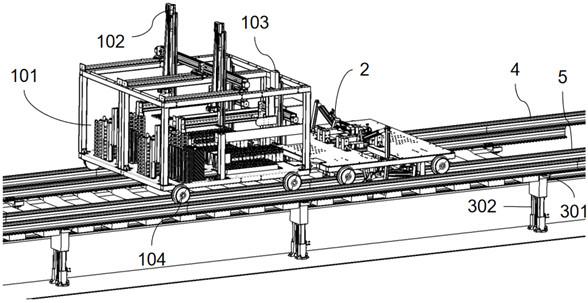
1.本发明属于建筑施工技术领域,尤其涉及一种基于智能控制的轨排自动拼装系统及方法。
背景技术:2.地铁轨排拼装的流程包括:摆放轨枕、摆放橡胶垫板、摆放铁垫板、上锚固螺栓、摆放轨下橡胶垫板、初步调整轨枕间距、紧固螺栓、摆放方正钢轨、精调轨枕间距、安装弹条与轨距垫板、上锚固t型螺栓、紧固t型螺栓、轨排存放等。受限于地铁地下隧道的尺寸限制,大型轨道铺设机不能进入隧道进行施工,因此需要在地上基地进行轨排拼装生产,拼装完成后再转运至地下隧道进行铺设。目前,地上基地的轨排拼装过程主要是利用龙门吊结合人工作业进行拼装操作,这种传统的人工拼装方式不仅费时费力,而且存在拼装一致性差、施工效率低等问题,导致铺设拼装工效和质量无法得到保障。本发明为填补轨排自动化拼装技术的空白,提出了一种地铁轨排自动拼装系统及方法,实现地铁轨排高度自动化的拼装作业,以提高轨排生产效率和精度。
技术实现要素:3.针对现有技术中存在的不足,本发明提供了一种基于智能控制的轨排自动拼装系统及方法,解决了传统的轨排拼装方法中存在的施工效率低、施工精度低、费时费力的问题。
4.本发明通过以下技术手段实现上述技术目的。
5.一种基于智能控制的轨排自动拼装系统,包括主机以及与主机信号连接的紧固件铺设操作子系统、轨枕位姿调整子系统、钢轨边距调整子系统;紧固件铺设操作子系统和轨枕位姿调整子系统分别集成于第一可移动底盘和第二可移动底盘上,第一可移动底盘和第二可移动底盘相互连接且均位于行车轨道上,行车轨道铺设于轨枕两侧,轨枕放置于枕下轨道上,且行车轨道的两条铁轨之间的距离大于轨排的两条铁轨之间的距离;多个钢轨边距调整子系统间隔均匀地固定安装在轨排拼装施工现场枕下轨道两侧空地上。
6.进一步地,所述紧固件铺设操作子系统包括物料库、物料取放操作装置、车体移动监测装置,物料库搭建于第一可移动底盘上表面,物料库中部留有物料铺设操作空间,物料库两侧平台上摆放有拼装单个轨排所需要的扣件和螺栓,且扣件和螺栓的摆放位置信息均存储于主机中;物料取放操作装置安装于物料库中,包括扣件抓取装置和螺栓抓取装置,扣件抓取装置和螺栓抓取装置的运动控制卡与主机之间通过pci通信协议进行通信;扣件抓取装置末端的抓取单元通过rs485总线与主机进行通信,用于抓取物料库中不同形状和尺寸的扣件;螺栓抓取装置末端的电动扳手通过rs485总线与主机进行通信,用于抓取物料库中不同尺寸的螺栓并完成螺栓的拧紧与拧松操作。
7.进一步地,所述车体移动监测装置包括编码器和第一高精度三维相机,编码器与
第一可移动底盘的驱动电机连接,测量第一可移动底盘车体的速度和当前位置;第一高精度三维相机安装在物料库操作空间上方的钢管架上,用于寻找固定在拼装现场的标志点,辅助定位当前第一可移动底盘车体位置,同时用于辅助物料取放操作装置寻找扣件或螺栓的安装位置;车体移动监测装置通过rs485通信协议与主机进行通信,采用pid控制算法闭环控制第一可移动底盘以及第二可移动底盘移动的距离。
8.进一步地,所述轨枕位姿调整子系统包括轨枕位姿调整机构和第二高精度三维相机,轨枕位姿调整机构整体由运动控制卡发出的脉冲信号控制,该运动控制卡与主机之间通过pci通信协议进行通信;轨枕位姿调整机构包括多个安装在第二可移动底盘底部以及两侧的第一电推缸,第二可移动底盘底部的第一电推缸伸缩端连接有用于在前后方向上对轨枕进行位姿调整的推动板;第二可移动底盘两侧的第一电推缸用于在左右方向上对轨枕进行位姿调整,其伸缩端与连杆连接,连杆穿过第二可移动底盘后通过销轴连接有推动板,且连杆中部与第二可移动底盘通过销轴连接;第二高精度三维相机安装在第二可移动底盘的底部,通过以太网与主机进行通信,用于获取当前轨枕的点云信息并传送到主机,由主机进行分析处理并根据分析结果控制轨枕位姿调整机构运动,推动轨枕进行位姿调整。
9.进一步地,所述钢轨边距调整子系统包括钢轨边距调整机构、钢轨顶升机构、第三高精度三维相机,钢轨顶升机构包括固定在地面上的第二电推缸,钢轨边距调整机构是一个固定在第二电推缸的推杆上的线性模组,钢轨放置在线性模组上;钢轨顶升机构用于调整钢轨的高度,钢轨边距调整机构用于调整钢轨的横向位置;钢轨顶升机构和钢轨边距调整机构均由运动控制卡发出的脉冲信号控制,该运动控制卡与主机之间通过rs485进行通信,实现数据交互;第三高精度三维相机安装在紧固件铺设操作子系统下方的第一可移动底盘底部,与主机通过以太网进行通讯,用于在第一可移动底盘移动时实时扫描下方钢轨,获取钢轨点云数据,并传递至主机,主机采用点云配准算法最终求解出钢轨边距调整机构和钢轨顶升机构的运动量,进而控制第二电推缸以及线性模组运动,对钢轨位姿进行调整。
10.一种利用上述基于智能控制的地铁轨排自动拼装系统的拼装方法,包括如下步骤:步骤1:首先将钢轨边距调整子系统中的钢轨边距调整机构、钢轨顶升机构安装固定在施工现场,然后铺设好枕下轨道,将轨枕放置于枕下轨道的相应安装位置上,然后于轨枕两侧铺设行车轨道;接着由现场施工人员将拼装用的扣件、螺栓放置在紧固件铺设操作子系统的物料库中,最后将拼装系统整体置于初始位置处;步骤2:主机控制第一可移动底盘和第二可移动底盘运动,带动紧固件铺设操作子系统和轨枕位姿调整子系统至第一个轨枕位置处;轨枕位姿调整子系统利用第二高精度三维相机扫描轨枕数据并传递至主机,主机识别出轨枕位姿,基于内部存储的轨排设计模型数据,采用迭代最近点点云配准算法计算出轨枕位姿调整子系统中轨枕位姿调整机构的运动量,进而推动轨枕调整至满足精度要求的安装位置处;主机控制第一可移动底盘和第二可移动底盘运动至下一轨枕位置处,继续进行轨枕位姿调整,直至完成整个轨排线上所有轨枕的位姿调整;步骤3:进行轨下物料的安装:主机根据内部预先存储的各扣件和螺栓的摆放位置
信息以及车体移动监测装置中的第一高精度三维相机扫描得到的各扣件和螺栓的安装位置信息,基于三维视觉技术对扣件以及螺栓安装区域进行识别与定位,并应用曲线插值拟合算法进行相应的运动路径规划;之后再控制扣件抓取装置以及控制螺栓抓取装置运动,完成当前位置处的轨下物料的安装;主机控制第一可移动底盘和第二可移动底盘运动至下一轨枕位置处,继续进行轨下物料的安装,直至整个轨排线上所有位置处的轨下物料全部安装完成;步骤4:由现场工作人员将钢轨置到已经铺设完成的轨下物料上,且保证钢轨端部放置于钢轨边距调整子系统上,主机控制第一可移动底盘和第二可移动底盘行走至第一块钢轨位置处,利用钢轨边距调整子系统中的第三高精度三维相机扫描钢轨数据并传递至主机,主机基于内部存储的轨排设计模型数据,同时采用点云配准算法计算出钢轨边距调整机构和钢轨顶升机构的运动量,进而控制线性模组以及第二电推缸运动,完成对第一块钢轨的位姿调整;主机控制第一可移动底盘和第二可移动底盘运动至下一钢轨位置处,继续进行钢轨位姿调整,直至完成整个轨排线上所有钢轨的位姿调整;步骤5:进行轨上物料的安装:主机根据内部预先存储的各扣件和螺栓的摆放位置信息以及车体移动监测装置中的第一高精度三维相机扫描得到的各扣件和螺栓的安装位置信息,控制扣件抓取装置以及螺栓抓取装置运动,完成当前位置处轨上物料的安装;主机控制第一可移动底盘和第二可移动底盘运动至下一轨枕位置处,继续进行轨上物料的安装,直至整个轨排线上所有位置处的轨上物料全部安装完成;步骤6:主机控制第一可移动底盘和第二可移动底盘行走,利用第三高精度三维相机进行复检;复检完成后,主机控制第一可移动底盘和第二可移动底盘运动,带动紧固件铺设操作子系统和轨枕位姿调整子系统回归到初始位置处。
11.进一步地,所述主机采用迭代最近点点云配准算法计算出轨枕位姿调整机构的运动量的具体过程如下:主机接收到第二高精度三维相机扫描得到的轨枕点云后,获取轨枕点云与目标点云之间的对应点对,基于对应点对,通过下式构造变换矩阵:利用构造的变换矩阵将扫描获取到的轨枕点云变换到目标点云的坐标下,然后通过下式获取轨枕点云与目标点云之间的误差函数:其中,表示轨枕当前姿态矩阵;表示轨枕当前位置矩阵;表示待配准轨枕点云数量;表示轨枕点云与目标点云配准位置;表示轨枕点云与目标点云配准姿
态;表示轨枕当前姿态与标准姿态偏差;表示轨枕当前位置与标准位置偏差;表示轨枕标准姿态;表示轨枕标准位置;误差函数大于设定的阈值时,则迭代上述变换矩阵构造过程,直至误差函数满足要求,然后利用迭代后满足要求的变换矩阵推算求解出轨枕位姿调整机构的运动量。
12.本发明具有如下有益效果:本发明为填补轨排自动化拼装技术的空白,结合视觉技术、机器人技术、多传感融合技术、控制技术和数字孪生技术,提出了一种地铁轨排自动拼装系统与拼装方法,实现了地铁轨排高度自动化的拼装以及位姿调整作业,提高了轨排施工效率,保证了施工精度,人工参与少,节省了大量的人力成本。
附图说明
13.图1为本发明所述轨排自动拼装系统局部结构三维示意图;图2为本发明所述轨排自动拼装系统局部主视图;图3为本发明所述紧固件铺设操作子系统结构示意图;图4为本发明所述轨枕位姿调整子系统结构示意图;图5为本发明所述钢轨边距调整子系统结构示意图;图6为本发明所述轨排自动拼装系统结构框图;图7为本发明所述轨排自动拼装系统拼装流程图。
14.图中:1-紧固件铺设操作子系统;101-物料库;102-扣件抓取装置;103-螺栓抓取装置;104-车体移动监测装置;2-轨枕位姿调整子系统;201-第一电推缸;202-连杆;3-钢轨边距调整子系统;301-钢轨边距调整机构;302-钢轨顶升机构;4-行车轨道;5-枕下轨道。
具体实施方式
15.下面结合附图以及具体实施例对本发明作进一步的说明,但本发明的保护范围并不限于此。
16.在本发明的描述中,需要理解的是,术语“安装”、“连接”、“固定”等应做广义理解,例如,可以是固定连接,也可以是可拆卸连接,或一体的连接,可以是直接相连,也可以是通过中间媒介间接相连,还可以是两个元件内部的连通。术语“第一”、“第二”、“第三”等的使用均是为了便于区分各名称相同的部件,因此不能理解为对本发明的限制。对于本领域的普通技术人员而言,可以根据具体情况理解上述术语在本发明中的具体含义。
17.如图1、2所示,本发明所述的基于智能控制的轨排自动拼装系统,包括主机以及与主机信号连接的紧固件铺设操作子系统1、轨枕位姿调整子系统2、钢轨边距调整子系统3。如图1、2所示,紧固件铺设操作子系统1和轨枕位姿调整子系统2分别集成于第一可移动底盘、第二可移动底盘上,第一可移动底盘与第二可移动底盘之间通过法兰盘连接,且第一可移动底盘与第二可移动底盘的行走轮均位于行车轨道4上,能够带动紧固件铺设操作子系统1和轨枕位姿调整子系统2在行车轨道4上运动,且行车轨道4的两条铁轨之间的距离大于轨排的两条铁轨之间的距离;钢轨边距调整子系统3间隔均匀地固定安装在轨排拼装施工现场,用于调整钢轨位姿。
18.如图1、3所示,紧固件铺设操作子系统1包括物料库101、物料取放操作装置、车体移动监测装置104。物料库101由钢管搭建而成,搭建于第一可移动底盘上表面,物料库101中部留有操作空间以供物料取放操作装置进行物料的铺设操作,操作空间两侧的物料库101平台上摆放有拼装单个轨排所需要的扣件(包括胶垫、铁垫板、轨下胶垫、轨距块、弹条)和螺栓(包括道钉螺栓和t型螺栓),各种扣件和螺栓在物料库101中的位置是确定的,且扣件和螺栓的位置信息均存储于主机中。
19.如图1、3、6所示,物料取放操作装置包括扣件抓取装置102和螺栓抓取装置103,扣件抓取装置102和螺栓抓取装置103的主体部分可以采用三轴操作机器人、四自由度机械臂、六自由度机械臂等机械结构,本实施例中均优选采用三轴操作机器人。三轴操作机器人固定在物料库101的钢管架上,三轴操作机器人的运动控制卡与主机之间通过pci通信协议进行通信,该运动控制卡通过脉冲信号控制三轴机器人运动。扣件抓取装置102的三轴操作机器人末端安装有抓取单元,用于抓取物料库101中不同形状和尺寸的扣件,抓取单元通过rs485总线与主机进行通信,其运动受主机控制。螺栓抓取装置103的三轴操作机器人末端安装有取放与拧紧一体化的电动扳手,用于抓取物料库101中不同尺寸的螺栓,电动扳手通过rs485总线与主机进行通信,在实时力矩反馈与螺栓扭矩控制技术的辅助之下,主机能够控制该一体化的电动扳手高效地完成螺栓的取、放、拧紧等一系列操作。
20.如图1、3、6所示,车体移动监测装置104包括编码器和第一高精度三维相机,编码器与第一可移动底盘的驱动电机连接,第一高精度三维相机安装在物料库101操作空间上方的钢管架上;编码器用于测量第一可移动底盘车体的速度和当前位置;第一高精度三维相机用于寻找固定在拼装现场的标志点,辅助定位当前第一可移动底盘车体位置;同时,物料取放操作装置抓取到扣件或螺栓后,第一高精度三维相机用于辅助物料取放操作装置寻找到扣件或螺栓的正确安装位置。车体移动监测装置104通过rs485通信协议与主机进行通信,采用pid控制算法闭环控制第一可移动底盘以及第二可移动底盘移动的距离;基于车体移动监测装置104的测量数据,主机能够控制紧固件铺设操作子系统1以及轨枕位姿调整子系统2在正确的位置完成铺设拼装任务,保证轨排拼装质量。
21.如图1、4、6所示,轨枕位姿调整子系统2包括轨枕位姿调整机构和第二高精度三维相机。轨枕位姿调整机构整体由运动控制卡发出的脉冲信号控制,包括多个安装在第二可移动底盘底部以及两侧的第一电推缸201;其中,第二可移动底盘底部的第一电推缸201伸缩端连接有推动板,用于在前后方向上对轨枕进行位姿调整;第二可移动底盘两侧的第一电推缸201用于实现在左右方向上对轨枕进行位姿调整,其伸缩端与连杆202连接,连杆202穿过第二可移动底盘后通过销轴连接有推动板,且连杆202中部与第二可移动底盘通过销轴连接。第二高精度三维相机安装在第二可移动底盘的底部,通过以太网与主机进行通信,用于获取当前轨枕的点云信息并传送到主机,由主机进行分析处理并根据结果控制轨枕位姿调整机构运动,从而推动轨枕进行位姿调整。
22.如图1、5、6所示,钢轨边距调整子系统3包括钢轨边距调整机构301、钢轨顶升机构302、第三高精度三维相机。钢轨顶升机构302包括固定在地面上的第二电推缸,钢轨边距调整机构301是一个固定在第二电推缸的推杆上的线性模组;钢轨放置在线性模组上,钢轨顶升机构302可带动钢轨上下移动,调整钢轨的高度,钢轨边距调整机构301可带动钢轨横向移动,调整钢轨的横向位置。钢轨顶升机构302和钢轨边距调整机构301均由运动控制卡发
出的脉冲信号控制,该运动控制卡与主机之间通过rs485进行通信,实现数据交互。第三高精度三维相机安装在紧固件铺设操作子系统1下方的第一可移动底盘底部,与主机通过以太网进行通讯,用于在第一可移动底盘移动时实时扫描下方钢轨,获取钢轨点云数据,并传递至主机,主机采用点云配准算法最终求解出钢轨边距调整机构301和钢轨顶升机构302的运动量,进而控制第二电推缸以及线性模组运动,对钢轨位姿进行调整。
23.利用上述地铁轨排自动拼装系统的拼装方法如图7所示,具体包括如下步骤:步骤1:拼装施工前,首先将钢轨边距调整子系统3中的钢轨边距调整机构301、钢轨顶升机构302安装固定在施工现场,然后铺设好枕下轨道5,将若干轨枕粗略地放置于枕下轨道5的相应安装位置上,然后于轨枕两侧铺设行车轨道4;接着由现场施工人员将拼装用的扣件、螺栓放置在紧固件铺设操作子系统1的物料库101中,最后将拼装系统整体置于初始位置处;步骤2:主机控制第一可移动底盘和第二可移动底盘运动,带动紧固件铺设操作子系统1和轨枕位姿调整子系统2至第一个轨枕位置处;轨枕位姿调整子系统2利用第二高精度三维相机扫描轨枕数据并传递至主机,主机识别出轨枕位姿,基于内部存储的轨排设计模型数据,采用迭代最近点点云配准算法计算出第一电推缸201的运动量,进而控制第一电推缸201运动,推动轨枕调整至满足精度要求的安装位置处;重复上述过程,直至完成整个轨排线上剩余轨枕的位姿调整;所述主机采用迭代最近点点云配准算法计算出第一电推缸201的运动量的具体过程如下:主机接收到第二高精度三维相机扫描得到的轨枕点云后,获取轨枕点云与目标点云之间的对应点对,基于对应点对,通过下式(1)构造变换矩阵,利用构造的变换矩阵将扫描获取到的轨枕点云变换到目标点云的坐标下;估计通过下式(2)获取到的轨枕点云与目标点云之间的误差函数,误差函数大于设定的阈值时,则迭代上述运算过程,直至误差函数满足要求,然后利用迭代后满足要求的变换矩阵推算求解出第一电推缸201的运动量即可;(1)(2)其中,表示轨枕当前姿态矩阵;表示轨枕当前位置矩阵;表示待配准轨枕点云数量;表示轨枕点云与目标点云配准位置;表示轨枕点云与目标点云配准姿态;表示轨枕当前姿态与标准姿态偏差;表示轨枕当前位置与标准位置偏差;表示轨枕标准姿态;表示轨枕标准位置。
24.步骤3:整个轨排线上的轨枕位姿全部调整完成后,进行轨下物料的安装:主机根据内部预先存储的各扣件和螺栓的位置信息以及车体移动监测装置104中的第一高精度三维相机扫描得到的各扣件和螺栓的安装位置信息,基于三维视觉技术对扣件以及螺栓安装区域进行识别与定位,并应用曲线插值拟合算法进行相应的运动路径规划;之后再控制扣件抓取装置102运动,先抓取胶垫放置到轨枕上,再抓取铁垫板放置到胶垫上,接着控制螺栓抓取装置103运动,抓取道钉螺栓并安装到位,然后拧紧;然后,主机控制扣件抓取装置102运动,抓取轨下胶垫并放置在铁垫板上,此时,该轨枕位置处的轨下物料安装完成;重复上述过程,直至整个轨排线上所有位置处的轨下物料全部安装完成;步骤4:整个轨排线上所有的轨下物料全部安装完成后,由现场工作人员将钢轨粗略放置到已经铺设完成的轨下物料上,且保证钢轨端部放置于钢轨边距调整子系统3上,主机继续控制第一可移动底盘和第二可移动底盘行走至第一块钢轨位置处,利用钢轨边距调整子系统3中的第三高精度三维相机扫描钢轨数据并传递至主机,主机基于内部存储的轨排设计模型数据,同时采用点云配准算法计算出钢轨边距调整机构301和钢轨顶升机构302的运动量,进而控制线性模组以及第二电推缸运动,完成对第一块钢轨的位姿调整;重复上述过程,直至完成整个轨排线上剩余钢轨的位姿调整;步骤5:整个轨排线上的钢轨位姿全部调整完成后,进行轨上物料的安装:主机根据内部预先存储的各扣件和螺栓的位置信息以及车体移动监测装置104中的第一高精度三维相机扫描得到的各扣件和螺栓的安装位置信息,控制扣件抓取装置102运动,先抓取轨距块并放置于对应的安装位置上,再抓取弹条并放置于对应的安装位置上,接着控制螺栓抓取装置103运动,抓取t型螺栓并安装到位,然后拧紧;重复上述过程,直至整个轨排线上所有位置处的轨上物料全部安装完成;步骤6:主机控制第一可移动底盘和第二可移动底盘行走,利用第三高精度三维相机进行复检以及数据存档;复检完成后,主机控制第一可移动底盘和第二可移动底盘运动,带动紧固件铺设操作子系统1和轨枕位姿调整子系统2回归到初始位置处。
25.所述实施例为本发明的优选的实施方式,但本发明并不限于上述实施方式,在不背离本发明的实质内容的情况下,本领域技术人员能够做出的任何显而易见的改进、替换或变型均属于本发明的保护范围。