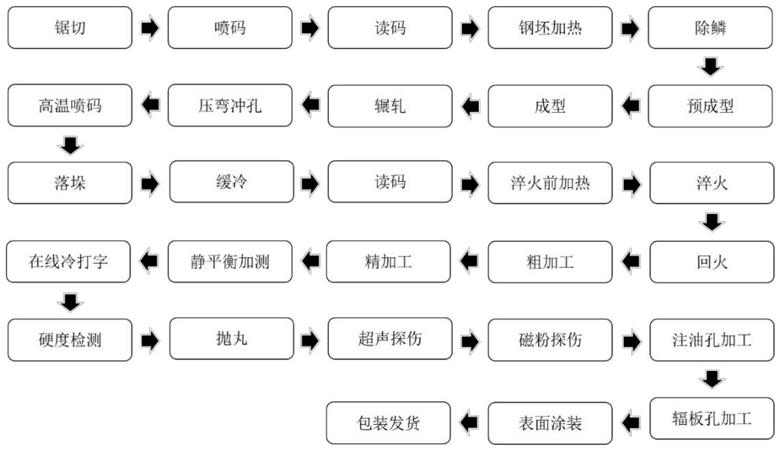
1.本发明涉及车轮技术领域,特别是涉及一种钢铝复合列车车轮一体化制造方法。
背景技术:2.近年来我国轨道车辆的高速、重载化程度不断提高,人们对环保和安全性要求的日益苛刻,进一步提高轨道车辆运行能效显得尤其重要,其中,车辆转向架系统的轻量化显得尤为关键。但是,车辆转向架系统的轻量化研究受制于材料成形技术的发展和安全的考虑,还处于相对滞后的阶段,面对车体承载结构及内饰等的轻量化技术趋于饱和,转向架系统的轻量化成为了亟待攻克的新方向,尤其是占转向架系统整体重量的30%~40%的车轮轮对的轻量化。轨道列车车轮是轨道运输工具中的重要组成部分,是轨道车辆至关重要的部件。
3.车轮支撑着整个车体的重量,因此,车轮不可能设计成带备用或保护的部件,需要具备绝对可靠性,尤其是车轮强度的设计至关重要。在强度作为基础保障的情况下,从性能优化的角度考虑,耐磨性、抗热裂能力以及抗噪/振动的能力也受到了人们的重点关注。另外,车轮是耗损件,因此其使用寿命和维护成本决定着生产成本的经济性。为了提高这些特性,目前国内外已经进行了相关研究和技术开发。目前,在高铁领域,大多数国家的列车车轮采用整体碾钢车轮,主要包括:锯切
‑
钢坯加热
‑
除磷
‑
预成型
‑
成型
‑
辗轧
‑
压弯冲孔
‑
热处理
‑
粗加工
‑
精加工
‑
检测探伤
‑
注油孔加工
‑
表面处理等工艺步骤。
4.随着列车的高速化,一方面要求提高机车的牵引功率,另一方面要求实现列车的轻量化。轻质结构材料的应用和零部件结构的优化设计是转向架系统轻量化最有效的途径,也是发展高速列车最重要的关键技术之一。列车车轮的轻量化应满足减重、降噪以及减振等复合功能的需求。车轮作为铁路车辆转向架系统的的主要部件,起到传递轮轨之间垂向力、横向力,为车辆运行提供粘着等作用,存在着超高周疲劳、极端冲击载荷、低噪声、高磨损及高热等特点,因此车轮对材料的要求较高,除了要有足够的强度、韧性、耐磨性外,还必须具有耐擦伤剥离和低运行噪音的特性。为能使车轮轻量化,虽然可以选择减少轮径来实现,但随着轮径的减少,会加大轮轨接触应力,增加轮轨磨耗并在运行里程相同的条件下,还将会加速轮轴、轴承的疲劳损伤。所以,本发明是基于维持轮径不变,以铝合金代替部分钢结构的理念来减小车轮质量,为此需要实现车轮有限元的优化设计和轻质材料在转向架部件中的应用,其中材料除了要求轻质之外,还必须具有更高的强度、模量、韧性、耐磨、耐疲劳、耐老化等性能。
5.专利cn207683235u提出了一种分体式火车车轮,采用凸台斜面结构,用螺栓连接轮辋和轮箍,单个车轮减重了13.2%。上述设计的技术缺陷是其螺栓连接方式中螺栓受到较大的剪切力,在服役过程中是疲劳失效发生的集中点。而且,传统整体碾钢车轮制造工艺流程十分复杂(参照图1),车轮生产成本过高,能耗和污染也过高,不适合当前绿色发展的理念。
技术实现要素:6.本发明的目的是提供一种钢铝复合列车车轮一体化制造方法,以解决上述现有技术存在的问题,降低车轮的生产成本。
7.为实现上述目的,本发明提供了如下方案:
8.本发明提供了一种钢铝复合列车车轮一体化制造方法,所述钢铝复合列车车轮包括钢制轮箍和铝合金轮芯,所述钢制轮箍与所述铝合金轮芯一体成型;所述制造方法包括以下步骤:
9.(1)切割铝合金厚板得到圆柱形坯料,并去除所述圆柱形坯料表面的油污;
10.(2)将所述铝合金坯料放置在电阻炉中进行加热保温,保温的温度范围为430℃~470℃,保温完成后立即将所述铝合金坯料置于预锻模中进行第一次预变形,预变形量控制在30%~50%,得到粗坯;将所述粗坯水冷至室温;
11.(3)对所述粗坯在室温下进行第二次预变形,所述第二次预变形为辊轧变形,变形量为5%~10%,并将所述粗坯的直角边辊轧为圆角;
12.(4)对所述粗坯进行二次加热得到液固混合坯料;所述二次加热分为三个阶段:第一阶段,升温速率10℃/min,达到保温范围:300℃~330℃,保温0.5h~1h;第二阶段,升温速率10℃/min,达到保温范围:470℃~500℃,保温0.5h~1h;第三阶段,升温速率,5℃/min,达到保温范围:570℃~660℃,保温0.5h~2h;
13.(5)在模锻成形模具的下模型腔中放置已制备好的所述钢制轮箍,并通过压圈固定所述钢制轮箍,然后将所述液固混合坯料导入所述模锻成形模具的型腔,并使所述液固混合坯料在压力下凝固成形,成形压力为10mpa~100mpa,下压速度5mm/s~10mm/s,保压10s~35s后,然后开模,得到钢铝复合一体式车轮;
14.(6)对所述钢铝复合一体式车轮整体进行t6热处理,其中固溶热处理温度为430℃~470℃,保温时间为1h~4h,并在保温后的20s内浸入水中快速冷却;随后的时效热处理温度为120℃~170℃,保温时间为8h~12h;
15.(7)在热处理温度下,直接对所述钢铝复合一体式车轮的钢铝结合部位和轮芯孔部位进行局部压力加工;
16.(8)将所述钢铝复合一体式车轮通过机加工获得符合尺寸公差和轮轴装配精度要求的所述钢铝复合列车车轮,并对钢铝复合界面结合处进行表面防护处理,即对所述钢铝复合列车车轮进行腐蚀防护。
17.优选的,在步骤(5)中将所述液固混合坯料导入所述模锻成形模具的型腔之前还需进行氧化皮去除步骤:通过坯料转移工具,在卸料时去除所述液固混合坯料的表层氧化皮。
18.优选的,在氧化皮去除步骤之前还需进行模具预热步骤:将所述模锻成形模具预热至300℃~350℃。
19.优选的,在所述模具预热步骤之前还包括模具喷涂步骤:在模锻成形模具预热前对所述模锻成形模具的型腔内壁均匀喷涂涂层,涂层选用氮化硼高温惰性高温无机润滑材料。
20.优选的,在步骤(6)中:所述钢铝复合一体式车轮需要在人工时效热处理后,立即利用液锻成形设备对钢铝结合部位进行局部温碾加工,温度为120℃~170℃,压力大小为
10mpa~30mpa。
21.优选的,在步骤(6)中:所述固溶热处理结束时还包括快速冷却,以获得时效所需的过饱和固溶体,所述快速冷却采用盐水冷却,所述盐水的水温为80
±
5℃。
22.优选的,在步骤(8)后,还需要对所述钢铝复合列车车轮进行无损检测。
23.优选的,所述钢制轮箍的内壁对应所述铝合金轮芯设置有环形凹槽,所述铝合金轮芯的边缘在所述环形凹槽内直接成形。
24.本发明相对于现有技术取得了以下技术效果:
25.本发明的钢铝复合列车车轮一体化制造方法,降低了钢铝复合列车车轮的生产成本。本发明的钢铝复合列车车轮一体化制造方法通过对铝合金原始坯料进行切割、加热、预变形并二次加热,获得液固混合触变形坯料,然后进行液固模锻成形,并在成形后进行固溶热处理和时效热处理,并在时效热处理温度下进行摆碾局部成型工艺,最后经过机加工和表面处理得到钢铝复合一体车轮,使得采用所述方法制造的车轮整体减重25%以上,且整体性能复合车辆应用需求。在实现车辆轻量化的同时,利用铝合金高回收率的特点及简化的生产工艺流程等特点,促进轨道车辆列车车轮生产的经济性,以及行车安全性和舒适性。
附图说明
26.为了更清楚地说明本发明实施例或现有技术中的技术方案,下面将对实施例中所需要使用的附图作简单地介绍,显而易见地,下面描述中的附图仅仅是本发明的一些实施例,对于本领域普通技术人员来讲,在不付出创造性劳动的前提下,还可以根据这些附图获得其他的附图。
27.图1为传统车轮制造方法的流程图;
28.图2为本发明钢铝复合列车车轮一体化制造方法中钢铝复合列车车轮的结构示意图;
29.图3为本发明钢铝复合列车车轮一体化制造方法的流程图;
30.其中:100、钢铝复合列车车轮;1、钢制轮箍;2、铝合金轮芯;3、结合界面。
具体实施方式
31.下面将结合本发明实施例中的附图,对本发明实施例中的技术方案进行清楚、完整地描述,显然,所描述的实施例仅仅是本发明一部分实施例,而不是全部的实施例。基于本发明中的实施例,本领域普通技术人员在没有付出创造性劳动的前提下所获得的所有其他实施例,都属于本发明保护的范围。
32.本发明的目的是提供一种钢铝复合列车车轮一体化制造方法,以解决上述现有技术存在的问题,降低车轮的生产成本。
33.为使本发明的上述目的、特征和优点能够更加明显易懂,下面结合附图和具体实施方式对本发明作进一步详细的说明。
34.如图2至图3所示:本实施例提供了一种钢铝复合列车车轮一体化制造方法,钢铝复合列车车轮包括钢制轮箍和铝合金轮芯,钢制轮箍与铝合金轮芯一体成型,钢制轮箍的内壁对应铝合金轮芯设置有环形凹槽,铝合金轮芯的边缘在环形凹槽内直接成形。
35.本实施例钢铝复合列车车轮一体化制造方法包括以下步骤:
36.(1)切割铝合金厚板得到圆柱形坯料,并去除圆柱形坯料表面的油污;
37.(2)将铝合金坯料放置在电阻炉中进行加热保温,保温的温度范围为430℃~470℃,保温完成后立即将铝合金坯料置于预锻模中进行第一次预变形,预变形量控制在30%~50%,得到粗坯;将粗坯水冷至室温;
38.(3)对粗坯在室温下进行第二次预变形,第二次预变形为辊轧变形,变形量为5%~10%,并将粗坯的直角边辊轧为圆角;
39.(4)对粗坯进行二次加热得到液固混合坯料;二次加热分为三个阶段:第一阶段,升温速率10℃/min,达到保温范围:300℃~330℃,保温0.5h~1h;第二阶段,升温速率10℃/min,达到保温范围:470℃~500℃,保温0.5h~1h;第三阶段,升温速率,5℃/min,达到保温范围:570℃~660℃,保温0.5h~2h;
40.(5)在模锻成形模具的下模型腔中放置已制备好的钢制轮箍,并通过压圈固定钢制轮箍;对模锻成形模具的型腔的内壁均匀喷涂涂层,涂层选用氮化硼高温惰性高温无机润滑材料;然后将模锻成形模具预热至300℃~350℃;然后通过机械臂辅助坩埚转移坯料,在卸料时去除液固混合坯料的表层氧化皮;
41.然后将液固混合坯料导入模锻成形模具的型腔,并使液固混合坯料在压力下凝固成形,成形压力为10mpa~100mpa,下压速度5mm/s~10mm/s,保压10s~35s后,然后开模,得到钢铝复合一体式车轮;
42.(6)对钢铝复合一体式车轮整体进行t6热处理,其中固溶热处理温度为430℃~470℃,保温时间为1h~4h,并在保温后的20s内浸入水中快速冷却;固溶热处理结束时还包括快速冷却,以获得时效所需的过饱和固溶体,快速冷却采用盐水冷却,盐水的水温为80
±
5℃;
43.随后的时效热处理温度为120℃~170℃,保温时间为8h~12h;在人工时效热处理后,立即利用液锻成形设备对钢铝复合一体式车轮的钢铝结合部位进行局部温碾加工,温度为120℃~170℃,压力大小为10mpa~30mpa;
44.(7)在热处理温度下,直接对钢铝复合一体式车轮的钢铝结合部位和轮芯孔部位进行局部压力加工;
45.(8)将钢铝复合一体式车轮通过机加工获得符合尺寸公差和轮轴装配精度要求的钢铝复合列车车轮,并对钢铝复合界面结合处进行表面防护处理,即对钢铝复合列车车轮进行腐蚀防护。
46.然后对钢铝复合列车车轮进行无损检测即可。
47.本说明书中应用了具体个例对本发明的原理及实施方式进行了阐述,以上实施例的说明只是用于帮助理解本发明的方法及其核心思想;同时,对于本领域的一般技术人员,依据本发明的思想,在具体实施方式及应用范围上均会有改变之处。综上所述,本说明书内容不应理解为对本发明的限制。