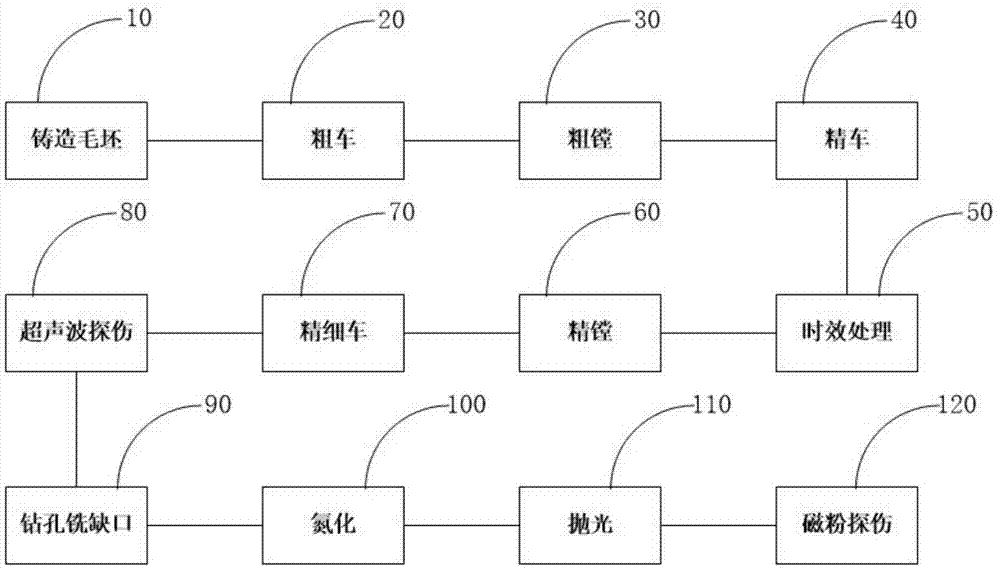
本发明涉及气缸套
技术领域:
,具体涉及一种表面石墨裸露球墨铸铁气缸套的制备工艺。
背景技术:
气缸套是发动机的心脏部件,其内表面与活塞顶部、活塞环、气缸盖底面一起构成了发动机的燃烧室,并引导活塞、活塞环的往复直线运动和向外传递热量,所以气缸套内表面既是装配表面又是工作表面,其加工质量的优劣直接影响到发动机的转配性能、使用性能和可靠性。气缸套内表面的加工技术也是气缸套机加工的核心技术之一。目前大多数气缸套内孔均是采用珩磨的方法进行加工,在珩磨过程中因受到砂条的挤压及外界的不良条件影响,缸套内表面的石墨会产生挤压变形,并且在缸套内表面产生金属覆盖和金属撕裂,从而大大影响了石墨的裸露,影响缸套的抗擦伤性能和磨合性能,延长了缸套和活塞环的磨合时间,不利发动机有效工作。经珩磨加工的气缸套主要靠加工纹理(网纹)储油,保证润滑性能,当出现断油等极端现象,缸套内孔由于石墨未裸露,无自润滑功能,会和活塞环黏合在一起造成拉缸等现象,导致发动机无法运行,特别是军品缸套尤其要注意缸套内孔的石墨裸露情况,以防出现发动机故障。中国专利库公开了一种球墨铸铁气缸套(cn102634720a),其公开了一种球墨铸铁气缸套的制备方法,包括配料工序、熔炼工序、球化孕育处理工序、浇注工序、冷却工序和成型工序。由该制备方法所制备的球墨铸铁气缸套具有良好的减磨性能、高的抗拉强度和疲劳强度,性能优于现有的高合金灰铸铁气缸套,完全能满足当代高性能、低排放、长寿命大功率内燃机的要求。然而,这种气缸套由于在加工过程中未注重对气缸套内孔的加工,导致其内孔工作表面的石墨裸露率较低,从而容易引起发动机故障。因此提升气缸套内孔表面加工质量,提高球墨铸铁气缸套石墨裸露率已成为刻不容缓的研究方向。技术实现要素:针对现有技术中的缺陷,本发明提供一种表面石墨裸露球墨铸铁气缸套的制备工艺,以提高球墨铸铁气缸套内孔工作表面的石墨裸露率。本发明提供的表面石墨裸露球墨铸铁气缸套的制备工艺,包括将气缸套半成品依次经过精车、精镗、精细车、钻孔铣缺口和氮化的步骤。可选地,所述气缸套半成品是指气缸套材料经过铸造毛坯、粗车、粗镗所得到的半成品。可选地,所述精车步骤的具体步骤如下:采用机夹刀车气缸套半成品的外圆及端面;所述精镗步骤的具体步骤如下:将所述气缸套半成品安装在机床的四爪卡盘上,安装时以所述气缸套半成品支承肩的上端面和外圆定位,以所述气缸套半成品支承肩的下端面夹紧,安装完毕后再调整四爪卡盘,开启机床,采用机床的镗刀对所述气缸套半成品进行精镗处理;所述精细车的具体步骤如下:将所述气缸套半成品安装在多功能数控车床上,依次进行粗车切削和精车切削,粗车切削去除所述气缸套半成品的外圆大部分余量,精车切削保留0.2~0.3mm的加工余量;所述钻孔铣缺口的具体步骤如下:采用精铰刀对所述气缸套半成品的内孔进行钻孔加工,再采用丝锥进行所述内孔表面进行铣缺口加工;所述氮化的具体步骤如下:将所述气缸套半成品送入氮化炉中,向所述氮化炉中通入氨气,使所述气缸套半成品除内孔之外的表面获得氮化层。可选地,所述气缸套半成品在所述精镗步骤之前还包括时效处理步骤,具体步骤如下:对所述气缸套半成品进行去应力退火。可选地,所述精细车步骤之后还包括超声波探伤步骤,具体步骤如下:采用超声波探伤仪对气缸套内部进行缺陷探伤。可选地,所述氮化步骤之后还包括抛光步骤,具体步骤如下:采用立式珩磨机进行抛光处理并在其磨头上安装软木以去除内孔氮化后的浮渣。可选地,最后还包括磁粉探伤步骤,具体步骤作如下:采用磁粉探伤机进行表面缺陷探伤以确保缸套表面无缺陷。可选地,所述氮化步骤中,氮化温度为550~570℃,氮化保温时间为250~290min,通入的氨气流量为200~400l/h,所述氮化炉内外压差为100~400mm水柱。可选地,所述铸造毛坯的具体步骤如下:首先将气缸套各材料按比例称量后送入中频感应电炉进行熔炼,待熔清之后,取光谱样和碳硫样进行铁水化学成分检测,待炉内铁水化学成分检测合格后,控制炉内铁水温度,当铁水温度在1520~1560℃时出铁水进行球化孕育处理,然后再将铁水浇注形成毛坯,最后对内孔进行冷却。可选地,所述气缸套是采用下列质量百分比的原料铸造而成:碳3.40~4.00%、硅2.20~2.80%、锰0.40~0.90%、磷≤0.08%、硫≤0.025%、铬≤0.08%、铜+镍0.80~1.30%、钼0.30~0.70%、镁0.03~0.08%、余量为铁。由上述技术方案可知,本发明提供的表面石墨裸露球墨铸铁气缸套的制备工艺,通过特殊的加工工艺,使得球墨铸铁气缸套内孔工作表面的石墨可以完全裸露,其状态接近于金相试块石墨情况,充分发挥石墨储油、自润滑功能,从而提高缸套表面耐磨性机断油抗黏合性能,提高发动机运行的可靠性。附图说明为了更清楚地说明本发明具体实施方式或现有技术中的技术方案,下面将对具体实施方式中所需要使用的附图作简单地介绍。图1为本发明实施例提供的表面石墨裸露球墨铸铁气缸套的制备工艺的步骤图;图2a及图2b是采用常规的珩磨工艺制备的气缸套;图3a及图3b是采用本发明的制备工艺制备的气缸套。具体实施方式下面将结合附图对本发明技术方案的实施例进行详细的描述。以下实施例仅用于更加清楚地说明本发明的技术方案,因此只作为示例,而不能以此来限制本发明的保护范围。需要注意的是,除非另有说明,本申请使用的技术术语或者科学术语应当为本发明所属领域技术人员所理解的通常意义。为了提高发动机功率的同时,减轻发动机体积和重量,本发明所要制备的气缸套的壁厚较一般船舶气缸套薄,因此本发明的气缸套采用qt600材质(抗拉强度≥600mpa的球墨铸铁),结合本发明的特殊制备工艺,使得球墨铸铁气缸套的内孔工作表面的石墨可以完全裸露,其状态接近于金相试块石墨情况,充分发挥石墨储油、自润滑功能,从而提高气缸套表面的耐磨性及机断油抗黏合性能,提高发动机运行的可靠性。由上,所述气缸套是采用下列质量百分比的原料铸造而成:碳3.40~4.00%、硅2.20~2.80%、锰0.40~0.90%、磷≤0.08%、硫≤0.025%、铬≤0.08%、铜+镍0.80~1.30%、钼0.30~0.70%、镁0.03~0.08%、余量为铁。图1为本发明实施例提供的表面石墨裸露球墨铸铁气缸套的制备工艺的步骤图。参见图1,本实施例提供一种表面石墨裸露球墨铸铁气缸套的制备工艺,具体包括以下步骤:铸造毛坯10:首先在铸造毛坯之前,需要进行气缸套原材料的配料,配料方案如下:球墨铸铁生铁3200kg±25kg、废钢800kg±25kg、硅铁40kg±2kg、锰铁12kg±2kg、铜合金20kg±2kg、钼铁10kg±2kg、增碳剂10kg±2kg、预处理剂5kg±1kg。配料完毕后,将各材料逐步送入中频感应电炉进行熔炼,待熔清之后,取光谱样和碳硫样进行铁水化学成分检测,要求炉内铁水成分应控制在表1所示的范围内。若检测结果不合格,则及时加废钢或合金来调整炉内铁水成分。表1炉内铁水化学成分待炉内铁水化学成分检测合格后,控制炉内铁水温度,当铁水温度在1520~1560℃时出铁水进行球化孕育处理。事先将称好的3.6kg球化剂加入球化包凹坑的底部,捣实,再将称好的3.3kg一次孕育剂加入到球化剂上面,再盖上厚度2~3mm的钢板,最后捣实,沿着钢板的一周撒上保温剂。球化处理铁水温度控制在1460~1500℃。将1.2kg二次孕育剂在球化时随流加入球化包,球化结束后,捞干净浮渣,并取光谱后撒330g硅铁和一层除渣剂。然后再将铁水浇注到模具中形成毛坯,浇注工序应当在一次孕育后10分钟浇注结束。浇注时模具温度为150-300℃,涂料厚度为2±0.5mm,浇注温度为1380-1400℃,主轴转速为780±20转/分,以90-120s的浇注速度浇注325±3kg重量的铁水。在浇注铁水重量的1/3时,开始随流孕育500g。浇注结束后按下冷却工艺按钮,在浇注完毕后120s,开始对内孔进行风冷,直至冷却工艺结束。接着对模具外表进行放水冷却和雾化气压冷却,冷却工艺为放水间隔30s,冷却时间550±20s,停水关机时间180±20s。雾化每组冷却水路的第一个喷嘴距离模具大端面150mm,喷嘴间距80mm,雾化气压3.5-4.0kg,雾化水压3.8-4.2kg,吹气压力2.0-4.8kg。经本步骤浇注出的毛坯大端外径为φ400.5mm。粗车20:采用机夹刀车毛坯的外圆、端面,并割断取样圈。粗镗30:采用机夹刀车毛坯的内孔,至此,获得气缸套半成品。精车40:采用机夹刀车气缸套半成品的外圆及端面。时效处理50:对气缸套半成品进行去应力退火。精镗60:将所述气缸套半成品安装在机床的四爪卡盘上,安装时以所述气缸套半成品支承肩的上端面和外圆定位,以所述气缸套半成品支承肩的下端面夹紧,保证夹紧力对镗孔的精度不受影响。安装完毕后可以粗调整四爪卡盘的中心,然后自车四爪卡盘的定位底面和止口面,以保证径向定位和轴向定位的准确性,从而保证缸套内外圆的同轴度。开启机床,采用机床的镗刀对所述气缸套半成品进行精镗处理。精细车70:该步骤再次对气缸套半成品的外圆进行加工,在多功能数控车床上进行,分粗、精两道工步进行切削。将所述气缸套半成品安装在多功能数控车床上,依次进行粗车切削和精车切削,粗车切削去除所述气缸套半成品的外圆大部分余量,精车切削保留0.2~0.3mm的加工余量。粗车切削采用cnma190616涂层刀片,r弧为1.6,保证刀具的耐用性,以切除大部分余量。精车切削采用43#cbn车刀切削,保证精度要求。超声波探伤80:采用超声波探伤仪对气缸套内部进行缺陷探伤。若探及气缸套内部有缺陷,则丢弃。钻孔铣缺口90:采用φ11.9的精铰刀对所述气缸套半成品的内孔进行钻孔加工,再采用丝锥进行所述内孔表面进行铣缺口加工,由于目标是m24x2.5-6h的螺纹孔,其螺纹精度为6级精度要求,因此,采用日本进口的osg丝锥。氮化100:将所述气缸套半成品送入氮化炉中,向所述氮化炉中通入氨气,使所述气缸套半成品除内孔之外的表面获得氮化层。氮化具体是采用气体硬氮化处理工艺,氮化温度为550~570℃,氮化保温时间为250~290min,通入的氨气流量为200~400l/h,所述氮化炉内外压差为100~400mm水柱。最终使得气缸套半成品的内孔表面硬度达到500-625hv0.1,且内孔表面无化合层(白亮层),氮化层深度在0.1mm-0.2mm。抛光110:采用立式珩磨机进行抛光处理并在其磨头上安装软木以去除内孔氮化后的浮渣。磁粉探伤120:采用磁粉探伤机进行表面缺陷探伤以确保缸套表面无缺陷。若探及气缸套表面有缺陷,则丢弃。最终通过经探及无缺陷的气缸套即为本发明所制备的球墨铸铁气缸套。经本发明的制备工艺所制备的球墨铸铁气缸套,根据gb9441球墨铸铁金相检测标准对其进行检测,石墨球化级别为2-4级(石墨大部分呈团絮状或球状,允许有少量蠕虫状,球化率≥70%),石墨大小为4-7级(15-250μm);基体为珠光体、屈氏体和铁素体,珠光体含量≥70%,渗碳体≤5%。本发明的制备工艺所制备的球墨铸铁气缸套,其硬度可达190-270hbs。图2a及图2b是采用常规的珩磨工艺制备的气缸套。参见图2a及图2b,可见气缸套内孔表面的石墨均被遮盖。图3a及图3b是采用本发明的制备工艺制备的气缸套。参见图3a及图3b,可见气缸套内孔表面的石墨均裸露出来。经过计算,石墨裸露面积占比为8%-15%。为了说明石墨裸露对球墨铸铁气缸套的影响,本发明通过贫油试验来验证石墨裸露率不同的两种气缸套的抗黏着性能。试验过程中实时监测摩擦力变化,用缸套在断油后发生拉缸前的持续时间表征其抗黏着能力。本发明的贫油试验分别采用常规的珩磨工艺制备的气缸套(气缸套一)和本发明的制备工艺制备的气缸套(气缸套二)作为试验对象。具体试验过程如下:为了保证试验过程中环配对副表面接触状态的稳定,贫油试验分为3个阶段:低载磨合阶段、高载磨合阶段、断油摩擦阶段。低载磨合阶段与高磨合阶段连续充分供油,供油量控制在3滴/min(约为0.1ml),磨合阶段结束时停止供油,保持载荷、温度不变,持续试验至拉缸。每组试验温度,载荷,磨合时间相同,保证环配对副在试验过程中供油量相等,各阶段试验参数见表2。表2贫油试验各阶段试验参数气缸套一和气缸套二分别进行四次贫油试验,并记录每次气缸套断油截止到拉缸的时间,参见表3。表3气缸套一和气缸套二断油截止到拉缸的时间第一次第二次第三次第四次平均时间气缸套一55min1h25min58min50min气缸套二6h11min5h29min7h02min6h45min6h22min由表3,从气缸套一与气缸套二的对比拉缸时间来看,气缸套二断油截止到拉缸的时间明显长于气缸套一断油截止到拉缸的时间。综上所述,本发明提供的表面石墨裸露球墨铸铁气缸套的制备工艺,通过特殊的加工工艺,使得球墨铸铁气缸套内孔工作表面的石墨可以完全裸露,其状态接近于金相试块石墨情况,充分发挥石墨储油、自润滑功能,从而提高缸套表面耐磨性机断油抗黏合性能,提高发动机运行的可靠性。本发明的说明书中,说明了大量具体细节。然而,能够理解,本发明的实施例可以在没有这些具体细节的情况下实践。在一些实例中,并未详细示出公知的方法、结构和技术,以便不模糊对本说明书的理解。最后应说明的是:以上各实施例仅用以说明本发明的技术方案,而非对其限制;尽管参照前述各实施例对本发明进行了详细的说明,本领域的普通技术人员应当理解:其依然可以对前述各实施例所记载的技术方案进行修改,或者对其中部分或者全部技术特征进行等同替换;而这些修改或者替换,并不使相应技术方案的本质脱离本发明各实施例技术方案的范围,其均应涵盖在本发明的权利要求和说明书的范围当中。当前第1页12