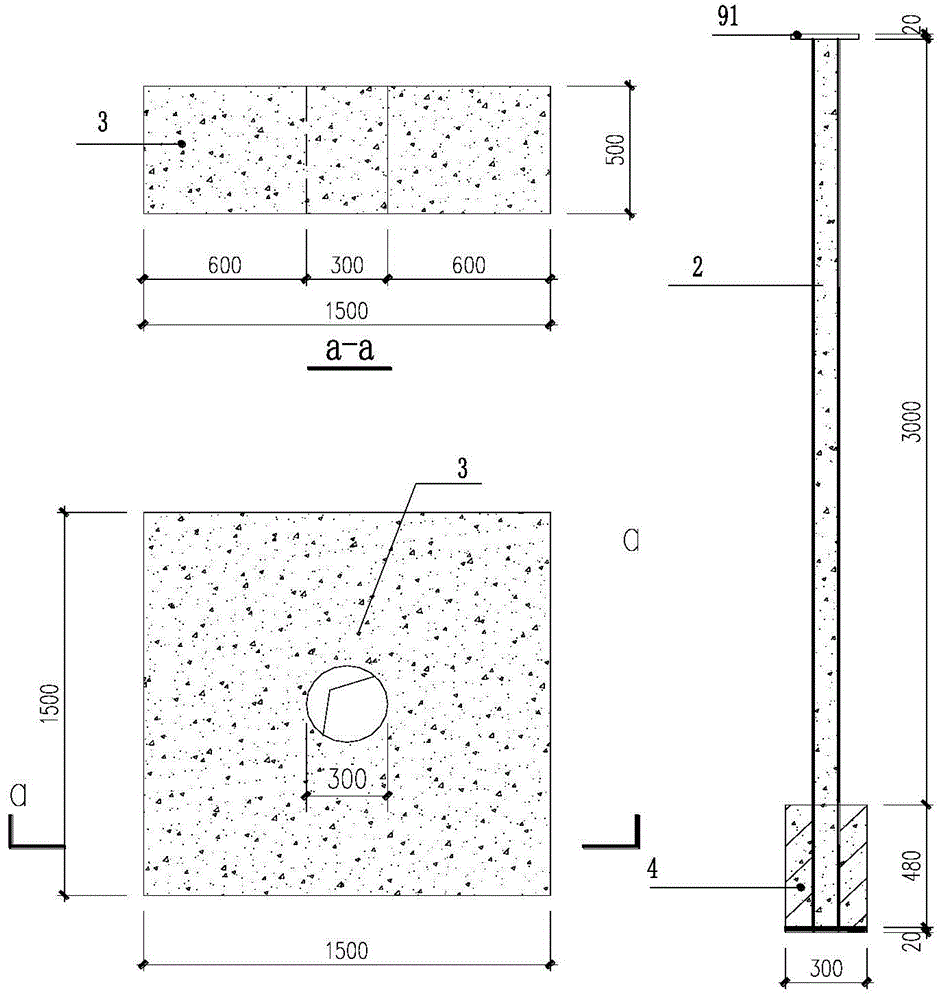
本发明涉及建筑施工试验的
技术领域:
,尤其涉及一种逆作法施工环境下竖向支撑柱承载能力试验模拟方法。
背景技术:
:随着中国城市建设的跨越式发展,大规模的高层建筑地基基础与地下室、大型地下商场、地下停车场、地下车站、地下交通枢纽和地下变电站等地下结构的建设都面临着深基坑施工处理的难题。由于施工场地的工程地质和水文地质条件往往复杂多变、而基坑施工又常处于超大面积和大深度施工情况,在保证工期进度、资源节约和环境保护等一系列要求的情况下,传统的深基坑施工方法很难适应日益复杂的开发条件。而逆作法与传统的深基坑施工方法相比,克服了常规临时支护存在的诸多不足之处,具有保护环境、节约社会资源、缩短建设周期等诸多优点,是进行可持续发展的城市地下空间开发和建设节约型社会的有效手段。逆作法施工技术的原理是将高层建筑地下结构自上往下逐层施工,即沿建筑物地下室四周施工连续墙或密排桩,作为地下室外墙或基坑的围护结构,同时在建筑物内部有关位置施工楼层中间支承柱,从而组成逆作的竖向承重体系;随后从上向下挖一层土方,同土模浇筑一层地下室梁板结构,当达到一定强度后,即可作为围护结构的内水平支撑,以满足继续往下施工的安全要求。与此同时,由于地下室顶面结构的完成,也为上部结构施工创造了条件,所以也可以同时逐层向上进行地上结构的施工。支承柱作为逆作法施工的重要部分,在进行逆作法施工期间,地下室基础底板未封底之前,它将承受地下各层和地上预加载控制最多层数的楼层结构自重和施工荷载。基础底板封底后,它又作为地下室竖向承重结构的一部分,将上部结构的荷载传递给地下室基础底板。支承柱布置的位置和数量,要结合施工方案等诸多因素考虑计算后确定。逆作法施工过程中,各层楼板的施工和各层土方的开挖会形成不同的荷载工况。在不同工况条件下,竖向支承柱承受的竖向荷载和计算长度各不相同,因此竖向支承柱需进行不同工况下的承载力计算和稳定性验算。实际逆作法工程中,绝大多数竖向支承柱的截面受长细比构造要求的控制,为研究桩柱之间采用不同空隙回填材料对支承柱的约束作用影响,需要进行逆作法施工环境下竖向支承柱承载性能试验研究。技术实现要素:为了模拟逆作法施工环境下竖向支撑柱的承载能力,为此,本发明提供一种逆作法施工环境下竖向支撑柱承载能力试验模拟方法。本发明采用以下技术方案:一种逆作法施工环境下竖向支撑柱承载能力试验模拟方法,包括以下步骤:s1、等比例缩小箱体、钢管试件、基岩、实际桩、土层、定型管、介质材料、施压组件尺寸;s2、制作钢管混凝土柱、实际桩、基岩、箱体;向钢管试件内浇筑混凝土形成钢管混凝土柱;在钢管混凝土柱周围制作实际桩,制作中间带孔的基岩,将包裹钢管混凝土柱的实际桩插入到基岩中部的孔中,使用木模板在基岩的四边围成箱体;s3、在钢管试件外同轴放置定型管,在定型管与钢管试件之间填充介质材料,在定型管外不同高度填充相应土层,填充过程中,定型管逐层拔出,在土层不同高度处设置检测部件;s4、安装施压组件,向钢管试件的顶部向下垂直施压;s5、采用荷载控制的分级加载制度,获得荷载级数记录各级荷载值和对应的应变及位移,同时绘制n-δ曲线,n为施压组件施加的轴向压力,u为不同高度处检测部件检测到的钢管混凝土柱的变形参数。进一步地,步骤s2中制作实际桩的步骤为:在钢管混凝土柱的周围使用钢筋笼包裹,然后浇筑混凝土。进一步地,所述钢管试件内浇筑c40的混凝土,还使用c40混凝土制作试验块。进一步地,所述土层从下到上依次设置二层,下层为模拟风化岩的级配砂石,上层为模拟地表土层的素土。进一步地,步骤s3填充相应土层的具体步骤如下:s3a1、在定型管外侧且位于基岩上方填充级配砂石并夯实,拔出部分高度定型管;s3a2、重复步骤s3a1,在此过程中,放置第五组应变片,直至级配砂石的厚度达到设定值;s3a3、在级配砂石上填充素土之前,级配砂石与素土的交界面作为第二交界面,在第二交界面上放置第四组应变片;s3a4、级配砂石上填充素土并夯实,然后拔出部分高度定型管;s3a5、重复步骤s3a4,直至素土的厚度达到设定值,素土上表面作为第一交界面,在第一交界面上放置第三组应变片,定型管全部拔出;s3a6、在设定的不同高度处设置第一组应变片和第二组应变片,并在相应的高度上放置位移计d。进一步地,当在钢管混凝土柱和定型管之间填充介质材料时,在步骤s3a1中,在填充土层之前;在钢管混凝土柱和定型管之间填充介质材料,所述介质材料为粗砂、预拌水泥灌浆料任意一种。进一步地,步骤s4具体如下:所述施压组件包括千斤顶、反力梁、反力架,在所述钢管试件的顶部安装加载板,在反力架的反力梁与加载板之间设置千斤顶,千斤顶和位移计d分别与数据采集仪连接;千斤顶对钢管试件顶部的加载板施加竖向轴力。进一步地,每组应变片均为8个,沿长度方向布置四个测竖向应变,沿周长方向布置四个测横向应变。进一步地,每个所述钢管试件上均布置五个位移计d,位移计d1位于加载板的下方;另外四个分成两组,位移计d2、位移计d3位于第一交界面上方设定距离处以测量钢管试件在试验过程中此截面的横向挠度;位移计d4、位移计d5位于第一交界面处以测量此截面在试验过程中的横向挠度。进一步地,所述箱体制作步骤如下:s1b1、使用木胶合板围成四边矩形槽作为箱体的内侧;s1b2、使用槽钢平行设置在在木胶合板外侧,相邻槽钢通过对拉螺杆固定,并且在平行的木胶合板和槽钢之间放置木方。本发明的优点在于:(1)桩为实际桩,填充有混凝土的钢管作为柱,本申请通过试验研究桩柱之间采用不同空隙回填材料对支承柱的约束作用影响,作为验证竖向支承柱长细比计算公式的合理性。将岩土工程及建筑工程集成与融合,可实现对逆作法施工环境及施工工况的模拟,为逆作竖向承力构件提供科学、便捷的承载能力测试方法。(2)试验块的设置可以测量钢管混凝土的强度。(3)本申请中使用定型管,定型管可以方便保持土层与钢管试件之间的空隙的要求下能将土层压实,保证真实的模拟状态。(4)在该方案中桩柱之间采用不同空隙回填材料可以有介质材料,也可以不填充,当有填充物时,粗砂或预拌水泥灌浆料中的一种模拟不同的介质材料。(5)本申请中土层、介质材料使用定型管的填充方式,可以更好地模拟实际情况。(6)应变片和位移计d的设置位置可以更好测量钢管试件的变形状态的变形情况。(7)所述试块用于换算抗压强度标准值。(8)箱体槽钢和对拉螺杆、木方的设置可以对箱体进行支撑加固,保证实验装置的稳定性。附图说明图1-4为四种不同约束条件下的状态图。图5-7为试验模拟装置的结构图。图8为应变片的位置图。图9为位移计d的位置图。图10a为制作模拟装置中的基岩、钢管混凝土柱和实际桩的结构图。左上图为基岩的主视图,左下图为基岩的俯视图,右图为钢管混凝土柱和实际桩的结构图。图10b将钢管混凝土柱和实际桩插入到基岩的中心孔中的过程图。图10c为在实际桩和基岩的中心孔内壁之间注入结构胶后的结构图。图10d为填充好介质材料厚度结构图。图10e为制作好箱体后的结构图。图10f-10i为填充土层的步骤过程图。图11a为无介质材料状态下钢管试件对应的n-δ曲线。图11b为介质材料是粗砂、预拌水泥灌浆料状态下钢管试件对应的n-δ曲线。图11c为介质材料是预拌水泥灌浆料状态下钢管试件对应的n-δ曲线。图12-15为竖向支撑柱的有限元分析模型图。图16为软件模拟和实验模拟状态下的介质材料分别是无、粗砂、预拌水泥灌浆料状态下钢管试件对应的n-δ曲线。图中标注符号的含义如下:1-箱体101-木胶合板102-槽钢103-对拉螺杆104-木方2-钢管混凝土柱21-钢管试件22-钢管混凝土3-基岩4-实际桩41-钢筋笼42-桩混凝土5-级配砂石6-素土7-介质材料8-定型管91-加载板92-千斤顶93-反力梁94-反力架10-开挖面110-结构胶具体实施方式一种约束条件下钢管混凝土柱计算长度lc及长细比λ计算方法,所述钢管混凝土柱2的计算长度lc的计算公式如下:所述钢管混凝土柱2包括钢管和在钢管内浇筑的混凝土,实际桩4由钢筋和桩混凝土42浇筑形成。为了方便计算,钢管混凝土柱2作为等效桩来计算。lc为钢管混凝土柱2的计算长度(m);μ为钢管混凝土柱2的柱端约束条件的计算长度系数,约束条件包括固接、铰接、半刚性连接。当钢管混凝土柱2两端铰接时取1.0,一端固定一端铰接时取0.7,两端固定时取0.5;l0为钢管混凝土柱2的外露长度;h1、h2分别为钢管混凝土柱2在土层中的长度和实际桩4的长度(桩身入硬岩时,h2的高度为从实际桩4的顶面至硬岩顶面),α1、α2分别为等效桩的水平变形系数、实际桩4的水平变形系数。具体来说,不同约束条件计算长度lc如下所示:如图1所示,当钢管混凝土柱2顶铰接且桩底支于非硬岩中,时,桩底部近似铰接,lc=1.0×(l0+h1+h2);时,桩底部近似固接,如图2所示,当钢管混凝土柱2顶铰接且桩底嵌于硬岩内,时,桩底部近似固接,lc=0.7×(l0+h1+h2);时,桩底部近似固接,如图3所示,当钢管混凝土柱2顶固接且桩底支于非硬岩中,时,桩底部近似铰接,lc=0.7×(l0+h1+h2);时,桩底部近似固接,如图4所示,当钢管混凝土柱2顶固接且桩底嵌于硬岩内,时,桩底部近似固接,lc=0.5×(l0+h1+h2);时,桩底部近似固接,以上公式中,等效桩的水平变形系数α1(1/m)计算公式如下:m1表示钢管混凝土柱2为等效桩的外侧介质材料7水平抗力系数的比例系数,通过查表1获得,b01表示等效桩桩身的计算宽度(单位:m),当钢管的外直径d1≤1时,b01=0.9(1.5d1+0.5),当d1>1时,b01=0.9(d1+1);d1单位为m.等效桩的抗弯刚度e1i1计算如下:i01=w01d01/2(4)e1i1=0.85ec1i01(5)其中e1表示等效桩的材料系数,i1表示等效桩的惯性矩(和钢管截面有关),d01表示扣除保护层厚度的等效桩直径(钢管混凝土柱2外无介质材料7时,d01即为d1),ρg1表示等效桩桩身配筋率,t表示钢管的壁厚(单位m);e01表示钢管弹性模量(单位:n/m2);ec1表示钢管内混凝土弹性模量(单位:n/m2)。实际桩4的水平变形系数α2(1/m)计算公式如下:m2表示实际桩4外侧介质材料水平抗力系数的比例系数,通过查表1获得,b02表示实际桩4的桩身计算宽度(单位:m),当实际桩4的桩身直径d2≤1时,b02=0.9(1.5d2+0.5),当d2>1时,b02=0.9(d2+1);d2单位为m。实际桩4的抗弯刚度e2i2计算如下:i02=w02d02/2(10)e2i2=0.85ec2i02(11)d02=d2-2c(13)其中e2表示实际桩4的材料系数,i2表示实际桩4的惯性矩(和桩身截面有关),d02表示实际桩4扣除保护层(保护层为从钢筋外皮到实际桩4外侧壁的距离)的桩直径(单位:m),ρg2表示实际桩4的桩身配筋率,e02表示钢筋弹性模量(单位:n/m2);ec2表示实际桩4的桩混凝土42的弹性模量(单位:n/m2),c表示实际桩4的保护层厚度(单位:m)。根据表1可获得公式中α1、α2获得水平抗力系数的比例系数m值:表1根据上述公式可以获得实际情况下钢管混凝土22长度lc。逆作法下钢管混凝土柱2的回转半径换算(1)钢管混凝土柱2的换算截面面积a*为:a*=(f×as+fc×ac)/f(14)式中:f表示钢管设计强度;as表示钢管横截面积(单位:mm2);fc表示钢管内的混凝土设计强度;ac表示钢管内的混凝土的横截面积(单位:mm2)。(2)钢管混凝土柱2的换算惯性矩i*为:i*=(es×is+ec×ic)/es(15)式中:es表示钢管弹性模量;is表示钢管惯性矩(mm4);d表示钢管外直径(mm);t表示钢管壁厚(mm);ec表示钢管内混凝土弹性模量(n/mm2);ic表示钢管内混凝土惯性矩(mm4)。(3)换算回转半径i为:逆作法支承钢管混凝土柱2的长细比计算考虑不同约束作用下,课题组推导的逆作施工条件下钢立柱长细比计算公式为:式中:lc表示不同约束作用下的钢管混凝土柱2计算长度(m);i表示钢管混凝土柱2换算回转半径(mm)。若长细比λ≤25,则满足规范要求,否则不满足规范要求。为了验证上述计算方法的正确性,本申请中提供了实物的模拟和软件模拟,使用两种方法来验证上述计算方法的准确性。实物模拟本方案提供了模拟装置和使用该模拟装置的方法,其中模拟装置如下所示:如图5-7所示,一种逆作法施工环境下竖向支撑柱承载能力试验模拟装置,包括箱体1、钢管试件21、基岩3、实际桩4、土层、定型管8、介质材料7、钢管混凝土柱2、施压组件、控制单元。在该实施例中,均按照1:7缩尺比例确定各部分尺寸。如图6所示,所述箱体1设置为内径为1500mm*1500mm*2500mm的木框架箱体1,为保障在试验加载过程中箱体1不会因侧向压力过大导致开裂,箱体1外侧使用支撑模板和拉杆对其进行支撑加固。在该方案中,箱体1内侧使用18mm厚的木胶合板101围成四边矩形槽,外侧四边使用槽钢102,相对的槽钢102通过m16对拉螺杆103固定,木胶合板101和槽钢102之间还分布有50mm*100mm的木方104,具体的,槽钢102是100×48×5.3轧制槽钢102,每侧上下平行设置多根,上下间距为400mm。所述箱体1用于模拟逆作法中的连续墙。所述钢管试件21为外直径100mm、壁厚3mm、长度3500mm、材料为q345b的钢材料。所述钢管试件21内填充有钢管混凝土22,最终形成钢管混凝土柱2,钢管混凝土22具体为c40混凝土。浇筑钢管试件21内的c40混凝土时,首先将钢管试件21竖立,从顶部灌入c40混凝土,并用插入式振捣棒振捣至密实。钢管试件21内部填充c40混凝土须自然养护28天,保证混凝土强度达到试验要求。在c40混凝土终凝后,需对c40混凝土表面做清凿与抹平处理,采用高强混凝土砂浆抹平,抹平完成后进行养护,保证加载面可以均匀加载。钢管混凝土柱2用于模拟逆作法施工环境下的竖向支撑柱。c40混凝土强度由同条件下成型养护的150mm立方体试块试验,最后换算为抗压强度标准值。所述基岩3为预制的c20混凝土块,尺寸为1500mm*1500mm*500mm,即作为计算方法中的硬岩。c20混凝土块采取预制而非现浇的方式制作。所述基岩3中部开设有预制实际桩4的桩孔,直径略大于300mm。所述实际桩4为设置在钢管混凝土柱2与基岩3之间的钢筋笼41和浇筑有c40的桩混凝土42。所述土层位于基岩3的上方,且均为夯实状。在该实施例中,土层从下到上依次设置二层,下层为模拟风化岩的级配砂石5,上层为模拟地表土层的素土6。所述介质材料7填充在土层与钢管试件21之间,用于获取水平抗力系数的比例系数m值。所述定型管8用于在土层和钢管混凝土柱2之间填充介质材料7之前给土层定型,定型管8在施压组件对钢管试件21施力之前抽出。在该实施例中包括三种类型的介质材料7,一种为粗砂、一种为预拌水泥灌浆料、另一种没有填充物。定型管8使用pvc管,直径为300mm。如图7所示,所述施压组件包括加载板91、千斤顶92、反力梁93、反力架94,所述加载板91为两块,分别设置在钢管试件21底部和顶部,所述千斤顶92一端固定在加载板91上,另一端固定在反力梁93上,通过调节千斤顶92给加载板91施力,所述反力梁93的两端架设在反力架94上。在该实施例中,加载板91均为20mm厚的钢板。所述钢管试件21上设置有多个应变片和位移计d,如图8所示,每组试验中的钢管试件21上设置有48个应变片,钢管试件21自上而下分为5个截面,每个截面处设置8个应变片,沿长度方向布置四个测竖向应变,沿周长方向布置四个测横向应变,其中11#-18#应变片,21#-28#应变片测量开挖面10形成的第一交界面以上的钢管混凝土22应变;31#-38#应变片测量第一交界面处的钢管混凝土22应变;41#-48#应变片测量素土与砂石形成的第二交界面处的钢管混凝土22的应变,51#-58#应变片测量第二交界面以下的钢管混凝土22应变。如图9所示,所述位移计d包括五个,位移计d1布置在顶部的加载板91下方,用来测量试验过程中的竖向位移;另外四个分成两组,位移计d2、位移计d3布置在第一交界面上方500mm处以测量钢管试件21在试验过程中此截面的横向挠度;位移计d4、位移计d5布置在第一交界面处以测量此截面在试验过程中的横向挠度。所述控制单元与千斤顶92的受控端、应变片和位移计d的信号端连接。控制单元通过控制千斤顶92的施加大小和施压时间。使用上述装置的方法,具体步骤如下:s1、根据实际情况按等比例缩小箱体1、钢管试件21、基岩3、实际桩4、土层、定型管8、介质材料7、施压组件尺寸;s2、制作钢管混凝土柱2、实际桩4、基岩3、箱体1;向钢管试件21内浇筑c40作为钢管混凝土22,从而形成钢管混凝土柱2,同时,为了测量钢管混凝土22的强度,制作1500mm立方体的c40混凝土试验块,钢管混凝土柱2和试验块并养护28天,并在钢管混凝土柱2的两端设置加载板91。钢管混凝土柱2周围使用钢筋笼41包裹,并浇筑c40混凝土作为包裹钢管混凝土柱2的实际桩4,在实验平台的钢板上制作中间带孔的基岩3,制作基岩3使用c20混凝土。将包裹钢管混凝土柱2的实际桩4插入到基岩3中部的孔中,在实际桩4和孔内壁之间注入结构胶110固定;钢板的设置上为了保护实验室中的地面不会被破坏。使用木模板在基岩3的四边围成箱体1,组成内径为1500mm*1500mm*2500mm的木框架,为保障在试验加载过程中箱体1不会因侧向压力过大导致开裂,箱体1外侧采用支撑模板和拉杆对其进行支撑加固。具体步骤为:s1b1、使用木胶合板101围成四边矩形槽作为箱体1的内侧;s1b2、使用槽钢102平行设置在在木胶合板101外侧,相邻槽钢102通过对拉螺杆103固定,并且在平行的木胶合板101和槽钢102之间放置木方104。s3、在实际桩4正上方放置定型管8,且与钢管混凝土柱2同轴,在钢管混凝土柱2与定型管8之间填充介质材料,在实际桩4上部放置土层、布置位移计d和应变片;定型管8协助填充级配砂石5、填充素土6,填充过程中分层密实,且定型管8同步分层拔出;不同组试验,介质材料7不同,在该实施例中设置三组试验,介质材料7分别是:一种为粗砂、一种为预拌水泥灌浆料、另一种没有介质材料7,即土层与钢管混凝土2之间为空部。本方案通过不同的介质材料7用于与模拟多组试验,分别对应计算方法中不同的m值。具体步骤如下:s3a1、在实际桩4正上方放置定型管8,且与钢管混凝土柱2同轴,在钢管混凝土柱2与定型管8之间填充介质材料7,所述介质材料7为粗砂、预拌水泥灌浆料任意一种。在定型管8外侧且位于基岩3上方填充级配砂石5并夯实,拔出部分高度定型管8;s3a2、重复步骤s3a1,在此过程中,放置51#-58#应变片,直至级配砂石5的厚度达到设定值;s3a3、在级配砂石5上填充素土6之前,级配砂石5与素土6的交界面作为第二交界面,在第二交界面上放置41#-48#应变片;s3a4、级配砂石5上填充素土6并夯实,然后拔出部分高度定型管8;s3a5、重复步骤s3a4,直至素土6的厚度达到设定值,素土6上表面作为第一交界面,在第一交界面上放置31#-38#应变片,定型管8全部拔出;s3a6、在设定的不同高度处设置21#-28#应变片和11#-18#应变片,并在相应的高度上放置位移计d。放置应变片的位置如图8所示,放置位移计d的位置如图9所示。s4、安装施压组件,在钢管试件21的顶部安装加载板91,在反力架94的反力梁93与加载板91之间设置千斤顶92,千斤顶92和位移计d分别与数据采集仪连接;本试验采用200t液压千斤顶92,千斤顶92对钢管试件21顶部的加载板91施加竖向轴力。s5、采用荷载控制的分级加载制度,正式加载前为消除试件与加载装置之间的安装误差导致的虚位移,先进行预加载,预加荷载值为预估极限荷载的20%。通过液压千斤顶92缓慢加压,每级加载值取为预估极限荷载的10%。荷载通过加载板91缓慢下降施加竖向轴力给轴心受压试件,加载至该级荷载最大值,持荷时间为2min。在试件达到预估极限荷载的70%后,每级加载值取为预估极限荷载的5%,持荷时间为2min-3min整个加载过程的加载速率保持在0.6kn/s,位移计d和应变片的数据均由量测系统进行采集。当试件荷载下降到极限荷载的80%以下时,停止加载,试验结束。根据荷载级数记录各级荷载值和对应的应变及位移,同时绘制n-δ曲线,其中n为千斤顶92施加的轴向压力,δ为布置在所在组钢管试件21跨中截面的位移计d数值。当介质材料7分别是无、粗砂、预拌水泥灌浆料,获得钢管试件21分别对应ccftc-1n-δ曲线、ccftc-2n-δ曲线和ccftc-3n-δ曲线,如图11a所示,ccftc-1n-δ曲线在最高峰的极限承载力为581kn,竖向位移为7.27mm;如图11b所示,ccftc-2n-u曲线在最高峰的极限承载力为723kn,竖向位移为15.2mm;如图11c所示,ccftc-3n-δ曲线在最高峰的极限承载力为781kn,竖向位移为16.1mm。软件模拟计算模型与参数选取本试验采用有限元分析软件abaqus进行数值模型与分析,对于级配砂石和粉质黏土以及包裹介质,均采用较适宜沙土类材料的drucker-prager参数模型进行模拟。在数值模拟中,相关参数的输入见表2土层性质和见表3构件计算参数。土层名称重度(kn·m-3)粘聚力(kn·m-2)内摩擦角(°)粉质黏土192215级配砂石21030粗砂20032预拌水泥灌浆料223524表2土层性质构件类型弹性模量(kn·m-2)泊松比重度(kn·m-3)基岩(c10素砼浇筑)2.5e+070.226c40桩基底座2.8e+070.226钢管混凝土柱3.0e+070.227加载垫板2.0e+080.278表3构件计算参数采用c3d8r六面体单元进行合理网格划分,以保证网格为正方形的原则优先进行,有无侧向约束竖向支承柱有限元分析模型分别如图12-15所示。桩基中的钢筋笼41与桩混凝土42采用嵌入约束,加载板91与钢管混凝土22外侧钢管试件21采用绑定约束;其余材料之间的接触存在法向接触和切向接触,法向接触设置为“硬接触”,使用“罚函数”定义切向接触,摩擦系数根据材料间摩擦力不同设置为0.3~0.7不等。加载时,对于整体基岩3、外侧级配砂石5以及素土6采用固接,荷载施加时采用rp点耦合加载板91上表面进行轴向位移加载。数值模拟结果通过将介质材料7属性分别设置为粗砂和预拌水泥灌浆料,可以得到三条与试验相对应的荷载-位移曲线,如图16所示。所有试件在弹性阶段与试验值保持高度一致,在屈服阶段模拟试件较试验试件拥有更好的延性特征,这可能是由于在模拟时,材料诸如级配砂石5以及粗砂等处于非常均匀的理论状态,而试验中由于条件限制可能会有分布较为不均匀的情况出现,导致试件延性下降而造成的。表4给出了试验承载力极限值与有限元计算承载力极限值的比较,误差整体较小,总体吻合良好。根据以上计算方法、模拟装置的试验实测、软件模拟,分别获得没有介质材料7和另外两种介质材料7的情况下的钢管混凝土柱2的承载力极限值。表4从上表可知,本申请中的计算方法是完全可以运用的。以上仅为本发明创造的较佳实施例而已,并不用以限制本发明创造,凡在本发明创造的精神和原则之内所作的任何修改、等同替换和改进等,均应包含在本发明创造的保护范围之内。当前第1页12