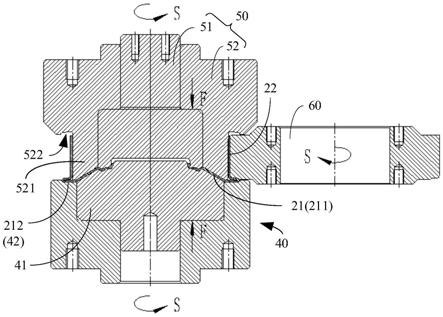
1.本发明属于机械加工技术领域,特别涉及一种皮带轮的加工方法。
背景技术:2.大轮缘的皮带轮通常采用铸铁铸造,小轮缘的皮带轮通常采用钢材锻造,铸造或锻造工艺生产得到的毛坯,还需经过粗车、精车等工序加工,会车去大量边料,材料耗损大,能耗高且生产效率低下。
3.旋压是将平板或空心坯料固定在旋压机的模具上,在坯料随机床主轴转动的同时,用旋轮或赶棒加压于坯料,使之产生局部塑性变形的工艺。目前采用旋压工艺生产的皮带轮与铸造皮带轮相比壁厚较薄,具有成本低、重量轻、使用寿命长的优点,已广泛应用于各领域。现有技术中,旋压皮带轮通常采用轮辐与轮缘联结呈t型状的结构,加工时先将板状坯料劈分为两瓣后旋压构成轮缘,或将板状坯料墩粗增厚为t型再旋压成型。大轮缘皮带轮旋压加工时,需要劈分或墩粗的物料量大,现有的旋压机旋压力过小无法实现大量物料的旋压加工,也就无法应用旋压工艺生产大轮缘的皮带轮。
技术实现要素:4.本发明的目的在于提供一种生产便捷且成品率高的皮带轮的加工方法。
5.为实现以上目的,本发明采用的技术方案为:一种皮带轮的加工方法,包括如下步骤:
6.a、一次成型:平板坯料居中圆形区域的板体向板面一侧凸伸构成碟型的底壁,底壁外部的板体向底壁凸伸侧翻折构成环形的侧壁,位于内侧的底壁和位于外侧的侧壁构成杯型坯料,
7.底壁中部冲裁有过孔,底壁包括凸伸部和位于凸伸部外侧的外板边、位于凸伸部内侧的内板边;
8.b、二次成型:侧壁邻近底壁的壁体向底壁凸伸侧翻折至与底壁边沿叠合状,构成沿杯型坯料径向微凸的第一凸缘;
9.d、焊接:步骤b制得的杯型坯料中部的过孔套设在管型轮毂的端部并实施焊接,两个杯型坯料的口沿相对并焊接连接。
10.与现有技术相比,本发明存在以下技术效果:皮带轮的加工步骤简单,能低成本、高效率地生产大轮缘皮带轮。步骤b可应用旋压工艺加工且所需旋压模具少,突破性地实现大轮缘皮带轮轮圈的旋压加工。
附图说明
11.下面对本说明书各附图所表达的内容及图中的标记作简要说明:
12.图1是平板坯料的俯视示意图;
13.图2是步骤a制得杯型坯料的剖切示意图;
14.图3是步骤b1的示意图;
15.图4是步骤b2的示意图;
16.图5是步骤c的示意图;
17.图6是步骤c制得杯型坯料的剖切示意图;
18.图7是步骤d制得皮带轮的剖切示意图。
19.图中:10.平板坯料,20.杯型坯料,21.底壁,211.凸伸部,212.外板边,213.内板边,22.侧壁,23.过孔,24.第一凸缘,30.轮毂,40.下模, 41.承台,42.浅槽,50.上模,51.内模,52.外模,521.凸环,522.环槽,60.第一旋转轮,70.第二上模,71.基座,72.凸柱
具体实施方式
20.下面结合附图,通过对实施例的描述,对本发明的具体实施方式作进一步详细说明。
21.实施例一
22.一种皮带轮的加工方法,包括如下步骤:
23.a、一次成型:平板坯料10居中圆形区域的板体向板面一侧凸伸构成碟型的底壁21,底壁21外部的板体向底壁21凸伸侧翻折构成环形的侧壁22,位于内侧的底壁21和位于外侧的侧壁22构成杯型坯料20。杯型坯料20如附图2所示,底壁21中部冲裁有过孔23,底壁21包括凸伸部211和位于凸伸部211外侧的外板边212、位于凸伸部211内侧的内板边213。一次成型可采用冲压加工工艺成型。
24.b、二次成型:侧壁22邻近底壁21的壁体向底壁21凸伸侧翻折至与底壁21边沿叠合状,构成沿杯型坯料20径向微凸的第一凸缘24。
25.二次成型可应用拉弯压弯等加工工艺成型,也可以应用旋压工艺加工,应用旋压工艺成型时,如附图3、4所示,具体步骤如下:
26.提供下模40、第一上模50和第一旋转轮60。下模40的上端型面与底壁21的下表面吻合,包括居中布置向上凸伸的承台41和位于承台 41的周侧的环形浅槽42。第一上模50包括同心布置的内模51和外模 52,内模51的下端面与底壁21的内板边213吻合,外模52包括凸环 521,凸环521的端面向内凹陷与底壁21的凸伸部211吻合,凸环521 基部的周侧设有环槽522。第一旋转轮60的轮心与第一上模50的轮心平行间隔布置且间距可调。
27.b1、步骤a制得的杯型坯料20置于下模40上,内模51下压并与下模40夹持底壁21的内板边213,外模52下压使其凸环521与底壁 21分离且环槽522与侧壁22的口沿贴合布置。
28.b2、第一旋转轮60的轮心沿第一上模50的径向做靠近外模50的平移运动,第一旋转轮60的轮圈贴合侧壁22驱使侧壁22的壁体位移并与凸环521的外壁贴合,同时驱使侧壁22邻近底壁21的壁体在第一旋转轮60的作用下向底壁21凸伸侧翻折,外模52随侧壁22的口沿向下位移至与下模40夹持底壁21凸伸部211的姿态。
29.d、焊接:步骤b制得的杯型坯料20中部的过孔23套设在管型轮毂30的端部并实施焊接,两个杯型坯料20的口沿相对并焊接连接。
30.本方法加工所得的旋压皮带轮如附图7所示,包括轮毂10和单元半体,单元半体整体呈外周面为圆柱面的杯体状,两单元半体的底壁21 相背、侧壁22顺齐、口部吻合对接布置,管状的轮毂10与单元半体的底壁21相互固连且管状轮毂10与单元半体同芯布置,单元
半体的底壁 21构成轮体的辐板,单元半体的侧壁22构成轮体的轮圈。轮毂10穿置于单元半体的底壁21上开设的过孔211且轮毂10与过孔23焊接,两单元半体的口部相互焊接。两单元半体以杯口贴合面为对称面轴向对称布置,轮毂10以杯口贴合面为对称面轴向对称布置。单元半体的底壁21 自边沿至中部逐渐向口部所在侧凸伸,单元半体的底壁21和侧壁22的交界处为折返式的叠合部构成的沿径向微凸的第一凸缘24。如附图1所示,底壁21自轮毂10的端部向外延伸,这样能在保证单元半体与轮毂 10的可靠连接的同时,增大轮圈尺寸。第一凸缘24能保证底壁21与侧壁22交接处的结构强度,同时,在使用时还能对包覆于其轮圈外的皮带起限位作用,避免皮带脱出轮圈。
31.实施例二
32.本实施例与实施例一的不同之处在于,所述的步骤b与步骤d之间还有步骤c,三次成型:侧壁22的口沿向杯型坯料20内弯折或翻折构成第二凸缘25。
33.三次成型可应用拉弯压弯等加工工艺成型,也可以应用旋压工艺加工,应用旋压工艺成型时,如附图5所示,提供下模40、第二上模70 和第二旋转轮80,第二上模70的基座71中部设有向下凸伸的凸柱72,第二旋转轮80的轮心与第二上模70的芯轴夹锐角且其轮盘呈内低外高式布置。凸柱72与下模40分别压、顶在杯型坯料20的底壁21上,第二旋转轮80的轴心沿第二上模70的径向平移时其下角部的型面将侧壁 22的口沿旋压成型为第二凸缘24。
34.本方法加工所得的旋压皮带轮与实施例一的不同之处在于,侧壁22 的口沿向内弯折或翻折构成第二凸缘25,第二凸缘25能增强单元半体口部结构强度,保证轮圈中部的形状与姿态。