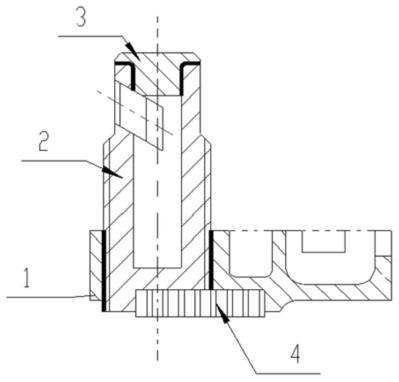
1.本发明涉及机械加工领域,特别涉及一种扇形薄壁蜂窝外环环段的加工方法及夹具。
背景技术:2.扇形薄壁蜂窝外环环段属于典型的结构件,如图1a、图1b、图 1c、图1d、图1e和图1f所示,由零件本体1、堵盖3、双头螺栓2 和蜂窝4组合而成,24个相同结构的扇形薄壁蜂窝外环环段可以通过首尾上下拼接,形成一个环形结构。零件本体1需要通过扇形精铸毛料加工而成,如图2、图3、图4、图5和图6所示,壁厚最小尺寸为0.5mm,其余壁厚基本为1.5mm,扇形弦长为102.6mm,宽为 32.1mm,高为11mm,型面上设计有各种大小不同的凹槽、台阶槽、方口、孔和螺纹等。
3.扇形薄壁蜂窝外环环段体积小,壁厚薄,由镍基高温合金制成,结构复杂,且扇形精铸毛料表面不规则,没有具体的加工流程和工艺,造成加工时难度大。
技术实现要素:4.针对现有技术中存在的问题,本发明提供一种扇形薄壁蜂窝外环环段的加工方法及夹具,可防止零件变形,加工的扇形薄壁蜂窝外环环段符合设计和装配的要求,提高了生产效率和质量,节约成本。
5.本发明是通过以下技术方案来实现:
6.一种扇形薄壁蜂窝外环环段的加工方法,包括如下步骤:s1,将待加工扇形精铸毛料沿其宽度方向垂直放置,以第二外圆槽为定位面,以第二外圆槽的下端面为压紧面,以第一凸台自下而上的一部分为顶紧面,将扇形薄壁最上端端面、未顶紧的第一凸台部分、间隔部和第一外圆槽多余的部分均进行去除,再以第二外圆槽的上端面和第一外圆槽的水平端面为压紧面,以第一凸台已加工的部分为顶紧面,将第一凸台多余的部分去除,最后以第一外圆槽的水平端面为压紧面,顶紧面不变,将扇形薄壁最上端端面和第二外圆槽多余的部分去除;
7.s2,先在工艺孔的外侧加工l型的第一台阶槽,之后将压缩段向外延伸至与第一台阶槽连通,在第一台阶槽垂直段与第一外圆槽对应的位置加工与外界连通的第一矩形缺口,在扇形薄壁长度方向外侧边缘且靠近第一矩形缺口的位置加工与外界连通的弧形缺口,最后将工艺孔加工成内螺纹孔;s3,使扇形薄壁远离第一台阶槽的一端形成一个t型结构且与第一矩形缺口错开,沿t型结构向内在扇形薄壁的内型面加工l型的第二台阶槽,在第二台阶槽水平端与第一矩形缺口相对的位置对称加工第二矩形缺口;然后将双头螺栓、堵盖和内螺纹孔安装后钎焊,在第一凸台上加工凹槽,将蜂窝点焊在凹槽中。
8.优选的,s1中第二外圆槽位于第一外圆槽的下方,水平方向支撑第二外圆槽,自下而上顶紧第一凸台的一部分,压紧第二外圆槽位于下端的水平端面后去除扇形薄壁最上端端面、未顶紧的第一凸台部分、间隔部和第一外圆槽;之后将加工后的扇形精铸毛料上下颠
倒,水平方向支撑第二外圆槽,顶紧与第一外圆槽相对应的扇形薄壁内型面,压紧第一外圆槽位于下端的水平端面和扇形薄壁最上端端面,去除第一凸台,然后不对扇形薄壁最上端端面压紧,其余部分不变,再去除扇形薄壁最上端端面和第二外圆槽。
9.进一步,s2将s1中压紧第一外圆槽位于下端的水平端面部分替换为压紧保留段与主体段的结合处,顶紧与第二外圆槽相对应的扇形薄壁内型面,其余部分不变,再依次加工第一台阶槽、延伸压缩段、第一矩形缺口、弧形缺口和内螺纹孔;s3将加工后的扇形精铸毛料保持s的位置,水平方向支撑第一外圆槽,顶紧与第二外圆槽相对应的扇形薄壁内型面和台阶槽的外侧,压紧扇形薄壁最上端端面,再依次加工t型结构、第二台阶槽和第二矩形缺口。
10.优选的,s3在与内螺纹孔相对应的双头螺栓下端的螺栓槽上加工一圈第一工艺槽,在第一工艺槽上放置钎料,当所述双头螺栓装入内螺纹孔时,双头螺栓的下端面预留加工余量,在与所述双头螺栓相对应的堵盖下端的外壁上加工一圈第二工艺槽,在第二工艺槽上放置钎料,将所述堵盖装入双头螺栓中,将形成的整体进行钎焊;之后将得到的组合物沿堵盖位于水平的方向放置,压紧扇形薄壁最上端端面,再在第一凸台上加工凹槽。
11.进一步,s3所述的钎焊按如下过程进行:先以320~380℃/h的升温速率从室温升到340~360℃,保温10~15min,之后以620~680℃/h 的升温速率从340~360℃升到940~960℃,保温15~20min,最后以 420~540℃/h的升温速率从940~960℃升到1090~1110℃,保温 10~15min;之后先在所述凹槽的底面涂抹相同的钎料,将钎料挤压进蜂窝的蜂格,在蜂窝两侧待焊处涂注相同的钎料,并按如下过程进行;先以320~380℃/h的升温速率从室温升到340~360℃,保温10~15min,之后以620~680℃/h的升温速率从340~360℃升到940~960℃,保温 15~20min,最后以420~540℃/h的升温速率从940~960℃升到 1070~1090℃,保温3~7min。
12.一种用于上述的扇形薄壁蜂窝外环环段的加工方法的加工夹具, s1在去除扇形薄壁最上端端面、未顶紧的第一凸台部分、间隔部和第一外圆槽多余的部分时采用如下所述的第一夹具:所述的第一夹具包括第一夹具本体、第一定位块、第一压紧块和第一压板,扇形精铸毛料垂直设置在第一夹具本体的上表面,第二外圆槽位于第一外圆槽的下方,第一夹具本体上表面沿垂直于扇形精铸毛料的方向开设有t 型槽,扇形精铸毛料沿t型槽固定在第一夹具本体上表面,第二外圆槽被压紧在第一压板的水平端下方,第一定位块固定在第一压板的一侧,第一定位块固定插接在第二外圆槽的末端中,第一压紧块的一侧与第一凸台的一部分接触设置,第一压紧块的另一侧与第一六角头压紧螺钉的一端接触设置,第一六角头压紧螺钉和第一压紧块接触部分的上表面设置有第一导板,第一六角头压紧螺钉在第一导板中活动设置,第一导板的一侧固定有第一支板,第一支板中设置有能与第一六角头压紧螺钉外螺纹配合的内螺纹,第一六角头压紧螺钉水平转动设置在第一支板的内螺纹中。
13.一种用于上述的扇形薄壁蜂窝外环环段的加工方法的加工夹具, s1在去除第一凸台多余的部分时采用如下所述的第二夹具:所述的第二夹具包括第二夹具本体、第二压板、第三压板和第二压紧块,加工后的扇形精铸毛料垂直设置在第二夹具本体的一侧,第二外圆槽位于第一外圆槽的上方,第二外圆槽中设置有支撑块,第二压板和第三压板通过螺柱和调节支撑均水平固定在第二夹具本体的上方,第二压板压紧在加工后的扇形薄壁最上
端端面,第三压板压紧在第一外圆槽位于下端的水平端面,第二压紧块的一侧与第一凸台的一部分接触设置,第二压紧块的另一侧与第二六角头压紧螺钉的一端接触设置,第二夹具本体上固定有支座,支座中设置有能与第二六角头压紧螺钉外螺纹配合的内螺纹,第二六角头压紧螺钉水平转动设置在支座的内螺纹中;s1在去除扇形薄壁最上端端面和第二外圆槽多余的部分时,采用将第二夹具中关于第二压板的部分去除后的夹角进行。
14.一种用于上述的扇形薄壁蜂窝外环环段的加工方法的加工夹具, s2在加工第一台阶槽、第一矩形缺口、弧形缺口、内螺纹孔和延伸压缩段时采用如下所述的第三夹具:所述的第三夹具包括基座、定位块、第四压板和第二压紧块,定位块开设有缺口,定位块固定在基座的上表面,车基准后的零件上下放置在定位块缺口的水平端,定位块缺口的另一端为与车基准后的零件配合的圆弧面,所述圆弧面设置有与第一外圆槽和第二外圆槽形状相适应的凸起,第一外圆槽和第二外圆槽分别插接在对应的凸起中,定位块与第二外圆槽靠近工艺孔的一侧之间填充有顶块,第四压板通过螺柱和调节支撑水平固定在基座的上方,第四压板压紧在车基准后的零件最上端端面,第二压紧块的一侧与第一凸台接触设置,第二压紧块的另一侧与第三六角头压紧螺钉的一端接触设置,基座上固定有支撑座,支撑座中设置有能与第三六角头压紧螺钉外螺纹配合的内螺纹,第三六角头压紧螺钉水平转动设置在支撑座的内螺纹中,第二压紧块的一侧固定有限位块,限位块顶紧在车基准后的零件靠近工艺孔的一端。
15.一种用于上述的扇形薄壁蜂窝外环环段的加工方法的加工夹具, s3在加工t型结构、第二台阶槽和第二矩形缺口时采用如下所述的第四夹具:所述的第四夹具包括第一基座、第一定位块、第五压板和第三压紧块,第一定位块开设有缺口,第一定位块固定在第一基座的上表面,车加工后的零件上下放置在第一定位块缺口的水平端,第一定位块缺口的另一端为与车加工后的零件配合的圆弧面,所述圆弧面设置有与第一外圆槽形状相适应的凸起,第一外圆槽插接在凸起中,第五压板通过螺柱和调节支撑水平固定在第一基座的上方,第五压板压紧在车加工后的零件最上端端面,第三压紧块的一侧与第一凸台接触设置,第三压紧块的另一侧与第四六角头压紧螺钉的一端接触设置,第一基座上固定有支撑座,支撑座中设置有能与第四六角头压紧螺钉外螺纹配合的内螺纹,第四六角头压紧螺钉水平转动设置在支撑座的内螺纹中,车加工后的零件靠近内螺纹孔的一侧固定有第一限位块。
16.一种用于上述的扇形薄壁蜂窝外环环段的加工方法的加工夹具, s3在加工第一凸台时采用如下所述的第五夹具:所述的第五夹具包括第五夹具本体、第六压板、调节支撑和螺柱,加工后的零件上下设置在第五夹具本体的一侧,第六压板通过螺柱和调节支撑水平固定在第五夹具本体的上方,调节支撑的上端位于第六压板的下端面,调节支撑的下端固定在第五夹具本体中,螺柱上位于第五夹具本体和第六压板之间的位置套接有压簧,第六压板压紧在加工后的零件最上端端面。
17.与现有技术相比,本发明具有以下有益的技术效果:
18.本发明一种扇形薄壁蜂窝外环环段的加工方法,将待加工扇形精铸毛料垂直放置可以保证有足够的压紧空间,可方便以第二外圆槽为定位面,以第二外圆槽下端面为压紧面,以第一凸台自下而上的一部分为顶紧面,便可顺利去除扇形薄壁最上端端面、未顶紧的第一凸台部分、间隔部和第一外圆槽多余的部分,之后以第二外圆槽的上端面和第一外圆槽的水平端面为压紧面,以第一凸台已加工部分为顶紧面,可将第一凸台多余的部分去除,
最后将压紧面变为第一外圆槽的水平端面,可将扇形薄壁最上端端面和第二外圆槽多余的部分去除,至此完成了基准的加工;所以之后可以方便地在工艺孔的外侧加工l型的第一台阶槽和压缩段向外延伸至与第一台阶槽连通,这样才可以在第一台阶槽垂直段与第一外圆槽对应的位置加工与外界连通的第一矩形缺口,在扇形薄壁长度方向外侧边缘且靠近第一矩形缺口的位置加工与外界连通的弧形缺口,最后将工艺孔加工成内螺纹孔,至此完成了台阶槽、缺口和内螺纹孔的加工,这样方可在扇形薄壁远离第一台阶槽的一端加工t型结构且与第一矩形缺口错开,沿t型结构向内在内型面加工l型的第二台阶槽,在第二台阶槽水平端与第一矩形缺口相对的位置对称加工第二矩形缺口;最后将双头螺栓、堵盖和内螺纹孔安装后钎焊,在第一凸台上加工凹槽,将蜂窝点焊在凹槽中即可。本发明加工质量高,满足了扇形薄壁蜂窝外环件的加工,解决了该类零件在加工时工艺过程冗长,圆弧方向无法确定,加工难度大和产品质量差的难题,在薄壁扇形零件的加工方面具有较高的技术含量和借鉴价值,也为后续类似零件的加工积累了丰富的技术经验。
19.本发明一种扇形薄壁蜂窝外环环段的加工夹具,将扇形精铸毛料上下设置在第一夹具本体上表面,可使第二外圆槽位于第一外圆槽下方,在第一夹具本体上表面沿垂直于扇形精铸毛料的方向开设有t 型槽,扇形精铸毛料可沿t型槽固定在第一夹具本体上表面,进而第二外圆槽被压紧在第一压板的水平端下方,第一定位块固定插接在第二外圆槽的末端中便于对扇形精铸毛料定位,第一压紧块一侧与第一凸台的一部分接触,另一侧与第一六角头压紧螺钉一端接触,这样当第一六角头压紧螺钉和第一压紧块接触部分的上表面设置第一导板后,第一六角头压紧螺钉能在第一导板中活动,在第一支板中设能与第一六角头压紧螺钉外螺纹配合的内螺纹,这样当第一六角头压紧螺钉水平转动后可顶紧顶紧第一凸台的一部分,最终可对扇形薄壁最上端端面、未顶紧的第一凸台部分、间隔部和第一外圆槽多余的部分进行去除。
附图说明
20.图1a为本发明所述扇形薄壁蜂窝外环环段的内部连接侧视图。图1b为本发明所述扇形薄壁蜂窝外环环段的内部连接主视图;图1c 为图1a中零件本体的部分表面结构图;图1d为图1b中b-b处的剖视图;图1e为本发明所述扇形薄壁蜂窝外环环段的内型面结构视角图;图1f为本发明所述扇形薄壁蜂窝外环环段的外型面结构视角图;图2为本发明所述扇形精铸毛料的剖面图;图3为图2中a-a处的剖面图;图4为本发明所述扇形精铸毛料的部分表面结构图;图5为图3中b-b处的剖视图;图6为本发明所述扇形精铸毛料的结构图;图7a为本发明所述的车基准部位示意图;图7b为图7a的a-a处剖面图;图7c为本发明所述扇形精铸毛料的车基准装夹部分俯视图;图7d为图7c的内部连接主视图;图8a为本发明所述的车另一基准部位示意图;图8b为图8a的a-a处剖面图;图8c为本发明所述车另一基准的装夹部分俯视图;图8d为图8c的内部连接主视图;图 9a为本发明所述的铣端面及台阶部位示意图;图9b为图9a的b-b 处剖面图;图9c为图9a的c-c处剖面图;图9d为本发明所述的铣端面及台阶表面部位示意图;图9e为本发明所述铣端面及台阶的装夹结构图;图10a为本发明所述的铣台阶部位示意图;图10b为图 10a的a-a处剖面图;图10c为图10b的c-c处剖面图;图10d为图 10a的b-b处剖面图;图10e为本发明所述铣台阶的装夹结构图;图 11a为本发明所述的钎焊螺栓及堵盖部位示意图;图11b为图11a虚线处的剖面图;图11c为本发明所述的堵盖加工部
位图;图11d为本发明所述的双头螺栓加工部位图;图12a为本发明所述的车内环槽部位示意图;图12b为图12a的b-b处剖面图;图12c为本发明所述车内环槽的装夹部分俯视图;图12d为图12c的内部连接主视图;图 13a为本发明所述的钎焊蜂窝部位示意图;图13b为图13a虚线处的剖面图;图13c为本发明所述的钎料在蜂窝的挤压部位图;图14a为本发明所述的线切割蜂窝部位示意图;图14b为图14a虚线处的剖面图;图15为本发明所述的电加工参数图。
21.图中:零件本体1、双头螺栓2、堵盖3、蜂窝4、通孔5、第一凸台6、内螺纹孔11、第一外圆槽12、基准圆13、工艺孔14、第二外圆槽15、第二凸台16、第一台阶槽171、第二台阶槽172、第一矩形缺口18、弧形缺口19、第二矩形缺口20、方槽21、第一工艺槽 22、第二工艺槽31、第一夹具本体32、第一定位块33、第一六角头压紧螺钉34、第一支板35、第一导板36、第一压紧块37、第一压板 38、第一六角螺母39、第一调节支撑310、第二六角螺母311、第一圆柱头螺钉312、第一吊环衬套313、第一带肩六角螺母314、第一等长双头螺柱315、第一圆柱销316、第一内六角螺钉317、多余蜂窝41、挤压钎料处42、切割处43、第二夹具本体44、螺纹衬套45、第二压板46、内六角圆柱头螺钉47、第二六角头压紧螺钉48、支座 49、第三六角螺母410、第二调节支撑411、螺柱412、第三压板414、螺栓415、第三调节支撑416、第二压紧块417、开槽圆柱头螺钉418、第二吊环衬套419、第二内六角螺钉420、第四调节支撑51、螺母52、第四压板53、第三六角头压紧螺钉54、第二压紧块55、支撑板56、限位块57、车基准后的零件58、顶块59、定位块510、基座511、第五压板63、第四六角头压紧螺钉64、第三压紧块65、第一支撑板 66、第一限位块67、车加工后的零件68、第一定位块610、第一基座611、第四六角螺母81、第五调节支撑82、第六压板83、第二带肩六角螺母84、第二等长双头螺柱85、压簧86、垫圈87、第五夹具本体88、衬套89、开槽圆柱头螺钉810。
具体实施方式
22.下面结合具体的实施例对本发明做进一步的详细说明,所述是对本发明的解释而不是限定。
23.本发明一种扇形薄壁蜂窝外环环段的加工方法,该外环环段的结构图如图1a、图1b、图1c、图1d、图1e和图1f所示,图中的粗实线代表加工部位。由于主体为扇形薄壁结构的零件本体1的内型面、外型面均属于圆弧,如图1d可以看到外型面有2处凹槽,内型面有 1处用于焊接蜂窝4的凹槽,双头螺栓2、堵盖3与零件本体1组合后高出零件本体1的外型面,因此需要在双头螺栓2、堵盖3与零件本体1组合前,将零件本体1外型加工到尺寸,双头螺栓2上加工有方槽21;同时装配后双头螺栓2与蜂窝4上表面接触的位置,不能满足蜂窝4的焊接要求,因此双头螺栓2大端需留一定的余量,并在组合后进行加工内孔蜂窝安装槽,满足焊接蜂窝4的要求。由于零件本体1与螺栓2采用螺纹连接,螺栓2与堵盖3通过止口配合,需要使钎焊无焊瘤,表面完整性好,能保证使用要求,对零件的影响较小,表面完整。同时由于蜂窝4材质较软、表面形状不规整,之后装配时不能和蜂窝4干涉,因此在焊接后切割蜂窝4的两端,与零件本体1 的基体接平。
24.零件本体1所使用的扇形精铸毛料如图2、图3、图4、图5和图6所示,图示中的为后续加工余量部位。扇形精铸毛料主体为扇形薄壁结构,扇形薄壁的外型面上沿扇形薄壁的长度方向设有长条状的第一外圆槽12和第二外圆槽15,第一外圆槽12和第二外圆槽15
之间的长条状部分即为间隔部,扇形薄壁的内型面与第二外圆槽15相对应的位置向内延伸有第一凸台6。具体地,第一外圆槽12 和第二外圆槽15沿扇形薄壁长度方向延伸至扇形薄壁的两端,第二外圆槽15包括相互连通的主体段和压缩段,压缩段宽度小于主体段且靠近第一外圆槽12,扇形薄壁外型面与压缩段、主体段相对应的部分为保留段,保留段预留有与外界连通的工艺孔14。扇形精铸毛料的水平长度为107.11mm,为铸件,按照铸件公差标准,所有零件本体1的直径公差应相等,且数值在0~+0.8mm,因为当尺寸不一致时就无法保证最小壁厚为0.5mm的要求,因此首先在该扇形精铸毛料上需要建立工艺基准,并且要控制基准尺寸的公差,根据最小壁厚尺寸的位置,将径向基准选择在基准圆13的凹槽里,直径公差按照 176
±
0.2mm控制,轴向尺寸的公差按照32.1
±
0.3mm控制。同时该扇形精铸毛料对应的扇形段小,各个台阶槽、通孔5在圆周方向都有相对确定的位置,因此在扇形精铸毛料上设计直径为6mm的工艺孔14,在后续的钻通孔5、铣加工以确定对应槽和通孔5的位置。具体的加工方法包括如下步骤:
25.步骤1,车基准:
26.如图7a和图7b所示,将扇形精铸毛料沿其宽度方向上下放置,第二外圆槽15位于第一外圆槽12的下方,以毛料的端面a来定位轴向(即图7b的高度方向);水平方向支撑第二外圆槽15,自下而上顶紧第一凸台6的一部分,压紧第二外圆槽15位于下端的水平端面,按照设计的尺寸,将扇形薄壁最上端端面多余的部分、未顶紧的第一凸台6部分多余的部分、间隔部多余的部分和第一外圆槽12多余的部分均进行去除。
27.具体地,如图7c和图7d所示,采用如下的第一夹具夹持扇形精铸毛料进行上述操作。第一夹具主要包括第一夹具本体32、第一定位块33、第一压紧块37和第一压板38,扇形精铸毛料上下放置在第一夹具本体32上表面,第二外圆槽15位于第一外圆槽12的下方,第一夹具本体32上表面沿垂直于扇形精铸毛料的方向开设有t型槽,扇形精铸毛料沿t型槽固定在第一夹具本体32上表面,第二外圆槽 15被压紧在第一压板38的水平端下方,即用第一压板38压紧了第二外圆槽15凹槽处的端面b,防止了零件在加工时窜动。第一定位块33固定在第一压板38的一侧,第一定位块33固定插接在第二外圆槽15的末端中,第一压紧块37的一侧与第一凸台6的一部分接触,因此第一压紧块37是与第一凸台6形状对应的扇形结构,即第一压紧块37支撑了图7b中的凹槽面c,第一压紧块37的另一侧与第一六角头压紧螺钉34一端接触,第一六角头压紧螺钉34和第一压紧块 37接触的部分上表面设有第一导板36,第一六角头压紧螺钉34在第一导板36中活动设置,第一导板36一侧固定有第一支板35,第一支板35中设有能与第一六角头压紧螺钉34外螺纹配合的内螺纹,第一六角头压紧螺钉34水平转动设置在第一支板35的内螺纹中,这样通过第一六角头压紧螺钉34的转动即可使第一六角头压紧螺钉34顶紧3b中的内孔面d控制径向,可防止内孔,采用了点接触顶紧零件,增加接触面积,消除压伤零件。为保证长方形的内孔面d有足够的压紧空间,在之后车内孔时不一次加工通,内孔面d一侧形成的台阶为预留的接刀台,在步骤2车另一基准工序时再将内孔加工通。
28.在具体操作时,将第一夹具本体32设计成一个整圆环形,通过第一圆柱头螺钉312和第一吊环衬套313将若干个形状相同的圆环固定成第一夹具本体32。第一压板38选择常规结构的压板,在固定第一压板38时,在远离零件的一端通过第一等长双头螺柱315和圆柱结构的第一调节支撑310将第一压板38固定在t型槽中,第一调节支撑310上端安装有第二
六角螺母311,第一等长双头螺柱315与第一夹具本体32上表面接触的位置安装有第一六角螺母39,第一等长双头螺柱315与第一压板38上表面接触的位置安装有第一带肩六角螺母314。在固定第一定位块33时,在第一定位块33上表面对称安装有两个第一圆柱销316和四个第一内六角螺钉317。如此一来,夹具的整个圆周方向便可依次装夹24个扇形精铸毛料拼成整圆,按照上述说明对每个扇形精铸毛料进行第一夹具的装配,同时注意消除零件之间的间隙,形成整盘装夹,这样可以提高加工效率;加工前打表检查基准圆13的径向尺寸,符合尺寸要求时依次车与上述说明对应的端面、外圆和内孔。为便于观察和装夹零件,加工时选择数控立车加工。车基准是之后工序的标准,起着至关重要的作用。
29.步骤2,车另一基准:
30.如图8a和图8b所示,采用端面e定位控制轴向;用已加工的外圆面f定位控制径向;将加工后的扇形精铸毛料上下颠倒,水平方向支撑第二外圆槽15,顶紧与第一外圆槽12相对应的扇形薄壁内型面,压紧第一外圆槽12位于下端的水平端面和扇形薄壁最上端端面,按照设计尺寸,将第一凸台6多余的部分去除;不对扇形薄壁最上端端面压紧,其余部分不变,按照设计尺寸,将扇形薄壁最上端端面和第二外圆槽15多余的部分去除。
31.具体地,如图8c和图8d所示,采用如下的第二夹具夹持加工后的扇形精铸毛料进行上述操作。第二夹具主要包括了第二夹具本体 44、第二压板46、第三压板414和第二压紧块417,加工后的扇形精铸毛料上下放置在第二夹具本体44的一侧,第二外圆槽15位于第一外圆槽12上方,第二外圆槽15中设有支撑块,第二外圆槽15作为辅助支撑,第二压板46和第三压板414通过两对螺柱412和调节支撑均水平固定在第二夹具本体44的上方,螺柱412和调节支撑垂直于第二压板46和第三压板414,第二压板46和第三压板414对称分布在加工后的扇形薄壁的两侧,第二压板46压紧在加工后的扇形薄壁最上端端面,第三压板414压紧在第一外圆槽12位于下端的水平端面,第二压紧块417的一侧与第一凸台6的一部分接触,第二压紧块417另一侧与第二六角头压紧螺钉48的一端接触,第二夹具本体 44上固定有支座49,支座49中设有能与第二六角头压紧螺钉48外螺纹配合的内螺纹,第二六角头压紧螺钉48水平转动设置在支座49 的内螺纹中,这样便可将内孔面(是本领域的一种通俗叫法,没有孔,是弧面)h顶紧,压紧a面和g面。本工序既要车端面内孔、又要车外圆,无法一次装夹完成,因此采用倒压板的形式,受零件过小,每个零件都需要压紧,先车内孔。之后在将扇形薄壁最上端端面和第二外圆槽15多余的部分去除时,采用将第二夹具中关于第二压板46 的部分去除后的夹角进行,即去掉第二压板46,依然压紧g面加工外圆。
32.在具体操作时,将第二夹具本体44设计成一个整圆环形,通过开槽圆柱头螺钉418、第二吊环衬套419将若干个形状相同的圆环固定成第二夹具本体44。调节支撑分为第二调节支撑411和第三调节支撑416,第二调节支撑411上位于第二压板46的下表面安装有第三六角螺母410,螺柱412上位于第三压板414的上表面安装有第一六角螺母39。在固定支座49时,在支座49上安装第二内六角螺钉 420和内六角圆柱头螺钉47。如此一来,装夹时在夹具的整个圆周方向依次装夹24个零件,可消除零件之间的间隙,形成整盘装夹,提高加工效率。为便于观察和装夹零件,加工时选择数控立车加工。
33.步骤3,铣各个缺口及台阶槽、通孔:
34.车加工已将毛料的轴向和径向加工余量去除,建立了精加工基准,铣加工相对较为容易,如图9a、图9b、图9c和图9d所示的部位,采用端面e定位控制轴向,外圆面f定位控制
径向。将上述步骤中压紧第一外圆槽12位于下端的水平端面部分代替为压紧保留段与主体段的结合处,顶紧与第二外圆槽15相对应的扇形薄壁内型面,其余部分不变,按照设计尺寸,先在工艺孔14的外侧加工l型的第一台阶槽171,将压缩段向外延伸至与第一台阶槽171连通,在第一台阶槽171垂直段与第一外圆槽12对应的位置加工与外界连通的第一矩形缺口18,在扇形薄壁长度方向外侧边缘并且靠近第一矩形缺口 18的位置加工与外界连通的弧形缺口19,最后将工艺孔14加工成内螺纹孔11,加工如图1f所述的通孔5,通孔5位于内螺纹孔11的侧面,与第二外圆槽15的主体段相对应,并与内螺纹孔11连通;
35.具体地,如图9e所示,采用如下的第三夹具夹持扇形精铸毛料进行上述操作。第三夹具主要包括基座511、定位块510、第四压板53 和第二压紧块55,定位块510开设有缺口,定位块510固定在基座 511的上表面,车基准后的零件58上下放置在定位块510缺口的水平端,定位块510缺口的另一端为与车基准后的零件58配合的圆弧面,圆弧面设置有与第一外圆槽12和第二外圆槽15形状相适应的凸起,第一外圆槽12和第二外圆槽15分别插接在对应的凸起中,定位块510与第二外圆槽15靠近工艺孔14的一侧之间填充有顶块59,第四压板53通过螺柱和第四调节支撑51水平固定在基座511的上方,螺柱和第四调节支撑51的下端均固定在位于基座511上的支撑板56 中,螺柱上位于第四压板53的上表面安装有螺母52,第四压板53 压紧在车基准后的零件58最上端端面,第二压紧块55的一侧与第一凸台6接触,第二压紧块55的另一侧与第三六角头压紧螺钉54的一端接触,基座511上固定有支撑座,支撑座中设置有能与第三六角头压紧螺钉54外螺纹配合的内螺纹,第三六角头压紧螺钉54水平转动设置在支撑座的内螺纹中,第二压紧块55的一侧固定有限位块57,限位块57顶紧在车基准后的零件58靠近工艺孔14的一端。这样可以压板压紧端面a,顶紧内孔面d,顶块59定位面t防止铣削时零件的窜移,对于零件的圆周方向,加工前找正工艺孔14(先不加工螺纹)以确定其余加工部位与它的相对关系。受加工部位的限制只能单件装夹加工,本工序的夹具结构与车基准时使用的夹具结构相同,只是尺寸需要适应性调整。为便于观察、装夹和对刀零件,加工时选择卧式加工中心。
36.步骤4,铣台阶槽、缺口:
37.如图10a、图10b、图10c和图10d所示,采用端面e定位控制轴向,外圆面f和面h定位控制径向。将加工后的扇形精铸毛料保持步骤3所述的位置,水平方向支撑第一外圆槽12,顶紧与第二外圆槽15相对应的扇形薄壁内型面和台阶槽17的外侧,压紧扇形薄壁最上端端面,按照设计的尺寸,先使扇形薄壁远离第一台阶槽171的一端形成一个t型结构且与第一矩形缺口18错开,t型结构中包含着一个第二凸台16,之后沿t型结构向内在扇形薄壁的内型面加工l 型的第二台阶槽172,最后在第二台阶槽172水平端与第一矩形缺口 18相对的位置对称加工第二矩形缺口20。
38.具体地,如图10e所示,采用如下的第四夹具夹持上述车加工后的零件68进行上述操作。第四夹具主要包括了第一基座611、第一定位块610、第五压板63和第三压紧块65,第一定位块610开设缺口,第一定位块610固定在第一基座611上表面,车加工后的零件 68上下放置在第一定位块610缺口水平端,第一定位块610缺口的另一端为与车加工后的零件68配合的圆弧面,圆弧面设有与第一外圆槽12形状相适应的凸起,第一外圆槽12插接在凸起中,第五压板 63通过螺柱和调节支撑水平固定在第一基座611的上方,螺柱和调节支撑的下端均固定在位于第一基座611上的第一支撑板66中,螺柱上位于第五压板63的上表面安
装有螺母,第五压板63压紧在车加工后的零件68最上端端面,第三压紧块65的一侧与第一凸台6接触,第三压紧块65的另一侧与第四六角头压紧螺钉64的一端接触,第一基座611上固定有支撑座,支撑座中设有能与第四六角头压紧螺钉 64外螺纹配合的内螺纹,第四六角头压紧螺钉64水平转动设置在支撑座的内螺纹中,车加工后的零件68靠近内螺纹孔11的一侧固定有第一限位块67。压紧端面a,顶紧内孔d进行铣零件的凹槽及外型面。受加工部位的限制只能单件装夹加工。为便于观察、装夹和对刀零件,加工时选择卧式加工中心。
39.步骤5,钎焊双头螺栓2及堵盖3:
40.扇形薄壁蜂窝外环环段中的堵盖3、双头螺栓2和零件本体1,受零件结构限制,零件焊前难以预置钎料,如图11c和11d所示,采用了焊前在堵盖3和双头螺栓2的螺栓槽上加工工艺槽的方式预置钎料,双头螺栓2的端面预留加工余量。具体地,如图11a和11b所示,在与内螺纹孔11相对应的双头螺栓2下端螺栓槽上加工一圈第一工艺槽22,在第一工艺槽22上放置钎料,当双头螺栓2装入内螺纹孔 11时,在双头螺栓2的下端面预留有加工余量,在与双头螺栓2相对应的堵盖3下端的外壁上加工一圈第二工艺槽31,在第二工艺槽 31上放置钎料,将堵盖3装入双头螺栓2中,将形成的整体进行真空钎焊。
41.具体地,在真空钎焊炉中制定阶梯式真空钎焊工艺参数,避免钎料的二次重熔,具体地,钎料选用b-ni73crsib-40ni-s,冷态真空度和工作真空度均小于4
×
10-2
pa,先以320~380℃/h的升温速率从室温升到340~360℃,保温10~15min,之后以620~680℃/h的升温速率从 340~360℃升到940~960℃,保温15~20min,最后以420~540℃/h的升温速率从940~960℃升到1090~1110℃,保温10~15min,真空冷却到950℃以下,填充高纯氮气,用风扇冷却到80℃以下。如图11a和图11b所示,在堵盖3和双头螺栓2装配定位前选配加工零件,保证零件的装配间隙在0.03~0.08mm。
42.步骤6,车内环槽:
43.如图12a和图12b所示,采用外圆面f控制径向,端面e定位控制轴向。将步骤5得到的组合物沿堵盖3位于水平的方向放置,压紧扇形薄壁最上端端面,按照设计的尺寸,在第一凸台6中加工用于焊接蜂窝4的凹槽。具体地,如图12c和图12d所示,采用如下的第五夹具夹持上述车加工后的零件进行上述操作。第五夹具主要包括了第五夹具本体88、第六压板83、第五调节支撑82和第二等长双头螺柱 85。将第五夹具本体88设计成一个整圆环形,通过衬套89、开槽圆柱头螺钉810将若干个形状相同的圆环固定成第五夹具本体88。加工后的零件上下设置在第五夹具本体88的一侧,第六压板83通过第二等长双头螺柱85和第五调节支撑82水平固定在第五夹具本体88 的上方,具体的是第五调节支撑82的上端位于第六压板83的下端面,第五调节支撑82的下端固定在第五夹具本体88中,第五调节支撑 82上位于第五夹具本体88的上表面安装有第四六角螺母81,第二等长双头螺柱85上位于第五夹具本体88和第六压板83之间的位置套接有压簧86,压簧86的下端和第五夹具本体88的上端安装有螺母,压簧86上端和第六压板83下端面之间的位置安装有垫圈87,第二等长双头螺柱85的上端安装有第二带肩六角螺母84,第六压板83 压紧在加工后的零件最上端端面,这样可以压紧面a,加工内孔槽得到用于焊接蜂窝4的凹槽,将零件装成整盘进行车削,在夹具的整个圆周方向依次装夹24个零件,互相之间搭肩装夹,此时模拟了零件的装配使用,形成整盘装夹。为便于观察和装夹零件,加工时选择数控立车加工。
44.步骤7,钎焊蜂窝:
45.如图13a和图13b所示,真空钎焊前在已加工好的凹槽内环槽底面涂抹步骤5所述的钎料,使用钎料挤压机将钎料挤压进蜂窝的蜂格,即如图13c所示的挤压钎料处42,然后使用软电极和夹具采用点焊方式,将蜂窝4点焊定位在凹槽上,焊点与焊点之间应搭接20%~30%,定位完成后在蜂窝4两侧待焊处涂注钎料并将零件放入真空钎焊炉中,按照如下的工艺进行焊接:冷态真空度和工作真空度均小于 4
×
10-2
pa,先以320~380℃/h的升温速率从室温升到340~360℃,保温10~15min,之后以620~680℃/h的升温速率从340~360℃升到 940~960℃,保温15~20min,最后以420~540℃/h的升温速率从 940~960℃升到1070~1090℃,保温3~7min,真空冷却到950℃以下,填充高纯氮气,用风扇冷却到80℃以下。
46.步骤8,线切割蜂窝,
47.如图14a和图14b所示,为保证焊接蜂窝4后,蜂窝4的完整性,将蜂窝4两端多出一定的长度,如图13a中所示的多余蜂窝41,然后按照设计要求的尺寸将多余的切除,保证装配时无干涉现象。由于蜂窝4承受力强,构造精巧,壁薄,无法采用机加的方式进行加工,只能采用电加工的方式按照图14a所示的切割处43去消除多余的蜂窝。
48.具体地,为将多余的蜂窝切除掉,选择在数控线切割机上进行加工,加工前找正零件的切割面,在零件本体1表面对丝,然后进行切割,保证与零件本体1齐平。
49.电加工参数如图15所示。最终该工艺满足了外环环段的使用要求,之后即可进行交付。