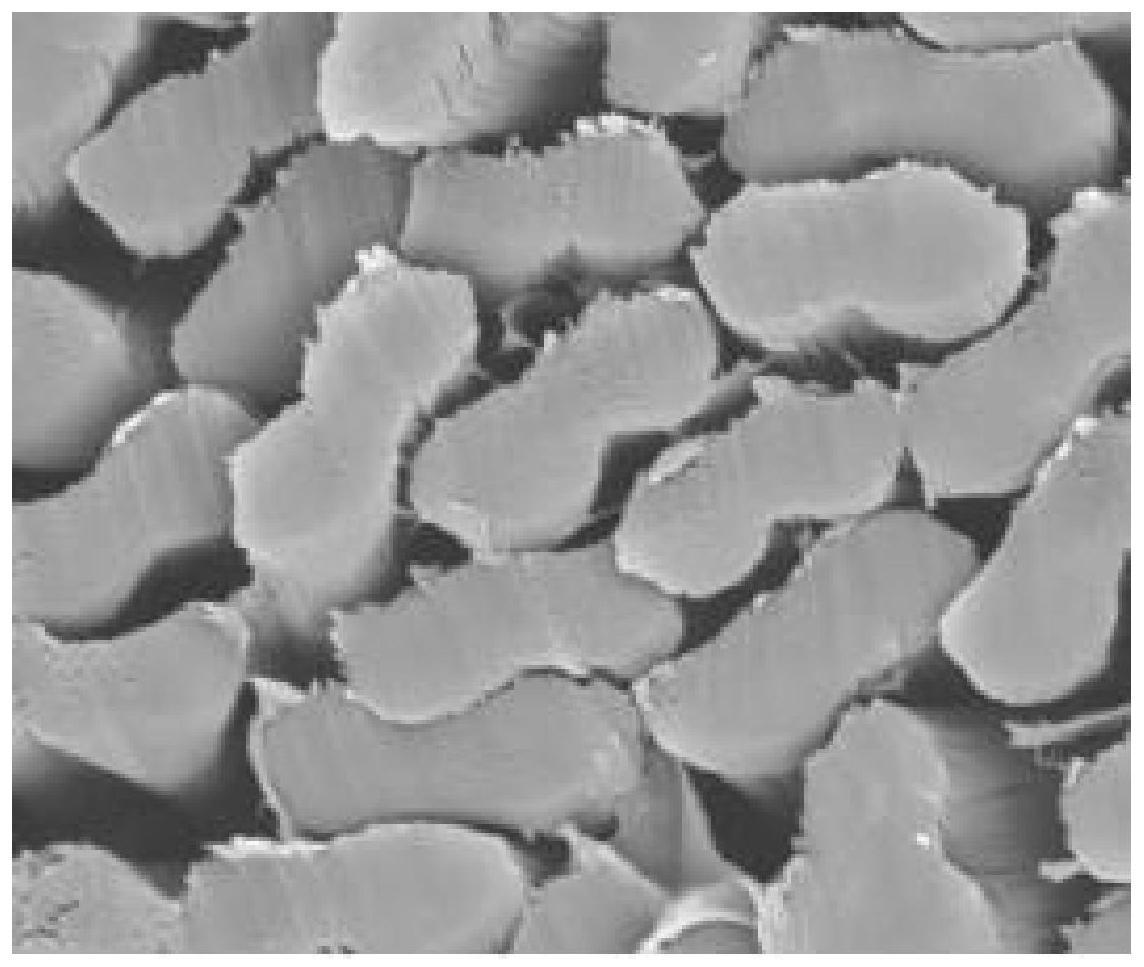
1.本发明涉及面料加工工艺领域,属于功能面料领域,尤其是涉及一种发热保暖的凹凸肌理立体面料的加工工艺。
背景技术:2.在冬季面料中,针织面料比较常见,其具有柔软保暖的特性。近年来随着人们生活水平的日益提高,消费观念的不断更新,消费者对针织面料的质量、样式、色泽等的消费要求越来越高。现有技术中,针织面料有利用组织结构的工艺在针织组织结构肌理表现中形成凹凸立体抽条效果,起到一种视觉引导作用,突出了服装的流线动感效果。在前期试验中,按照常规工艺上机织造,其混纺纱线不平衡内部应力较大,面料经常会发生布面线圈歪斜情况,进而导致了凹凸肌理立体面料整体肌理上比较杂乱,肌理视觉上不流畅,因此本发明旨在提供一种视觉流畅的凹凸肌理面料。
3.另外一方面,在冬季,人体产生的汽态和液态汗水极不容易穿过厚重的服装散入空气,往往集聚在服装内侧,渐渐的会使人感到湿冷。冬季需要一种在更轻更薄的情况下却可以实现更强的发热和保暖效果的功能面料。现有技术中采用具有良好吸湿保暖的功能纱成为主流,为了改进优化功能纱的吸湿性能,是各个厂商的重点研发方向,本发明另外一个次要目的是提供一种吸湿效果更好的功能面料。
技术实现要素:4.本发明的目的在于克服现有技术中存在的上述不足,而提供一种结构设计合理,具有流畅凹凸立体风格的发热保暖的凹凸肌理立体面料的加工工艺。
5.本发明解决上述问题所采用的技术方案是:该发热保暖的凹凸肌理立体面料的加工工艺,所述发热保暖的凹凸肌理立体面料包括面纱和地纱,所述面纱与地纱编织形成凹凸肌理立体面料,所述凹凸肌理立体面料的加工工艺如下:
6.(1)选择高吸湿发热混纺纱为面纱;
7.(2)将高吸湿发热混纺纱进行蒸纱,所述蒸纱工艺为:将面纱放入蒸纱机中,在蒸纱前对面纱盖上棉布,蒸纱机先抽真空到负压500pa,升温至95℃,保温5 分钟,放气,蒸纱机再抽真空到负压500pa,再升温到115℃,保温60分钟,蒸纱机中的低温饱和蒸汽的水分被转移到混纺纱中,放气,再抽真空负压500pa,最后进气,到正常气压,打开锅门,自动冷却,重复以上工序,二次循环蒸纱;
8.(3)对面纱和地纱进行穿纱上机织造,采用正反线圈纵行不同组合配置的罗纹组织,编织面料呈凹凸肌理立体面料。
9.本发明通过采用低温蒸纱工艺,将所用混纺纱在全自动真空定型蒸箱进行给湿定型,通过在蒸纱前盖上棉布,防止水滴对纱线的影响,先抽真空到负压 500pa,降低水的沸点,以便产生所需的低温饱和蒸汽,升温到95℃,保温5分钟,放气,抽真空到负压500pa,再升温到115℃,保温60分钟,由真空转变为低温饱和蒸汽状态使整个筒子纱完全得到处理,
冷蒸汽的水分被转移到混纺纱线,混纺纱的水分分布均匀,达到一致的强度和摩擦值,同时,梯度的低温热处理还松弛了捻度,放气,并且采用低温蒸纱减少纱线上的油剂损失率,使得纱线整体的平滑度能够保持。在多次真空和一定温度范围下增加湿度,多次蒸纱选择小梯度升温,降低纱线缩率,改善了成品手感、光泽度,提高纱线张力、强度,同时消除静电及各部分的不平衡应力,在采用正反线圈纵行不同组合配置的罗纹组织时,减少了线圈歪斜程度,使得最终成品的凹凸纹理流畅。
10.在上述技术方案中,所述高吸湿发热混纺纱由超细旦抗起球腈纶纤维和高吸湿性粘胶纤维混纺,所述高吸湿发热混纺纱规格为80nm 60/40,所述地纱为 40d/36f尼龙+10d/15d氨纶/尼龙耐磨包芯纱。
11.在上述技术方案中,所述面料包括若干最小循环结构单元,所述最小循环结构单元由八路纱线组成,八路纱线中至少有两路的尼龙纤维纱为s捻,其余的尼龙纤维纱为z捻。
12.通过选择不同的纤维种类混纺,通过采用超细旦抗起球腈纶/粘胶纤维混纺纱、尼龙纤维纱,氨纶/尼龙纤维包芯纱为原料,在保障发热保暖面料的基本功能的基础上,中和了纱线捻度活性,平衡织物强度、柔软度和保暖性能,从整体上减低纱线捻度活性,减低织物纵行的歪斜角,以及采用在八路纱线中至少有两路的尼龙纤维纱为s捻,其余的尼龙纤维纱为z捻,来抵消纱线的残余扭矩的对线圈歪斜的影响。
13.在上述技术方案中,步骤三的穿纱方式为面纱80nm 60/40高吸湿发热混纺纱穿4路+地纱40d/36f尼龙穿6路+地纱10d/15d氨纶/尼龙耐磨包芯纱穿2路,第一路:2号纱嘴进40d/36f尼龙,z捻,6号纱嘴进80nm 60/40高吸湿发热混纺纱;第二路:2号纱嘴进10d/15d氨纶/尼龙包纱;
14.第三路:2号纱嘴进40d/36f尼龙,z捻,6号纱嘴进80nm 60/40高吸湿发热混纺纱;
15.第四路:2号纱嘴进40d/36f尼龙,s捻,5号纱嘴进40d/36f尼龙;
16.第五路:1号纱嘴进收边线,2号纱嘴进40d/36f尼龙,z捻,3号纱嘴进尼龙扎口线,6号纱嘴进80nm 60/40高吸湿发热混纺纱做面纱;
17.第六路:2号纱嘴进10d/15d氨纶/尼龙包纱;
18.第七路:2号纱嘴进40d/36f尼龙,z捻,6号纱嘴进80nm 60/40高吸湿发热混纺纱;
19.第八路:2号纱嘴进40d/36f尼龙,s捻。
20.通过在八路纱线中不同路的纱线采用超细旦抗起球腈纶/粘胶纤维混纺纱、尼龙纤维纱,氨纶/尼龙纤维包芯纱不同种类的纤维配合,其中四路采用尼龙纤维纱和超细旦抗起球腈纶/粘胶纤维混纺纱混纺,另外四路添加尼龙纤维和氨纶 /尼龙纤维增加织物的耐磨度和强度,并保障发热保暖面料的基本功能,从整体上减低纱线捻度活性,减低织物纵行的歪斜角。
21.在上述技术方案中,所述正反线圈纵行不同组合配置方式为:
22.正面线圈*1+反面线圈*1;
23.或正面线圈*1+反面线圈*2;
24.或正面线圈*2+反面线圈*2;
25.或正面线圈*4+反面线圈*3。
26.在上述技术方案中,所述高吸湿发热混纺纱的超细旦抗起球腈纶纤维的单丝横截面为哑铃型。
27.其哑铃型为不规则哑铃型,使得纤维之间留有孔隙,孔隙能储存较多静止空气,有较好的蓬松性和保暖性,纤维单丝之间有明显的毛细管区,水分芯吸效应明显,人体产生的湿气易于排出,湿气疏导速度快不会感到湿冷。
28.在上述技术方案中,所述超细旦抗起球腈纶纤维和高吸湿性粘胶纤维加工工艺中的上油处理步骤为:在丝条冷却后,将油剂稀释,通过静电雾化喷头对丝束进行喷淋,所述喷淋方式为环向喷淋,再通过压辊将多余油分压出。
29.在纺织过程中纤维单丝之间或与设备之间会相互摩擦而产生大量静电,现有技术中通过上油步骤,改善纤维的抱合性差,以及容易产生起皱或断头的现象,上油工艺以及油剂组成都会影响纤维表面的状态,现有上油工艺主要包括两种,一种是通过油辊上油,另外一种是通过油嘴喷淋上油,两种工艺都存在各自的缺点,通过油辊上油容易导致纤维张力变大,产生较多的毛丝和断头,另外通过油嘴喷淋上油的上油均匀性不强。本发明通过将上油步骤,通过静电雾化喷头将油剂雾化对丝束喷淋,并采用环向喷淋,能够避免油辊对纤维单丝的摩擦损伤,降低纤维单丝张力,减少毛丝和断头。同时通过更加均匀的上油,使得超细旦抗起球腈纶纤维和高吸湿性粘胶纤维单丝上油后期单丝表面的毛绒减少,进而使得超细旦抗起球腈纶纤维单丝之间形成的毛细管区流通性好,增加吸湿性能,并且高吸湿性粘胶纤维单丝表面的毛绒减小,以避免毛绒过多对纤维单丝在吸湿抓捕汗液时毛绒阻碍水分被吸入丝芯中,增加吸湿性能。
30.在上述技术方案中,所述油剂由下列重量份组成:
31.平滑剂70-75份;
32.抗静电剂8-10份;
33.保湿剂4-5份;
34.集束剂8-10份;
35.抗氧化剂2-4份;
36.调整剂6-10份。
37.在上述技术方案中,所述油剂的浓度为5g/l,油剂的喷淋的温度为55℃。
38.在上述技术方案中,所述压辊施加的压强为0.01mpa。
39.采用低浓度油剂,使得油剂能够在纤维单丝表面均匀成膜,由于采用静电雾化喷头上油雾化喷淋,同时采用较小的压力通过压辊压出多余油剂,使得纤维的含油量在适当持有量,均衡了纤维的强度和摩擦力,纤维单丝之间达到一致的强度和摩擦值,纤维的平滑性能佳,同时抱合力强。
40.在上述技术方案中,所述平滑剂为质量比为1:2的聚氧乙烯月桂醚和聚氧乙烯失水山梨醇单月桂酸酯混合物,
41.所述抗静电剂为聚氧乙烯烷基磷酸酯盐;
42.所述保湿剂为异构聚氧乙烯聚氧丙烯脂肪醇醚;
43.所述集束剂为月桂酸聚氧乙烯酯;
44.所述抗氧化剂为双酚类抗氧化剂;
45.所述调整剂包括消泡剂、稳定剂。
46.采用聚氧乙烯月桂醚和聚氧乙烯失水山梨醇单月桂酸酯混合物作为平滑剂,改善了油剂乳液的稳定性,使得形成稳定的分散体系,分散想粒径小,使得在静电雾化上油时更
加均匀,并且使得油剂能够快速铺展,在纤维单丝上均匀成膜,采用双酚类抗氧化剂在提供优异抗氧化的同时,能够改善油剂的热稳定性,减少热分解,减少油剂的损失率。
附图说明
47.图1本发明实施例1超细旦抗起球腈纶纤维的不规则而哑铃状的示意图。
48.图2本发明实施例1超细旦抗起球腈纶纤维的毛细管区的示意图.
49.图3a为本发明的实施例1的面料实物电镜图,3b为本发明的实施例2的面料实物电镜图,3c为本发明的实施例3的面料实物电镜图,3d为本发明的实施例4的面料实物电镜图。
50.图4a为本发明的实施例3的面料实物图,4b为图4a的局部放大图, 4c为本发明的对比例1的面料实物图,4d为图4c的局部放大图。
具体实施方式
51.下面将结合实施例和效果例对本发明做进一步的详述,而非限制本发明的范围。
52.实施例1
53.参见图1至图3所示,须知,本说明书所附图式所绘示的结构、比例、大小等,均仅用以配合说明书所揭示的内容,以供熟悉此技术的人士了解与阅读,并非用以限定本发明可实施的限定条件,故不具技术上的实质意义,任何结构的修饰、比例关系的改变或大小的调整,在不影响本发明所能产生的功效及所能达成的目的下,均应仍落在本发明所揭示的技术内容能涵盖的范围内。同时,本说明书中若有引用如“上”、“下”、“左”、“右”、“中间”及“一”等的用语,亦仅为便于叙述的明了,而非用以限定本发明可实施的范围,其相对关系的改变或调整,在无实质变更技术内容下,当亦视为本发明可实施的范畴。
54.本实施例中的发热保暖的凹凸肌理立体面料的加工工艺,所述发热保暖的凹凸肌理立体面料包括面纱和地纱,所述面纱与地纱编织形成凹凸立体抽条面料,所述凹凸肌理立体面料的加工工艺如下:
55.(1)选择高吸湿发热混纺纱为面纱,高吸湿发热混纺纱为80nm混纺比例60/40 超细旦抗起球腈纶/粘胶纤维混纺纱,地纱为40d/36f尼龙+10d/15d氨纶/尼龙耐磨包芯纱;
56.高吸湿发热混纺纱中的超细旦抗起球腈纶纤维和粘胶纤维的制备工艺中纺丝喷丝、牵伸、冷却、烘干采用现有技术中的常规工艺,其上油工艺采用:在丝条冷却后,将油剂稀释至5g/l,控制油剂温度为55℃,通过静电雾化喷头对丝束进行喷淋,所述喷淋方式为环向喷淋,再通过压辊将多余油分压出,压辊施加的压强为0.01mpa;
57.油剂由下列重量份组成:25份聚氧乙烯月桂醚,50份聚氧乙烯失水山梨醇单月桂酸酯;8份聚氧乙烯烷基磷酸酯盐;5份异构聚氧乙烯聚氧丙烯脂肪醇醚; 10份月桂酸聚氧乙烯酯;5份双酚类抗氧化剂;1份消泡剂;1份稳定剂。
58.以超细旦抗起球腈纶纤维为例,制备的丝束如图1-2所示,其单丝表面上油均匀,并且可以看出其表面的毛绒量大大减少,使得单丝之间形成的毛细血管更加通畅。
59.(2)将高吸湿发热混纺纱进行蒸纱,所述蒸纱工艺为:将面纱放入蒸纱机中,在蒸纱前对面纱盖上棉布,蒸纱机先抽真空到负压500pa,升温至95度,保温 5分钟,放气,蒸纱机再抽真空到负压500pa,再升温到115度,保温60分钟,蒸纱机中的低温饱和蒸汽的水分被转移到混纺纱中,放气,再抽真空负压500pa,最后进气,到正常气压,打开锅门,自动冷却,
重复以上工序,二次循环蒸纱;
60.(3)对面纱和地纱进行穿纱上机织造,采用正反线圈纵行不同组合配置的罗纹组织,编织面料呈凹凸肌理立体面料。
61.面料包括若干最小循环结构单元,最小循环结构单元由八路纱线组成,八路纱线其中:
62.第一路为10d/15d尼龙纤维纱和80nm混纺比例60/40超细旦抗起球腈纶/粘胶纤维混纺纱,所述尼龙纤维纱为z捻;
63.第二路为10d/15d氨纶/尼龙包芯纱,氨纶/尼龙包芯纱为s捻;
64.第三路为40d/36f尼龙纤维纱和80nm混纺比例60/40超细旦抗起球腈纶/粘胶纤维混纺纱,所述尼龙纤维纱为z捻;
65.第四路为两条40d/36f尼龙纤维纱,尼龙纤维纱为z捻;
66.第五路为40d/36f尼龙纤维纱和80nm混纺比例60/40超细旦抗起球腈纶/粘胶纤维混纺纱,尼龙纤维纱为z捻;
67.第六路为10d/15d氨纶/尼龙包芯纱,氨纶/尼龙包芯纱为s捻;
68.第七路为40d/36f尼龙纤维纱和80nm混纺比例60/40超细旦抗起球腈纶/粘胶纤维混纺纱,尼龙纤维纱为z捻;
69.第八路为40d/36f尼龙纤维纱,s捻。
70.每路纱线采用正反线圈纵行不同组合配置方式的罗纹组织编织而成,其正反线圈纵行配置方式为:正面线圈*1+反面线圈*1,其面料罗纹组织如图3a所示。
71.实施例2相对实施例1不同的在于,其正反线圈纵行配置方式为:正面线圈*1+反面线圈*2,其面料罗纹组织如图3b所示;
72.实施例3相对实施例1不同的在于,其正反线圈纵行配置方式为:正面线圈*2+反面线圈*2,其面料罗纹组织如图3c所示;
73.实施例4相对实施例1不同的在于,其正反线圈纵行配置方式为:正面线圈*4+反面线圈*3,其面料罗纹组织如图3d所示。
74.如图3a-3d所示,其线圈整体歪斜程度低,最终成品的凹凸纹理流畅。
75.对比例1
76.与实施例1不同的在于,所述蒸纱工艺采用现有技术中的高温蒸纱,将混纺纱放入高温高压蒸锅内,升温至105度,保温5分钟,放气,再升温到135 度,保温60分钟,放气到正常气压,打开锅门,自动冷却。
77.实施例3和对比例1最终制备的面料实物照片如图4所示,其中图4a的凹凸纹理的线圈歪斜程度和图4c采用普通工艺的线圈歪斜程度明显要低,图4c 中贴纸表示为一条纵线线圈的走向,图4c中的白色线条标记为普通工艺中平针横向线圈的走向,表明图4a和4c均为水平平铺的面料,可以看出本发明发明实施例3制备的面料其线圈整体歪斜程度相对对比例1来说大大减少,提升了面料整体凹凸纹理的流畅性。
78.对比例2
79.与实施例1不同的在于,所述油剂为本公司在先用的油剂,油剂的成分为: 52%多元醇酯平滑剂,20%脂肪醇聚氧乙烯醚乳化剂,10%丙三醇醚抱合剂,16%的抗静电剂,2%的抗菌剂。
80.对比例3
81.与实施例1不同的在于,所述上油工艺采用在常规的辊式上油,将实施例1 中的油剂储放在油槽内,经由上油滚轮对丝束上油,再通过压辊将多余油分压出,压辊施加的压强为0.25mpa。
82.芯吸高度是指在30分钟之内试验样品被水分浸到的高度,毛细管效应是在纤维与水分接触之后,水分沿着纤维与纤维之间孔洞形成的毛细管上升,从而浸润到没有接触过水分的纤维和织物部分,实验样品最后得到的水迹高度就是所要测试的芯吸高度。芯吸高度与织物的吸湿性能有关,芯吸高度大,那么织物的吸湿性能好,穿着时就能很好的排走身体表面湿气,可以保持体表和织物干爽,不会让人感受到湿冷。
83.对实施例1和对比例2和对比例3的面料样品测试其芯吸高度,实验仪器采用yg(b)871型毛细管效应测定仪参照标准fz/t01071-2008《纺织品毛细效应测试方法》,将织物放在20℃,相对湿度为65%的条件下平衡24小时,每种织物分别剪取经向和纬向两个方向的试样,经向30cm,纬向5cm,另一条为纬向30cm,经向5cm,在毛细管效应测定仪水槽中的蒸馏水加入几滴红墨水,便于观察,调整液面与标尺的零点对齐,将试验样品下端10mm部位垂直浸入水槽中,试样上端用夹子固定,记录30min之后,溶液在布面上升的高度,即为芯吸高度。如果溶液在布面上升的高度不一致,则取最低高度为所测结果。
84.透湿量是指在单位时间内通过单位面积的水蒸气的量。透湿性体现了织物湿传递的能力,主要是通过纤维与纤维之间的孔洞以及纱线之间的孔隙向外传递气态水,或者是经过纤维和纱线的孔洞在织物内表面形成液态水,然后经过毛细管运输到织物外表面之后蒸发扩散。
85.对实施例1和对比例2和对比例3的面料样品测试其透湿量,实验仪器采用yg601型透湿量测试仪,参照gb/t12704.1-2009纺织品织物透湿性试验方法第1部分:吸湿法,把盛有干燥机和水并在上面封住试样的透湿杯放置在有规定温度和湿度的仪器中,根据放置前后组合体的重量变化来计算透湿量的值,每种样品要选取三个试样,然后取平均值,所用干燥剂为无水氯化钙,使用前在烘箱中干燥3小时。
86.织物透湿量按照下面公式进行计算,其中wvt-每天24小时每平方米的透湿量g/m2·
d);t-实验时间(h);δm-同一个组合体前后两次称重之差(g); s-试样的实验面积(m2)0.00385m2(直径为70mm)。
[0087][0088]
结果如下表所示
[0089] 实施例1对比例2对比例3芯吸高度(mm)14.312.910.4透湿量(g/m2·
d)584154785246
[0090]
根据上述实验结果,可以看出本发明实施例1提供的面料其吸湿性能最佳,说明通过本发明提供的油剂和上油工艺制备的腈纶纤维和黏胶纤维的吸湿性能大大提高,可能是由于本发明通过静电喷雾法对单丝表面上油均匀,并且可以看出其表面的毛绒量大大减少,使得单丝之间形成的毛细血管更加通畅,毛细效应好,吸湿性越好,粘胶纤维的吸水性得到改善以及超细旦腈纶的芯吸效应使水蒸气更容易通过。
[0091]
最后有必要在此说明的是:以上实施例只用于对本发明的技术方案作进一步详细地说明,不能理解为对本发明保护范围的限制,本领域的技术人员根据本发明的上述内容作出的一些非本质的改进和调整均属于本发明的保护范围。