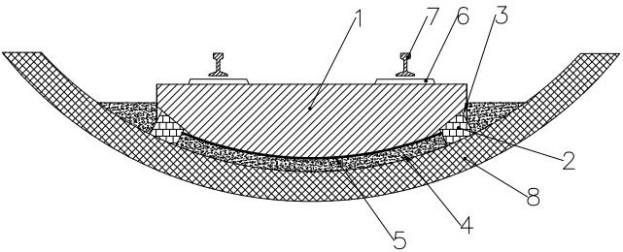
1.本发明涉及轨道交通技术领域,尤其是涉及一种全断面装配式轨道结构。
背景技术:2.目前整体式轨道结构主要分为现浇整体道床轨道结构和预制轨道结构。现浇整体道床存在现场浇筑钢筋混凝土量大、现场人工强度大、施工质量不易控制、运营阶段不易更换等问题,预制式整体道床因其标准化设计、工厂化预制、机械化施工、维修更换方便、结构可靠性高的特点成为目前轨道结构发展的重点和趋势。
3.目前的轨道交通预制轨道结构包括预制板、填充层和底座构成的三层结构,以及预制板和填充层构成的两层结构。其中,预制板、填充层和底座构成的三层预制轨道结构组成复杂,且因混凝土底座和填充层现场施工,结构复杂、装配化率低、施工工序较多、施工效率低。另外,现有预制板和填充层构成的两层预制结构,预制装配率低、隐蔽工程圬工量大,预制轨道板现场需采用专用预制板架设装备,且填充层未达到强度下需占用施工作业面,施工工效较低,在场地狭小的地下线不利于快速施工。
技术实现要素:4.本发明要解决的技术问题是:为了解决现有的预制轨道结构仍存在的装配率低、施工工序多、施工效率低的问题。
5.本发明提供一种全断面装配式轨道结构,包括预制轨道板和若干个预制支撑块,所述预制轨道板的两侧均设有若干个与预制支撑块卡合配合的预留导槽,所述预制轨道板的底部设有向外凸出的圆弧面,所述圆弧面和盾构管片之间形成填充层,所述预制轨道板的中部贯穿设有与填充层相连通的灌注孔。
6.作为本发明的一种实施方式,所述预制支撑块为楔形块,沿着所述预制支撑块的插入方向,所述预制支撑块厚度递减。
7.作为本发明的一种实施方式,所述预制支撑块的顶端设有第一弧面,所述预留导槽内设有与第一弧面相匹配的曲面,所述预制支撑块的底端设有与盾构管片相匹配的第二弧面。
8.作为本发明的一种实施方式,所述填充层的填充厚度均一。
9.作为本发明的一种实施方式,所述填充层的填充厚度为3~12cm。
10.作为本发明的一种实施方式,所述预制轨道板的两侧侧壁均设有多个第一预留孔。
11.作为本发明的一种实施方式,所述预制轨道板的顶部设有多个用于安装棱镜的第二预留孔。
12.作为本发明的一种实施方式,所有预留导槽呈两两对称分布在所述预制轨道板的两侧。
13.作为本发明的一种实施方式,所有预留导槽呈交错分布在所述预制轨道板的两
侧。
14.作为本发明的一种实施方式,所述预制轨道板的下表面、侧面和灌注孔内设置均有隔离层,所述隔离层与所述预制轨道板复合为一体化结构。
15.本发明的有益效果在于:其一,本发明的一种全断面装配式轨道结构,预制轨道板和预制支撑块均能够在工厂预制,仅填充层为现场浇筑,结构简单,提高了轨道结构的装配化率,减少了现场浇筑工作量。
16.其二,本发明的一种全断面装配式轨道结构,所有预制支撑块能够直接对预制轨道板进行支撑,预制支撑块与预留导槽的配合能够对预制轨道板产生纵横向限位力,避免预制轨道板发生意外偏移。
17.其三,本发明的一种全断面装配式轨道结构,在灌注现浇填充层时,圆弧面有利于预制轨道板下气体向两侧的排出,填充层的填充厚度均一,提高了浇筑质量,这样也减少了填充层的浇筑量。
18.其四,本发明的一种全断面装配式轨道结构,填充层的填充厚度小于12cm,圬工量小,浇筑质量更容易控制,降低了施工成本。
19.其五,本发明的一种全断面装配式轨道结构,预制支撑块的重量控制在10kg以内便于工人将预制支撑块安装至预留导槽内,降低人工操作预制支撑块难度。
附图说明
20.为了更清楚地说明本发明或现有技术中的技术方案,下面将对本发明或现有技术描述中所需要使用的附图作简单地介绍,显而易见地,下面描述中的附图是本发明的一些实施方式,对于本领域普通技术人员来讲,在不付出创造性劳动的前提下,还可以根据这些附图获得其他的附图。
21.图1为本发明的全断面装配式轨道结构的结构示意图;图2为预制轨道板的俯视图;图3为预制轨道板的侧视图;图4为预制支撑块的结构示意图;图5为预制轨道板的局部示意图。
22.附图标记:1、预制轨道板;11、灌注孔;12、第一预留孔;13、第二预留孔;2、预制支撑块;21、第一弧面;22、第二弧面;3、预留导槽;31、曲面;4、填充层;5、隔离层;6、承轨台;7、钢轨;8、盾构管片。
具体实施方式
23.下面将结合附图对本发明的技术方案进行清楚、完整地描述,显然,所描述的实施例是本发明一部分实施例,而不是全部的实施例。
24.在本实施方式中,如图1至图5所示,一种全断面装配式轨道结构,包括预制轨道板1和若干个预制支撑块2,预制轨道板1的两侧均设有若干个与预制支撑块2卡合配合的预留
导槽3,预制轨道板1的底部设有向外凸出的圆弧面,圆弧面和盾构管片8之间形成填充层4,预制轨道板1的中部贯穿设有与填充层4相连通的灌注孔11。
25.基于上述预制轨道结构的现有结构,本发明实施例的特征之一在于,预制轨道板1为工厂化预制,仅填充层4为现场浇筑,结构简单,轨道结构中预制结构占道床结构的比例不低于76%,提高轨道结构的装配化率,减少现场浇筑工作量20%以上。
26.具体地,所述预制轨道板1的厚度较现有预制轨道板厚度加厚,一方面能满足填充层4的最小结构受力要求;另一方面是在调研了不同工程不同线路盾构施工误差基础上,保证预制轨道板1能适应90%以上的盾构竖向、横向偏差以及曲线超高及隧道偏移的影响。
27.进一步地,在预制轨道板1的上部设置有承轨台6,通过扣件将钢轨7固定在预制轨道板1的承轨台6上。承轨台6的纵向间距为固定值,预制轨道板1上承轨台6的数量优选为6对、8对。
28.并且,在所述承轨台6的上部设置有扣件螺栓孔,扣件螺栓孔深入预制轨道板1内,扣件螺栓孔用来连接扣件、固定钢轨7。施工阶段可作为预制轨道板1的吊装孔,经计算可满足预制轨道板1的吊装要求,并减少现有预制轨道板1结构上的吊装孔。
29.在所述预制轨道板1的侧面有多个第一预留孔12,通过第一预留孔12的设置一方面能够固定板下粘贴性隔离层5;另一方面当预制轨道板1位于线路大坡度地段时,板两侧需安装模板,防止填充层4的溢出,第一预留孔12可用于固定模板。
30.此外,在所述预制轨道板1的上面还预留有多个安装棱镜的第二预留孔13,用于预制轨道板1的精调、定位。
31.本发明实施例的特征之二在于,所述预制支撑块2为楔形块,施工阶段采用楔形块对预制轨道板1进行支撑和固定,无需特殊支撑、固定机械,轨道板断面较大,自重较大,无需压板装置,可防止轨道板施工上浮,节省施工机具、减少现场人工工程量,降低施工成本。
32.具体地,所述预制支撑块2为厂内预制结构,插入预制轨道板1下部时,沿着预制支撑块2的插入方向,预制支撑块2的厚度递减,即朝下端头薄,朝上端头厚,并且预制支撑块2沿线路方向的宽度略小于预制板侧面预留导槽3的宽度,方便预制支撑块2的安装。
33.本发明实施例中的预留导槽3在预制轨道板1两侧对称布置,预留导槽3的数量可为2对、3对、4对,可满足预制支撑块2的安装要求,以及预制轨道板1的限位要求。预留导槽3沿线路方向的分布,可以采取两两对称分布在预制轨道板1的两侧,也可以采用交错分布在预制轨道板1的两侧,但这两种布置方式都需保证预制支撑块2不作用在盾构管片8缝隙上,且每对预留导槽3分布在线路中心线的两侧,保证垂直于线路方向的每对预留导槽3至少有一个不在盾构管片8的缝隙中。
34.同时,预留导槽3在预制轨道板1侧面向板内凹陷,由板的侧面斜向板底面,所述预制支撑块2的顶端设有第一弧面21,所述预留导槽3内设有与第一弧面21相匹配的曲面31;考虑到本发明实施例中轨道结构下部为圆形盾构管片8,所述预制支撑块2的底端设有与盾构管片8相匹配的第二弧面22;当预制支撑块2运用至例如马蹄形断面隧道结构时,也可以根据具体的轨道结构进行适应性改变以使得预制支撑块2的下表面与隧道结构下部充分接触。
35.通过上述弧面和曲面31的设计,在预制轨道板1的厚度和宽度在满足预制轨道板1占道床结构装配化率不低于76%的前提下,适应盾构、马蹄形隧道至少90%的垂向和横向偏
差,能满足填充层4的强度要求;同时接触面不小于60cm
²
,满足支撑强度要求。
36.本发明实施例的特征之三在于,预制轨道板1的底部设有向外凸出的圆弧面,利于灌注现浇填充层4时板下气体向两侧的排出,提高填充层4现浇质量。同时相较于现有技术中的平底结构,加厚板中间的高度,减少现浇工程量,提高装配率。
37.具体地,预制轨道板1的圆弧面的截面所在的圆与盾构管片8的截面所在的圆共圆心,即,填充层4的填充厚度均一,但在实际的施工作业时,考虑到结构施工偏差的情况下,厚度可能会出现微小的波动。
38.其中,填充层4的厚度为30mm~120mm,最小厚度可满足填充层4在列车疲劳荷载作用下不压溃,最大厚度可控制轨道结构占道床结构的装配化率不低于76%。
39.本发明实施例在填充层4现场浇筑时,可通过灌注孔11向填充层4灌注填充材料,灌注孔11优选为两个;填充层4的材料为微膨胀水泥灌浆料,具有流动性好、微膨胀、凝结速度快的功能,免振捣,可控制硬化过程中的收缩,保证板下填充密实,同时可在短时间内达到强度要求,同时,无需布置钢筋,减少现场配筋及布置钢筋笼工序,减少施工工序,节约人工,提高施工工效,降低施工成本。
40.浇筑时,可同时浇筑于多块预制轨道板1下,减少施工中的磨具数量和支模人工量,并且每隔几块预制轨道板1,在预制轨道板1之间设置伸缩缝,相隔预制轨道板1数量优选为2块、3块、4块。
41.待填充层4凝结达到强度要求后,由填充层4和预制支撑块2共同对预制轨道板1起支撑和限位作用,保证预制轨道板1受力均匀。
42.预制支撑块2在施工阶段对预制轨道板1起支撑和限位作用,无需额外预制轨道板1的固定和安装机械;预制轨道板1的厚度高、自重大,填充层4的现浇量少,填充层4灌注及养护阶段无需压板装置,即可保证板不上浮。减少施工作业设备、减少现场人工作业量,提高施工工效,降低施工成本。
43.在预制轨道板1投产时,预制轨道板1可根据板厚不同分为几种不同板型,优选的可为1-3种,其长度也可分为两种不同板型,以使得能够适应半径不下于300m的曲线和直线地段。
44.最后应说明的是:以上各实施例仅用以说明本发明的技术方案,而非对其限制;尽管参照前述各实施例对本发明进行了详细的说明,本领域的普通技术人员应当理解:其依然可以对前述各实施例所记载的技术方案进行修改,或者对其中部分或者全部技术特征进行等同替换;而这些修改或者替换,并不使相应技术方案的本质脱离本发明各实施例技术方案的范围。