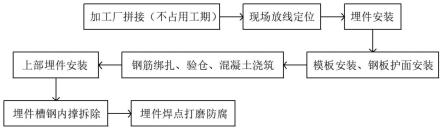
1.本发明涉及水运工程施工技术领域,具体涉及一种新型整体全钢浮式系船柱埋件施工方法。
背景技术:2.在航道扩能升级工程中,传统的系船柱埋件安装是通过预留二期槽待闸室到顶后再进行系船柱埋件安装等工序的施工方法。由于工程施工从脚手架平台搭设、二期槽模板拆除、凿毛到埋件层层拼接、钢筋绑扎、模板安装、混凝土分层浇筑再到模板拆除等工序复杂,花费大量的时间与人力,传统施工方法将会囤积大量的模板及钢管脚手架无法周转,不仅难以达到节约工期的目的,还需投入较大的成本。具体主要存在以下三个问题:1、埋件护角与导轨相互独立,容易造成移位,单套系船柱埋件包含两个护角、两个导轨,在安装过程中两两相互独立,现场分层施工,安装过程中需要反复定位,容易造成错位、移位,影响安装质量;2、作业空间小、施工困难、安全系数小,在安装过程中受空间的限制对埋件拼装、钢筋绑扎、模板安拆、混凝土振捣等都造成了不小的施工难度,安全系数较低;3、工序繁杂、工程量大、工期长,闸室到顶后再开始系船柱埋件施工,每个船闸24套浮式系船柱,系船柱埋件高度较大,需搭设脚手架、对二期槽凿毛、安装埋件、绑扎钢筋、模板安装等工序,工序复杂占用工期较长。由此,现急需一种焊缝少、制造容易、工期短、综合造价低的新型整体全钢浮式系船柱埋件施工方法。
技术实现要素:3.本发明要解决的技术问题是针对现有技术的不足,提供一种新型整体全钢浮式系船柱埋件施工方法。
4.本发明要解决的技术问题是通过以下技术方案实现的,本发明公开了一种新型整体全钢浮式系船柱埋件施工方法,包括如下步骤,步骤ⅰ,加工厂拼接:按照加工图纸,定位两个导轨间距和两个护角间距,两个导轨之间、导轨与护角之间均采用圆弧钢板连接,点焊将各构件固定,加固后将拼接好的埋件水平放置进行各纵向焊缝的连续焊接过程;步骤ⅱ,放线定位:闸室砼浇筑至于18.82高程后,通知测量人员按照施工图纸对系船柱埋件放样,放出系船柱埋件中心线位置;步骤ⅲ,系船柱埋件吊装:将已在加工厂拼装成整体的埋件运输至安装部位并利用汽车吊设备进行吊装;步骤ⅳ,钢板护面安装:将模板安装好后,按照施工图纸,对钢板护面进行焊接安装固定,采用槽钢10#a以45度角斜撑形式对埋件外侧进行支撑固定,且安装后浇筑在混凝土里;步骤
ⅴ
,钢筋绑扎、验仓、混凝土浇筑:按施工图纸要求进行钢筋绑扎、待监理验收后进行混凝土浇筑;步骤ⅵ,下一节埋件安装:待混凝土初凝后,重复拼装上述埋件,施工人员进入安装部位进行安装、调整和加固,直至达到系船柱顶部;步骤ⅶ,埋件内元字形槽钢内撑拆除:使用气割对内撑进行拆除,从而完成整个施工过程。
5.进一步,所述步骤ⅰ中的两个导轨定位间距1410mm;两个护角定位间距600mm,两个
导轨之间采用厚度为8mm、r647mm,弧长1414mm的第一圆弧钢板连接;导轨与护角之间采用厚度为8mm、r647mm,弧长352mm的第二圆弧钢板连接,所述导轨和护角通过第一圆弧钢板和第二圆弧钢板连接成ω形对称埋件截面结构。
6.进一步,所述埋件内壁通过槽钢组进行内部焊接支撑,所述槽钢组呈纵向间距1.5m布置排列,所述槽钢组每组包括一根长为600mm的第一槽钢、一根长为1410mm的第二槽钢和两根长均为548mm的第三槽钢,所述槽钢组在埋件截面内形成元字形。
7.进一步,所述槽钢组采用10#a槽钢制作,第一槽钢用于连接左右两侧的护角,第二槽钢用于连接左右两侧的导轨,第三槽钢用于通过左右对称连接方式将第一圆弧钢板与第二槽钢相连。
8.进一步,所述步骤ⅲ中吊装埋件的汽车吊设备的起重吊索具选择安全系数不小于6倍,吊装时利用卸扣将钢丝绳与导轨槽顶部的吊耳连接,起吊前严格按照起重作业技术要求进行作业。
9.进一步,所述步骤ⅲ包括埋件吊装就位后,利用线锤、花篮螺栓工具对其进行位置调整的过程,并在位置合格后,用槽钢进行外撑加固。
10.进一步,所述步骤ⅵ包括在拼装过程中先后对埋件节间对接缝打磨光洁和涂刷油漆防腐的步骤,并确保焊缝光滑过渡且焊缝余高不大于1mm,保证相邻导轨间错位小于1mm。
11.进一步,所述步骤ⅵ所需安装的单套系船柱埋件总高为22.2m且在步骤ⅰ中分为6节制作,其中最后一节高度为2.2m,其余5节高度均为4m,第一节埋件质量最大且为1.1t。
12.进一步,所述步骤ⅶ包括拆除时气割距离埋件表面不小于2mm,表面切割剩余部分采用角磨机打磨平滑并涂刷油漆及进行防腐。
13.本发明与现有技术相比具有以下优点:
14.(1)本发明将钢导轨、钢护角等分离式埋件结构调整为全断面钢结构,便于加工厂统一加工,使得物料钢结构的准备跟随适应施工进度的要求,在降低施工难度的前提下,提高了施工效率;
15.(2)本发明优化了浮式系船柱埋件的断面型式,创新地将六边形断面调整为圆形断面,克服了六边形断面拼接繁杂、焊缝多、制造效率低等缺点,大大提高了埋件整体性,确保了埋件安装精度;
16.(3)本发明将浮式系船柱埋件由二期施工调整为一期施工,减少了二期施工的插筋安装、模板安拆、施工平台搭设、混凝土凿毛等周转工序;同时创新采用了内外双撑加固技术,即埋件外部采用三道槽钢斜撑,埋件内部采用“元”型槽钢内撑,保证一期混凝土浇筑过程中埋件装置不易产生变形等问题。
附图说明
17.图1是本发明施工方法流程简图;
18.图2是本发明系船柱埋件的截面结构示意图;
19.图3是本发明船柱埋件的拼装结构前视图;
20.图4是本发明原有系船柱埋件截面结构形式示意图;
21.1-导轨,2-护角,3-第一圆弧钢板,4-第二圆弧钢板,5-第一槽钢,6-第二槽钢,7-第三槽钢,8-斜撑,9-原埋件,9a-系船柱体。
具体实施方式
22.如图1-4所示,本发明一种新型整体全钢浮式系船柱埋件施工方法,包括如下步骤,步骤ⅰ,加工厂拼接:按照加工图纸,定位两个导轨1间距和两个护角2间距,两个导轨1之间、导轨1与护角2之间均采用圆弧钢板连接,点焊将各构件固定,加固后将拼接好的埋件水平放置进行各纵向焊缝的连续焊接过程,可点焊将各构件固定,加固后,将拼接好的埋件水平放置进行各纵向焊缝的连续焊;
23.步骤ⅱ,放线定位:闸室砼浇筑至于18.82高程后,通知测量人员按照施工图纸对系船柱埋件放样,放出系船柱埋件中心线位置;
24.步骤ⅲ,系船柱埋件吊装:将已在加工厂拼装成整体的埋件运输至安装部位并利用汽车吊设备进行吊装,本步骤ⅲ中吊装埋件的汽车吊设备的起重吊索具选择安全系数不小于6倍,汽车吊设备选用25t汽车吊,吊装时利用卸扣将钢丝绳与导轨1槽顶部的吊耳连接,起吊前严格按照起重作业技术要求进行作业,且本步骤ⅲ包括埋件吊装就位后,利用线锤、花篮螺栓工具对其进行位置调整的过程,并在位置合格后,用槽钢进行外撑加固;
25.步骤ⅳ,钢板护面安装:将模板安装好后,按照施工图纸,对钢板护面进行焊接安装固定,采用槽钢10#a以45度角斜撑8形式对埋件外侧进行支撑固定,且安装后浇筑在混凝土里;
26.步骤
ⅴ
,钢筋绑扎、验仓、混凝土浇筑:按施工图纸要求进行钢筋绑扎、待监理验收后进行混凝土浇筑;
27.步骤ⅵ,下一节埋件安装:待混凝土初凝后,重复拼装上述埋件,施工人员进入安装部位进行安装、调整和加固,直至达到系船柱顶部,本步骤ⅵ包括在拼装过程中先后对埋件节间对接缝打磨光洁和涂刷油漆防腐的步骤,并确保焊缝光滑过渡且焊缝余高不大于1mm,保证相邻导轨1间错位小于1mm,本步骤ⅵ所需安装的单套系船柱埋件总高为22.2m且在步骤ⅰ中分为6节制作,其中最后一节高度为2.2m,其余5节高度均为4m,第一节埋件质量最大且为1.1t;
28.步骤ⅶ,埋件内元字形槽钢内撑拆除:使用气割对内撑进行拆除,从而完成整个施工过程,本步骤ⅶ包括拆除时气割距离埋件表面不小于2mm,表面切割剩余部分采用角磨机打磨平滑并涂刷油漆及进行防腐。
29.具体地,上述步骤ⅰ中的两个导轨1定位间距1410mm;两个护角2定位间距600mm,两个导轨1之间采用厚度为8mm、r647mm,弧长1414mm的第一圆弧钢板3连接;导轨1与护角2之间采用厚度为8mm、r647mm,弧长352mm的第二圆弧钢板4连接,所述导轨1和护角2通过第一圆弧钢板3和第二圆弧钢板4连接成ω形对称埋件截面结构。所述埋件内壁通过槽钢组进行内部焊接支撑,所述槽钢组呈纵向间距1.5m布置排列,所述槽钢组每组包括一根长为600mm的第一槽钢5、一根长为1410mm的第二槽钢6和两根长均为548mm的第三槽钢7,所述槽钢组在埋件截面内形成“元”字形,且安装后拆除可重复利用。所述槽钢组采用10#a槽钢制作,第一槽钢5用于连接左右两侧的护角2,第二槽钢6用于连接左右两侧的导轨1,第三槽钢7用于通过左右对称连接方式将第一圆弧钢板3与第二槽钢6相连,通过第一圆弧钢板3、第二圆弧钢板4而与导轨1和护角2焊接而组成原埋件9,实际应用时,系船柱体9a的滚动装置在原埋件9的导轨1中滑动,护角2用于对连接部件进行摩擦防护,从而实现系船柱的升降系船作用。
30.现有传统系船柱埋件一般通过预留二期槽进行二期施工,需要对二期槽绑扎钢筋、安拆模板、搭设脚手架、二期槽凿毛等工序。计算发现按照传统的施工方式施工,需耗费大量材料、人工,且对施工工期影响较大,还可采用根据系船柱埋件槽的尺寸,用五块8mm钢板拼装成钢板a,用两块8mm钢板拼装成钢板b,将钢板a、钢板b与系船柱导轨1、护角2在加工厂进行整体拼装,整条系船柱埋件分为6节(总高22.2m),其中5节4m,1节2.2m。导轨1与导轨1、倒角之间的钢板a、钢板b充当一期模板作用并和外部支撑槽钢一起埋入混凝土里边不拆除;槽内肋板间隔1米布置,混凝土浇筑后拆除,但该方式焊缝多,且难以掌握焊接精度,并需要耗费大量的加工厂焊接人工,而本技术方法整体全钢浮式系船柱埋件施工技术综合加工及施工两方面因素,使得焊缝较少、制造容易、工期短、造价最低。相对于传统二期安装施工工艺,简化工序、减少对施工材料的周转,降低了施工成本,同时最重要的是加快了施工效率,节约了大量的工期。
31.以上所述仅为本发明的优选实施例而已,并不用于限制本发明,对于本领域的技术人员来说,本发明可以有各种更改和变化。凡在本发明的精神和原则之内,所作的任何修改、等同替换及改进等,均应包含在本发明的保护范围之内。