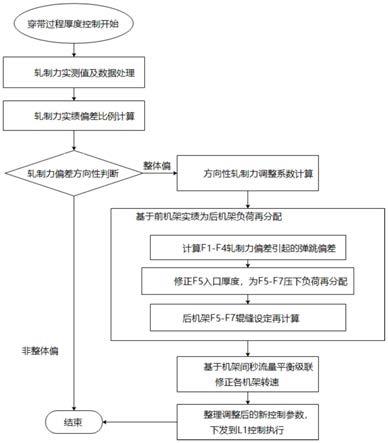
[0001]
本发明属于控制领域,尤其涉及一种用于轧钢过程中带钢头部厚度的控制方法。
背景技术:[0002]
在带钢的精轧工序(或称为工段)中,带钢经过多道次连续轧制,在精轧出口 处通过厚度测量装置检测带钢厚度,监控agc(automatic gauge control,热轧自 动厚度控制)根据该带钢实绩厚度、带钢目标厚度,确定厚度偏差,在一定程度上 调节末机架辊缝,以此修正带钢厚度。
[0003]
目前的常见的精轧厚度控制系统如图1图所示。图中f1至f7为精轧区域各机 架从前到后的依次编号(按照业内习惯,机架f1至f3,通常被称为前机架;f5至 f7,通常被称为后机架;亦有直接用f1至f7来代表第一至第七机架的习惯,下同)。
[0004]
厚度测量仪表一般安装在距离精轧出口约10米处,因此agc从带钢10米以 后位置介入调整,可以有效控制带身厚度精度。
[0005]
在少数产线上应用过穿带过程辊缝修正方法,但未考虑轧制稳定性,无法实现 大幅度厚度修正。
[0006]
明显地,在现有技术中,由于精轧来料信息的不准确或l2(过程控制计算机或 过程控制层别)控制模型设定不准等原因,往往会导致精轧出口厚度出现较大偏差。
[0007]
同时,一般热轧精轧在f7轧机后有厚度测量仪表。一般厚度测量后反馈到l1 (基础自动化计算机或基础自动化层别)监控agc控制系统,进行偏差识别后用 于辊缝动态调节,监控agc控制在穿带后1秒左右才能正式启动执行。因此只能 解决带钢的带身厚度偏差问题,对于带钢头部厚度异常难以改善。
[0008]
授权公告日为201年02月06日,授权公告号为cn 102233358 b的中国发明 专利中,公开了一种“利用穿带自适应修正热轧精轧机组辊缝的方法”,其包括以 下步骤,步骤一、确定第1~3机架轧制力偏差,步骤二、确定对设定变形抗力 造成影响的参数;步骤三、确定四种变形抗力调整策略,并根据偏差方式选用相应 的调整策略;步骤四、根据测量得到的第1~3机架的实际轧制力计算得到第1~ 3机架的变形抗力调整量,通过第1~3机架的变形抗力调整量得到第4~7机 架的变形抗力调整量;步骤五、最后根据厚度增量方程计算得到第4~7机架的 辊缝调整量。
[0009]
该技术方案采用前三个机架实测与设定轧制力的偏差信息,判断变形抗力的调 整类型,并分不同类型求得变形抗力调整量,最后求得后续机架的辊缝调整量并进 行动态设定,从而提高带钢的头部厚度控制精度。但这种方法没有对机架间秒流量 进行平衡,也未对后段机架进行压下负荷重新分配,不能很好的实现大幅度厚度纠 偏。
技术实现要素:[0010]
本发明所要解决的技术问题是提供一种精轧穿带过程中的厚度控制方法。其利 用精轧穿带过程中的前3个机架的实绩轧制力测量数据,动态识别预设定偏差,预 测带钢
出口厚度偏差,采用全线压下负荷重新分配、轧机转速、辊缝动态再计算方 式,重新对精轧所有机架进行控制参数再设定的方法,尽可能在后续道次中修正预 计算整体偏差带来的厚度异常情况,从而显著提高了热轧厚度控制精度。
[0011]
本发明的技术方案是:提供一种精轧穿带过程中的厚度控制方法,其特征是所 述的厚度控制方法包括下列步骤:
[0012]
1)轧制力实测值及数据处理;
[0013]
2)实绩轧制力与设定的偏差计算;
[0014]
3)设定的偏差方向性判断:若不存在整体性偏差,执行第8步骤;若存在整 体性偏差,执行下一步骤;
[0015]
4)方向性轧制力调整系数计算;
[0016]
5)基于前机架实绩为后机架负荷再分配;
[0017]
6)基于机架间秒流量平衡级联修正各机架转速;
[0018]
7)整理调整后的新控制参数:各机架转速、各机架辊缝等,并将设定值下发到 l1控制执行;
[0019]
8)结束本次精轧穿带过程的厚度控制。
[0020]
其中,所述步骤1)中的轧制力实测值及数据处理,包括精轧道次穿带完成后, 实际测量到带钢头部实绩轧制力数据由l1发到l2,l2对于测量数据进行基本处理, 判定数据是否有效,对于异常数据进行滤波处理。
[0021]
所述步骤2)中的实绩轧制力与设定的偏差计算,包括比较前三机架实绩值轧 制力与设定轧制力的分布,计算f1-f3机架实绩偏差比例。
[0022]
所述步骤3)中的设定的偏差方向性判断,包括根据前三机架实绩偏差比例, 判定是否具备方向性偏差特性与偏差方向。
[0023]
所述步骤4)中的方向性轧制力调整系数计算,包括根据偏差方向与偏差幅度 计算轧制力计算方向性调整系数。
[0024]
所述步骤5)中的基于前机架实绩为后机架负荷再分配,包括根据偏差系数计 算f4机架预计偏差,进一步计算f4机架辊缝差,得到f5机架入口厚度。结合精 轧目标厚度,对f5、f6、f7机架进行负荷再分配。
[0025]
所述步骤6)中的基于机架间秒流量平衡级联修正各机架转速,包括f1-f4机 架根据各机架新的出口厚度,级联修正轧辊转。
[0026]
进一步的,所述设定的偏差方向性判断,按照下列方式进行:
[0027]
单机架通过实绩轧制力f
sj
与设定轧制力f
set
比,计算出偏差系数f
corr
,判断实绩 偏向:
[0028][0029]
式中,f
sj
为机架穿带时l1采集实绩轧制力;f
set
为机架模型预设定轧制力;f
corr
为实绩轧制力与设定轧制力比例系数;
[0030]
分别计算f1、f2、f3三个机架轧制力系数,识别偏差方向,再组合多机架综 合判断整体设定偏差;
[0031]
当f1、f2、f3偏差方向相同时,判断为设定轧制力存在整体方向偏差;否则 当f2、
f3同向,且偏差系数均大于6%时,判断为设定轧制力存在整体偏差;否则 当f1、f3同向,且偏差系数均大于6%,判断为设定轧制力存在整体偏差。
[0032]
进一步的,所述的方向性轧制力调整系数计算,按照下列方式进行:
[0033]
具备轧制力整体方向性偏差时,计算方向性调整系数δf
corr
,用于重新优化计算 后机架轧制力;
[0034]
整体方向性轧制力调整系数δf
corr
计算方法如下:
[0035]
δf
corr
=f1
corr
*c1+f2
corr
*c2+f3
corr
*c3
[0036]
式中,δf
corr
为整体方向性轧制力系数,f1
corr
为f1机架轧制力偏差系数,f2
corr
为 f2机架轧制力偏差系数,f3
corr
为f3机架轧制力偏差系数,c1为f1机架权重,c2 为f2机架权重,c3为f3机架权重;
[0037]
由于方向性偏差存在误判的可能,为了防止过调,在方向性系数计算时,增加 限幅与衰减操作;
[0038]
方向性系数修正:
[0039]
δf
corr
=1
±
abs(δf
corr-1)*alpha
[0040]
式中,δf
corr
为调整系数,alpha为衰减系数,当δf
corr
>0时式中
±
取正号,
[0041]
δf
corr
<1时取负号。
[0042]
进一步的,在进行所述的基于前机架实绩为后机架负荷再分配之前,先计算 f1-f4轧制力偏差引起的弹跳偏差;
[0043]
计算f1-f4轧制力偏差引起的弹跳偏差,按照弹跳方程计算弹跳引起的厚度偏 差:
[0044][0045]
在计算弹跳偏差时,由于f4没有实绩轧制力,所以采用设定轧制力乘以方向性 修正系数代替;
[0046]
式中,δgap(i)为弹跳偏差量,f(i)
sj
为实绩轧制力,f(i)
set
为设定轧制力, stiffness(i)为轧机刚度,i为机架号(1、2、3、4)。
[0047]
进一步的,所述的基于前机架实绩为后机架负荷再分配,按照下列公式进行:
[0048]
eps(i)=h(i-1)-h(i)/h(i-1)
[0049]
式中,eps(i)为各机架新压下率,h(i)为各机架出口厚度,h(i-1)为各机架入口厚 度,i为机架号。
[0050]
进一步的,所述的基于机架间秒流量平衡级联修正各机架转速,还包括对后机 架f5-f7辊缝设定的再计算,即,在不改变预设定机架水、穿带速度的基础上,按 预计算流程重新计算f5、f6、f7的轧制力与辊缝。
[0051]
具体的,所述的轧制力采用如下公式计算:
[0052]
f=k
m
·
w
·
l
d
·
q
p
·
k
f
[0053]
式中,f—轧制力,w—宽度,l
d
—压扁接触弧长,k
m
—材料变形抗力,q
p
—外 摩擦影响系数,k
f
—轧制力学习系数。
[0054]
具体的,所述的辊缝采用如下公式计算:
[0055]
s
set
=h+s
z-s
m
+s
oil
+s
b
+s
wrs
+s
wrc-s
rw
+s
rh
+s
zset
[0056]
式中,s
set
为辊缝计算值,h为机架目标出口厚度,s
z
为零调轧制力时的辊缝, s
m
为轧制力引起的弹跳,s
oil
为油膜厚度偏差,s
b
为弯辊力引起的弹跳,s
wrs
为窜 辊引起的位置补偿量,s
wrc
为工作辊原始凸度补偿,s
rw
为工作辊磨损,s
rh
为工作 辊热膨胀偏差,s
zset
为零调时辊缝设定值。
[0057]
进一步的,所述的基于机架间秒流量平衡级联修正各机架转速,包括f1-f4各 机架新出口厚度计算和f1-f4各机架新轧辊转速计算。
[0058]
具体的,所述f1-f4各机架新出口厚度计算按照下列公式进行:
[0059]
h(i)
new
=h(i)
old
+δgap(i)
[0060]
式中,h(i)
new
为各机架新出口厚度,h(i)
old
为各机架预设定出口厚度,δgap(i)为 各机架弹跳偏差,i为机架号。
[0061]
具体的,所述f1-f4各机架新轧辊转速计算按照下列公式进行:
[0062]
v(i)
new
=v(i)
old
*h(i)
old
/h(i)
new
[0063]
式中,v(i)
new
为各机架新转速,v(i)
old
为各机架预设定转速,h(i)
old
为各机架预 设定出口厚度,h(i)
new
为各机架新出口厚度,i为机架号。
[0064]
与现有技术比较,本发明的优点是:
[0065]
1.本发明的技术方案,充分利用带钢在精轧前三道次测量得到的轧制力数据, 判定设定整体偏差方向与幅度,利用控制参数重新计算与设定实现精轧穿带过程中 带钢头部厚度的动态控制,来解决精轧设定整体偏差带来的头部厚度控制异常现象, 有效地提升了头部厚度控制指标精度;
[0066]
2.本发明的技术方案,在控制参数重新调整方面,覆盖了各机架出口厚度、轧 机速度两个关键因素,在1780热轧中实际应用,带钢头部厚度异常引起的封锁量 下降了60%;
[0067]
3.在传统控制原理的基础上,本发明的技术方案增加了精轧穿带过程中的多种 控制量动态再设定功能:控制系统在前三个机架穿带结束采集实绩轧制力测量数据 后,综合三个机架的偏差情况,进一步判定设定与实绩偏差方向,同时结合精轧目 标厚度,对未穿带机架进行厚度负荷再分配,在新负荷分配基础上,对精轧全线进 行流量平衡与速度级联调整,很好的解决了设定整体偏差带来的带钢头部厚度偏差 大的现象。
附图说明
[0068]
图1是现有精轧厚度控制系统的构成结构示意图;
[0069]
图2是本发明精轧穿带过程中厚度动态控制系统的构成结构示意图;
[0070]
图3是本发明精轧穿带过程中厚度动态控制流程方框图。图中,f1至f7为精轧区域各机架从前到后的依次编号。
具体实施方式
[0071]
下面结合附图和实施例对本发明做进一步说明。
[0072]
图2中,本申请的技术方案,利用f1、f2、f3穿带时头部实绩测量的轧制力 数据,识别带钢全长轧制力设定偏差,预测带钢头部厚度偏差量,开发出带钢精轧 穿带过程中的控
制调节技术,藉此来解决带钢轧制力设定整体偏差带来的带钢头部 厚度异常问题。
[0073]
本申请的技术方案,在传统控制原理的基础上,增加了精轧穿带过程中的多种 控制量动态再设定功能:控制系统在前三个机架穿带结束采集实绩轧制力测量数据 后,综合三个机架的偏差情况,进一步判定设定与实绩偏差方向,同时结合精轧目 标厚度,对未穿带机架进行厚度负荷再分配,在新负荷分配基础上,对精轧全线进 行流量平衡与速度级联调整,很好的解决了设定整体偏差带来的带钢头部厚度偏差 大的现象。
[0074]
具体的,对本发明技术方案详述如下:
[0075]
一、技术原理:
[0076]
l2厚度控制各种设定均是解决带钢头部厚度偏差情况,对于全长方向的厚度不 均匀不予考虑。本技术方案充分利用前机架测量得到的带钢头部实绩轧制力数据, 判定设定整体偏差方向与幅度,利用控制参数重新计算与设定实现精轧穿带过程中 带钢头部厚度的动态控制。其模型原理如下:
[0077]
(1)轧制力偏差方向性判:
[0078]
单机架通过实绩轧制力f
sj
与设定轧制力f
set
比,计算出偏差系数f
corr
,判断实绩 偏向:
[0079][0080]
式中,f
sj
为机架穿带时l1采集实绩轧制力;f
set
为机架模型预设定轧制力;f
corr
为实绩轧制力与设定轧制力比例系数。
[0081]
分别计算f1、f2、f3(即前述的第一至第三机架,下同)三个机架轧制力系数, 识别偏差方向,再组合多机架综合判断整体设定偏差,当f1、f2、f3偏差方向相 同时,判断为设定轧制力存在整体方向偏差;否则当f2、f3同向,且偏差系数均 大于6%时,判断为设定轧制力存在整体偏差;否则当f1、f3同向,且偏差系数均 大于6%,判断为设定轧制力存在整体偏差。
[0082]
(2)方向性轧制力调整系数计算:
[0083]
具备轧制力整体方向性偏差时,计算方向性调整系数δf
corr
,用于重新优化计算 后机架轧制力。
[0084]
整体方向性轧制力调整系数δf
corr
计算方法如下:
[0085]
δf
corr
=f1
corr
*c1+f2
corr
*c2+f3
corr
*c3
ꢀꢀꢀꢀꢀꢀ
(2)
[0086]
式中,δf
corr
为整体方向性轧制力系数,f1
corr
为f1机架轧制力偏差系数,f2
corr
为 f2机架轧制力偏差系数,f3
corr
为f3机架轧制力偏差系数,c1为f1机架权重,c2 为f2机架权重,c3为f3机架权重。
[0087]
由于方向性偏差存在误判的可能,为了防止过调,在方向性系数计算时,增加 限幅与衰减操作。
[0088]
方向性系数修正:
[0089]
δf
corr
=1
±
abs(δf
corr-1)*alpha
ꢀꢀꢀꢀꢀꢀ
(3)
[0090]
式中,δf
corr
为调整系数,alpha为衰减系数,当δf
corr
>0时式中
±
取正号,δf
corr <1时取负号。
[0091]
(3)计算f1-f4轧制力偏差引起的弹跳偏差:
设定出口厚度,h(i)
new
为各机架新出口厚度,i为机架号。
[0116]
二、技术方案:
[0117]
如图3中所示,本专利利用f1、f2、f3机架测量的头部轧制力实绩数据,识别 带钢设定与实绩偏差幅度,开发出带钢穿带过程中的控制参数再设定技术,解决了 带钢预设定整体偏差带来的厚度偏差量大问题。
[0118]
其具体技术步骤如下:
[0119]
2.1轧制力实测值及数据处理:
[0120]
精轧道次穿带完成后,实际测量到带钢头部实绩轧制力数据由l1发到l2,l2 对于测量数据进行基本处理,判定数据是否有效,对于异常数据进行滤波处理。
[0121]
l1采集实绩数据:
[0122][0123]
2.2实绩轧制力与设定的偏差计算:
[0124]
比较前三机架实绩值轧制力与设定轧制力的分布,计算f1-f3机架的实绩偏差 比例。
[0125]
2.3设定的偏差方向性判断:
[0126]
根据前三机架实绩偏差比例,判定是否具备方向性偏差特性与偏差方向。
[0127]
2.4方向性轧制力调整系数计算:
[0128]
根据偏差方向与偏差幅度计算轧制力计算方向性调整系数。
[0129]
2.5基于前机架实绩为后机架负荷再分配:
[0130]
根据偏差系数计算f4机架的预计偏差,进一步计算f4机架的辊缝差,得到f5 机架的入口厚度。结合精轧目标厚度,对f5、f6、f7机架进行负荷再分配。
[0131]
2.6基于机架间秒流量平衡级联修正各机架转速:
[0132]
所述的基于机架间秒流量平衡级联修正各机架转速,包括对后机架f5-f7辊缝 设定的再计算,即,在不改变预设定机架水、穿带速度的基础上,按预计算流程重 新计算f5、f6、f7的轧制力与辊缝。
[0133]
2.7整理调整后的新控制参数:各机架转速、各机架辊缝等,并将设定值下发 到l1控制执行:
[0134]
入口修正数据结构体:
[0135][0136]
实施例:
[0137]
入口厚度:45.71mm
[0138]
穿带带钢速度:11m/s
[0139]
目标宽度:1265mm 冷态
[0140]
目标厚度:3.53mm 冷态
[0141]
预设定数据:
[0142][0143]
1、轧制力实测值及数据处理:
[0144]
要求l1收集头部0.2s轧制力实绩值,剔除头部2个实绩点,去除最大最小值, 计算剩余点的平均轧制力。
[0145][0146]
l1返回f1、f2、f3机架的实绩轧制力分别为19038.3kn、17488.8kn、17178.5kn。
[0147]
2、轧制力实绩偏差比例计算:
[0148]
计算f1、f2、f3机架的实绩轧制力偏差比例:
[0149][0150]
[0151][0152]
f1-f3三个机架实绩轧制力偏差比例分别是-0.21、-0.09826、-0.08166。
[0153]
3、轧制力偏差方向性判断:
[0154]
三个机架实绩轧制力均小于0,偏差方向一致,且偏差比例绝对值均大于6%, 故判定为轧制力存在方向性偏差。
[0155]
4、方向性轧制力调整系数计算:
[0156]
权重系数c1设为0.2,c2设为0.3,c3设为0.4,衰减系数alpha取值0.63。
[0157]
δf
corr
=1+(-0.21*0.2-0.09826*0.3-0.08166*0.4)*0.6=0.934
[0158]
轧制力方向性调整系数通过f1、f2、f3机架的轧制力偏差加权计算得到0.934。
[0159]
5、计算f1-f4机架轧制力偏差引起的弹跳偏差:
[0160]
预测f(4)
sj
=0.934*16008.3=14951.7
[0161]
弹跳偏差:
[0162][0163][0164][0165][0166]
精轧前4机架f1至f4的弹跳偏差计算结果分别为:-0.8448、-0.3176、-0.2046、
ꢀ-
0.1921,单位mm。
[0167]
6、修正f5机架的入口厚度,为f5-f7机架压下负荷再分配:
[0168]
以f4机架出口厚度为输入,精轧目标厚度为输出,重新分配压下率:
[0169]
通过轧制力模型对后机架f5、f6、f7轧制力重新计算,得到新负荷下的轧制力:
[0170]
f(5)=12559(kn)
[0171]
f(6)=9191(kn)
[0172]
f(7)=7825(kn)
[0173]
使用轧制力调整系数进行乘法计算:
[0174]
f(5)
adj
=12559*0.934=11730(kn)
[0175]
f(6)
adj
=9191*0.934=8584(kn)
[0176]
f(7)
adj
=7825*0.934=7309(kn)
[0177]
至此,完成后机架负荷分配与轧制力计算。
[0178]
7、后机架f5-f7辊缝设定再计算:
[0179]
使用修正后的轧制力,通过辊缝模型对后机架f5、f6、f7辊缝重新计算:
[0180]
gap(5)
adj
=2.972(mm)
[0181]
gap(6)
adj
=2.337(mm)
[0182]
gap(7)
adj
=2.055(mm)
[0183]
至此,完成后机架辊缝计算,辊缝值随负荷分配变化而有所调整。
[0184]
8、基于机架间秒流量平衡级联修正各机架转速:
[0185]
f1、f2、f3机架根据实际轧制力所对应弹跳偏差δgap,计算实际流量厚度:
[0186]
eps(5)=0.2632
[0187]
eps(6)=0.18967
[0188]
eps(7)=0.13737
[0189]
h(1)
new
=24.919+(-0.8448)=24.0742(mm)
[0190]
h(2)
new
=15.1798+(-0.3176)=14.8622(mm)
[0191]
h(3)
new
=9.95581+(-0.2546)=9.7012(mm)
[0192]
f4机架根据预测弹跳偏差δgap(4),计算流量厚度:
[0193]
h(4)
new
=7.02141+(-0.1921)=6.829(mm)
[0194]
f5、f6、f7机架根据重新负荷分配,设定流量厚度:
[0195]
h(5)
new
=5.17339(mm)
[0196]
h(6)
new
=4.19214(mm)
[0197]
h(7)
new
=3.61626(mm)
[0198]
以出口带钢速度不变为原则,根据流量平衡计算f1-f4机架转速(线速度):
[0199]
v(1)
new
=1.44011*24.919/20.791=1.491(m/s)
[0200]
v(2)
new
=2.38645*15.1798/14.8622=2.437(m/s)
[0201]
v(3)
new
=3.67312*9.95581/9.70123=3.77(m/s)
[0202]
v(4)
new
=5.24077*7.02141/6.86075=5.388(m/s)
[0203]
f5-f7机架的转速根据负荷分配,调整计算输出:
[0204]
v(5)
new
=7.191(m/s)
[0205]
v(6)
new
=8.989(m/s)
[0206]
v(7)
new
=10.474(m/s)
[0207]
至此,根据机架间秒流量平衡原则,所有机架转速重新修正完毕。
[0208]
9、整理调整后的新控制参数,下发到l1控制执行:
[0209][0210]
至此,穿带过程厚度控制模型所有计算完成,有如下控制数据需要下发到l1执 行:精轧所有机架转速;后机架f5-f7的轧制力、出口厚度、辊缝。
[0211]
10、结论:
[0212]
现有在线控制模型仅在f7机架进行微量辊缝调整,在厚度控制上难以起到有效 控制。本申请技术方案中的模型基于精轧全线进行流量平衡,通过对后部3组机架 f5、f6和
f7进行厚度偏差修正,修正幅度大,调整能力强。
[0213]
本实施例中经穿带厚度控制模型修正,生产结束后f4-f7头部实绩轧制力如下:
[0214]
f
sj
(4)=15149(kn)
[0215]
f
sj
(5)=11260(kn)
[0216]
f
sj
(6)=8465(kn)
[0217]
f
sj
(7)=7453(kn)
[0218]
实绩出口厚度为3.633(mm),假设未使用本技术方案进行厚度修正,实绩轧制 力偏差按修正系数0.934计算,轧制力偏差量为:
[0219]
δf(7)=f
set
(7)*(1-δf
corr
)=7999.61*(1-0.934)=528(kn)
[0220]
在f7机架,528kn轧制力差,将造成大约0.1mm弹跳偏差,本案例带钢将偏 薄约0.1mm。
[0221]
由上可知,本申请的技术方案,利用精轧穿带过程中的前3个机架实绩轧制力 测量数据,动态识别预设定偏差,预测带钢出口厚度偏差,采用全线压下负荷重新 分配、轧机转速、辊缝动态再计算方式,重新对精轧所有机架进行控制参数再设定 的方法,尽可能在后续道次中修正预计算整体偏差带来的厚度异常情况,从而显著 提高热轧厚度控制精度。
[0222]
本发明可广泛用于精轧工段的带钢厚度控制领域。