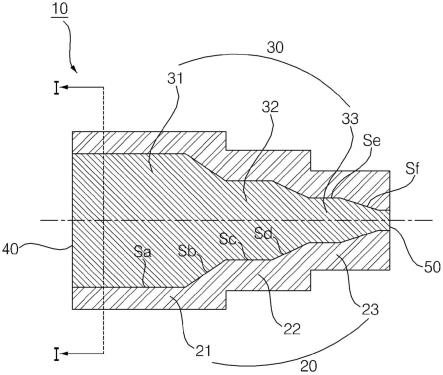
1.本发明涉及挤压管嘴装置及利用挤压管嘴装置的热电材料的挤压方法,更详细而言,涉及一种其截面积从投入口越靠近吐出口越小的多段形态的挤压管嘴装置及利用其的热电材料的挤压方法。
背景技术:2.最近,随着通过收集日常生活中浪费或消耗的能量来作为电力再利用的能量收集(energy harvesting)技术的应用,热电材料备受关注。
3.热电材料是指利用热电现象的材料。热电现象(thermoelectric effect)是由材料内部的电子和空穴的移动产生的现象,热电现象是指热与电之间可逆且直接的能量转换。
4.热电元件可以应用于利用由热电材料两端的温度差产生的电动势的热电发电领域,并且可以应用于利用由供电形成的材料两端的温度差的热电冷却及加热领域。通常,热电元件具有通过将p型热电材料和n型热电材料接合于金属电极之间来形成pn接合对的结构。
5.热电元件可以分为利用电阻温度变化的元件、利用塞贝克效应(seebeck effect)的元件、利用珀尔帖效应(peltier effect)的元件等。
6.在此,塞贝克效应是温度差被直接转换为电力的现象,珀尔帖效应是电流流经不同材料的接合部位时,在上部接合部位(upper junction)处放热并在下部接合部位(lower junction)处吸热的现象。塞贝克效应和珀尔帖效应与焦耳加热(joule heating)的区别在于,他们在热力学上是可逆的。
7.利用塞贝克效应可以将废热用作能量源。因此,可以用于汽车发动机和排气装置、利用人体热量的医疗器械等多样的领域。另外,利用珀尔帖效应可以在不使用制冷剂气体的无振动、低噪音冰箱、空调、各种微型冷却系统等中使用热电材料,也可以用于半导体设备的冷却系统等。
8.另一方面,在增加晶粒(grain)的晶体取向性的情况下,这样的热电材料可以通过提高导电率来改善材料的性能。作为控制热电材料的晶体结构的方法之一,正在进行对诸如热压(hot pressing)等热变形(hot deformation)的研究。
9.随着进行多次热变形,热电材料的晶粒在预定的方向上排列,霍尔迁移率(hall mobility)增加。
10.图1是示出根据热变形工艺的应用次数来排列热电材料的晶粒的方向的图。
11.如图所示,随着实施热变形的次数从一次增加到三次,晶体颗粒向一个方向取向的倾向增加。在此情况下,导电率增加,从而能够提高热电材料的性能。
12.但是,存在的问题在于,随着热变形的进行次数增加,制造热电材料所需的工艺步骤增加,挤压转角(press zig)增大,并且由于工艺的单件产品生产时间(tact time)增加而导致材料的成本升高。
技术实现要素:13.所要解决的技术问题
14.为了解决上述问题,本发明的目的是提供一种挤压管嘴装置及利用其的热电材料的挤压方法,包括其截面积从投入口越靠近吐出口越小的多段形态,从而仅通过一次挤压就能够获得复数次热变形效果。
15.另外,为了解决上述问题,本发明的目的是提供一种挤压管嘴装置及利用其的热电材料的挤压方法,包括其截面积从投入口越靠近吐出口越小的多段形态,从而能够减少生产工艺的单件产品生产时间并降低材料的生产成本。
16.另外,为了解决上述问题,本发明的目的是提供一种挤压管嘴装置及利用其的热电材料的挤压方法,能够通过加热为使温度从投入口侧的段越靠近吐出口侧的段越小来提高热电材料的性能。
17.本发明的课题不限于以上提及的课题,并且本领域普通技术人员可以从以下描述中清楚地理解未提及的其他课题。
18.解决问题的技术方案
19.用于实现上述目的的本发明一实施例的挤压管嘴装置包括:投入口,投入材料;吐出口,吐出投入的材料;以及吐出管,形成为包括复数个段的多段形态,使得投入的材料在其内部被施压并沿从投入口朝吐出口的第一方向移动,复数个段的与第一方向垂直的截面积可以从投入口越靠近吐出口越小。
20.另一方面,在用于实现上述目的的本发明一实施例的挤压管嘴装置中,吐出管中包括的复数个段可以包括边界面,每个段的边界面与第一方向构成的角度可以大于0
°
且小于或等于90
°
。
21.另一方面,在用于实现上述目的的本发明一实施例的挤压管嘴装置中,复数个段可以包括从投入口侧到所述吐出口侧按序配置的第一段至第n段(n为2以上的自然数),当将第一段至第n段中的每个段的边界面与第一方向构成的角度设为r1至rn时,
22.可以满足r1≥r2≥r3≥...≥rn的条件式。
23.另一方面,在用于实现上述目的的本发明一实施例的挤压管嘴装置中,吐出管中包括的复数个段包括内表面,每个段的内表面可以形成为与第一方向平行。
24.另一方面,在用于实现上述目的的本发明一实施例的挤压管嘴装置中,复数个段包括从投入口侧到吐出口侧按序配置的第一段至第n段(n为2以上的自然数),当将第一段至第n段中的每个段的内表面的长度设为l1至ln时,
25.可以满足l1≤l2≤l3≤...≤ln的条件式。
26.另一方面,在用于实现上述目的的本发明一实施例的挤压管嘴装置中,吐出口的截面积可以小于投入口的截面积。
27.另一方面,在用于实现上述目的的本发明一实施例的挤压管嘴装置中,吐出口的截面的形状可以包括圆形或椭圆形或多边形或角形。
28.另一方面,在用于实现上述目的的本发明一实施例的挤压管嘴装置中,复数个所述段的与所述第一方向垂直的截面的形状可以包括圆形或椭圆形或多边形或角形。
29.另一方面,用于实现上述目的的本发明一实施例的挤压管嘴装置还可以包括:加热部,加热吐出管的每个段。
30.另一方面,在用于实现上述目的的本发明一实施例的挤压管嘴装置中,加热部可以加热每个段,使得吐出管的每个段的温度保持恒定。
31.另一方面,在用于实现上述目的的本发明一实施例的挤压管嘴装置中,复数个段包括从投入口侧到吐出口侧按序配置的第一段至第n段(n为2以上的自然数),当将第一段至第n段中的每个段的温度设为t1至tn时,
32.加热部可以加热每个段,以满足t1≥t2≥t3≥...≥tn的条件式。
33.另一方面,用于实现上述目的的本发明一实施例的挤压管嘴装置还可以包括:复数个温度传感器,包括在吐出管的每个段中并位于与每个段的内表面邻近的位置,加热部可以基于复数个温度传感器测量的每个段的温度来加热每个段。
34.另一方面,在用于实现上述目的的本发明一实施例的挤压管嘴装置中,加热部可以包括:加热装置,分别单独形成在每个段,以分别单独加热吐出管的每个段的温度。
35.另一方面,在用于实现上述目的的本发明一实施例的挤压管嘴装置中,加热装置可以包括:加热块,沿吐出管的每个段的外表面形成。
36.另一方面,用于实现上述目的的本发明一实施例的挤压管嘴装置还可以包括:凸缘部,形成在吐出管的设置有投入口的外表面并包括复数个孔,可以利用凸缘部能够与挤压成型机本体进行装卸。
37.另一方面,用于实现上述目的的应用本发明一实施例的挤压管嘴装置的热电材料的挤压方法可以包括:投入步骤,向投入口投入热电材料的材料;施压步骤,利用活塞从投入口向吐出口方向施压,使得投入的材料在包括形成为其截面积从投入口越靠近吐出口越小的复数个段的吐出管的内部移动;以及挤出步骤,将投入的材料向吐出口挤出。
38.另一方面,在用于实现上述目的的应用本发明一实施例的挤压管嘴装置的热电材料的挤压方法中,施压步骤可以包括:加热步骤,加热每个段,使得吐出管中包括的复数个段的温度从位于投入口侧的段越靠近位于吐出口侧的段越小。
39.其他实施例的具体事项包括在详细的说明和附图中。
40.技术效果
41.根据本发明,具有如下效果。
42.根据本发明一实施例的挤压管嘴装置及利用其的热电材料的挤压方法,包括其截面积从投入口越靠近吐出口越小的多段形态,从而仅通过一次挤压就能够获得执行复数次热变形的效果。
43.另外,根据本发明一实施例的挤压管嘴装置及利用其的热电材料的挤压方法,包括其截面积从投入口越靠近吐出口越小的多段形态,从而具有能够减少工艺的单件产品生产时间并降低材料的生产成本的效果。
44.另外,根据本发明一实施例的挤压管嘴装置及利用其的热电材料的挤压方法,具有能够通过加热为使温度从投入口侧的段越靠近吐出口侧的段越小来提高热电材料的性能的效果。
45.本发明的效果不限于以上提及的效果,并且本领域技术人员可以从权利要求的描述中清楚地理解未提及的其他效果。
附图说明
46.图1是示出根据热变形工艺的应用次数来排列热电材料的晶粒的方向的图。
47.图2是本发明一实施例的挤压管嘴装置的一方向上的剖视图。
48.图3是图2的挤压管嘴装置的另一方向上的剖视图。
49.图4是为了说明图2的挤压管嘴装置的内表面及边界面的角度而参照的图。
50.图5是为了说明施加于本发明实施例的挤压管嘴装置中被挤压的材料的压力而参照的图。
51.图6是为了说明图2的挤压管嘴装置的内表面的长度而参照的图。
52.图7是本发明另一实施例的挤压管嘴装置的一方向上的剖视图。
53.图8是示出本发明一实施例的热电材料的制造方法的流程图。
54.图9是示出图8的制造方法中的烧结过程的详细步骤的流程图。
55.图10是为了说明由本发明实施例的挤压管嘴装置挤出的热电材料的晶体方向而参照的图。
56.图11是为了说明由本发明的挤压管嘴装置挤出的热电材料的切割工艺及切割形态而参照的图。
具体实施方式
57.以下,将参照附图对本发明进行更详细的说明。
58.与图号无关地,对相同或相似的结构要素赋予了相同的附图标记,并省略了对其的重复说明。在以下的说明中所使用的结构要素的后缀“模块”和“部”是,为了便于说明书撰写而赋予或混用的,其自身并不具有相互区别的含义或作用。因此,所述“模块”和“部”可以彼此互换使用。
59.另外,在说明本说明书公开的实施例时,当判断为对相关公知技术的具说体明可能使本说明书公开的实施例的要旨不清楚时,将省略对其的详细说明。另外,附图是为了便于理解本说明书公开的实施例而提供的,本说明书公开的技术思想并不局限于附图,而是应当被理解为包括本发明的技术思想和技术范围内作出的所有变更、等同物及替代物。
60.第一、第二等包括序数的术语可以用于说明多样的结构要素,然而这些结构要素不限于这些术语。这些术语仅为了将一个结构要素区别于另一个结构要素而使用。
61.当提及到某一结构要素与另一个结构要素“连结”或“连接”时,应理解为该结构要素可以与另一个结构要素直接连结或连接,或者也可以在他们之间存在其他结构要素。相反,当提及到某一结构要素与另一个结构要素“直接连结”或“直接连接”时,应理解为在他们之间不存在任何其他结构要素。
62.除非上下文另外明确指出,否则单数表达包括复数表达。
63.在本技术中,术语“包括”或“具有”应被理解为旨在指示存在本说明书中公开的特征、数量、步骤、动作、结构要素、部件或他们的组合,而非旨在预先排除一个或一个以上的其他特征、数字、步骤、动作、结构要素、部件或他们的组合的存在或附加可能性。
64.本发明涉及一种能够提高热电材料的性能的挤压管嘴装置及利用其的热电材料的挤压方法。
65.热电材料的性能可以使用由下述数学式1定义的无量纲性能指数zt来评价。
66.[数学式1]
[0067][0068]
在数学式1中,zt表示热电材料的无量纲性能指数,s表示塞贝克系数,σ表示导电率,t表示绝对温度,k表示导热率。在此,s2σ被定义为功率因数(power factor)。
[0069]
无量纲性能指数越大,判断为热电材料的性能越好。为了增大无量纲性能指数zt,需要塞贝克系数s和导电率σ,即功率因数大且导热率k小的材料。
[0070]
但是,塞贝克系数和导电率通常为交换抵消关系(trade-off)。若要想使塞贝克系数高,则电子需具有较重的有效质量,反之,若要想使导电率高,则电子需具有较轻的有效质量。例如,导电率高的金属的塞贝克系数较低,而导电率高的绝缘物质的塞贝克系数较高。因此,由于这样的交换抵消关系,在提高热电材料的热电性能方面存在困难。
[0071]
另外,热电材料的能带的简并度(degeneracy)越大,塞贝克系数越大,能带的分散性(dispersion)越大,导电率越大。但是,通常由于热电材料的能带分散性(band dispersion)越小,能带简并度(degeneracy)越大,因此提高热电性能方面存在困难。
[0072]
通常,颗粒的尺寸越小,导热率越小,电流通过的晶体颗粒数越小,导电率越大。因此,可以通过控制晶体的生长来提高热电材料的无量纲性能指数。
[0073]
另一方面,热压(hot pressing)被用作作为晶体结构控制技术之一。
[0074]
在热电材料的制造过程中,粉碎固化的热电材料,并通过热压等固化成型来形成烧结体。但是,在热压下固化成型时,晶体颗粒具有晶体的取向方向被固化的倾向,以向与压力方向垂直的方向取向。
[0075]
在本发明的一实施例提出的用于制造热电材料的挤压管嘴装置中,提出一种能够通过多段形态来提高热电材料的性能并减少工艺次数的结构。
[0076]
图2是本发明一实施例的挤压管嘴装置的一方向上的剖视图,图3是图2的挤压管嘴装置的另一方向上的剖视图。
[0077]
在热电材料的制造过程中,可以应用挤压-烧结方法(extrusion-sintering)。挤压-烧结方法是通过施压热电材料使其通过管嘴来制造热电材料的方法。为了挤压烧结热电材料,可以使用挤压管嘴装置。
[0078]
参照图2,本发明一实施例的挤压管嘴装置10可以包括:吐出管30、投入口40以及吐出口50。
[0079]
吐出管30形成挤压管嘴装置的本体。吐出管30可以由金属材料形成,并且可以是沿一方向较长地延伸形成的空心管形状。
[0080]
投入口40可以形成在吐出管30的一侧面,使其具有垂直于吐出管30的长度方向(以下称为“第一方向”)的截面。材料可以通过投入口40投入到挤压管嘴装置10的内部。
[0081]
吐出口50可以形成在吐出管30的另一侧面,使得其具有垂直于第一方向的截面。通过投入口40投入到挤压管嘴装置10的内部的材料可以通过吐出口50吐出。另一方面,与吐出口50的第一方向垂直的截面积可以小于投入口40的截面积。
[0082]
吐出口50的截面的形状可以是圆形或椭圆形或多边形或角形。这里的角形是指其一侧弯折的形态的图形。例如,角形可以是“l”字形态,可以是“u”字形态,但不限于此。
[0083]
吐出管30中供材料移动的空间31、32、33可以形成为从投入口40到吐出口50沿第
一方向包括复数个段的多段形态。附图中示出了吐出管30由三个段,即第一段31、第二段32以及第三段33形成的情形。但是,吐出管30中包括的段的数量不限于此,可以由两个以上的多样的数量的段形成。
[0084]
在每个段中各个段的与第一方向垂直的截面积都可以不同。具体而言,从位于投入口40侧的段越靠近位于吐出口50侧的段,段的截面积可以相同或越小。
[0085]
图3是沿图2的i-i线剖开的剖视图。在附图的例示中,假设为截面呈圆形的情形。但是,每个段的与长度方向垂直的截面的形状不限于此,可以是诸如椭圆形、多边形、角形等多样的形态。
[0086]
参照附图,第二段32的截面积可以等于或小于第一段31的截面积,并且第三段33的截面积可以等于或小于第二段32的截面积。
[0087]
由此,投入到投入口40的材料可以沿第一方向在吐出管30的内部移动,并被活塞(未图示)和吐出管30阶段性地施压,然后通过吐出口50吐出。
[0088]
另一方面,挤压管嘴装置10可以以能够装卸于挤压热电元件的挤压成型机(未图示)的方式形成。挤压管嘴装置10可以包括形成在吐出管30末端的设置有投入口40的外表面并包括复数个孔的凸缘部(未图示)。挤压管嘴装置10的凸缘部可以通过复数个孔与形成在挤压成型机的一侧的凸缘部螺栓紧固而贴合。例如,挤压管嘴装置10的凸缘部可以通过与挤压成型机的容器一侧的凸缘部螺栓紧固而贴合。
[0089]
另一方面,在挤压管嘴装置10的下端可以形成有支撑单元(未图示),以能够通过与挤压成型机的特定部位螺栓紧固来实现牢固结合。支撑装置的螺栓紧固方向可以与凸缘部的螺栓紧固方向彼此垂直。通过这样的结构,挤压管嘴装置10可以与挤压成型机牢固地结合,并且可以在挤压管嘴装置10稳定地执行热挤压工艺。
[0090]
另一方面,挤压管嘴装置10可以由诸如std61的热作工具钢形成,但不限于此,可以由具有优异的高温强度和耐磨性等的多样的种类的材料形成。
[0091]
图4是为了说明图2的挤压管嘴装置10的内表面和边界面的角度而参照的图,图5是为了说明施加于图2的挤压管嘴装置10中被挤压的材料的压力而参照的图。
[0092]
参照图4和图5,挤压管嘴装置10的吐出管30的每个段可以包括内表面和边界面。
[0093]
例如,第一段31可以包括第一内表面sa和第一边界面sb,第二段32可以包括第二内表面sc和第二边界面sd,第三段33可以包括第三内表面se和第三边界面sf。
[0094]
在吐出管30中包括的复数个段中,各个内表面可以形成为与第一方向平行。例如,第一内表面sa至第三内表面sf可以形成为与第一方向平行。流入到吐出管30的材料可以在经由每个段的过程中在内表面和边界面被施压。因此,根据内表面和边界面形成的方向,流入的材料内的晶粒排列的方向可以改变。在内表面形成为与流入的材料移动的第一方向平行的情况下,流入的材料内的晶粒可以被排列为与第一方向平行。
[0095]
但是,第一内表面sa至第三内表面sf可以形成为与第一方向构成的角度为45
°
以下,而不与第一方向平行。在此情况下,流入的材料内的晶粒可以被排列为朝第一方向。
[0096]
另一方面,在吐出管30中包括的复数个段中,各个边界面与第一方向构成的角度可以大于0
°
且小于或等于90
°
。例如,第一边界面至第三边界面se与第一方向构成的角度r1、r2、r3可以大于0
°
且小于或等于90
°
。因此,流入到吐出管30的材料可以从投入口40向吐出口50方向移动,并且从截面积不同的各个段的边界面顺畅地移动到下一个段。
[0097]
参照图5,流入的材料可以被从边界面向斜线方向作用的力施压。根据边界面形成的方向,流入的材料内的晶粒的排列方向可以改变。但是,边界面可以是形成为能够使流入的材料从截面积不同的每个段的边界顺畅地移动到下一个段的面。因此,在挤压管嘴装置10中被挤压的晶粒的排列方向可以主要由内表面的方向来确定。
[0098]
另一方面,为使晶粒的排列方向由内表面方向来确定,每个段中的内表面的长度可以大于边界面的长度。例如,第一内表面sa的长度可以大于第一边界面sb的长度,第二内表面sc的长度可以大于第二边界面sd的长度,第三内表面se的长度可以大于第三边界面sf的长度。
[0099]
另一方面,在吐出管30中包括的复数个段中,从位于投入口40侧的段越靠近位于吐出口50侧的段,各个边界面与第一方向构成的角度可以相同或越小。具体而言,复数个段可以包括从投入口40侧到吐出口50侧按序配置的第一段至第n段(n为2以上的自然数)。当将第一段至第n段中的每个段的边界面与第一方向构成的角度设为r1至rn时,
[0100]
可以满足r1≥r2≥r3≥...≥rn的条件式。
[0101]
在附图的例示中,可以满足r1≥r2≥r3的条件式。
[0102]
如前所述,边界面可以形成为能够使流入的材料从截面积不同的每个段的边界顺畅地移动到下一个段。如果随着越靠近截面积变小的吐出口50侧的段,流入的材料行进的方向与边界面构成的角度越小,则流入的材料可以顺畅地移动到下一个段。但是,每个边界面与第一方向构成的角度不限于此,可以形成为多样的角度。
[0103]
图6是为了说明图2的挤压管嘴装置10的内表面的长度而参照的图。
[0104]
在吐出管30中包括的复数个段中,从位于投入口40侧的段越靠近位于吐出口50侧的段,每个段的第一方向上的长度可以相同或越长。具体而言,复数个段包括从投入口40侧到吐出口50侧按序配置的第一段至第n段(n为2以上的自然数),当将第一段至第n段中的每个段的第一方向上的长度设为l1至ln时,
[0105]
可以满足l1≤l2≤l3≤...≤ln[0106]
的条件式。
[0107]
在附图的例示中,可以满足l1≤l2≤l3的条件式。
[0108]
如前所述,从第一段越靠近第n段,各个段的截面积可以越小。在此情况下,随着越靠近其截面积变小的吐出口50侧的段,材料在相应段内沿第一方向移动的速度可以越大。因此,随着越靠近其截面积变小的吐出口50侧的段,相应段的第一方向上的长度越长,从而能够使流入的材料在位于吐出口50侧的段的内部停留的时间最小化。
[0109]
另外,吐出管30的最后一个段的截面积越窄且流入的材料在最后一个段中移动的时间越长,流入的材料内的晶粒排列的方向可以越均匀地形成为与第一方向平行。因此,能够通过使吐出管30的每个段的长度形成为逐渐变长来提高晶粒的取向性。
[0110]
另一方面,在吐出管30中包括的复数个段中,每个段的第一方向上的长度可以根据流入的材料在每个段的内部停留的时间来不同地形成。
[0111]
在多段形态的挤压管嘴装置10中,流入的材料可以在从投入口40侧向吐出口50侧移动的活塞的作用下,在各个段的内部移动。在此,由于各个段的截面积都不同,因而相应段的截面积越小,流入的材料在各个段的内部停留的时间越短。因此,在需要增加流入的材料在特定段内停留的时间的情况下,可以通过延长相应段的第一方向上的长度来调整在相
应段的内部停留的时间。
[0112]
但是,每个段的第一方向上的长度不限于此,可以形成为多样的长度。
[0113]
图7是本发明另一实施例的挤压管嘴装置10的一方向上的剖视图。
[0114]
参照附图,本发明另一实施例的挤压管嘴装置10可以包括:吐出管30、投入口40以及吐出口50,并且还可以包括加热部60。
[0115]
加热部60可以加热吐出管30的每个段。为了加热每个段,加热部60可以形成为包围吐出管30的外表面的形态。加热部60可以形成为与吐出管30的外表面接触,并且可以形成为与外表面隔开预定间隔。另一方面,加热部60也可以一体地形成在吐出管30的内部。
[0116]
加热部60可以加热每个段31、32、33,使得吐出管30的每个段31、32、33的温度保持恒定。为此,挤压管嘴装置10可以包括复数个温度传感器64、65、66,复数个所述温度传感器64、65、66包括在每个段31、32、33中并位于与每个段的内表面sa、sc、se邻近的位置。
[0117]
另外,加热部60可以包括温度控制装置(未图示)。温度控制装置可以控制加热部60对每个段进行加热的温度。
[0118]
另一方面,温度控制装置可以由与加热部60分别单独的装置构成,并且可以与加热部60连接并控制加热部60的动作。
[0119]
温度控制装置可以基于复数个温度传感器64、65、66测量的每个段31、32、33的温度来控制加热部60,从而使加热部60加热每个段31、32、33以使温度保持恒定。复数个温度传感器64、65、66可以在每个段各形成一个,并且形成在各个段的复数个温度传感器64、65、66可以形成为彼此隔开。
[0120]
另一方面,加热部60可以分别单独加热吐出管30的每个段31、32、33。为此,加热部60可以包括每个段31、32、33中分别单独形成的复数个加热装置61、62、63。
[0121]
复数个加热装置61、62、63可以以包围吐出管30的每个段31、32、33的外表面的形态彼此隔开形成。复数个加热装置61、62、63可以形成为与吐出管30的外表面接触,并且可以形成为与外表面隔开预定间隔。另一方面,复数个加热装置61、62、63也可以一体地形成在吐出管30的内部。
[0122]
复数个加热装置61、62、63可以由诸如铜或包含铜的合金(例:黄铜)的高导热材料形成。
[0123]
复数个加热装置61、62、63可以是沿吐出管30的每个段31、32、33的外表面形成的加热块。
[0124]
加热块可以在内部包括加热线圈(未图示)。加热线圈可以在加热块内形成为螺旋形,从而被配置为能够包围吐出管30的段的整个外表面的形态。加热线圈可以由诸如铜或包含铜的合金的高导热材料形成,也可以是能够使诸如水或油的加热介质在其内部通过的管形态的线圈。加热块可以通过对加热线圈进行加热或使加热介质穿过加热线圈的内部,来加热吐出管30的每个段31、32、33。
[0125]
另一方面,加热块可以形成为与吐出管30的外表面接触和拆卸的形态。由于加热块的结构属于相关技术领域的一般结构,因此省略具体的说明。
[0126]
另一方面,加热部60可以进行加热,使得吐出管30的每个段31、32、33的温度相同,并且可以通过分别单独加热每个段31、32、33来控制每个段的温度不同。例如,加热部60可以加热每个段,使得段的温度从投入口40侧的段越靠近吐出口50侧的段越小。
[0127]
复数个段包括从投入口40侧到吐出口50侧按序配置的第一段至第n段(n为2以上的自然数),当将第一段至第n段中的每个段的温度设为t1至tn时,
[0128]
可以满足t1≥t2≥t3≥...≥tn的条件式。
[0129]
在附图的例示中,可以满足t1≥t2≥t3的条件式。
[0130]
[表1]
[0131][0132]
上述表1是比较包括三个段的挤压管嘴装置中根据施加于每个段的温度条件变化的热电材料的导电率、导热率以及zt。
[0133]
在表1中,第二温度t2高于第一温度t1,第三温度t3高于第二温度t2。温度分布(profile)表示施加于每个段的温度条件。导电率、导热率以及zt是以表1的第四实例为基准,以百分比(%)示出其余实例的相对大小。
[0134]
参照表1,在从第一段31越靠近第三段33时相应段的温度越小的实例5的情况下,热电材料的无量纲性能指数zt表现为最高。在将实例4与实例5进行比较时,在与各个段的温度都相同的情况(实例4)比较而从第一段越靠近第三段时相应段的温度越小的情况下,虽然热电材料的导热率减小,但是导电率较大地增加,其结果可以确认出无量纲性能指数zt增加。
[0135]
另一方面,在将实例1、2与实例4进行比较时,在段的温度从第一段31到第二段32或者从第二段32到第三段33时升高的情况下,可以确认出热电材料的导电率较大地降低,相应地无量纲性能指数zt较大地降低。
[0136]
如上所述,即使使用其截面积从投入口40侧的段越靠近吐出口50侧的段越小的吐出管30结构,热电材料的导电率也可能根据各个段的温度设定而不同。这是因为,随着进行热挤压工艺,由于烧结(sintering)而产生微细晶粒(grain)的尺寸变大的情况。
[0137]
如实例5所示,可以通过控制加热部60,使得从第一段越靠近第三段时相应段的温度越小,来抑制晶粒(grain)的尺寸变大的现象,以增加热电材料的无量纲性能指数zt。
[0138]
图8是示出本发明一实施例的热电材料的制造方法的流程图。
[0139]
为了制造热电材料,使用热电材料的原材料来制造块体热电材料(锭,ingot)(步骤s10)。在此,热电材料的原材料可以包括cu、i、bi、sb、te。
[0140]
具体而言,在步骤s10中,作为热电材料的组分将原材料按摩尔比称量后装入石英管中并真空密封。随后,可以通过装入熔炉中并在约1000℃的高温下熔融后冷却至常温来制造锭(ingot)。
[0141]
通过将制造的块体热电材料(锭)进行粉碎来制造为粉末形态(步骤s20)。例如,可
以通过球磨(ball milling)工艺将锭制成粉末形态。
[0142]
向制造成粉末形态的块体热电材料添加预定量的金属添加剂(步骤s30)。金属添加剂可以是选自热电材料的原材料中的任意一种或一种以上的物质。另外,金属添加剂可以是其熔点低于锭的物质。
[0143]
金属添加剂可以是在形成中间体时在晶格内部或边界面能够形成电位d的物质。例如,如果熔点低到在形成固体结晶之前被熔融的程度,则无法如上所述在晶格内部或边界面形成电位d。
[0144]
相对于原材料,可以包含超过20至25重量%的金属添加剂。另外,金属添加剂可以是碲(te)。
[0145]
通过在制造成粉末形态的块体热电材料中混合有金属添加剂的状态下熔融和利用急速冷却装置来形成中间体(步骤s40)。中间体可以是带(ribbon)形态的材料。中间体可以形成为金属添加剂分散在热电材料的形态。
[0146]
在急速冷却工艺中,将材料装入具有较窄的管嘴尺寸的石英管中,进行感应加热而使其熔融后,施加气体压力并瞬间吐出到高速旋转的铜转盘来进行冷却固化,从而制成带形态的颗粒。
[0147]
形成中间体的过程可以包括:向具有管嘴的管中装入热电材料粉末和金属添加剂的过程;将热电材料粉末和金属添加剂熔融成液态的过程;以及将熔融的材料吐出到转盘来形成带形态的颗粒的过程。
[0148]
随后,通过将形成的中间体进行烧结来制造热电材料(步骤s50)。此时,烧结温度可以实现为金属添加剂的熔点以上的温度。
[0149]
在中间体烧结时,可以应用挤压烧结法(extrusion sintering)。带形态的材料利用挤压烧结来被制成块形态的热电材料。在此,挤压烧结法可以使用本发明一实施例的多段形态的挤压管嘴装置10来执行。
[0150]
随后,将块形态的热电材料切割并加工成所需的形态,并观察热电特性(塞贝克系数、导电率、导热率)以及微观组织。
[0151]
以下,详细说明本发明一实施例的热电材料的制造方法。
[0152]
1.制造锭(ingot)
[0153]
根据(cui)
x
(bi2se
2.7
te
0.3
)
1-x
,x=0.003组分比,按摩尔比定量测量cu、i、bi、sb、te并装入到石英管。
[0154]
此时,在真空度为10-5
torr下进行真空密封。
[0155]
将如上所述真空密封的石英管放入电炉中,将温度缓慢提升至1050℃,并在1050℃下保持12小时后进行冷却,从而制造锭(ingot)。
[0156]
2.制造块体热电材料
[0157]
由(cui)
x
(bi2se
2.7
te
0.3
)
1-x
,x=0.003材料组分制造的锭材料通过研磨工艺来制造成数微米至数十微米大小的粉末。
[0158]
随后,为了形成纳米粒子(例如,cu2te),作为金属添加剂将20至25重量%的碲(te)和1至5重量%的铜(cu)粉末混入到基体组分粉末后,利用急速冷却装置来形成中间体。
[0159]
即,为了使用急速冷却装置来制作带,制成直径为10至15mm、高度为10mm以上的大
小的颗粒(pellet)形态后,放入具有直径为约0.3至0.4mm程度的管嘴大小的石英管。
[0160]
随后,将粉末进行感应加热而熔融后,施加压力并吐出到高速旋转的直径为300mm的铜转盘来进行冷却固化,从而可以获得金属添加剂被析出的带形状的中间体。即,金属添加剂可以构成纳米粒子进行分布。
[0161]
此时,在转盘以2800至3200rpm旋转时,将获得具有约1μm至100μm厚度的带形状的材料。这样的带形状的材料以金属添加剂在热电材料中构成纳米粒子进行分布的形态来获得,并且在急速冷却的效果的作用下,热电材料和金属添加剂的大小可以形成为数十nm至数百nm。
[0162]
例如,可以包括(cui)
x
(bi2se
2.7
te
0.3
)
1-x
材料作为热基体和cu/te作为金属添加剂,并通过使用急速冷却装置来制造带形状的材料。
[0163]
随后,使用急速冷却装置将通过急速冷却固化法制造的带形状的中间体进行粉碎(pulverizing),然后,通过利用本发明的多段形态的挤压管嘴装置10的挤压烧结法(extrusion sintering)来进行施压烧结。
[0164]
图9是示出图8的制造方法中的烧结过程(s50)的详细步骤的流程图,图10至图11是为了说明由挤压烧结方法形成的热电材料的晶体取向方向以及根据切割形态的元件应用方向而参照的图。
[0165]
以下,参照图9至11详细说明本发明一实施例的热电材料的挤压方法。
[0166]
参照图9,在通过将形成的中间体进行烧结来制造热电材料的步骤中,可以应用挤压烧结法(extrusion sintering)。
[0167]
将热电材料(中间体)投入到挤压成型机。具体而言,向本发明一实施例的多段形态的挤压管嘴装置10的投入口40投入热电材料的材料(步骤s510)。
[0168]
利用活塞从所述投入口40向吐出口50方向施压,使得投入的材料在包括形成为其截面积从投入口40越靠近吐出口50越小的复数个段的吐出管30的内部移动(步骤s520)。
[0169]
随后,通过活塞的移动将投入的材料向吐出口挤出(步骤s530)。
[0170]
投入的材料可以在挤压过程中以规定的温度加热规定时间而被制造成热电材料。具体而言,可以在形成为多段形态的挤压管嘴装置10的各个段的内部以规定的温度加热规定时间。投入的材料在每个段中停留的时间可以利用各个段的截面积、各个段的长度以及活塞的移动速度来控制。另一方面,为了控制投入的材料在每个段内停留的时间,也可以控制为,使活塞先是沿第一方向移动,然后以预定时间保持停止的状态。
[0171]
为了热电材料颗粒的均匀化、细微化,可以确定投入口40和吐出口50的比例,使得挤出比至少达到5以上。例如,挤出比可以被确定为5:1、10:1、20:1、30:1等,但不限于此。
[0172]
压力可以被施加至5至20mpa,吐出管30的温度可以被加热到300℃至600℃。活塞可以在吐出管30内移动,使得投入到投入口40的材料在被吐出到吐出口50为止将经过数秒至数十分钟。但是,这样的挤压环境条件不限于此,可以根据热电材料的特性以及挤压管嘴装置10的结构等而改变。
[0173]
图10是对利用现有的放电等离子烧结方法和本发明的挤压烧结方法来制造的热电材料的晶体取向方向进行了比较的情形。
[0174]
放电等离子烧结方法是,将材料装入碳模具内后施压并接通电流,以在构成材料的粉末粒子之间产生火花形态的等离子来进行烧结的方法。当接通电流时,随着材料瞬间
被加热,粉末粒子将彼此连接并进行烧结。
[0175]
利用现有的放电等离子烧结方法来形成的晶粒的取向方向与元件应用方向不同。因此,热电材料中的电流通路长度增加,由此可能会降低热电材料的导电率。
[0176]
与此相比,利用本发明的挤压烧结方法来制造的热电材料的晶粒的取向方向与元件应用方向相同。如图10所示,在多段形态的挤压管嘴装置10中挤压烧结的热电材料的晶粒可以被取向为与第一方向平行,并且晶粒的取向方向和切割热电材料后的材料应用方向可以相同。
[0177]
参照图11,在本发明的挤压管嘴装置10中挤压烧结的热电材料可以沿被挤压的长度方向进行切割并使用。在此情况下,可以使在切割被烧结的材料时丢弃的部分最小化,并且可以使晶粒的取向方向与切割热电材料后的材料应用方向相同。
[0178]
另外,在现有的放电等离子烧结方法的情况下,随着烧结面积增加,使纳米粒子均匀地分散到基体化合物内时存在局限,而在挤压烧结方法的情况下,由于其采用的是小面积连续工艺,因此具有能够使纳米粒子较为均匀地分散到基体化合物内的优点。
[0179]
另一方面,根据利用本发明的多段形态的挤压管嘴装置10的挤压烧结方法,仅挤压一次就如同执行多次热变形一样,能够提高晶粒的取向性。
[0180]
[表2]
[0181]
样品hphd1hd2hd3导电率100%116%128%133%导热率100%108%113%116%材料zt100%107%128%133%
[0182]
上述表2是对应用热压(hot press)来烧结热电材料的情况和应用一段、二段以及三段(本发明的挤压管嘴装置)形态的挤压管嘴装置来进行热挤压烧结的情况进行比较的结果。
[0183]
在表2中,hp表示应用热压的结果,hd1至hd3分别表示应用一段、二段以及三段形态的挤压管嘴装置的结果。在表中,导电率、导热率以及zt是以hp的结果为基准,以百分比(%)示出其余结果的相对大小。
[0184]
参照表2,与应用热压来进行烧结的情况hp相比,在进行热挤压烧结的情况hd1下,导电率、导热率以及热电材料的无量纲性能指数zt增加。另外,随着用于热挤压烧结的挤压管嘴装置中包括的段数增加,导电率、导热率以及热电材料的无量纲性能指数zt增加。
[0185]
如上所述,通过利用本发明的多段形态的挤压管嘴装置10来对材料进行热挤压烧结,从而可以仅挤压一次就如同执行多次热变形一样,能够提高晶粒的取向性,并且能够提高热电材料的导电率而改善无量纲性能指数zt。
[0186]
由此,可以通过减少热变形的次数来减少生产工艺的单件产品生产时间,其结果能够降低热电材料的生产成本。
[0187]
另一方面,在步骤s520中,可以加热每个段,使得吐出管30中包括的复数个段的温度从位于投入口40侧的段越靠近位于吐出口50侧的段越小。如以上关于表1的说明,可以通过将各个段进行加热以使各个段的温度减小,来抑制晶粒的尺寸变大的现象,从而可以增加热电材料的无量纲性能指数zt。
[0188]
以上,尽管参考附图说明了本发明的优选实施例,但是,本发明不限于上述特定的
实施例,在不脱离权利要求所要求的本发明的要旨的范围内,本发明所属领域的普通技术人员在可以做出多样的修改,并且这些修改不应脱离本发明的技术思想或前景而单独地加以理解。