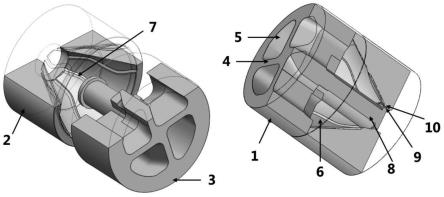
1.本发明属于型材加工成形领域,具体涉及一种利用自旋转剪切应变改善中空型材力学性能的方法和模具。
背景技术:2.中空型材作为轻质关键结构件,在航空航天、轨道交通、汽车工程等领域是不可或缺的重要零部件。长度较长、截面复杂的中空型材往往采用分流-组合模具进行正向挤压来制备。然而,在此过程中,预热后的坯料首先被压入钢模孔中,然后由分流桥将坯料劈开成几道金属流。随着挤压过程的继续,分离的几道金属流在组合模的焊合室内形成固相焊接。最后,挤出成形。这个过程不可避免地形成几个纵向焊缝,贯穿整个型材的长度方向,对合金成形能力和固相焊合能力有极高的要求。传统的挤压技术制备空心型材存在组织均匀性差、力学性能均一性差等问题,严重恶化空心型材使役过程中的可靠性。
3.为了解决上述问题,国内外专家对中空型材挤压成形技术进行了大量研究。中国专利cn104741402a中提出了一种5a06铝合金小规格中空型材的加工方法,该专利所述成形方法具有工艺流程短、生产效率高、成本低等优点,适合制备具有一定强度要求的小规格中空型材。中国专利cn103586303a中提出了一种高倍数铝型材挤压模具及挤压工艺,通过对各分流孔结构进行均匀流量分配的设计,保证金属流动速度和流量一致,从而减轻模具受力。结合对工作带的设计,实现了挤压铝型材良品率的提高。
4.但是,这些方法对合金的耐蚀性和可焊性有很高的要求,仍然难以保证中空型材微观组织均匀性和力学性能均一性。
技术实现要素:5.针对现有技术中存在的不足,本发明提出了一种利用自旋转剪切应变改善中空型材力学性能的成形方法和模具,解决中空型材组织均匀性差以及力学性能均一性差等显著影响产品可靠性的问题。同时,该技术方法的实施可以有效降低挤压力,节约能耗,易于推广应用,具有显著的经济价值。
6.本发明是通过以下技术手段,实现上述技术目的的。
7.本发明提供了一种利用自旋转剪切应变改善中空型材力学性能的挤压模具,模具包括分流模和组合模,分流模进料面上沿圆周方向均匀分布有多个分流桥和分流孔,锭坯挤压经过分流模后,被分流桥分裂成多股金属流,通过分流孔进入分流模的导流腔,导入组合模,组合模的导流面采用涡旋结构设计,使合金在挤压过程中自发产生垂直于挤压方向的圆周向剪切应变;组合模与分流模配合使用,将多股金属流在高温高压环境下发生固相焊合,最终挤出成形。
8.优选的,所述涡旋结构布设在组合模焊合室内,挤压过程中组合模不沿周向自转,涡旋结构的存在即可为坯料提供圆周方向的旋转剪切应变分量。
9.优选的,所述组合模的导流面相对于挤压方向的倾斜度为20
°‑
90
°
。
10.优选的,在垂直于挤压方向的截面上,涡旋结构上任意一点的切向与该点处沿圆周方向(圆心为模具轴与该截面交点)的切向的夹角α呈0
°‑
45
°
。
11.利用所述中空型材挤压模具挤压合金的方法,具体方法如下:将锭坯预热后放入挤压筒内,驱动挤压杆挤压锭坯,使锭坯依次经过分流模-组合模后挤出成形,获得中空型材。
12.优选的,中空型材包括但不限于圆管、三角管、方管、六方管等,通过分流-焊合挤压成形的中空型材均适用本方法成形。
13.本发明所述的利用自旋转剪切应变改善中空型材力学性能的方法和模具,合理地在传统挤压的三向正应变中引入自旋转剪切应变,在金属分流后的焊合过程中,巧妙地通过导流面的涡旋结构,使金属变形过程中,微观组织均匀性明显改善,力学性能均一性显著提高,有利于提高固相焊合的接头质量。与此同时,有效降低了挤压力,节约能耗,易于推广应用。
附图说明
14.图1为本发明模具的立体结构示意图。
15.图2为组合模具的俯视图。
16.图3为组合模a截面中涡旋结构示意图。
17.图4为利用本专利方法制备的镁型材中挤压焊缝显微组织。
18.图中:1、分流模;2、组合模;3、进料面;4、分流桥;5、分流孔;6、导流腔;7、导流面;8、模芯;9、分流模工作带;10、组合模工作带。
具体实施方式
19.下面结合附图,对本发明的优选实施例做进一步的阐述,但本发明的保护范围并不限于此。
20.本发明所述利用自旋转剪切应变改善中空型材力学性能的挤压模具如图1所示,包括分流模1和组合模2,所述分流模1的进料面3上沿圆周方向均匀分布有4个分流桥4,分流桥将分流面均匀分割出4个花瓣状的分流孔5,锭坯挤压经过分流模1后,被分流桥4分裂成4股金属流,通过分流孔5进入导流腔6,导入组合模,导流腔由分流模1的模芯8外表面和组合模的导流面7共同组成。导流面7呈涡旋状设计,涡旋导流面7相对于挤压方向的倾斜度为30
°
~60
°
。在垂直于挤压方向的截面上,涡旋结构上任意一点的切向与该点处沿圆周方向(圆心为模具轴与该截面交点)的切向的夹角α呈0
°‑
35
°
。组合模与分流模配合使用,将4股金属流在高温高压环境下发生固相焊合,最终在分流模的工作带9和导流模的工作带10作用下,挤出成形。
21.以6063铝合金挤压成圆管型材为例,利用本发明所述自旋转剪切应变改善中空型材力学性能的成形方法和模具,制造空心型材,具体方法如下:
22.a.对6063铝合金铸坯进行均匀化热处理,工艺参数如下:均匀化温度为530℃,保温3h,随后空冷至室温。
23.b.将6063铝合金锭坯加热至480℃,挤压筒加热至450℃,模具加热至460℃,进行
挤压,挤压杆推进速度控制在4mm/s。
24.c.6063铝合金锭坯在挤压垫推动下,在挤压筒内与分流模1的进料面3作用,发生预变形。预变形的锭坯经分流桥4作用,分成多股金属流,流入分流孔5中。随后流入组合模2的导流腔6内,发生焊合。同时,在组合模的导流面7作用下产生自旋转的剪切应变,促进塑性变形和固相焊合过程中组织的细化。最后,在分流模的工作带9和导流模的工作带10作用下,挤出成形。
25.d.切除6063铝合金空心型材头部30cm和尾部20cm,进行等温时效热处理,时效温度190℃,时效时间4h。最后按照型材交付的实际要求截取相应长度。
26.以上述方法制备的6063铝合金型材(6063-xj)与传统挤压工艺制备的铝合金型材(6063-zj)力学性能对照,结果如表2所示。抗拉强度表示为uts,拉伸屈服强度表示为tys,断裂延伸率表示为el。
27.表2自旋转挤压与传统挤压工艺制备的6063铝合金型材力学性能对比
28.样品uts(mpa)tys(mpa)el(%)6063-zj232
±
14198
±
86
±
2.86063-xj266
±
11232
±
88
±
2.2
29.再以vw84m镁合金挤压成圆管型材为例,利用本发明所述自旋转剪切应变改善中空型材力学性能的成形方法和模具,制造空心型材,具体方法如下:
30.a.对vw84m镁合金铸坯进行均匀化热处理,工艺参数如下:均匀化温度为540℃,保温4h,随后空冷至室温。
31.b.将vw84m镁合金锭坯加热至470℃,挤压筒加热至460℃,模具加热至470℃,进行挤压,挤压杆推进速度控制在0.4mm/s。
32.c.vw84m镁合金锭坯在挤压垫推动下,在挤压筒内与分流模1的进料面3作用,发生预变形。预变形的锭坯经分流桥4作用,分成多股金属流,流入分流孔5中。随后流入组合模2的导流腔6内,发生焊合。同时,在组合模的导流面7作用下产生自旋转的剪切应变,促进塑性变形和固相焊合过程中组织的细化。最后,在分流模的工作带9和导流模的工作带10作用下,挤出成形。
33.d.切除vw84m镁合金空心型材头部30cm和尾部20cm,进行等温时效热处理,时效温度200℃,时效时间60h。最后按照型材交付的实际要求截取相应长度。
34.以上述方法制备的vw84m镁合金型材(vw84m-xj)与传统挤压工艺制备的镁合金型材(vw84m-zj)力学性能对照,结果如表2所示。vw84m-xj镁型材中挤压焊缝显微组织如图4所示。
35.表2自旋转挤压与传统挤压工艺制备的vw84m镁合金型材力学性能对比
36.样品uts(mpa)tys(mpa)el(%)vw84m-zj472
±
15335
±
108.3
±
3.5vw84m-xj515
±
10406
±
810.5
±
2.3
37.本发明并不限于上述实施方式,凡采用和本发明相同或相似结构来实现本发明目的地所有方式,皆在本发明的保护范围之内。