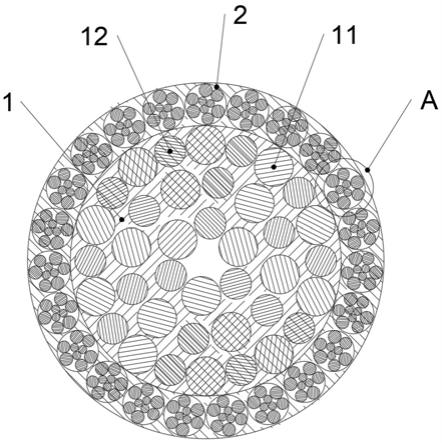
1.本发明涉及摩擦材料结构领域,具体为用于摩擦材料的预氧丝包芯纱的制作方法。
背景技术:2.摩擦材料是一种应用在动力机械上,依靠摩擦作用来执行制动和传动功能的部件材料,它主要应用在制动器衬片和离合器面片上,其中刹车片用于制动,离合器片用于传动。任何机械设备与运动的各种车辆都必须要有制动或传动装置,摩擦材料是这种制动或传动装置上的关键性部件,它最主要的功能是通过摩擦来吸收或传递动力,如离合器片传递动力,制动片吸收动能,它们使机械设备与各种机动车辆能够安全可靠地工作。
3.中国专利文献(公开号:cn105041926a)公开了一种金属摩擦材料,其组分的重量百分比是:粘结剂,由丁腈改性酚醛树脂和丁腈橡胶粉组成;增强纤维,由芳纶纤维、碳纤维和钢纤维组成;润滑剂,由鳞片石墨和人造石墨组成;填料,包括重晶石、摩擦粉、锆英粉和膨胀蛭石;制备方法包括配料、混料、压制、热处理和机械加工。该发明的一种少落灰低金属摩擦材料及其制备方法,具有不易锈蚀,制动噪音低,制动热衰退少,更耐磨,落灰少的特点。
4.但是这种摩擦材料中包含价格比较昂贵的碳纤维,因此生产成本较高;此外,这种摩擦材料还存在着质量较大和不容易混纺的问题,使用起来较为不便。
技术实现要素:5.本发明要解决的技术问题是提供一种价格便宜、使用方便的用于摩擦材料的预氧丝包芯纱的制作方法。
6.本发明解决上述技术问题所采取的技术方案:一种用于摩擦材料的预氧丝包芯纱的制作方法:先将无碱玻璃纤维直接纱制成无碱玻璃纤维,再将无碱玻璃纤维和铜丝送入捻线机制成内芯,捻线机对铜丝和无碱玻璃纤维的捻度系数为每米捻26~28下,捻向为z形;将涤纶纤维、粘胶纤维、预氧丝纤维和短切玻璃纤维通过制条机制成混纺条;制成的混纺条通过并条机进行均匀并条,通过空气摩擦纺纱机对并条好的混纺条进行抽丝,将抽出来的混纺丝均匀包缠内芯上形成皮纱,所述芯纱和皮纱共同构成包芯结构的绳状纱线,绳状纱线形成摩擦材料的基材。
7.使用价格便宜的预氧丝纤维作为碳纤维的替代品制成新型的摩擦材料,该摩擦材料与现有摩擦材料的机械性能相差无几,同时更加低碳环保。
8.作为本发明的一种优选技术方案,所述皮纱混纺时加入表面活性剂。纤维之间抱合力不足的情况下,皮纱在混纺时无法聚集在一起,通过表面活性剂使纤维聚在一起。
9.作为本发明的一种优选技术方案,所述无碱玻璃纤维直接纱的单丝直径为16μm~17μm。此种规格的无碱玻璃纤维宽度适中,具有较好的机械强度。
10.作为本发明的一种优选技术方案,所述铜丝为黄铜丝和紫铜丝中的一种,根据不
同使用需求选择相应的铜丝。
11.作为本发明的一种优选技术方案,所述铜丝的横截面直径为0.12mm~0.20mm。本发明选择规格较细的铜丝,一则能与无碱玻璃纤维直接纱形成紧密抱合;二来细的铜丝耐磨性好,能够提高摩擦材料的耐磨性提高。
12.本发明的有益效果是:该种用于摩擦材料的预氧丝包芯纱结构通过空气摩擦纺纱机将混合纤维层均匀缠包于并行的无碱玻璃纤维直接纱和铜丝表面,制成包芯结构的绳状纱线,应用于摩擦材料的增强基材。相比于传统结构,本发明的基材皮层材料选取价格相对较为低廉的预氧丝纤维代替价格比较昂贵的碳纤维,预氧丝纤维质量轻,易于混纺,并能使摩擦材料保持原有的摩擦性能。
附图说明
13.附图用来提供对本发明的进一步理解,并且构成说明书的一部分,与本发明的实施例一起用于解释本发明,并不构成对本发明的限制。在附图中:图1是本发明用于摩擦材料的预氧丝包芯纱结构的结构示意图;图2是本发明用于摩擦材料的预氧丝包芯纱结构图1中a处的放大结构示意图;图中:1、芯纱;11、无碱玻璃纤维直接纱;12、铜丝;2、皮纱;21、涤纶纤维;22、粘接纤维;23、预氧丝纤维;24、短切玻璃纤维。
具体实施方式
14.以下结合附图对本发明的优选实施例进行说明,应当理解,此处所描述的优选实施例仅用于说明和解释本发明,并不用于限定本发明。
15.现有的用于摩擦材料的包芯纱的结构如图1所示,其包含价格较昂贵的碳纤维,碳纤维含碳量在90%以上,是一种耐高温的优良材料。但是碳纤维价格过于昂贵,使得摩擦材料的生产成本过高,生产厂家的利润较低。
16.现有的用于摩擦材料的包芯纱包括:芯纱和皮纱。芯纱成分为中碱玻璃纤维直接纱和铜丝,两者并行排列。皮纱成分包括:腈纶纤维、粘胶纤维、短切玻璃纤维和碳纤维,上述材料进行混纺制成皮纱。再通过一般纺纱机将混合纤维层均匀缠包于上述的无碱玻璃纤维直接纱和铜丝表面,制成包芯结构的绳状纱线,以形成应用于摩擦材料的增强基材。
17.本发明采取的现使用与碳纤维性能相近的预氧丝纤维作为替代材料加工皮纱,能够节约生产成本。预氧丝纤维质量轻,易于混纺,并能使摩擦材料保持原有的摩擦性能。
18.本发明使用无碱玻璃纤维直接纱,该无碱玻璃纤维直接纱的制作方法为:将氰化乙烯类单体13份、aes树脂18份、石棉段9份、月桂二酸10份、三聚磷酸钠7份、玻璃纤维矿物粉6份、乙基三甲氧基硅烷12份置于搅拌机中搅拌至混合均匀,然后将混合物放入马弗炉中以生成玻璃液,然后将玻璃液送至孔径为0.013毫米的多孔漏板处进行高速挤出,生成200tex~300tex的玻璃纤维原纱,其单丝直径小于或等于13微米。然后通过喷雾器冷却成玻璃纤维原纱。
19.接着再将玻璃纤维原纱缠绕到一个收线装置上,这种收线装置可以是具有耐酸性的纱锭,然后将耐酸纱锭连同玻璃纤维原纱放入酸沥滤槽中,然后槽中加入一定浓度的酸,加热酸到50度左右,保持这一温度直至酸沥滤完成,然后把玻璃纤维原纱放入水槽中清洗
直至清洗完成,便可以将玻璃纤维原纱加工成无碱玻璃纤维直接纱。酸处理可以去除玻璃纤维内的大部分碱性混合物,这样便可以获得机械性能更好的无碱玻璃纤维纱。一般的中碱玻璃纤维纱的折弯使用寿命只有2000次,而无碱玻璃纤维纱的折弯寿命却在5000次以上,且无碱玻璃纤维纱的抗拉强度远高于中碱玻璃纤维纱,无碱玻璃纤维纱更适合作为刹车带的组成基材。
20.再将多根无碱玻璃纤维纱进行捻合制成无碱玻璃纤维直接纱。无碱玻璃纤维直接纱的单丝直径为16μm~17μm。再将多根无碱玻璃纤维直接纱捻合成股线,并将股线与铜丝并行排列,无碱玻璃纤维直接纱捻合时为100根1股,超过100根这个临界值使股线强度将会下降,在摩擦材料使用的过程中易断裂开。上述铜丝12为黄铜丝和紫铜丝中的一种;所述铜丝12的横截面直径为0.12mm~0.20mm的细铜丝,此种铜丝延展性较好,具有较强的机械强度,能够增加摩擦材料的抗拉强度。
21.还可将股线与铜丝进行捻合,这样能够进一步增加内芯的抗拉强度,使股线能够与铜丝一起受力,减少两者单独受力的几率。
22.皮纱2,所述皮纱2通过空气摩擦纺纱机均匀缠包于并行的无碱玻璃纤维直接纱11和铜丝12表面;所述芯纱和皮纱共同构成包芯结构的绳状纱线。所述皮纱2包括涤纶纤维21、粘胶纤维22、预氧丝纤维23和短切玻璃纤维24,所述皮纱2由涤纶纤维21、粘胶纤维22、预氧丝纤维23和短切玻璃纤维24混合纺成。
23.预氧丝纤维与碳纤维的性能区别在于,预氧丝纤维质量轻,易于混纺,加工成皮纱较为方便。碳纤维的强度远高于预氧丝纤维23,与铜丝12配合能弥补这一缺点,加工工艺:将股线和铜丝的线头并行喂入空气摩擦纺纱机,或将股线与铜丝进行捻合后送入空气摩擦纺纱机。再将涤纶纤维21、粘胶纤维22、预氧丝纤维23和短切玻璃纤维24喂入空气摩擦纺纱机的纺杯内,通过空气摩擦纺纱机将上述材料均匀缠包与内芯上,形成用于摩擦材料的包芯结构的绳状纱线。
24.在通过空气摩擦纺纱机进行混纺前,将制成皮纱的各个纤维投入表面附着剂进行浸泡,这样晾干后各个纤维之间的抱合力便会增强,在混纺时更容易聚集在一起,增加纤维的可纺性。