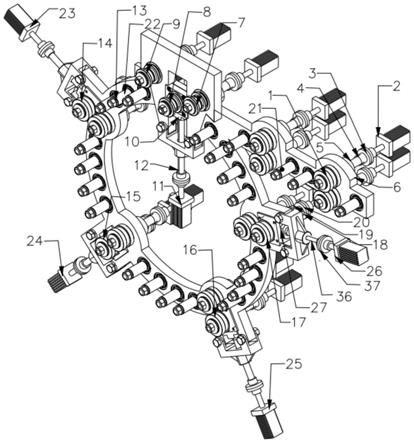
1.本发明属于金属成形技术领域,具体涉及一种环形扁平管一体化成形装置及工艺。
背景技术:2.环形扁平管是一种重要的航天工业零部件,在运载火箭的分离装置中起着重要的作用;同时,在翅片扁平管换热器中,环形扁平管作为最终的换热执行部件必不可少。目前市场上有些换热器采用换热效果差的圆管作为换热装置,其原因在于环形扁平管在生产过程中存在制造难度大、制造过程繁琐、制造效率低、生产设备所需空间大等问题。
3.现有环形扁平管的加工工艺主要有:多道次辊轧成形,其成形轧辊为直线形排布,生产设备所占空间较大;拉拔成形也同样存在生产设备所占空间较大的问题;申请号为201310746574.9的中国专利公开了一种扁平管热压成形的制造方法,此方法加工工艺较为复杂;且上述成形工艺仅可加工截面,无法生产带有弧度的扁平管。
技术实现要素:4.为了克服上述现有技术的缺点,本发明的目的在于提供了一种环形扁平管一体化成形的装置及工艺,能把加工扁平截面与辊弯成环的功能集合,减小所占的空间,具有装夹次数少,机械结构简单,生产效率高,生产成本低等优点。
5.为了达到上述目的,本发明采取的技术方案为:
6.一种环形扁平管一体化成形的装置,包括截面预成型系统、辊弯系统、多道次的辊轧压平成形辊、道次间导引装置,截面预成型系统的输出和辊弯系统输入配合,辊弯系统输出依次排布有多道次的辊轧压平成形辊,多道次的辊轧压平成形辊间分布有用于引导工件运动的道次间导引装置。
7.所述的截面预成型系统包括m对预成形辊,m取值范围为2
‑
4;m对预成形辊1之间设有第一导向辊21,第一导向辊21安装在机架6上;每一个预成形辊1被第一伺服电机2驱动,第一伺服电机2的转子通过第一联轴器3与第一阶梯轴4连接,第一阶梯轴4上通过轴承安装有第一套筒5,第一套筒5装在机架6上;第一阶梯轴4端头连接预成形辊1,预成形辊1的工作表面为圆柱面。
8.所述的辊弯系统包括有动力源的第一固定轧辊7、第二固定轧辊9和一个无动力源的随动轧辊8形成的垂直下调式三辊辊弯装置,随动轧辊8由第二伺服电机11控制径向运动;随动轧辊8安装在第一导向块10上,第一导向块10两侧与机架6过渡配合,第一导向块10通过第一连杆12和第二伺服电机11输出轴连接;第二伺服电机11带动第一连杆12旋转,进而带动第一导向块10作直线运动,从而微调第一固定轧辊7、第二固定轧辊9、随动轧辊8之间公切线的弧度,进而调节辊弯后工件的弧度。
9.所述的多道次的辊轧压平成形辊包括n对的成形轧辊,其相互间夹角为依次
排布于辊弯系统之后;多道次成形轧辊的对称面连心线上工作面距离随截面形状变化,其中前n
‑
1对成形轧辊工作面为圆柱面,最终第n对成形轧辊工作面与扁平管外表面一致;n对的成形轧辊装配关系与最终成形轧辊17相同,最终成形轧辊17装在第二阶梯轴18上,第二阶梯轴18中间通过轴承连接第二套筒19,第二套筒19装配在机架6上;第二阶梯轴18的另外一端通过第二联轴器20和第三伺服电机38连接;第二阶梯轴18装配在第二导向块27上,第二导向块27装配在机架6上;第二导向块27的一端装有带螺纹的第二连杆36,第二连杆36另一端通过第三联轴器37和第四伺服电机26连接,第四伺服电机26带动第二连杆36旋转,通过螺纹副把第二连杆36的旋转运动转化为与之相连的第二导向块27的直线运动,从而调节成形轧辊对的中心距。
10.所述的道次间导引装置13包括第三阶梯轴28,第三阶梯轴28通过与轴承29配合连接在机架6上,第三阶梯轴28一端通过第一挡圈30与螺母31固定装在机架6上,第三阶梯轴28的另一端装有阶梯状套筒22,阶梯状套筒22两端分别通过第三阶梯轴28的轴肩和第二挡圈32定位,道次间导引装置13均匀地分布在机架6的圆周上。
11.利用一种环形扁平管一体化成形装置的工艺,包括以下步骤:
12.1)下料,待加工金属圆管的长度l=πr2,其中r为最终工件的几何中性层半径;
13.2)金属管预成型,定长度金属圆管通过m对预成形辊1,其圆形截面初步变形为容易辊弯成环形的扁平截面;
14.3)扁平金属管辊弯,预成型的金属管通过辊弯系统,其中第一固定轧辊7、第二固定轧辊9顺时针旋转,随动轧辊8逆时针旋转,金属管通过第一固定轧辊7、随动轧辊8与第二固定轧辊9,利用垂直下调式三辊辊弯装置把金属管加工成带有弧度的扁平管;
15.4)开始截面加工,辊弯后的弧形扁平管经过辊弯成形轧辊与第一道次的截面成形轧辊间的导引装置进入第一道次成形轧辊,规定扁平管扁平截面存在大径与小径,大径为扁平截面对称轴中较长的对称线,大径大于原圆截面直径;小径为扁平截面对称轴中较短的对称线;经过第一道次截面成形辊轧后扁平截面小径减小;
16.5)截面加工,上述经第一道次截面成形辊的弧形扁平管经过后续第2至n
‑
1次辊轧成形,其大径不断延长,小径均匀缩短,截面逐渐接近最终要求的扁平管截面;
17.6)扁平管截面最终成形,上述经多道次截面成形辊的弧形扁平管通过导引装置进入第n道次成形轧辊,第n道次成型辊的工作表面与成品零件扁平截面相同,经过多道次截面成形辊轧后金属管截面被辊成最终要求的扁平管截面;
18.7)工件定形,调节前n
‑
1对成形轧辊的中心距至成形轧辊工作表面的法向距离与扁平管小径相同,对扁平管进行1
‑
2圈校圆;
19.8)取下工件,调大成形轧辊对的中心距,取出加工好的工件。
20.本发明的有益效果为:
21.本发明使用一台装置,进行一次安装实现了辊弯成环与扁平截面成形两个加工步骤,有效降低了环形扁平管的加工工时与加工成本。在加工过程中通过道次间的导引实现了降低工人操作难度的同时也很好的保证了扁平管的环状外形。
22.本发明把辊弯成形、扁平管截面成形的功能集成在了同一台设备上,并通过合理的环形机架空间布局进一步降低了设备所占空间,为工厂节省了场地成本;本发明采用了分散多动力技术,有效简化了加工装置的机械复杂度,降低了机械零部件的设计与计算难
度。
附图说明
23.图1为本发明结构示意图。
24.图2为本发明辊弯系统结构示意图。
25.图3为本发明最终成形辊装配关系剖视图。
26.图4为本发明最终成形轧辊工作示意图。
27.图5为本发明扁平管外形及截面示意图。
28.图6为本发明道次间导引装置各零件装配示意图。
具体实施方式
29.下面结合附图和实施例对本发明做详细描述。
30.参照图1,一种环形扁平管一体化成形的装置,包括截面预成型系统、辊弯系统、多道次的辊轧压平成形辊、道次间导引装置,截面预成型系统的输出和辊弯系统输入配合,辊弯系统输出依次排布有多道次的辊轧压平成形辊,多道次的辊轧压平成形辊间分布有用于引导工件运动的道次间导引装置。
31.参照图1,为保证待加工工件水平进入辊弯系统,并考虑结构平衡性,所述的截面预成型系统包括两对预成形辊1,两对预成形辊1之间设有第一导向辊21,第一导向辊21安装在机架6上;每一个预成形辊1被第一伺服电机2驱动,第一伺服电机2的转子通过第一联轴器3与第一阶梯轴4连接,第一阶梯轴4上装有一对轴承,轴承外圈与第一套筒5配合,第一套筒5装在机架6上;第一阶梯轴4端头通过键连接预成形辊1,预成形辊1一端由第一阶梯轴4的轴肩定位,预成形辊1另一端用挡圈定位,预成形辊1的工作表面为圆柱面,其作用为把圆管初步加工成更易辊弯成环形的扁平管。
32.参照图1、图2,所述的辊弯系统包括有动力源的第一固定轧辊7、第二固定轧辊9和一个无动力源的随动轧辊8形成的垂直下调式三辊辊弯装置,随动轧辊8由第二伺服电机11控制径向运动,随动轧辊8安装在第一导向块10上,第一导向块10两侧与机架6过渡配合,第一导向块10一端安装有驱动第一导向块10的第二伺服电机11,第二伺服电机11与第一导向块10间的第一连杆12上加工有外螺纹,第一连杆12与机架6间存在螺纹副;在收到控制信号后时,第二伺服电机11带动第一连杆12旋转,通过螺纹副把第一连杆12的旋转运动转化为与之相连的第一导向块10的直线运动,从而微调第一固定轧辊7、第二固定轧辊9、随动轧辊8之间公切线的弧度,进而调节辊弯后工件的弧度。
33.参照图1、图3、图4、图5,所述的多道次的辊轧压平成形辊包括4对的成形轧辊,第一成形轧辊14、第二成形轧辊15、第三成形轧辊16、最终成形轧辊17相互间夹角为72
°
,依次排布于辊弯系统之后,成形轧辊的截面相同,其中心距随截面形状均匀变化,其中第一成形轧辊14、第二成形轧辊15、第三成形轧辊16工作面为圆柱面,最终成形轧辊17由上辊17a与下辊17b组成,工作面与扁平管35外表面一致,目标工件扁平管35的整体外形35a与截面形状35b如图5所示。
34.参照图1、图3,4对的成形轧辊装配关系与最终成形轧辊17相同,最终成形轧辊17装在第二阶梯轴18上,一端由第三挡圈33定位并用螺母34拧紧,另外一端使用第二阶梯轴
18的轴肩定位;第二阶梯轴18中间装配有两个轴承,轴承外圈装配在第二套筒19里,第二套筒19装配在机架6上;第二阶梯轴18的另外一端通过第二联轴器20和第三伺服电机38连接;第二阶梯轴18装配在第二导向块27上,第二导向块27装配在机架6上,第二导向块27的一端装有带螺纹的第二连杆36,第二连杆36另一端通过第三联轴器37和第四伺服电机26连接,第四伺服电机26带动第二连杆36旋转,通过螺纹副把第二连杆36的旋转运动转化为与之相连的第二导向块27的直线运动,从而调节成形轧辊对的中心距。
35.参照图1、图6,所述的道次间导引装置13包括第三阶梯轴28,第三阶梯轴28通过与轴承29配合连接在机架6上,第三阶梯轴28一端通过第一挡圈30与螺母31固定装在机架6上,第三阶梯轴28的另一端装有阶梯状套筒22,阶梯状套筒22两端分别通过第三阶梯轴28的轴肩和第二挡圈32定位,道次间导引装置13均匀地分布在机架6的圆周上。
36.利用一种环形扁平管一体化成形装置的工艺,包括以下步骤:
37.1)下料,待加工金属圆管的长度l=πr2,其中r为最终工件的几何中性层半径;
38.2)金属管预成型,参照图1,定长度金属圆管通过两对预成形辊,其圆形截面初步变形为容易辊弯成环形的扁平截面;
39.3)扁平金属管辊弯,预成型的金属管通过辊弯系统,参照图2,第一固定轧辊7、第二固定轧辊9顺时针旋转,随动轧辊8逆时针旋转,金属管通过第一固定轧辊7、随动轧辊8与第二固定轧辊9,利用垂直下调式三辊辊弯装置把金属管加工成带有弧度的扁平管;
40.4)开始截面加工,辊弯后的弧形扁平管经过辊弯成形轧辊与第一道次的截面成形轧辊间的导引装置进入第一道次成形轧辊,参照图6,规定扁平管扁平截面存在大径与小径,大径为扁平截面对称轴中较长的对称线,大径大于原圆截面直径;小径为扁平截面对称轴中较短的对称线;经过第一道次截面成形辊轧后扁平截面小径减小;
41.5)截面加工,上述经第一道次截面成形辊的弧形扁平管经过后续2次辊轧成形,其大径不断延长,小径均匀缩短,截面逐渐接近最终要求的扁平管截面;
42.6)扁平管截面最终成形,上述经多道次截面成形辊的弧形扁平管通过导引装置进入第4道次成形轧辊,第4道次成型辊的工作表面与成品零件扁平截面相同,参照图5,经过多道次截面成形辊轧后金属管截面被辊成最终要求的扁平管截面35b;
43.7)工件定形,参照图1,控制第五伺服电机23、第六伺服电机24、第七伺服电机25调节前3对成形轧辊的中心距至成形轧辊工作表面的法向距离与扁平管小径相同,对扁平管进行2圈校圆。参照图5,经过2圈校圆后金属管外形被辊弯成最终要求的扁平管外形35a;
44.8)取下工件,控制第五伺服电机23、第六伺服电机24、第七伺服电机25、第四伺服电机26调大成形轧辊对的中心距,取出加工好的工件。