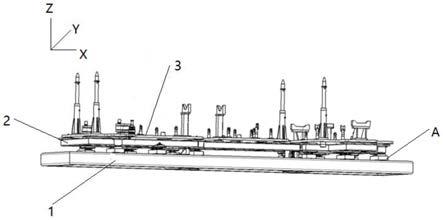
1.本发明涉及车辆装配设备技术领域,尤其涉及一种整体浮动合装托盘系统。
背景技术:2.在车辆自动化装配过程中,大部分采用模块化生产方式,即将底盘零件按模块划分,通过设置多个托盘,将不同模块分装在不同的托盘上,然后通过吊装设备将分装完成的托盘搬运至底部框架上,以形成一套承载了底盘总成的合装托盘。
3.现有的车辆车身与预装有底盘总成的合装托盘进行合装时,首先将车辆车身预装在吊具上,z向通过吊具将车辆车身置于预装有底盘模块的合装托盘上,完成合装。而实际装配时,由于车身的制造偏差、合装托盘的制造偏差、底盘模块零件的装配偏差的存在,导致车身定位孔与合装托盘上的定位销错位不能完成合装。合装时,需分别调节吊具、合装托盘和底板模块的零部件位置以消除错位才能完成合装,故大大降低了合装效率。且调节过程中错位不可能完全消除,此种情况下进行合装,合装托盘、合装设备或车辆零部件将会受到较大侧向力,使合装托盘、设备或车辆零部件受损。
技术实现要素:4.(一)要解决的技术问题
5.鉴于现有技术的上述缺点、不足,本发明提供一种整体浮动合装托盘系统,解决了现有技术中合装托盘水平方向不可移动导致的合装效率低、合装托盘及车辆零部件易损坏的问题。
6.(二)技术方案
7.为了达到上述目的,本发明提供了一种整体浮动合装托盘系统,具体技术方案如下:
8.一种整体浮动合装托盘系统,包括由下至上依次设置的运输底框层、支撑层和合装托盘;
9.合装托盘设置于支撑层,支撑层通过连接机构连接于运输底框层,连接机构包括:
10.浮动机构,与支撑层和运输底框层相连接,并能够带动支撑层相对于运输底框层在第一平面内沿x向和/或y向移动;
11.浮动锁定机构,与支撑层和运输底框层相连接,浮动锁定机构被配置为适于使支撑层相对于运输底框层锁定或可移动。
12.进一步,浮动机构包括第一浮动装置和限位装置;第一浮动装置包括第一底板、第一万向滚珠、第一安装板和第一滚动板;
13.第一安装板与支撑层相连接,第一滚动板与第一安装板相连接;
14.第一底板与运输底框层相连接,第一万向滚珠设置于第一底板,其中,第一滚动板与第一万向滚珠滚动连接;
15.限位装置与第一安装板和第一底板连接,用于限定第一滚动板相对于第一万向滚
珠的滚动范围。
16.进一步,限位装置包括限位柱、限位盖板、锁紧螺母和限位套;限位柱的一端与第一底板相连接,另一端穿设于限位盖板;
17.限位套套设于限位柱外周,并位于第一底板和限位盖板之间,限位套与第一安装板相连接;
18.其中,限位套内径大于限位柱外径,限位盖板通过锁紧螺母压接于限位套的顶部,并能够使限位柱在限位套内部移动。
19.进一步,浮动锁定机构包括锁定套和锁定装置,锁定套设置于支撑层,锁定装置设置于运输底框层;
20.锁定装置能够与锁定套可选择的连接,连接时支撑层相对于运输底框层锁定。
21.进一步,锁定装置包括安装件、导轨滑块、拉伸弹簧、滑块安装板、推板、锁定销、转柄和锁定套;
22.安装件固定于运输底框层,导轨沿垂直于第一平面的方向设置于安装件;
23.滑块安装板与滑块相连接,并相对于焊接安装件可滑动,锁定销和推板均设置于滑块安装板,推板通过拉伸弹簧与焊接安装件连接,锁定销能够在外力或拉伸弹簧力的作用下插入或拔出锁定套;
24.转柄转动连接于安装件,转柄转动能够使部分转柄与锁定套的通孔相对设置。
25.进一步,锁定装置还包括第二压缩弹簧、转动座和转轴;转动座与安装件连接,转柄通过转轴转动连接于转动座;
26.第二压缩弹簧的两端分别与转柄和安装件连接,在外力或第二压缩弹簧的弹簧力的作用下,转柄能够绕转轴转动。
27.进一步,连接机构还包括自动对中机构;自动对中机构包括第二浮动装置和对中装置;
28.第二浮动装置与支撑层和运输底框层相连接,并能够带动支撑层相对于运输底框层在第一平面内沿x向和/或y向移动;
29.对中装置与第二浮动装置相连接,用于对支撑层的中位线与运输底框层的中位线的对准进行复位。
30.进一步,第二浮动装置包括第二底板、第二万向滚珠、第二安装板和第二滚动板;
31.第二安装板与支撑层连接,第二滚动板与第二安装板连接;
32.第二底板与运输底框层连接,对中装置和第二万向滚珠分别设于第二底板的两端,其中,第二滚动板滚动连接于第二万向滚珠。
33.进一步,对中装置包括回位板、第三万向滚珠、滑动轴、铜套、滑动套和第一压缩弹簧;
34.回位板固定于第二底板;
35.滑动轴通过铜套套装于滑动套内,一端通过第一压缩弹簧与滑动套弹性连接,另一端通过第三万向滚珠与回位板抵接;
36.回位板上表面设置有回转斜面,在第一压缩弹簧力或外力的作用下,滑动轴能够推动第三万向滚珠沿回转斜面滚动。
37.进一步,支撑层上还设置有多个定位销支撑和/或多个平板支撑,位于支撑层和合
装托盘之间;
38.多个定位销支撑与合装托盘相抵接或相连接,用于限定合装托盘沿x向和y向移动;
39.多个平板支撑与合装托盘相接触用于承托合装托盘。
40.本发明提供的的整体浮动合装托盘系统,用于车辆底盘模块与车辆车身进行合装。合装托盘设于支撑层,支撑层通过连接机构连接于运输底框层。其中,连接机构包括浮动机构和浮动锁定机构,其中浮动机构为平面移动副,水平方向上可x向或y向移动,以使支撑层相对于运输底框层浮动。合装时,将底盘模块预安装在合装托盘上,通过吊具将车辆车身移动至合装托盘上方,如果存在错位,外力推动支撑层x向或y向移动以消除错位,使合装托盘上的定位销的定位销顺利插入车身定位孔,撤去外力,通过浮动锁定机构将支撑层位置锁定,完成合装。合装时无需调节其它零部件的装配尺寸,仅通过调节支撑层即可消除错位,大大提高了车辆车身与底盘总成的合装效率,且错位可完全消除,进而避免了由于错位导致的合装托盘、合装设备或车辆零部件将会受到较大侧向力,使合装托盘、设备或车辆零部件受损。
附图说明
41.此处所说明的附图用来提供对本申请的进一步理解,构成本申请的一部分,本申请的示意性实施例及其说明用于解释本申请,并不构成对本申请的不当限定,在附图中:
42.图1为具体实施方式中整体浮动合装托盘系统的结构示意图;
43.图2为具体实施方式中整体浮动合装托盘系统的爆炸图;
44.图3为具体实施方式中整体浮动合装托盘系统中支撑层和运输底框层的结构示意图;
45.图4为具体实施方式中浮动机构的结构示意图;
46.图5为具体实施方式中自动对中机构的结构示意图;
47.图6为具体实施方式中浮动锁定机构的结构示意图。
48.【附图标记说明】
49.1、运输底框层;2、支撑层;
50.3、合装托盘;31、前托盘;32、中托盘;33、后托盘;
51.a、连接机构;4、浮动机构;
52.41、第一浮动装置;411、第一万向滚珠;412、第一底板;413、第一滚动板;414、第一安装板;
53.42、限位装置;421、限位柱;422、限位套;423、限位盖板;424、锁紧螺母;
54.5、自动对中机构;
55.51、第二浮动装置;511、第二万向滚珠;512、第二底板;513、第二安装板;514;第二滚动板;
56.52、对中装置;521、回位板;522、第三万向滚珠;523、滑动轴;524、铜套;525、滑动套;526、第一压缩弹簧;
57.6、浮动锁定机构;
58.61、锁定套;
59.62、锁定装置;621、安装件;622、导轨滑块;623、滑块安装板;624、推板;625、锁定销;626、转动座;627、转柄;628、第二压缩弹簧;629、转轴;630、拉伸弹簧;
60.7、平板支撑;8、定位销支撑。
具体实施方式
61.为了更好的解释本发明,以便于理解,下面结合附图,通过具体实施方式,对本发明作详细描述。
62.参见图1,本实施例提供了一种整体浮动合装托盘系统,包括由下至上依次设置的运输底框层1、支撑层2和合装托盘3。其中,合装托盘3设置于支撑层2,支撑层2通过连接机构a连接于运输底框层1,合装托盘3用于预装底盘总成。合装时,通过吊具将车辆底盘吊至合装托盘3上方进行合装。
63.具体地,参见图2至图6,本实施例中的连接机构a具体包括浮动机构4、自动对中机构5和浮动锁定机构6,分别设于支撑层2和运输底框层1之间。其中,浮动机构4为平面移动副,在第一平面内可x向和/或y向移动,以使支撑层2浮动连接于运输底框层1。自由状态下,支撑层2和运输底框层1处于中位。合装时,当车辆车身和底盘总成出现错位时,外力推动支撑层2相对于运输底框层1x向和/或y向移动,以消除车辆车身与底盘总成的错位,使合装托盘3定位销顺利插入车身定位孔。随后撤去外力,支撑层2在自动对中机构5的作用下自动复位至中位,然后通过浮动锁定机构6将支撑层2锁定,使支撑层2相对于运输底框层1不能移动,进行拧紧作业完成合装。
64.进一步,参见图3,本实施例中的浮动机构4包括第一浮动装置41和限位装置42。其中,第一浮动装置41包括第一安装板414、第一滚动板413、第一底板412和第一万向滚珠411。第一安装板414固定于支撑层2的底部,第一滚动板413固定于第一安装板414的底部,第一底板412固定于运输底框层1的上部。第一底板412上设置有第一安装孔,第一万向滚珠411安装在第一安装孔内,可以在第一安装孔内自由转动,同时与第一滚动板413滚动连接。第一安装板414和第一底板412通过限位装置42连接,限位装置42用于限制第一滚动板413相对于与第一万向滚珠411的滚动范围,进而限定支撑层2相对于运输底框层1的移动范围,以使支撑层2在一定范围内浮动。合装时,外力推动支撑层2,第一滚动板413在第一万向滚珠411上滚动以使支撑层2相对于运输底框层1移动,消除错位,第一万向滚珠411和第一滚动板413的设置大大减小了支撑层2移动时的摩擦阻力,且所需的外力比较小,便于调节。进一步,第一滚动板413具有较高的表面粗糙度,为机械加工面,进而降低了第一万向滚珠411的滚动阻力,同时减小了第一万向滚珠411和第一滚动板413的磨损程度,进而延长了设备的使用寿命。
65.本实施例中限位装置42包括限位柱421、限位套422、限位盖板423和锁紧螺母424。其中,限位套422固定于第一安装板414,限位柱421固定于第一底板412,限位套422套装在限位柱421的外周,限位盖板423套装于限位柱421的端部,并通过锁紧螺母424压接于限位套422的顶部。限位套422内径大于限位柱421的外径,限位柱421只能在限位套422内x向和/或y向移动,以使支撑层2相对于运输底框层1在一定范围内浮动。本实施例中,第一浮动装置41可以和限位装置42配合使用,也可以单独设置,可根据具体承重和运动需求配置第一浮动装置41和限位装置42的套数。作为示例,本实施例共配置8套第一浮动装置41,4套限位
装置42。其中4套限位装置42和4套第一浮动装置41配合使用,剩余4套第一浮动装置41单独使用,第一浮动装置41和限位装置42关于运输底框层1的x轴中心线对称布置,以使支撑层1相对运输底框层1平稳地浮动,提高了使用安全性。
66.参见图5,本实施例中的自动对中机构5包括第二浮动装置51和对中装置52。其中,第二浮动装置51的结构与第一浮动装置41的结构相同,包括第二底板512、第二万向滚珠511、第二滚动板514和第二安装板513。第二安装板513固定于支撑层2的底部,第二滚动板514固定于第二安装板513的底部,第二底板512固定于运输底框层1的上部,第二底板512的两端分别设置有第二安装孔和第三安装孔。第二万向滚珠511安装于第二安装孔内,对中装置52安装于第三安装孔内,用于对支撑层2的中位线与运输底框层1的中位线对准进行复位。具体地,对中装置52包括回位板521、第三万向滚珠522、滑动轴523、铜套524、滑动套525和第一压缩弹簧526。滑动套525通过铜套524套装在滑动轴523的端部,滑动轴523一端通过第一压缩弹簧526与滑动套525弹性连接,另一端连接第三万向滚珠522,第三万向滚珠522在第一压缩弹簧526的弹簧力的作用下与回位板521抵接,滑动套525在第一压缩弹簧526的弹簧力的作用下抵接于合装托盘3底部。回位板521固定于第三安装孔内,上表面设置有回转斜面。当第三万向滚珠522轴线与回位板521轴线重合时,支撑层2相对于运输底框层1处于中位。当支撑层2受到外力作用移动偏离中位,第三万向滚珠522跟随移动至回位板521的回转斜面上,由于支撑层2与运输底框层1相对高度不变,进而第一压缩弹簧526被压缩。当外力撤去后,第三万向滚珠522在第一压缩弹簧526弹力作用下滑离回转斜面,直至第三万向滚珠522的轴线与回位板521轴线重合,此时支撑层2相对于运输底框层1处于中位。可根据称重及运动需求配置至少2套自动对中机构5。作为示例,本实施例配置4套自动对中机构5,4套自动对中机构关于运输底框层1的x轴中心线对称布置,自由状态下,使支撑层2相对于运输底框层处于中位,无需手动调节,方便快捷。
67.本实施例中,参见图6,浮动锁定机构6包括锁定套61和锁定装置62,锁定套61固定于支撑层2,锁定装置62固定于运输底框层1,锁定装置62能够可选择地插接于锁定套61内。当锁定装置62插接于锁定套61内时,支撑层2相对运输底框层1位置锁定,不能浮动。当锁定装置62从锁定套61内脱离时,支撑层2相对于运输底框层1解除锁定,可以浮动。其中,锁定装置62具体包括安装件621、导轨滑块622、拉伸弹簧630、滑块安装板623、推板624、锁定销625、转柄627、第二压缩弹簧628、转动座626、转轴629和锁定套61。安装件621为焊接件,固定于运输底框层1,导轨固定在安装件621上,滑块固定在滑块安装板623上,滑块滑动连接在导轨上。锁定销625和推板624分别固定在滑动安装板623上,拉伸弹簧630一端与推板624连接,另一端与安装件621连接,锁定销625能够在外力或拉伸弹簧630力的作用下插入或拔出锁定套61。转动座626固定于安装件621,转动座626上设置有与转轴629匹配的通孔,并设有转柄卡槽,转柄627通过转轴629连接在转柄卡槽内,转柄627可以绕转轴629在转柄卡槽内转动。转柄627一端通过第二压缩弹簧628连接于安装件621,转柄627和安装件621上对应设置有第二压缩弹簧628安装盲孔,转柄627可以在外力或第二压缩弹簧628力的作用下绕转轴629转动。当支撑层2需要锁定时,手动按压转柄627一端,使转柄627向贴合安装件621的方向移动,使转柄627让开锁定销625。然后外力z向向上推动推板624,带动滑块安装板623沿导轨向上滑动,直至锁定销625插入锁定套61内,以将支撑层2锁定。撤去转柄627上外力,转柄627在第二压缩弹簧628的弹簧力的作用下向远离安装件621的方向移动,转柄627
复位将锁定销625挡住,并保持在此位置,使锁定销625无法z向向下运动,使支撑层2相对于运输底框层1不能浮动,并保持在此锁定状态。当需要解除锁定时,手动按压转柄627,使转柄627向贴合安装件621的方向移动,使转柄627让开锁定销625,锁定销625在拉伸弹簧630的拉伸力的作用下z向向下运动,脱离锁定套61,解除锁定,支撑层2可相对于运输底框层1浮动。拧紧作业时,尤其是大扭矩作业时,拧紧枪提供的扭矩会使车辆车身连带支撑支撑层2相对运输底框层1转动,造成扭矩损失,严重会损伤设备与车辆零部件。作为示例,本发明中配置2套浮动锁定机构6,2套浮动锁定机构6关于运输底框层1的x轴中心线对称布置,拧紧作业时同时使用,有效地防止支撑层2相对运输底框层1转动,从而避免了托盘系统及车辆零部件的损坏。
68.进一步,参见图2,本实施例中的合装托盘3包括相互独立的前托盘31、中托盘32和后托盘33。支撑层2上设置有定位销支撑和平板支撑,前托盘31、中托盘32和后托盘33分别通过定位销支撑8和平板支撑7连接于支撑层2。为保证支撑强度及定位需求,每个托盘至少配置2个定位销支撑8和一个平板支撑7。作为示例,本发明中,前托盘31配备有2个定位销支撑8和2个平板支撑7,中托盘32配备有2个定位销支撑8和2个平板支撑7,后托盘33配备有2个定位销支撑8和4个平板支撑7。其中,2个定位销支撑7用于x向和y向固定各托盘,防止托盘移动。各托盘依靠自身重力贴合在平板支撑7的上表面,以限制各托盘z向向下运动,但z向向上没有限制,前托盘31、中托盘32和后托盘33可在z向外力作用下轻松离开支撑层2。对于其它同种类托盘,在保证定位孔间距尺寸一致的情况下,也可以放置于支撑层2上,即支撑层2上的托盘都可随意切换,可根据不同汽车型号更换不同的托盘,更换时可任意更换其中一种或几种托盘,满足了不同车型的生产需求,提高了合装托盘3系统的标准化程度。
69.上述为本发明的整体浮动合装托盘3系统的具体机械结构,采用本发明的合装托盘3系统将车辆车身与底盘总成进行合装的过程:首先将不同的底盘模块预先安装在前托盘31、中托盘32和后托盘33上。通过吊具将预装有底盘模块的前托盘31、中托盘32和后托盘33分别安装在支撑层2的对应位置。进入合装工位前,确认支撑层2相对于运输底框层1处于中位,2套浮动锁定机构6均处于解锁状态,即支撑层2相对于运输底框层1可浮动。通过吊具将车辆车身吊至预装有底盘模块的合装托盘系统上方,通过调节支撑层2以消除车辆车身与底盘总成的错位,支撑层2偏离中位,使合装托盘3定位销顺利插入车身定位孔。随后撤去外力,支撑层2在自动对中机构5的作用下复位至中位,外力调节浮动锁定机构6将支撑层2锁定,使支撑层2相对于运输底框层1不可运动,进行拧紧作业,以完成底盘总成与车辆车身的合装。合装完成后进入分离工位,在分离前,外力调节浮动锁定机构6将支撑层2解除锁定,即支撑层2相对于运输底框层1浮动进行分离,此为一次车辆装配循环,本发明中施加在支撑层2和浮动锁定机构6上的外力可以由合装工位的设备提供,例如气缸等。合装时无需调节其它零部件的装配尺寸,仅通过调节支撑层2即可消除错位,大大提高了车辆车身与底盘总成的合装效率,且错位可完全消除,进而避免了由于错位导致合装托盘3、合装设备或车辆零部件将会受到较大侧向力,使合装托盘3、设备或车辆零部件受损。
70.以上所述,仅为本发明的较佳的具体实施方式,但本发明的保护范围并不局限于此,任何熟悉本技术领域的技术人员在本发明揭露的技术范围内,根据本发明的技术方案及其发明构思加以等同替换或改变,都涵盖在本发明的保护范围内。