳纤维,复数根该碳纤维的平均长度是大于或等于35mm,且小于或等于95mm,该碳纤维为二次回收的碳纤维。
10.在另一实施例中,复数根该热可塑性纤维于该二维平面上的投影是杂乱或随机地以各方向延伸,该热可塑性纤维是不连续的热可塑性纤维,复数根该热可塑性纤维的平均长度是大于或等于35mm,且小于或等于 95mm。
11.在另一实施例中,该碳纤维复合材料是包含复数个空腔,复数个该空腔是以杂乱
或随机地分布于该碳纤维复合材料内部,该空腔的内部为空气。
12.在另一实施例中,每个该突缘设有复数个通孔,该通孔是沿与该侧边平行的方向排列。
13.在另一实施例中,每个该突缘的该通孔具有相同的孔径且该通孔间具有相同的间距。
14.在另一实施例中,至少一个该加强肋与至少一个该突缘平行。
15.在另一实施例中,该加强肋的末端以该第二表面为基准面的高度是等于该突缘的末端以该第二表面为基准面的高度。
16.在另一实施例中,该碳纤维模板更包括复数个辅助加强肋,该辅助加强肋设置于该加强肋与该突缘之间且连接该加强肋与该突缘,且该辅助加强肋的末端以该第二表面为基准面的高度是小于该加强肋的末端以该第二表面为基准面的高度。
17.本实用新型也提供一种碳纤维模板的制造系统,其至少包括:一碳纤维开纤机、一热塑性纤维开纤机、一叠合机、一混纤机以及一热压成型机。该碳纤维开纤机以一碳纤维输送装置连接该叠合机;该热塑性纤维开纤机以一热塑性纤维输送装置连接该叠合机;该叠合机以一叠合输送装置连接该混纤机;该混纤机以一混纤输送装置连接该热压成型机。
18.在另一实施例中,该碳纤维开纤机将复数个碳纤维束中的复数根碳纤维彼此分散,将分散的复数根该碳纤维散布于该碳纤维开纤机的该碳纤维输送装置上使复数根该碳纤维彼此相互缠绕成无方向性分布的一碳纤维带状物。
19.在另一实施例中,该热塑性纤维开纤机将复数个热塑性纤维束中的复数根热可塑性纤维彼此分散,将分散的复数根该热可塑性纤维散布于该热塑性纤维开纤机的该热塑性纤维输送装置上使复数根该热可塑性纤维彼此相互缠绕成无方向性分布的一热塑性纤维带状物。
20.在另一实施例中,该叠合机是将该碳纤维带状物及该热塑性纤维带状物彼此叠置成一预混纤带状物;该叠合机是将该碳纤维带状物叠于该热塑性纤维带状物的上方,或者将该热塑性纤维带状物叠于该碳纤维带状物的上方。
21.在另一实施例中,该混纤机将该预混纤带状物中的复数根该碳纤维及复数根该热可塑性纤维混合彼此分散,将分散的复数根该碳纤维及复数根该热可塑性纤维散布于该混纤机的输送带上使其彼此相互缠绕成无方向性分布的一混纤带状物。
22.在另一实施例中,该混纤带状物的厚度方向的下半部,该碳纤维的重量或数量比例大于该热可塑性纤维。
23.在另一实施例中,该热压成型机将该混纤带状物经过热压而成为一预成型体。
24.在另一实施例中,该碳纤维模板的制造系统包含一裁切机,该热压成型机以一热压成型输送装置连接该裁切机,该裁切机将该预成型体裁切成预定的尺寸。
25.在另一实施例中,该碳纤维模板的制造系统包含一成品机,该裁切机以一裁切输送装置连接该成品机,该成品机在该预成型体设置一突缘与一加强肋。
26.在另一实施例中,该混纤机与该热压成型机之间设置有一针轧机。
27.本实用新型也提供一种碳纤维模板的制造方法,其至少包括以下步骤:一提供碳纤维回收材料步骤,是提供成束的碳纤维;一提供热塑性纤维步骤,是提供成束的热塑性纤维;一碳纤维开纤步骤,将成束的碳纤维进行开纤,即形成复数根可交错缠绕的碳纤维;一
热塑性纤维开纤步骤,将成束的热塑性纤维进行开纤,即形成复数根可交错缠绕的热可塑性纤维;一叠合步骤,将已开纤的复数根该碳纤维及复数根该热可塑性纤维进行叠合;一混纤步骤,将叠合后的复数根该碳纤维与复数根该热可塑性纤维混织;一预成型步骤,将完成混纤后的复数根该碳纤维及复数根该热可塑性纤维进行预成型。
28.在另一实施例中,该提供碳纤维回收材料步骤中,所述成束的碳纤维是指从高分子复合材料中所取得的二次回收的复数个碳纤维束,该碳纤维束是由复数根碳纤维捻在一起所构成。
29.在另一实施例中,该提供热塑性纤维步骤中,所述成束的热塑性纤维是指由复数根热可塑性纤维捻在一起所构成的复数个热可塑性纤维束。
30.在另一实施例中,该碳纤维开纤步骤中,将复数个该碳纤维束中的复数根该碳纤维彼此分散,将分散的复数根该碳纤维散布并使其彼此相互缠绕成无方向性分布的一碳纤维带状物;该碳纤维是不连续的碳纤维。
31.在另一实施例中,该热塑性纤维开纤步骤中,将复数个该热塑性纤维束中的复数根该热可塑性纤维彼此分散,将分散的复数根该热可塑性纤维散布并使其彼此相互缠绕成无方向性分布的一热塑性纤维带状物;该热可塑性纤维是不连续的热可塑性纤维。
32.在另一实施例中,该叠合步骤中,是将该碳纤维带状物及该热塑性纤维带状物彼此叠置成一预混纤带状物;该碳纤维带状物叠于该热塑性纤维带状物的上方,或者该热塑性纤维带状物叠于该碳纤维带状物的上方。
33.在另一实施例中,该混纤步骤中,将该预混纤带状物中的复数根该碳纤维及复数根该热可塑性纤维混合彼此分散,将分散的复数根该碳纤维及复数根该热可塑性纤维散布并使其彼此相互缠绕成无方向性分布的一混纤带状物。
34.在另一实施例中,该混纤带状物的厚度方向的下半部,该碳纤维的重量或数量比例大于该热可塑性纤维。
35.在另一实施例中,该预成型步骤依序包含一针轧步骤及一热压步骤,该针轧步骤是使该混纤带状物中的复数根该碳纤维及复数根该热可塑性纤维彼此相互缠绕,该热压步骤是使经过针轧后的该混纤带状物经过热压而成为一预成型体。
36.在另一实施例中,该预成型步骤包含一热压步骤,热压步骤将该混纤带状物经过热压而成为一预成型体。
37.在另一实施例中,该预成型步骤包含一热压成卷步骤,该热压成卷步骤将该混纤带状物经过热压后再收卷而成为一预成型体。
38.在另一实施例中,该碳纤维模板的制造方法更包含一裁切步骤,该裁切步骤是将该预成型体裁切成预定的尺寸而成为一板体。
39.在另一实施例中,该碳纤维模板的制造方法更包含一成品步骤,该成品步骤是在该板体上设置一突缘与一加强肋之后,再加热进行热熔粘合而得到一碳纤维模板。
40.本实用新型的有益效果如下:本实用新型的碳纤维模板,其碳纤维板材是由碳纤维相互缠绕地分布在热塑性基材中,使碳纤维模板具有相当的强度,而且其重量轻且方便裁切。另外本实用新型的碳纤维模板在边缘设置多个突缘,在突缘围成的区域内设置多个加强肋及辅助加强肋,可以增加碳纤维模板的强度,承载较大的重量。另外,本实用新型的碳纤维模板可以从碳纤维高分子复合材料回收的碳纤维材料以及从其他材料回收的热塑
性纤维经过开纤、叠合及混织后,以针轧或热压等方式形成碳纤维模板。
附图说明
41.图1:为本实用新型碳纤维模板一实施例的立体图。
42.图2:为第1图碳纤维模板另一视角观看的立体图。
43.图3a:为本实用新型碳纤维复合材料的结构示意图。
44.图3b:为本实用新型碳纤维复合材料包含空腔的结构示意图。
45.图4:为本实用新型碳纤维复合材料预成型体的结构示意图。
46.图5:为本实用新型碳纤维模板制造方法的流程图。
47.图6:为本实用新型碳纤维模板制造系统一实施例的方块图。
48.图7:为本实用新型碳纤维模板制造系统另一实施例的方块图。
49.图8:为本实用新型碳纤维模板制造系统又另一实施例的方块图。
50.图号说明:
51.10:板体
52.11:第一表面
53.12:第二表面
54.13:侧边
55.20:突缘
56.21:通孔
57.30:加强肋
58.40:辅助加强肋
59.100:碳纤维模板
60.110:碳纤维开纤机
61.111:碳纤维输送装置
62.120:热塑性纤维开纤机
63.121:热塑性纤维输送装置
64.130:叠合机
65.131:叠合输送装置
66.140:混纤机
67.141:混纤输送装置
68.150:热压成型机
69.151:热压成型输送装置
70.160:裁切机
71.161:裁切输送装置
72.180:成品机
73.190:针轧机
74.a:空腔
75.c:碳纤维
76.p:热塑性纤维
77.s:热塑性基材
78.s11:提供碳纤维回收材料步骤
79.s12:提供热塑性纤维步骤
80.s13:碳纤维开纤步骤
81.s14:热塑性纤维开纤步骤
82.s15:叠合步骤
83.s16:混纤步骤
84.s17:预成型步骤
85.s171:针轧步骤
86.s172:热压步骤
87.s173:热压成卷步骤
88.s18:裁切步骤
89.s19:成品步骤
90.f0:碳纤维复合材料
91.f1:碳纤维复合材料预成型体。
具体实施方式
92.请参阅图1及图2,其表示本实用新型的碳纤维模板的一实施例。本实用新型的碳纤维模板100包括一板体10、复数个突缘20以及复数个加强肋30。该板体10是以一碳纤维复合材料(carbon fibercomposite material)f0(第3a图)制成且呈平板状,所以该碳纤维复合材料f0也可以被称为碳纤维板。该板体10具有一第一表面11、一第二表面12以及复数个侧边13,该第一表面11与该第二表面12相对设置,该侧边13连接该第一表面11与该第二表面12。在本实施例中,该板体10呈矩形,因此该第一表面11与该第二表面12均为矩形,四个该侧边13连接该第一表面11与该第二表面12。复数个该突缘20连接于该侧边13,且从该第一表面11朝该第二表面12的方向延伸,每个该突缘20呈板状,该第二表面12被该突缘20围绕。在本实施例中,每个该突缘20是设置在该板体10的整个该侧边13上,而且该板体10、该突缘20及该加强肋30皆为相同或不相同的该碳纤维复合材料f0所制成。较佳地,该板体10及该突缘20为一体成型。特别说明的是,该第一表面11是用以与灌浆作业的混凝土接触。
93.复数个该加强肋30设置在该第二表面12且连接于该突缘20。由于该板体10呈矩形,因此该突缘20是沿该板体10的长度方向与宽度方向设置。多个该加强肋30中的数个该加强肋30沿该板体10的长度方向延伸,多个该加强肋30中的数个该加强肋30沿该板体10的宽度方向延伸,沿该板体10长度方向与宽度方向延伸的该加强肋30连接两个相对设置的该突缘20且彼此相交。由于该加强肋30沿该板体10长度方向与宽度方向延伸,因此该加强肋30与该突缘20平行设置。另外,该加强肋30 的末端以该第二表面12为基准面的高度是等于该突缘20的末端以该第二表面12为基准面的高度。即该加强肋30的顶部与该突缘20的顶部齐平,如此该加强肋30可以对该突缘20及该板体10提供强化的效果,使该板体10及该突缘20可承受较大的外力。
94.在另一实施例中,更包括复数个辅助加强肋40,该辅助加强肋40 设置于该加强肋30与该突缘20之间且连接该加强肋30与该突缘20。在另一实施例中,该辅助加强肋40也可
以设置在两个相邻的该加强肋 30之间且连接两相邻的该加强肋30。该辅助加强肋40的末端以该第二表面12为基准面的高度是小于该加强肋30的末端以该第二表面12为基准面的高度。即该辅助加强肋40的顶部低于该加强肋30及该突缘20的顶部。该辅助加强肋40可以在强度需求较低的位置对该突缘20及该板体10提供强化的效果,也可以强化该加强肋30。
95.另外,每个该突缘20设有复数个通孔21,该通孔21是沿与该侧边 13平行的方向排列。每个该突缘20的该通孔21具有相同的孔径且该通孔21间具有相同的间距。特别说明的是,该通孔21是用以与相邻的另一该碳纤维模板100中的另一该通孔21以一结合件(图未绘出)彼此组装固定,该结合件例如为螺丝与螺帽的组合。
96.请一并参阅图3a,较佳地,该碳纤维复合材料f0是由复数根碳纤维c分布于热可塑性树脂所构成的一热塑性基材s中所构成。请一并参阅图4,更佳地,该碳纤维复合材料f0是由复数根该碳纤维c与复数根热可塑性纤维p彼此相互缠绕成无方向性分布的一碳纤维复合材料预成型体f1,之后再将该碳纤维复合材料预成型体f1经由热压所构成该碳纤维复合材料f0,因此该碳纤维复合材料f0的物性于各方向皆均一,换言之,该碳纤维复合材料f0于各方向的撕裂强度、抗弯强度与抗弯模数可达均一,能抵抗来自各方向的破坏力。特别说明的是,前述将该碳纤维复合材料预成型体f1热压后,复数根该热可塑性纤维p可以是全部热熔形变彼此黏合而构成该热塑性基材s,或者复数根该热可塑性纤维p 可以是只有一部分该热可塑性纤维p热熔形变与另一部分维持纤维形状的该热可塑性纤维p彼此粘合而构成该热塑性基材s。
97.所述无方向性分布是指将该碳纤维复合材料f0或该碳纤维复合材料预成型体f1投影于一个二维平面,而复数根该碳纤维c于该二维平面上的投影是杂乱或随机地以各方向延伸,复数根该热可塑性纤维p于该二维平面上的投影是杂乱或随机地以各方向延伸。更佳地,该碳纤维 c是不连续的碳纤维,复数根该碳纤维c的平均长度是大于或等于35mm,且小于或等于一预定平均长度以形成前述的“不连续的”,例如平均长度是小于或等于500mm或95mm。更佳地,该热可塑性纤维p是不连续的热可塑性纤维,复数根该热可塑性纤维p的平均长度是大于或等于 35mm,且小于或等于一预定平均长度以形成前述的“不连续的”,例如平均长度是小于或等于500mm或95mm。更佳地,该碳纤维c与该热可塑性纤维p皆分别为二次回收的碳纤维与热可塑性纤维。特别说明的是,二次回收的碳纤维可以是依照发明专利中国台湾twi663192及中国台湾 twii663194碳纤维回收方法及装置或者其他的方式所取得。须注意的是,如果二次回收的碳纤维为复数个碳纤维束所组合而成,此时通常每一个该碳纤维束是由复数根该碳纤维c以z捻或s捻而捻在一起;因此,即使是相邻的该碳纤维束中的复数根该碳纤维c,其彼此间也不会交缠。至于如何完成该碳纤维复合材料f0是由复数根该碳纤维c与复数根热可塑性纤维p彼此相互缠绕成无方向性分布的该碳纤维复合材料预成型体f1的方法,将于后述碳纤维模板的制造方法中说明。
98.请一并参阅图3b,较佳地,该碳纤维复合材料f0是包含复数个空腔a,复数个该空腔是以杂乱或随机地分布于该碳纤维复合材料f0内部,该空腔a的内部为空气,因此整体的该碳纤维复合材料f0的重量会更轻,这进一步使得该碳纤维模板100的重量也更轻。
99.将图1及图2所示的结构分别制作成比较例1、比较例2及实施例1,其对应所使用的材质分别为钢、铝及本实用新型使用碳纤维复合材料的碳纤维模板。比较例1、比较例2及实施例1除了对应所使用的材质有所区别之外,其余有关于结构、尺寸大小及位置等皆相同。
将比较例1、比较例2及实施例1进行测试的结果列于以下表1。
100.表1
[0101][0102]
从表1中可以得知,实施例1与比较例1的不同处在于,实施例1 的重量为13kg,而比较例1的重量为50kg,因此相较于比较例1而言,实施例1实现了轻量化。又由于实施例1的重量仅为比较例的26%(实施例的13公斤除以比较例1的50公斤),因此实施例1的拆卸速度轻便且快速。于产生破洞后,比较例1须回收熔炼再制灌模,实施例1只需加热后再施压10-13分钟,破洞处会自动融合完成,因此实施例1具有回收便利性。比较例1会受到混凝土及灌浆作业中的水分影响而生锈变形,实施例1则不会受到水分而影响结构。生锈后的比较例1其表面无法维持光滑平整,这使得拆模后的混凝土表面呈现坑坑洞洞而需要额外的施工使混凝土表面变得平整,然而实施例1因为无生锈的问题因此表面可以维持光滑平整。
[0103]
接续地,实施例1与比较例2的不同处在于,实施例1的重量为13 kg,而比较例2的重量为22kg,因此相较于比较例2而言,实施例1 实现了轻量化。又由于实施例1的重量仅为比较例的59%(实施例的13 公斤除以比较例2的22公斤),因此实施例1的拆卸速度轻便且快速。于产生破洞后,比较例2须回收熔炼再制灌模,实施例1只需加热后再施压10-13分钟,破洞处会自动融合完成,因此实施例1具有回收便利性。
[0104]
显然地,实施例1在轻量化、拆模速度、回收性、水分的影响及表面平整性,优于比较例1或2。
[0105]
请一并参阅图5至图8,其表示本实用新型的碳纤维模板的制造方法及制造系统。其中,该碳纤维模板的制造方法包含以下步骤。
[0106]
提供碳纤维回收材料步骤s11,是提供成束的碳纤维,如中国台湾专利i663192所示的回收方法,从高分子复合材料中回收碳纤维。例如,提供前述二次回收的复数个该碳纤维束,如前述发明专利中国台湾 twi663192及中国台湾twii663194,从高分子复合材料中
所取得的二次回收的复数个该碳纤维束,该碳纤维束是由复数根该碳纤维c捻在一起所构成。
[0107]
提供热塑性纤维步骤s12,是提供成束的热塑性纤维。例如,提供二次回收的复数个热可塑性纤维束,该热可塑性纤维束是由复数根该热可塑性纤维p捻在一起所构成。
[0108]
碳纤维开纤步骤s13,将成束的碳纤维以一开纤机进行开纤,即形成多根可交错缠绕的碳纤维,由于开纤机为通常技术,因此不在此赘述。例如,复数个该碳纤维束以一碳纤维开纤机110将复数个该碳纤维束中的复数根该碳纤维c彼此分散,将分散的复数根该碳纤维c散布于该碳纤维开纤机110的输送带上使其彼此相互缠绕成无方向性分布的一碳纤维带状物。其中,该碳纤维c是不连续的碳纤维,复数根该碳纤维c的平均长度是大于或等于35mm,且小于或等于500mm或95mm。
[0109]
热塑性纤维开纤步骤s14,将成束的热塑性纤维以一开纤机进行开纤,即形成多根可交错缠绕的热塑性纤维。例如,复数个该热塑性纤维束以一热塑性纤维开纤机120将复数个该热塑性纤维束中的复数根该热塑性纤维p彼此分散,将分散的复数根该热塑性纤维p散布于该热塑性纤维开纤机120的输送带上使其彼此相互缠绕成无方向性分布的一热塑性纤维带状物。其中,该热可塑性纤维p是不连续的热可塑性纤维,复数根该热可塑性纤维p的平均长度是大于或等于35mm,且小于或等于 500mm或95mm。
[0110]
叠合步骤s15,将已开纤的碳纤维及热塑性纤维进行叠合。例如,该碳纤维开纤机110的输送带及该热塑性纤维开纤机120的输送带分别将该碳纤维带状物及该热塑性纤维带状物,输送至一叠合机130。该叠合机130是将该碳纤维带状物及该热塑性纤维带状物彼此叠置成一预混纤带状物,换言之,该叠合机130是将该碳纤维带状物叠于该热塑性纤维带状物的上方,或者将该热塑性纤维带状物叠于该碳纤维带状物的上方。
[0111]
混纤步骤s16,将已叠合的碳纤维及热塑性纤维以混纤机进行混纤,使碳纤维及热塑性纤维形成如图3a所示的交互缠绕的状态,由于混纤机为通常技术,因此不在此赘述。例如,将该预混纤带状物以输送带输送至一混纤机140,该混纤机140将该预混纤带状物中的复数根该碳纤维c及复数根该热可塑性纤维p混合彼此分散,将分散的复数根该碳纤维c及复数根该热可塑性纤维p散布于该混纤机140的输送带上使其彼此相互缠绕成无方向性分布的一混纤带状物。特别说明的是,该混纤带状物的厚度方向的下半部,该碳纤维c的重量或数量比例大于该热可塑性纤维p,这是因为该混纤机140的混纤过程中,该碳纤维c的比重大于该热可塑性纤维p所导致。相对地,该混纤带状物的厚度方向的上半部,该碳纤维c的重量或数量比例小于该热可塑性纤维p。
[0112]
预成型步骤s17,将完成混纤后的碳纤维及热塑性纤维进行预成型。例如,该预成型步骤s17依序包含针轧步骤s171及热压步骤s172,该针轧步骤s171是使用一针轧机190对该混纤带状物进行针轧,使该混纤带状物中的复数根该碳纤维c及复数根该热可塑性纤维p彼此更加相互缠绕,然后该热压步骤s172是使用一热压成型机150将经过针轧后的该混纤带状物经过热压而成为一预成型体。再例如,该预成型步骤s17只包含该热压步骤s172,该热压成型机150将该混纤带状物经过热压而成为该预成型体。又例如,该预成型步骤s17只包含一热压成卷步骤s173,是该混纤带状物经过热压后再收卷而成为该预成型体。
[0113]
裁切步骤s18,使用一裁切机160将该预成型体裁切成预定的尺寸,即为前述该板体10。
[0114]
成品步骤s19,使用一成品机180将裁切成预定的尺寸的该预成型体(该板体10)上设置该突缘20与该加强肋30之后,再加热进行热熔粘合而得到本实用新型的碳纤维模板100。
[0115]
请参阅图6,其表示本实用新型的一实施例。依据前述该碳纤维模板的制造方法,本实用新型的一碳纤维模板的制造系统至少包括:一碳纤维开纤机110、一热塑性纤维开纤机120、一叠合机130、一混纤机140 以及一热压成型机150。该碳纤维开纤机110以一碳纤维输送装置111(例如前述的输送带)连接该叠合机130,该碳纤维开纤机110用于将成束的碳纤维进行开纤,此处成束的碳纤维可以是如中国台湾专利i663192所示的回收方法,从高分子复合材料中回收碳纤维。该热塑性纤维开纤机 120以一热塑性纤维输送装置121(例如前述的输送带)连接该叠合机130,该热塑性纤维开纤机120用于将成束的热塑性纤维进行开纤。该叠合机 130以一叠合输送装置131(例如前述的输送带)连接该混纤机140,开纤后的该碳纤维及该热塑性纤维传送至该叠合机130进行叠合,叠合后的该碳纤维及该热塑性纤维传送至该混纤机140进行混纤。该混纤机140 以一混纤输送装置141(例如前述的输送带)连接该热压成型机150,混纤后的该碳纤维及该热塑性纤维传送至该热压成型机150成型而得到碳纤维板材。
[0116]
请参阅图7,其表示本实用新型的碳纤维模板的制造系统的另一实施例。本实施例与图6所示的实施例的结构是部分相同,相同的元件给予相同的符号并省略其说明。本实施例与图6的实施例的差异在于本实施例还包括一裁切机160,该热压成型机150以一热压成型输送装置 151(例如前述的输送带)连接该裁切机160,成型后的碳纤维板材经由该裁切机160裁切成预定的尺寸。接着该裁切机160以一裁切输送装置 161(例如前述的输送带)连接一成品机180,该成品机180在碳纤维板材上设置突缘与加强肋后得到本实用新型的碳纤维模板。
[0117]
请参阅图8,其表示本实用新型的碳纤维模板的制造系统的另一实施例。本实施例与图7所示的实施例的结构是部分相同,相同的元件给予相同的符号并省略其说明。本实施例与图7的实施例的差异在于本实施例在该混纤机140与该热压成型机150之间设置有一针轧机190。
[0118]
本实用新型的碳纤维模板,其碳纤维板材是由碳纤维相互缠绕地分布在热塑性基材中,使碳纤维模板具有相当的强度,而且其重量轻且方便裁切。另外本实用新型的碳纤维模板在边缘设置多个突缘,在突缘围成的区域内设置多个加强肋及辅助加强肋,可以增加碳纤维模板的强度,承载较大的重量。另外,本实用新型的碳纤维模板可以从碳纤维高分子复合材料回收的碳纤维材料以及从其他材料回收的热塑性纤维经过开纤、叠合及混织后,以针轧或热压等方式形成碳纤维模板。