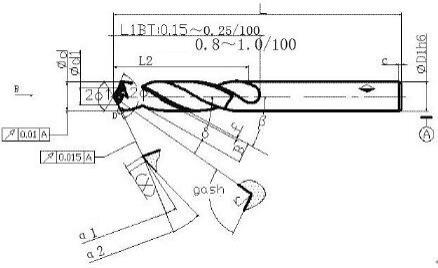
1.本实用新型涉及精加工用刀具领域,特别是一种抛物线槽型凸圆弧刃复合钻尖球头孔钻孔刀具。
背景技术:2.目前,我国水泥行业、矿山行业辊压机轧辊的球头辊压齿安装球头孔的制造工艺绝大部分是采用钻孔—扩孔——用球形铣刀铣球头形孔,这样加工出来的加工孔的尺寸精度低、孔的位置精度低、孔的圆柱度低、孔壁粗糙度值大。
3.虽然为了解决这样的问题市面上出现了一些针对该加工孔的复合刀具,但是取得的效果普遍差强人意。
技术实现要素:4.本实用新型的目的在于提供一种抛物线槽型凸圆弧刃复合钻尖球头孔钻孔刀具,解决现有复合刀具加工出来的辊压机轧辊的球头辊压齿安装球头孔不仅尺寸精度低、孔的位置精度低、还存在孔的圆柱度低、孔壁粗糙度值大等问题。
5.为解决上述的技术问题,本实用新型采用以下技术方案:
6.一种抛物线槽型凸圆弧刃复合钻尖球头孔钻孔刀具,包括刀体,所述刀体依次设置的包括刀体端刃部和刀体周刃部,所述刀体端刃部采用麻花钻型钻尖与凸圆弧刃相结合的结构,所述麻花钻型钻尖与凸圆弧刃相交,凸圆弧刃与刀体周刃部相切,所述麻花钻型钻尖后角采用圆弧后角,凸圆弧刃采用双平面后角,所述刀体端刃部还采用负倒棱结构,所述刀体周刃部则采用麻花钻型周刃与定径带相结合的结构。
7.抛物线槽型凸圆弧刃复合钻尖球头孔钻孔刀具在工艺流程上虽因制造精度要求高而使流程稍微复杂一点,但是该刀具的结构是集凸圆弧刃与麻花钻钻尖的功能于一体的复合钻尖,而且该刀具加工的孔底形状接近于球头形状,所以其切削性能好、加工出来的加工孔尺寸精度高、孔位置精度高、圆柱度高、加工孔孔壁粗糙度值小(达可到ra0.8~ra0.4)、加工的孔底形状接近于球头形状,节省了球头铰刀铰孔工序,具有性价比高,寿命好等优点,在刀体端刃部采用负倒棱结构是为了加强刀体端刃部刃口的强度,所述刀体周刃部为校准部分,留定径带之目的是为钻孔刀具多次修磨后能控制钻孔的尺寸。
8.作为本实用新型的进一步优选,所述刀体的沟槽槽型采用抛物线螺旋槽型,抛物线螺旋槽型的沟槽前角设计为γ=2
°
~10
°
,抛物线螺旋槽型的构槽螺旋角设计为β=10
°
~30
°
。
9.满足上述结构条件能有效的提高切削性能和排屑性能,提高端刃部的结构强度,这里的γ=2
°
~10
°
是指刨去负倒棱后。
10.作为本实用新型的进一步优选,所述刀体的抛物线螺旋槽型的沟槽周刃也为负倒棱结构,该周刃负倒棱的角度设计为γ1=-5
°
~+5
°
,该周刃负倒棱角宽度设计为m=0.3~0.5mm。
11.刀体的抛物线螺旋槽型的沟槽周刃负倒棱能防止沟槽周刃崩刃。
12.作为本实用新型的进一步优选,所述麻花钻型钻尖的直径d1=(1/3~1/2)d,麻花钻型钻尖的顶角2φ=135
°
~150
°
,所述麻花钻型钻尖的后角角度α=10
°
~15
°
。
13.当麻花钻型钻尖的钻尖角小于150
°
时所钻孔的孔底更趋近于球头。
14.作为本实用新型的进一步优选,所述凸圆弧刃半径rr=d/2,所述凸圆弧刃的双平面后角第一后角为α1=10
°
~15
°
,第二后角为α2=20
°
~30
°
,第一后刀面宽度为x=(0.03~0.08)d。
15.作为本实用新型的进一步优选,所述刀体端刃部负倒棱的宽度为:k=(0.05~0.15)mm、k1=k+0.1mm,端刃负倒棱与刀体轴向的夹角ζ=15
°
~25
°
。
16.所述k为钻尖切齿隙段、k1为凸圆弧刃段。
17.作为本实用新型的进一步优选,所述定径带的长度l3=rr+(3~5)mm。
18.作为本实用新型的进一步优选,所述刀体由co8超细晶粒硬质合金棒材材料制成的,刀体的前、后刀面表面粗糙度达到ra0.2。
19.刀体选用了的co8超细晶粒硬质合金棒材材料硬度较高,颗粒度比较均匀,耐磨性能良好,而刀体的前、后刀面表面粗糙度达到ra0.2能防止刃口粘屑。
20.作为本实用新型的进一步优选,所述刀体端刃部均涂有耐磨的多层复合涂层。
21.耐磨的多层复合涂层包括tialn涂层、巴尔查斯的pt3涂层等,这样涂上后能以提高刀具的耐磨性能。
22.作为本实用新型的进一步优选,所述刀体(1)的齿数为2齿,刀体的芯厚设计为dc=(0.3~0.4)d,,刀体的容屑槽宽与刀体刃背宽比设计为m=(1.5~2.0):1。
23.与现有技术相比,本实用新型至少能达到以下有益效果中的一项:
24.1、抛物线槽型凸圆弧刃复合钻尖球头孔钻孔刀具在工艺流程上虽因制造精度要求高而使流程稍微复杂一点,但是该刀具的结构是集凸圆弧刃与麻花钻钻尖的功能于一体的复合钻尖,而且该刀具加工的孔底形状接近于球头形状,所以其切削性能好、加工出来的加工孔尺寸精度高、孔位置精度高、圆柱度高、加工孔孔壁粗糙度值小(达可到ra0.8~ra0.4)、加工的孔底形状接近于球头形状,节省了球头铰刀铰孔工序,具有性价比高,寿命好等优点,在刀体端刃部采用负倒棱结构是为了加强刀体端刃部刃口的强度,所述刀体周刃部为校准部分,留定径带之目的是为钻孔刀具多次修磨后能控制钻孔的尺寸。
25.2、刀体的抛物线螺旋槽型的沟槽周刃负倒棱能防止沟槽周刃崩刃。
26.3、刀体选用了的co8超细晶粒硬质合金棒材材料硬度较高,颗粒度比较均匀,耐磨性能良好,而刀体的前、后刀面表面粗糙度达到ra0.2能防止刃口粘屑。
附图说明
27.图1 为本实用新型的结构示意图。
28.图2 为刀具轴向前刀面示意图。
29.图3 为图1的b向视图。
30.图4为图3中c处的放大图。
31.图5 为图1的d处放大图。
32.图6为图3的e处放大图。
具体实施方式
33.为使本实用新型实施方式的目的、技术方案和优点更加清楚,下面将结合本实用新型实施方式中的附图,对本实用新型实施方式中的技术方案进行清楚、完整地描述,显然,所描述的实施方式是本实用新型一部分实施方式,而不是全部的实施方式。通常在此处附图中描述和示出的本实用新型实施方式的组件可以以各种不同的配置来布置和设计。
34.因此,以下对在附图中提供的本实用新型的实施方式的详细描述并非旨在限制要求保护的本实用新型的范围,而是仅仅表示本实用新型的选定实施方式。基于本实用新型中的实施方式,本领域普通技术人员在没有作出创造性劳动前提下所获得的所有其他实施方式,都属于本实用新型保护的范围。
35.需要说明的是,在不冲突的情况下,本实用新型中的实施方式及实施方式中的特征可以相互组合。
36.应注意到:相似的标号和字母在下面的附图中表示类似项,因此,一旦某一项在一个附图中被定义,则在随后的附图中不需要对其进行进一步定义和解释。
37.在本实用新型的描述中,需要说明的是,术语“中心”、“上”、“下”、“左”、“右”、“竖直”、“水平”、“内”、“外”等指示的方位或位置关系为基于附图所示的方位或位置关系,或者是该实用新型产品使用时惯常摆放的方位或位置关系,或者是本领域技术人员惯常理解的方位或位置关系,仅是为了便于描述本实用新型和简化描述,而不是指示或暗示所指的装置或元件必须具有特定的方位、以特定的方位构造和操作,因此不能理解为对本实用新型的限制。此外,术语“第一”、“第二”等仅用于区分描述,而不能理解为指示或暗示相对重要性。
38.在本实用新型的描述中,还需要说明的是,除非另有明确的规定和限定,术语“设置”、“安装”、“相连”、“连接”应做广义理解,例如,可以是固定连接,也可以是可拆卸连接,或一体地连接;可以是机械连接,也可以是电连接;可以是直接相连,也可以通过中间媒介间接相连,可以是两个元件内部的连通。对于本领域的普通技术人员而言,可以具体情况理解上述术语在本实用新型中的具体含义。
39.具体实施例1:
40.图1、图2、图3、图4、图5、图6示出了一种抛物线槽型凸圆弧刃复合钻尖球头孔钻孔刀具,包括刀体1,所述刀体依次设置的包括刀体端刃部和刀体周刃部,所述刀体端刃部采用麻花钻型钻尖与凸圆弧刃相结合的结构,所述麻花钻型钻尖与凸圆弧刃相交,凸圆弧刃与刀体周刃部相切,所述麻花钻型钻尖后角采用圆弧后角,凸圆弧刃采用双平面后角,所述刀体端刃部还采用负倒棱结构,所述刀体周刃部则采用麻花钻型周刃与定径带相结合的结构。
41.抛物线槽型凸圆弧刃复合钻尖球头孔钻孔刀具在工艺流程上虽因制造精度要求高而使流程稍微复杂一点,但是该刀具的结构是集凸圆弧刃与麻花钻钻尖的功能于一体的复合钻尖,而且该刀具加工的孔底形状接近于球头形状,所以其切削性能好、加工出来的加工孔尺寸精度高、孔位置精度高、圆柱度高、加工孔孔壁粗糙度值小(达可到ra0.8~ra0.4)、加工的孔底形状接近于球头形状,节省了球头铰刀铰孔工序,具有性价比高,寿命好等优点,在刀体端刃部采用负倒棱结构是为了加强刀体端刃部刃口的强度,所述刀体周刃部为校准部分,留定径带之目的是为钻孔刀具多次修磨后能控制钻孔的尺寸。
42.具体实施例2:
43.本实施例是在具体实施例1的基础上对刀体1的沟槽槽型进行了进一步的说明,所述刀体1的沟槽槽型采用抛物线螺旋槽型,抛物线螺旋槽型的沟槽前角设计为γ=2
°
,抛物线螺旋槽型的构槽螺旋角设计为β=15
°
。
44.满足上述结构条件能有效的提高切削性能和排屑性能,提高端刃部的结构强度,这里的γ是指刨去负倒棱后。
45.具体实施例3:
46.本实施例是在具体实施例1的基础上对刀体1的沟槽槽型进行了进一步的说明,所述刀体1的沟槽槽型采用抛物线螺旋槽型,抛物线螺旋槽型的沟槽前角设计为γ=5
°
,抛物线螺旋槽型的构槽螺旋角设计为β=30
°
。
47.具体实施例4:
48.本实施例是在具体实施例1的基础上对刀体1的沟槽槽型进行了进一步的说明,所述刀体1的沟槽槽型采用抛物线螺旋槽型,抛物线螺旋槽型的沟槽前角设计为γ=:10
°
,抛物线螺旋槽型的构槽螺旋角设计为β=10
°
。
49.具体实施例5:
50.本实施例是在具体实施例1的基础上对刀体的抛物线螺旋槽型的沟槽周刃进行了进一步的说明,所述刀体的抛物线螺旋槽型的沟槽周刃也为负倒棱结构,该周刃负倒棱的角度设计为γ1=-5
°
,该周刃负倒棱角宽度设计为m=0.3mm。
51.刀体的抛物线螺旋槽型的沟槽周刃负倒棱能防止沟槽周刃崩刃。
52.具体实施例6:
53.本实施例是在具体实施例1的基础上对刀体的抛物线螺旋槽型的沟槽周刃进行了进一步的说明,所述刀体的抛物线螺旋槽型的沟槽周刃也为负倒棱结构,该周刃负倒棱的角度设计为γ1=+5
°
,该周刃负倒棱角宽度设计为m=0.4mm。
54.刀体的抛物线螺旋槽型的沟槽周刃负倒棱能防止沟槽周刃崩刃。
55.具体实施例7:
56.本实施例是在具体实施例1的基础上对刀体的抛物线螺旋槽型的沟槽周刃进行了进一步的说明,所述刀体的抛物线螺旋槽型的沟槽周刃也为负倒棱结构,该周刃负倒棱的角度设计为γ1=0,该周刃负倒棱角宽度设计为m=0.5mm。
57.刀体的抛物线螺旋槽型的沟槽周刃负倒棱能防止沟槽周刃崩刃。
58.具体实施例8:
59.本实施例是在具体实施例1的基础上对麻花钻型钻尖进行了进一步的说明,所述麻花钻型钻尖的直径d1=1/3d,麻花钻型钻尖的顶角2φ=150
°
,所述麻花钻型钻尖的后角角度α=12
°
。
60.当麻花钻型钻尖的钻尖角小于150
°
时所钻孔的孔底更趋近于球头。
61.具体实施例9:
62.本实施例是在具体实施例1的基础上对麻花钻型钻尖进行了进一步的说明,所述麻花钻型钻尖的直径d1=1/2d,麻花钻型钻尖的顶角2φ=135
°
,所述麻花钻型钻尖的后角角度α=15
°
。
63.具体实施例10:
64.本实施例是在具体实施例1的基础上对麻花钻型钻尖进行了进一步的说明,所述麻花钻型钻尖的直径d1=1/2.5d,麻花钻型钻尖的顶角2φ=140
°
,所述麻花钻型钻尖的后角角度α=10
°
。
65.具体实施例11:
66.本实施例是在具体实施例1的基础上对凸圆弧刃进行了进一步的说明,所述凸圆弧刃半径rr=d/2,所述凸圆弧刃的双平面后角第一后角为α1=10
°
,第二后角为α2=20
°
,第一后刀面宽度为x=0.03d。
67.具体实施例12:
68.本实施例是在具体实施例1的基础上对凸圆弧刃进行了进一步的说明,所述凸圆弧刃半径rr=d/2,所述凸圆弧刃的双平面后角第一后角为α1=15
°
,第二后角为α2=30
°
,第一后刀面宽度为x=0.08d。
69.具体实施例13:
70.本实施例是在具体实施例1的基础上对凸圆弧刃进行了进一步的说明,所述凸圆弧刃半径rr=d/2,所述凸圆弧刃的双平面后角第一后角为α1=11
°
,第二后角为α2=23
°
,第一后刀面宽度为x=0.05d。
71.具体实施例14:
72.本实施例是在具体实施例1的基础上对所述刀体端刃部进行了进一步的说明,所述刀体端刃部负倒棱的宽度为:k=0.1mm、k1=k+0.1mm,端刃负倒棱与刀体轴向的夹角ζ=25
°
。
73.所述k为钻尖切齿隙段、k1为凸圆弧刃段。
74.具体实施例15:
75.本实施例是在具体实施例1的基础上对所述刀体端刃部进行了进一步的说明,所述刀体端刃部负倒棱的宽度为:k=0.05mm、k1=k+0.1mm,端刃负倒棱与刀体轴向的夹角ζ=15
°
。
76.具体实施例16:
77.本实施例是在具体实施例1的基础上对所述刀体端刃部进行了进一步的说明,所述刀体端刃部负倒棱的宽度为:k=0.15mm、k1=k+0.1mm,端刃负倒棱与刀体轴向的夹角ζ=20
°
。
78.具体实施例17:
79.本实施例是在具体实施例1的基础上对定径带进行了进一步的说明,所述定径带的长度l3=rr+3mm。
80.具体实施例18:
81.本实施例是在具体实施例1的基础上对定径带进行了进一步的说明,所述定径带的长度l3=rr+5mm。
82.具体实施例19:
83.本实施例是在具体实施例1的基础上对定径带进行了进一步的说明,所述定径带的长度l3=rr+4mm。
84.具体实施例20:
85.本实施例是在具体实施例1的基础上对刀体1进行了进一步的说明,所述刀体1由
co8超细晶粒硬质合金棒材材料制成的,刀体的前、后刀面表面粗糙度达到ra0.2。
86.刀体选用了的co8超细晶粒硬质合金棒材材料硬度较高,颗粒度比较均匀,耐磨性能良好,而刀体的前、后刀面表面粗糙度达到ra0.2能防止刃口粘屑。
87.具体实施例21:
88.本实施例是在具体实施例1的基础上对刀体端刃部进行了进一步的说明,所述刀体端刃部涂有耐磨的多层复合涂层。
89.耐磨的多层复合涂层包括tialn涂层、巴尔查斯的pt3涂层等,这样涂上后能以提高刀具的耐磨性能。
90.具体实施例22:
91.本实施例是在具体实施例1的基础上对刀体1进行了进一步的说明,所述刀体1的齿数为2齿,刀体的芯厚设计为dc=0.3d,,刀体的容屑槽宽与刀体刃背宽比设计为m=1.5:1。
92.具体实施例23:
93.本实施例是在具体实施例1的基础上对刀体1进行了进一步的说明,所述刀体1的齿数为2齿,刀体的芯厚设计为dc=0.4d,,刀体的容屑槽宽与刀体刃背宽比设计为m=2.0:1。
94.具体实施例24:
95.本实施例是在具体实施例1的基础上对刀体1进行了进一步的说明,所述刀体1的齿数为2齿,刀体的芯厚设计为dc=0.35d,,刀体的容屑槽宽与刀体刃背宽比设计为m=1.8:1。
96.尽管参照前述实施例对本实用新型进行了详细的说明,对于本领域的技术人员来说,其依然可以对前述各实施例所记载的技术方案进行修改,或者对其中部分技术特征进行等同替换,凡在本实用新型的精神和原则之内,所作的任何修改、等同替换、改进等,均应包含在本实用新型的保护范围之内。