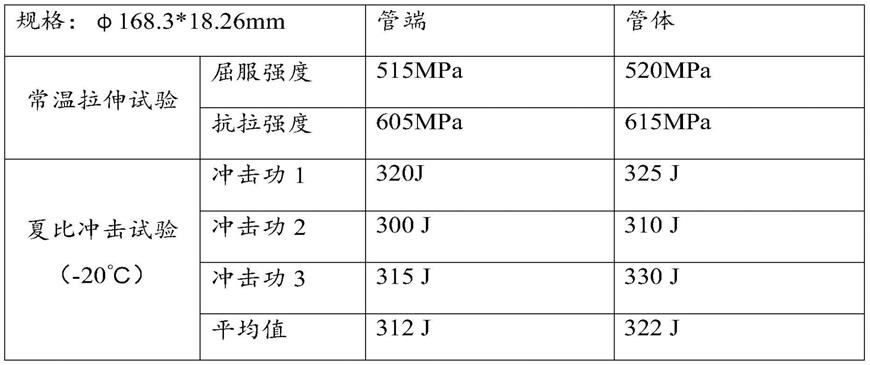
1.本发明属于石油管加工制造技术领域,尤其涉及提高深海用钢悬链立管的管端尺寸精度的方法。
背景技术:2.随着海洋油气产业的发展,越来越多的深海或者超深海油气资源被勘探和发现,不管海洋油田开发采用何种浮式平台,都需要使用立管,而钢悬链立管在深海及超深海油田的开采中使用最为广泛。钢悬链立管在服役过程中由于受到海浪、涡流、内压作用的影响,成为海洋管道系统中薄弱易损的构件之一,在内部流体和外部载荷的作用下会发生疲劳破坏造成失效,尤其是触地点和顶部连接处极易受到疲劳损伤,而焊接接头则是疲劳失效的薄弱部位,管与管之间的尺寸精度影响了焊接匹配度,从而影响了焊接接头的疲劳寿命,因此对于钢悬链立管来说,管端尺寸精度成为提高深海钢悬链立管的疲劳寿命的关键。
3.钢悬链立管的管端尺寸精度要求极为苛刻,钢悬链立管要求:high/low错位差:≤0.5mm,内径公差:≤
±
0.25mm。目前热轧无缝钢管的尺寸远达不到钢悬链立管的使用要求,而热处理后管端定径虽然能够改善管端尺寸精度,但是也无法满足钢悬链立管的尺寸要求,管端尺寸问题成为了制约深海钢悬链立管研发的关键。
4.专利ca2680943中提到了管端墩粗的方法可用于钢悬链立管触地点,通过壁厚加厚来降低分布在横截面上的应力,从而提高疲劳寿命。但是也存在以下几个问题:1,此发明没有提到墩粗后需要进行机加工,所以墩粗后管端尺寸精度问题会影响焊接匹配度,进而影响疲劳性能;2,此发明中墩粗壁厚增加较厚,需要通过提高cr、mo等合金元素来增加淬透性,增加了成本;3,墩粗后管子分为加厚端、过渡段和管体,以上三个区域金相组织不一样,力学性能也有差别,过渡段这种几何结构会造成服役过程的应力集中。
5.因此,基于这些问题,提供一种能解决钢悬链立管的管端尺寸精度问题的提高深海用钢悬链立管的管端尺寸精度的方法,具有重要的现实意义。
技术实现要素:6.本发明的目的在于克服现有技术的不足,提供一种能解决钢悬链立管的管端尺寸精度问题的提高深海用钢悬链立管的管端尺寸精度的方法。
7.本发明解决其技术问题是采取以下技术方案实现的:
8.提高深海用钢悬链立管的管端尺寸精度的方法,包括如下步骤:
9.热轧后进行立管两端100
‑
350mm范围墩粗,达到管端壁厚微增加;
10.墩粗过程管端整体壁厚增加4
‑
8mm,壁厚单边增加2
‑
4mm;
11.墩粗后进行调质热处理,得到均匀细小的回火贝氏体和铁素体的混合组织,且管端与管体组织性能基本保持一致;
12.管端内、外壁进行机加工,在墩粗的过渡段平滑过渡;
13.机加工后,管端内径公差小于
±
0.25mm,管端内径比名义内径小约0.25
‑
2mm。
14.进一步的,所述热轧后进行立管两管端墩粗的方法为:
15.对热轧后立管进行感应加热,加热到950℃
‑
1150℃,保温100
‑
200s;
16.保温后的管料运送到加厚模具,用冲头进行挤压;
17.冲头达到设定的保护限位后恢复原位,加厚过程完成。
18.进一步的,所述墩粗后进行调质热处理的方法为:
19.将立管在步进炉内加热到900
‑
950℃,保温15
‑
40min,出炉,浸入式旋转淬火,然后在步进炉内加热到620
‑
670℃,保温30
‑
90min,进行回火处理,达到x60q
‑
x70q钢级性能水平。
20.进一步的,所述管端内、外壁进行机加工,在墩粗的过渡段平滑过渡的方法为:
21.将热处理后的立管定心,进行内外表面机加工,加工后管端外径与管体外径保持一致,管端内径比名义内径小约0.25
‑
2mm,然后将机加工末端处理成平滑过渡。
22.本发明的优点和积极效果是:
23.1、本发明使用墩粗、热处理、机加工的方法,从根本上解决了热轧无缝管线的管端尺寸精度问题;本发明中使用较低的墩粗变形温度(950
‑
1150℃),使其在墩粗过程中防止晶粒粗大,墩粗后得到较为细小晶粒,减小热处理前管端墩粗段与管体的原始组织差异,为后面热处理保证管端与管体组织性能一致奠定基础;本发明设计墩粗微加厚(整体壁厚增加4
‑
8mm),减小了管端墩粗段与管体的壁厚差异,不需要因为管端的加厚来增加合金元素,降低了成本,同时壁厚的微量增加也能防止在淬火过程中管端因为太重而发生弯曲;
24.2、本发明中的热处理工艺,调制处理后管端与管体的晶粒度和组织基本保持一致,管端与管体的力学性能差异很小,保证了管子性能的均匀性,避免因组织性能差异造成服役过程中产生应力集中而降低疲劳寿命;
25.3、本发明热处理后对管端进行内、外表面机加工,得到了很好的管端尺寸精度,内径公差能很好的满足甚至超越钢悬链立管的要求(
±
0.25mm),除此之外,外径公差、管端不圆度等尺寸公差也极大的超越了钢悬链立管的要求,这极大的提高了后续焊接过程中管与管之间的匹配度,避免了因为尺寸公差引起焊接应力集中带来的疲劳寿命下降,并且在内、外壁机加工后,保证内外表面加工末端平滑过渡,降低应力集中,从而提高疲劳性能;
26.4、本发明机加工后外径与名义外径保持一致,内径要比名义内径小0.25
‑
2mm,因此,壁厚要稍大于名义壁厚,管端的横截面积要稍大于名义值,因此可以通过微增加横截面来降低焊接接头的循环加载应力值,从而提高焊接接头的疲劳寿命;本发明无需通过整管壁厚增加,然后内壁机加工来满足内径要求,本方法避免了因为管体壁厚增加带来的钢悬链立管重量增加问题,避免了因重量增加带来的成本增加,同时也避免了重量增加带来的服役过程中的安全问题,提高了使用安全系数。
附图说明
27.以下将结合附图和实施例来对本发明的技术方案作进一步的详细描述,但是应当知道,这些附图仅是为解释目的而设计的,因此不作为本发明范围的限定。此外,除非特别指出,这些附图仅意在概念性地说明此处描述的结构构造,而不必要依比例进行绘制。
28.图1为本发明实施例中提供的墩粗加厚后的立管的管端结构示意图;
29.图2为本发明实施例中利用提高深海用钢悬链立管的管端尺寸精度的方法进行管
端机加工后的结构示意图;
具体实施方式
30.需要说明的是,在不冲突的情况下,本申请中的实施例及实施例中的特征可以相互组合。
31.实施例1
32.本实例采用管端墩粗、热处理、机加工的方法实现深海用φ168.3*18.26mm规格钢悬链立管管端内径公差达到≤
±
0.25mm。在热轧后选取φ168.3*18.26mm规格管子一根。墩粗设计图纸如图1所示,壁厚整体增加4
‑
8mm,壁厚单边外壁增加2
‑
4mm,壁厚单边内壁增加2
‑
4mm。将管子置于墩粗线上,a端进行夹持固定,b端进行感应加热,温度为1050℃,保温150s,在设计的模具内一次变形,实现管端150mm范围墩粗加厚4
‑
8mm左右,空冷至室温。然后用同样的墩粗工艺将管子a端150mm范围墩粗加厚4
‑
8mm左右,空冷至室温;
33.将φ168.3*18.26mm规格墩粗后的管子进行调制热处理,将管子在高温步进炉内加热到900
‑
950℃,保温15
‑
30min,出炉,浸入式旋转淬火,然后在低温步进炉内加热到620
‑
670℃,保温30
‑
80min,进行回火处理,达到x65q钢级性能水平;
34.将热处理后φ168.3*18.26mm规格墩粗管子进行管端内表面和外表面机加工,定心后,进行内外表面机加工,加工后管端外径与管体外径保持一致,管端内径比名义内径小约0.25
‑
2mm,然后将机加工末端处理成平滑过渡。对管端150mm尺寸进行测量,内径范围:130.90
‑
131.21mm,只有0.31mm的波动范围,远远超出了
±
0.25mm的要求;对管端和管体进行晶粒度组织分析,发现管端和管体晶粒度和组织基本一致,回火贝氏体和铁素体的混合组织,晶粒度9.0
‑
9.5级。对管端和管体进行力学性能测试,如表1,可以看出管端与管体性能基本一致,波动很小:
35.表1
[0036][0037]
实施例二
[0038]
本实例采用管端墩粗、热处理、机加工的方法实现深海用φ273.1*25.4mm规格钢悬链立管管端内径公差达到≤
±
0.25mm。在热轧后热处理前选取φ273.1*25.4mm规格管子一根,墩粗设计图纸如图1所示,壁厚整体增加4
‑
8mm,壁厚单边外壁增加2
‑
4mm,壁厚单边内壁增加2
‑
4mm。将管子置于墩粗线上,a端进行夹持固定,b端进行感应加热,温度为1100℃左右,保温200s,在设计的模具内一次变形,实现管端200mm墩粗加厚4
‑
8mm左右,空冷至室温。
然后用同样的墩粗工艺将管子a端200mm范围内墩粗加厚4
‑
8mm左右,空冷至室温;
[0039]
将φ273.1*25.4mm规格墩粗后的管子在步进炉内进行调制热处理,将管子在高温步进炉内加热到900
‑
950℃,保温15
‑
40min,出炉,浸入旋转式水淬,然后在低温步进炉内加热到620
‑
670℃,保温30
‑
90min,进行回火处理,达到x65q钢级性能水平;
[0040]
将热处理后φ273.1*25.4mm规格墩粗管子进行管端内表面和外表面机加工,定心后,进行内外表面机加工,管端内径比名义内径小0.25
‑
2mm左右,然后将机加工末端处理成平滑过渡。对管端200mm尺寸进行测量,内径范围:222.13
‑
222.34mm,只有0.21mm波动的范围,远远超出了
±
0.25mm的要求;对管端和管体进行晶粒度组织分析,发现管端和管体晶粒度和组织基本一致,回火贝氏体和铁素体的混合组织,晶粒度9.0~9.5级。对管端和管体进行力学性能测试,如表2,可以看出管端与管体性能基本一致,波动很小:
[0041]
表2
[0042][0043]
以上实施例对本发明进行了详细说明,但所述内容仅为本发明的较佳实施例,不能被认为用于限定本发明的实施范围。凡依本发明申请范围所作的均等变化与改进等,均应仍归属于本发明的专利涵盖范围之内。