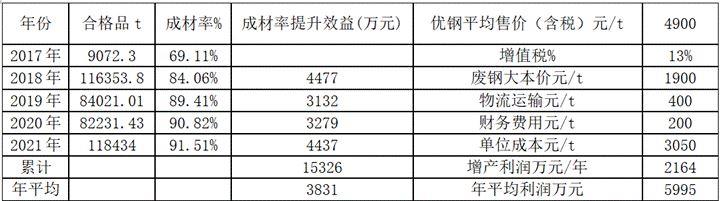
1.本发明涉及一种抑制中小棒优特钢热顶锻裂纹的轧制工艺。
背景技术:2.中小棒优特钢表面裂纹通常通过热顶锻试验和金相试验进行检测;而中小棒优特钢表面裂纹是经常出现的一种严重缺陷,往往由于裂纹处应力集中导致异常开裂或断裂,严重影响下游终端产品的质量;但因热顶锻裂纹其形态表面各异,形成原因复杂,关联因素较多,所以在研究该类缺陷时,很难做出定性分析,更难做出定量分析。 目前国内涉及热顶锻缺陷研究的著述甚少,尚无一部较系统的研究著述问世,这对优特钢表面质量的研究是一大缺憾。
3.八钢小型机组自2000年初开始产品转型,开发轧制中小棒优特圆钢产品,主要以抽油杆钢、齿轮钢、弹簧圆钢等优质碳素结构钢、合金结构钢产品为主。抽油杆钢和齿轮钢圆钢母材在下游用户使用过程中首先要经过锻压成型,弹簧圆钢需进行折弯变形。若圆钢母材没有合格的表面质量,在变形加工过程中就会出现开裂、爆料、断裂等质量缺陷,对用户的连续生产造成影响。
4.由于热顶锻裂纹缺陷产生的原因较为复杂,小型机组前期对其研究总结不够透彻,没建立起一套实用有效的热顶锻裂纹缺陷判断、控制方法。生产过程中出现热顶锻裂纹缺陷时,没有有效性的解决方案,大多靠停机换槽、换导卫进行尝试性解决。一次热顶锻性能不合,需要进行轧槽、导卫检查确认,换槽、换导卫,加热炉升降温过程。调试轧制时,一次热顶锻不合处置经常需要2-4小时才能解决,影响日作业率8.3%
‑‑
16.67%,再剔除正常的换计划时间,小型机组圆钢日作业率实际仅有77%左右。
技术实现要素:5.本发明的目的在于提供一种抑制中小棒优特钢热顶锻裂纹的轧制工艺,设计了圆钢优特钢φ12-60mm规格的孔型、导卫系统经过工艺测试和优化,实现了工厂大批量生产、质量稳定。
6.本发明采用的技术方案是,一种抑制中小棒优特钢热顶锻裂纹的轧制工艺,1)、优特钢防止表面裂纹加热工艺:正常烧嘴开度控制在50%,局部高温烧嘴控制在30%,煤气压力控制在8-10kpa,空气压力控制在4-5kpa,控制火焰长度,控制过热造成热顶锻裂纹;加热温度控制:小型机组在优化加热温度时尽可能的降低加热炉高温段温度,一般高温段温度控制在1150℃以下,保温时快速降低到1100℃以下,控制高温段1160-1120℃的炉内为还原气氛,加热时间为24分钟,过剩系数控制在1.02;加热段1170-1120℃控制为弱氧化气氛,加热时间为25分钟,过剩系数控制在1.05,采用煤气热值作为前馈,空煤比按2.1-2.5设定,利用阀门特性控制空气、煤气阀门的开度,随着温度的变化,接近目标温度时,对空、煤气流量进行控制,烟气残氧量做为后馈控制,实时修正空燃比,达到最优空气、煤气配比,残氧量控制在3-8%,实现高温区域炉内为弱氧化气氛和还原气氛,抑制脱碳层从
而有效防止褶皱热顶锻裂纹缺陷;2)、优特钢防止表面裂纹轧制工艺:设计一种角部r=20mm、孔深=10mm的2#箱型孔型和3#椭箱孔型,箱型孔孔型锁口宽度-轧件边宽≥2mm且≤5mm;立轧圆形轧件孔型基圆直径d≥槽底值≥槽口值,改造立轧进口导板原则如下:宽度l比轧件宽度l大8-10mm,导板高度2h比轧件h大8-10mm。
7.将导轮孔型弧度r1改为与轧件完全匹配的弧度r,使轧件扶持接触部分由点接触变为面接触,增强扶持效果;设计各道次孔型有效杜绝因孔型过充满折叠产生的热顶锻裂纹;对全规格各道次滚动导卫导轮进行优化改型,将导轮孔型弧度r与椭圆轧件弧度r1适配,解决压痕类热顶锻裂纹缺陷;将导卫夹板内部外形结构由矩形变更为椭圆形,椭圆形弧度r与轧件圆弧为同径r弧,使轧件角部接触的部位与夹板接触部位形成圆滑平缓过渡;导卫夹板:粗轧:轧件尺寸+15;中轧:轧件尺寸+8;精轧:轧件尺寸+3;夹板内壁接触面均为曲面、倒角处均为r弧圆滑过渡设计,滚动导卫导轮r弧与椭圆轧件 r弧一致,按上述原则设计各架次导卫有效杜绝中间道次轧件扭转、划伤经后道次连续轧制造成折叠产生的热顶锻裂纹;安装喷淋出水面宽度为115mm的轧辊冷却水管有效解决轧槽均匀冷却避免局部烧槽龟裂;通过粗轧采用箱型孔及孔型角部采用r弧过渡设计,对铸坯角部形成加工面,解决表面缺陷向后道次遗传造成热顶锻裂纹问题。
8.发明效果:表1 2017年-2021.11中小棒优特钢圆钢效益核算表成材率效益提升:从2017年累计69.77%提升至2021年最高91.51%,成材率提升22.4%,成材率年均提升经济效益3831万元/年;增产经济效益:圆钢优特钢产量在2017年前因热顶锻裂纹更换轧槽、导卫、料型调整日均3h左右,按小型各规格平均台时60t/h,影响日产180t/d,按全年生产10个月,每月15天生产优特圆钢核算,全年增产27000t,增产年边际效益总额=801.3
×
27000=2163.5万元/年;累计经济效益总额=3831+2163.5=5995万元/年。
具体实施方式
9.一种抑制中小棒优特钢热顶锻裂纹的轧制工艺,按照下列步骤实施:1、防止过烧、过热热顶锻开裂控制技术:局部过热过烧主要是煤气烧嘴压力控制不合理,火焰过长直接喷到钢坯上,造成这一区域钢坯温度过高,超过过热温度,产生钢坯局部过热。通过调整烧嘴前阀门的开度,正常烧嘴开度控制在50%,局部高温烧嘴控制在30%,煤气压力控制在8-10kpa,空气压力控制在4-5kpa,控制火焰长度,局部过热现象得以
解决。
10.2、防止脱碳引起热顶锻褶皱开裂控制技术,见表2:表2 中小棒优特钢加热温度制度加热温度控制:小型机组在优化加热温度时尽可能的降低加热炉高温段温度,一般高温段温度控制在1150℃以下,保温时快速降低到1100℃以下。
11.炉内气氛的控制:小型机组残氧均热段过剩系数控制在1.02;加热段控制为弱氧化气氛,过剩系数控制在1.05。采用煤气热值作为前馈,空煤比按2.1~2.5设定,利用阀门特性控制空气、煤气阀门的开度,随着温度的变化,接近目标温度时,对空、煤气流量进行控制。烟气残氧量做为后馈控制,实时修正空燃比,达到最优空气、煤气配比,残氧量控制在3-8%。实现高温区域炉内为弱氧化气氛和还原气氛,减少脱碳层。
12.3、防止铸坯角裂遗传热顶锻开裂控制技术:设计一种角部r=20mm、孔深=10mm的2#箱型孔型和3#椭箱孔型。使用这种工艺设计优点如下:
①
可有效对铸坯角部加工“焊合”减轻甚至消除角部缺陷;
②
从根本上避免了角部冷速过快问题;
③
避免了平辊长时间轧制矩形轧件由于磨损形成“箱型孔”轧件从箱型孔边部溢出形成较宽的薄耳。
13.4、防止孔型过充满热顶锻开裂控制技术:依据:型孔孔型锁口宽度-轧件边宽≥2mm且≤5mm;立轧圆形轧件孔型基圆直径d≥槽底值≥槽口值;孔型设计原则工艺人员将各道次实测轧件尺寸与小型基础孔型系统进行比对,经工艺人员辨识发现基础孔型系统2#、8#、10#孔型存在工艺设计缺陷(各规格精轧道次同理),立即进行工艺优化。
14.5、防止轧件倒钢热顶锻开裂控制技术:导卫装置是轧制中必不可少的轧件引导装置,其作用是引导轧件按按既定的轧制轨迹进行轧制。导卫工艺设计不合理会导致椭圆轧件扭转咬入圆孔,变成对角线咬入,俗称“倒钢”。对角线咬入意味着、增大了相对压下量δh,依据宽展模型宽展量随之大幅增大,宽展方向的金属向辊缝处溢出形成耳子,经后续轧制形成折叠。改造立轧进口导板原则如下:宽度l比轧件宽度l大8~10mm,导板高度2h比轧件h大8~10mm。将导轮孔型弧度r1改为与轧件完全匹配的弧度r,使轧件扶持接触部分由点接触变为面接触,增强扶持效果。
15.6、防止导轮压痕热顶锻开裂控制技术:下线的滚动导卫导轮中部经常生锈,边部较其它部位磨损严重现象。这一现象说明导轮在扶持轧件时,只有轮边与轧件接触,为2点接触而非面接触。不但扶持效果不佳还易对热轧态轧件造成表面压痕,经后道次连续轧制仍可形成折叠;工艺技术人员对全规格各道次滚动导卫导轮进行优化改型,将导轮孔型弧度r椭圆轧件弧度r1适配,解决了压痕类热顶锻裂纹缺陷。
16.7、防止导卫夹板划伤热顶锻开裂控制技术:针对于轧件与导卫夹板内壁尖角接触
产生划伤,工艺技术人员将导卫夹板内部外形结构由矩形变更为椭圆形,椭圆形弧度r与轧件圆弧为同径r弧,使轧件角部接触的部位与夹板接触部位形成圆滑平缓过渡;8、防止轧辊辊印、异常磨损引起热顶锻开裂控制技术:辊印折叠重点是轧辊表面的冷却,小型机组技术人员对轧辊冷却水管形式由喷头式改型至双进水管喷淋式水管,按槽宽的1.2倍进行改进,水管宽度由原来的95.8mm,扩展到现在的115mm,极大改善了轧辊表面大面积龟裂。