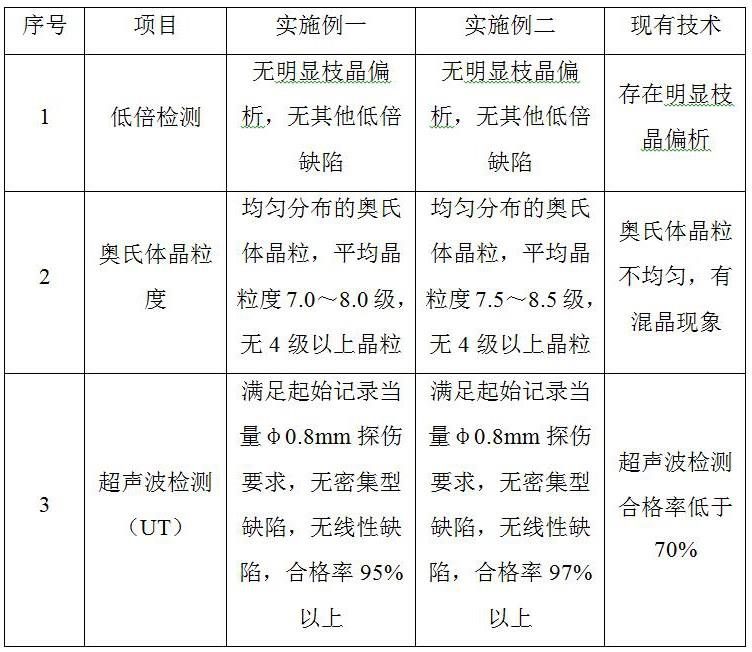
1.本发明涉及锻件加工技术领域,涉及一种行星轮锻件用原材料及行星轮加工方法,具体涉及一种风电增速箱行星轮锻件用原材料及风电增速箱行星轮碾环成形的加工方法。
背景技术:2.由于具有结构紧凑,体积小、传动效率高和传动比大等优点,行星齿轮传动广泛的应用在风力发电机传动系统、航空动力传动系统、车辆传动系统等领域。
3.行星轮作为行星齿轮传动的重要部件,特别是作为双馈式风力发电机组核心部件的增速箱,其服役条件恶劣,技术要求高,要求使用寿命长。因此,一般选用低碳高合金的cr
‑
ni
‑
mo系渗碳钢进行制作,这种材质的锻件要保证其渗碳淬火后的力学性能满足使用要求,必须对行星轮锻件用材料、锻造成形过程提出严格的技术要求和验收标准,以确保行星成品的质量可以完全满足风力发电机的服役要求。
4.但是,随着风力发电机组日益大型化的发展,其增速箱用行星轮锻件需要有一整套完整的锻造成形技术、热处理技术和检测验收手段,对其内部质量提供保障。
5.为此,我们在国内陆上和海上风力发电机组快速发展的今天,提出了一整套可以快速、高效完成风力发电机增速箱行星轮锻件制作的方法,确保国内行星轮锻件可以快速实现完全替代进口的局面。
技术实现要素:6.针对现有技术的不足,本发明提供一种行星轮锻件用原材料及行星轮加工方法,可以获得少无枝晶偏析、奥氏体晶粒均匀细小、超声波检测(ut)满足起始记录当量φ0.8mm的探伤要求的行星轮。
7.本发明是通过如下技术方案实现的:提供一种加工风电增速箱行星轮锻件用原材料,包括连铸圆坯或精炼钢锭,其包括以下重量份数(%wt)组分:0.15~0.21c,0.20~0.40si,0.50~0.80mn,≤0.010p,≤0.005s,1.50~1.80cr,1.50~1.80ni,0.20~0.35mo,0.020~0.040al,0.020~0.040nb,≤0.003ti,≤0.20cu,≤0.001ca,≤0.15v,≤0.010pb,≤0.010sn,≤0.010sb,≤0.010bi,≤0.015as且pb+sn+sb+bi+as≤0.035,[o]≤15ppm,n:60~120ppm,[h]≤1.5ppm,其余为fe和其他残余元素。
[0008]
一种使用行星轮锻件用原材料的行星轮加工方法,包括以下步骤:a、使用原材料下料;b、镦拔变料:包括镦粗和拔长,其中:每次镦粗或拔长时的锻造比,不小于2:1,且不大于2.5:1;镦粗和拔长过程总锻造比,只计算镦粗比或拔长比;镦粗或拔长比不小于6:1;c、镦粗、冲孔、扩孔:将镦拔后的坯料回炉加热,保温后将料坯镦粗至需求高度,实
施冲孔和扩孔;d、成形:将扩孔后的锻坯回炉加热,保温后经辗环机环轧成形或油压机、电液锤扩孔成形,完成后将行星轮锻件缓冷至少24h;e、正火+回火处理:具体步骤包括:e1、将行星轮锻件装入炉温不超过350℃的热处理炉内,保持各件之间间距不小于100mm,以≤120℃/h的速度升温至650℃
±
10℃,并保温1h~3h;e2、保温结束后,以全功率快速升温至930℃~950℃,并按照行星轮有效厚度,依据15mm/h~25mm/h实施保温;e3、保温结束后,出炉,实施冷却;e4、待行星轮表面冷却至350℃左右时,装入炉温不超过300℃的热处理炉内实施回火;e5、保温结束后,出炉空冷至室温。
[0009]
进一步的,在步骤a中:根据要求选择原材料种类,可以是连铸圆坯,可以是精炼钢锭。
[0010]
其中,选用连铸圆坯进行行星轮锻件制作的,可以直接将选择好的连铸圆坯锯切下料即可;选用3.5t及以下精炼钢锭进行行星轮锻件制作的,可以直接将选择好的精炼钢锭锯切下料,精炼钢锭的冒口端去除量不少于15%,水口端去除量不少于5%;选用3.5t以上精炼钢锭进行行星轮锻件制作的,应先进行钢锭开坯,即将钢锭按照设置的方案实施加热,出炉后对钢锭实施镦粗和拔长变形,保证镦粗和拔长锻比不小于3:1,且拔长后的坯料截面满足行星锻件锻造要求。开坯完成的坯料,应趁热放入沙坑或温度不超过680℃的加热炉内,实施缓冷;缓冷结束后的坯料,按照设计好的方案实施锯切下料,其中,对于10t及以下规格的精炼钢锭开坯料,冒口端去除量不少于15%,水口端去除量不少于5%;对于10t以上精炼钢锭,其开坯料冒口端去除量不少于18%,水口端去除量不少于7%。
[0011]
进一步的,在步骤b中,对于下料重量在1200kg及以下的行星轮锻件,选取8t~15t电液锤实施镦拔变料;对于下料重量大于1200kg,不超过2000kg的行星轮锻件,选取2000t~4000t油压机实施镦拔变料;对于下料重量大于2000kg的行星轮锻件,选取4000t及以上的油压机实施镦拔变料;进一步的,在步骤c中,对于下料重量在1200kg以上的行星轮锻件,选取8t~15t电液锤实施镦粗、冲孔;进一步的,在步骤c中,在第一个料坯冲孔回炉后,立即将加热炉的温度下调30℃~50℃。
[0012]
进一步的,在步骤d中,对于下料重量在1200kg及以下的行星轮锻件,选取辗环机环轧成形或8t~15t电液锤扩孔成形;对于下料重量在1200kg以上的行星轮锻件,选取辗环机环轧成形或2000t以上油压机扩孔成形。
[0013]
进一步的,在步骤e的e4中,回火时,以≤80℃/h的速度升温至650℃~690℃,并按
照行星轮有效厚度,依据10mm/h~20mm/h实施保温。
[0014]
进一步的,在步骤e的e3中,冷却时,依据行星轮锻件尺寸和壁厚,选择冷却方式:对于行星轮锻件高度在300mm及以下,高度与壁厚比值大于1.50的,选择空冷;对于行星轮锻件高度在300mm以上,高度与壁厚比值不超过1.50的,选择风冷。
[0015]
进一步的,在步骤e和步骤f之间还设置有取样检测:低倍检测不允许有明显的枝晶偏析缺陷;检测行星轮锻件的奥氏体晶粒度满足n≥6;带状组织评级满足≤2级;显微组织为均匀的正火回火组织、不允许存在魏氏体组织;以及成品光谱化学成分、表面硬度、端淬特性、非金属夹杂物含量等其他理化特性的检测,确保满足技术要求。
[0016]
进一步的,还包括:f、车削加工,车削加工包括粗车和精车,粗车时对正火+回火处理结束的行星轮锻件,确保各部粗车度满足ra3.2μm~ra6.3μm。
[0017]
本发明的有益效果:通过本发明制作的行星轮锻件,其本体表面少无枝晶偏析,锻件内部奥氏体晶粒均匀细小,超声波检测(ut)满足起始记录当量φ0.8mm的探伤要求。
[0018]
晶粒度的大小,反映着钢中奥氏体晶粒的粗细程度,奥氏体晶粒越细小,经渗碳淬火回火处理后的齿轮产品强度越高,塑韧性越好,抗冲击脆断性能越高。锻件晶粒度细化,主要源于锻造过程保证锻件充分锻透,确保充分打碎材料内部粗大的原始奥氏体晶粒,打碎材料在冶金冷却过程中形成的粗大树枝晶。同时,在锻件成形阶段,由于锻比较小,锻造变形较小,采取较低的加热温度,有助于反复镦拔变形过程中形成的较细奥氏体晶粒不易长大和粗化,对确保锻件最终形成均匀分布的细小奥氏体晶粒具有重要作用。
[0019]
锻后的缓冷和随后的正火+回火处理,对锻造过程中形成的组织有进一步细化作用,同时有效去除锻造过程中产生的内应力,让齿轮内部的组织和晶粒更加均匀。正火后的冷却方式,随着锻件壁厚的不同,采取不同的冷却方式,有利于避免锻件因质量效应产生的冷却差异,对于保证锻件满足超声波检测(ut)要求有重要作用。
[0020]
说明书附图图1为本发明加工行星轮与现有技术行星轮性能检测结果对比表;图2为本发明中实施例一的行星轮锻件本体试样在950℃
×
8h出炉水冷后的奥氏体晶粒度示意图;图3为本发明中实施例二的行星轮锻件本体的低倍检测结果示意图;图4为本发明中实施例二的行星轮锻件本体正火回火态奥氏体晶粒示意图;图5为本发明中实施例二的行星轮锻件本体试样在950℃
×
8h出炉水冷后的奥氏体晶粒度示意图。
具体实施方式
[0021]
为能清楚说明本方案的技术特点,下面通过具体实施方式,对本方案进行阐述。
[0022]
实施例一:本实施例提供一种尺寸为:外径φ615mm,内径φ300mm,高度为245mm的行星轮锻
件的加工方法。
[0023]
首先:(1)根据产品尺寸、形状及重量,进行工艺设计;(2)根据设计方案,选择直径为φ390mm的连铸圆坯原材料,进行复验,其化学成分满足(%wt):0.19c,0.28si,0.68mn,0.010p,0.003s,1.60cr,1.58ni,0.29mo,0.026al,0.020nb,0.002ti,0.015cu,0.0003ca,0.005v,0.0002pb,0.0010sn,0.0003sb,0.0002bi,0.0020as,[o]=8ppm,n:65ppm,[h]=0.8ppm,其余为fe和其他残余元素。
[0024]
风电增速箱行星轮辗环成形的加工方法具体操作步骤如下:a、依据原材料规格和重量,进行下料。
[0025]
b、镦拔变料:将锯切的坯料实施加热,并在1200℃
±
20℃,按照0.7mm/min实施保温,将8件坯料实施加热后,保温3.5h,出炉后采用8t电液锤,依据镦粗和拔长参数,对料坯实施镦粗和拔长,其中:拔长:将加热好的坯料变方,拔长至高度620mm
±
10mm;镦粗:将拔长后的坯料镦粗至高度300mm
±
10mm;拔长:将镦粗后的坯料拔长至高度620mm
±
10mm;镦粗:将拔长后的坯料镦粗至高度300mm
±
10mm;拔长:将镦粗后的坯料拔长,并滚圆至直径φ350mm
±
10mm,高度580mm
±
10mm,回炉;料坯拔长比为6.41:1。
[0026]
c、成形:将镦拔后的坯料回炉,按照预定规范实施加热,并保温1.0h,出炉后将料坯采用8t电液锤,镦粗至高度255mm
±
10mm,选用φ180mm冲头对其实施冲孔,并扩孔至内孔为φ210mm。同时,在第一个料坯冲孔回炉后,立即将加热炉的温度下调至1180℃。
[0027]
d、辗环:将扩孔后的锻坯回炉加热,保温0.5h,出炉后经卧式辗环机环轧成形即可。辗环完成后,将行星轮锻件放入炉温≤700℃的锻造加热炉内,缓冷24h。
[0028]
e、正火+回火处理:待辗环成形的行星轮锻件冷却至室温后,测量各部尺寸,确保各部尺寸满足技术要求之后,将行星轮锻件装入热处理炉内按照正火工艺实施正火+回火处理,具体步骤包括:e1、将行星轮锻件装入炉温不超过350℃的热处理炉内,保持各件之间间距不小于100mm;以≤120℃/h的速度升温至650℃
±
10℃,并保温2h;e2、保温结束后,以全功率快速升温至940℃
±
10℃,并按照行星轮有效厚度,依据20mm/h实施保温;e3、保温结束后,出炉,对工件实施空冷;e4、待行星轮表面空冷至350℃左右时,装入炉温不超过300℃的热处理炉内实施回火;回火时,以≤80℃/h的速度升温至680℃
±
10℃,并按照行星轮有效厚度,依据15mm/h实施保温;e4、保温结束后,出炉空冷至室温;取样检测:如图1所示,正火回火完成的行星轮本体取样检测,其950℃
×
8h出炉水
冷后的奥氏体晶粒评级为n=8.9,带状组织评级为1.0级,显微组织为均匀的正火回火组织,未发现魏氏体组织,表面硬度为160
‑
180hb,成品光谱化学成分、端淬特性、非金属夹杂物检测结果均满足技术要求。
[0029]
粗车:对正火+回火处理结束的行星轮锻件,依据粗车图纸进行粗车,确保各部粗车度满足ra3.2μm~ra6.3μm。
[0030]
无损检测:依据要求,对粗车完成的行星轮锻件实施无损检测,要求:行星轮内部缺陷水平满足φ0.6mm起始记录当量的探伤要求,内部无当量在φ0.6mm及以上的点状缺陷,未发现线性缺陷和密集性缺陷,满足技术要求。
[0031]
精车:依据精车图纸对行星轮锻件实施精车,确保各部尺寸及表面质量满足加工要求。
[0032]
终检:依据成品图纸,按照技术要求,对行星轮实施终检,确保其表面质量、内部质量、各部尺寸等均可以满足技术要求。
[0033]
实施例二:本实施例提供一种尺寸为:外径φ800mm,内径φ470mm,高度为600mm的行星轮锻件的加工方法。
[0034]
首先:(1)根据产品尺寸、形状及重量,进行工艺设计;(2)根据设计要求,选择规格为10t的精炼钢锭,进行复验,其化学成分满足(%wt):0.18c,0.24si,0.68mn,0.003p,0.001s,1.65cr,1.70ni,0.29mo,0.032al,0.020nb,0.002ti,0.030cu,0.0002ca,0.015v,0.0006pb,0.0030sn,0.0003sb,0.0004bi,0.0065as,[o]=12ppm,n=100ppm,[h]=0.8ppm,其余为fe和其他残余元素。
[0035]
风电增速箱行星轮成形的加工方法具体操作步骤如下:a、依据钢锭规格和重量,进行下料,在下料前对钢锭开坯,步骤如下:a1、将选择好精炼钢锭装入加热炉内,按照设置好的加热方案实施加热和保温,出炉后对精炼钢锭实施镦粗和拔长,在开坯过程中,当坯料表面温度低于800℃时,将坯料回炉加热,并保温1h~2h,出炉后继续实施锻造,确保坯料截面为(500mm
±
10mm)
×
(500mm
±
10mm)。
[0036]
a2、将开坯完成的坯料放入炉温不高于680℃的加热炉内,实施缓冷;a3、缓冷结束后,开始锯切下料,冒口去除量控制在16%左右,水口端去除量控制在6%左右,锭身坯料按照策划的方案分别锯切下料,同时,在冒口端锯切低倍试片;a4、检测:对冒口端的低倍试片实施检测,确保低倍检测结果满足技术要求,且无明显严重的枝晶偏析,冒口端化学成分、气体含量满足技术要求。
[0037]
b、镦拔变料:将锯切的坯料实施加热,并在1200℃
±
20℃,按照0.7mm/min实施保温,将8件坯料实施加热后,保温6.0h,出炉后采用2000t油压机,依据镦粗和拔长参数,对料坯实施镦粗和拔长,其中:拔长:将加热好的坯料变方,拔长至高度950mm
±
10mm;镦粗:将拔长后的坯料镦粗至高度480mm
±
10mm;拔长:将镦粗后的坯料拔长至高度950mm
±
10mm;
镦粗:将拔长后的坯料镦粗至高度480mm
±
10mm;拔长:将镦粗后的坯料拔长,并滚圆至直径φ470mm
±
10mm,高度1100mm
±
10mm,回炉;料坯拔长比为6.20:1。
[0038]
c、镦粗、冲孔、扩孔:将镦拔后的坯料回炉,按照预定规范实施加热,并保温1.0h~3.0h,出炉后将料坯采用8t电液锤,镦粗至高度590mm
±
10mm,选用φ180mm冲头对其实施冲孔,并扩孔至内孔为φ240mm。同时,在第一个料坯冲孔回炉后,立即将加热炉的温度下调至1170℃。
[0039]
d、成形:将扩孔后的锻坯回炉加热,保温0.5h~1.0h,出炉后经2000t油压机扩孔成形即可。成形完成后,将行星轮锻件放入炉温≤700℃的锻造加热炉内,缓冷24h。
[0040]
e、正火+回火处理:待成形的行星轮锻件冷却至室温后,测量各部尺寸,确保各部尺寸满足技术要求之后,将行星轮锻件装入热处理炉内按照正火工艺实施正火+回火处理,具体步骤包括:e1、将行星轮锻件装入炉温不超过350℃的热处理炉内,保持各件之间间距不小于100mm;以≤120℃/h的速度升温至650℃
±
10℃,并保温2h;e2、保温结束后,以全功率快速升温至940℃
±
10℃,并按照行星轮有效厚度,依据20mm/h实施保温;e3、保温结束后,出炉,对工件实施风冷;e4、待行星轮表面风冷至350℃左右时,装入炉温不超过300℃的热处理炉内实施回火;回火时,以≤80℃/h的速度升温至680℃
±
10℃,并按照行星轮有效厚度,依据15mm/h实施保温;e4、保温结束后,出炉空冷至室温;取样检测:如图2所示,正火回火完成的行星轮本体取样检测,其表面低倍检测未发现枝晶偏析;如图3所示,正火回火态奥氏体晶粒度评级n=10.3级;如图4所示,950℃
×
8h出炉水冷后的奥氏体晶粒评级为n=8.0级带状组织评级为1.0级,显微组织为均匀的正火回火组织,未发现魏氏体组织,表面硬度为160
‑
180hb,成品光谱化学成分、端淬特性、非金属夹杂物检测结果均满足技术要求。
[0041]
粗车:对正火+回火处理结束的行星轮锻件,依据粗车图纸进行粗车,确保各部粗车度满足ra3.2μm~ra6.3μm。
[0042]
无损检测:依据要求,对粗车完成的行星轮锻件实施无损检测,要求:行星轮内部缺陷水平满足φ0.6mm起始记录当量的探伤要求,内部无当量在φ0.6mm及以上的点状缺陷,未发现线性缺陷和密集性缺陷,满足技术要求。
[0043]
精车:依据精车图纸对行星轮锻件实施精车,确保各部尺寸及表面质量满足加工要求。
[0044]
终检:依据成品图纸,按照技术要求,对行星轮实施终检,确保其表面质量、内部质量、各部尺寸等均可以满足技术要求。
[0045]
针对本发明实施例制得的行星轮与现有技术行星轮性能检测结果如图1所示。与现有锻造和热处理技术制作的行星轮锻件相比,采用本发明制作的行星轮锻件,其表面少无枝晶偏析、内部奥氏体晶粒均匀细小、内部缺陷水平满足起始记录当量为φ0.8mm的超声
波探伤要求,不存在密集型缺陷,不存在任何线性缺陷。
[0046]
当然,上述说明也并不仅限于上述举例,本发明未经描述的技术特征可以通过或采用现有技术实现,在此不再赘述;以上实施例仅用于说明本发明的技术方案并非是对本发明的限制,参照优选的实施方式对本发明进行了详细说明,本领域的普通技术人员应当理解,本技术领域的普通技术人员在本发明的实质范围内所做出的变化、改型、添加或替换都不脱离本发明的宗旨,也应属于本发明的权利要求保护范围。