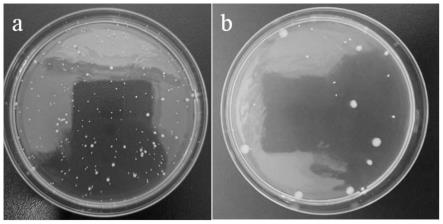
0.01%~0.1%的mos2纳米粒子,经过纺丝后,mos2纳米粒子均匀地分布于纤维的内部和表面,在达到优异的抑菌效果的同时,抑菌效果稳定长久,经过多次水洗后,抑菌性仅有轻微的下降,远远优于现有的经抗菌整理剂处理的纤维织物。优选地,所述mos2纳米粒子的添加量占纺丝液总质量的0.02%~0.08%,更优选为0.05%。
9.本发明中,所述mos2纳米粒子的粒径范围优选为3~10nm,例如可以为4nm、5nm、6nm、 7nm、8nm、9nm等。发明人经试验发现,mos2纳米粒子的粒径对于抑菌性能有很大的影响。当mos2的粒径低于10nm时,可在太阳光照条件下大幅提高抑菌效果;但当粒径高于10nm 时,其抑菌效果有大幅度下降。因此,当mos2纳米粒子的粒径分布范围为3~10nm时,制备的抗菌再生纤维素材料具有较好的抑菌效果。
10.另外,再生纤维素纤维的强度低于棉纤维,为了提高其强度,本发明在黏胶纺丝原液中加入2%~10%的丙烯腈,丙烯腈分子中具有c-c双键和c-n三键等活性基团,丙烯腈的加入使得粘胶纺丝液中化学性质活泼的基团增加,能够与纤维素分子上存在的-oh、氢键等基团发生双键加成反应,从而实现纤维素分子的交联,聚合度的增加使得再生纤维素材料的强力大大提高。优选地,所述丙烯腈的添加量占纺丝液总质量的4%~9%,更优选为9%。
11.本发明中,所述黏胶纺丝原液可从各大化纤工厂购买得到,其是化纤工厂生产再生纤维素纤维(黏胶纤维)的原料,主成分为纤维素。
12.本发明还提供了所述的一种抗菌再生纤维素材料的制备方法,包括以下步骤:
13.s1.将丙烯腈与mos2纳米粒子混合,搅拌均匀后,得到均匀的溶液;
14.s2.将上述溶液按比例加入到黏胶纺丝原液中,搅拌均匀后得到纺丝液,接着将所述纺丝液进行纺丝,即得到所述抗菌再生纤维素材料。
15.进一步地,步骤s1中,搅拌时,控制体系的温度为60~65℃。
16.进一步地,步骤s1中,搅拌时的转速为400~450rpm。
17.进一步地,步骤s2中,搅拌时的转速为100~150rpm。
18.本发明还提供了一种抗菌再生纤维素面料,所述抗菌再生纤维素面料是由所述的抗菌再生纤维素材料经织造工艺得到的。
19.进一步地,所述抗菌再生纤维素面料的克重为120~123g/m2,断裂强力超过300n,对金黄色葡萄球菌和大肠杆菌的抑菌率超过95%。
20.与现有技术相比,本发明的有益效果在于:
21.1.本发明在再生纤维素材料的制备过程中加入了丙烯腈和二硫化钼纳米粒子(mos2),利用二硫化钼纳米粒子在光催化下产生活性氧的特性,赋予了纤维良好的抑菌性能,同时由于mos2纳米粒子均匀地分布于纤维的内部和表面,在达到优异的抑菌效果的同时,抑菌效果稳定长久,经过多次水洗后,抑菌性仅有轻微的下降;另外,利用丙烯腈与纤维素之间发生的双键加成反应,实现再生纤维素的交联,从而使得再生纤维素材料的强力大大提高。
22.2.本发明制备的再生纤维素面料制备工艺简便,将丙烯腈和二硫化钼纳米粒子这两种物质按照比例加入纺丝液,通过纺丝、制造工艺即可得到黏胶面料,相比于现有技术中的抗菌整理工艺,本发明大大简化了制备工艺;另外,加工后的黏胶面料不但具有优异的抑菌性能,而且织物强力可以提高20%以上,大大提高了面料的使用性能。
附图说明
23.图1为实施例1的抑菌高强黏胶织物对于金黄葡萄球菌(a)、大肠杆菌(b)的抑菌效果图。
具体实施方式
24.下面结合附图和具体实施例对本发明作进一步说明,以使本领域的技术人员可以更好地理解本发明并能予以实施,但所举实施例不作为对本发明的限定。
25.除非另有定义,本文所使用的所有的技术和科学术语与属于本发明的技术领域的技术人员通常理解的含义相同。在本发明的说明书中所使用的术语只是为了描述具体的实施例的目的,不是旨在于限制本发明。本文所使用的术语“及/或”包括一个或多个相关的所列项目的任意的和所有的组合。
26.下述实施例中所使用的实验方法如无特殊说明,均为常规方法,所用的材料、试剂等,如无特殊说明,均可从商业途径得到。
27.以下实施例和对比例中,所使用的黏胶纺丝液购自新乡化纤有限公司,主要成分为纤维素;各种粒径的mos2纳米粒子均购自南京先丰纳米材料科技有限公司。
28.1.纺丝液的配制方法为:
29.第一步:首先在搅拌容器中加入丙烯腈,控制温度为60~65℃,逐渐添加mos2,搅拌均匀,搅拌转速介于400~450rpm,得到均匀的溶液。
30.第二步:将上述溶液按比例缓慢加入黏胶纺丝液,搅拌均匀,搅拌转速介于100~150rpm,即可进行纺丝。
31.2.实施例及对比例的抑菌高强黏胶织物的织造方法为:
32.开清棉(打手速度400-500r/min,罗拉速度10-11r/min)
→
络丝(筒槽速度700-900r/min,张力1.3-2g)
→
捻丝(纱线捻系数375-430)
→
并丝(1.5-2倍后区牵伸倍数)
→
整经(地经张力2-6g,边经张力4-8g)
→
织造(经密
×
纬密=434
×
270)。
33.3.普通黏胶织物(未添加丙烯腈和mos2)的织造方法为:
34.开清棉(打手速度350-400r/min,罗拉速度8-10r/min)
→
络丝(筒槽速度600-800r/min,张力1-1.5g)
→
捻丝(纱线捻系数360-397)
→
并丝(1.5-2倍后区牵伸倍数)
→
整经(地经张力1-4g,边经张力2-5g)
→
织造(经密
×
纬密=434
×
270)。
35.实施例1
36.本实施例中,原料的成分为:mos2(粒径范围5~8nm,占纺丝液质量的0.072%)、丙烯腈(占纺丝液质量的8%)和黏胶纺丝液(占纺丝液质量的91.928%)。
37.按照上述方法将mos2、丙烯腈和黏胶纺丝液配制成纺丝液,并织造成为抑菌高强黏胶织物,克重为121.7g/m2。
38.对制备的抑菌高强黏胶织物进行断裂强力和抑菌性能进行测试,结果如表1和附图1所示。其中测试依据的标准为:
39.抗菌性(抑菌率):gb 20944.3-2008-t《纺织品抗菌性能的评价第3部分:振荡法》测试。断裂强力:按照gb/t 3923.1-2013《纺织品织物拉伸性能第1部分:断裂强力和断裂伸长率的测定(条样法)》测定。
40.表1实施例1抑菌高强黏胶织物性能测试
[0041][0042]
注:“—”表示抑菌性能低于75%,表明无抑菌效果。
[0043]
从表1的结果可以看出,本实施例制备的黏胶织物,其断裂强力显著高于普通黏胶织物;并且,该黏胶织物还具备了抑菌性能,对于金黄色葡萄球菌和大肠杆菌均具有良好的抑制效果,并且水洗20次后,抑菌性能仅有轻微下降,显示出良好的抑菌稳定性。
[0044]
图1的结果进一步证明了本实施例制备的黏胶织物对于金黄色葡萄球菌和大肠杆菌均具有良好的抑制效果。
[0045]
实施例2
[0046]
本实施例中,原料的成分为:mos2(粒径范围5~8nm,占纺丝液质量的0.05%)、丙烯腈(占纺丝液质量的6%)和黏胶纺丝液(占纺丝液质量的93.95%)。
[0047]
按照上述方法将mos2、丙烯腈和黏胶纺丝液配制成纺丝液,并织造成为抑菌高强黏胶织物,克重为121.4g/m2。
[0048]
对制备的抑菌高强黏胶织物进行断裂强力和抑菌性能进行测试,结果如表2所示。
[0049]
表2实施例2抑菌高强黏胶织物性能测试
[0050][0051]
实施例3
[0052]
本实施例中,原料的成分为:mos2(粒径范围5~8nm,占纺丝液质量的0.025%)、丙
烯腈(占纺丝液质量的4%)和黏胶纺丝液(占纺丝液质量的95.975%)。
[0053]
按照上述方法将mos2、丙烯腈和黏胶纺丝液配制成纺丝液,并织造成为抑菌高强黏胶织物,克重为121.9g/m2。
[0054]
对制备的抑菌高强黏胶织物进行断裂强力和抑菌性能进行测试,结果如表3所示。
[0055]
表3实施例3抑菌高强黏胶织物性能测试
[0056][0057]
实施例4
[0058]
本实施例中,原料的成分为:mos2(粒径范围5~8nm,占纺丝液质量的0.04%)、丙烯腈(占纺丝液质量的4%)和黏胶纺丝液(占纺丝液质量的95.96%)。
[0059]
按照上述方法将mos2、丙烯腈和黏胶纺丝液配制成纺丝液,并织造成为抑菌高强黏胶织物,克重为120.8g/m2。
[0060]
对制备的抑菌高强黏胶织物进行断裂强力和抑菌性能进行测试,结果如表4所示。
[0061]
表4实施例4抑菌高强黏胶织物性能测试
[0062][0063]
实施例5
[0064]
本实施例中,原料的成分为:mos2(粒径范围5~8nm,占纺丝液质量的0.072%)、丙烯腈(占纺丝液质量的4%)和黏胶纺丝液(占纺丝液质量的95.928%)。
[0065]
按照上述方法将mos2、丙烯腈和黏胶纺丝液配制成纺丝液,并织造成为抑菌高强黏胶织物,克重为122.9g/m2。
[0066]
对制备的抑菌高强黏胶织物进行断裂强力和抑菌性能进行测试,结果如表5所示。
[0067]
表5实施例5抑菌高强黏胶织物性能测试
[0068][0069]
实施例6
[0070]
本实施例中,原料的成分为:mos2(粒径范围5~8nm,占纺丝液质量的0.025%)、丙烯腈(占纺丝液质量的9%)和黏胶纺丝液(占纺丝液质量的90.975%)。
[0071]
按照上述方法将mos2、丙烯腈和黏胶纺丝液配制成纺丝液,并织造成为抑菌高强黏胶织物,克重为121.7g/m2。
[0072]
对制备的抑菌高强黏胶织物进行断裂强力和抑菌性能进行测试,结果如表6所示。
[0073]
表6实施例6抑菌高强黏胶织物性能测试
[0074][0075]
对比例1
[0076]
本对比例中,原料的成分为:mos2(粒径范围10~15nm,占纺丝液质量的0.072%)、丙烯腈(占纺丝液质量的9%)和黏胶纺丝液(占纺丝液质量的90.928%)。
[0077]
按照上述方法将mos2、丙烯腈和黏胶纺丝液配制成纺丝液,并织造成为抑菌高强
黏胶织物。
[0078]
对制备的抑菌高强黏胶织物进行断裂强力和抑菌性能进行测试,结果如表7所示。
[0079]
表7对比例1抑菌高强黏胶织物性能测试
[0080][0081][0082]
对比例2
[0083]
本对比例中,原料的成分为:mos2(粒径范围12~15nm,占纺丝液质量的0.072%)、黏胶纺丝液(占纺丝液质量的99.928%)。
[0084]
按照上述方法将mos2和黏胶纺丝液配制成纺丝液,并织造成为抑菌黏胶织物。
[0085]
对制备的抑菌黏胶织物进行断裂强力和抑菌性能进行测试,结果如表8所示。
[0086]
表8对比例2抑菌黏胶织物性能测试
[0087][0088]
对比例3
[0089]
本对比例中,原料的成分为:mos2(粒径范围5~8nm,占纺丝液质量的0.072%)、黏胶纺丝液(占纺丝液质量的99.928%)。
[0090]
按照上述方法将mos2和黏胶纺丝液配制成纺丝液,并织造成为抑菌黏胶织物。
[0091]
对制备的抑菌黏胶织物进行断裂强力和抑菌性能进行测试,结果如表9所示。
[0092]
表9对比例3的抑菌黏胶织物性能测试
[0093][0094][0095]
对比例4
[0096]
本对比例中,原料的成分为:mos2(粒径范围5~8nm,占纺丝液质量的0.025%)、黏胶纺丝液(占纺丝液质量的99.975%)。
[0097]
按照上述方法将mos2和黏胶纺丝液配制成纺丝液,并织造成为抑菌黏胶织物(克重为 120.9g/m2)。
[0098]
对制备的抑菌黏胶织物进行断裂强力和抑菌性能进行测试,结果如表10所示。
[0099]
表10对比例4的抑菌黏胶织物性能测试
[0100][0101]
对比例5
[0102]
本对比例中,原料的成分为:丙烯腈(占纺丝液质量的9%)、黏胶纺丝液(占纺丝液质量的91%)。
[0103]
按照上述方法将丙烯腈和黏胶纺丝液配制成纺丝液,并织造成为高强黏胶织物。
[0104]
对制备的高强黏胶织物进行断裂强力和抑菌性能进行测试,结果如表11所示。
[0105]
表11对比例5的高强黏胶织物性能测试
[0106][0107][0108]
对比例6
[0109]
本对比例中,原料的成分为:丙烯腈(占纺丝液质量的4%)、黏胶纺丝液(占纺丝液质量的96%)。
[0110]
按照上述方法将丙烯腈和黏胶纺丝液配制成纺丝液,并织造成为高强黏胶织物。
[0111]
对制备的高强黏胶织物进行断裂强力和抑菌性能进行测试,结果如表12所示。
[0112]
表12对比例6的高强黏胶织物性能测试
[0113][0114]
对比例7
[0115]
本对比例中,原料的成分为:丙烯腈(占纺丝液质量的3%)、黏胶纺丝液(占纺丝液质量的97%)。
[0116]
按照上述方法将丙烯腈和黏胶纺丝液配制成纺丝液,并织造成为高强黏胶织物。
[0117]
对制备的高强黏胶织物进行断裂强力和抑菌性能进行测试,结果如表13所示。
[0118]
表13对比例7的高强黏胶织物性能测试
[0119]
[0120][0121]
对比例8
[0122]
本对比例中,原料的成分为:丙烯腈(占纺丝液质量的1%)、黏胶纺丝液(占纺丝液质量的99%)。
[0123]
按照上述方法将丙烯腈和黏胶纺丝液配制成纺丝液,并织造成为高强黏胶织物。
[0124]
对制备的高强黏胶织物进行断裂强力和抑菌性能进行测试,结果如表14所示。
[0125]
表14对比例8的高强黏胶织物性能测试
[0126][0127]
由实施例1-6、对比例1-8的结果可知,当采用粒径超过10nm的mos2纳米粒子时,织物的抑菌性能出现了下降,且随着粒径的增大,抑菌性能下降的越多。另外,在一定的范围内,随着丙烯腈的添加量的增加,织物的断裂强力也随之增加。
[0128]
综上,本发明在黏胶纺丝原液中加入一定量的mos2纳米粒子和丙烯腈,最终制备的再生纤维素面料不但具有优异和持久的抑菌性能,而且织物强力可以提高20%以上,大大提高了面料的使用性能。
[0129]
以上所述实施例仅是为充分说明本发明而所举的较佳的实施例,本发明的保护范围不限于此。本技术领域的技术人员在本发明基础上所作的等同替代或变换,均在本发明的保护范围之内。本发明的保护范围以权利要求书为准。