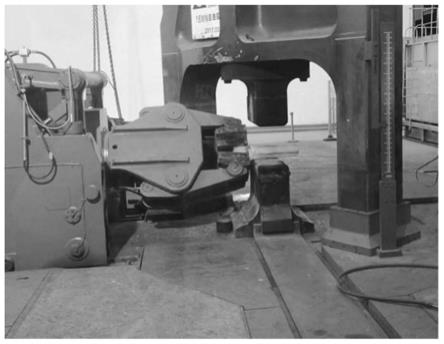
[0001]
本发明涉及智能锻造领域,具体涉及一种机器人智能自由锻拔长方法。
背景技术:[0002]
锻件在先进武器装备研制和发展中占有十分重要的地位,航空、航天、船舶、兵器等先进武器装备中的发动机、机体、弹体等大部分的关键受力构件均采用锻造工艺制造,而这些关键受力锻件形状尺寸和组织性能的精确控制程度,直接影响武器装备性能、结构重量系数、打击精度、可靠性、制造成本和寿命等各种重要指标。目前,我国锻件产量居世界第一位,已成为世界锻造大国。但是国内锻件生产大多数是由人工操作,锻件质量不稳定、生产效率低和工作环境恶劣,尤其是人工拔长工艺不适用于机器人智能拔长,成为制约我国向锻造强国发展的瓶颈,提升锻造工艺、装备和生产线的技术水平,实现锻造自动化、数字化和智能化尤为紧迫和重要。
[0003]
针对航空锻件组织性能对变形量、应变速率、变形温度反应灵敏的工艺特点,零件服役工况恶劣、锻件技术指标要求苛刻、服役寿命长的使用特点,以及产品一致性、可靠性和多品种小批量生产的特殊需求,开发适合轴类锻件自动化锻造工艺势在必行。
技术实现要素:[0004]
本发明为克服现有技术不足,提供一种机器人智能化自由锻拔长方法,该方法能解决目前轴类锻件产品一致性差、生产效率低的问题,可有助于提高轴类锻件的自动化、数字化和智能化制造水平。
[0005]
本发明的技术方案是:一种机器人智能化自由锻拔长方法包括以下步骤:
[0006]
一、有限元模拟,机器人末端执行器一般存在行程限制,最大压下量不超过70mm,根据轴类锻件工艺特征、机器人特性、设备参数,通过deform-mo模块对工艺方案进行模拟,对缺陷进行分析,工艺参数修正,确定适用于机器人自由锻的拔长工艺;所述适用于机器人自由锻的拔长工艺包含多道次的送进量、横截面尺寸和旋转角度参数;
[0007]
二、下料,获得一定规格的原始棒材;
[0008]
三、坯料加工,在原始棒材上加工出退刀槽,用于机器人夹持定位及翻转;
[0009]
四、加热,按加热规范对锻件加热至995-1005℃并保温一段时间;
[0010]
五、拔长,按照步骤一确定的工艺参数,在快锻机上进行多道次拔长,获得最终锻件;
[0011]
六、检测,进行锻件检查。
[0012]
本发明相比现有技术的有益效果是:本发明提出了一种可实现轴类锻件自动化锻造的拔长方法。考虑工艺特征、机器人特性、设备参数等因素,通过有限元模拟建立拔长工艺,使工艺满足机器人自动化锻造要求,从而实现轴类锻件自动化锻造。通过此方法能够实现轴类锻件智能自由锻,使得产品一致性好、提高了生产效率,获得形状尺寸及组织性能均符合要求的锻件。本发明可以应用与轴类锻件的成形过程中,是实现轴类锻件自动化锻造
的有效方法。此外,本发明拔长方法还可在汽车、能源、轨道交通、电力、船舶和航天等领域推广应用,将产生巨大的效益。
附图说明
[0013]
图1为具有轴线弯曲缺陷的传统人工拔长工艺锻件示意图;
[0014]
图2为表面具有裂纹缺陷的传统人工拔长工艺锻件示意图;
[0015]
图3为模拟缺陷图;
[0016]
图4为模拟缺陷应变分布图;
[0017]
图5为合格件有限元模拟结果图;
[0018]
图6为合格件有限元模拟应变分布图;
[0019]
图7为坯料加工图;
[0020]
图8为坯料加热规范图;
[0021]
图9为坯料机械手夹持位置图;
[0022]
图10为坯料锻造过程图;
[0023]
图11为坯料锻造工序图;
[0024]
图12为实施例的最终锻件图;
[0025]
图13为实施例的发动机主轴锻件最终锻件高倍组织图。
[0026]
具体实施方法
[0027]
下面结合附图并通过具体实施方案来进一步说明本发明的技术方案。
[0028]
如图1、图2所示,采用传统人工拔长工艺,依赖工艺制定人员的经验,工艺参数难以保证,且传统人工锻造的工艺参数需手工记录,难以实时监测锻件的温度及形状尺寸,易出现锻件轴线弯曲、表面裂纹等缺陷,造成产品一致性差,合格率低等问题。如图1所示轴线弯曲缺陷的锻件,图2所示的表面裂纹缺陷的锻件。
[0029]
结合图3-图11说明,一种可适合轴类锻件的机器人智能自由锻拔长方法,它包括以下步骤:
[0030]
一、有限元模拟,机器人末端执行器一般存在行程限制,最大压下量不超过70mm,根据轴类锻件工艺特征、机器人特性、设备参数,通过deform-mo模块对工艺方案进行模拟,对缺陷进行分析,工艺参数修正,确定适用于机器人自由锻的拔长工艺;所述适用于机器人自由锻的拔长工艺包含多道次的送进量、横截面尺寸和旋转角度参数,其中,每次压下量需满足机器人末端执行器行程范围要求;如图5和图6所示;
[0031]
二、下料,获得一定规格的原始棒材;如图7所示;
[0032]
三、坯料加工,在原始棒材上加工出退刀槽,用于机器人夹持定位及翻转;如图7所示;
[0033]
四、加热,按加热规范对锻件加热至1000℃并保温54min;如图8所示;
[0034]
五、拔长,按照步骤一确定的工艺参数,在机器自由锻压机上进行多道次拔长,如图9-图11所示,采用先锻方形后锻圆形的方式,经10道次拔长,获得最终锻件。例如,总锻造时间为3-4min。
[0035]
六、检测,进行锻件检查。对最终锻件进行形状尺寸及组织性能检查,应符合相关要求,最终锻件的温度要大于800℃。
[0036]
为了便于说明此智能自由锻拔长方法,以一种c250钢发动机主轴锻件成形过程为例:传统拔长工艺往往在空气锤等设备上进行,压下量与送进量均为人工控制,工艺参数不稳定,难以满足自动化锻造的要求。传统拔长工艺方案如表1所示。
[0037]
表1传统拔长工艺方案
[0038][0039]
首先进行拔长工艺计算,实际生产中对压下量取值范围常取故取δh>54mm。实际生产中确定送进量时常取l=(0.4~0.8)b,故取l=100~200mm,其中l表示送进量,h表示压下量,b表示表示平砧宽度,考虑到选用机器人末端执行器的压下量最大量为70mm,因此,首次压下量的值为54mm<δh<70mm。选用设备为16mn快锻机,最大行程为1400mm,最大速度为0.9m/s,可满足工艺要求。结合锻件工艺计算对传统工艺方案进行调整,拟定自由锻过程的送进量、压下量、压下速度、始锻温度、终锻温度等工艺参数,锻造工序如图11所示。
[0040]
通过deform-mo模块对拔长过程进行模拟,有限元模拟可以看出,拔长过程易出现应变分布不均,表面折迭,端面内凹,表面不平整等缺陷如图3和图4所示。通过对模拟结果的分析可知,送进量过大或压下量过小易产生折叠;拔长温度过低易产生裂纹;首次送进量太小,表面金属变形而中心部位金属变形较小,易产生端面缩口等。因此,对工艺参数进行修正调整,获得质量较好的锻件模拟结果如图5所示,应变分布结果如图6所示,可看出该工艺方案基本可以解决应变分布不均,表面折叠,轴线弯曲等缺陷,其拔长工艺方案如表2所示。
[0041]
表2智能自由锻拔长工艺方案
[0042][0043]
对原始坯料进行加工,如图7所示,将直径d为180mm,长度l为580mm的原始棒材机加出宽度w为20mm的退刀槽,用于机器人夹持定位和翻转,如图7所示。按加热规范对机加后坯料进行加热,加热规范如图8所示,实际按加热规范对锻件加热至1000℃并保温54min,
[0044]
自由锻在16mn快锻机上进行,锻造前锤砧及工夹具接触坯料的部位充分预热至250
±
50℃,采用自动化锻造工艺进行十道次拔长,坯料夹持位置及锻造过程如图9和图10所示。如图9-图11所示,经十道次自动化拔长后,采用先锻方形后锻圆形的方式,其中原始棒材的待拔长度l1=330mm,第一工序的锻方形拔长后,拔长部分的长度l2=630mm,截面宽度h约为120mm,第二工序的锻造滚圆拔长后,得到的轴类锻件如图12所示,拔长部分滚圆后
的长度l3=650mm,直径d约为122mm。
[0045]
对锻件进行检测,总锻造时间约为3-4min,最终拔长后的温度为820℃,符合终锻温度标准。最终锻件直径d约为122mm,拔长段的长度l3=650mm,形状尺寸符合锻件公差要求。对同轴度进行检测,检测结果满足拔长端与非拔长端的同轴度要求。对表面质量进行检测,无折叠、端面内凹、表面不平整等缺陷。对锻件性能进行检测,屈服强度为1720mpa,抗拉强度为1800mpa。对锻件组织进行检测,锻件的晶粒度均为6级,满足标准要求,夹杂物优于标准要求,高倍组织照片如图8所示。说明采用此发明方法可以完成智能拔长,可以有效改善成形缺陷,得到形状尺寸及组织性能均符合要求的锻件,克服了过去传统人工拔长中的锻件一致性较差、拔长过程实时工艺参数无法直接记录等问题。
[0046]
本发明已以较佳实施案例揭示如上,然而并非用以限定本发明,任何熟悉本专业的技术人员,在不脱离本发明技术方案范围内,当可以利用上述揭示的结构及技术内容做出些许的更动或修饰为等同变化的等效实施案例,均仍属本发明技术方案范围。