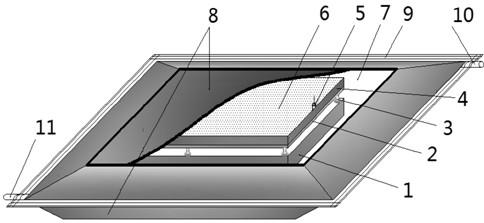
1.本发明涉及爆炸焊接领域技术领域,具体涉及一种氖气保护新型爆炸焊接方法及爆炸焊接结构。
背景技术:2.爆炸焊接的能量来源于低爆速炸药,利用炸药爆炸产生的爆炸产物急速膨胀,驱动复板向下高速运动,直到与基板产生斜碰撞。同时金属本体在高压、大变形、高速绝热变形和高压压缩所产生高温的共同作用下,使得射流后部的金属产生固相扩散和熔化焊合。
3.爆炸焊接过程中不需要大型的设备,能量来源于专用的低爆速炸药,其爆速介于1800~2200m/s之间,因此也决定了爆炸焊接过程是极其迅速的,特别适合于大面积同种或异种金属板材之间的焊接。对于常规焊接方法难以焊接或者焊接不成的两种金属,如熔点差异较大,热膨胀系数差异较大的两种金属,也可以采用爆炸焊接的方式进行焊合。
4.新形势下,爆炸焊接金属复合板应用领域不断扩展,对板幅的要求也是越来越大,对其界面的结合质量要求也越来越高。对于大面积的板材的爆炸焊接,目前都是在野外进行,暴露在大气当中。采用常规的爆炸焊接工艺,在爆炸焊接过程中,待焊面产生的金属射流很容易与大气中的成分发生反应,生产氧化物、氮化物、碳化物、氢化物等脆性产物。对于复层为活泼金属的板材爆炸焊接,如钛、锆、钽、铌、铝、镁等纯金属板或其合金板等,这种现象更加明显,爆炸焊接结合界面生成的脆性产物,在机械加工过程中更容易开裂、分层或断裂,加工和使用过程中存在安全隐患。而且这些金属其爆炸焊接“窗口”小,工艺参数难以控制。
技术实现要素:5.本发明要解决的技术问题是提供一种氖气保护新型爆炸焊接方法,以解决现有技术中对于复层为活泼金属焊接过程中脆性产物含量高导致焊接工件易出现开裂、分层和断裂的技术问题。
6.为解决上述技术问题,本发明采用如下技术方案:
7.设计一种氖气保护新型爆炸焊接方法,包括如下步骤:
8.s1清理:分别将基板和复板待结合的表面清理干净;
9.s2装配:将步骤s1清理干净的基板和复板按照“基板在下,复板在上、待焊接面相对”原则进行装配,在基板和复板之间放入间隙支撑,其中基板为碳钢、不锈钢或镍基合金;复板为钛、锆、钽、铌、铝、镁的一种或几种;
10.s3布药和雷管:在复板的上表面布置药剂和雷管;
11.s4焊接密闭空间的制备:采用铝塑热熔膜将s3装配好的基板和复板密封,并形成一个密闭的空间,并在对角线位置预留抽气/
12.充气口、气体成分/压力检测口;
13.s5充入氖气:将步骤s4中的密闭空间中的空气抽出形成负压状态,再向其中充入
氖气,直到空间内完全充满氖气停止;
14.s6实施爆炸焊接:用雷管引爆药剂,实施爆炸焊接。
15.优选的,在步骤s1中,若钢板的表面清理采用80目千叶轮进行抛光处理;钛、锆、钽、铌板材的表面采用40目千叶轮进行抛光处理,并在抛光过程中,抛光设备下压强度不高于0.6mpa,防止金属表面氧化;铝、镁板材采用不锈钢钢丝轮进行处理,抛光过程中,下压强度不高于0.4mpa,防下压力不宜过大,防止金属表面氧化和表面严重划伤。
16.优选的,在步骤s2中,所述间隙支撑为圆柱形支撑,其材质为铝、铜、不锈钢或者与复板相同的材质中的任意一种,圆柱形支撑的壁厚0.2~0.5mm,外径为3~6mm,高度为4~20mm。
17.优选的,所述圆柱形支撑下部带有底座,所述底座材质与圆柱形支撑材质相同,厚度0.2~0.5mm,外径8~12mm。
18.优选的,在步骤s3中,所述药剂如下质量百分数的原料:40%~50%分散剂、5%~10%木粉或硅藻土密度调节剂、45%~55%粉状乳化炸药;其中粉状乳化炸药一种经过自敏化的油包水型爆炸性物质。
19.优选的,单位面积装药量上、下限分别为:其中:w
min
为单位面积装药量下限,kg/m2;w
max
为单位面积装药量上限,kg/m2;ρ
f
为复板密度,g/cm3;δ
f
为复板厚度,mm;σ
f
为复板屈服强度极限,mpa;h为间隙高度;mm。
20.优选的,在步骤s4中,焊接密闭空间的制备步骤为取上下两片铝塑热熔膜边部对齐,将s3装配好的基板和复板放入两铝塑热熔膜之间,采用热熔方法将两片铝塑热熔膜边部密封,热熔温度为75~150℃,每次封口长度小于300mm,并在对角线位置预留抽气/充气口、气体成分/压力检测口。
21.一种基板与复板的爆炸焊接结构,包括待焊接板材和包覆在所述待焊接板材外侧的铝塑热熔膜层;所述待焊接板材包括自下而上依次放置的基板、间隙支撑、复板,所述复板的上端面设有炸药、雷管。
22.优选的,所述复板边部设置有限位炸药的边框。
23.与现有技术相比,本发明的有益技术效果在于:
24.本发明将待爆炸焊接的基板、复板、炸药、雷管等放置在一个由铝塑热熔膜构造的密闭体系中,通入氖气,氖气是一种惰性气体,其密度与空气密度较为接近的惰性气体,在铝塑热熔膜构成的密闭空间内,通入氖气将空气完全置换出来,使得在爆炸焊接过程中,通过隔离大气,有效避免和减弱金属射流与大气组分氮、氧、二氧化碳发生反应生成与之相应的氮化物、氧化物、碳化物等脆性产物,如图3所示(其中可以明显看出,在空气中产生的脆性物质的含量远远大于采用本发明焊接方法所生成的脆性物质),有效避免由于间隙大气近乎绝热压缩产生高温而造成界面熔化,提高了界面结合质量,提高了焊接强度,降低爆炸焊接界面在外力作用下发生开裂的风险。以钛/钢爆炸焊接复合板为例,通过观察界面金相,在界面旋涡区域,氖气环境下爆炸焊接产生的脆性相,对比在常规大气环境中爆炸焊接,脆性相可脆性相减少80%以上。扩大了爆炸焊接“窗口”,降低了活性金属爆炸焊接的焊
接难度,提高了界面结合质量,提高了焊接强度。
25.本发明适用于大面积的基板、复板的焊接,大面积板材爆炸焊接过程中,由于界面压缩空气温度为:当降低初始界面大气压力和体积时,可以有效减少由于界面空气近乎绝热压缩产生的热量。在爆炸焊接过程中,基、复板间置换成氖气或者抽取大气形成负压环境,都可以有效降低结合界面的温度,避免界面熔化。
26.本发明采用的铝塑热熔膜具有强度,其中铝箔面可防止在外力作用下破损,塑料面可以采用热熔的方式进行粘合,粘合强度高,密封可靠。可通过热熔粘合的方式,根据板材的尺寸调整铝塑热熔膜的尺寸,使用便利。通过将铝塑热熔膜热封的方式构成特定的密闭空间,相对于爆炸焊接用真空容器而言,具有成本低廉、操作简单、安全性高、不受板幅和装药量限制、不受地域限制等诸多优点。具体表现在:
27.1、真空容器属于承压设备,其设计、制作和安装过程中,均在安全方面有特殊要求,受国家部门监管。设计、制作、安装、安评等环节,费用昂贵。铝塑热熔膜构成的密闭空间,不需要复杂的设计,可在空旷的野外进行,不受地域限制,不需要大型设备,每平方成本5元以内,热熔封口即可,操作简单快速;如果按1吨起爆药用量来算,制造一个真空容器,需要2000万,用铝塑热熔膜制备焊接空间仅400元;本发明采用铝塑热熔膜与普通薄膜相比,具有质量稳定性高,容易封装的特点。
28.2、真空容器为了承受大气压力,容器选材一般为刚性材料,爆炸焊接过程中,炸药爆炸产生的气体和水蒸汽迅速膨胀,因此对材料的抗疲劳性要求也高,一旦材料失效,飞散的破片对周围环境破坏力极大,因此需要定期对容器进行检测。铝塑热熔膜的方式构成特定的密闭空间,是在目前广泛采用的露天爆炸焊接的基础上改进的,铝塑热熔膜为柔性材料,炸药爆炸后消失,不会对人员和设备造成危险因素。
29.3、真空容器在设计时,空间大小固定,存在着承压极限,对爆炸焊接的板幅和装药量均有限制,而且在容器中,中厚重板的吊装、宽长板的运输,结合容器舱门的密闭问题,对于设计和施工,都具有很大的挑战。铝塑热熔膜为带状薄膜,长度不受限制,通过热熔方式增加宽度,可根据板材大小调整,不受板幅和装药量限制,质量轻,使用便捷。
30.优选的,本发明采用的药剂中粉状乳化炸药一种经过自敏化的油包水型爆炸性物质,具有一定的抗水性,空气湿度低于80%,其爆炸性能保持稳定,保证了爆炸焊接结合质量。分散剂为固体颗粒,主要作用是降低炸药爆温,阻碍爆轰波传递,降低炸药爆速,其结构紧密、不吸潮、不潮解,与粉状乳化炸药混合后稳定性好,对焊接融合度好,可降低融合温度。木粉或硅藻土密度调节剂主要作用是调节炸药密度,进而控制炸药爆速。
附图说明
31.图1为密闭空间爆炸焊接装配图;
32.图2为闭空间爆炸焊接装配剖视图。
33.图3为三种状态下爆炸焊接钛/钢复合板界面金相焊接对比图。
34.图中,1.基板;2.复板;3.间隙支撑;4.药框(纸框或木框);5.雷管;6.炸药;7.密闭空间;8.热熔铝塑薄膜;9.热熔封边部;10.抽气/充气口;11.气体成分/压力检测口。
35.注:在图3中黑色代表是脆性物质。
具体实施方式
36.下面结合附图和实施例来说明本发明的具体实施方式,但以下实施例只是用来详细说明本发明,并不以任何方式限制本发明的范围。
37.为了避免活性金属爆炸焊接界面脆性相的生产,达到提高其界面结合质量的目标,本发明通过以下具体实施方法实现:
38.实施例1:一种氖气保护新型爆炸焊接方法,包括如下步骤:
39.s1清理:分别将基板和复板待结合的表面清理干净;
40.s2装配:将步骤s1清理干净的基板和复板按照“基板在下,复板在上、待焊接面相对”原则进行装配,在基板和复板之间放入间隙支撑,其中基板为碳钢、不锈钢或镍基合金;复板为钛、锆、钽、铌、铝、镁的一种或几种;
41.s3布药和雷管:在复板的上表面布置药剂和雷管;
42.s4焊接密闭空间的制备:采用铝塑热熔膜将s3装配好的基板和复板密封,并形成一个密闭的空间,并在对角线位置预留抽气/充气口、气体成分/压力检测口;铝塑热熔膜具有强度,其中铝箔面可防止在外力作用下破损,塑料面可以采用热熔的方式进行粘合,粘合强度高,密封可靠。可通过热熔粘合的方式,根据板材的尺寸调整铝塑热熔膜的尺寸,使用便利;
43.s5充入氖气:将步骤s4中的密闭空间中的空气抽出形成负压状态,再向其中充入氖气,直到空间内完全充满氖气停止;
44.s6实施爆炸焊接:用雷管引爆药剂,实施爆炸焊接。
45.本实施例中,若钢板的表面清理采用80目千叶轮进行抛光处理;钛、锆、钽、铌板材的表面采用40目千叶轮进行抛光处理,并在抛光过程中,抛光设备下压强度不高于0.6mpa,防止金属表面氧化;铝、镁板材采用不锈钢钢丝轮进行处理,抛光过程中,下压强度不高于0.4mpa,防止金属表面氧化和表面严重划伤。
46.本实施例中,在步骤s2中,所述间隙支撑为圆柱形支撑,其材质为铝、铜、不锈钢或者与复板相同的材质中的任意一种,圆柱形支撑的壁厚0.2~0.5mm,外径为3~6mm,高度为4~20mm。
47.本实施例中,所述圆柱形支撑下部带有底座,所述底座材质与圆柱形支撑材质相同,厚度0.2~0.5mm,外径8~12mm。
48.本实施例中,所述药剂如下质量百分数的原料:40%~50%分散剂、5%~10%木粉或硅藻土密度调节剂、45%~55%粉状乳化炸药;其中粉状乳化炸药一种经过自敏化的油包水型爆炸性物质。单位面积装药剂量上、下限分别为:其中:w
min
为单位面积装药量下限,kg/m2;w
max
为单位面积装药量上限,kg/m2;ρ
f
为复板密度,g/cm3;δ
f
为复板厚度,mm;σ
f
为复板屈服强度极限,mpa;h为间隙高度;mm。
49.本实施例中,s4焊接密闭空间的制备:取上下两片铝塑热熔膜边部对齐,将s3装配好的基板和复板放入两铝塑热熔膜8之间,采用热熔方法将两片铝塑热熔膜边部具有热熔封边部9,热熔温度为75~150℃,每次封口长度小于300mm,并在对角线位置预留抽气/充气
口10、气体成分/压力检测口11,密闭空间7的真空度为
‑
0.05至
‑
0.08mpa。
50.如图1和2所示,一种基板与复板的爆炸焊接结构包括待焊接板材和包覆在所述待焊接板材外侧的铝塑热熔膜层;所述待焊接板材包括自下而上依次放置的基板1、间隙支撑3、复板2,所述复板的上端面设有炸药6、雷管5;所述复板2边部设置有限位炸药的药框4。
51.实施例2:一种氖气保护新型爆炸焊接方法,包括如下步骤:
52.s1清理:分别将基板和复板待结合的表面清理干净;
53.s2装配:将步骤s1清理干净的基板和复板按照“基板在下,复板在上、待焊接面相对”原则进行装配,在基板和复板之间放入间隙支撑,其中基板为碳钢;复板为钛、锆合金;
54.s3布药和雷管:在复板的上表面布置药剂和雷管;
55.s4焊接密闭空间的制备:采用铝塑热熔膜将s3装配好的基板和复板密封,并形成一个密闭的空间,并在对角线位置预留抽气/充气口、气体成分/压力检测口;铝塑热熔膜具有强度,其中铝箔面可防止在外力作用下破损,塑料面可以采用热熔的方式进行粘合,粘合强度高,密封可靠。可通过热熔粘合的方式,根据板材的尺寸调整铝塑热熔膜的尺寸,使用便利;
56.s5充入氖气:将步骤s4中的密闭空间中的空气抽出形成负压状态,再向其中充入氖气,直到空间内完全充满氖气停止;
57.s6实施爆炸焊接:用雷管引爆药剂,实施爆炸焊接。
58.本实施例中,若钢板的表面清理采用80目千叶轮进行抛光处理;钛、锆、钽、铌板材的表面采用40目千叶轮进行抛光处理,并在抛光过程中,抛光设备下压强度0.6mpa,防止金属表面氧化;铝、镁板材采用不锈钢钢丝轮进行处理,抛光过程中,下压强度不高于0.4mpa,防止金属表面氧化和表面严重划伤。
59.本实施例中,在步骤s2中,所述间隙支撑为圆柱形支撑,其材质为铝、铜、不锈钢或者与复板相同的材质中的任意一种,圆柱形支撑的壁厚0.35mm,外径为4mm,高度为10mm。
60.本实施例中,所述圆柱形支撑下部带有底座,所述底座材质与圆柱形支撑材质相同,厚度0.3mm,外径10mm。
61.本实施例中,所述药剂如下质量百分数的原料:45%分散剂、5%木粉或硅藻土密度调节剂、50%粉状乳化炸药;其中粉状乳化炸药一种经过自敏化的油包水型爆炸性物质。单位面积装药剂量上、下限分别为:其中:w
min
为单位面积装药量下限,kg/m2;w
max
为单位面积装药量上限,kg/m2;ρ
f
为复板密度,g/cm3;δ
f
为复板厚度,mm;σ
f
为复板屈服强度极限,mpa;h为间隙高度;mm。
62.本实施例中,s4焊接密闭空间的制备:取上下两片铝塑热熔膜边部对齐,将s3装配好的基板和复板放入两铝塑热熔膜之间,采用热熔方法将两片铝塑热熔膜边部密封,热熔温度为75~100℃,每次封口长度小于300mm,并在对角线位置预留抽气/充气口、气体成分/压力检测口,密闭空间的真空度为
‑
0.05至
‑
0.08mpa。
63.一种基板与复板的爆炸焊接结构,包括待焊接板材和包覆在所述待焊接板材外侧的铝塑热熔膜层;所述待焊接板材包括自下而上依次放置的基板、间隙支撑、复板,所述复
板的上端面设有炸药、雷管;所述复板边部设置有限位炸药的边框。
64.实施例3:一种氖气保护新型爆炸焊接方法,包括如下步骤:
65.(1)实施爆炸焊接前,需要将基、复板待结合的表面氧化皮清理干净。通常情况下,普通钢板的表面采用80目千叶轮进行抛光处理;钛、锆、钽、铌板材的表面采用40目千叶轮进行抛光处理,抛光过程中,抛光设备下压强度不高于0.6mpa,防止金属表面氧化;铝、镁板材采用不锈钢钢丝轮进行处理,抛光过程中,下压强度不高于0.4mpa,防止金属表面氧化和表面严重划伤。
66.(2)爆炸焊接密闭空间的制备:密闭空间由铝塑热熔膜构成,分为上下两片;在平整爆炸焊接用的场地后,将下层铝塑热熔膜平铺在地面上,平铺时需注意,铝膜面向下,内塑料膜向上。
67.(3)下膜平铺完成后,将基板放置于下膜中间位置,经表面处理的待焊接面向上。
68.(4)将间隙支撑均匀地摆放在基板的待焊接面及四周,间隙支撑间的间距为350mm。间隙支撑的高度,可按(5)进行理论计算及选择。间隙支撑的材质为铝、铜、不锈钢或者与复板相同的材质,壁厚0.3mm,圆柱形支撑外径为4mm,高度为12mm;圆柱形支撑下部带有底座,底座材质与圆柱形支撑材质相同,厚度0.3mm,外径10mm。
69.(5)基、复板间间隙高度的上、下限公式分别为:其中h
min
为间隙高度下限,mm;h
max
为间隙高度上限,mm;ρ
f
为复板密度,g/cm3;δ
f
为复板厚度,mm。
70.(6)放置复板,将复板经表面处理的待结合向下,与基板对齐放置于间隙支撑上,放置后观察基、复板间的间距,防止支撑倒塌。
71.(7)复板四周粘贴药框,药框可选用厚纸板或木板,厚度2~5mm,高度与所要布置的爆炸焊接炸药的高度一致。
72.(8)爆炸焊接用炸药为低爆速炸药,以粉状乳化炸药为主炸药,添加分散剂和密度调节剂,使其爆速降低至1800~2200m/s,炸药猛度≥9mm。炸药需均匀布置,整板上炸药厚度偏差不超过2mm,炸药厚度可按(9)进行理论计算及选择。
73.(9)单位面积装药量上、下限公式分别为:其中:w
min
为单位面积装药量下限,kg/m2;w
max
为单位面积装药量上限,kg/m2;ρ
f
为复板密度,g/cm3;δ
f
为复板厚度,mm;σ
f
为复板屈服强度极限,mpa;h为间隙高度;mm。
74.(10)放置雷管,放置雷管的位置可根据板幅面积进行确定,一般较小面积的板材进行爆炸焊接,其雷管放置与边部或者角部;对大面积板材的爆炸焊接,其雷管放置于板材中心位置。
75.(11)将上层铝塑热熔膜平铺在最上层,平铺时需注意,铝膜面向上,内塑料膜向下。
76.(12)铝塑热熔膜四周采用手钳式封口机对其进行热熔密封,密封时封口机温度为100℃,每次封口长度小于300mm,连续封口,避免中间间隔,必要时可以密封两道封口。最后在一个对角线位置留置抽气/充气口、气体成分/压力检测口。
77.(12)铝塑热熔膜四周采用手钳式封口机对其进行热熔密封,密封时封口机温度为100℃,每次封口长度小于300mm,连续封口,避免中间间隔,必要时可以密封两道封口。最后在一个对角线位置留置抽气/充气口、气体成分/压力检测口。
78.(13)抽取大气产生负压空间:在抽取大气制造负压环境前,需要将真空压力表装在11气体压力检测口处,随后将真空泵与10抽气口相连,启动抽取大气,待密闭空间内真空度为
‑
0.05至
‑
0.08mpa时,停止抽气。
79.(14)充入氖气气体:将氧气浓度测量仪放置在11气体成分检测口处,氖气罐与充气口相连,向其中充入高纯度氖气,直到氧气浓度测量仪数据迅速下降至5%以下,说明密闭空间内充满氖气,停止充气,并将10和11口进行密封。
80.(15)实施爆炸焊接:静置5min,其密闭空间没有变化,即可起爆雷管和炸药,实施爆炸焊接。
81.图3为采用实施例2中的焊接方法,焊接后的效果图,由图3可知,对三种状态下爆炸焊接的金属复合板结合界面进行金相分析,在电镜放大倍数为50倍情况下电镜图片如图3所示,在大气环境下进行爆炸焊接,其“旋涡区(黑色框框内)”内存在脆性化合物,在氖气保护下和真空环境下进行爆炸焊接,观察其“旋涡区”内无明显的脆性化合物,可见氖气保护下爆炸焊接效果与真空环境下效果接近,甚至一定程度上优于真空环境焊接效果。所以说采用本发明的焊接方法,可以减少脆性物质的生产量,有效避免由于间隙大气近乎绝热压缩产生高温而造成界面熔化,提高了界面结合质量,提高了焊接强度,降低爆炸焊接界面在外力作用下发生开裂的风险。
82.上面结合附图和实施例对本发明作了详细的说明,但是,所属技术领域的技术人员能够理解,在不脱离本发明宗旨的前提下,还可以对上述实施例中的各个具体参数进行变更,形成多个具体的实施例,均为本发明的常见变化范围,在此不再一一详述。