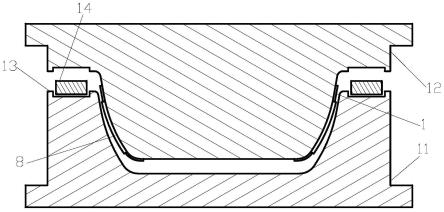
1.本技术涉及飞机制造领域的一种钣金件制造技术,具体是一种提升硬铝合金回转体钣金件航向载荷性能的制备方法。
背景技术:2.公知金属板材存在各项异性,板料沿纤维方向的强度、塑性、弯曲等性能明显优于垂直于沿纤维方向。航向载荷性能即沿飞行方向承载以拉伸为主载荷的性能,目前各类飞机用于机身纵向加强结构的零件,如飞机的长桁均采用挤压型材,其原因是挤压型材纤维组织与飞机航向一致。国产牌号2a12、国外牌号2024等硬铝合金具备重量轻、强度高的显著优点,是航空飞行器钣金零件使用最广泛的材料。加工纤维组织与服役主载荷方向一致的钣金件,不仅利于飞机减重,而且可显著提高产品的服役寿命。
3.申请人在先专利公布号:cn113787129a,公开了一种通过相变、形变、细化晶粒方式提升硬铝合金钣金零件综合力学性能方法。由于金属纤维是热轧、挤压时热软化金属晶粒被压扁或拉长形成沿流料方向纤维状组织,然而金属纤维组织形成要求金属晶粒明显压扁或拉长,宏观上体现为极高的塑性变形,常规变形方式只能改变纵向与横向晶粒的比例,因此该方法不能形成纤维组织与航向载荷一致产品。尤其是硬铝合金回转体钣金件在战机的机头、机身等部位应用较为广泛;制造的零件沿航向纤维组织数量越多,顺航向承载拉伸、弯曲载荷性能越强,战机进行高机动加速顺航向承载拉伸载荷时机体安全系数越高。
技术实现要素:4.为了克服现有技术制备的回转体钣金件的金属纤维方向不能与航向拉伸、弯曲载荷一致,影响产品服役寿命方面的缺陷。本技术的目的在于提供一种提升硬铝合金回转体钣金件航向载荷性能的制备方法,通过强冷厚向压缩变形、再结晶热处理、大塑性冷拉深成形、强热厚向挤压顺航向大塑性蠕变方式实现回转体钣金件形成航向纤维组织。
5.一种提升硬铝合金回转体钣金件航向载荷性能的制备方法,其特征包含以下内容:1)将圆形钣金胚料在常温状态下进行厚向压缩变形储能,使胚料的厚度变薄,胚料的纤维晶粒被压扁加宽;2)将厚向压缩处理后的胚料在双面受压状态进行再结晶热处理,使胚料被压扁加宽的纤维晶粒破碎形成等轴细晶粒;3)再将热处理后胚料置于拉深模具进行塑性极限冷拉深成形,使胚料沿径向受拉形成回转体,胚料的等轴细晶粒沿径向拉长为椭圆形细晶粒;4)将回转体切割余量后进行氧化处理;5)将氧化处理后的回转体通过挤压模具进行厚向热挤压,使回转体的壁厚减薄,回转体的环形壁上的椭圆形细晶粒沿侧壁被拉长为顺航向纤维晶粒;6)最后将回转体进行加热固溶和淬火冷却完成最终热处理强化,再切割回转体的余量后得到回转体钣金件成品。
6.进一步地,在步骤1)中,采用滚轮对胚料反复冷滚挤压,使胚料垂直于纤维方向为减薄延展主变形方向,挤压减薄率大于胚料厚度30%。
7.进一步地,在步骤2)中,胚料在双面受压状态进行再结晶热处理时,先将胚料双面
用钢板压紧,然后将压紧状态胚料在300
±
20℃温度环境下预热,再将预热后胚料在420
±
20℃温度硝盐炉内保温,使变形晶粒再结晶比率达到80%以上后自然冷却。
8.进一步地,在步骤3)中,拉深成形时,热处理后胚料以垂直于纤维方向为主变形方向。
9.进一步地,在步骤3)中,所述的拉深模具的拉深下模工作面与回转体钣金件内表面一致,拉深上模与拉深下模工作面合模状态下,上下模之间的间隙与热处理后胚料厚度一致,该间隙大于回转体钣金件理论厚度。
10.进一步地,在步骤5)中,厚向挤压时,将回转体与挤压下模加热到400
±
20℃温度保温,挤压上模加热到280
±
20℃温度。
11.进一步地,在步骤5)中,所述的挤压模具的挤压上模工作面与回转体钣金件内表面一致,挤压上模与挤压下模工作面合模状态下,上下模之间的间隙等于回转体钣金件理论厚度,该挤压上模与挤压下模工作面大于回转体钣金件的面积。
12.进一步地,在步骤5)中,所述的挤压模具的挤压下模与挤压下模工作面的外侧还设有环形非工作面,在环形非工作面上设有限制合模间隙的耐热承压块。
13.进一步地,步骤6)中,对回转体进行加热固溶时,先将回转体在300
±
20℃温度预热,再将回转体转移至494
±
5℃盐炉保温固溶。
14.进一步地,步骤6)中,对回转体进行淬火冷却时,先将回转体置于190
±
10℃温度盐炉内预降温,然后将预降温回转体置于常温水中冷却。
15.本技术有益效果是:
16.本技术通过控制厚向压缩形变储能时胚料挤压延展方向,既使得再结晶处理后等轴细晶粒优先沿垂直于纤维方向形成,又使材料拉深冷塑性成形工艺性整体得到改善,利于更大拉深塑性变形量使更多材料晶粒沿径向拉长为椭圆形,增加挤压后沿航向纤维晶粒的数量。本技术挤压时利用金属热状态高强度挤压蠕变易流动特性,通过厚向挤压使材料沿航向动态再结晶大塑性减薄延展,既可愈合拉深变形产生微观裂纹,提高材料组织致密度,又形成更多沿航向纤维晶粒。因此本技术制备方法制备的回转体钣金件不仅整体组织致密度高,而且可形成大量沿航向的纤维晶粒,可显著提升钣金件沿航向承受拉伸载荷的性能。
17.下面结合附图和实施例对本技术进一步说明。
附图说明
18.图1是本技术回转体钣金件形状示意图
19.图2是本技术回转体钣金件胚料厚向滚挤压变形储能原理示意图
20.图3是本技术回转体钣金件胚料再结晶热处理前后晶粒分布对比示意图
21.图4是本技术回转体钣金件拉深成形示意图
22.图5是本技术回转体钣金件拉深成形后晶粒分布示意图
23.图6是本技术回转体钣金件挤压模具厚向挤压原理示意图
24.图中编号说明:1.回转体钣金件,2.航向,3.环形壁,4.晶粒,5.胚料,6.滚轮,7.纤维方向,8.回转体,9.拉深上模,10.拉深下模,11.挤压下模,12.挤压上模,13.环形非工作面,14.承压块。
具体实施方式
25.参照附图1至附图6,本技术涉及的硬铝合金回转体钣金件1如图1所示,是一个沿航向2承载以拉伸为主载荷的钣金件,回转体环形壁3四周含有航向纤维状晶粒4可明显提升沿航向2承受拉伸载荷的性能,根据本技术的发明方案,其制备过程如下:
26.步骤1)将厚度大于回转体钣金件1的圆形钣金胚料5在常温状态下进行厚向压缩变形储能,使胚料5的厚度变薄,胚料纤维晶粒4被压扁加宽。具体操作方法是采用滚轮6对胚料5反复冷滚挤压,使胚料5垂直于纤维方向7为减薄延展主变形方向,挤压减薄率大于胚料5厚度30%。需要补充说明三点:一是圆形胚料5厚度大于回转体钣金件1厚度,目的提高压缩变形储能及挤压沿航向2减薄流料形成航向纤维晶粒效果。二是用滚轮6反复冷滚挤压时胚料5局部区域进行连续减薄,受力面积小压强高,利于提高胚料5储能效果。三是胚料5垂直于纤维方向7为减薄延展主变形方向,即挤压后胚料5为椭圆形状,目的是使胚料5储能具有明显方向性,可以增加步骤2)再结晶热处理后垂直于原纤维方向7等轴细晶粒4数量。
27.步骤2)将厚向压缩处理后的胚料5在双面受压状态进行再结晶热处理,使胚料被压扁加宽的晶粒破碎,由一个纤维晶粒破碎形成数个等轴细晶粒4。需要补充说明四点:一是步骤1)中胚料5厚向压缩变形储能具有方向性,容易在垂直于原纤维方向7以较低温度下获得更多、更细等轴细晶粒4。二是再结晶热处理时胚料5受热会膨胀,挤压状态再结晶组织致密度更高,因此热处理前先将胚料5双面用钢板压紧。三是再结晶组织大小与加热温度及高温停留时间关系紧密,温度过高或保温时间过长材料会产生部分二次再结晶粗大晶粒,会抵消部分再结晶细化效果。因此先将压紧状态胚料5在300
±
20℃温度环境下预热,再将预热后胚料5在420
±
20℃温度硝盐炉内保温,使变形晶粒4再结晶比率达到80%以上后自然冷却,其目的是既减少高温停留时间避免组织粗大,又提高变形晶粒4再结晶比率。
28.步骤3)将热处理后胚料5置于拉深模具进行塑性极限冷拉深成形,使胚料5沿径向受拉形成回转体8,胚料5的等轴细晶粒4沿径向拉长为椭圆形晶粒4。需要补充说明四点:一是拉深成形时,热处理后胚料5以垂直于原纤维方向7为主变形方向。其原因是步骤1)、步骤2)只能使垂直于原纤维方向等轴细晶粒4数量多于原纤维方向,减少胚料5各项异性差,以垂直于原纤维方向7为主变形方向既可增加晶粒4沿径向拉长形成椭圆形晶粒4的数量,又再次通过形变改变部分未变形晶粒数量,目的是进一步降低拉深成形后回转体材料各项异性,可以通过增加对应法兰边阻力方式实现。二是拉深成形变形量越大沿航向2被拉长形成椭圆形晶粒4越多,因此控制拉深最大减薄区减薄率接近材料等效双拉胀形减薄率。三是拉深成形与挤压相比材料厚度变化相对较小,因此拉深模具的拉深上模9与拉深下模10工作面合模状态理论间隙与厚向压缩处理后的胚料5厚度一致,该理论间隙大于回转体钣金件1理论厚度。
29.步骤4)将回转体8切割余量后进行氧化处理;需要补充说明二点:一是切割余量后回转体8重量略大于回转体钣金件1理论重量,目的是为了兼顾步骤5)挤压填充率及提高厚向挤压压强,降低设备吨位要求。二是氧化处理目的是在表面形成耐高温氧化膜起到隔离作用,避免金属受热挤压与模具粘连。
30.步骤5)将氧化处理后的回转体8通过挤压模具进行厚向热挤压,使回转体8的壁厚减薄,回转体的环形壁3上的椭圆形细晶粒4顺侧壁被拉长为顺航向纤维晶粒4。需要补充说明四点:一是厚向挤压时,将回转体8与挤压下模11加热到400
±
20℃温度保温,挤压上模12
加热到280
±
20℃温度,目的是避免挤压升温局部组织粗大,确保挤压时材料沿航向大塑性延展,得到类似板料热轧航向纤维晶粒4。二是挤压模具的挤压上模12工作面与回转体钣金件1内表面一致,挤压上模12与挤压下模11工作面合模状态下,上下模之间的间隙等于回转体钣金件1理论厚度,该挤压上模12与挤压下模11工作面大于回转体钣金件1的面积,其目的是利用厚度差增加挤压形成航向纤维晶粒4的数量。三是挤压模具的挤压上模12与挤压下模11工作面的外侧还设有环形非工作面13,在环形非工作13上设有限制合模间隙的耐热承压块14,目的既减少挤压模具精加工区面积,又确保壁厚均匀。
31.步骤6)将回转体8进行加热固溶和淬火冷却完成最终热处理强化,再切割回转体8的余量后得到回转体钣金件1成品。需要补充说明两点:一是对回转体8进行加热固溶时,先将回转体8在300
±
20℃温度预热,再将回转体8转移至494
±
5℃盐炉保温固溶,目的减少高温停留时间,达到充分固溶又减少再结晶,尽量保留步骤5)挤压形成的航向纤维晶粒4。二是对回转体8进行淬火冷却时,先将回转体置于190
±
10℃温度盐炉内预降温,然后将预降温回转体8置于常温水中冷却。目的有两个:一是可以降低大温差极速冷却引起变形,二是硬铝合金主强化相al2cumg析出敏感温度区间300~400℃的,在190℃人工时效温度盐炉环境预冷,可以增加主强化相al2cumg析出时长,进一步提高强化效果。
32.最后为了便于本领域人员理解本技术发明内容,本技术还需要补充说明如下:对金属纤维方向7及纤维组织的解释,通常金属纤维方向是指绝大多数晶粒被明显拉长的方向,对于多数轧制金属板材一般肉眼能看到类似线状条纹,但并无明显手感,这是一个相对概念。实际生产中所指纤维方向一般指宏观肉眼可见条纹方向,实际上金属板材类似多层叠加粘连的棉线条,纤维组织在金属中是相互缠结交错的。在垂直于宏观条纹方向也会存在一定比例被拉长晶粒4,这是轧制金属板材的固有属性;因此本技术所述提升航向载荷性能其实质是沿航向形成了明显多于垂直航向被拉长的纤维状晶粒,并不非将所有晶粒形状全部转变为顺航向纤维晶粒4。